连杆自动化精密锻造生产线
锻造生产线方案
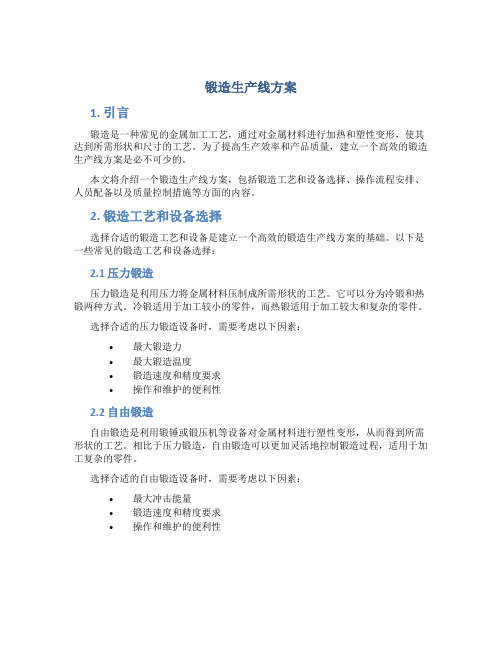
锻造生产线方案1. 引言锻造是一种常见的金属加工工艺,通过对金属材料进行加热和塑性变形,使其达到所需形状和尺寸的工艺。
为了提高生产效率和产品质量,建立一个高效的锻造生产线方案是必不可少的。
本文将介绍一个锻造生产线方案,包括锻造工艺和设备选择、操作流程安排、人员配备以及质量控制措施等方面的内容。
2. 锻造工艺和设备选择选择合适的锻造工艺和设备是建立一个高效的锻造生产线方案的基础。
以下是一些常见的锻造工艺和设备选择:2.1 压力锻造压力锻造是利用压力将金属材料压制成所需形状的工艺。
它可以分为冷锻和热锻两种方式。
冷锻适用于加工较小的零件,而热锻适用于加工较大和复杂的零件。
选择合适的压力锻造设备时,需要考虑以下因素:•最大锻造力•最大锻造温度•锻造速度和精度要求•操作和维护的便利性2.2 自由锻造自由锻造是利用锻锤或锻压机等设备对金属材料进行塑性变形,从而得到所需形状的工艺。
相比于压力锻造,自由锻造可以更加灵活地控制锻造过程,适用于加工复杂的零件。
选择合适的自由锻造设备时,需要考虑以下因素:•最大冲击能量•锻造速度和精度要求•操作和维护的便利性2.3 选材和加热设备选择适合的材料对于锻造过程至关重要。
常见的锻造材料包括碳钢、合金钢、不锈钢和铝合金等。
在选择锻造材料时,需要考虑材料的机械性能、加工性能和成本等因素。
加热设备对于锻造过程中的材料加热至适宜温度也非常重要。
常见的加热设备包括电阻炉、感应加热设备和气体加热设备等。
选择合适的加热设备时,需要考虑加热效率、温度控制精度和经济性等因素。
3. 操作流程安排建立一个高效的锻造生产线方案需要合理安排操作流程,以最大程度地提高生产效率和产品质量。
以下是一个典型的锻造生产线操作流程安排:1.材料准备:选择适当的锻造材料,并进行材料的切割或锯割。
2.加热:将材料加热至适宜的锻造温度。
根据材料类型和尺寸选择合适的加热设备。
3.锻造:根据产品要求选择合适的锻造工艺和设备进行锻造操作。
连杆机械加工工艺分析及精铣连杆上端面夹具设计

机械制造工艺及设备毕业设计是我们完成本专业教学计划的最后一个极为重要的实践性教学环节,是使我们综合运用所学过的基本课程,基本知识与基本技能去解决专业范围内的工程技术问题而进行的一次基本训练。
我们在完成毕业设计的同时,也培养了我们正确使用技术资料,国家标准,有关手册,图册等工具书,进行设计计算,数据处理,编写技术文件等方面的工作能力,也为我们以后的工作打下坚实的基础,所以我们要认真对待这次综合能力运用的机会!本次我的毕业设计题目是:连杆机械加工工艺分析及精铣连杆上端面夹具设计。
连杆是柴油机的主要传动件之一,本文主要论述了连杆的加工工艺及其夹具设计。
连杆的尺寸精度、形状精度以及位置精度的要求都很高,而连杆的刚性比较差,容易产生变形,因此在安排工艺过程时,就需要把各主要表面的粗精加工工序分开。
逐步减少加工余量、切削力及内应力的作用,并修正加工后的变形,就能最后达到零件的技术要求。
关键词:连杆变形加工工艺夹具设计摘要 (I)1.绪论 (1)1.1选题的目的和意义 (1)1.2国内现状 (2)1.3国外现状 (2)1.4课题研究的内容 (3)2.机械加工工艺规程设计 (4)2.1零件的分析 (4)2.1.1连杆零件图分析 (4)2.1.2零件的工艺分析 (4)2.2毛坯的选择 (5)2.2.1选择毛坯时应考虑的因素 (5)2.2.2选择毛坯 (5)2.2.3确定毛坯的制造流程,确定毛坯的形状 (6)2.2.4确定毛坯的尺寸公差和机械加工余量 (7)2.2.5绘制锻件毛坯简图 (8)2.3机械加工工艺规程的制定 (8)2.3.1定位基准的选择 (8)2.3.2零件表面加工方法的选择 (10)2.3.3加工顺序的安排原则 (10)2.3.4加工阶段的划分 (11)2.3.5工序顺序的安排 (11)2.3.6确定工艺路线 (12)2.4机床工艺装备的确定 (12)3.工艺夹具设计 (14)3.1研究原始质料 (14)3.2定位基准的选择 (14)3.3切削力及夹紧分析计算 (14)3.4误差分析与计算 (15)3.5零、部件的设计与选用 (16)3.5.1定位销选用 (16)3.5.2定向键与对刀装置设计 (17)3.6夹具设计及操作的简要说明 (18)参考文献 (20)致谢 (21)1.绪论1.1选题的目的和意义机械的加工工艺及夹具设计是在完成了大学的全部课程之后,进行的一次理论联系实际的综合运用,使我对专业知识、技能有了进一步的提高,为以后从事专业技术的工作打下基础。
连杆类零件柔性制造车间设计
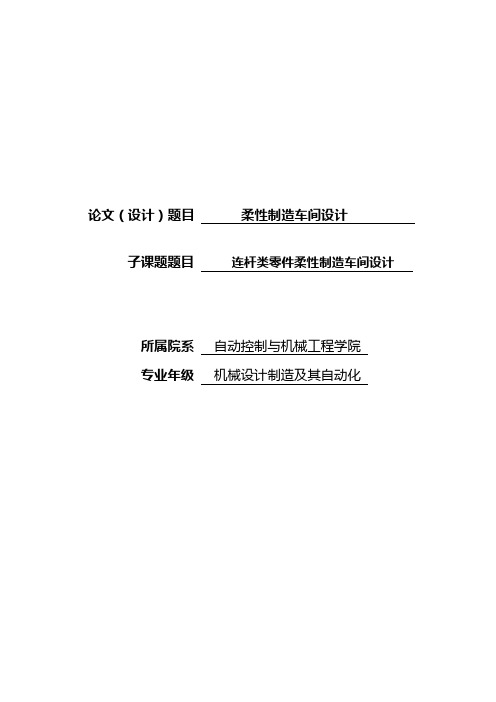
论文(设计)题目柔性制造车间设计子课题题目连杆类零件柔性制造车间设计所属院系自动控制与机械工程学院专业年级机械设计制造及其自动化摘要为了适应快速变化的市场需要,满足多品种、小批量的产品加工需求,柔性制造应运而生。
连杆类零件形状复杂,精度要求高,设计连杆类零件柔性制造车间需要选择典型的连杆零件进行工艺分析,根据工艺进行车间平面布局的设计。
柔性制造车间除了能够满足连杆类零件的加工,还需要有更多的柔性发展空间。
关键词:连杆;柔性制造;工艺分析;车间布局ABSTRACTI n order to adapt to the rapidly changing needs of the market, meet the many varieties, the processing needs of small quantities of products, flexible manufacturing came into being. Connecting rod parts of complex shape, high precision, flexible design rod parts manufacturing plant need to select the typical rod parts for process analysis, process design workshop layout. Flexible manufacturing plant in addition to meet the processing of rod parts, but also the need for more flexible space for development.Key words: connecting rod;flexible manufacturing;Process analysis ;Workshop layout目录第一章绪论 (1)1.1柔性制造产生的背景 (1)1.2柔性制造系统发展状况 (1)1.3柔性制造系统的优点 (2)1.4柔性制造车间的设计意义 (2)第二章成组技术 (3)2.1成组技术产生的意义 (3)2.2成组技术的基本原理 (3)2.3分组技术的应用 (4)第三章连杆工艺设计 (6)3.1连杆的结构特点 (6)3.2连杆的技术要求 (7)3.3连杆的材料和毛坯 (9)3.4基准选择 (10)3.5连杆加工工序安排原则 (11)3.5.1加工工序原则 (11)3.5.2其它辅助工序 (11)3.5.2.1检验工序 (11)3.5.2.2清洗工序 (12)3.5.2.3去毛刺工序 (12)3.5.2.4探伤检查工序 (12)3.5.2.5编码 (12)3.5.2.6称重工序 (12)3.6连杆加工工艺过程 (13)3.7加工余量的选择 (19)3.7.1余量参考数据 (19)3.7.2加工余量的确定 (20)第4章柔性制造系统 (22)4.1柔性制造系统 (22)4.1.1柔性制造系统的定义 (22)4.1.2柔性制造系统的组成 (22)4.1.3柔性制造系统的工作原理 (24)4.2柔性制造系统中的加工系统 (25)4.3柔性制造系统中的物流系统 (28)4.3.1物流系统的组成 (28)4.3.2工件夹具系统 (29)4.3.3工件输送系统 (30)4.3.4刀具输送流 (31)4.3.5柔性制造物流设备 (31)4.4柔性制造系统控制系统 (32)4.5柔性制造中的质量控制系统 (33)4.6柔性制造车间的设计 (34)4.7各设计方案的特点 (43)4.7.1方案一的特点 (43)4.7.2方案二的特点 (44)4.7.3方案三的特点 (45)4.8柔性制造车间展望 (46)第五章结论 (47)参考文献 (49)谢辞 (50)第一章绪论1.1柔性制造产生的背景随着科学技术的发展,人类社会对产品的功能与质量的要求越来越高,越来越多样化,产品的生命周期越来越短,产品的复杂程度也不断增高。
浅谈汽车连杆模锻工艺及其配套设备

GF 轿车连杆重量要求 390 克~410 克,即重量公差±10 克,实际测量 120 件,控制在 388 克~398 克,即实际重量公差控制在±5 克。
h
lj
GF轿车连杆 材料:40Cr
技术要求 1.连杆体经调质处理,硬度为223~280HBW,硬度差不大于 35HBW。 2.连杆纵向剖面的金属宏观组织的纤维方向应沿连杆中心线 并与外形相符,无紊乱及间断现象。 3.成品连杆的金相显微组织在连杆头工字形截面应均匀晶粒 索氏体结构,不允许有片状铁素体和非金属夹杂物存在,脱 碳层在工字形表面不得大于0.1。 4.尺寸按交点标注,[]为精锻尺寸,模锻斜度为5-7°,未 注圆角R2-3。 5.连杆不得有因金属未充满锻模而产生的缺陷,不得焊补。 6.连杆毛坯应进行抛丸强化处理。 7.连杆非加工面不得有裂纹、夹层、夹渣、折叠、氧化皮、 锈蚀等缺陷,分模面飞边高度不大于0.5,错模量小于0.3。 8.连杆应进行磁力探伤,并应退磁处理。 9.未注锻造尺寸公差按GB12362-90《钢质模锻公差及机械教 加工余量》精密级执行。 10.其余按JB/6721-93《内燃机连杆技术条件》执行。 12.连杆锻件重量应为(390~410)kg。
图 4 GF 轿车发动机连杆体锻件图
Ii
图 5 生产过程
|:!
图 6 辊锻毛坯图
63
1■—■——r——互 图 7 GF 轿车连杆终锻锻件图(一模两件)
k√’
图 8 切边后的连杆
自动锻造连杆生产线
由于汽车规模的迅猛扩张及结构的转变,发动机连杆的需求量也日益增加,一些企业也专业从事连杆
、 的锻造生产,可以形成批量生产,由于生产制造过程人力成本的上升,原有的多台组线手工锻造生产线已
■曹 成形。增设“解除闷车装置”满足一旦操作不当造成机床闷车,能够方便的解除,不损坏机床和模具。
先进制造工艺--精密洁净铸造成形工艺

第二讲1. 精密洁净铸造成形工艺气化模铸造工艺与设备概述气化模铸造按工艺方法主要分为两种:气化模-铡压铸造(EPC-V法)和气化模-精铸-负压复合铸造(EPC-CS法)。
EPC-V法铸造是气化模-振动计紧实负压工艺。
它利用气化模作一次性模型和不含水分、粘结剂及任何其他附加物的干砂造型,浇注和凝固期间铸型保持一定的负压度,由此获得近零起模斜度,可直接铸螺纹及曲折通道,表面光洁、尺寸精确、无飞边的近无余量少加工精密铸件。
EPC-CS法复合铸造是气化模-精铸-振动紧实负压复合铸造工艺。
它是用气化模代替蜡融出,将超薄型壳埋入无粘结剂干砂中,采用振动紧实造型,浇注和凝固期间铸型保持一定的负压度,而获得表面光洁、尺寸精确的无余量精密铸件。
气化模铸造是在实型铸造基础上发展起来的。
实型铸造由美国H.F.Shoyer发明并于1958年获得专利。
后经德国Witmoser等深入研究,1961年进入工业化生产,尤其对冶金矿山、造船和机械用大型、单件、小批量生产的铸件更为适宜,在工业生产中应用实型铸造的国家主要有美、英、法、俄、日、德、和中国等。
由于实型铸造采用可消失的聚苯乙烯塑料模,不存在普通砂型铸造从铸型中取出模样的困难,简化了铸造工序,降低劳动强度和成本,提高了生产效率。
但实型铸造存在着铸件表面质量差,尺寸精度低,易造成中、低碳钢铸件表面增碳和缺陷,因此限制了该工艺的发展和应用。
80年代,工业发达国家,在实型铸造基础上,针对上述问题进行了研究,推出了EPC-V法铸造工艺,引起了铸造界的关注,认为这是铸造行业上的一项突破。
福特、通用、菲亚特等汽车公司已开始应用该工艺生产汽车、发动机和涡轮机用铸件,如图28所示。
该工艺在欧洲、美洲、日本及中国也等到大力开发和应用。
然而,EPC-V法铸造工艺易于在铸件内存在气化残物和造成中、低碳钢铸件表面增碳、增氢缺陷[59],一般渗碳层深度为0.5~2.5mm,渗碳量(质量分数)在0.01%~0.6%之间,使铝合金铸件的气密性较差,从而限制了EPC-V铸造在生产铸铝、铸钢件中的应用。
锻造自动化及其周边设备 PPT
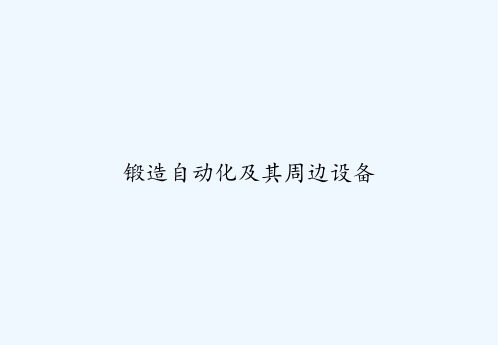
QDC设计效果图
现场实际图
2 锻造自动化的核心组件
锻造自动化的核心组件:
1、步进梁组件;2、喷淋冷却及回收过滤组件;3、快速换模组件;4、除尘组件;5、润滑油过滤 组件
4、除尘组件; 1)彻底锻压设备循环润滑油乳化问题; 2)解决空气达标排放问题; 3)改善车间作业环境。
产生时设备内部大量的水气和烟尘
喷淋冷却阀组
喷淋冷却伸缩组件
脱模剂回收、过滤组件
大家学习辛苦了,还是要坚持
继续保持安静
2 锻造自动化的核心组件
锻造自动化的核心组件:
1、步进梁组件;2、喷淋冷却及回收过滤组件;3、快速换模组件;4、除尘组件;5、润滑油过滤 组件
3、快速换模组件: 1)提高流程产能:缩短切换的停车时间,提高设备的利用率,换型时间从3.5小时缩短至0.5小时; 2)快速交付缩短交货时间,不需额外的库存即可满足客户交货要求,资金不压在额外库存上; 3)灵活生产,提高换线的频率。
锻造自动化及其周边设备
CONETENTS 目录
1 锻造自动化产线布局 2 锻造自动化的核心组件 3 锻造自动化连接
1 锻造自动化产线布局
汽车发动机连杆生产工艺
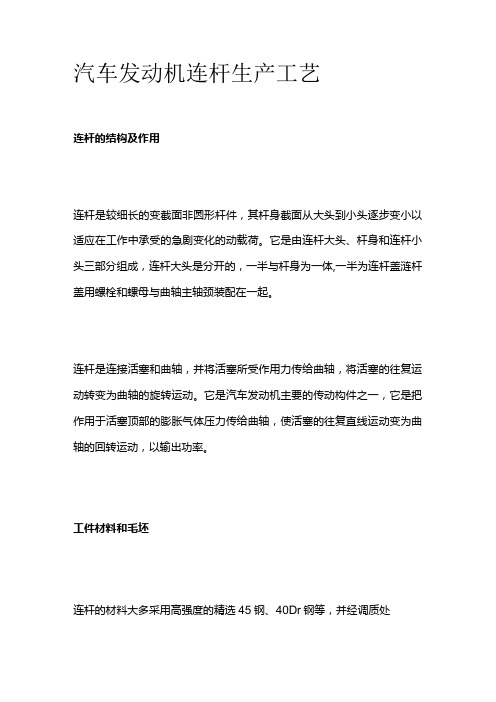
汽车发动机连杆生产工艺连杆的结构及作用连杆是较细长的变截面非圆形杆件,其杆身截面从大头到小头逐步变小以适应在工作中承受的急剧变化的动载荷。
它是由连杆大头、杆身和连杆小头三部分组成,连杆大头是分开的,一半与杆身为一体,一半为连杆盖涟杆盖用螺栓和螺母与曲轴主轴颈装配在一起。
连杆是连接活塞和曲轴,并将活塞所受作用力传给曲轴,将活塞的往复运动转变为曲轴的旋转运动。
它是汽车发动机主要的传动构件之一,它是把作用于活塞顶部的膨胀气体压力传给曲轴,使活塞的往复直线运动变为曲轴的回转运动,以输出功率。
工件材料和毛坯连杆的材料大多采用高强度的精选45钢、40Dr钢等,并经调质处理以改善切削性能和提高抗冲击能力,硬度要求45钢为HB217~ 293,40Dr为HB223~280。
也有采用球墨铸铁和粉末冶金技术的,可降低毛坯成本。
钢制连杆的毛坯一般都是锻造生产,其毛坯形式有两种:一种是体、盖分开锻造;另一种是将体、盖锻成一体,在加工过程中再切开或采用胀断工艺将其胀断。
另外为避免毛坯出现缺陷,要求对其进行100%的硬度测量和探伤。
连杆加工工艺过程1.定位及夹紧1)粗基准的正确选择和初定位夹具的合理设计是加工工艺中至关重要的问题。
在拉连杆大小头侧定位面时,采用连杆的基准端面及小头毛坯外圆三点和大头毛坯外圆二点粗基准定位方式。
这样保证了大小头孔和盖上各加工面加工余量均匀,保证了连杆大头称重去重均匀,保证了零件总成最终形状及位置。
2)在连杆杆和总成的加工中,采用杆端面、小头顶面和侧面、大头侧面的加工定位方式。
在螺栓孔至止口斜结合面加工工序的连杆盖加工中,采用了以其端面、螺栓两座面、一螺栓座面的侧面的加工定位方法。
这种重复定位精度高且稳定可靠的定位、夹紧方法,可使零件变形小,操作方便,能通用于从粗加工到精加工中的各道工序。
由于定位基准统一,使各工序中定位点的大小及位置也保持相同。
这些都为稳定工艺、保证加工精度提供了良好的条件。
2.加工顺序的安排和加工阶段的划分连杆的尺寸精度、形状精度和位置精度的要求都很高,但刚度又较差,容易产生变形。
典型精密热锻生产线举例

锻造生产线的发展方向主要有两个,一是出现了锻造柔性生产线,以满足用户对产品多样化的需求;另外一个是由于推广采用非调质钢,锻造生产线与热处理生产线可以连在一起建设,直接利用锻造余热淬火,省去再次加热的时间及费用,而且有利于锻件质量的提高。
1—感应加热机床 2—传送带 3—辊锻机 4、7、12、17—机械手 5、13—分料架
6—120000kN斜楔式热模锻压力机 8—中央控制台 9—模具清理与喷雾装置
10—带随行小车的传送带 11—切边压力机
14—曲拐扭转机 15 —校正压力机 16—链式传送带 18—悬挂式输送机
2.汽车前梁精密辊锻-模锻生产线
利用辊锻逐步变形原理将锻件的大部分在辊锻工序中锻出来,再通过模锻把弹簧座等不能精确辊锻成形部锻出来,这样可以大大减少模锻设备负荷,成功地利用25000kN螺旋压力机作为主设备,大幅度降低了生产线投资。其主要工艺流程如下:
中频感应加热(750kW中频炉)→4道次整体精密成形辊锻(φ1000辊锻机及辊锻机器人)整体弯曲、模锻(25000kN 螺旋压力机)→整体切边(10000kN螺旋压力机)→整体校正(16000kN螺旋压力机)→调质处理(调质生产线)→校正(1000kN液压机)→喷九→检验。根据需要,螺旋压力机可全部配机器人,成为全自动生产线;锻件重量较轻时,也可部分采用机器人。
在大批量模锻件生产中热锻生产线技术已经成熟,既有针对→般锻件的生产线,又有针对特殊锻件以专机为主体的生产线,后者例如以高速镦锻机为主体的环类件热锻生产线,以多锤头径向锻机为主体轴类件锻造生产线等,以下介绍几种常见的→般锻件生产线。
10kN热模锻压力机自动线
当中型卡车曲轴采用锻件时,主锻造压力机将需要120000kN,其工艺流程如下:
- 1、下载文档前请自行甄别文档内容的完整性,平台不提供额外的编辑、内容补充、找答案等附加服务。
- 2、"仅部分预览"的文档,不可在线预览部分如存在完整性等问题,可反馈申请退款(可完整预览的文档不适用该条件!)。
- 3、如文档侵犯您的权益,请联系客服反馈,我们会尽快为您处理(人工客服工作时间:9:00-18:30)。
连杆自动化精密锻造生产线王 强1,袁文生2,吕富强2(11济南大学,山东济南 250022;21济南铸造锻压机械研究所,山东济南 250022)摘 要:介绍了连杆精密锻造工艺,自动化精密锻造生产线的组成、功能、特点及应用。
关键词:连杆;锻造;自动化;生产线中图分类号:T G 315 文献标识码:B 文章编号:10012196X (2002)022*******Auto ma ti c prec isi on forg i n g producti on l i n e for connecti n g rodsWAN G Q iang 1,YUAN W en 2sheng 2,LUFu 2qiang2(11J i Εnan U n iversity ,J i Εnan 250022,Ch ina )(21J i Εnan M etalfo r m ing M ach inery R esearch In stitute ,J i Εnan 250022,Ch ina )Abstract :T h is paper p resen ts the p recisi on fo rging techno l ogy of connecting rods ,together w ith the compo siti on ,functi on s ,p roperties and app licati on of the autom atic p roducti on line .Keywords :connecting rod ;fo rging ;autom ati on ;po rducti on line1 引言连杆属于长轴类精密锻件,是发动机内最重要的零件之一,市场需求量巨大。
连杆不仅要求较高的尺寸精度,而且对重量公差也有严格的要求。
另外,由于发动机高速运转导致连杆内部产生高频交变应力,因此,对连杆强度,特别是疲劳强度,也提出了较高的要求。
长期以来,连杆一直被视为较难锻造的精密锻件[1,2,5,7]。
在我国,传统的连杆锻造工艺是采用火焰加热,空气锤上型砧制坯,摩擦压力机或蒸空锤锻造,切边、冲连皮,最后进行热校正。
其缺点表现为:(1)自动化程度低。
主要工序全部依靠手工操作,导致生产率低,操作人数多且劳动强度大,生产节拍难以保证,产品质量受操作水平的影响程度较大;(2)锻件精度低,一致性差,锻件表层易产生脱碳,很难达到488、捷达等高精度连杆锻件对精度和质量提出的要求;(3)将切边、冲连皮与热校正分成多个独立的工序,不仅增加了操作人数及设备数量,而且收稿日期:2001210215作者简介:王强,男,38岁,高工(博士)济南大学(250022)也不易保证连杆大小头的中心距精度;(4)制坯精度底,飞边肥大,材料利用率低;(5)加热炉及锻造设备的能耗高。
为了满足高精度连杆对锻造生产线提出的自动化及质量方面的要求,缩短该领域内我国与国际先进水平之间的差距,我们开发了连杆精密锻造工艺,研制成功了自动化精密锻造生产线。
2 连杆精密锻造工艺各类生产线均应以特定的产品为对象,以相应的工艺为基础,设备为工艺服务,又是工艺的具体体现。
研制高性能连杆锻造生产线应以精密锻造工艺为龙头。
图1所示为某型号摩托车连杆锻件示意图,根据其形状复杂程度,尺寸精度、重量公差要求高等特点,确定出锻造工艺流程如图2所示。
由于该锻件尺寸小,重量轻,为了提高生产率,模锻工步可采用一模两件的方法。
3 自动化精密锻造生产线连杆自动化精密锻造生产线以年产锻件120万件(一模两件时为240万件 年)为生产纲领,生产节拍为7~8件 分,锻件最大重量为015kg 。
主要产品为摩托车发动机连杆、488连杆、捷达连・91・2002 N o 12 重型机械 杆,也可用来生产其它长轴类精密锻件。
图1 某型号摩托车连杆锻件图自动化上料中频感应加热料温自动分选楔横轧自动制坯电液锤模锻切边、冲连皮、热校图2 连杆精密锻造工艺 整条锻造生产线的设备为顺序动作,安全可靠,且节拍可调。
采用PC 控制联线技术,实现了从振动上料、感应加热、料温分选到楔横轧机制坯的自动化。
工件在楔横轧机与电液锤之间、电液锤与压力机之间的传输均采用输送机。
全线最多需要3名工人,分别负责锻造、切边和全线巡视。
连杆自动化精密锻造生产线的总体布置如图3所示。
整条生产线的长度约1615m ,宽度约615m ,最高点处(电液锤)的高度为5109m 。
加热炉毛坯水平送进的高度为1182m ,楔横轧机水平送料的高度为01725m 。
各部分的设备组成、功能及特点分别介绍如下:图3 连杆自动化精密锻造生产线总体布置图11振动排序上料机 21水平振动给料机 31中频感应加热炉 41红外测温仪 51料温分选执行机构61辊式楔横轧机 711号输送机 81短行程电液模锻锤 912号输送机 101开式固定台压力机311 自动上料系统自动上料系统由液压翻转加料机、振动排序上料机[4]和水平振动给料机组成,其主要功能和动作如下所述:(1)用叉车将存放在料箱中的毛坯连同料箱一起推入液压翻转加料机。
加料机提升料箱,将毛坯缓慢倒入振动排序上料机的料斗内。
料斗直径为1600mm ,最大加料重量700kg ,最大棒料直径<60mm 。
根据毛坯单件重量的不同,一次加料可维持315~6h 的连续正常生产;(2)在振动电机的作用下,毛坯沿上料机料斗内壁的螺旋料道向上爬升,并在上升过程中自动进行排序;(3)上料机的出口通过水平振动给料机与加热炉送料装置的入口衔接,毛坯可按照事先设定的节拍,顺序送入感应加热线圈,从而可实现中频加热炉上料过程的自动化。
当上料机料斗内出现缺料时,控制系统将发出缺料报警信号,通知巡视工人进行下一次加料。
312 感应加热及料温自动分选系统中频感应加热炉的额定功率为250k W ,实际加热功率根据毛坯重量和生产节拍确定。
为了适应不同直径毛坯的加热要求,感应加热线圈部件采用了快换接头,可实现不同规格线圈之间的快速更换。
加热线圈入口处安装有滚压轮推料机构[3],与水平振动给料机的出口衔接。
毛坯的送进速度,换言之整条生产线的生产节拍,可以通过无级调节滚压轮的转速来实现。
感应加热线圈出口处安装有引料装置和料温自动分选系统。
料温自动分选系统由红外测温仪、料温分选执行机构和出料滑道组成。
出料滑道分为三路:正常料道、过烧料道和欠温料道。
根据连杆材料的不同,可确定相应的始锻温・02・ 重型机械 2002 N o 12度范围,并将温度上、下临界值输入到控制系统内。
若红外测温仪测出的料温高于上临界值,则毛坯过烧,执行机构启动过烧料道使毛坯进入废料箱。
若料温低于下临界值,则毛坯欠温,执行机构启动过欠温道使毛坯进入回收箱。
回收箱内的毛坯可再次加热使用。
只有料温介于上、下临界值之间的毛坯,才能通过正常料道输送到后续工位。
整个料温分选过程是自动完成的,严格的料温控制措施为确保连杆锻造质量提供了可靠的保障。
313 楔横轧机自动制坯采用楔横轧机进行制坯可获得高精度锻造毛坯,具有节能、节材、生产率高、模具寿命长等优点,并可实现轧制过程的自动化,是替代空气锤制坯的换代工艺和设备[6]。
与同属连续回转成形工艺的辊锻技术相比,楔横轧机具有设备成本低的优点[1]。
该生产线配备了一台DA462500型辊式楔横轧机,附带自动上料装置,可轧毛坯最大直径<35 mm,长度为400mm。
设备采用整体式结构,PC 控制,工作规范有连续、半自动单次、单次、和寸动调整四种。
在半自动单次工作模式下,楔横轧机的动作受料温分选系统的控制:当温度正常的坯料落入楔横轧机送料位置后,由接近开关检测有料并发讯,推料气缸自动推动毛坯进入到两个轧辊之间,从而启动一个轧制动作循环。
轧制成形后的坯料依靠重力落入输送机,并被输送到模锻工步。
314 电液锤模锻采用从德国米勒万家顿股份公司引进的KGH型短行程电液模锻锤进行模锻,分为压扁、预锻和终锻三个工位。
设备额定打击能量为3115 kJ。
采用进油打击原理,打击过程可实现PC控制,能够精确控制打击能量、打击次数、两次打击之间间歇时间等工作参数。
该设备还具备参数存储,故障报警及自动诊断等功能。
电液锤能量利用率高,锤头导向精度好,抗偏载能力强,操作安全可靠,锻件质量基本不受工人操作水平的影响,从而为实现连杆精密锻造提供了可靠的设备保障。
与热模锻压力机相比,电液锤使用灵活方便,投资较低,尤其适合中小批量锻件的生产。
锻件沿高度方向的尺寸精度较高,沿水平方向的尺寸精度由锻模精度保证。
锻模采用镶块式结构,通过螺杆式固定斜楔与模座连接,更换模块快捷,调整方便,模具费用低。
315 压力机切边、冲连皮、热校由于连杆杆部的腹板较薄,在模锻、切边、冲连皮过程中易产生弯曲或扭曲变形。
传统工艺是将热切边和热校正分成几个独立的工步,热校正的作用是校正已经发生的弯曲或扭曲变形,效果不明显,尤其很难保证大小头的中心距公差。
我们开发研制成功了切边、冲连皮、热校复合工艺,使用一副复合模具,在压力机的一个工作循环内,首先通过弹性压紧装置压住锻件,然后顺序完成切边和冲连皮动作,从而有效阻止和预防扭曲变形的产生。
该工艺不仅保证了连杆精度,而且节省了工人人数及设备数量,减少了生产线占地面积。
压力机的公称压力为1600kN。
4 结论以连杆精密锻造工艺为基础,研制成功了自动化精密锻造生产线,可实现从振动上料、感应加热、料温分选到楔横轧机制坯的自动化,可用来生产摩托车发动机连杆、488连杆、捷达连杆等长轴类精密锻件,具有节能、节材、效率高、产品精度高、质量好等优点,是替代传统连杆锻造生产设备的换代产品。
该类型生产线已有三条投入使用,取得了良好的经济效益。
参考文献:[1] 王强,雷家琨,毛胜如1欧洲锻造工业的新进展[J]1锻压机械,2001,36(3):3~61[2] 罗晴岚1连杆锻造工艺技术的进步[J]1锻压机械,2000,35(4):1~31[3] 吕富强1滚压轮推料机构的参数设计[J]1锻压机械,1998,33(2):26~271[4] 吕富强,刘桂荣1振动排序上料机[J]1锻压机械,1997,32(6):17~181[5] 罗晴岚1摩托车锻件生产工艺的改造[J]1锻压机械,1997,32(2):3~71[6] 袁文生1楔横轧工艺在摩托车锻造行业中的应用[J]1锻压机械,1995,30(3):24~251[7] M anfred M uller,雷家琨1连杆锻造工艺及设备[J]1锻压机械,1995,30(3):43~451・12・2002 N o12 重型机械 。