一种柔性冲压自动化生产线系统的研制
电子设备制造中的柔性生产线设计与控制方法

电子设备制造中的柔性生产线设计与控制方法随着科技的不断进步和人们对电子产品的需求增加,电子设备制造行业也在迅速发展。
为了提高生产效率和降低成本,制造商们开始采用柔性生产线的设计与控制方法。
本文将探讨电子设备制造中柔性生产线的设计原则和控制方法。
一、柔性生产线的概念柔性生产线是一种能够适应不同产品生产需求的生产线系统。
它具有模块化设计和可重构的特点,能够灵活应对市场需求的变化。
在电子设备制造行业,柔性生产线可以根据订单需求进行快速调整,提高生产效率和产品质量。
二、柔性生产线的设计原则1. 模块化设计:柔性生产线应该采用模块化设计,使各个生产环节可以独立运作。
这样一旦出现故障或需要调整,只需更换或调整相应模块,而无需停止整条生产线的运作。
2. 可重构性:柔性生产线需要具备可重构性,即能够根据市场需求的变化自动或快速调整生产流程。
这可以通过智能化的设备和自动化的控制系统来实现。
3. 多品种生产:柔性生产线应能够同时生产多种型号的电子设备,并能根据需求灵活切换生产任务。
这可以通过设备的切换模式和生产规划的优化来实现。
三、柔性生产线的控制方法1. 自动化控制:柔性生产线应采用自动化控制方法,在保证生产质量和效率的前提下减少人工干预。
通过传感器和控制系统的联动,可以实现生产过程的自动监测和自动调整。
2. 数据分析和优化:柔性生产线需要收集和分析生产过程中的数据,以实现生产过程的优化。
通过对生产数据的分析,可以找到生产过程中的瓶颈和改进空间,进而提高生产效率和产品质量。
3. 供应链协同:柔性生产线的设计应考虑供应链的协同作用。
制造商需要与供应商、物流公司和客户等各方密切合作,实现供需的匹配和生产流程的协调,以实现整体生产效益的最大化。
四、柔性生产线的挑战与展望尽管柔性生产线在电子设备制造行业中具有巨大的潜力,但也面临一些挑战。
其中包括设备标准化、人力资源培训和供应链集成等方面的问题。
未来,随着科技的不断发展,柔性生产线将更加智能化和自动化,以适应电子设备制造的新需求。
柔性自动化生产线_图文

一专周背景柔性制造系统(FlexibleManufacturingSystem简称FMS,采用FMS的主要技术经济效果是:能按装配作业配套需要,及时安排所需零件的加工,实现及时生产,从而减少毛坯和在制造的库存量,及相应的流动资金占有量,缩短生产周期;提高设备的利用率,减少设备数量和厂房面积;减少直接劳动力,在少人看管条件下可实现昼夜24小时的连续“无人化生产”;提高产品质量的一致性。
整个系统由MES生产制造管理系统计算机、组态王监控计算机、主控PLC和下位PLC 通过网络通信技术构成一个完整的多级计算机控制系统。
现场总线技术的定义:是用于现场仪表与控制室之间的一种”全数字化、双向、多变量、多点多站的通信系统”,其本质含义表现在以下几个方面:现场通信网络、现场设备互连、互操作性、分散功能模块和开放式互联网络。
柔性制造系统的ROFIBUS-DP数据通信网络组成。
二.专周目的1.熟悉STBP7MICROWIN软件的主要操作功能。
2.初步掌握STBP7WICROWIN软件对PLC的编程和监控。
3.学会编织一个简单的程序并能正确的运行。
三.专周内容A.机械手左右运输1.题目要求机械手的动作过程如图所示。
1.从原点开始,按下启动开关,下降电磁阀通电,机械手下降,下降到位后,碰到下限位开关,下降电磁阀断电,停止下降。
2同时接通夹紧电磁阀,机械手夹紧。
3夹紧后,上升电磁阀通电,机械手上升。
上升到位时,碰到上限位开关,上升电磁阀断电,停止上升。
4同时接通右移电磁阀,机械手右移。
右移到位时,碰到右限位开关,右移电磁阀断电,停止右移。
5若此时右工作台上无工件,则光电开关接通,下降电磁阀通电,机械手下降。
下降到位后,碰到下限位开关,下降电磁阀断电,停止下降。
6同时夹紧电磁阀断电,机械手放松。
7放松后,上升电磁阀通电,机械手上升。
上升到位后,碰到上限位开关,上升电磁阀断电,停止上升。
8同时接通左移电磁阀,机械手左移。
左移到位后,碰到左限位开关,左移电磁阀断电,停止左移。
机器人冲压自动线的生产节拍优化
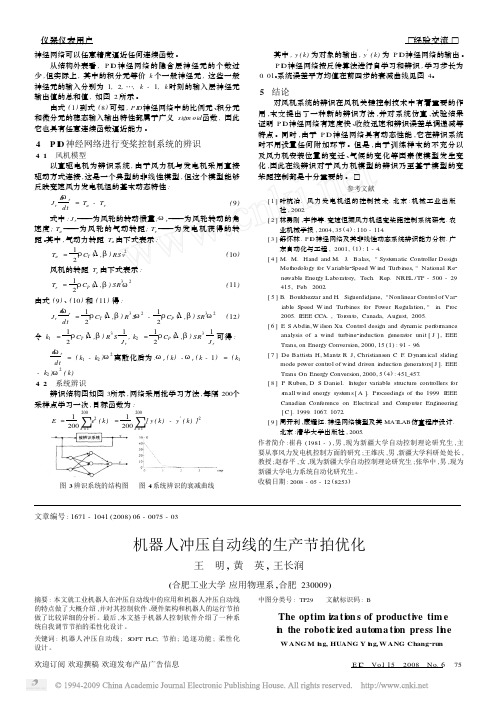
欢迎订阅欢迎撰稿欢迎发布产品广告信息E I C Vo l .15 2008 No.6 75 神经网络可以任意精度逼近任何连续函数。
从结构外表看,P I D 神经网络的隐含层神经元的个数过少,但实际上,其中的积分元等价k 个一般神经元,这些一般神经元的输入分别为1,2,…,k -1,k 时刻的输入层神经元输出值的总和值,如图2所示。
由式(1)到式(8)可知,P I D 神经网络中的比例元、积分元和微分元的稳态输入输出特性都属于广义sigm oid 函数,因此它也具有任意连续函数逼近能力。
4 P I D 神经网络进行变桨控制系统的辨识4.1 风机模型以直驱电机为辨识系统,由于风力机与发电机采用直接驱动方式连接,这是一个典型的非线性模型,但这个模型能够反映变速风力发电机组的基本动态特性:J r dωr d t=T a -T e(9)式中:J r ———为风轮的转动惯量;ωr ———为风轮转动的角速度;T a ———为风轮的气动转距;T e ———为发电机获得的转距。
其中,气动力转距T a 由下式表示:T a =12ρC T (λ,β)RS v2(10)风机的转距T e 由下式表示:T e =12ρC P (λ,β)SR 3ω2(11)由式(9)、(10)和(11)得:J r d ωr d t =12ρC T (λ,β)R 3S ω2-12ρC P (λ,β)SR 3ω2(12)令k 1=12ρC T (λ,β)R 3S 1J r ,k 2=12ρC P (λ,β)SR 31J r可得:d ωr d t=(k 1-k 2)ω2离散化后为:ωr (k )-ωr (k -1)=(k 1-k 2)ω2(k )4.2 系统辨识辨识结构图如图3所示,网络采用批学习方法,每隔200个采样点学习一次,目标函数为:E =1200∑200k =1e 2(k )=1200∑200k =1[y (k )-y ′(k )]2图3辨识系统的结构图 图4系统辨识的衰减曲线其中,y (k )为对象的输出,y ′(k )为P I D 神经网络的输出。
自动化生产线柔性制造技术 - 教案
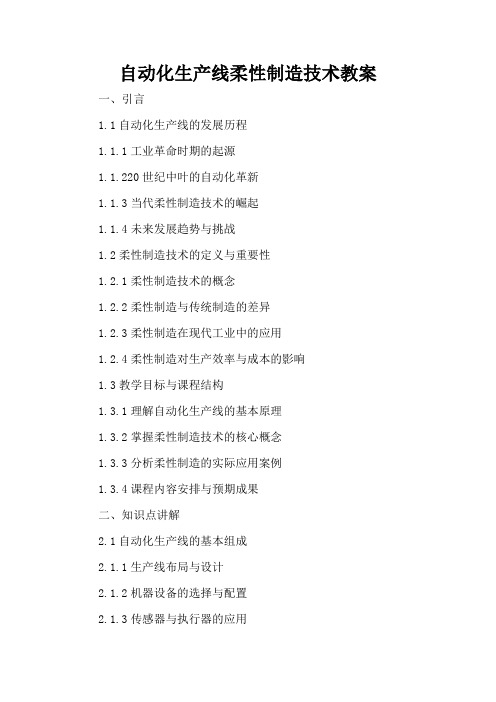
自动化生产线柔性制造技术教案一、引言1.1自动化生产线的发展历程1.1.1工业革命时期的起源1.1.220世纪中叶的自动化革新1.1.3当代柔性制造技术的崛起1.1.4未来发展趋势与挑战1.2柔性制造技术的定义与重要性1.2.1柔性制造技术的概念1.2.2柔性制造与传统制造的差异1.2.3柔性制造在现代工业中的应用1.2.4柔性制造对生产效率与成本的影响1.3教学目标与课程结构1.3.1理解自动化生产线的基本原理1.3.2掌握柔性制造技术的核心概念1.3.3分析柔性制造的实际应用案例1.3.4课程内容安排与预期成果二、知识点讲解2.1自动化生产线的基本组成2.1.1生产线布局与设计2.1.2机器设备的选择与配置2.1.3传感器与执行器的应用2.1.4控制系统的集成与管理2.2柔性制造技术的关键要素2.2.1模块化设计理念2.2.2可编程逻辑控制器(PLC)的应用2.2.3机器视觉系统的作用2.2.4与机器学习的融合2.3柔性制造技术的实施策略2.3.1生产流程的优化与重组2.3.2供应链管理的调整2.3.3人力资源的配置与培训2.3.4质量控制与维护保养三、教学内容3.1自动化生产线的案例分析3.1.1汽车制造行业的自动化应用3.1.2电子制造业的柔性生产线3.1.3食品加工行业的自动化改造3.1.4案例分析与讨论3.2柔性制造技术的模拟实验3.2.1实验室模拟自动化生产线3.2.2柔性制造系统的搭建与测试3.2.4实验成果展示与评价3.3柔性制造技术的未来趋势3.3.1工业物联网(IIoT)的应用3.3.2云计算与大数据的集成3.3.3增材制造(3D打印)的发展3.3.4未来挑战与机遇自动化生产线柔性制造技术教案四、教学目标4.1知识与技能目标4.1.1理解自动化生产线的原理和组成4.1.2掌握柔性制造技术的核心概念和应用4.1.3学习自动化生产线的设计、优化和管理4.1.4分析实际案例,提高问题解决能力4.2过程与方法目标4.2.1通过案例分析,培养学生观察和思考能力4.2.2通过模拟实验,提高学生的动手操作能力4.2.3通过小组讨论,增强学生的团队协作能力4.2.4通过项目实践,提升学生的创新设计能力4.3情感态度与价值观目标4.3.1培养学生对自动化技术的兴趣和热情4.3.2增强学生对工业自动化的认识和理解4.3.3培养学生的工程思维和工匠精神4.3.4提高学生对未来工业发展的责任感和使命感五、教学难点与重点5.1教学难点5.1.1自动化生产线的集成与管理5.1.2柔性制造技术的实施策略5.1.3模拟实验的操作与数据分析5.1.4未来趋势的分析与预测5.2教学重点5.2.1自动化生产线的基本组成和原理5.2.2柔性制造技术的核心概念和应用5.2.3案例分析与讨论的方法和技巧5.2.4实验操作步骤和注意事项六、教具与学具准备6.1教具准备6.1.1自动化生产线模型或实物6.1.2柔性制造系统的演示设备6.1.3多媒体教学设备(投影仪、电脑等)6.1.4教学课件和案例分析材料6.2学具准备6.2.1笔记本电脑或平板电脑6.2.2实验报告模板和数据分析软件6.2.3小组讨论记录表和汇报材料6.2.4安全防护用品(如安全眼镜、手套等)七、教学过程7.1导入新课7.1.1引入自动化生产线的发展背景7.1.2提出柔性制造技术的应用问题7.1.3激发学生的学习兴趣和好奇心7.1.4明确教学目标和内容安排7.2知识讲解与案例分析7.2.1讲解自动化生产线的基本组成和原理7.2.2分析柔性制造技术的核心概念和应用7.2.3案例分析:自动化生产线的设计与优化7.2.4案例分析:柔性制造技术的实施策略7.3模拟实验与小组讨论7.3.1分组进行模拟实验操作7.3.2记录实验数据和观察结果7.3.3小组讨论:实验现象和问题解决7.3.4汇报实验成果和讨论结果7.4.2分析未来工业发展的趋势和挑战7.4.3强调学生的职业发展和学习方向7.4.4布置课后作业和思考题自动化生产线柔性制造技术教案八、板书设计8.1板书内容8.1.1自动化生产线的组成与原理8.1.2柔性制造技术的核心概念8.1.3案例分析与讨论要点8.2板书布局8.2.1左侧列出关键词和概念8.2.2中间展示流程图和示意图8.2.3右侧记录案例分析和讨论结果8.3教学辅助材料8.3.1PPT课件和视频资料8.3.2实验操作手册和数据分析表8.3.3案例分析材料和小组讨论记录表8.3.4课后作业和思考题九、作业设计9.1课后作业9.1.1分析自动化生产线的设计和优化策略9.1.2探讨柔性制造技术的实施方法和挑战9.1.3调研工业物联网在自动化生产中的应用9.1.4设计一个简单的自动化生产线模型或流程9.2思考题9.2.1自动化生产线与手工生产的优缺点对比9.2.2柔性制造技术对生产效率和成本的影响9.2.3未来工业发展的趋势和挑战9.2.4学生对未来职业发展的规划和准备十、课后反思及拓展延伸10.1课后反思10.1.1教学内容的深度和广度是否适中10.1.2教学方法和手段的有效性和创新性10.1.3学生的参与度和学习效果的评价10.1.4教学目标和预期的达成情况10.2拓展延伸10.2.1引导学生关注工业4.0和智能制造的发展10.2.2提供相关的在线课程和阅读材料10.2.3鼓励学生参加相关的竞赛和实践活动10.2.4与企业合作,提供实习和就业机会重点环节补充和说明:1.案例分析与讨论:通过实际案例分析,帮助学生理解自动化生产线和柔性制造技术的应用,培养问题解决和团队协作能力。
冲压生产线柔性制造布局

。
改进措施制定
针对瓶颈工序,制定具体的改进措 施,如优化作业方法、提高设备性 能等。
实施效果评估
对改进措施进行实施,并跟踪评估 效果,确保瓶颈问题得到有效解决 。
多品种小批量生产调度
生产计划制定
01
根据市场需求和产品特点,制定合理的生产计划,确保多品种
优先选用环保型原材 料和辅助材料,减少 对环境的影响。
THANKS
感谢观看
建立物料仓储系统,实现 原材料的自动存储、管理 和配送,提高物料利用率 和管理效率。
快速换模技术
模具快速更换装置
采用快速更换装置实现模具的快速更 换,减少换模时间和生产停机时间。
模具状态监测与预警系统
建立模具状态监测与预警系统,实时 监测模具状态和使用情况,提前预警 并避免模具故障和损坏。
标准化模具设计
信息系统
引入物料管理信息系统,实现 物料信息实时更新、查询。
搬运路径
规划合理的物料搬运路径,减 少交叉、回流现象。
辅助设施规划
供电系统
设计稳定、可靠的供电系统,确保设备正常 运行。
照明与通风
提供充足的照明和通风设施,营造舒适的生 产环境。
排水与废气处理
合理规划排水管道、废气处理设施,满足环 保要求。
柔性化生产
通过模块化设计和快速换模技术,实现生产线的快速切换和适应多 品种、小批量生产。
智能化监控
利用机器视觉、智能传感器等技术,实时监控生产过程和设备状态, 及时发现并处理异常情况。
人工智能技术在冲压领域应用
智能排程
利用人工智能技术实现生产计划的智能排程,提 高生产效率和设备利用率。
自动化生产线柔性制造系统的设计与优化

自动化生产线柔性制造系统的设计与优化随着科技的进步和生产环境的变化,越来越多的企业开始实施自动化生产线,以提高生产效率和降低成本。
然而,传统的自动化生产线在面对市场需求变化时难以快速适应,因此柔性制造系统的设计与优化成为了一个重要的问题。
本文将探讨自动化生产线柔性制造系统的设计与优化的一些关键要素。
一、需求分析在设计和优化柔性制造系统之前,首先需要进行需求分析。
这包括了对市场需求、产品特性以及生产能力的全面评估。
通过全面了解市场需求和产品特性,企业可以更好地预测未来的生产需求,并根据需求调整柔性制造系统的性能指标和功能特点。
二、布局设计柔性制造系统的布局设计是设计与优化的关键一步。
柔性制造系统通过模块化和灵活配置的方式,可以实现多种产品生产,因此其布局设计需要充分考虑生产流程的合理性和资源利用率。
布局设计应该优先考虑生产设备之间的相互关联性和生产过程的流畅性,以确保生产过程的高效运行和产品质量的稳定。
三、设备选择柔性制造系统的设备选择需要兼顾生产需求和经济效益。
在设备选择过程中,企业需要考虑设备的生产能力、稳定性、可靠性以及维护成本。
同时,为了实现柔性生产,设备应具有可编程和可调节的功能,以满足不同产品的生产要求。
四、控制与调度柔性制造系统的控制与调度是其设计与优化的关键问题之一。
通过合理的控制和调度策略,可以实现生产线的高效运行和资源的最佳利用。
这包括了生产任务的分配、设备的调度以及物料的流动控制等。
目前,基于人工智能和优化算法的智能控制与调度技术在柔性制造系统中得到了广泛应用,通过自动化的方式实现了生产过程的优化和自动化。
五、质量控制柔性制造系统的设计与优化还需要充分考虑质量控制的问题。
质量控制包括产品的质量检测、故障预测和质量改进等。
通过合理的质量控制策略,可以保证产品的稳定质量,并及时发现和解决生产过程中的问题,从而提高生产效率和降低成本。
六、持续改进柔性制造系统的设计与优化不是一次性的过程,而是一个持续改进的过程。
柔性生产线系统设计与实现研究

柔性生产线系统设计与实现研究柔性生产线是一种能够根据产品需求和生产任务,灵活调整生产流程和生产能力的生产方式。
它通过引入先进的生产技术和智能化的控制系统,实现生产过程的可调度性和可重构性。
本文将从柔性生产线系统的设计和实施两个方面进行研究。
柔性生产线系统设计主要包括以下几个方面:流程设计、设备配置、任务分配和控制系统设计。
首先是流程设计。
柔性生产线的流程应能够适应不同产品的生产需求。
在流程设计中,需要明确每个工序的具体任务和目标,确定工序之间的先后顺序以及工序之间的交互关系。
同时,还要考虑工序的平衡性和生产能力的匹配,确保生产过程的连贯性和高效性。
设备配置是柔性生产线系统设计的关键环节。
柔性生产线需要配置能够适应多种产品生产需求的设备。
这些设备应具备快速转换能力,能够在短时间内实现从一种产品生产到另一种产品生产的转换。
此外,设备配置还要考虑生产线的灵活性和可扩展性,以适应未来生产需求的变化。
任务分配是柔性生产线系统设计中的核心问题。
在柔性生产线上,任务分配应能够合理调度生产资源,使得生产过程能够在最短的时间内完成。
任务分配涉及到产品的生产能力分配、设备的使用状态分配以及人员的工作任务分配。
通过合理的任务分配,可以实现生产线的高效运行和资源的最优利用。
控制系统设计是柔性生产线系统设计中的最重要的一环。
控制系统应能够实时监控生产过程,及时调整和优化生产流程。
控制系统需要有一定的智能化和自适应能力,能够根据不同的生产任务和生产需求,动态调整工序之间的协调和资源的调度。
控制系统还应具备数据采集和分析的功能,能够为生产过程的优化提供依据和支持。
柔性生产线系统的实施是一个复杂的工程,需要各方面的资源支持和合作。
实施过程中需要先进行系统的评估和规划,明确系统的设计目标和需求,确定所需资源和预期效果。
在系统实施过程中,需要加强对各方面的培训和支持,确保系统的顺利运行和性能优化。
同时,还需要建立完善的监控机制和维护体系,定期对系统进行检查和维护,以确保系统的长期稳定性和可持续发展。
柔性生产线控制系统研究

柔性生产线控制系统研究随着工业化的快速发展,机器自动化技术日新月异。
其中,柔性生产线控制系统是一种新型的生产方式,它采用先进的计算机技术自动化控制整个生产过程。
这种生产方式可以根据设定的参数对不同的生产需求作出快速反应,并实现生产的高效、高质量、低成本和可靠性等目标。
本文将重点讨论柔性生产线控制系统的相关研究。
一、柔性生产线控制系统的概述柔性生产线控制系统是指通过智能化的硬件和软件技术来实现生产过程的控制和调度。
它可以适应不同的产品类型和生产需求,自动调节机器的工作模式以及其他相应的参数,保证生产线的高效性和高品质。
同时,柔性生产线还具有自我监测和故障诊断等功能,可以保证生产线的可靠性和鲁棒性。
柔性生产线控制系统与传统的生产线系统相比,具有以下优势:1. 可以在不同的模式下进行切换,适应不同产品的生产需求;2. 可以自动进行机器调度和设备配置,提高生产效率;3. 可以自动诊断和预测设备的故障,保证生产线的正常运行。
二、柔性生产线控制系统的研究方向1. 机器学习技术的应用柔性生产线控制系统需要自动化地进行机器调度和配置,这就需要对生产过程中的数据进行分析和处理。
机器学习技术可以帮助控制系统从数据中学习模式和规律,并自动调整生产过程中的参数,提高生产效率。
2. 多智能体协同处理柔性生产线控制系统包含多种不同类型的设备,这些设备需要通过协同处理来完成生产任务。
多智能体协同处理技术可以帮助这些设备实现自动协同,并通过分布式的决策制定来提高生产线的性能和鲁棒性。
3. 云计算技术的应用柔性生产线控制系统需要处理大量的数据和信息,而云计算技术可以帮助系统更高效地处理这些数据。
云计算技术还可以提供更强大的计算和存储能力,支持控制系统进行分布式计算和决策制定。
三、柔性生产线控制系统的发展前景柔性生产线控制系统具有极高的应用价值和发展潜力,未来将会在以下方面得到更深入的发展:1. 物联网技术的应用。
随着物联网技术的不断发展,柔性生产线控制系统可以更好地与物联网技术进行结合,实现实时监控和自动化调度。
- 1、下载文档前请自行甄别文档内容的完整性,平台不提供额外的编辑、内容补充、找答案等附加服务。
- 2、"仅部分预览"的文档,不可在线预览部分如存在完整性等问题,可反馈申请退款(可完整预览的文档不适用该条件!)。
- 3、如文档侵犯您的权益,请联系客服反馈,我们会尽快为您处理(人工客服工作时间:9:00-18:30)。
一种柔性冲压自动化生产线系统的研制⒇邱继红 熊丽英 王玉山 刘 凯 史启礼 宋克威(中国科学院沈阳自动化研究所机器人工程部 110015)摘 要 本文介绍了一种用于大型汽车覆盖件冲压生产的柔性自动化生产线,系统由6台压机、12台上下料机械手、1台翻转传输装置、4台穿梭传输装置及1台磁力分层装置构成.给出了生产线的主要性能指标、机械手结构简图及单元控制系统框图,简要介绍了系统的工作原理.关键词 冲压线,上料机械手,下料机械手1 引言随着我国汽车工业发展规划的日益壮大,汽车覆盖件特别是大型覆盖件冲压生产的手工操作方式已经越来越不适应现代化大规模生产的要求,尤其是汽车的年产量超过15万辆时,这一矛盾更加突出,采用机器人完成压机的上下料工作,构成柔性冲压自动化生产线是解决这一矛盾的一种有效方法,也是现代汽车制造业的重要发展方向.机器人在冲压车间的应用,将冲压工人从单调、繁重而又危险的工作状态下解放出来,提高了生产的效率,同时也避免了大型覆盖件在生产传输过程中因划伤、碰撞、扭曲等带来的质量问题.我所机器人工程部为一汽-大众研制的“一汽捷达轿车冲压自动化生产线”正是针对这种情况而设计的,也是我国第一条自行研制、开发的用于大型覆盖件冲压生产的柔性自动化系统.经过一年的现场安装、调试及试运行,该系统已于1997年底通过国家机械部的验收鉴定.2 系统构成柔性冲压自动化生产线系统由6台压力机、12台上、下料机械手、1台翻转传输装置、4台穿梭传输装置及一台磁力分层装置构成.6台压力机(1台2000吨双动式、5台1000吨单动式,德国ERFU RT 公司生产)串联排列,原为手工生产线.此生产线主要为生产大型覆盖件使用,安装时各压机中心线间距离较长为9m .构成自动化生产线后上下料机械手分别安装于压1.磁力分层装置2.上料机械手3.下料机械手4.翻转传输车5.穿梭传输车图1 柔性冲压自动化生产线机前侧及后侧立柱间的横梁上,完成压机的上、下料任务,不占用地面空间.前后两台压机之间第20卷第6期1998年11月机器人 R OBOT V ol.20,No.6 N ov.,1998⒇1998-06-18收稿DOI:10.13973/ k i .rob ot.1998.06.004由穿梭传输装置完成工件的传送任务.由于第1台压力机为上传动双动式,拉伸后工件的上下方位置与后续的单动式压力机模具要求的位置正好相反,因此1、2台压力机间的传输车上另有一套同步翻转装置,按工艺要求,可以完成工件的180°翻转.3 生产线主要性能指标[1]配套压机: 2000吨双动机械式1台,1000吨单动机械式5台压机间距: 9000mm工件种类: 5种8件(系统可同时存储15种工件程序)同步方式: 压机单次行程,间歇同步生产节拍: 4~5件/分钟工作方式: 示教、手动、故障复位、单循环、联线机械手控制方式: 离线规划,在线示教,连续轨迹控制 重复定位精度: ±0.5mm自由度: 两自由度摇臂式负载能力: 60kg驱动系统: 交流伺服水平行程: 3000m m速度: 4000m m /s运动方式: 关节坐标,直角坐标穿梭传输装置控制方式: 离线编程工作方式: 手动、自动运行速度: 2200m /s 侧移距离: ±350mm 驱动系统: 交流伺服4 机械手结构及本地控制单元工作循环柔性冲压自动化生产线由7个就地控制单元及一个总控制台构成,就地控制单元包括一台压机、一台上料机械手、一台下料机械手及与下料机械手相连的传输装置,如图2所示.图2 机械手结构简图及单元工作情况上料机械手、压机、下料机械手及传输车之间构成循环启动方式,即上料机械手→压机→下料机械手→传输手↑ | 以第一单元为例,机械手运动轨迹及工作循环解释如下.4.1 上料机械手运动轨迹及工作循环S 2点:上料机械手接到启动指令后,首先由初始点运动到循环起始点S 2点,并准备好到磁力分层装置上抓取工件.417第20卷第6期邱继红等: 一种柔性冲压自动化生产线系统的研制418 机 器 人1998年11月S2→S1点:上料机械手接到磁力分层准备好信号以后,向下运动到抓料位置,真空吸盘吸气,机械手抓取一张料片.S1→S2点:上料机械手抓取料片后上升,同时传感器检测料片是否是一张.S2→S3点:上料机械手抓料前行向压机模具内送料,同时由软、硬件共同发出锁住压机滑块动作的安全信号,并检测下料机械手是否处在干涉位置,若条件不满足,上料机械手停止向前运动.S3→S4点:上料机械手下降,将料片放入压机模具中,料片入模位置的准确性一方面取决于机械手的定位精度,另一方面取决于模具的辅助定位装置.S4→S3:上料机械手上升.S3→S2:上料机械手退出模具,返回起始点.准备进入下一个工作循环,并向压机发出指令,滑块下行完成冲压作业.4.2 下料机械手运动轨迹及工作循环S′3:下料机械手接到启动信号后,首先由初始点运动到循环起始点S′3点,并准备好进入压机模具内取料.S′3→S′2:压机滑块完成冲压作业后由下死点返回上死点,升至干涉高度以上时由电子凸轮发出允许下料手进入信号,下料手前行进入模具内取料.S′2→S′1:下料手下降,真空吸盘接触工件.S′1→S′2:真空吸盘吸附牢固后机械手抓件上升.S′2→S′3:下料机械手抓件退出压机,同时发出信号允许上料机械手向模具内送下一张料.S′3→S′4:下料手下降至翻转传输车高度,翻转装置在左、右两侧夹住拉延成形的工件.S′4→S′5:下料手上升,避让工件的翻转空间,并发出启动翻转传输车运动信号,向下一工作单元传递工件.S′5→S′3:工件翻转完毕后,下料手返回循环起始点S′3点,准备进入下一工作循环.5 单元控制系统单元控制系统框图如图3所示.冲压车间环境恶劣、振动、干扰情况严重,因此要求控制系统稳定、可靠、抗干扰能力强.系统采用了德国SIEM EN S公司的中规模可编程控制器S5-115U接一扩展单元做为单元控制器.主机架配置为:电源模块、CPU模块、上下料机械手、传输车位控模块、电子凸轮模块、数字量输入模块等.扩展模块由8块数字量输入、输出模块组成.位控模块完成上、下料机械手及传输车的运动控制功能,采用码盘译码模块外接一绝对码盘作为电子凸轮来实时检测压机滑块的位置.各种传感器及按键信号由DI模块送入PLC中.各种指令信号,如压机滑块的启停控制、保护、工作状态显示等由DO模块输出.由SIEM ENS 公司的O P5操作员面板开发成的示教盒通过CPU模块的串口与PLC相联,可对生产线上的机械手进行示教,同时还可以对各单元的运动故障及部分系统故障进行诊断.PLC程序可用语句表(STL)、梯形图(LAD)或控制系统流程图(CSF)等形式编写.机械手及传输车的运动程序用机床数控标准代码编写,包括数学模型、运动规划、轨迹参数的生成等内容,由编程器下装至位控模块.机械手的示教数据存放在可编程控制器CPU模块的RAM内,工作时根据操作员选择的工件号自动地将对应的示教数据传入位控模块内.由于生产线生产工件种类多,更换模具时要相应更换机械手的端拾器,为防止出现端拾器装错等情况的出现,在每一个端拾器上均安装有编码装置,单元自动检测编码是否正确.图3 单元控制系统框图由于生产线针对大型冲压件设计,所以要求机械手能在重负载、大惯量下高速运行,并满足精度要求.系统采用了SIEM EN S 公司的交流伺服电机做为执行部件,其内置的测速电机及增量式码盘构成速度反馈及位置反馈,电机具有过载、过热保护功能.6 结束语柔性冲压自动化生产线是一个多环节、多设备组成的大系统,不同于一般的单个机器人工作站小系统.生产线中各种设备的设定、调整、联锁、保护等控制系统非常复杂,控制电缆和接线多.压机、模具、物料、机械手本身、传输装置、气动系统等有任何一个环节出现问题或不符合自动化生产的要求,都会直接影响到生产线的顺利运行.由于该冲压生产线原为针对手工操作而设计,因而有以下3个方面不满足自动化联线的要求,因此必须在联线前或在联线的过程中加以解决.1.人工操作压机工作时由操作人员按压机操作按钮控制压机的起停.而在柔性自动化生产线中压机的起、停由各本地控制单元给出,同时各就地控制单元需实时得到压机滑块的位置及上死点停车等情况.因此需设计各就地控制单元与压机控制器之间的接口电路.2.由于目前捷达车的模具是用于手工生产的模具,因此必须对其进行改造,以满足自动化联线生产的要求,改造工作包括:(1)废料应能自动、顺畅地排入废料槽内,而非滞留在模具地.(2)模具应安装辅助定位装置,保证机械手所持工件能正确入模.(3)模具内安装传感器,以检测工件是否正确入模,或废料是否已顺畅排走,以防工件或419第20卷第6期邱继红等: 一种柔性冲压自动化生产线系统的研制420 机 器 人1998年11月模具损坏.(4)每道工序冲压完毕后,工件应能完全脱模,由于机械手不具备视觉、触觉等传感器同时受自由度的限制,因此不能象人一样实现各种复杂的取件动作,所以要求工件在冲压后不能卡在模具内.以便机械手能顺畅地从模具内取出冲压完毕的工件.3.实现自动化联线后,生产线的运行管理生产调度安排就适合自动化生产的特点,适应多品种、中小批量生产的要求.国外由于汽车工业发展较早,早在19世纪60年代中期,就开始有机器人用于汽车冲压件上下料的应用实例[3],由于受技术条件的限制,80年代以前的自动冲压线一般只能生产一种或二、三种零件,柔性差,机械手多为气动或液压驱动,笨重且精度低[3],更改程序困难.80年代以后随着机器人技术,模具结构设计和输送料装置的改进,自动冲压线的柔性有了很大的改善,一条自动生产线可以生产多种冲压件,进入90代后,一条自动冲压线可以生产十几种或种类更多的冲压件[2],而且随着现代科技水平的飞速发展,越来越多的高、新技术出现在柔性自动化冲压生产线中,如无刷直流伺服电机、交流伺服电机的采用、高速、可靠的计算机通信网络、现场总线技术的应用等等.这些高新技术的采用进一步提高了生产线的可靠性,缩短了生产的安装、调试周期,极大地提高了生产效率.柔性冲压自动化生产线在我国汽车行业的采用,提高了汽车的年产量,降低了成本,节约了投资,使我国的汽车工业更具竞争力和生命力.因此,在冲压生产中采用机器人完成压机的上下料工作,构成柔性冲压自动化生产线,必将成为我国现代汽车制造业的一个重要发展方向.参 考 文 献1 一汽-大众捷达轿车冲压自动化生产线技术说明.内部资料,中国科学院沈阳自动化所,19972 周晓平.板冲压力机及其自动冲压线.一重技术,1994,(3)3 Rich ard K M iller.Ind ustrial Robot Handbook.The Fairmon t Pres s,INC,1987RESEARCH AND DEVELOPMEN T OF A FLEXIBLEAUTOMATIC PRESS LINE SYSTEMQIU J iho ng XION G Liying W ANG Yusha n LIU Kai SHI Qili SON G Kew ei (Shenyan g Institute of Automation,the Chines e Academy of S ciences,110015) Abstract T his pa pe r pr ese nts a flexible automa tic pr oduction line for the productio n of la rg e-sca le automo-bile cap pieces,which is co mposed o f6pr esses,12feeding a nd unloading manipulato rs,1tur ning transmis-sio n dev ice,4shuttle tra nsmissio n devices and1mag netic decker.M ain per for mance index o f the productio n line,st ructure dra wing s o f the manipula tor s,a nd blo ck diag rams o f the unit co nt ro l sy stem a re pr esented. Also,the system o perating principle is intr oduced. Key words Press line,feeding ma nipula to r,unlo ading ma nipula to r作者简介 邱继红:男,32岁,博士研究生.研究领域:机器人控制、机器人柔性自动化生产线. 熊丽英:女,高级工程师.研究领域:机器人控制、机器人柔性自动化生产线.。