浅析FMEA实际应用中的局限性20140603
FMEA失效模式与影响分析
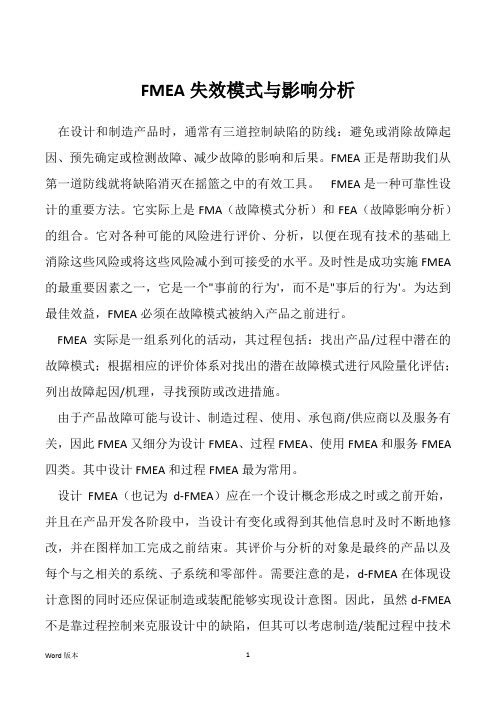
FMEA失效模式与影响分析在设计和制造产品时,通常有三道控制缺陷的防线:避免或消除故障起因、预先确定或检测故障、减少故障的影响和后果。
FMEA正是帮助我们从第一道防线就将缺陷消灭在摇篮之中的有效工具。
FMEA是一种可靠性设计的重要方法。
它实际上是FMA(故障模式分析)和FEA(故障影响分析)的组合。
它对各种可能的风险进行评价、分析,以便在现有技术的基础上消除这些风险或将这些风险减小到可接受的水平。
及时性是成功实施FMEA 的最重要因素之一,它是一个"事前的行为',而不是"事后的行为'。
为达到最佳效益,FMEA必须在故障模式被纳入产品之前进行。
FMEA实际是一组系列化的活动,其过程包括:找出产品/过程中潜在的故障模式;根据相应的评价体系对找出的潜在故障模式进行风险量化评估;列出故障起因/机理,寻找预防或改进措施。
由于产品故障可能与设计、制造过程、使用、承包商/供应商以及服务有关,因此FMEA又细分为设计FMEA、过程FMEA、使用FMEA和服务FMEA 四类。
其中设计FMEA和过程FMEA最为常用。
设计FMEA(也记为d-FMEA)应在一个设计概念形成之时或之前开始,并且在产品开发各阶段中,当设计有变化或得到其他信息时及时不断地修改,并在图样加工完成之前结束。
其评价与分析的对象是最终的产品以及每个与之相关的系统、子系统和零部件。
需要注意的是,d-FMEA在体现设计意图的同时还应保证制造或装配能够实现设计意图。
因此,虽然d-FMEA 不是靠过程控制来克服设计中的缺陷,但其可以考虑制造/装配过程中技术的/客观的限制,从而为过程控制提供了良好的基础。
进行d-FMEA有助于:设计要求与设计方案的相互权衡;制造与装配要求的最初设计;提高在设计/开发过程中考虑潜在故障模式及其对系统和产品影响的可能性;为制定全面、有效的设计试验计划和开发项目提供更多的信息;建立一套改进设计和开发试验的优先控制系统;为将来分析研究现场情况、评价设计的更改以及开发更先进的设计提供参考。
FMEA:缺陷模式和影响分析.pptx
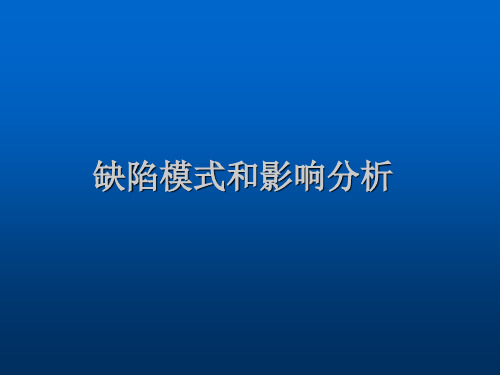
LATCH
FINAL ARM ARM SUB ARM COIL
BOBBIN ROT. ARM
ARM SUB ARM SUB
必须建立团队来评估FMEA的应用。应用范围列在图中,团队需在以下原则 的指导下展开工作:
-建立策略聚焦于新技术、过去的问题、新的或重新设计的元件上。从产品(设计)和过 程两方面来考虑
4. 通过脑力激荡法确定潜在的缺陷
模式
功能 缺陷模式
基本步骤
1. 确定战略 2. 评审设计/过程 3. 列出功能清单 4.通过脑力激荡法确定潜在的缺陷模式
5. 组织潜在的缺陷模式
topic
topic
亲和图
基本步骤
1. 确定战略 2. 评审设计/过程 3. 列出功能清单 4.通过脑力激荡法确定潜在的缺陷模式 5. 组织潜在的缺陷模式
缺陷模式和影响分析
FMEA的定义
FMEA是一种系统化的设计评估系统,其目标为:
1. 认可和评估潜在的缺陷模式及其原因与设计 及制造新产品或升级现有产品的关系。
2. 确定用于消除和降低潜在缺陷发生机会的行 动。
3. 文件化过程。
缺陷模式可能是 . .
完成一个确定功能时的缺陷 不希望发生的事件 错误的应用
• 14、Thank you very much for taking me with you on that splendid outing to London. It was the first time that I had seen the Tower or any of t he other famous sights. If I'd gone alone, I couldn't have seen nearly as much, because I wouldn't have known my way about.
FMEA常见问题及改进措施

FMEA常见问题及改进措施摘要:本文主要阐述了故障模式及影响分析(FMEA)工作在产品研发过程中开展的意义,列举了FMEA工作开展过程中存在的一些问题,并针对这些问题提出了改进建议,使FMEA工作在提高产品可靠性方面发挥更大的效能。
关键词:故障模式,故障影响,预防纠正措施,使用补偿措施引言故障模式及影响分析(Failure Mode and Effect Analysis,FMEA)是指分析产品所有可能的故障模式及其可能产生的影响,并按每个故障模式产生影响的严重程度予以分类的一种归纳分析方法。
其目的是通过系统地分析,找出潜在的薄弱环节,并提出有针对性的改进措施,以提高产品的可靠性。
它是一种自下而上的(由元器件到产品)的故障因果关系的单因素的、定性的分析方法,该方法为人们提供了一种规范化、标准化、系统化的有效分析工具。
目前,大多数型号研制工作都要求开展FMEA工作,FMEA方法的技术核心其实并不复杂,但在实际开展过程中仍然存在种种问题。
下面分别从管理和技术两方面进行分析。
1FMEA工作存在的问题1.1FMEA工作中存在的管理问题1)FMEA工作缺乏系统性“关键项目”的确定、“约定层次”的划分、严酷度等级的定义、下级产品对上级产品层次的故障影响等工作,需经过设计师系统之间详细沟通和系统策划,而现状是单机、分系统和总体设计之间往往各自为战【1】。
另外,FMEA工作目前通常只在某一研制阶段开展,FMEA作为一个反复迭代的过程,放弃“FMEA与设计同步开展”的原则,在某种意义上讲,就是放弃了在设计阶段及时、全面发现设计薄弱环节并改进设计的机会。
2)FMEA工作没有闭环FMEA工作的目的是找出分析对象的薄弱环节,如“严酷度等级为Ⅰ、Ⅱ类的故障”、“关键项目/关重件”、“单点故障”、“不可检测故障”等,并针对薄弱环节提出设计改进措施、使用补偿措施。
目前FMEA工作大多被简化成了FMEA填表工作,只完成了FMEA报告,没有FMEA分析结果或有结果而未反馈到产品设计中,对促进产品改进设计的作用有限。
FMEA第五版教材的潜在失效模式分析在实际应用中的价值与意义
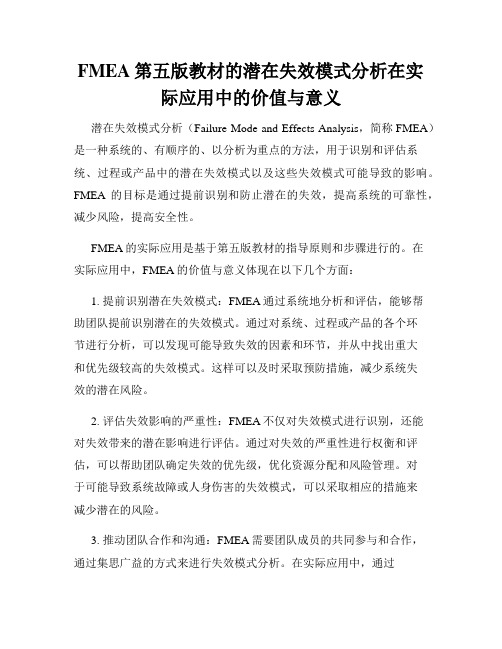
FMEA第五版教材的潜在失效模式分析在实际应用中的价值与意义潜在失效模式分析(Failure Mode and Effects Analysis,简称FMEA)是一种系统的、有顺序的、以分析为重点的方法,用于识别和评估系统、过程或产品中的潜在失效模式以及这些失效模式可能导致的影响。
FMEA的目标是通过提前识别和防止潜在的失效,提高系统的可靠性,减少风险,提高安全性。
FMEA的实际应用是基于第五版教材的指导原则和步骤进行的。
在实际应用中,FMEA的价值与意义体现在以下几个方面:1. 提前识别潜在失效模式:FMEA通过系统地分析和评估,能够帮助团队提前识别潜在的失效模式。
通过对系统、过程或产品的各个环节进行分析,可以发现可能导致失效的因素和环节,并从中找出重大和优先级较高的失效模式。
这样可以及时采取预防措施,减少系统失效的潜在风险。
2. 评估失效影响的严重性:FMEA不仅对失效模式进行识别,还能对失效带来的潜在影响进行评估。
通过对失效的严重性进行权衡和评估,可以帮助团队确定失效的优先级,优化资源分配和风险管理。
对于可能导致系统故障或人身伤害的失效模式,可以采取相应的措施来减少潜在的风险。
3. 推动团队合作和沟通:FMEA需要团队成员的共同参与和合作,通过集思广益的方式来进行失效模式分析。
在实际应用中,通过FMEA可以促进团队成员之间的沟通和交流,激发各个专业领域的专家共同参与,从而获得更全面、准确的失效模式分析结果。
4. 指导改进和优化措施:通过对失效模式进行分析,FMEA可以帮助团队识别系统、过程或产品中的问题点和风险点。
在实际应用中,团队可以根据FMEA的结果制定相应的改进和优化措施,以改善产品的质量和可靠性。
FMEA提供了一种系统化的方法,可以指导团队在改进过程中进行决策和优化,从而提高效率和降低成本。
5. 改善工程设计和开发流程:FMEA对于工程设计和开发流程也具有重要价值。
通过对系统、过程或产品进行分析,可以发现潜在的设计缺陷、工艺瑕疵和系统弱点。
FMEA有哪些相对其它工具存在的明显缺陷?

FMEA有哪些相对其它工具存在的明显缺陷?
FMEA(失效模式及其影响分析)是一种常用的风险评估工具,用于识别和解决潜在的系统故障。
然而,尽管其广泛应用,FMEA 仍然存在一些明显的缺陷。
天行健FMEA培训辅导公司总结如下:
首先,FMEA容易受到主观因素的影响。
由于评估的主要依据是专家经验和判断,不同的专家可能会有不同的意见和评估结果。
这种主观性可能导致评估结果的不一致性,影响最终的决策和风险控制措施的制定。
其次,FMEA在评估过程中可能存在信息不全的问题。
由于数据收集和分析的局限性,FMEA可能无法获取充分和准确的信息,从而无法全面评估潜在的失效模式和其影响。
这可能导致评估结果的不准确性,影响后续的风险管理工作。
此外,FMEA在处理复杂系统时可能存在困难。
对于复杂的系统,涉及的元素和关联关系非常多,FMEA难以完全捕捉和分析所有的潜在失效模式。
这可能导致一些潜在风险被忽略或未能充分评估,增加了系统故障的风险。
末了,FMEA在应对新技术和新产品时可能存在局限性。
由于缺乏相关的经验和数据支持,FMEA在评估新技术和产品的风险时可能缺乏准确性和可靠性。
这可能导致对潜在风险的误判或忽视,增加了新技术和产品引入的风险。
综上所述,FMEA相对其它工具存在着明显缺陷。
主观性影响评估的一致性,信息不全限制了准确性,处理复杂系统的困难增加了遗漏风险的可能性,应对新技术和产品的局限性降低了可靠性。
因此,在使用FMEA时,需要注意这些缺陷,并考虑其他补充手段和方法来增加评估的准确性和全面性。
【最新文档】fmea,优缺点-范文模板 (8页)
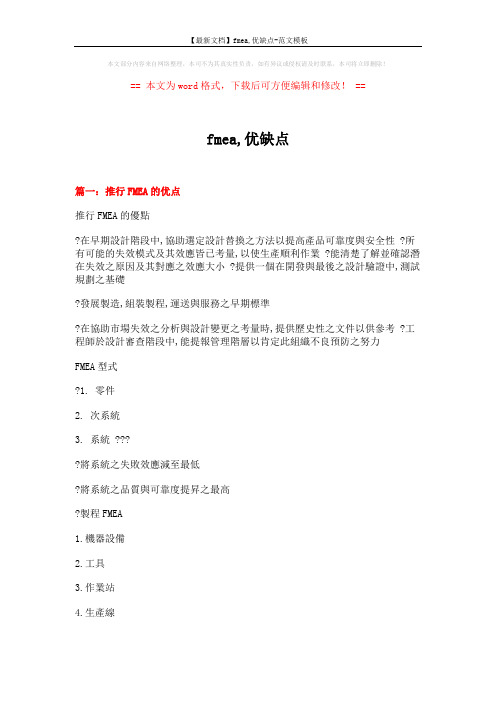
本文部分内容来自网络整理,本司不为其真实性负责,如有异议或侵权请及时联系,本司将立即删除!== 本文为word格式,下载后可方便编辑和修改! ==fmea,优缺点篇一:推行FMEA的优点推行FMEA的優點?在早期設計階段中,協助選定設計替換之方法以提高產品可靠度與安全性 ?所有可能的失效模式及其效應皆已考量,以使生產順利作業 ?能清楚了解並確認潛在失效之原因及其對應之效應大小 ?提供一個在開發與最後之設計驗證中,測試規劃之基礎?發展製造,組裝製程,運送與服務之早期標準?在協助市場失效之分析與設計變更之考量時,提供歷史性之文件以供參考 ?工程師於設計審查階段中,能提報管理階層以肯定此組織不良預防之努力FMEA型式?1. 零件2. 次系統3. 系統 ????將系統之失敗效應減至最低?將系統之品質與可靠度提昇之最高?製程FMEA1.機器設備2.工具3.作業站4.生產線?5.各種流程(製程)?6.量具?7.工作人員訓練?將生產製程對系統之失敗效應減至最低?將系統之品質,可靠度及產能提昇至最高如何組織FEAM小組?設計FMEA小組?設計工程師?測試/開發工程師?可靠度工程師?材料工程師?售後服務工程師?製造/製程工程師?製程/裝配FMEA小組?設計工程師?製造/製程工程師1?品質工程師?可靠度工程師?工具工程師?各站擔當之工作人員註:當協力廠商之品質需被應用與整合時,此外部廠商之工程師與其製程應視為此小組之一部份功能(Function)之定義?針對零件、次系統或產品的工作,必須能:?簡潔(Concise)?正確(Exact)?並使所有使用者容易了解?(Easy to unstand for all users)?典型之範例如:?位置、支撐、附著、拔脫、保留、潤滑等失效(Failure)之定義?在原設計面上,無法於零件/次系統/系統上扮演其功能失效模式(Failure Mode)?在零件/次系統/系統上,在其應有之功能無法使用之情形(功能要求為負面表象者)。
FMEA的应用及分析
FMEA的应用及分析摘要:FMEA属于定量化的分析方法,可对产品加工、质量管理等过程中存在的潜在失效问题进行分析,实现优化过程的目标,在保障性分析、安全性分析以及维修性分析中发挥作用。
本文对FMEA的概念、流程、特点以及作用进行研究,再结合具体的案例,分析应用要点,找出漆包线生产系统中的中拉机设备存在的问题,并确定改造方法,降低加工成本,展现出FMEA的优越性。
关键词:FMEA;失效模式;中拉机FMEA是一种分析工具,其讨论的重点主要是失效情况,可以帮助使用者发现产品在多个环节中可能存在的缺陷,从而预先形成具体可行的改善方案,实现对失效情况的有效预防,这种方法在轻工业中有良好的使用效果。
现探讨FMEA的实际应用情况。
1、FMEA的概念FMEA是失效模式及后果分析的简称,其能够被应用到分析产品可行性的工作中,这一工程技术能够消除、预防、识别与确定产品在设计、系统、服务与应用等多个环节的潜在的或者已知的错误、问题与失效情况[1]。
通过FMEA可掌握产品产生过程中的各种故障模式及其产生机理与构成的影响,并借此消除或者预防故障。
FMEA分析流程:首先需要对系统进行定义,可围绕分析对象的情况,进行可靠性框图的设计,确保分析的全面性,使与其相关的影响、原因以及全部故障模式都得到精准的分析;根据调查收集的材料分析流程与产品特性,主要掌握流程要求;对可能出现的失效模式进行预估,依据包括工程分析数据、终端用户具体使用状况、模拟验证数据、同行业同类别产品产生的故障问题以及故障判定情况;分析失效效应,以产品自身的功能、相关部件以及涉及的法规制度等方面为切入点;分析具体失效风险的严重程度、造成原因以及发生频率,严重程度指产品出现失效情况后造成的主要影响;研究当前使用的失效管理方法,包括正在使用的可行性评审、安全与失效设计与设计评审等方法,展开难检度分析与关键性分析;确定改进措施,确保检测度、发生度与严重度都得到控制;最后对失效模式的严重度、难检度、发生率与改善情况等数据进行汇总。
为什么你的FMEA总做不好,原因就在这儿!
为什么你的FMEA总做不好,原因就在这儿!FMEA(失效模式和影响分析)是目前全球众多优秀企业在设计开发和生产制造领域应用最为广泛的质量风险管控工具,被誉为事前预防的利器。
虽然FMEA方法在企业实施已久,表面上似乎很重视它,但实际上却是另一回事。
要想真正发挥FMEA的作用并非易事,依然有很多需要我们直面的问题……据统计,89.4%的中国企业推动FMEA一直都得不到很好的实施成效!因此,到目前为止,如何有效进行产品设计和制造的失效预防而不是事后“救火”,仍是企业最头痛的问题之一,以下是根据调研、实践整理出的关于FMEA软件做不好的原因,一起来看看吧。
问题1、FMEA活动时间投入不足许多公司并未把FMEA作为真正的风险分析工具,只是把FMEA 做为一份体系要求的文件来做,为了完成文件而做文件。
通常在设计或者过程结束后才开始补文件,经常会以客户开发时间节点太短为由,不愿意花时间来分析风险,一直等到问题发生后才开始补救,反而导致更多的时间和费用的投入。
问题2、缺少真正的员工授权组织内缺少对FMEA专员授权。
多数企业未设FMEA专人专岗,大多数都是兼职。
有些情况较好的企业,有FMEA专员,但他/她不是负责这方面的专家,而是错误地把FMEA文件全部交给FMEA专员来做,设计工程师或者制造工程师甚至不参与风险分析。
问题3、FMEA仅仅是某一个人的工作FMEA工作被分配给某一个人,而不是一个精英团队。
机构内,研发部门、制造部、品管部、质量部、货运物流部等部门很少在设计方案之初坐下来一起谈风险性,缺乏合理的内部沟通交流。
问题4、FMEA文件分散未关联FMEA相关文件很多,但是每个文件的内容都缺乏关联性,而且很多都是重复的,容易造成信息孤岛;同一FMEA中的多个相关文件未打通,如DFMEA和DVP、PFMEA、控制计划等;FMEA文件内容更新不及时,逆向FMEA没有有效实现;缺乏统一的FMEA开发信息协作平台,无法及时沟通横向和纵向信息。
FMEA失效模式和相应后果分析
FMEA失效模式和相应后果分析FMEA(Failure Mode and Effects Analysis)是一种系统性的、分析性的过程,用于识别和评估可靠性和可维修性问题。
它主要用于评估系统或过程中的潜在失效模式及其可能的影响,以便能够采取适当的措施来预防或减轻这些失效的后果。
FMEA可以应用于各种不同领域和行业,例如制造业、医疗保健、航空航天、汽车等。
它被广泛用于提高产品或过程的质量和可靠性,并减少可能导致故障或损害的潜在因素。
FMEA的过程可以分为以下几个步骤:1.识别失效模式:通过分析系统或过程的各个组成部分和步骤,识别可能导致失效的模式。
失效模式可以是组件的异常操作、材料的磨损或老化、不正确的装配等。
2.评估失效后果:对于每个失效模式,评估它可能导致的后果。
后果可以是人员伤亡、生产延误、产品质量下降、环境污染等。
3.评估失效频率:评估每个失效模式发生的频率。
频率可以通过历史数据、实验或专家意见进行估算。
4.评估探测和防范控制措施:评估已经存在的或可行的探测和防范措施,以减少失效的可能性或降低其后果。
这些措施可以包括使用更可靠的材料、改进设计、增加监控和检测设备等。
5.重新评估风险优先级:根据探测和防范措施的效果,重新评估每个失效模式的风险优先级。
优先级较高的失效模式可能需要采取更严格的措施来管理和避免。
FMEA的结果通常以表格的形式呈现,每个失效模式都有一个风险优先级,由失效频率、后果严重性和探测和防范控制措施的效果决定。
这些表格可以用于指导制定改进措施、预测潜在问题并制定应对计划。
FMEA的优点在于它能够通过系统性的分析和评估来识别和控制潜在的问题,减少了产品或过程的故障和损害的风险。
它还可以促进跨功能团队的合作,提高团队成员对系统或过程的理解和意识。
然而,FMEA也有一些局限性。
首先,它的结果是基于已有的信息和数据进行估算的,因此可能存在一定的不确定性。
其次,FMEA的结果仅仅是估算的风险优先级,实际的风险可能会因为未知因素而有所变化。
关于FMEA,你犯过这些错误吗?
关于FMEA,你犯过这些错误吗?关于FMEA,你犯过这些错误吗?FMEA(FailureModeandEffectsAnalysis)是这种可靠性设计的关键方式。
FMEA事实上是FMA(常见故障模式分析)和FEA(常见故障影响剖析)的组成。
通称失效模式与影响分析或潜在失效模式与后果分析。
FMEA做为这种方案策划作为防范措施专用工具,其关键目地是发觉、点评商品/全过程中潜在性的无效以及不良影响;寻找可以防止或降低潜在性无效产生的对策而且不断健全。
可以非常容易、成本低地对商品或全过程开展改动,进而缓解过后改动的危機。
并寻找可以防止或降低这种潜在性无效产生的对策。
有关FMEA,许多公司在执行过程中存有错误观念:1、FMEA活动时间投入不足许多公司仍未把FMEA做为真实的鉴别潜在性无效的专用工具,只是把FMEA做为这份管理体系规定的文档来做,以便进行文档而做文档。
2、FMEA仅仅某一人的工作中FMEA工作中被分配成某一人的工作中,而并不是1个精英团队工作中。
机构内,研发部门、制造部、品管部、质量部和货运物流部等非常少会在设计方案之初坐着来一块儿谈风险性,缺乏合理的內部沟通交流。
3、FMEA工作中走过场大部分公司以便应收商品定形、国防部查验、管理体系审批等必须,把FMEA工作中做为方式工作中其一,仅仅处理有没有难题。
另一个,许多公司沒有可信性专业技术人员。
即便有专业技术人员,也并不是承担方式的权威专家,只是不正确地把FMEA文档所有交到专业技术人员来做,设计方案技术工程师或是生产制造技术工程师不参加潜在性失效分析工作中。
4、把FMEA作为迅速解决困难的方式许多公司把FMEA做为解决困难的专用工具。
当难题产生时,会提出质疑FMEA有木有用。
FMEA对公司而言,是工作经验积淀的全过程。
FMEA在本新项目中较大底限分折风险性,但不可以确保全过程出現新的自变量,FMEA是动态性文档,人们必须真實纪录全部全过程的难题,并将本新项目产生的难题在下一个新项目提早防止。
- 1、下载文档前请自行甄别文档内容的完整性,平台不提供额外的编辑、内容补充、找答案等附加服务。
- 2、"仅部分预览"的文档,不可在线预览部分如存在完整性等问题,可反馈申请退款(可完整预览的文档不适用该条件!)。
- 3、如文档侵犯您的权益,请联系客服反馈,我们会尽快为您处理(人工客服工作时间:9:00-18:30)。
浅析FMEA在实际应用中的局限性
关键词:FMEA
FMEA,质量圈称之为“飞马”,实际意义是故障模式与影响分析,常用于六西格玛分析。
人们常说“FMEA是个好东西”,“FMEA很重要”,但是这里有一位质量人却不这么认为,他认为FMEA 本身具有局限性,以至于在实际应用中,真正做的好的FMEA少之又少。
小编认为这个观点很特别,因此就“拿来主义”与大家分享,当然这只是一家之言,仅供参考。
下面就来听听这位质量人是怎么说的吧。
浅析FMEA在实际应用中的局限性
FMEA局限性之一:格式化
FMEA的本质是一个风险评估的工具,它的标准的格式化为顾客和供应商的沟通提供一个公共的语言平台,但问题也就在这里,格式化意味着亦步亦趋,不可越矩。
FMEA建立的过程是通过一个多方认证的小组,采取头脑风暴的方法,再加上历史的经验数据,小组完成。
头脑风暴意味着创造性,而格式化则会破坏人们自由思考的环境。
在会议讨论中,大家花在“如何填写”的时间上多过“分析问题”。
FMEA局限性之二:结构复杂
FMEA的第二个局限性是结构复杂,复杂的结构容易让人忽略最本源的东西。
FMEA是控制计划的输入,识别产品/过程中的质量风险控制点是非常重要的。
而结构复杂的后果是,FMEA过程中对产品/过程的要求识别不充分,导致很多FMEA案例中该说的没说,不该说的说了一堆,甚至和现场控制不一致。
FMEA局限性之二:格式繁琐覆盖信息
FMEA的第三个局限性是繁琐的格式企图覆盖所有信息,但很多时候因为技术的复杂性而说不清楚,换来的只是审核员或顾客的叫停。
总是所述,无论是格式化、结构复杂还是格式繁琐,其思想只有一个,那就是FMEA对形式强
调太重,导致人们忽略了一些本来本质的、基本的东西。