COPLEY驱动器用户指南
贝利莫 CQ24A 区域式阀门电动齿轮驱动器说明书

CQ24A ArrayRotary actuator for zone valves• Torque motor 1 Nm• Nominal voltage AC/DC 24 V• Control Open/close, 3-point• Snap-assembly of the actuator• Flow setting variableTechnical dataElectrical data Nominal voltage AC/DC 24 VNominal voltage frequency50/60 HzNominal voltage range AC 19.2...28.8 V / DC 21.6...28.8 VPower consumption in operation0.3 WPower consumption in rest position0.2 WPower consumption for wire sizing0.6 VAConnection supply / control Cable 1 m, 3 x 0.75 mm²Parallel operation Yes (note the performance data)Functional data Torque motor1 NmManual override with actuator (clicked out)Running time motor75 s / 90°Sound power level, motor35 dB(A)Position indication YesFlow setting see product featuresSafety data Protection class IEC/EN III, Safety Extra-Low Voltage (SELV)Degree of protection IEC/EN IP40EMC CE according to 2014/30/EUCertification IEC/EN IEC/EN 60730-1 and IEC/EN 60730-2-14Type of action Type 1Rated impulse voltage supply / control0.8 kVPollution degree2Ambient humidity Max. 95% RH, non-condensingAmbient temperature 5...40°C [41...104°F]Storage temperature-40...80°C [-40...176°F]Servicing maintenance-freeWeight Weight0.21 kgCQ24A••••••Simple direct mountingManual overrideAdjustable angle of rotation High functional reliabilityFlow settingSafety notesThis device has been designed for use in stationary heating, ventilation and air-conditioning systems and must not be used outside the specified field of application, especially in aircraft or in any other airborne means of transport.Outdoor application: only possible in case that no (sea) water, snow, ice, insolation or aggressive gases interfere directly with the device and that it is ensured that the ambient conditions remain within the thresholds according to the data sheet at any time.Only authorised specialists may carry out installation. All applicable legal or institutional installation regulations must be complied during installation.The device may only be opened at the manufacturer's site. It does not contain any parts that can be replaced or repaired by the user.Cables must not be removed from the device.The device contains electrical and electronic components and must not be disposed of as household refuse. All locally valid regulations and requirements must be observed.Product featuresTool-free snap assembly.The actuator can be plugged on the valve by hand (Caution! Just vertical movements). Pins must match the holes on the flange.The mounting orientation in relation to the valve can be selected in 180° increments. (Possible two times)Click out the actuator and rotate the valve spindle with the help of the actuator.The angle of rotation of the actuator can be changed by clip in 2.5° increments. This is used to set the maximum flow rate of the valve.The actuator is overload protected, requires no limit switches and automatically stops when the end stop is reached.Adjustable kv-values (C2..Q-.., C4..Q-..) / V'max-values (C2..QP(T)-..) are given in the respective zone valve data sheets.2-way valve: Remove end stop clip and place at desired position.3-way valve: Remove end stop clip (change-over application).AccessoriesMechanical accessoriesDescriptionType Spindle extension CQZCQ-E Housing cover CQ, Colour: white (RAL 9010)ZCQ-W End stop clip, Multipack 5 pcs.ZCQ-C End stop clip, Multipack 20 pcs.Z-ESCMElectrical installationSupply from isolating transformer.Parallel connection of other actuators possible. Observe the performance data.CQ24A Wire colours:1 = black2 = red3 = whiteWiring diagramsAC/DC 24 V, open/close AC/DC 24 V, 3-pointDimensionsFurther documentation• The complete product range for water applications• Data sheet for zone valves• Installation instructions for zone valves and actuators• General notes for project planning。
XPL-ds_ Xenus Copley交流伺服驱动器

descriptionXenus Plus set new levels of performance, connectivity, and flexibility. CANopen communication provides a widely used cost-effective industrial bus. A wide range of absolute interfaces are built-in including EnDat, Hiperface, and BiSS.High resolution A/D converters ensure optimal current loop performance. Both isolated and high-speed non-isolated I/O are provided. For safety critical applications, redundant power stage enable inputs can be employed.Model Vac Ic Ip XPL-230-18100 - 240618XPL-230-36100 - 2401236XPL-230-40100 - 2402040Add -R for resolver feedback optioncontrol Modes• Indexer, Point-to-Point, PVT • Camming, Gearing• Position, Velocity, Torquecommand interface• CANopen• ASCII and discrete I/O • stepper commands• ±10V position/velocity/torque (2 inputs) • PWM velocity/torque command• Master encoder (Gearing/Camming)Communications• CAN • RS-232• RS-485 (Optional)Accessories• External regen resistors • External edge filterFeedback• Digital quad A/B encoder• EnDat, Hiperface, BiSS, SSI, & panasonic encoders• Aux. encoder / encoder out • Analog sin/cos encoder • Resolver option • Digital HallsSafe Torque Off (STO)• Two active inputs enable power stage • One output confirms power stage status I/O Digital• 15 inputs, 6 outputs I/O Analog• 2, 16 bit inputs • 1, 12 bit input • 1, 12 bit outputDimensions: in [mm]• 7.9 x 5.5 x 2.3 [202 x 139 x 52]GENERAL SPECIFICATIONSTest conditions: Wye connected load: 2 mH line-line. Ambient temperature = 25 °C. Power input = 230 Vac, 60 Hz, 1 ØModeL XPL-230-18 XPL-230-36 XPL-230-40OUTPUT CURRENTPeak Current 18 (12.7) 36 (25.5) 40 (28.3) Adc (Arms, sinusoidal)Peak time 1 1 1 sContinuous current (Note 1) 6 (4.24) 12 (8.5) 20 (14.1) Adc (Arms, sinusoidal)INPUT POWERMains voltage, phase, frequency 100~240 Vac, ±10%, 1Ø or 3Ø, 47~63 Hz Maximum Mains Current, 1Ø (Note 3) 10.1 20.0 20.0 ArmsMaximum Mains current, 3Ø (Note 3) 6.4 10.4 15.4 Arms+24 Vdc Control power +20 to +32 Vdc, 500 mA max Required for operationDIGITAL CONTROLDigital Control Loops Current, velocity, position. 100% digital loop controlSampling rate (time) Current loop: 16 kHz (62.5 µs), Velocity & position loops: 4 kHz (250 µs)Bus voltage compensation Changes in bus or mains voltage do not affect bandwidthMinimum load inductance 200 µH line-lineCOMMAND INPUTS (NOTE: DIGITAL INPUT FUNCTIONS ARE PROGRAMMABLE)Distributed Control ModesCANopen Position, Velocity, Torque, Homing, Profile, and Interpolated profile modesStand-alone modeAnalog torque, velocity, position reference ±10 Vdc, 16 bit resolution Dedicated differential analog inputInput impedance 74.8 kΩBetween Ref(+), Ref(-)Digital position reference Pulse/Direction, CW/CCW Stepper commands (2 MHz maximum rate)Quad A/B Encoder 2 M line/sec, 8 Mcount/sec (after quadrature) Digital torque & velocity reference PWM , Polarity PWM = 0% - 100%, Polarity = 1/0PWM 50% PWM = 50% ±50%, no polarity signal requiredPWM frequency range 1 kHz minimum, 100 kHz maximumPWM minimum pulse width 220 nsIndexing Up to 32 sequences can be launched from inputs or ASCII commands.Camming Up to 10 CAM tables can be stored in flash memoryASCII RS-232, 9600~115,200 Baud, 3-wire, RJ-11 connectorDIGITAL INPUTSNumber 15[IN1,2] Non-isolated Schmitt trigger, 1 µs RC filter, 24 Vdc max, Vt + = 2.5~3.5 Vdc, Vt- = 1.3~2.2 Vdc, VH+ = 0.7~1.5 Vdc10 kΩ programmable per input to pull-up to +5 Vdc or pull-down to ground[IN3~6] Non-isolated line receiver, 100 ns RC filter, +12 Vdc max, programmable as 4 single-ended, or 2 differentialSingle-ended: [IN3,4] or [IN5,6]: Vin-LO <= 2.3 Vdc, Vin-HI >= 2.7 Vdc, Vhysteresis = 400 mVdcDifferential: [IN3/4] or [IN5/6]: Vin-LO <= -200 mVdc, Vin-HI >= 200 mVdc, Vhysteresis = ±200 mVdc [IN7~14] Opto-isolated, ±15~30 Vdc compatible, bi-polar, 2 groups of 4 with common for each group[IN15] Encoder fault; same electrical specs as [IN1,2,15] except 10 kΩ fixed pull-up to +5 VdcANALOG INPUTSNumber 3[AIN1~2] Differential, ±10 Vdc, 5 kΩ input impedance, 16-bit resolution[AIN3] Single-ended, motor temperature sensor, 4.99 kΩ pulled-up to +5 Vdc, 12-bit resolutionDIGITAL OUTPUTSNumber 6[OUT1~2] Current-sinking MOSFET with 1 kΩ pullup to +5 Vdc through diode1 Adc max, +40 Vdc max; external flyback diode required if driving inductive loads[OUT3] High-speed CMOS buffer, ±32 mA[OUT4~5] Opto-isolated Darlingtons with 36V Zener flyback diodes, 20 mA max[OUT6] Motor brake control: opto-isolated, current-sinking with flyback diode to +24 Vdc, 1 Adc maxANALOG OUTPUTRange ±5 Vdc single-ended, 12-bit resolutionMULTI-MODE ENCODER PORTAs Input Secondary digital quadrature encoder (A, /A, B, /B, X, /X), 121 Ω terminating resistors18 M-counts/sec, post-quadrature (4.5 M-lines/sec)As Output Quadrature encoder emulation with programmable resolution to 4096 lines (65,536 counts) per revfrom analog sin/cos encoders or resolvers. Buffered signals from digital quad A/B/X primary encoderA, /A, B, /B, X, /X, from MAX3032 differential line driverRS-232 PORTSignals RxD, TxD, Gnd in 6-position, 4-contact RJ-11 style modular connectorMode Full-duplex, DTE serial communication port for drive setup and control, 9,600 to 115,200 baudProtocol Binary and ASCII formatsCAN PORTSignals CANH, CANL, Gnd in 8-position dual RJ-45 style modular connector, wired as per CAN Cia DR-303-1, V1.1Format CAN V2.0b physical layer for high-speed connections compliantData CANopen Device Profile DSP-402Address selection 16 position rotary switch on front panel with 3 additional address bits available asdigital inputs or programmable to flash memory (7-bit addressing, 127 nodes per CAN network)STATUS INDICATOR LEDSDrive Status Bicolor LED, drive status indicated by color, and blinking or non-blinking conditionCAN Status Bicolor LED, status of CAN bus indicated by color and blink codes to CAN Indicator Specification 303-3NOTES:1. Heatsinking and/or forced-air cooling is required for the continuous output power rating2. Brake[OUT6] is programmable as motor brake, or as general purpose digital output3. The actual mains current is dependent on the mains voltage, number of phases, and motor load and operating conditions. The Maximum Mains Currents shown aboveoccur when the drive is operating from the maximum input voltage and is producing the rated continuous output current at the maximum output voltage.5V OUTPUTTwo independent 5 Vdc @ 400 mA outputs: J8-20 and J10-6,17REGENERATIONOperation Internal solid-state switch drives external regen resistor (see Ordering Guide for types)Cut-In Voltage +HV > 390 Vdc Regen output is on, (optional external) regen resistor is dissipating energy Drop-Out Voltage +HV < 380 Vdc Regen output is off, (optional external) regen resistor not dissipating energy Tolerance ±2 Vdc For either Cut-In or Drop-Out voltage protections HV Overvoltage +HV > 400 Vdc Drive PWM outputs turn off until +HV is less than overvoltage HV Undervoltage +HV < 60 Vdc Drive PWM outputs turn off until +HV is greater than undervoltage Drive over temperature IGBT > 80 °C ±3 °C Drive PWM outputs turn off until IGBT temperature is below threshold Short circuitsOutput to output, output to ground, internal PWM bridge faults i 2T Current limiting Programmable: continuous current, peak current, peak timeMotor over temperature Programmable input to disable drive when voltage is above or below a set point 0~5 Vdc Feedback power loss Fault occurs if feedback is removed or +5 V is <85% of normalMECHANICAL & ENVIRONMENTAL Size 7.55 in (191,8 mm) X 5.57 in (141,5 mm) X 2.57 in (65,3 mm) Weight 3.0 lb (1.36 kg) for drive without heatsink3.1 lb (1.40 kg) for XPL-HS heatsink, 1.86 lb (0.84 kg) for XPL-HL heatsink Ambient temperature 0 to +45 °C operating, -40 to +85 °C storage Humidity 0% to 95%, non-condensing Contaminants Pollution degree 2Vibration 2 g peak, 10~500 Hz (sine), IEC60068-2-6 Shock 10 g , 10 ms, half-sine pulse, IEC60068-2-27 Environment IEC68-2: 1990CoolingHeat sink and/or forced air cooling required for continuous power outputAGENCy STANDARDS CONFORMANCEIn accordance with EC Directive 2004/108/EC (EMC Directive)EN 55011: 2007 CISPR 11:2003/A2:2006Industrial, Scientific, and Medical (ISM) Radio Frequency Equipment –Electromagnetic Disturbance Characteristics – Limits and Methods of Measurement Group 1, Class AEN 61000-6-1: 2007 Electromagnetic Compatibility (EMC) – Part 6-1: Generic Standards –Immunity for residential, Commercial and Light-industrial EnvironmentsIn accordance with EC Directive 2006/95/EC (Low Voltage Directive) IEC 61010-1:2001 Safety Requirements for Electrical Equipment for Measurement, Control and Laboratory Use Underwriters Laboratory Standards UL 61010-1, 2nd Ed.: 2004 Safety Requirements for Electrical Equipment for Measurement, Control and Laboratory Use UL File Number E24989425.40TYP2.3776.20diMensions Inches (mm)Chassis groundingtabFEEDBACk SPECIFICATIONSDIGITAL QUAD A/B ENCODERType Quadrature, differential line driver outputsSignals A, /A, B, /B, (X, /X, index signals optional)RS-422/RS-485 line receivers with fault detection for open/shorted inputs, or low signal amplitude Frequency 5 MHz line frequency, 20 MHz quadrature count frequencyANALOG ENCODERType Sin/cos/index, differential line driver outputs, 0.5 Vpeak-peak (1.0 Vpeak-peak differential)centered about 2.5 Vdc typical. Common-mode voltage 0.25 to 3.75 VdcSignals Sin(+), sin(-), cos(+), cos(-), index(+), index(-)Frequency 230kHz maximum line (cycle) frequencyInterpolation 10 bits/cycle (1024 counts/cycle)DIGITAL HALLSType Digital, single-ended, 120° electrical phase differenceSignals U, V, WInputs 10 kΩ pullups to +5 Vdc, 1 µs RC filter to Schmitt trigger invertersMULTI-MODE ENCODER PORTAs Input Secondary digital quadrature encoder (A, /A, B, /B, X, /X), 121 Ω terminating resistors18 M-counts/sec, post-quadrature (4.5 M-lines/sec)As Emulated Output Quadrature encoder emulation with programmable resolution to 4096 lines (65,536 counts) per revfrom analog sin/cos encoders or resolvers.A, /A, B, /B, X, /X, from MAX3032 differential line driverAs Buffered Output Digital encoder feedback signals from primary digital encoder are buffered by MAX3032 line driver RESOLVER (-R OPTION)Type Brushless, single-speed, 1:1 to 2:1 programmable transformation ratioResolution 14 bits (equivalent to a 4096 line quadrature encoder)Reference frequency 7.5 kHzReference voltage 2.8 Vrms, auto-adjustable by the drive to maximize feedbackReference maximum current 100 mAMaximum RPM 10,000+ENCODER POWER SUPPLIESNumber 2Ratings +5 Vdc @ 400 mA from J10-6 and J8-20Protection Current-limited to 750 mA @ 1 Vdc if overloadedEncoder power developed from +24 Vdc so position information is not lost when AC mains power is removedSAFE TORQUE OFF (STO)Inputs 2 two-terminal: [ENH+], [ENH-], [ENL+], [ENL-]Type Opto-isolators, 24V compatibleOutput 1 two-terminal: [LED+], [LED-]24V compatiblenote!help you get the best results when using Copley Controls products.6915D-Sub 9F3322CAN_L CAN_GNDCAN_HCAN_L RJ-45CAN_GND CAN_H71J7Pin 8CANOPEN CONNECTORSDual RJ-45 connectors that accept standard Ethernet cables are provided for CAN bus connectivity. Pins are wired-through so that drives can be daisy-chained and controlled with a single connection to the user’s CAN interface. A CAN terminator should be placed in the last drive in the chain. The XPL-Nk connector kit provides a D-Sub adapter that plugs into a CAN controller and has an RJ-45 socket that accepts the Ethernet cable.XPL-Nk CAN CONNECTOR kITThe kit contains the XPL-CV adapter that converts the CAN interface D-Sub 9M connector to an RJ-45 Ethernet cable socket, plus a 10 ft (3 m) cable and terminator . Both connector pin-outs conform to the CiA DR-303-1 specification.J7 CAN CONNECTIONSpin SIGNAL 2RxD 3,4Gnd 5TxdJ6: RS-232 PORTRJ-12 receptacle, 6 position, 4 contactSTAT LED (ON J6)A bi-color LED gives the state of the Xenus Plus drive. Colors do not alternate, and can be solid ON or blinking:Green/Solid = Drive Ok and enabled. Will run in response to reference inputs or EtherCAT commands. Green/Slow-Blinking = Drive Ok but NOT-enabled. Will run when enabled.Green/Fast-Blinking = Positive or Negative limit switch active. Drive will only move in direction not inhibited by limit switch. Red/Solid = Transient fault condition. Drive will resume operation when fault is removed. Red/Blinking = Latching fault. Operation will not resume until drive is Reset.Drive Fault conditions: • Over or under-voltage • Motor over-temperature • Encoder +5 Vdc fault • Drive over-temperature • Short-circuits from output to output • Short-circuits from output to ground • Internal short circuitsFaults are programmable to be either transient or latchingSTATnetCOMMUNICATIONSRS-232 MULTI-DROPThe RS-232 specification makes no allowance for more than two devices on a serial link. But, multiple Xenus drives can communicateover a single RS-232 port by daisy-chaining a master drive to other drives using CAN cables. In the CAN protocol, address 0 is reserved for the CAN master and thereafter all other nodes on a CAN network must have unique, non-zero addresses. When the Xenus CANaddress is set to 0, it acts as a CAN master , converting the RS-232 data into CAN messages and passing it along to the other driveswhich act as CAN nodes.CAN Addr 0CAN Master CAN Node CAN NodeCAN Addr 1CAN Addr nTxD RxD RJ-1153GndGndRxD TxD6915D-Sub 9FASCII COMMUNICATIONSThe Copley ASCII Interface is a set of ASCII format commands that can be used to operate and monitor Copley Controls Accelnet, Stepnet, and Xenus series amplifiers over an RS-232 serial connection. For instance, after basic amplifier configuration values have been programmed using CME 2, a control program can use the ASCII Interface to:• Enable the amplifier in Programmed Position mode.• Home the axis.• Issue a series of move commands while monitoring position, velocity, and other run-time variables.Additional information can be found in the ASCII Programmers Guide on the Copley website:/Motion/pdf/ASCII_ProgrammersGuide.pdfpin SIGNAL 2RxD 3,4Gnd 5TxdJ6: RS-232 PORTRJ-11 receptacle, 6 position, 4 contactRS-232 COMMUNICATIONSXPL is configured via a three-wire, full-duplex DTE RS-232 port that operates from 9600 to 115,200 Baud, 8 bits, no parity, and one stop bit. Signal format is full-duplex, 3-wire, DTE using RxD, TxD, and Gnd. Connections to the XPL RS-232 port are through J7, an RJ-11 connector . The XPL Serial Cable kit (SER-Ck) contains a modular cable, and an adapter that connects to a 9-pin, Sub-D serial port connector (COM1, COM2, etc.) on PC’s and compatibles.SER-Ck SERIAL CABLE kITThe SER-Ck provides connectivity between a D-Sub 9 male connector and the RJ-11 connector on the XPL. It includes an adapter that plugs into the COM1 (or other)port of a PC and uses common modular cable to connect to the XPL. The connections are shown in the diagram below.Don’t forget to order a Serial Cable kit SER-Ck when placing your order for an XPL!For Serial-multi-drop you’ll need an Serial Cable Kit SER-CK plus CANopen network cables to connect the drives as shown. The XPL-NC-01 and XPL-NC-10 are 1 ft (0.3m) and 10 ft (3m) cables that will do the job.These connections MUST be made to enable the Xenus.Xenus PlusSTO (Safe Torque Off)Override ConnectionsdescriptionThe XPL has a safety feature that is designed to provide the Safe Torque Off (STO) function as defined in IEC 61800-5-2. Two opto-couplers are provided which, when de-energized, prevent the upper and lower devices in the PWM outputs from being operated by the digital control core. Thisprovides a positive OFF capability that cannot be overridden by the control firmware, or associated hardware components. When the opto-couplers are activated (current is flowing in the input diodes), the control core will be able to control the on/off state of the PWM outputs.SAFE TORQUE OFF (STO)FUNCTIONAL DIAGRAMIn order for the PWM outputs of the Xenus Plus to be activated, current must be flowing through both opto-couplers that are connected to the ENH and ENL terminals of J5, and the drive must be in an ENABLED state. The LED outputs on J5 connect an opto-coupler to an external LED and will conduct current through the LED to light it whenever the PWM outputs can be activated, or the drive is in a diagnostic state. When the LED opto-coupler is OFF , the drive is in a Safe state and the PWM outputs cannot be activated to drive a motor .STO OVERRIDEThe diagram below shows connections that will energize both ENH and ENL opto-couplers.When this is done the STO feature is defeated and control of the output PWM stage is under control of the digital control core. If not using the STO feature, these connections must be made in order for the Xenus to be enabled.sto connectorFUNCTIONAL DIAGRAMpin SIGNAL pin SIGNAL 1Frame Gnd 6Enable LED(+)2Safe Enable HI(+)7Enable LED(-)3Safe Enable HI(-)824 Vdc Common 4Safe Enable LO(+)9+24 Vdc Input5Safe Enable LO(-)J5 SIGNALSJ51695SAFETYCOMMAND INPUTSDIGITAL POSITIONDigital position commands can be in either single-ended or differential format. Single-ended signals should be sourced from devices with active pull-up and pull-down to take advantage of the high-speed inputs. Differential inputs have 121 Ω line-terminators.DIGITAL TORQUE, VELOCITyDigital torque or velocity commands can be in either single-ended or differential format. Single-ended signals must be sourced from devices with active pull-up and pull-down to take advantage of the high-speed inputs.SINGLE-ENDED PWM & DIRECTIONSINGLE-ENDED 50% PWMDIFFERENTIAL 50% PWMDIFFERENTIAL PWM & DIRECTIONSINGLE-ENDED PULSE & DIRECTIONSINGLE-ENDED CU/CDCU (Count-Up)CD (Count-Down)QUAD A/B ENCODER SINGLE-ENDEDEncoder ph. BEncoder ph. ADIFFERENTIAL CU/CDDIFFERENTIAL PULSE & DIRECTIONQUAD A/B ENCODER DIFFERENTIALEncoder ph. AEncoder ph. BDuty = 0~100%Duty = 50% ±50%<no connection>This port consists of three differential input/output channels that take their functions from the Basic Setup of the drive.With quad A/B encoder feedback, the port works as an output, buffering the signals from the encoder . With resolver or sin/cos encoder versions, the feedback is converted to “emulated” quad A/B/X signals with programmable resolution. These signals can then be fed back to an external motion controller that closes the position or velocity loops. As an input, the port can take quad A/B signals to produce a dual-loop position control system or use the signals as master-encoder commands in camming mode. In addition, the port can takestepper command signals (CU/CD or Pulse/Direction) in differential format.Secondary Encoder Input Input/Output Select AS BUFFERED OUTPUTS FROM A DIGITAL QUADRATURE PRIMARy ENCODERWhen using a digital quadrature feedback encoder , the A/B/X signals drive the multi-mode port output buffers directly. This is useful in systems that use external controllers that also need the motor feedback encoder signals because these now come from J8, the Control connector . In addition to eliminating “y” cabling where the motor feedback cable has to split to connect to both controller and motor , the buffered outputs reduce loading on the feedback cable that could occur if the motor encoder had to drive two differential inputs in parallel, each with it’s own 121 ohm terminating resistor .Secondary Encoder InputInput/Output Selector resolverAS EMULATED QUAD A/B/X ENCODER OUTPUTS FROM AN ANALOG SIN/COS FEEDBACk ENCODERAnalog sin/cos signals are interpolated in the drive with programmable resolution. The incremental position data is then converted back into digital quadrature format which drives the multi-mode port output buffers. Some analog encoders also produce a digital index pulse which is connected directly to the port’s output buffer . The result is digital quadrature A/B/X signals thatcan be used as feedback to an external control system.Input/Output SelectAS A MASTER OR CAMMING ENCODER INPUT FROM A DIGITAL QUADRATURE ENCODERWhen operating in position mode the multi-mode port can accept digital command signals from external encoders. These can be used to drive cam tables, or as master-encoder signals when operating in a master/slave configuration.AS DIGITAL COMMAND INPUTS IN PULSE/DIRECTION,PULSE-UP/PULSE-DOWN, ORDIGITAL QUADRATURE ENCODER FORMATThe multi-mode port can also be used when digital command signals are in a differential format. These are the signals that typically go to single-ended inputs. But, at higher frequencies these are likely to be differential signals inwhich case the multi-mode port can be used.Input/Output SelectMULTI-MODE ENCODER PORTAS COMMAND INPUTSAS AN OUTPUT FOR FEEDBACk SIGNALS TO AN EXTERNAL CONTROLLERINPUTSDIGITAL INPUTS [IN3~6]These inputs have all the programmable functions of the GP inputs plus these additional functions on [IN8] & [IN9] which can be configured as single-ended or differential:• PWM 50%, PWM & Direction for Velocity or Current modes• Pulse/Direction, CU/CD, or A/B Quad encoder inputs for Position or Camming modesDIFFERENTIAL SINGLE-ENDED 12 Vdc max12 Vdc maxNON-ISOLATED DIGITAL INPUTSInputs [IN1~2] are 24V tolerantThese are high-speed types with pull-up resistors to +5 Vdc and 1 µs RC filters when driven by active sources. The active level is programmable on each input. Input [IN1] is dedicated to the drive enable function. The remaining inputs [IN2~IN14] have programmable functions.HS Inputs [IN1~2]24 Vdc maxPLC outputs are frequently current-sourcing from 24V for driving grounded loads. PC based digital controllers commonly use NPN or current-sinking outputs. Set the Xenus inputs to pull-down to ground for current-sourcing connections, and to pull-up to 5V for current-sinking connections.+J8 ControlANALOG INPUTSTwo differential analog inputs with ±10 Vdc range have programmable functions. As a reference input [AIN1] can take position/velocity/torque commands from a controller . A second input [AIN2] is programmable for other functions. The ratio of drive output current or velocity vs. reference input voltage is programmable.J8J924V GND24VOPTO-ISOLATED DIGITAL INPUTSThese inputs have all the programmable functions of the GP inputs plus opto-isolation. There are two groups of four inputs, each with its’ own common terminal. Grounding the common terminal configures the inputs to work with current-sourcing outputs from controllers like PLC’s. When the common terminal is connected to +24V , then the inputs will be activated by current-sinking devices such as NPN transistors or N-channel MOSFETs. The minimum ON threshold of the inputs is ±15 Vdc.J924V GND24V[IN11~14][IN7~10]±30 Vdc max±30 Vdc maxInputs [7~14] work with current-sourcing OR current-sinking connections. Connect the COMM to controller ground/common for current-sourcing connections and to 5~24V from the controller for current-sinking connections.J9DIGITAL OUTPUTS [OUT1], [OUT2]These are open-drain MOSFETs with 1 k Ω pull-up resistors in series with a diode to +5 Vdc. They can sink up to 1 Adc from external loads operating from power supplies to +30 Vdc. The output functions are programmable. The active state of the outputs is programmable to be on or off. When driving inductive loads such as a relay, an external fly-back diode is required.The internal diode in the output is for driving PLC inputs that are opto-isolated and connected to +24 Vdc. The diode prevents conductionfrom +24 Vdc through the 1 k Ω resistor to +5 Vdc in the drive. This could turn the PLC input on, giving a false indication of the drive output state.OUTPUTSANALOG OUTPUTThe analog output is programmable and has an output voltage range of ±5 Vdc. An op-amp buffers the output of a 12-bit D/A converter .HIGH SPEED OUTPUT [OUT3]5V CMOSOPTO-ISOLATED OUTPUTS [OUT4,5]30 Vdc maxZener clamping diodes across outputs allow driving of resistive-inductive (R-L) loads without external flyback diodes.J8BRAkE OUTPUT [OUT6]This output is an open-drain MOSFET with an internal flyback diode connected to the +24 Vdc input. It can sink up to 1A from a motor brake connected to the +24 Vdc supply. The operation of the brake is programmable with CME 2. It can also be programmed as a general-purpose digital output.+J4QUAD A/B ENCODER WITH FAULT PROTECTIONEncoders with differential line-driver outputs provide incremental position feedback via the A/B signals and the optional index signal (X) gives a once per revolution position mark. The MAX3097 receiver has differential inputs with fault protections for the following conditions:Short-circuits line-line: This produces a near-zero voltage between A & /A which is below the differential fault threshold.Open-circuit condition: The 121Ω terminator resistor will pull the inputs together if either side (or both) is open. This will produce the same fault condition as a short-circuit across the inputs.Low differential voltage detection: This is possible with very long cable runs and a fault will occur if the differential input voltage is < 200mV .±15kV ESD protection: The 3097E has protection against high-voltage discharges using the Human Body Model.Extended common-mode range: A fault occurs if the input common-mode voltage isoutside of the range of -10V to +13.2VANALOG SIN/COS INCREMENTAL ENCODERThe sin/cos/index inputs are differential with 121 Ω terminating resistors and accept 1 Vp-p signals in the format used by incremental encoders with analog outputs, or with ServoTube motors.EncoderRESOLVER (-R MODELS)Connections to the resolver should be made with shielded cable that uses three twisted-pairs. Once connected, resolver set up, motor phasing, and other commissioning adjustments are made with CME 2 software. There are no hardwareadjustments.Motor connectionsMotor connections are of three types: phase, feedback, and thermal sensor . The phase connections carry the drive output currents that drive the motor to produce motion. A thermal sensor that indicates motor overtemperature is used to shut down the drive to protect the motor . Feedback can be digital quad A/B encoder , analog sin/cos encoder , resolver or digital Halls, depending on the version of the drive.SSI ABSOLUTE ENCODERThe SSI (Synchronous Serial Interface) is an interface used to connect an absolute position encoder to a motion controller or control system. The XPL drive provides a train of clock signals in differential format to the encoder which initiates the transmission of the position data on the subsequent clock pulses. The polling of the encoder data occurs at the current loop frequency (16 kHz). The number of encoder data bits and counts per motor revolution are programmable. The hardware bus consists of two signals: SCLk and SDATA. Data is sent in 8 bit bytes, LSB first. The SCLk signal is only active during transfers. Data is clocked out on the falling edge and clock in on the rising edge of the Master .ENDAT ABSOLUTE ENCODERThe EnDat interface is a Heidenhain interface that is similar to SSI in the use of clock and data signals, but which also supports analog sin/cos channels from the same encoder . The number of position data bits is programmable as is the use of sin/cos channels. Use of sin/cos incremental signals is optionalin the EnDat specification.B i SS ABSOLUTE ENCODERBiSS is an - Open Source - digital interface for sensors and actuators. BiSS refers to principles of well known industrial standards for Serial Synchronous Interfaces like SSI, AS-Interface® and Interbus® with additional options.Serial Synchronous Data Communication Cyclic at high speed 2 unidirectional lines Clock and Data Line delay compensation for high speed data transfer Request for data generation at slaves Safety capable: CRC, Errors, Warnings Bus capability incl. actuators Bidirectional BiSS B-protocol: Mode choice at each cycle start BiSS C-protocol: Continuous modeNIkON-A ABSOLUTE ENCODERThe Nikon A interface is a serial, half-duplex type that iselectrically the same as RS-485BiSSNikon-AXenus。
托希巴调速电机驱动器应用指南说明书

G9APPLICATION GUIDELINE 8.1Auto TuneIntroductionAuto Tune is a function in the drive that calculates and measures the motor constants used to define the motor model while in the Auto Torque Boost, Sensorless Vector, or Sensored Vector control mode (V/f Pattern).While the differences may be minor, the motor constant settings in the G9/H9 differ from the 7-series.In lieu of manually calculating the motor constants of your motor, the drive provides you the option to have it calculate the constants for you. This is the recommended method when the motor data provided is limited to Capacity, Current, and RPM.Programming*Must have the motor connected to the drive. NotesTo use auto tune, you will need to provide the:•Motor’s Base Frequency (Hz)•Motor’s Base Frequency Voltage (VAC)•Motor’s Rated Capacity (kW)•Motor’s Rated Current (A)•Motor’s Rated RPM (RPM)Table 1 shows the items that need to be set for proper auto tune operation. If you did not use the Setup Wizard when starting your drive you can manually enter the information through the Direct Access menu in Programming.F014 – Defines the base frequency at which the motor is rated for. This can be found on the motor nameplate.F409 – Defines the voltage at which the motor is rated at its base frequency. This can be found on the motor nameplate.F402 – Adds a thermal component to the motor model. You can select a motor that is self-cooled (ODP, TEFC), one that has a blower attached to it providing constant air flow regardless of rotor speed, or you can leave the compensation OFF.F405 – Defines the kW capacity of the motor. This can be found on the motor nameplate.F406 – Defines the full load current of the motor at base voltage and frequency. This can be found on the motor nameplate.F407 – Defines the rated rotor RPM at full load current, base voltage, and base frequency.F400 – Enables Auto tune 1.0: Auto Tune Disabled1: Reset Motor Defaults2: Enable Auto tune on RUN command3: Auto Tuning by input terminal signal4: Motor constant auto calculationYou should enter all the information in all the previously listed parameters. Then enter a “4” in F400. This instantaneously auto updates parameters F410 – F413 according to the items set previously and resets F400 to “0”. Now set F400 to “2”. The next time the drive is ran, the drive sends a pulse to the motor and measures its feedback adjusting F410 and F412 as necessary. It will then set F400 back to “0”. Auto tune is now complete.。
Copley产品选型样本Nov. 2009

Stepnet
步进 VAC, VDC
2-10 A E
Accelus
无刷/有刷 20-180 VDC
3-12 A E
Junus
有刷 20-180 VDC
5-15 A V
•
•
•
•
•
•
•
•
•
•
•
•
•
•
码器, V=反电动势
适应恶劣环境的驱动器
R系列高规格驱动器包含了 Xenus 和 Accelnet两个版本。驱动器 设计耐温范围更宽,防潮,抗震,抗冲击性能更强。主要用于COTS 军工,航海,航空,是由提炼及车辆系统。
Xel
VAC Ic Ip
XTL-230-18 100-240 6
18
XTL-230-36
100-240 12
36
XTL-230-40
100-240 20
40
XSJ
Micro Panel
控制模式 • Indexer, 点到点, PVT • 电子凸轮, 电子齿轮 • 位置, 速度, 力矩 命令接口 • CANopen/DeviceNet • ASCII 和离散 I/O • 步进脉冲命令 • ±10V 位置/速度/力矩命令 • PWM 速度/力矩命令 • 主编码器 [电子齿轮/凸轮] 通讯 • CANopen/DeviceNet • RS-232 附件 • 外置再生电阻器 • 外置边缘滤波器
旋转变压器
旋转变压器通常用于恶劣工作环境。Xenus 和 Accelnet系 列驱动可选配此接口。Copley驱动器对旋变提供14位的分辨 率,接收速度高达10,000 rpm.
绝对值编码器
Copley 驱动器可提供市场上多家标准的开放型绝对值编码器 接口。包括 EnDat, BiSS, Hiperface 和 SSI.
Copley驱动器用户的指南

Copley驱动器总结一、驱动器简介-S和-R版本可以从模拟正弦/余弦编码器和无刷解析器中模拟出正交编码器的输出信号,我们的驱动器是XTL-230-40,输入标准版本,支持正交编码器。
驱动器可以以以下几种方式进行操作:1.作为一个传统的电机驱动器,接受外部控制器发出的电流,速度和位置信号。
在电流和速度模式下,可以接受正负10V的模拟信号;占空比50%的PWM波,或者PWM/极性输入。
在位置模式下,输入可以是从步进电机控制器发出的位置增量命令(以脉冲方向格式或者递增递减计数格式)或者是从主编码器输出的A/B正交指令。
2.作为CANopen网络的一个网点。
3.作为DeviceNET网络的一个网点。
4.作为一个独立的控制器运行虚拟机上的程序,或者通过RS232串口运行ASCII码格式的指令。
另外还需要一个独立的+24V电源给内部控制电路供电,这个电源跟主电源隔离开来。
这个设计保证了主电源断开,+24v电源不断开的时候,驱动器能保留位置信息和通信。
CME2CME2是对驱动器进行配置和调试的软件,通过RS232串口连接电脑和驱动器。
所有的配置驱动器的操作都可以通过这个软件完成。
电机数据存储为.CCM文件,驱动器数据存储为.CCX 文件。
二、驱动器操作供电和接地图电源交流电压经过整流滤波输出直流驱动PWM逆变器。
+24V电源经过一个DC/DC变换器,产生控制电路所需的电压和一个+5V电源给HALL电路和编码器供电。
操作模式控制环的嵌套和模式驱动器可以使用最多三个嵌套的控制环,电流环、速度环、位置环在三种相关联的模式下控制电机控制环图解在位置模式下,驱动器用到了三个环。
如上图所示,位置环驱动速度环,速度环驱动电流环。
在速度模式下,速度环驱动电流环,在电流模式下,电流环直接由外部或内部的电流指令驱动。
环路基本属性这些环路和一般的伺服控制环路有一些相同的属性环路属性描述命令输入每个环路给定一个需要达到的值。
例如,速度环接受一个速度指令,它是期望的电动机速度限制每个环路上都有限制,以保护电机或者机械系统反馈伺服控制环接受反馈。
罗赫高压电源驱动器BM61M41RFV-C评估板说明书
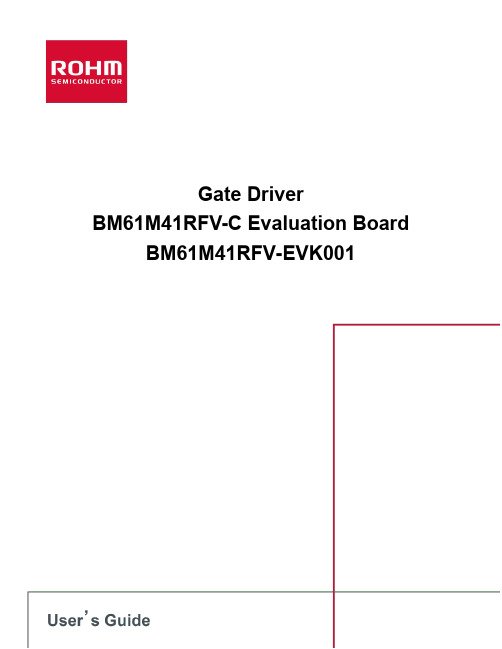
During Use
[5] Be careful to not allow conductive objects to come into contact with the board. [6] Brief accidental contact or even bringing your hand close to the board may result in
Bill of Materials Device
Parts Number
Gate Driver
U1
C11 Input Capacitor
C14
Input signal filter
R12, R13 C12, C13
C21 Output Capacitor
C22
R21
Gate
R22
Test pin Spacer
2/7
2019.10
BM61M41RFV-EVK001
User’s Guide
Schematics R12, R13, R21 and R22 are implemented interim resisters for shipment check.பைடு நூலகம்Please replace each resister which can work with Power Device or input device appropriately.
depending on the circumstances, explosion or other permanent damages. [8] Be sure to wear insulated gloves when handling is required during operation.
cople电机资料

Hygienic ServoTube 38 INSTALLATION GUIDEPublication Ref: UM03018/BCopley Motion Systems LLCWollaston Way, Burnt Mills, Basildon, Essex SS13 1DJ EnglandTel: +44 (0)1268 287070 Fax +44 (0)1268 928372Copley Motion SystemsA Subsidiary of Analogic Corp.WARRANTYCopley Motion Systems guarantees its equipment against faulty components for a period of twelve months from delivery. Replacement components will be free of charge. Copley Motion Systems shall not in any event be liable for consequential damage or loss.Copley Motion Systems operates a customer care facility and all requests for repair and replacement should be directed to the Customer Care Department. The serial number of the equipment should be quoted in any communications. The right to change specification and price is reserved by Copley Motion Systems.DISCLAIMERCopley Motion Systems makes no guarantees of any kind with regard to this manual. Copley Motion Systems shall not be liable for errors contained herein or for consequential or incidental damages incurred as a result of acting on information contained in the manual.CUSTOMER CAREFor enquiries relating to the operation and use of the Hygienic ServoTube described in this Manual please contact the Customer Care Helpdesk, Telephone : +44 (0)1268 287070.Copley Motion Systems LLCWollaston Way, Burnt Mills, Basildon, Essex, SS13 1DJ EnglandTel: +44 (0)1268 287070 Fax: +44 (0)1268 928372(c) Copley Motion Systems 2010Page (ii)Hygienic ServoTube 38INSTALLATION GUIDEContentsPreliminary pagesTitle page (i)Copyright notice / disclaimer (ii)Contents list (this page) (iii)Warnings (iv)Cautions (v)Reader’s Notes (vi)Abbreviations (vii)Chapters1 Overview (1)2 Installation (3)3 Maintenance (9)4 Service (13)AppendicesA Glossary of terms & Abbreviations (17)B Trouble Shooting (19)C Technical Specification (20)Page (iii)Page (iv)WARNINGSWarning symbols and meaningsIn this User Manual warning symbols are used. These are intended to alert you to the potential hazards to personnel which are associated with the equipment described, in all aspects of use, including handling, installation, operation and maintenance.Heart pacemakers. Personnel fitted with pacemakers must not handle or work on this equipment.Strong magnets. The thrust rod contains powerful magnets and will strongly attract ferrous objects. Damage can occur to computer disks and credit cards.Electric shock. Potentially lethal voltages may be present during the commissioning and servicing of this equipment. Isolate and disconnect all sources of electrical supply before working on the equipment. Particular care needs to be taken when working on or around motor phase connections.Hot surface. Surface temperatures of up to 80 °C can be present during the commissioning and servicing of this equipment. Allow the forcer and thrust rod to cool before working on the equipment.Crush hazard. The forcer may move unexpectedly. Always isolate all sources of electrical supply before working on the equipment.General hazard. Follow the advice given.Electrical safetyThis equipment must be earthed.EMC precautionsThis equipment is intended for use in a light industrial environment. It is recommended that the following precautions be observed during installation:Keep all cable lengths to a minimum.Provide as much physical separation as possible between power and signal cables. In particular, avoid long, parallel runs of cables.Maintain screen continuity throughout the cable run.Use 360 degree screen terminations where possible. “Pig-tail” terminations are not recommended.It is the responsibility of the User to ensure compliance with any local electrical and EMC regulations in force atthe time of installation.READER’S NOTESGENERALThis manual describes the Installation, Maintenance and Spares of the Hygienic ServoTube 38 linear motor.ASSOCIATED PUBLICATIONSThe following publications are associated with the Hygienic ServoTube 38 Installation Guide.Title Reference NumberXHA38 Data sheet DS01102XHB38 Data sheet DS01103Xenus User Guide-Xenus Data Sheet-Xenus Micro Panel User Guide-Xenus Micro Panel Data sheet-Page (v)Page (vi)Chapter 1 Product OverviewHYGIENIC SERVOTUBE 38 ACTUATORThe Hygienic ServoTube is a stainless steel, water-cooled, 600V version of the XTA38 actuator. A single model is available, delivering peak force up to 744 N. With smooth surfaces and IP69K high-pressure wash-down rating, Servotube is ideal for material handling applications in the Packaging, Food & Beverage and Pharmaceutical industries.The IP69K rating of Hygienic ServoTube facilitates high-pressure wash-down techniques which use significantly less water and cleansing agents than typical low-pressure hose-down. The cleaning process itself is easier and quicker. Cost is reduced and there is less environmental impact.The ruggedness and mechanical simplicity of Hygienic ServoTube can bring significant cost savings to sterile environment applications. Simply mount the forcer directly to the machine. The food-safe dry bearings of the moving-rod actuator deliver quiet, long life and are conveniently field replaceable.Hygienic ServoTube features a standard incremental encoder output and digital Halls. The encoder delivers 10 micron resolution with 25 micron repeatability. The drive power interface is three phase and can operate at 600V. While drive connectivity and configuration is simplest with Copley drives, it is possible to use any third party drive with Hygienic ServoTube.HYGIENIC SERVOTUBE 38 COMPONENTThe Hygienic ServoTube is a stainless steel, water-cooled, 600V version of the XTB38 component. A single model is available, delivering peak forces up to 1860 N. With smooth surfaces and IP69K high-pressure wash-down rating, Servotube is ideal for material handling applications in the Packaging, Food & Beverage and Pharmaceutical industries.The IP69K rating of Hygienic ServoTube facilitates high-pressure wash-down techniques which use significantly less water and cleansing agents than typical low-pressure hose-down. The cleaning process itself is easier and quicker. Cost is reduced and there is less environmental impact.The ruggedness and mechanical simplicity of Hygienic ServoTube can bring significant cost savings to sterile environment applications. Simply mount the load directly to the forcer.Typically supported by a single bearing rail. The thrust rod is mounted at both ends, similar to a ballscrew. Alarge air gap reduces alignment constraints.Page 7Hygienic ServoTube 38 Installation GuidePage 8Chapter 1OverviewHygienic ServoTube 38 Installation GuidePage 9Chapter 2InstallationChapter 2InstallationUNPACKINGCheck packaging for signs of damage.Metal surfaces may be hot or below 0o C following prolonged storage.Remove the packaging. Do not discard. In the event of items requiring return, it is recommended that the original packaging be used.Ensure that the delivery note correctly reflects your order and the items delivered.Check the equipment for signs of damage. Never use the equipment if it appears damaged in any way.Read the Installation Guide before installing and using this equipment.INSTALLATIONIntended operating environmentThis equipment is intended for use in an environment within the following conditions:••••••Hygienic ServoTube 38 Installation GuideChapter 2InstallationPage 10Mechanical - XHAThe outline drawing of the XHA is shown in Figure 2.1. It comprises the forcer with integrated plastic bearings and the thrust rod. The integrated bearings act as a guide for the moving thrust rod. It is not intended to withstand side loading. If side loading is expected then it is advised that an external bearing is fitted.The XHA forcer can be mounted by using the M5 threaded fixings on the forcer body (8 off on each of two sides).The thrust rod has M10 male and female connections at each end. These are intended to interface to a number of standard accessories. CAUTIONAlways use a 28 mm AF spanner on the flats on the thrust rod before applying torque to the fixing. Failure to do so could result in damage to the thrust rod.The recommended tightening torque for the fixings are:M5, 2 - 10 Nm; M10 15 - 80 Nm (both non-lubricated i.e. no thread lock).Table 2.1 Thrust rod detailsStroke mm38043810OverallActive Overall Active 5542136263557591457398671611127493434706646162528469742681198564505778718233599540813753269636576849789305671612885825340706647920860Hygienic ServoTube 38 Installation GuideChapter 2InstallationFigure 2.1 XHA3804 outline drawings and mounting details;+$ +<*,(1,& :$7(5 &22/(' )25&(5 ,167$//$7,21 ',0(16,216Hygienic ServoTube 38 Installation GuideChapter 2InstallationMechanical - XHBThe outline drawing of the XHB is shown in Figure 2.2. It comprises the forcer and the thrust rod. With the addition of thrust rod supports and a linear bearing, a moving forcer solution can be implemented.Mounting holes are provided on the forcer body that are tapped M5. Dimensional details are shown in Figure 2.2. The recommended tightening torque for the fixings are:M5 bearing to forcer 2 - 10 NmAll torque figures are non-lubricated i.e. no thread lock.As the XHB has a moving forcer it is supplied with highly flexible cables suitable for continuous flexing operation In order to achieve the best reliability and life from these cables it is advised that some form of cable management system is used. Typically, this will be an energy chain mounted parallel to the direction of motion. Always follow the manufacturers recommendations when installing cables into energy chains. In particular:Observe cable minimum bend radius requirements (see Appendices).Never allow the cable to be under tension within the energy chain.Physically separate cables within the energy chain to prevent premature failure due to abrasion.Never cross cables within the energy chain.Be careful to prevent the cable from twisting or becoming kinked during installation into the energy chain.•••••Hygienic ServoTube 38 Installation GuideChapter 2InstallationFigure 2.2 XHB outline drawings and mounting details;+% +<*,(1,& :$7(5 &22/(' )25&(5 ,167$//$7,21 ',0(16,216$// ',0(16,216 ,1 00127( 0 7$33(' +2/(6 ($&+ (1' 127 5(&200(1'(' )25 02817,1* 127( [ ($&+ (1' 127 5(&200(1'(' )25 02817,1* 127( 72/(5$1&( $5281' 6:$*(' $5($ 0$< 9$5<Hygienic ServoTube 38 Installation GuideChapter 2InstallationElectricalAll electrical connections to the XHA and XHB are made via two cables, see Figure 2.3. One carries power to the forcer and the other carries signals from the position sensor. These cables are supplied either pre-terminated for a specific drive or with flying leads. Where they are pre-terminated, simply plug the cables into the relevant connectors on the drive.FORCER POWER CONNECTOR REFERENCE POSITION SENSOR CONNECTOR REFERENCEAMPLIFIER J2J8Copley Xenus J2J6Copley Xenus Micro PanelWARNINGTHE THRUST ROD ON BOTH XHA AND XHB MUST BE EARTHED. THIS CAN BE ACHIEVED BY EARTHING THE CONNECTED MECHANICAL PARTS ON THE USER’S MACHINE.Figure 2.3 - Schematic showing connection of XHA / XHB to the Xenus AmplifiersXENUS XTLXENUS MICRO PANEL XSJHYGIENIC SERVOTUBE 38HYGIENIC SERVOTUBE 38Hygienic ServoTube 38 Installation GuideChapter 3MaintenanceChapter 3MaintenanceWARNINGISOLATE AND DISCONNECT ALL SOURCES OF ELECTRICAL SUPPLY BEFORE WORKING ONTHE EQUIPMENT.PREVENTATIVEXHAThe XHA is low maintenance and as such requires only minimal periodic inspection.The integral bearing is dry running, requiring no lubrication.Periodically:Check that the thrust rod can move freely over the entire stroke.Clean any accumulated debris from the thrust rod surface (ferrous material, in particular, can beattracted to the thrust rod surface).Check all fixings are tight and secure.XHBThe XHB is low maintenance and as such requires only minimal periodic inspection.Where an external linear bearing is used, please consult the bearing manufacturer for recommendations on lubrication types and lubrication intervals.Periodically:Check that the forcer can move freely over the entire stroke.Clean any accumulated debris from the thrust rod surface (ferrous material, in particular, can be attracted to the thrust rod surface).Check all fixings are tight and secure.Check all flexing cables for signs of wear or damage.•••••••Hygienic ServoTube 38 Installation GuideChapter 3MaintenanceCORRECTIVE MAINTENANCECABLE REPLACEMENTIt is recommended that cable replacement is carried out by the equipment supplier. However, if the user wishes to carry out cable replacement the following procedure should be used.This procedure applies to both XHA and XHB versions.There are two replaceable cables that can be replaced independently.Power Cable RemovalUsing a 7mm AF spanner or similar, undo the six M4 fixings holding on the terminal box lid and remove along with the spring washers, see Figure ing a flat blade screwdriver release the three power conductors from the spring-loaded terminal ing a Pozidrive screwdriver undo the M3 screw holding the safety earth conductor to the forcer body. Remove the screw and the shakeproof ing a 19mm AF spanner or similar, undo the cable gland nut completely before withdrawing the cable assembly from the terminal box.ReplacementPass the new cable through the entry on the terminal box. Hand tighten the cable gland nut.Using a 19 mm AF spanner or similar, tighten the cable gland nut until there is no gap between it and the forcer ing a Pozidriver screwdriver, connect the safely earth conductor to the forcer body using the M3 screw and shakeproof washer. The shakeproof washer must be between the forcer body and the crimped ing a flat blade screwdriver, release the sprung loaded contacts in the terminal block and reconnect the three power conductors.•••••••• EARTH TERMINAL CABLE POWER SENSOR PL1 SCREW BLOCK GLAND NUT CABLE CABLEFigure 3.1Hygienic ServoTube 38 Installation GuideChapter 3MaintenanceReplace the terminal box lid. Using a 7 mm AF spanner or similar, secure the lid using the six M4 fixings and spring washers.Sensor Cable RemovalUsing a 7mm AF spanner or similar, undo the six M4 fixings that secure the terminal box lid, and remove along with the spring washers.Unplug the sensor cable connector from PL1 on the PCB.Using a 19mm AF spanner or similar, undo the cable gland nut completely before withdrawing the cable assembly from the terminal box.ReplacementPass the new cable through the entry on the terminal box. Hand tighten the cable gland nut.Using a 19 mm AF spanner or similar, tighten the cable gland nut until there is no gap between it and the forcer housing.Plug the sensor cable connector into PL1 on the PCB.Replace the terminal box lid. Using a 7 mm AF spanner or similar, secure the lid using the six M4 fixings and spring washers.BEARING REPLACEMENTIt is recommended that bearing replacement is carried out by the equipment supplier. However, if the user wishes to carry out cable replacement the following procedure should be used.This procedure applies only to the XHA version.There are two replaceable bearings located at each end of the housing. Both bearings should be replaced at the same time, see Figure 3.2 and Figure 3.3.••••••••Figure 3.3Figure 3.2Hygienic ServoTube 38 Installation GuideChapter 3MaintenanceRemovalWithdraw the thrust rod away from the end containing the bearing to be replaced until the thrust rod disengages from the bearing. Do not remove the thrust rod ing a 5.5mm AF spanner or similar, undo the four M3 fixings and remove along with the spring washers, see Figure 3.4.Pull the bearing housing out of the forcer ing a 41 +/-0.5mm round bar and a press, gently push the bearing out of the housing, see Figure 3.5.ReplacementUsing a flat plate and a press, gently push the new bearing into the housing, see Figure 3.6.Push the bearing housing into the forcer end.Replace the four M3 fixings and spring washers and tighten to a torque of 2 Nm.Repeat the above procedure for the bearing at the opposite end.Note. The bearing housings are notinterchangeable and only fit on their respective forcer ends.••••••••HOUSINGFigure 3.4M3 FIXINGHygienic ServoTube 38 Installation Guide Chapter 4ServiceChapter 4ServiceSERVICEShould you need to return any items to Copley Motion Systems, before doing so, please call our Sales coordinator on +44 (0)1268 287070 or send a fax to +44 (0)1268 928372 in order to obtain an RMA (Returned Materials Authorisation) number. The RMA number should then be quoted on all items returned and quoted for all enquiries.Please note that when returning items it is recommended that the original packaging be used.SPARESThe available spares for the XHA and XHB are listed in Tables 4.1 and Table 4.2.Table 4.1 Cables avaialable: terminated forXenus, Xenus Micro Panel and with flying leadsTable 4.2 HardwareTo place an order for spare parts please telephone or fax your order to the Sales co-ordinator: Tel: +44 (0)1268 287070Chapter 4Hygienic ServoTube 38 Installation GuideServiceFax: +44 (0)1268 928372AppendicesCONTENTSAPPENDIX A - GLOSSARY OF TERMS & ABBREVIATIONSAPPENDIX B - TROUBLE SHOOTINGAPPENDIX C - TECHNICAL SPECIFICATIONAppendicesHygienic ServoTube 38 Installation GuideAppendix AGlossary of Terms & AbbreviationsGLOSSARY OF TERMSTERM DESCRIPTION OF TERMPeak force Peak force is the force produced when the peak current is applied to the motor. It is the product of Force constant (N/Apk) and Peak current (Apk).The motor is not moving, there is no forced cooling and no additional heat-sinking. The durationof the peak force is thermally limited and is therefore only allowable for a period of 1 second. Continuous stall force Continuous stall force is the force produced when the continuous current is applied to themotor.It is the product : Force constant (N/Apk) x Continuous stall current (Apk)or : Force constant (N/Arms) x Continuous stall current (Arms).The motor is not moving and there is no forced cooling.It is quoted with and without the addition of a 25 x 25 x 2.5 cm heatsink plate mounted withthermal grease to the mounting surface of the motor.Peak current Peak current is the current required to heat the motor phases to their maximum operatingtemperature when the ambient temperature is 25°C, the motor is not moving, there is no forcedcooling and no additional heat-sinking.It is the maximum allowable current before demagnetisation of the magnets occurs when themagnet temperature is 100°C.The duration of the peak current is thermally limited and is therefore only allowable for a periodof 1 second.Continuous stall current Continuous stall current is the current required to heat the motor phases to their maximumoperating temperature when the ambient temperature is 25°C, the motor is not moving andthere is no forced cooling.It is quoted with and without the addition of a 25 x 25 x 2.5 cm heatsink plate mounted withthermal grease to the mounting surface of the motor.Force constant Force constant is the peak force produced when 1 ampere (peak) flows into one phase and 0.5 ampere (peak) flows out of the remaining two phases (as in sinusoidal commutation) quotedin N/Apk. Alternatively, it is the peak force produced when 0.707 ampere (rms) flows into onephase and 0.353 ampere (rms) flows out of the remaining two phases (again as in sinusoidalcommutation) quoted in N/Arms.Back EMF Back EMF constant is the peak phase to phase voltage generated when the motor is travelling at a velocity of 1m/s.Fundamental motorconstant Fundamental motor constant is the continuous stall force divided by the square root of the power dissipated in the motor at that continuous stall force.Eddy current loss Eddy current loss is the amount of opposing force produced by the motor when it is travelling ata velocity of 1m/s.Sleeve clogging force Sleeve clogging force is the amount of force variation produced by having an iron sleeve. The variation is independant of motor current.Resistance Resistance is measured phase to phase at temperatures of 25°C and 100°C.Inductance Inductance is measured phase to phase at a frequency of 1 kHz. The actual value ofinductance varies as the motor position varies so it is the minimum value that is quoted.Hygienic ServoTube 38 Installation Guide AppendicesElectrical time constant Electrical time constant is the time taken for a step current input to the motor to reach 63.2% of its value.Continuous workingvoltage Continuous working voltage is the maximum allowable continuous voltage between any two motor phases or between any motor phase and the motor safety earth.Pole pitch Pole pitch is the distance in millimetres for one complete electrical cycle (between like magnetic poles).Power dissipation Power dissipation is the maximum power that can be dissipated by the motor when the motor phases are at their maximum operating temperature, the ambient temperature is 25°C, themotor is not moving and there is no forced cooling. It is quoted with and without the addition ofa 25 x 25 x 2.5cm heatsink plate mounted with thermal grease to the mounting surface of themotor.Maximum phasetemperature Maximum phase temperature is the maximum operating temperature for the motor phases. It is limited to provide a safe operating temperature for the magnets.Rthphase-houslng Rthphase-houslng is the temperature rise from the motor housing to the motor phases for an input power of 1 watt to the motor. The motor is not moving, there is no forced cooling and noadditional heatsinking.Rthhousing-ambient Rthhousing-ambient is the temperature rise from ambient temperature to the motor housing for an input power of 1 watt to the motor. The motor is not moving and there is no forced cooling.It is quoted with and without the addition of a 25 x 25 x 2.5cm heatsink plate mounted withthermal grease to the mounting surface of the motor.Thermal time constant Thermal time constant is the time taken for the motor phases to cool to 36.8% of the difference between motor phase and ambient temperatures when there is no current flowing, the motor isnot moving there is no forced cooling and no additional heatsinking.ABBREVIATIONSThe abbreviations used in this Guide are listed in the following table.Apk Ampere peak PCB Printed circuit boardArms Ampere root mean square PUR PolyurethaneAWG American Wire Gauge PVC Poly Vinyl ChlorideCOS cosine s secondd.c.direct current SIN sineEMC Electro-Magnetic Compatibility TYP TypicalEMF Electro-Motive Force UL Underwriters Laboratorykg kilogramme V Voltm metre Vpk Volt peakmA milliampere Vpk-pk Volt peak to peakmH millihenry Vrms Volt root mean squaremm millimetre W WattMTG Mounting °C degrees CelsiusN Newton mm micrometre (micron)PTC Positive Temperature CoefficientAppendix BTroubleshootingTROUBLESHOOTING CHARTCheck to see if the problem you are experiencing is listed in the chart below. If the problem cannot be solved with reference to this chart, contact the customer services department.Fault Possible cause ActionForcer/thrust rod fails to move and produces no force.1. Drive not powered.2. Forcer phase connections notmade.3. Forcer over-temperature sensornot connected.4. Forcer over-temperature.1. Apply power to drive.2. Check forcer phase connectionson drive.3. Check forcer over-temperaturesensor connections on drive.4. Allow forcer to cool.Forcer/thrust rod fails to move but does produce force.1. One or more motor phaseconnections not made or madeincorrectly.2. One or more position sensorconnections not made or madeincorrectly.3. Forcer/thrust rod mechanicallyblocked.1. Check forcer phase connectionson drive.2. Check position sensorconnections on drive.3. Check forcer/thrust rod is free tomove.Forcer/thrust rod moves but is jerky in motion.Incorrect pole pitch set up or phaseoffset between position sensor andforcer back emf.Check drive or controller set up.Forcer/thrust rod moves in wrong direction.One or more position sensor andforcer phase connections madeincorrectly.Check position sensor and forcerphase connections on drive.Hygienic ServoTube 38 Installation Guide AppendicesAppendix CTechnical DatasheetELECTRICAL SPECIFICATIONSNotes(1) S=series forcer phases, P=parallel forcer phases(2) Water at 25o C and flow rate of 80 litres/hour(3) Reduce continuous stall force to 89% at 40°C ambient.(4) Based on a moving thrust rod with 55 mm stroke and no payload (5) Based on a moving thrust rod with triangular move over maximum stroke and no payload.(6) Based on a moving forcer with typical bearings and no payload.(7) Based on a moving forcer with triangular move over maximum stroke and no payload.THERMAL SPECIFICATIONSMOTOR TYPE 3804 3810UnitsMaximum phase temperature 100o CWith water cooling optionPower dissipation @ 25o C ambient220357Watt0.060.07o C/WattThermal resistance Rthhousing-ambientThermal resistance R0.280.14o C/Wattthphase-housingWithout water cooling optionPower dissipation @ 25o C ambient 47.869.4WattThermal resistance R1.220.88o C/Wattthhousing-ambient0.350.20o C/WattThermal resistance Rthphase-housingMECHANICAL SPECIFICATIONSFORCER TYPE XHA 3804XHA 3810 XHB 3804XHB 3810Units Maximum stroke34013161103mmForcer mass(1) 6.511.7 6.111.3kgThrust rod mass/metre8.3kg/m Notes(1) XHA excluding thrust rod and cable. XHB excluding thrust rod and bearings.AppendicesHygienic ServoTube 38 Installation Guide POSITION SENSORThe position sensor comprises Hall effect sensors and incremental encoder. The Hall sensors output signals providing coarse position feedback for commutation. Shown below are relationships between forcer phase back EMF and Hall sensor outputs for one diection of motion (as shown by the arrows). It should be noted that each Hall output is always in phase with its respective forcer phase back EMF for the motion shown. For motion in the opposite direction each Hall output is inverted with relation to its respective forcer phase back EMF.Figure C.2 - Arrows indicate direction of motionThe Hall sensor outputs use 74AHCT125 line drivers.The incremental encoder outputs signals providing fine position feedback for forcer control. It is in the form of phase quadrature as shown below. The outputs use RS422/485 compatible line drivers.SPECIFICATION VALUE UNITSSupply voltage 5 ± 0.25 V d.c.Supply current (output current =0) 110 ± 20mAResolution 10micronPosition Repeatability (1)±20micronAbsolute Accuracy (2)±400 micronNotes(1) Dependent on amplifier. Under constant operating conditions. Self-heating of the forcer will cause expansion in the thrust rod during the initial warm up period. In high duty applications (corresponding to an internal forcer temperature of 80 o C) a1 metre thrust rod will expand typically by 250 microns.(2) Maximum error over 1 metre under constant operating conditions.FORCER OVER TEMPERATURE SENSORIt is strongly recommended that the forcer over-temperature sensor is connected to the drive amplifier or servo controller at all times in order to reduce the risk of damage to the forcer due to excessive temperatures. Protection is provided by three, positive temperature coefficient (PTC) thermistors embedded in the forcer phases. As the forcer phase temperature approaches 100°C, the PTC thermistors exhibit a sharp increase in electrical resistance. This change in resistance can be detected by circuitry within the drive amplifier or servo controller and used to reduce or disable the output of the drive amplifier in order to protect the forcer.。
Parker AC30驱动器用户指南说明书

Using PMAC motors with the AC30The AC30 drive can run both AC induction motors as well as permanent magnet AC motors (also known as brushless DC motors). The AC30 can run PMAC motors with and without feedback (Sensorless Vector Mode). Currently the AC30 supports incremental encoders and resolvers, with absolute encoders support coming in the future.The setup for a PMAC motor starts by selecting the CONTROL MODE, CONTROL STRATEGY, and CONTROL TYPE. Next you will want to populate all the PMAC MOTOR DATA for the PMAC motor that you are driving with the AC30. If you are using a Parker Motor you can use the Motor Wizard function in DSELite/DSE890 to auto-populate this data. If not most motor manufacturers will have this data published either on the motor nameplate, the motor catalog, the motor product manual, or some combination of the three. An auto-tune will need to be performed if BACK EMF CONSTANT KE, WINDING RESISTANCE, WINDING INDUCTANCE, and TORQUE CONSTANT KT are not known.When using Sensorless Vector Mode there are instances where the motor will have low torques at the low speeds. To remedy this, you can use the “PMAC SVC” function block. This function block allows the user to start the motor in an “Open Loop” mode by selecting the output current and ramp rate until a selected speed is hit. The drive will then switch back in to Sensorless Vector Mode. This function block is always where you will tune the Sensorless Vector Mode gains and low pass filter.When using a feedback device with a PMAC motor the POSTION FEEDBACK ALIGNMENT PROCEDURE is important for calculating the relative offset between the rotor and the stator. This procedure will involve giving the drive a run command to spin the shaft. If using a resolver this procedure would need to be done once, if using an incremental encoder this procedure will have to be done after every startup. Programming can be done to have this automatically start when the drive is powered up. This is important to consider if your application involves an incremental encoder.If you are using a feedback device you will need to begin the POSITION FEEDBACK ALIGNMENT PROCEDURE. To do this set the ALIGNMENT ENABLE parameter to TRUE and the ALIGNMENT METHOD parameter to AUTOMATIC, the other two parameters (ALIGNMENT LEVEL and ALIGNMENT RAMP TIME) will depend on how much you want the motor to rotate during this test. Next give the drive aSTART/RUN command. Once ALIGNMENT STATE has been set to ENDED you can stop the motor, if this parameter changes to ERROR check ALIGNMENT ERROR to see what cause the POS FBK ALIGNMENT errored.Once this process is complete you can begin tuning the drive and the motor to improve the response to changes.Attached is a flow chart of the steps to follow for setting up an AC30 with a PMAC motor for both Sensorless Vector mode and Closed Loop Vector mode.。
- 1、下载文档前请自行甄别文档内容的完整性,平台不提供额外的编辑、内容补充、找答案等附加服务。
- 2、"仅部分预览"的文档,不可在线预览部分如存在完整性等问题,可反馈申请退款(可完整预览的文档不适用该条件!)。
- 3、如文档侵犯您的权益,请联系客服反馈,我们会尽快为您处理(人工客服工作时间:9:00-18:30)。
Copley驱动器总结
一、驱动器简介
-S和-R版本可以从模拟正弦/余弦编码器和无刷解析器中模拟出正交编码器的输出信号,我们的驱动器是XTL-230-40,输入标准版本,支持正交编码器。
驱动器可以以以下几种方式进行操作:
1. 作为一个传统的电机驱动器,接受外部控制器发出的电流,速度和位置信号。
在电流和速度模式下,可以接受正负10V的模拟信号;占空比50%的PWM波,或者PWM/极性输入。
在位置模式下,输入可以是从步进电机控制器发出的位置增量命令(以脉冲方向格式或者递增递减计数格式)或者是从主编码器输出的A/B正交指令。
2. 作为CANopen网络的一个网点。
3. 作为DeviceNET网络的一个网点。
4. 作为一个独立的控制器运行虚拟机上的程序,或者通过RS232串口运行ASCII码格式的
指令。
另外还需要一个独立的+24V电源给内部控制电路供电,这个电源跟主电源隔离开来。
这个设计保证了主电源断开,+24v电源不断开的时候,驱动器能保留位置信息和通信。
CME2
CME2是对驱动器进行配置和调试的软件,通过RS232串口连接电脑和驱动器。
所有的配置驱动器的操作都可以通过这个软件完成。
电机数据存储为.CCM文件,驱动器数据存储为.CCX文件。
1。