粗苯的加氢精制
粗苯加氢

粗苯加氢焦化粗苯(混合芳烃)的精制最早是采用酸洗法,该法只能部分脱除粗苯中的含硫化合物(主要是噻吩)和杂质,在加工过程中芳烃化合物损失较大(8%一10%),其副产废物酸焦油和残渣尚无有效的治理方法,造成环境的污染。
随着有机化学工业的迅速发展,对苯系芳烃产品的质量要求很高,酸洗法得到的芳烃产品已无法满足需要,在发达国家该方法早已被淘汰。
二十世纪五十年代初期,美、英、德、法等国相继开发成功粗苯催化加氢精制法,所得苯的凝固点为5.2℃一5.4℃,噻吩质量分数为1×10-6—10×10-6,苯的品质还不是很高。
二十世纪六十年代,美国胡德利空气产品公司开发出一种高温的粗苯加氢精制法(Litol法)。
该方法反应温度为600℃-630℃。
Litol法除了加氢精制功能,还能将粗苯中的甲苯和二甲苯经催化脱烷基反应转化为苯,苯的质量分数达到99.9%,苯凝固点大于5.4℃,噻吩质量分数小于0.5×106 ,苯产品质量很高。
后来由于萃取蒸馏法的开发成功,采用较低温度(小于400℃)的粗苯加氢精制法,也能得到高质量的苯、甲苯和二甲苯。
目前国外粗苯加氢精制过程以反应温度区分有高温法(600℃一630℃)与低温法(320℃一380℃)二种。
Litol法(即高温法)反应温度与反应压力(6.0MPa)都很高,对设备、管道、仪表等的材质和质量要求很高,制造难度与投资极大,操作运转过程危险性相对较大,经济上不尽合理。
20世纪80年代上海宝钢引进Litol法建造了国内第一家粗苯加氢及精制工厂。
总投资4亿元人民币,其中专利使用费、工艺包、设计费1亿元人民币。
全套设备及催化剂为美国lummus 公司提供。
低温法加氢精制法主要包括三个关键单元:焦炉煤气变压吸附制纯氢(纯度大于99.9%);催化加氢精制过程(预加氢和主加氢);产品提纯过程(萃取或萃取蒸馏)。
低温法也能得到优质的苯、甲苯和二甲苯等产品,三种苯系芳烃收率为:苯98%、甲苯98%、二甲苯89%。
加氢法粗苯精制耗能少质量好
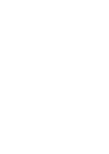
加氢法粗苯精制耗能少质量好焦化粗苯精制是煤化工的基础技术之一,粗苯通过进一步加工精制后,可以获得如纯苯、甲苯、二甲苯和重苯等多种产品。
由于近年来油价大幅上涨,与以石油为原料生产的石油苯相比,焦化苯有着很大的利润空间,因此粗苯精制产业引起了业界的广泛关注。
目前国内粗苯精制工艺主要有酸洗法和加氢法。
酸洗法投资少、见效快,生产装置易建设,国内大多数精苯生产装置采用该生产工艺。
但是,酸洗法工艺生产的苯纯度低,而且不能有效分离甲苯、二甲苯,生产过程中产生大量无法处理的酸焦油,严重污染环境,产品质量和产品收率低下,生产成本高,很难与大型精苯装置竞争,被国家明令禁止并限期取缔。
粗苯加氢精制技术则是通过催化加氢,脱除粗苯中含硫化合物及非芳香烃等物质,制取高质量苯族烃的技术。
催化加氢概括起来分为高温高压、中温中压和低温低压三种工艺。
应用较广泛的是LITOL法、加氢脱硫净化脱烷基工艺和莫非兰法加氢脱硫净化工艺。
粗苯加氢精制装置投资大、建设周期长,但是技术先进,生产的苯纯度高,与石油苯产品性能基本没有差异,能实现与甲苯、二甲苯等的有效分离,产品为纯苯、甲苯、二甲苯(包括邻二甲苯、间二甲苯和对二甲苯)、三甲苯和重苯等。
粗苯加氢精制工艺能耗低、成本低、产品质量好、竞争能力强,代表了粗苯加工精制的发展方向。
早在上世纪60年代发达国家已经淘汰了酸洗精制法,用加氢精制取代。
20世纪80年代,宝钢首次引进第一套Litol苯加氢装置生产纯苯,90年代石家庄焦化厂又引进第一套K-K技术苯加氢装置,生产纯苯、甲苯、二甲苯等产品。
目前我国宝钢、石家庄焦化厂共有4套粗苯加氢装置,产能约21万吨/年。
目前有实力的焦化企业或化工企业都在争取建设大型精苯装置。
《石家庄循环经济化工示范基地建设实施方案》中规划的石家庄焦化集团粗苯精制项目将采用具有国际先进水平的以N-甲酰吗啉为溶剂的粗苯加氢工艺技术,总投资1.7亿元,年生产粗苯精制10万吨。
山西省“十一五”期间,粗苯加工利用项目计划投资就达78亿元,并且禁止新建并逐步淘汰现有酸洗法苯精制装置和工艺,鼓励发展先进的粗苯加氢精制工艺。
粗苯精制

粗苯精制
按预处理方法不同,分酸洗法和加氢精制法
目前,国内的粗苯精制产能中,酸洗法占大多数,而所得焦化苯的质量只能定位于顺酐等低端产品市场,其生产销售亦受顺酐生产的制约,而且三苯的收率低,只能达到80%,生成废物酸焦油和残渣,尚无有效的治理方法,造成环境的污染严重。
粗苯催化加氢精制是通过加氢,部分脱除粗苯中所含的硫、氮及不饱和烃,再经萃取分离精制得高纯度纯苯、纯甲苯、二甲苯等产品。
加氢纯苯的纯度可高达99. 95%、二甲苯纯度可达99.8%,产品回收率高。
国产化的粗苯加氢精制流程如下:
加氢条件如下:预反应温度190℃,压力2. 9MPa,主反应温度280℃,压力2.7MPa。
如图4 所示,原料粗苯经脱重组分塔脱除重苯后,轻苯与循环氢混合,经连续蒸发进入加氢反应器,加氢反应为连续固定床气相加氢反应。
加氢过程产生的硫化氢及其他酸性气体从稳定塔顶排出。
加氢油经SED(环丁矾)三苯萃取蒸馏工艺,把非芳烃分离掉。
再经连续精馏得到产品苯、甲苯及混合二甲苯。
二甲苯中非芳烃的质量分数小于 2.5%。
由于设置了脱重组分塔,对组成变化大的原料适应性强,采用SED萃取精馏后,产品苯、甲苯的质量高,操作方便。
常用催化剂有Ni-Mo、Co-Mo、Ni- Cr等。
粗苯加氢精制工艺设计
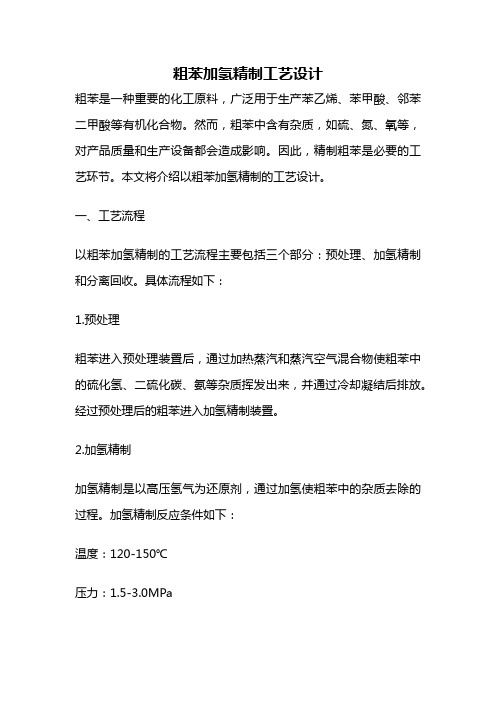
粗苯加氢精制工艺设计粗苯是一种重要的化工原料,广泛用于生产苯乙烯、苯甲酸、邻苯二甲酸等有机化合物。
然而,粗苯中含有杂质,如硫、氮、氧等,对产品质量和生产设备都会造成影响。
因此,精制粗苯是必要的工艺环节。
本文将介绍以粗苯加氢精制的工艺设计。
一、工艺流程以粗苯加氢精制的工艺流程主要包括三个部分:预处理、加氢精制和分离回收。
具体流程如下:1.预处理粗苯进入预处理装置后,通过加热蒸汽和蒸汽空气混合物使粗苯中的硫化氢、二硫化碳、氨等杂质挥发出来,并通过冷却凝结后排放。
经过预处理后的粗苯进入加氢精制装置。
2.加氢精制加氢精制是以高压氢气为还原剂,通过加氢使粗苯中的杂质去除的过程。
加氢精制反应条件如下:温度:120-150℃压力:1.5-3.0MPa氢油比:300-1000催化剂:铜、铝、钼、钴等金属催化剂在加氢精制过程中,杂质会被还原成硫化氢、氨等气体,通过气液分离器分离,然后通过洗涤器洗涤,最终得到精制苯。
3.分离回收精制苯通过分馏塔进行分馏,得到苯和轻杂质。
苯进入产品收集罐,轻杂质则通过冷却凝结后排放。
二、工艺特点以粗苯加氢精制的工艺具有以下特点:1.精制效果好加氢精制工艺可以有效地去除粗苯中的硫、氮、氧等杂质,使得精制后的苯产品纯度高、质量好。
2.操作简便加氢精制过程中,催化剂的选择和操作比较简单,不需要特别复杂的设备和技术。
3.节能环保加氢精制工艺是一种节能环保的工艺,不需要高温高压操作,可以减少能源消耗和环境污染。
4.适应性强加氢精制工艺适用于各类粗苯,不受原料质量的限制。
三、工艺优化为了进一步提高以粗苯加氢精制的工艺效率和产品质量,可以从以下几个方面进行优化:1.选择优质催化剂铜、铝、钼、钴等金属催化剂的选择会对加氢精制的效果产生影响,因此应根据不同原料的特性选择适合的催化剂。
2.控制反应条件反应温度、压力和氢油比的控制对于加氢精制的效果有着至关重要的影响。
应根据原料特性和产品要求,合理选择反应条件进行控制。
粗苯的加氢精制(精制甲类)
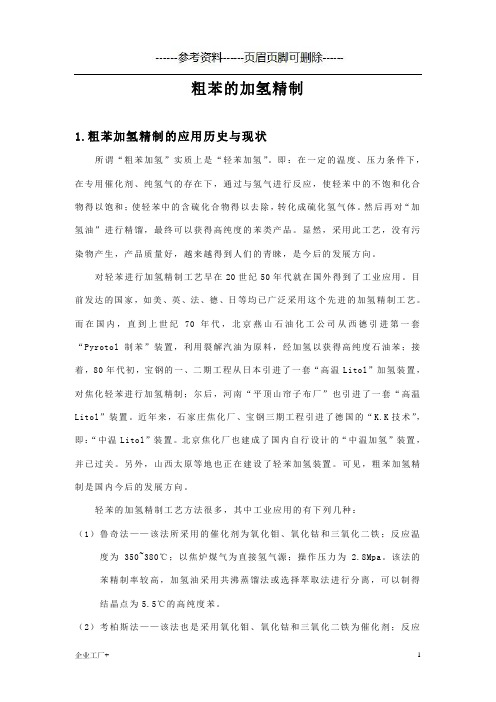
粗苯的加氢精制1.粗苯加氢精制的应用历史与现状所谓“粗苯加氢”实质上是“轻苯加氢”。
即:在一定的温度、压力条件下,在专用催化剂、纯氢气的存在下,通过与氢气进行反应,使轻苯中的不饱和化合物得以饱和;使轻苯中的含硫化合物得以去除,转化成硫化氢气体。
然后再对“加氢油”进行精馏,最终可以获得高纯度的苯类产品。
显然,采用此工艺,没有污染物产生,产品质量好,越来越得到人们的青睐,是今后的发展方向。
对轻苯进行加氢精制工艺早在20世纪50年代就在国外得到了工业应用。
目前发达的国家,如美、英、法、德、日等均已广泛采用这个先进的加氢精制工艺。
而在国内,直到上世纪70年代,北京燕山石油化工公司从西德引进第一套“Pyrotol制苯”装置,利用裂解汽油为原料,经加氢以获得高纯度石油苯;接着,80年代初,宝钢的一、二期工程从日本引进了一套“高温Litol”加氢装置,对焦化轻苯进行加氢精制;尔后,河南“平顶山帘子布厂”也引进了一套“高温Litol”装置。
近年来,石家庄焦化厂、宝钢三期工程引进了德国的“K.K技术”,即:“中温Litol”装置。
北京焦化厂也建成了国内自行设计的“中温加氢”装置,并已过关。
另外,山西太原等地也正在建设了轻苯加氢装置。
可见,粗苯加氢精制是国内今后的发展方向。
轻苯的加氢精制工艺方法很多,其中工业应用的有下列几种:(1)鲁奇法——该法所采用的催化剂为氧化钼、氧化钴和三氧化二铁;反应温度为350~380℃;以焦炉煤气为直接氢气源;操作压力为 2.8Mpa。
该法的苯精制率较高,加氢油采用共沸蒸馏法或选择萃取法进行分离,可以制得结晶点为5.5℃的高纯度苯。
(2)考柏斯法——该法也是采用氧化钼、氧化钴和三氧化二铁为催化剂;反应温度也为360~370℃,操作压力较高,为 5.0Mpa;也可采用焦炉煤气作为氢气源;苯的精制率为可达到97~98%。
(3)莱托法——该法采用三氧化二铬为催化剂;反应温度为600~650℃;操作压力为 6.0Mpa,可以采用焦炉煤气作为氢气源。
粗苯加氢工艺

粗苯加氢工艺1粗苯加氢工艺石家庄焦化集团的粗苯加氢精制装臵由六部分组成:PSA制氢单元、粗苯预处理催化加氢单元、预蒸馏及热油单元、萃取蒸馏单元、二甲蒸馏单元、油库单元。
1.1制氢单元焦炉煤气经煤气压缩机压缩至1.7好a,在预处理单元除去气体中携带的机油及使分子筛中毒的有害组分,送至变压吸附单元。
在此,除氢气外其他组分均被吸附,得到纯度为99.5%的氢气,经缓冲槽进入脱氧、干燥工序;氢气中含有的微量氧及脱氧后产生的水在此工序除去,得到纯度为99.99%的氢气送至加氢单元,多余氢气和解吸气送回荒煤气系统。
1.2粗苯预处理和催化加氢单元粗苯经油库粗苯原料泵送入预处理塔,塔顶轻苯进入加氢缓冲槽,塔底重苯送到煤气净化分厂焦油加工。
轻苯经高速泵加压进入预蒸发器和多段蒸发器,和循环氢气混合后加热蒸发,变成蒸气后进入预反应器。
在预反应器内,双烯烃、苯乙烯、二硫化碳在催化剂Ni-Mo作用下被加氢饱和,气体混合物从预反应器顶部离去。
从预反应器顶部出来的气体混合物经反应器换热器被主反应物流加热后,再经主反应器加热炉加热到主反应器所需的入口温度(290'-'350℃),从主反应器顶部进入,经过Co-Mo催化剂床层向下流动,在此发生原料脱硫、脱氮和烯烃饱和反应,从主反应器底部出来的加氢气体经过一系列换热最后冷却到40℃进入高压分离器。
从分离器分离出的气相作为循环气体经循环气体预热器及循环气体撞击分离器到循环气体压缩饥,被加压至2.8 MPa送至反应部分预蒸发器及循环气体加热器。
液相经加热进入稳定塔,提取出溶解在液相中的气体,气体从塔顶排出,通过管道送至焦炉煤气系统。
塔底产品加氢油从塔底排出,送到预蒸馏单元的加氢油缓冲槽。
1.3预蒸馏及导热油单元加氢油经加氢油原料泵,送到预蒸馏塔,预蒸馏塔顶BT馏份气体作为汽提塔重沸器的加热介质,空冷器冷凝多余BT馏份,冷凝后的BT 馏份收集在回流槽。
回流液由回流泵送到预蒸馏塔顶部,多余的BT馏份送到油库BT馏份槽。
苯精制厂工艺流程
(二)、粗苯精制工艺流程:1、加氢精制:加氢精制包括粗苯原料预分离部分、反应部分、稳定部分。
主要包括脱重组分塔、蒸发器、反应器、压缩机、稳定塔和加热炉等设备。
(1)原料预分离自罐区来的粗苯原料经原料过滤器过滤、与进料换热器换热后进入脱重组分塔,粗苯原料在塔中进行轻、重组分预分离,塔顶气体经脱重组分塔顶冷凝器冷凝冷却后进入脱重组分塔顶回流罐,罐中少量气体和漏入系统空气经减压抽空系统后出装置,罐中液体一部分经脱重组分塔塔顶回流泵升压后,作为脱重组分塔顶回流,另一部分经轻苯泵升压后进入加氢进料缓冲罐,罐中的轻苯经加氢进料泵升压后进入蒸发器,脱重组分塔底重苯一部分进脱重组分塔底重沸器泵升压并经脱重组分塔底重沸器加热后返回脱重组分塔;另一部分经脱重组分塔底泵升压,经脱重组分塔底冷却器冷却后送出装置。
脱重组分塔底重沸器热源采用2.2MPa(G)饱和蒸汽。
(2)反应部分反应原料在轻苯/主反产物换热器中与主反应产物进行换热后部分汽化,并在轻苯/主反产物换热器的混合器与循环气混合后进入蒸发塔,一小部分高沸点的物质从塔底间歇排出,蒸发塔顶部气体进入主反应产物/预反应进料换热器,与主反应产物换热后进入加氢预反应器底部,逆流向上通过催化剂床层,烯烃和苯乙烯等不饱和物在催化剂的作用下进行加氢饱和,该反应为放热反应。
进入预反应器的温度可通过主反应产物/预反应进料换热器旁路的量来控制,高沸点的液体由预反应器底部间断排出。
在预反应器内进行如下反应:二烯烃等不饱和物的加成转化反应:Cn H2n-2+H2−−→−NiMo C n H2nC6H5C2H3+H2−−→−NiMo C6H5C2H5含硫化合物的加氢脱硫反应:CS2+4H2−−→−NiMo CH4+2H2S预反应产物经主反应产物/预反应产物换热器、主反应器进料加热炉换热,加热后进入主反应器顶部。
在主反应器进行如下反应:烯烃的加成反应C n H2n+H2−−→−CoMo C n H2n+2加氢脱硫反应C4H4S+4H2−−→−CoMo C4H10+H2S加氢脱氮反应C6H7N+H2−−→−CoMo C6H14+NH3加氢脱氧反应C6H6O+H2−−→−CoMo C6H6+H2O副反应、芳香烃氢化反应C6H6+3H2−−→−CoMo C6H12C7H8+3H2−−→−CoMo C7H14C8H10+3H2−−→−CoMo C8H16物料气体通过催化剂床层流下,在那里进行脱硫、脱氮和烯烃加氢反应。
粗苯加氢精制工艺及节能环保研究
1粗 苯 加氢 精 制工艺 分析
以及高化学需要量 、 难处理 的污水, 这些污水的产生必须要经 过预 粗 苯加氢工艺 具有苯类 产品质量 高 、 收率高 , 低污 染等特点 预处 理 后 方 可 排 入 城 市 污 水 管道 。 . 3环境 风 险 而逐渐受 到普遍 应用 , 目前 国内在粗苯加氢精制工艺 中更趋 向于 2 粗 苯加氢精 制工程环境 风险较和液液萃取[ 1 _ 。 品, 这些都具有相 当的易燃易爆属性 。环评时应重点分析筛选 出 1 . 1高温 高压 加 氢 精 制 工 艺
2 . 1废 气 问 题
42- 4 4.
2 ] 李俊 勤. 苯加氢精制 过程危险源辨识 与评价技术研究 [ D ] . 郑 州: 粗 苯加氢精制过程 中由于工艺及设 备的条件限制 , 难 免会出 [ 2 0 1 2 . 现苯、 甲苯 、 二 甲苯等有机废气对周 围环境产生污染 , 对人体 健康 河南理工大学, 造 成危害, 苯及 苯系物是有毒 、 有害 、 易燃 、 易爆 的危 险化学品, 苯 【 3 ] 王绪 鑫. 苯加氢精制 工程环境影 响评 价共性 问题研究 [ D 】 . 沈 阳: 2 0 0 7 . 加 氢精制废气理化性质见表 1 。 此外, 苯加氢生产过程需要蒸 汽, 如 东北大学, 果 没有蒸气来源 , 则需要新建新的燃煤蒸气锅炉 , 燃煤锅炉在 生产 作 者简 介
馏 生产出高纯度苯化物。
2 粗 苯 加 氢 精 制 共 性 问 题 分 析
量 的分离效果 , 应先进 行蒸 氨 , 然后 再进入 厂区酚氰废水 处理净 化 。待废水预处理达到城市污水处理标准后接入 市政管 网系统 , 集 中到污水处理厂后统一处理 。
粗苯加氢精制操作手册
年产5万吨粗苯加氢装置技术操作规程概述1、本装置采用国内自行开发的粗苯中温加氢精制技术。
本装置的原料为从煤中提炼的粗苯和甲醇裂解制备的氢气,本装置生产的产品有纯苯、甲苯、二甲苯、非芳烃和重苯,其中主要的产品为纯苯、甲苯和二甲苯。
2、工艺基本原理:粗苯经过预精馏出去重质组分后,同压缩来的氢气进入加氢工序反应;利用中温加氢将粗苯中以噻吩为主的各种杂质全部除去,其中硫化物全部转化为H2S,氮化物转化为NH3,氧化物转化为H2O,不饱和烃加氢饱和;经加氢后的粗产品进入精馏工序,经常规精馏和萃取精馏后得到纯苯、甲苯和二甲苯等产品。
本装置主体共为六个工序:100#原料预处理工序、200#氢气压缩工序、300#加氢工序、400#脱轻工序、500#精馏工序、600#罐区工序。
本装置所用的公用工程有:配电、循环水、空压站、锅炉、制氢、消防站、废水处理。
第一章原料预处理工序(100#)一. 岗位说明1.工艺说明自罐区粗苯贮罐V601A、B来的粗苯,经粗苯进料泵(P602A、B)打入两苯塔(T101)中部,在两苯塔中进行轻重苯的分离,所需热能由中压蒸汽加热再沸器E101A、B提供。
塔顶溢出轻苯油馏分蒸汽进入两苯塔冷凝冷却器(E102),经冷却后进入两苯塔油水分离器(V101),分离掉水后的轻苯油经两苯塔回流泵(P101A、B),一部分打入两苯塔塔顶作为回流,其余部分送到罐区轻苯贮槽(V603)作为加氢的原料,两苯塔底采出的重质苯通过重质苯泵(P102A、B)送到罐区重苯贮槽V602。
2.工艺控制指标:水运时温度不同,不按以上的指标执行。
二. 岗位操作1.开车前的准备:(1)检查各设备、管道、阀门、分析取样点、仪表等,必须正常完好(特别检查调节阀的动作状态现场与DCS室是否一致)。
(2)检查系统内所有阀门的开、关位置,应符合开车要求。
特别注意与高压系统300单元取通阀是否处于正常状态。
(3)与供水、供电、供汽、供气部门等公用工程联系,确保公用工程电、压缩空气、仪表风、氮气、蒸汽、循环水等满足开工要求。
宝钢三期的K.K法粗苯加氢精制工艺介绍
宝钢三期的K.K法粗苯加氢精制工艺介绍1.1"K.K法粗苯加氢工艺简介”该工艺包括加氢精制、预蒸储、萃取蒸储、二甲苯蒸储和罐区等5个单元。
煤气精制厂送来的粗苯与焦油精制装置送来的脱酚轻油,首先在“加氢精制单元”中进行多级蒸发,再进行两级加氢处理,即:预加氢、主加氢净化。
该加氢所需要的补充氢气由外界供给。
粗苯加氢后所产生的轻质组分和H2S气体,靠“稳定塔”将它们分离出来,气体部分则送往“煤气精制厂”处理。
而蒸发后的残油送经“残油蒸储塔”,以获得“重质苯”、并送往“古马隆-荀树脂生产装置二经加氢后所得到的“加氢油”,即“三苯储分(BTXS)”进入“预蒸储单元”,将其中的重组分(即:XS微分)和轻组分(即:BT僧分)分离开来。
轻组分储分(BT)进入“萃取蒸储单元”,以除去非芳香燃储分,并获得苯嫌纯产品。
重组分播分(XS)进入“二甲苯蒸储单元”,以除去“轻组分”和“重组分”,并获得纯二甲苯产品。
上述所获得的非芳香烧储分、轻组分、重组分都送往“罐区单元”。
该K.K加氢技术工艺的特点有:*1对全部的粗苯进行加氢,而不是像“Litol”加氢那样需要对粗苯进行“预先分储二*2整个工艺过程的操作全部实现连续化、自动化。
*3产品的得率较高,与酸洗法精制相比,其产品得率约提高8~10虬*4氢气的消耗量比其它工艺(如:Litol法)要低。
这是因为该加氢方法中,需要氢来转化的仅仅是粗苯中的杂质。
*5该工艺方法能够深度地进行“脱硫”、“脱氧”与“脱氮”,而对苯煌产品的得率没有影响。
*6所获得的产品纯度高,而且还可根据用户的要求,分别生产出“硝化甲苯”或“纯甲苯”。
*7本工艺采用“甲酰吗琳”作为萃取蒸储的萃取溶剂,起分离非芳香燃的效果特别好。
而该溶剂的消耗量低,每年仅消耗约为500kg。
1.2“加氢单元”的工艺技术1.2.1工艺流程“加氢单元”包括粗苯蒸发、加氢反应、残油蒸储和稳定塔处理等4个系统。
加氢反应所需要的氢气由外界提高。
- 1、下载文档前请自行甄别文档内容的完整性,平台不提供额外的编辑、内容补充、找答案等附加服务。
- 2、"仅部分预览"的文档,不可在线预览部分如存在完整性等问题,可反馈申请退款(可完整预览的文档不适用该条件!)。
- 3、如文档侵犯您的权益,请联系客服反馈,我们会尽快为您处理(人工客服工作时间:9:00-18:30)。
粗苯的加氢精制1. 粗苯加氢精制的应用历史与现状所谓“ 粗苯加氢”实质上是“ 轻苯加氢”。
即:在一定的温度、压力条件下,在专用催化剂、纯氢气的存在下,通过与氢气进行反应,使轻苯中的不饱和化合物得以饱和;使轻苯中的含硫化合物得以去除,转化成硫化氢气体。
然后再对“加氢油”进行精馏,最终可以获得高纯度的苯类产品。
显然,采用此工艺,没有污染物产生,产品质量好,越来越得到人们的青睐,是今后的发展方向。
对轻苯进行加氢精制工艺早在20 世纪50 年代就在国外得到了工业应用。
目前发达的国家,如美、英、法、德、日等均已广泛采用这个先进的加氢精制工艺。
而在国内,直到上世纪70 年代,北京燕山石油化工公司从西德引进第一套“ Pyrotol 制苯” 装置,利用裂解汽油为原料,经加氢以获得高纯度石油苯;接着,80 年代初,宝钢的一、二期工程从日本引进了一套“ 高温Litol ”加氢装置,对焦化轻苯进行加氢精制;尔后,河南“ 平顶山帘子布厂” 也引进了一套“ 高温Litol ”装置。
近年来,石家庄焦化厂、宝钢三期工程引进了德国的“ K.K 技术”,即:“ 中温Litol ”装置。
北京焦化厂也建成了国内自行设计的“ 中温加氢”装置,并已过关。
另外,山西太原等地也正在建设了轻苯加氢装置。
可见,粗苯加氢精制是国内今后的发展方向。
轻苯的加氢精制工艺方法很多,其中工业应用的有下列几种:(1)鲁奇法——该法所采用的催化剂为氧化钼、氧化钴和三氧化二铁;反应温度为350~380 C;以焦炉煤气为直接氢气源;操作压力为2.8Mpa。
该法的苯精制率较高,加氢油采用共沸蒸馏法或选择萃取法进行分离,可以制得结晶点为5.5 C的高纯度苯。
(2)考柏斯法——该法也是采用氧化钼、氧化钴和三氧化二铁为催化剂;反应温度也为360~370 C ,操作压力较高,为5.0Mpa ;也可采用焦炉煤气作为氢气源;苯的精制率为可达到97~98%。
(3)莱托法——该法采用三氧化二铬为催化剂;反应温度为600~650 C ;操作压力为6.0Mpa ,可以采用焦炉煤气作为氢气源。
该法的特点是能够使苯的同系物脱烷基转化成苯,故苯的总收率可高达110%。
此外,还有美国环球石油产品公司以金属钴、钼作为催化剂的U.O.P 催化加氢法;以加氢净化与选择萃取相结合的深度净化的尤迪克斯法等。
以上各法在许多国家均有应用,其中“ Litol 法”虽然于上世纪60 年代才用于工业生产,但由于该法的苯产率高、苯产品纯度高,故获得广泛的应用。
其实,宝钢一、二期所采用的就是该“高温Litor 法”。
而宝钢三期采用的就是“鲁奇法”。
2、催化加氢的反应机理 2.1 催化反应的基本概念在化学反应中,由反应物转变为产物,反应物分子的原子或原子团必须重新组合,要实现这一过程,该反应物分子必须获得足够的能量才行。
获得能量的分子称为“活化分子”。
但是,对许多化学反应来说,在一般的条件下,活化分子的数量极少,以使反应实际上并不能进行。
若要使得反应顺利进行,就必须使大量的反应分子获得至少等于活化能“ E”的额外能量。
升高温度是常用的方法之一。
但是,在高温下进行工业生产,必然要从外界提供能量,增加能量消耗与生产成本。
再说,有很多反应即使在高温下也难以顺利进行。
因此,必须采用催化反应,即:加入适当的催化剂,以降低反应的活化能。
显然,在催化反应过程中,催化剂能使反应的活化能降低,即:反应分子不需要具有像非催化过程中那么高的能量就能使反应顺利进行。
由于反应速度与活化能呈指数函数的关系。
所以,活化能的降低对反应速度的增加影响极大。
但必须注意,催化剂的存在只能改变化学反应大平衡的速度和使化学反应朝向几个可能的方向之一进行,而不能使那些在热力学上不可能进行的反应发生。
这就是催化剂的功用所在。
(1)催化剂——催化剂是一种能够改变化学反应速度、而本身并不参与反应生成最终产物的物质。
它可以是单一物质、或几种物质组成的复合物。
其存在的状态可以为气体、液体或固体。
其中固体催化剂在工业上的应用最广,也最为重要。
固体催化剂通常由活性物质(金属或金属氧化物,称为“主催化剂”)、助催化剂和载体等物质组成。
有时还添加成型剂或造孔物质,以便于制成所需的形状或改变孔隙的结构与强度。
催化剂的催化功效的大小,一般以催化剂的活性来衡量。
对工业催化剂而言,其活性常以单位体积(或重量)催化剂在一定温度、压力、反应物浓度和空速等反应条件下,单位时间内所得到的产品产量来表示。
或者以产物的产量换算为“转化率x”表示,即:x= (反应了的克分子数/ 通过催化剂床层的反应物的克分子数)*100% 上述表示式并不严格,只是便于衡量催化剂的能力。
当研究物质的催化化学性能时,可采用所谓的“催化剂比活性” 来表示。
若1 克催化剂的表面积为S 比,总活性为A,则:比活性A比=A/S比。
当化学反应在理论上可能有几个反应方向时,通常一种催化剂在一定条件下,只对其中一个反应方向起加速作用,这种性能称为“ 催化剂的选择性”。
该催化剂的选择性(s )常以下式表示:s=(所需产物的克分子数/ 通过催化剂床层后反应了的原料的克分子数)*100%由于许多工业过程除主反应外,常伴有副反应,所以选择性总是小于100%。
固体催化剂的表面能够吸附各种气体或液体分子,这种吸附现象与多相催化作用间有密切关系。
根据分子在固体表面上的吸附性质,可以分为物理吸附与化学吸附。
物理吸附是靠分子间的“范德华力”,即分子间的引力来进行的。
该类型的吸附只有在低温下才能呈现;吸附热很小,吸附速度快,易达到平衡,故没有选择性。
由于物理吸附是在低温下进行,且吸附的速度随着温度的升高而下降。
故此类型的吸附在催化作用中的影响很小。
化学吸附是指被吸附分子与固体能发生某种化学作用,具有化学反应的性质。
吸附热一般大于42kj/mol 。
在一定的温度范围内,化学吸附的速度随温度的升高而增加。
化学吸附有一定的吸附选择性,且常是不可逆的。
工业催化剂在性能上的要求是:活性要高;选择性要好;对热与毒物要稳定;机械强度要高;反应物易于流过;导热性要好等固体催化剂应根据使用要求,制成粉状、粒状。
、柱状、环状和球状。
催化剂在使用过程中会逐渐老化,催化活性逐渐下降。
催化剂的老化一般是重结晶和相应的表面结构的改变而引起的。
也可能是由于催化剂表面被副反应生成的树脂状物质及沉积碳覆盖所致。
对失去活性的催化剂,可以根据具体情况采用氧化还原法或用酸、或碱浸渍处理等方法予以再生。
(2)助催化剂——助催化剂是加入到催化剂中的少量物质。
其本身没有活性或活性很小。
但它的加入能显著提高主催化剂的活性、选择性或稳定性。
助催化剂的作用十分复杂。
它在催化剂中的含量不同会对主催化剂产生不同影响。
在其它许多条件相同的情况下,同一种物质在某一温度下可以是助催化剂,而在另一温度下又可能是催化剂的毒物。
助催化剂按作用特征可以分为结构性助催化剂和调变性助催化剂两类。
前者能增加催化剂活性物质微晶的稳定性,即:可延长催化剂的寿命。
后者能改变催化剂活性物质的结构和化学组成,使活性物质的微晶形成晶格缺陷,产生新的晶格中心,或者也可能产生或增多催化剂中的晶相间、或微晶间活性界面的数量,从而提高催化剂的活性与选择性。
用来制作助催化剂的物质主要有金属、金属氧化物和某些磷酸盐类等。
(3)载体——所谓“载体” 是指催化剂活性物质的分散剂、粘合剂和支撑物。
许多工业催化剂通常使用“ 比表面积” 大于50m2 /g 、平均孔径小于200 0A 的高比表面载体。
女口:Al 2Q(比表面积为100~200m 2/g )、白土(比表面积为150~280m 2/g )、氧化硅-氧化铝(比表面积为350m2/g )等。
当物质的催化活性很高时,反应过深会使选择性下降,此时要选用低表面载22 体,如:碳化硅(比表面积小于1m /g )、硅藻土(比表面积为2~30m /g )等。
载体不仅能对催化活性物质起到分散、粘合、支撑等作用,以提高催化剂的使用寿命;并且它们常常能与活性物质发生作用而生成新的化合物或固溶体,从而使催化剂的活性和选择性变更。
因此,在通常情况下,制备催化剂时,不能任意选择载体。
在实际应用时,必须要根据催化活性物质的物理化学特性、催化反应类型及反应操作条件等因素来加以选择。
只有这样才能最大限度地发挥催化剂各类组分的功用,达到最理想的效果。
2.2 催化加氢用的催化剂对于粗苯等芳香烃的催化加氢而言,主要的催化化学反应有:含硫化合物的加氢裂解、环烯烃的加氢及脱氢、烷烃与环烷烃的加氢裂解、或带侧链烷烃的苯烃的脱烷基反应等。
其实,这些反应均是属于氧化-还原催化反应。
在它们所用的强活性催化剂中,不论其组成可能不同,但总是至少含有一个位于元素周期表的长周期中部的元素,如:Cr、Fe、Mn、Co、Ni 、Mo 等(还有:钯、铂,因是贵金属,较少采用)。
这充分说明元素与其化合物的催化性质是在一定的条件下表现出来的物质本性。
即:它们具有的催化特性是与这些元素在周期表中的位置存在着内在的联系。
众所周知,元素的化学性质,包括催化特性,取决于原子核外的电子分布,特别是最外层电子的分布。
在元素周期表长周期中部的那些“d副层”未能充满电子的元素,对氧化-还原反应具有独特的催化活性。
在大多数情况下,催化活性随着原子中“ d副层”电子数的减少而升高,如:第4周期第忸族的Ni元素的电子分布为——Ni :1s 2 2s2 2p6 3s2 3p6 3d8 4s2即:Ni 有8 个d 电子,对双键加氢即表现出很大活性。
而当过渡到Cu 时,由于Cu原子的d层有10个电子,已经充满,故其催化活性即显著下降。
粗苯中的有机硫化物主要有噻吩、二硫化碳等,从对难于加氢分解的噻吩的加氢脱硫反应,也可以看出元素的催化性能。
根据多种载在v -Al 203上的金属对噻吩加氢的催化活性所进行的研究,表明:铬、钴、镍、钯、铂等均具有较高的脱硫活性,其中铂的催化活性最高。
十分明显,这些具有催化特性的金属全部属于周期表中的第忸族和B族的过渡元素。
当采用双金属催化剂时,Mo-Co 或Mo-Ni 系催化剂,对噻吩的加氢脱硫反应表现出最大的催化活性。
因此,目前苯烃加氢工艺中,广泛应用这两种金属或其氧化物为主体的催化剂,其中最常用的是以活性氧化铝为载体的Co-Mo 系催化剂。
分散在大比表面积载体氧化铝上的氧化钴与氧化钼的混合物所构成的新催化剂,实际上是由Al 203、CoAl 204、CoO、MoO、CoMoO和结构复杂的Co-Mo氧化物所组成。
其中,Al 203、CoAl 204 是没有活性的,Co0、Mo03、CoMo04 具有中等的活性,而结构复杂的Co-Mo 氧化物才具有较高的活性。
上述催化剂在新鲜氧化状态时,对加氢反应能显示很高的活性,但主要起催化裂解的作用,如:QH6+9H2 T 6CH4 (在CoO/MoO存在下)。