橡胶制品的配方设计原理介绍
原来橡胶制品配方是这样设计出来的?

原来橡胶制品配方是这样设计出来的?1、配方设计的目的简要说橡胶配方设计的目的是客户给定的橡胶制品的机械物理和化学性能(或制品的使用环境自己设计符合使用要求的物性),设计出橡胶材料助剂配合的最佳比例,最佳配比要满足现实工厂的生产设备、工艺要求,生产出合格的结构尺寸和物化性能橡胶制品。
配方设计顺序:a、根据制品的具体使用环境确定胶料的物化指标和应许波动范围;b、按照性能要求,根据工程师的经验确定出合适的胶料,设计出适合自己设备、模具的生产工艺条件;c、根据胶料的性能和加工工艺要求选择合适的胶料并确定相应的配比(质量份数)。
这种设计方法是先给出制品的物性,后设计所需的原料和生产工艺,所谓的倒逆分子设计方案。
由于胶料的混炼、流动和反应均未达到分子水平,只能是物料配比的估算,需要通过小实验配合,来验证配方设计的合理性(正交设计、仿真分析等不再阐述)。
2、配方设计的原则a、橡胶制品必须要符合相关的环保要求(VOCs),设计要求:产品尺寸结构、外观、气味(VOC)、ROSHREACH、食品级饮水级医疗级、细菌滋生、物理机械性能、化学耐腐蚀性能,产品收缩等等。
b、制品必须遵循:节能高效,经济合理原则,估算出原料成本、加工工艺和性能(使用要求)最佳平衡点;c、在原有的设计上不断优化材料配比(新材料的应用)和加工工艺(性设备和自动化的应用)获得预期的可行性。
3、配方设计的程序和方法a、准备和收集阶段查阅资料、标准文献,了解产品的使用环境和设计条件(温度、介质、动静负荷、温度、气候、老化、臭氧等),按照以往设计配方经验和相似配方,设计出胶料配比、加工工艺、硫化工艺等。
b、配方实验设计实验方法,一般有经验的工程师会根据以往设计经验估算出大概材料配合,实验并验证。
但:优选法、一元变量法、正交设计、回归分析、均匀设计、高等线、计算机辅助设计、仿真分析等的应用,会让我们更快更合理的找到材料设计的黄金配合点。
配方实验分为:基础配方、性能配方和满足生产的生产配方。
橡胶配方设计整理
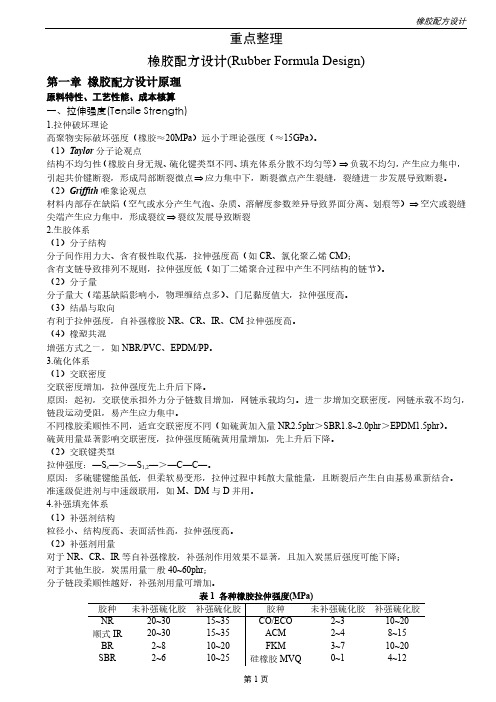
重点整理橡胶配方设计(Rubber Formula Design)第一章橡胶配方设计原理原料特性、工艺性能、成本核算一、拉伸强度(Tensile Strength)1.拉伸破坏理论高聚物实际破坏强度(橡胶≈20MPa)远小于理论强度(≈15GPa)。
(1)Taylor分子论观点结构不均匀性(橡胶自身无规、硫化键类型不同、填充体系分散不均匀等)⇒负载不均匀,产生应力集中,引起共价键断裂,形成局部断裂微点⇒应力集中下,断裂微点产生裂缝,裂缝进一步发展导致断裂。
(2)Griffith唯象论观点材料内部存在缺陷(空气或水分产生气泡、杂质、溶解度参数差异导致界面分离、划痕等)⇒空穴或裂缝尖端产生应力集中,形成裂纹⇒裂纹发展导致断裂2.生胶体系(1)分子结构分子间作用力大、含有极性取代基,拉伸强度高(如CR、氯化聚乙烯CM);含有支链导致排列不规则,拉伸强度低(如丁二烯聚合过程中产生不同结构的链节)。
(2)分子量分子量大(端基缺陷影响小,物理缠结点多)、门尼黏度值大,拉伸强度高。
(3)结晶与取向有利于拉伸强度,自补强橡胶NR、CR、IR、CM拉伸强度高。
(4)橡塑共混增强方式之一,如NBR/PVC、EPDM/PP。
3.硫化体系(1)交联密度交联密度增加,拉伸强度先上升后下降。
原因:起初,交联使承担外力分子链数目增加,网链承载均匀。
进一步增加交联密度,网链承载不均匀,链段运动受阻,易产生应力集中。
不同橡胶柔顺性不同,适宜交联密度不同(如硫黄加入量NR2.5phr>SBR1.8~2.0phr>EPDM1.5phr)。
硫黄用量显著影响交联密度,拉伸强度随硫黄用量增加,先上升后下降。
(2)交联键类型拉伸强度:—S x—>—S1,2—>—C—C—。
原因:多硫键键能虽低,但柔软易变形,拉伸过程中耗散大量能量,且断裂后产生自由基易重新结合。
准速级促进剂与中速级联用,如M、DM与D并用。
4.补强填充体系(1)补强剂结构粒径小、结构度高、表面活性高,拉伸强度高。
橡胶制品的配方设计原理
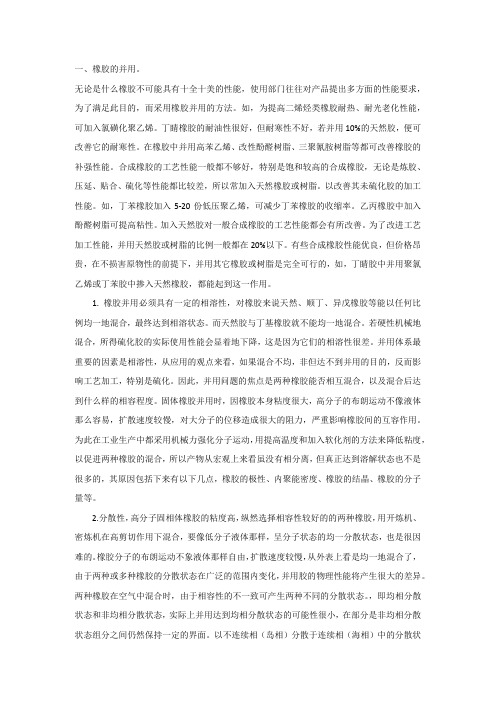
一、橡胶的并用。
无论是什么橡胶不可能具有十全十美的性能,使用部门往往对产品提出多方面的性能要求,为了满足此目的,而采用橡胶并用的方法。
如,为提高二烯烃类橡胶耐热、耐光老化性能,可加入氯磺化聚乙烯。
丁睛橡胶的耐油性很好,但耐寒性不好,若并用10%的天然胶,便可改善它的耐寒性。
在橡胶中并用高苯乙烯、改性酚醛树脂、三聚氰胺树脂等都可改善橡胶的补强性能。
合成橡胶的工艺性能一般都不够好,特别是饱和较高的合成橡胶,无论是炼胶、压延、贴合、硫化等性能都比较差,所以常加入天然橡胶或树脂。
以改善其未硫化胶的加工性能。
如,丁苯橡胶加入5-20份低压聚乙烯,可减少丁苯橡胶的收缩率。
乙丙橡胶中加入酚醛树脂可提高粘性。
加入天然胶对一般合成橡胶的工艺性能都会有所改善。
为了改进工艺加工性能,并用天然胶或树脂的比例一般都在20%以下。
有些合成橡胶性能优良,但价格昂贵,在不损害原物性的前提下,并用其它橡胶或树脂是完全可行的,如,丁睛胶中并用聚氯乙烯或丁苯胶中掺入天然橡胶,都能起到这一作用。
1. 橡胶并用必须具有一定的相溶性,对橡胶来说天然、顺丁、异戊橡胶等能以任何比例均一地混合,最终达到相溶状态。
而天然胶与丁基橡胶就不能均一地混合。
若硬性机械地混合,所得硫化胶的实际使用性能会显着地下降,这是因为它们的相溶性很差。
并用体系最重要的因素是相溶性,从应用的观点来看,如果混合不均,非但达不到并用的目的,反而影响工艺加工,特别是硫化。
因此,并用问题的焦点是两种橡胶能否相互混合,以及混合后达到什么样的相容程度。
固体橡胶并用时,因橡胶本身粘度很大,高分子的布朗运动不像液体那么容易,扩散速度较慢,对大分子的位移造成很大的阻力,严重影响橡胶间的互容作用。
为此在工业生产中都采用机械力强化分子运动,用提高温度和加入软化剂的方法来降低粘度,以促进两种橡胶的混合,所以产物从宏观上来看虽没有相分离,但真正达到溶解状态也不是很多的,其原因包括下来有以下几点,橡胶的极性、内聚能密度、橡胶的结晶、橡胶的分子量等。
橡胶制品是如何生产制作的?配方、工艺、设备基础介绍

橡胶制品是如何生产制作的?配方、工艺、设备基础介绍一、概论1.橡胶分子链几何形状大致分为三类:线型橡胶分子,支链型橡胶分子,网状橡胶分子。
2.胶料的组成可概括为五个体系,即生胶,硫化体系,增塑及软化体系,补强与填充体系,仿护体系。
3.橡胶制品生产的基本工艺过程包括塑炼、混炼、压延、压出、成型、硫化六个基本工序。
★橡胶的流动性是整个加工过程中最重要的工艺特性。
★分子量较高且分布窄的橡胶,物理机械性能较好,但加工性较差。
★生胶分子量越低,生胶的可塑度越大.★生胶分子量分布越宽,在开炼机上混炼时包辊性越好。
二、橡胶配方设计(一)、生胶1.SBR是丁苯橡胶,BR是顺丁橡胶,EPDM是三元乙丙橡胶,CR是氯丁橡胶。
★合成丁苯橡胶的单体是丁二烯和苯乙烯,合成乙丙橡胶的单体是乙烯和丙烯丁腈橡胶和氟橡胶----------耐油性最好丁基橡胶----------------------气密性最好氟橡胶----------最佳耐热耐化学药品性三元乙丙橡胶---------------耐候性最好丁腈橡胶的耐油性、耐热性及机械强度随丙烯腈含量的增加而提高,而弹性和耐寒性却有所下降。
三元乙丙橡胶大分子主链不含双键,双键在侧链上。
主链为稳定的碳碳饱和键,受到老化因素的影响时,主链不易短链,因此三元乙丙橡胶具有优良的耐老化性能。
二元乙丙橡胶主链和侧链都不含双键,用过氧化物硫化后,形成稳定的碳碳饱和键,因此二元乙丙橡胶的耐老化性能比三元乙丙橡胶还好。
(二)、配合剂补强与填充剂1.炭黑的混炼性主要取决于炭黑的结构,粒径和表面化学性质。
★炭黑粒径减小,硫化胶硬度升高。
★炭黑结构越高,炭黑在胶料中的分散越容易。
增塑剂2.增塑剂应与橡胶具有良好的相溶性。
3.促进剂M可作天然胶的化学增塑剂(塑解剂)。
硫化与促进剂、活性剂4.在橡胶硫化中,凡能加快橡胶与硫化剂的交联作用,使硫化时间缩短的物质,都叫硫化促进剂。
5.按促进剂的活性可将其分为以下四类超促进剂,中超促进剂,中等促进剂,弱促进剂。
橡胶配方设计原理及工艺
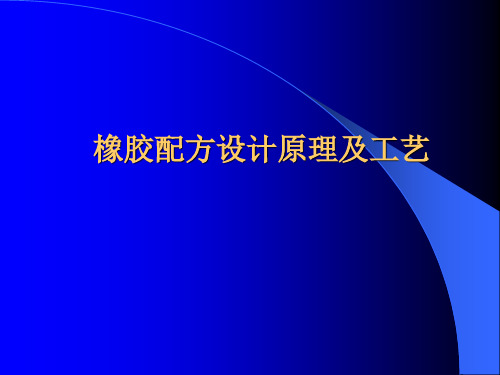
3制定基本配方和性能试验项目 制定基本配方步骤如下: 1确定生胶的品种和用量; 根据主要性能指标确定主体胶料品种;用量与含胶率有关。 2)确定硫化体系。根据生胶的类型和品种,硫化工艺及产品性能要求来确定。 3)确定补强剂品种和用量。根据胶料性能 比重及成本确定。 4)确定软化剂品种和用量。根据生胶及填料种类,胶料性能及加工条件确定。 5)确定防老剂品种和用量。根据产品使用环境的条件来确定。 6)确定其它专用配合剂的品种和用量。如着色剂,发泡剂等)
20˚C
75˚C
150˚C
偏差加大:包容胶活动性增强所致;
Ef/Eg
胶种
纯胶基本硬度
填料品种
估算硬度
NBR
44
FEF,HAF
+1/2份数
CR
44
ISAF
+1/2份数+2
NR
40
SAF
+1/2份数+4
SBR
40
SRF
+1/3份数
IIR
35
陶土
+1/4份数
碳酸钙
+1/7份数
油
-1/2份数
填料与硬度的关系
一 配方设计定义 橡胶材料是生胶与多种配合剂构成的多相体系; 橡胶制品的性能取决于橡胶分子本身;以及各种配合剂性质及它们之间的相互作用关系。 定义:根据产品的性能要求及工艺条件,合理选用原材料,制订各种原材料的用量配比关系的设计方法。 配方设计决定着产品质量、成本和加工性能。
橡胶配方设计原理

软质橡胶的炭黑用量在40~60质量份时,硫化胶的拉伸性能较好。
2020/1/6
橡胶配方设计原理
(四)拉伸强度与软化体系的关系 一般来说,加入软化剂会降低硫化橡胶的拉伸强度。但 软化剂的用量如果不超过5质量份时,硫化胶的拉伸强度 还可能增大,因为胶料中含有少量软化剂时,可改善炭 黑的分散性。例如填充炭黑的丁腈橡胶胶料中,加入10 质量份以下的邻苯二甲酸二丁酯(DBP)或邻苯二甲酸二辛 酯(DOP)时,可使拉伸强度提高;拉伸强度达到最大值之 后,如继续增加软化剂用量,则拉伸强度急剧下降。
2020/1/6
橡胶配方设计原理
二、撕裂强度
橡胶的撕裂是由于材料中的裂纹或裂口受力时迅速扩大
开裂而导致破坏的现象,这是衡量橡胶制品抵抗破坏能
力的特性指标之一。
(一)撕裂强度与橡胶分子结构的关系
橡胶类型 纯胶胶料
炭黑胶料
20℃ 50℃ 70℃ 100℃ 25℃ 30℃ 70℃ 100℃
NR
51
57
56
43
115 90
76 61
CR(GN型) 44
18
8
4
77
75
48 30
IIR
22
4
4
2
70
67
67 59
SBR
5
6
5
4
39
43
47 27
2020/1/6
橡胶配方设计原理
(二)撕裂强度与硫化体系的关系 撕裂强度随交联密度增大而增大,但达到最大值后,交联密度再增 加,则撕裂强度随密度比拉伸强度达到最佳值的交联密度要低。 多硫键具有较高的撕裂强度,故在选用硫化体系时,要尽量使用传 统的硫黄—促进剂硫化体系。硫黄用量以2.0~3.0质量份为宜,促进剂 选用中等活性、平坦性较好的品种,如DM、CZ等。 (三)撕裂强度与填充体系的关系 随炭黑粒径减小,撕裂强度增加。在粒径相同的情况下,能赋予高 伸长率的炭黑,也即结构度较低的炭黑对撕裂强度的提高有利。 使用各向同性的补强填充剂,如炭黑、白炭黑、白艳华、立德粉和 氧化锌等,可获得较高的撕裂强度;而使用各向异性的填料,如陶土、 碳酸镁等则不能得到高撕裂强度。
橡胶配方设计基础资料
实际用量表示。
表1-1 橡胶配方的表示形式
原材料名称, 基本配方, 质量分数 体积分数 生产配
(g/cm3)
质量份 配方/% 配方/% 方,kg
NR 0.92
100 62.20① 76.70② 50.0③
1.4 橡胶配方设计方法
橡胶配方设计主要依赖于人们在生产当中积累的 经验规律,通过大量而繁复的试验来优化配方,造 成大量人力、物力的浪费。
随着科学技术在各个领域的进步和发展,尤其是 计算机技术的迅速发展,橡胶行业已经开始采用计 算机进行配方设计。
1.单因素设计方法
因素:需要考察的影响试验胶料性能指标的因素, 如橡胶配方组分中的硫化剂、补强剂、防老剂等; 水平:每个试验因素可能取值的状态
确定性能 试验项目
➢加工性能 ➢ 物机性能 ➢ 使用性能
➢其他性能:视产品而定
(4)进行试验并选取最佳配方(试验室进行)
塑炼 混炼 制成硫化胶试样 性能测试 数据整理 对比,取舍 初选最佳配方
(5)复试并扩大中试(车间中进行)
试验配方 复试3-5次
车间规模 试验
检验胶料的工艺性能、 硫化胶的物机性能 和成品的机床性能
单因素配方试验设计主要就是研究某单一试验因 素,如促进剂、炭黑、防老剂或某一新型原材料, 在某一变量区间内,确定哪一个值的性能最优。
这样的设计方法主要包括:黄金分割法(0.618 法)、平分法(对分法)、分批试验法、抛物线法、 爬山法。
2020/9/25
黄金分割法
黄金分割点在线段L的0.618处,故此法又称0.618 法。
(3)原材料价廉易得; (4)重点设计主要性能
原来橡胶胶管配方设计是这样的
原来橡胶胶管配方设计是这样的橡胶胶管是一种用于输送各种介质的管道,广泛应用于汽车、机械、农业等领域。
胶管的耐压、耐腐蚀、耐磨、耐高温等性能取决于其配方设计。
下面将详细介绍橡胶胶管的配方设计原理。
橡胶胶管的主要原料是橡胶、添加剂和填充剂。
其中,橡胶起到了增加弹性和抗拉强度的作用,添加剂用于改善橡胶的加工性能和耐用性,填充剂用于改善橡胶的物理性能。
首先,选择合适的橡胶作为胶管的主要原料。
常用的橡胶包括天然橡胶(NR)和合成橡胶(SBR、EPDM等)。
天然橡胶具有良好的弹性和耐磨性,而合成橡胶则具有耐油、耐腐蚀等特性。
根据不同的应用场景选择不同的橡胶。
其次,根据胶管的使用环境和要求,添加适量的添加剂。
添加剂是提高橡胶性能的关键。
主要包括硫化剂、活化剂、稳定剂、活性剂等。
硫化剂用于加强橡胶的硫化性能,提高其耐温、耐老化性能;活化剂用于提高橡胶的加工性能,提高其流动性和可塑性;稳定剂用于延长橡胶的寿命,防止其过早老化;活性剂用于降低橡胶的粘度,提高其可加工性。
最后,添加填充剂以改善橡胶的物理性能。
填充剂主要包括碳黑、沙子等。
碳黑可提高橡胶的强度、耐磨性和耐候性,同时也可以降低其成本。
沙子主要用于增加橡胶的硬度和耐磨性。
配方设计时,需要根据实际需求进行调整。
如对于汽车制动胶管,需要优先考虑其耐压和耐高温性能;而对于输送饮用水的胶管,则需要考虑其耐腐蚀和无毒的特性。
另外,不同的橡胶胶管制造工艺也会对配方设计产生影响。
例如,对于拉伸成型的胶管,需要添加抗拉伸剂,以增强其拉伸性能;而对于挤出成型的胶管,需要添加抗挤出剂,以增强其挤压性能。
总之,橡胶胶管的配方设计是一个综合考虑物理性能、加工性能和耐用性的过程。
合理的配方设计可以提高胶管的使用寿命和性能,满足不同工况的需求。
随着技术的不断发展,对橡胶胶管配方设计的研究也在不断深入,使得橡胶胶管在各个领域的应用得到了进一步的拓展。
橡胶配方设计 概述
橡胶配方设计概述橡胶的硫化(交联)交联是橡胶高弹性的基础,其特点是在一个橡胶分子链上仅形成少数几处交联点,因此不会影响橡胶分子链段的运动。
橡胶的硫化体系较多,常见的有:硫黄硫化体系、过氧化物硫化体系、树脂硫化体系、氧化物硫化体系等。
硫黄硫化体系主要适应于二烯类橡胶,其硫化活性点是在双键旁边的α氢原子。
组成:硫黄活性剂:氧化锌,硬脂酸促进剂:噻唑类(DM,M),次磺酰胺类(CZ,NOBS),秋兰姆类(TETD,TMTM,TMTD),胍(D)表1硫黄硫化体系分类过氧化物硫化体系-自由基机理1常见的过氧化物有:DCP (二枯基过氧化物)、BPO 、DCBP 、双2,52助交联剂:抑制聚合难自由基无用的副反应。
如TAIC ,TAC ,HVA-2过氧化物硫化橡胶性能特点:老化性能好,压缩永久变形小,制品透明性好。
表2过氧化物的交联效率这是含卤素橡胶的主要硫化剂。
通常有氧化锌/氧化镁(5/4)、氧化铅或四氧化三铅(10-20,耐水制品)橡胶的填料未加填料的橡胶,力学性能和工艺性能均较差,无法使用。
作用·补强性:拉伸强度,撕裂强度,耐磨性·加工性能·降低成本填料的结构粒径一般来说,粒径越小,强度越高。
表3常用补强剂及填充剂的粒径范围(mμ)粒子形状及内部结构(吸油值法,DBP)。
一般吸油值越大,结构性越强,改善性能越明显。
比表面积粒子形状(BET法,CATB法)。
比表面积越大,强度越高。
化学结构反应性(PH值表示)。
如炭黑表面的羧基、白炭黑和普通浅色填料表面的羟基等,酸性填料常影响橡胶的硫化,因此需加入活性剂,消除酸性。
填料的处理方法填料表面一般为亲水性的,而聚合物是憎水的,两者相容性较差,必须进行表面处理。
表面活性剂(1)结构:有机化合物,具有不对称的分子结构,由亲水和疏水两部分基团组成。
(2)亲水部分:-OH,-COOH,-NH2,-NO2,-SH(3)疏水部分:长链式、苯环式或烃类偶联剂(1)分类:硅烷,钛酸酯、铝酸酯、高分子偶联剂等(2)结构特点:亲水部分与表面活性剂相似,但疏水部分能与聚合物形成化学结合或物理缠结。
橡胶制品配方设计原理
橡胶制品配方设计原理
②交联健的类型 硫化胶的拉伸强度随着交联键能的增加而减小。当交联键能较弱 时,在高应力集中下会很快断裂,从而解除了所承受的负荷,而将应 力转移分配给相邻链段上,使得网络作为一个整体均匀地承受较大应 力;同时,弱交联键的较早断裂还有利于该部分主链的定向排列和结 晶,因此存在弱交联键的硫化胶的拉伸强度较大。例如,适当增加硫 黄用量,采用促进剂M或与胍类促进剂并用,可提高键能较低的多硫键 (—Sx—)的含量,提高拉伸强度。 ⑶ 填充体系 一般而言,填充剂粒径越小、比表面积越大、结构性越高,补强 效果越好。
高分子科学与工程学院
橡胶制品配方设计原理
1.2 配合体系与制品性能的关系 1.2.1 配合体系与拉伸强度的关系 拉伸强度是指试片受拉伸作用至断裂时单位面积上所承受的最 大拉伸应力,单位MPa。在硫化胶的测定项目中一般都包括这项指 标。工业用橡胶制品,多以拉伸强度作为产品质量的主要指标。 ⑴ 橡胶品种 主链上有极性取代基或芳基的橡胶的拉伸强度较高。就纯橡胶 配合而言,天然橡胶和聚氨酯橡胶的拉伸强度最高,丁基橡胶、乙 丙橡胶、氯丁橡胶次之,丁苯橡胶、丁腈橡胶较差。 ⑵ 硫化体系 ①交联密度 随着交联密度的增加,橡胶拉伸强度,出现先增后降的趋势, 存在最佳值,这就要求适当选择硫化剂的用量。
高分子科学与工程学院
橡胶制品配方设计原理
1.3.4 配合体系对焦烧特性的影响 焦烧产生的原因主要是硫化体系选择不当导致。因此,应尽量 选用后效性或临界温度较高的促进剂,也可添加防焦剂进一步改 善。碱性炉法炭黑及高结构性炭黑具有促进硫化作用,易引起焦 烧;而酸性的槽法炭黑,对硫化起延缓作用,一般不易焦烧。 增塑剂的加入一般都具有延缓焦烧的作用。
高分子科学与工程学院
- 1、下载文档前请自行甄别文档内容的完整性,平台不提供额外的编辑、内容补充、找答案等附加服务。
- 2、"仅部分预览"的文档,不可在线预览部分如存在完整性等问题,可反馈申请退款(可完整预览的文档不适用该条件!)。
- 3、如文档侵犯您的权益,请联系客服反馈,我们会尽快为您处理(人工客服工作时间:9:00-18:30)。
橡胶制品的配方设计原理一、橡胶的并用。
无论是什么橡胶不可能具有十全十美的性能,使用部门往往对产品提出多方面的性能要求,为了满足此目的,而采用橡胶并用的方法。
如,为提高二烯烃类橡胶耐热、耐光老化性能,可加入氯磺化聚乙烯。
丁睛橡胶的耐粙性很好,但耐寒性不好,若并用10%的天然胶,便可改善它的耐寒性。
在橡胶中并用高苯乙烯、改性酚醛树脂、三聚氰胺树脂等都可改善橡胶的补强性能。
合成橡胶的工艺性能一般都不够好,特别是饱和较高的合成橡胶,无论是炼胶、压延、贴合、硫化等性能都比较差,所以常加入天然橡胶或树脂。
以改善其未硫化胶的加工性能。
如,丁苯橡胶加入5-20份低压聚乙烯,可减少丁苯橡胶的收缩率。
乙丙橡胶中加入酚醛树脂可提高粘性。
加入天然胶对一般合成橡胶的工艺性能都会有所改善。
为了改进工艺加工性能,并用天然胶或树脂的比例一般都在20%以下。
有些合成橡胶性能优良,但价格昂贵,在不损害原物性的前提下,并用其它橡胶或树脂是完全可行的,如,丁睛胶中并用聚氯乙烯或丁苯胶中掺入天然橡胶,都能起到这一作用。
1. 橡胶并用必须具有一定的相溶性,对橡胶来说天然、顺丁、异戊橡胶等能以任何比例均一地混合,最终达到相溶状态。
而天然胶与丁基橡胶就不能均一地混合。
若硬性机械地混合,所得硫化胶的实际使用性能会显着地下降,这是因为它们的相溶性很差。
并用体系最重要的因素是相溶性,从应用的观点来看,如果混合不均,非但达不到并用的目的,反而影响工艺加工,特别是硫化。
因此,并用问题的焦点是两种橡胶能否相互混合,以及混合后达到什么样的相容程度。
固体橡胶并用时,因橡胶本身粘度很大,高分子的布朗运动不像液体那么容易,扩散速度较慢,对大分子的位移造成很大的阻力,严重影响橡胶间的互容作用。
为此在工业生产中都采用机械力强化分子运动,用提高温度和加入软化剂的方法来降低粘度,以促进两种橡胶的混合,所以产物从宏观上来看虽没有相分离,但真正达到溶解状态也不是很多的,其原因包括下来有以下几点,橡胶的极性、内聚能密度、橡胶的结晶、橡胶的分子量等。
橡胶网为广大从事橡胶行业的朋友提供交流学习交易的平台。
2.分散性,高分子固相体橡胶的粘度高,纵然选择相容性较好的的两种橡胶,用开练机、密练机在高剪切作用下混合,要像低分子液体那样,呈分子状态的均一分散状态,也是很因难的。
橡胶分子的布朗运动不象液体那样自由,扩散速度较慢,从外表上看是均一地混合了,由于两种或多种橡胶的分散状态在广泛的范围内变化,并用胶的物理性能将产生很大的差异。
两种橡胶在空气中混合时,由于相容性的不一致可产生两种不同的分散状态。
,即均相分散状态和非均相分散状态,实际上并用达到均相分散状态的可能性很小,在部分是非均相分散状态组分之间仍然保持一定的界面。
以不连续相(岛相)分散于连续相(海相)中的分散状态。
非均相分散状态分为以下三级A,宏观非均相级,区域尺寸为10-100微,B,微观非均相为0.1-2微C,半均相级成接枝或嵌段两种共聚体。
一种并用体的分散状态不可能单一纯地存在着一个状态,而是以几种状态并存的局面,只不过某一级为主而已。
3.共硫化,除了相容性和分散性外,橡胶并用的另一个重要因素是共硫化性。
它是指并用橡胶的硫化体系选择和硫化速度的调整问题。
对相同硫化速度而言,通用橡胶以天然胶为最快,其次是异戊橡胶,顺丁橡胶、乳聚顺丁、丁苯胶。
硫化速度较慢的橡胶可采用减少硫黄,增加促进剂的方法,以与天然橡胶的硫化速度互相配合。
一般对同一硫化速度的橡胶,天然橡胶为高硫黄低促进剂、丁苯橡胶为低硫黄高促进剂,顺丁胶处于两者之间。
橡胶硫化速度的差异与其分子结构的关系很大。
不同硫化体系橡胶,如天然胶与氯丁胶或丁基橡胶并用。
虽可以提高并用体系的加工性能,但因缺泛共硫化性能所得的硫化胶性能比平均值还低,不能获得满意的性能。
把丁基橡胶卤化后或提高不饱和度,可改善与天然胶的共硫化。
选用适宜的共硫化剂,如天然胶与氯丁胶的共硫化剂可为醛类物质,并用性能差不多呈直线变化。
从实际生产看,并用橡胶的共硫化性与分散性是不可分割的。
橡胶之间分散越均匀,硫化的物理性能越好,但并用橡胶多为非均相分散状态,由于两相间硫化程度的差异以及界面之间的不同橡胶能否交联、接枝等因素,对硫化胶的物性有决定性的影响,造成并用橡胶两相间硫化程度不均的原因是1.硫化胶的溶解度,在温室条件下,按通常配方所加入的硫化剂数量为过保和或近似于保和状态,在硫化温度范围内就变成不保和状态,并用两相间的溶解度之差,造成两相间硫化剂分配不均一,也存在浓度差,从而导致并用橡胶两相间的硫化程度非均性2.硫化剂的扩散性,由于橡胶的溶解度不同,在并用体系的两相间,硫化剂会引起扩散引起迁移,在一定温度下,通常向硫化剂溶解度高的橡胶相迁移,当达到分配系数后,为平衡状态。
硫化剂等配合剂的扩散速度非常迅速,同一种橡胶中的浓度差异在短时间内就可消除。
总之并用橡胶物性的好坏与其硫化系统有密切的关系,选择两种橡胶并用时,要考滤到两者所采用的硫化体系是否一致,有没共硫化作用,对同一硫化体系而言,还存在着硫化剂的溶解度和扩散的差异,硫化时由于硫化剂偏向于扩散浓度大的橡胶,导致硫化速度快,结果造成过硫或欠硫的两种橡胶并存,从而异相间形成不均一硫化,并用橡胶物性下降,如三元乙丙与丁苯胶并用效果就不够好。
为了提高二烯烃类橡胶的抗臭氧性能,并用相容性差的EPDM时,将EPDM的各种硫化促进剂做接枝处理,可大大改善对NR的混合性,用加成硫黄法亦可改进EPDM/NR并用体系的耐疲劳、耐曲绕性。
此外,并用体系中加入第三组份,或提高不保和度,如IIR的异戊二烯烃从1.8%提高到18%,可提高二烯烃类橡胶的并用性能。
还有使丙烯酸酯橡胶主链引入不保和基团,使之能用硫黄共硫化。
羟甲基化树脂和丁睛橡胶并用可制得高抗张强度、高硬度产物。
4.并用橡胶中的化学反应。
天然橡胶与顺丁橡胶并用有交联反应,而天然胶与丁睛胶则无交联反应。
聚胺脂橡胶与丁睛胶并用体系也有交联反应。
总之并用橡胶必须充分考滤以上四点二、配方设计与胶料工艺性能的关系。
所谓加工性能好的配方是配方与制造方法和加工设备相适应的配方。
1.可塑性,可塑性除了塑练工艺外,还可以通过调整软化剂的用量来得到。
软化剂对可塑性影响顺序为;油酸>松焦油>硬脂酸>松香>沥青>植物油>矿物油。
填充剂降低可塑性,影响大小按下列顺序;槽法碳黑>乙炔炭黑>陶土>氧化镁>碳酸镁>炉法炭黑>硫酸钡>立德粉>氧化锌>碳酸钙>热裂法碳黑。
同一种胶种因使用设备、工艺方法、工艺条件不同具有的可塑性也有差异,不能一概而论。
在密练机中高速混练时,丁苯橡胶与氯丁橡胶在高温中最易生成凝胶,粘度反而上升,使填充剂分散不良导致硫化胶物性不理想,这也是造成复合制品粘着不好的原因。
配方中加入防老剂、及亚硝基-2-萘酚有防止丁苯胶凝胶作用,加入五氯硫酚或DM可防止硫黄调节型氯丁胶凝胶。
使用两种橡胶并用时粘度高的必须先塑练,因为两种橡胶粘度两差太远,易引起聚合物分散不良。
聚氯乙烯或聚乙烯与热塑性塑料并用时,在加入填充前必须比塑料熔点稍高点温度下使两者混合均匀。
2.混练特性,填充剂混入速度快而分散不良的情况很多,一般来说,粒子近于球形、假比重的填充剂混入速度快,炭黑的结构低的有利于混入。
压出收缩与结构有关,结构愈高收缩愈小。
比表面积大不利于混入。
加入填充之前加入油类软化剂可使胶料粘度下降,加快填充剂的混入速度,但会带来分散不良。
因此原则上是后加油。
高填充配方在混练时,可分批加入填充及油料。
从配方设计角度方面考滤,可选用分散良好的填充剂。
分散良好的填充剂应具备以下条件,A,补强性较小B相同配方中粒经较大C,含水份较少D,假比重较大E,具有异向性能F,碳黑结构度较高等。
操作油中芳烃含量高亦能促进分散。
促进剂一般易分散,但必须注意硫黄的分散。
3.包辊性。
强度高、粘性好、具有收缩性的生胶包辊性好,天然胶的粘性,强度高所以包辊性好,合成橡胶中除了氯丁橡胶外一般强度都很低,所以在配合上要多想办法,选择增加混练胶强度的填充剂,补强性高的炭黑、白炭黑、硬质陶土、碳酸镁、白艳华等。
而氧化锌、硫酸镁、钛白等填充剂的混练强度降低。
此外,易脱辊的还有陶土类、滑石粉、白艳化等。
相反硬质陶土、碳酸钙、白艳华等易粘辊,含芳烃高和操作油粘度高的,如,松焦油、树脂、古马隆树脂、烷基酚醛树脂等可以提高粘性着性。
4.焦烧,当前生产中应用的槽法炭黑粒径小,生热大,但PH值低,一般不易焦烧,反之炉法炭黑则有促进硫化作用,容易焦烧,所以在碳黑用量多的配方中软化剂用量要增加,这除了帮助分散作用外,还可以减少胶料的生热对防止早期硫化是有效的。
在配方中采用迟效性促进剂或临界活化温度高的促进剂,如DM或DM与D并用等。
也可适量地配入防焦剂。
5.喷霜,若喷出的是硫黄再次硫化可以消除,不是硫黄可以用稀盐酸暂时擦去。
为了防止喷霜,应选用颗粒小的硫黄,且用量要适当,应严格控制正硫化,并加强对游离硫的控制。
其它配合剂如石腊、防老剂等在橡胶中都有一定的溶解度,当外界条件变化形成过保和,就可能喷出表面,防老剂选用分子量低的物质,则易喷出,易挥发,反之选用分子量高的则不易从胶料中迁到表面,因而起不到防止制品易老化的作用。
防老剂用量在1.5份,多了也有喷出的可能。
橡胶网为广大从事橡胶行业的朋友提供交流学习交易的平台。
6.压延压出性,压延是由压延机辊筒施力作用于热练胶而使之压成一定形状,压延效果的好坏决定于胶料的压延能力或压延后的收缩率。
胶料的压延能力是指压延时胶料的塑性变型能力。
它受到胶料的可塑性和应力松驰能力的影响。
经压延后,胶料在压延方向上长度缩短,宽度变窄及厚度增加的现象叫收缩,其长度变化的比率叫收缩率。
我们希望胶料在压延后保持压延形状的能力,即希望胶料的塑性大,应力松驰能力大。
影响压延过程的主要因素有两个方面,一是胶料方面,这是决定胶料流变形为的内在因素,二是工艺条件,如辊温、辊速等。
这是决定胶料流变形为的外在因素。
胶料配方设计时主要考滤以下几点。
A.生胶的选型,各种生胶分子结构特征不同,蠕变特性亦不一样,丁苯胶分子结构的特征是侧基比较笨重,分子比较僵硬,柔顺性差,因而变形总是比较慢,在压延辊筒上停留的时间内不能很好地达到平衡,而保持较大的弹性复原性,当离开辊筒后就改变了自已的形状,所以丁苯橡胶较之天然橡胶具有较大的收缩率。
天然橡胶的分子柔顺性大应力松驰得快,在压延机辊筒上能产生较大的塑性变形,保持压延形状能力最大。
一般来说,所有合成橡胶的压延能力比天然胶小,天然橡胶压延后的收缩率最小。
B,胶料的含胶率,胶料配方中同类生胶含胶率不同时对压延的影响亦不同,含胶率高,胶料的弹性大,收缩率就较大。