液力变矩器课程设计说明书
第2章液力变矩器

(2)单向离合器的工作原理
单向离合器又称为单向啮合器、超越 离合器或自由轮离合器,与其他离合器的 区别是,单向离合器无需控制机构,它是 依靠单向锁止原理来固定或连接的,转矩 的传递是单方向的。
当与之相连接元件的受力方向与锁止 方向相同时,该元件即被固定或连接;当 受力方向与锁止方向相反时,该元件即被 释放或脱离连接。汽车自动变速器用单向 离合器主要有楔块式和滚柱式两种。
当车速较低时,锁止控制阀让油液从 油道B进入变矩器,使传力盘两侧保持相 同的油压,锁止离合器处于分离状态,这 时输入变矩器的动力完全通过油液传至涡 轮。
当汽车在良好道路上高速行驶,且车 速、节气门开度、变速器油液温度等因素 符合一定要求时,ECU即操纵锁止控制阀, 让油液从油道C进入变矩器,而让油道B与 泄油口相通,使传力盘左侧的油压下降。
设置导轮后,改变了回流油液的流向, 油液冲击泵轮叶片的背面,促使泵轮旋转。 于是,作用在涡轮上的转矩由发动机的输 入转矩和回流油液的转矩两部分组成。
可见,由于导轮的存在,涡轮上的输 出转矩大于发动机输入转矩。可以想象, 泵轮与涡轮的转速差越大,回流冲击越厉 害,则转矩增加越多;而且随着转速差的 缩小,增加转矩的作用越来越小。图2-3所 示为导轮的结构。
⑦ 使用橇棒等工具使自动变速器壳与 发动机后端分离。 ⑧ 降下高位运输器,取出变速器总成。
⑨ 从变矩器壳内取出编制变矩器(取 出时,应平行拉出,否则可能会导致变矩 器油封损坏)。
2.液力变矩器的清洗
自动变速器的机油污染多表现为在油 中可见到金属粉末。
这些金属粉末大部分来自多片离合器 上的磨耗;清洗时,可加入专用清洗剂或 煤油,在清洗台上一边旋转变矩器,一边 不停地注入压缩空气以便使清洗液作用得 彻底(不能用切开变矩器总成,清洁完毕 再焊接的方法),如图2-8所示。
02液力变矩器
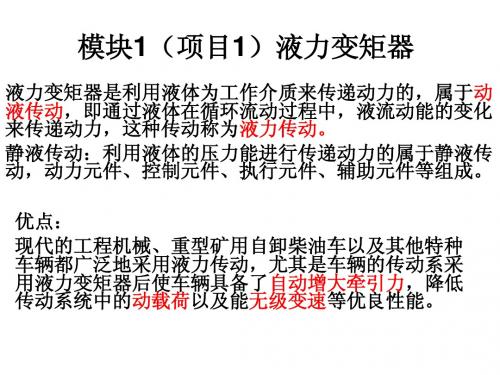
拆装和调整注意事项
• 1. 变矩器与变速箱合箱前,超越离合器以及输入一级齿轮5、输入二 级齿轮8连同轴承应先行装上变速箱。(两个压力阀32和33的压力由设 计和制造保证,拆装时不应随意增减垫圈。) • 2. 变矩器与变速箱合箱后,在固紧周边螺栓和安装变速泵1之前,必 须使变速泵轴线与变速泵安装平面的垂直度在半径80范围内不大于0.03。 • 3. 两个涡轮18和19组装后再一体安装。I涡轮18与涡轮罩23在出厂前 是经过平衡校验的,拆装时应注意两者上的箭头标记必须对齐。 • 4. 最后才安装罩轮25和弹性板28。后者共四片,两圈螺栓孔应校对整 齐以避免某一、两片单独受力。 • 5. 变矩器——变速箱与柴油机合套应采用吊装法。两者对中准确,即 可推入合套。切忌在尚未对中前强行打击合套,以免损坏机件。 • 6. 合套后,由壳体13的窗口P将弹性板28与飞轮22固紧。每两个螺孔 有一垫片20,不得省略。注意应绝对避免任何零件或杂物掉进壳体,一 旦发生,应坚决拆套取出。
双涡轮变矩器油口
• • • • • •
1—(变矩器出口)油温表接头 2—(变矩器出口)管接头(接往散热器进 油口) 3—(变矩器进口)堵头 4—压力阀(调节变矩器进口压力 0.56MPa) 5—(润滑油)管接头(接散热器出油口) 6—背压阀(调节润滑压力0.2MPa) 工作介质:8号液力传动油 工作介质:
变矩器原理图
• • • • • • • • • • 1—— 柴油机飞轮 2——变矩器 3——超越离合器 B——泵轮 D——导轮 T1、T2——涡轮 Z1——输入一级齿轮 Z2——外环齿轮 Z3——输入二级齿轮 Z4——中间输入轴
泵轮B 泵轮B:将柴油机的机械能转换为油液的动能。 涡轮T 涡轮T:将油液的动能还原为机械能。 导轮D 导轮D:反射力矩叠加到涡轮T上,使涡轮力矩大于或小于泵轮力矩,达到变矩的可能。 超越离合器: 超越离合器:将Ⅰ涡轮T1和Ⅱ涡轮T2的二个输出自动整合为中间输入轴的一个输出(变速箱输入)。
液力变矩器教案

教学环节
教学内容
教法说明
复习
引入新课
讲授新课教学环节复习提:1、自动变速器的组成
2、按车辆的驱动方式自动变速器分类
活动二液力变矩器的结构和工作原理
液力变矩器安装位置识别
变矩器是传动系中的重要零件(在发动机和变速器之间)。它用螺栓固定在发动机后端的驱动盘上,随着发动机的旋转而转动。
当发动机高速时,流出涡轮的油液是顺时针流向导轮,打在导轮叶片的反面,单向离合器分离,导轮旋转,油液顺时针流向泵轮内圈。
由于从涡轮叶片下缘流向导轮的液压油仍有相当大的冲击力,只要将泵轮、涡轮和导轮的叶片设计成一定的形状和角度,就可以利用上述冲击力来提高涡轮的输出扭矩
1、指出图示液力变矩器的组成构件
2、根据实物叙述变矩器的油液流向。
其他构件:
单向离合器:涡轮低速时锁住导轮,改变油液流向;但涡轮高速旋转时,导轮旋转,不改变油液流向。
三、液力变矩器的工作原理
怠速或低速时,油液从泵轮的外圈流向涡轮的外圈,从涡轮的内圈流出,由于转速较慢,流出涡轮的油液是逆时针流向导轮,打在导轮叶片的正面,单向离合器锁住,导轮不旋转,油液改变方向顺时针流向泵轮内圈。
一、液力变矩器的作用
1、将发动机的动力平稳的传递到变速器。
2、增加发动机的扭矩。
3、起到飞轮的作用,使发动机运转平稳。
4、驱动变速器的油泵运行。
二、液力变矩器的基本结构
1、泵轮:泵轮安装在变矩器的外壳上,和发动机的曲轴连接。发动机的扭矩传递到泵轮上,然后将液压力传递给涡轮。
2、涡轮:涡轮通过花键和变速器的输入轴连接。
3、导轮:导轮安装在泵轮和涡轮之间的导轮支架上。导轮上有单向离合器,使导轮只能和泵轮一个方向旋转。
2液力变矩器

变矩器各工作轮扭矩作用关系
2.5变矩器的类型
1.按各工作轮在循环圆中的排列顺序可分为 123型(正转变矩器):涡轮旋转方向与泵轮一致 132型(反转变矩器):涡轮旋转方向与泵轮相反 变矩器大多采用123型
1-泵轮 2-涡轮 3-导轮
图2-14 123型和132型变矩器简图 a)123型; b)132型
图2-17 单级二相液力变矩器 1-泵轮;2-涡轮;3-导轮; 4-主动轴5-壳体;6-从动轴; 7-单向离合器
2.6典型液力变矩器结构与特点
2. ZL50装载机液力变矩器
(1)主动部分 (2)从动部分
(3)固定部分
(4)单向离合器
作 用 单向传动
单向锁定
2.7液力变矩器的常见故障与排除
2.7.1油温过高
2.7液力变矩器的常见故障与排除
2.7.2供油压力过低
3.诊断与排除
①检查油位是否位于油尺两标记之间。 ②若进出油管密封良好,应检查进出口压力阀的工作情况, ③如果进出口压力阀正常,应拆下油管和滤网进行检查。如 有堵塞,应进行清洗并清除沉积物;如油管畅通,则需检 修液压泵,必要时更换液压泵。 ④观察液压油是否起泡沫。如果油起泡沫,应检查回油管的 安装情况,如回油管的油低于油池的油位,应重新安装回 油管。
能针对不同的变矩器,分析出其类型特点
学会初步诊断变矩器的常见故障
2.1概念
1. 液力变矩器:利用液体增大转矩并传递动力 液力偶合器:利用液体等大传递动力 动液传动:通过液体在循环流动过程中, 液体动能变 化来传递动力 2.特点 ①自动增大牵引力 ②降低动载荷及减振 ③自动适应外界载荷 ④能无级变速
2.7液力变矩器的常见故障与排除
2.7.3机械行驶速度过低或行驶无力
液力变矩器工作原理学习教案

会计学
1
第一页,共29页。
耦合器
两个相互间没有刚性(ɡānɡ xìnɡ)连接的 叶轮,同样可以进行能量的传递
第1页/共29页
第二页,共29页。
1、液力耦合器的组成(zǔ chénɡ):泵轮、涡轮
发动机曲轴凸缘上 装有外壳,泵轮与 外壳连接(或焊接) 在一起,随曲轴一 起转动,为液力偶 合器的主动 (zhǔdòng)部分。与 泵轮相对安装的涡 轮,与输出轴连接 第2页/共29页 在一起,为液力变
第22页/共29页
第二十三页,共29页。
带锁止离合器的液力变矩器
锁止离合器摩擦片、减震(jiǎn zhèn)弹簧
第23页/共29页
第二十四页,共29页。
减振盘:它与涡轮连接在一起,减振盘上装有减振弹簧,在离合器接合时, 可防止产生扭转振动。
锁止离合器压盘:通过凸起卡在减振盘上,可在油压的作用下轴向移动。 离合器壳:它与泵轮连接在一起,前盖上粘有一层摩擦(mócā)材料,以增 加离合器接合时的摩擦(mócā)力。
第8页/共29页
第九页,共29页。
2.涡轮:涡轮上也装有许多叶片。但涡轮叶片的扭曲 方向与泵轮叶片的扭曲方向相反。涡轮中心 (zhōngxīn)有花键孔与变速器输入轴相连。泵轮叶片 与涡轮叶片相对安装,中间有3~4 mm的间隙。
第9页/共29页
第十页,共29页。
3.导轮:导轮位于(wèiyú)泵轮与涡轮之间,通过单向离 合器安装在与自动变速器壳体连接的导管轴上。它也是 由许多扭曲叶片组成的,通常由铝合金浇铸而成,其目 的是为了变矩器在某些工况下具有增大扭矩的功能。
第27页/共29页
第二十八页,共29页。
变矩器锁止离合器的主要功能是: 在汽车低速时,利用变矩器低速扭矩增大的 特性,提高汽车起步和坏路的加速性; 在高速时,变矩器锁止离合器作用,使液力 偶合(“软连接(liánjiē)”)让位于直接的机 械传动(“硬连接(liánjiē)”),提高传动效 率,降低燃油消耗。
液力变矩器教案

(2)运动特性方程:
n1+αn2—(1+α)n3=0
太阳轮、齿圈和行星架三者的大小关系是:太阳轮<齿圈<行星架
(3)传动规律
1)降速档:
4)倒档
将行星架固定,无论太阳轮为主动件或从动件,齿圈作为从动件或主动件,太阳轮的转动与齿圈的转动方向始终相反。这是因为行星齿轮此时起惰轮作用,所以以主动件相反的方向驱动从动件。如太阳轮为主动件时,由于行星架被固定,行星齿轮只能在行星架上自转而不能绕着太阳轮公转。因此当太阳轮驱动行星齿轮时,一对外齿轮啮合转动方向相反,行星齿轮又驱动齿圈,一对内啮合齿轮转动方向相同,所以太阳轮的转动方向与齿圈相反。这样行星齿轮机构提供了降速倒档。同样以齿圈为主动件,太阳轮为从动件可以实现超速转动的倒档。
特性方程中n3=0,因此有:n1+αn2=0
传动比:ί= n1/ n2=-α传动比为负值,所以反向传力。
5)空档
当行星齿轮机构的所有元件都不受约束,可以自由转动时,则无论从那一个元件输入动力都不会有动力输出。此时行星齿轮机构处于空档位置。
状态
档位
固定部件
主动部件
从动部件
旋转方向
1
降速档
太阳轮
齿圈
行星架
一种是固定太阳轮,另一种是固定齿圈。
固定太阳轮时,齿圈为主动件,行星架为从动件。当动力输入给齿圈时,齿圈将使行星齿轮在行星架上自转,由于太阳轮被固定,则自转着的行星齿轮与行星架将一起绕着太阳轮公转。因为齿圈转动一圈不能使行星架也转动一圈,所以实现了降速转动。因为行星架以较低的速度转动,所以输出扭矩增大。另外,由于太阳轮固定,行星架和齿圈同向转动。
第三章 液力变矩器

按涡轮的型式分类
1. 向心涡轮变矩器 循环圆如图3-21(a)所示 . 正透穿 2. 轴流涡轮变矩器 循环圆如图3-21(b)所示 .接近非透穿 3.离心涡轮变矩器 循环圆如图3-21(c)所示。具有负透穿的 无因次特性.
按循环圆中各叶轮的衔接序分类
1.泵轮—涡轮—导轮—泵轮型 记作“B—T—D—B”,绝大多数变矩器为此型。 2.泵轮—导轮—涡轮—泵轮型 记作“B—D—T—B”,由于位于涡轮前面的导轮叶 片,改变了进入涡轮的液流方向,使损失增大, 效率低 。此外由于涡轮位于泵轮之前,涡轮的转 速使其出口速度矩的改变,直接影响泵轮入口, 使泵轮力矩有很大的改变,所以透穿性特别强, 只适用于特殊的场合。 工程机械绝大多数使用泵轮—涡轮—导轮—泵轮 型变矩器
返回
返回
正透穿型变矩器与汽油机特性配合很合理 。因为: 1)因为起动工况i=i0时,共同工作使原动机在力矩 最大点工作,同时,在该点的变矩系数也是最大 值,那么涡轮力矩也可达到最大,因为
2) i0工况也是机器工作机的由静止起动的工况, 负载的惯性阻力矩最大,需要涡轮有最大的驱动 力矩. 3) 变矩器的最高效率工况与原动机最低油耗工况 为同一工况,这样,使整个机器在最经济工况下 运行。
液力变矩器的特性曲线
什么是液力变矩器的特性曲线 ? 液力变矩器的特性曲线有: 1.输出特性曲线(外特性曲线) 2.原始(类型)特性曲线 3.输入特性曲线 4.通用特性曲线 5.液力变矩器系列型谱
变矩器特性理论分析 :
输出特性曲线——外特性曲线
输出特性是指液力变矩器各参数与涡轮转速之间的关系; 它们是由试验和计算得出来的。
自动变速器教案液力变矩器一
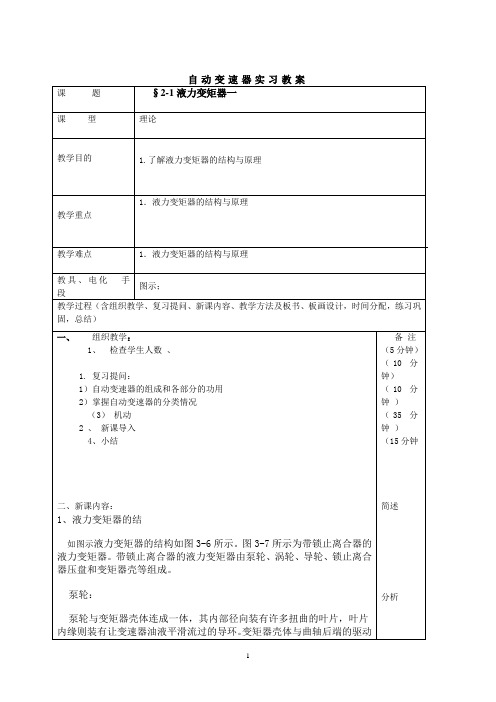
2、离合器的摩擦片的检验;检查离合器的摩擦片,如有烧焦、表面粉末冶金层脱落或变形,摩擦片的花键齿变形,则应更换。
当摩擦片表面上印有符号被磨去或模糊不清,应更换。
也可测量摩擦片的厚度,若小于极限厚度,则说明摩擦片已磨损至极限,应更换。
3、钢片的检验:检查钢片,如有磨损或翘曲变形,则应更换。
4、挡圈的检验:检查挡圈的摩擦面,如有磨损,则应更换。
用厚薄规或百分表检验离合器工作间隙,如间隙不符合标准值,应更换调整片调整。
10、操作要求及注意事项。
- 1、下载文档前请自行甄别文档内容的完整性,平台不提供额外的编辑、内容补充、找答案等附加服务。
- 2、"仅部分预览"的文档,不可在线预览部分如存在完整性等问题,可反馈申请退款(可完整预览的文档不适用该条件!)。
- 3、如文档侵犯您的权益,请联系客服反馈,我们会尽快为您处理(人工客服工作时间:9:00-18:30)。
液力变矩器课程设计说明书内蒙古农业大学汽车设计课程设计说明书学院:机电工程学院班级:车辆工程S日期: 2012年12月28日目录一.课程设计的目的 (3)二.课程设计任务及内容 (3)三.课程设计设计题目 (4)四.设计原始数据 (4)五.设计计算 (5)六.液力操控系统设计 (12)七.参考书目 (13)八.附录:零件图、装配图 (14)设计题目:丰田轿车自动变速器锁止离合器设计一、课程设计的目的汽车设计课程设计是汽车设计课的重要组成部分,也是获得工程师基本训练的一个教学环节。
其目的在于:1、通过汽车部件(总成)的设计,培养学生综合运用所学过的基本理论、基本知识和基本技能分析和解决汽车工程技术实际问题的能力;2、掌握资料查询、文献检索的方法及获取新知识的方法,书面表达能力。
进一步培养学生运用现代设计方法和计算机辅助设计手段进行汽车计算机零部件设计的能力。
3、培养和树立学生正确的设计思想,严肃认真的科学态度,理论联系实际的工作作风。
二、课程设计要求完成的工作内容1、各总成装配图及零件图,采用二维设计和三维设计;2、设计计算说明书1 份,A4 纸。
设计计算说明书内容包括以下部分:1)封面;2)目录(标题及页次);3)设计任务(即:设计依据和条件);4)方案分析及选择;5)主要零件设计及校核计算;6)参考文献(编号,作者、书名,出版单位,出版年月)。
三、《汽车设计课程设计》题目设计题目:丰田轿车自动变速器锁止离合器设计课程设计的内容为:在丰田轿车自动变速器的液力变矩器中设计一锁止离合器,以提高自动变速器稳定工况下的传动效率。
四、原始数据第三组:发动机最大功率:240马力发动机最大功率时转速:4500 r/min发动机最大扭矩:40kgm发动机最大扭矩时转速:2500-3200 r/min车轮B-d:6.90-13英寸汽车总质量:m a=3050 Kg最高车速:175 km/h变速器传动比:I1=1.80, I2=1, I R=2.45锁止传动比:I m=0.82最大变矩比:k=2.55主减速器传动比:I o =3.50液力变矩器中最高油压:4.2 kg/cm2液力变矩器容量:12.5公升液力变矩器工作温度:82-95 o C 液压油最高许用温度:115-120 o C 全油门车速85-100 km/h 时换入直接档 离合器结合时间:取0.45s 离合器储备系数:β=1.25 离合器分离间隙:0.4-0.5 mm 结合期间最大吸热率:110J/s.c ㎡操纵控制系统有关参数:空档和前进档时:发动机750 r/min主油路压力6.0~6.5 kg/cm 2倒车时:发动机1600 r/min 主油路压力16~19 kg/cm 2 钢与纸质浸树材料摩擦系数:0.14 钢与粉末冶金摩擦系数:0.08五、计算 (1)计算力矩为了保证离合器在任何工况下都能可靠地传递发动机的最大转矩, Tc 应大于发动机最大转矩,即:max c e c T T fFZR =β=T c 离合器能传递的最大转矩T emax 发动机最大转矩,Temax=392N ·m ,已知数据。
后备系数β取1.2,已知。
计算离合器能传递的最大转矩为:Tc=βT e max=1.2x392N·m=470.4 N·m。
f摩擦副的摩擦系数,选取f=0.08Z摩擦片工作面,为Z=1F离合器工作压紧力(2)根据经验公式初选摩擦片外径DmaxTeKD=乘用车直径系数K取14.6计算得摩擦片外径 D=289mm,选取D=325mm(3)摩擦片内径 d根据摩擦片外径D 从表1中选取摩擦片内径d=190mm C=d/D=0.585 A=54600表1 离合器摩擦片尺寸系列和参数表外径D/mm 160 18020225252830325 35038405内径d/mm 110 1251415155165175190 195205220厚度b/mm 3.2 3.53.53.53.53.53.53.5 4 4 4c=d/D 0.6870.6940.700.6670.620.5890.5830.5850.5570.540.5431-c30.6760.6670.6570.7030.7620.7960.8020.8000.8270.8430.840单位 面积a (cm 2)106 132160221302402466546 678729908(4)摩擦片厚度b 有三种厚度,选取b =3.5mmR T C C fFz = R c = )(3)(22233d D d D --=263mm (5)摩擦面单位压力p(N/mm 2)][p aFp <=F 是压紧力,RT Ccfz F ==263108.04.470⨯⨯•mN =22357.41Nf 是摩擦片的摩擦因数;Z 是摩擦面数量;a 是摩擦片单片面积(mm 2);[p]摩擦面许用压力,见参考书目1。
P=F/a=0.409 N/ mm 2 < [P]=[0.35~~0.50 N/ mm 2] 符合要求 (4)单位滑磨功为了减少汽车起步过程中离合器的滑磨,防止摩擦片表面温度过高而发生烧伤,离合器每一次结合的单位摩擦面积滑磨功w 应小于其许用值[w]。
224[]()Ww w Z D d π=≤- [w]摩擦面许用单位滑磨功。
* W 结合一次摩擦面总滑磨功。
见参考书目1W=⎪⎪⎭⎫⎝⎛2202221800g r a e i i r m n πm a =3050kg i 0主减速器传动比=3.5 i g 汽车起步变速器档位传动比=1.8, n e 是发动机转速,乘用车取2000r/min r r =(d+2B)/2=270.26mm=0.27026mm 带入数据计算得:W=1.23105⨯Jw=2.25J/mm 2<[w]=[6.88J/mm 2] 符合要求(5)温升速率H R表征摩擦片结合与分离时摩擦生热导致摩擦片温度升高的量。
)10sin 81.9/(301047.0H 10max 1maxR a a e o ae fm m r i i T i i nrm nT --=θηπ公路轿车,θsin 取1/8=0.125; n=1500r/min 总机械效率η取0.88;滚动阻力系数f 取0.015,一般沥青和混凝土道路。
要求:H R /A ≤[H R /A] A 为摩擦片总面积,mm 2;许用值[H R /A]为3.88(N ·m/mm 2·s 1/2) ,小轿车。
带入数据得 : H R = 142211.916JAH R =2.60<[H R /A]=[ 3.88(N ·m/mm 2·s 1/2)] 符合要求(6)扭转减振器的设计计算带扭转减振器的的从动盘结构简图如下图1所示弹簧摩擦式:图1 带扭转减振器的从动盘总成结构示意图1—从动盘;2—减振弹簧;3—碟形弹簧垫圈;4—紧固螺钉;5—从动盘毂;6—减振摩擦片;7—减振盘;8—限位销1)扭转减振器极限转矩T j极限转矩受限于减振弹簧的许用应力等因素,与发动机最大转矩有关,一般可取,T j=(1.5~2.0)T,对于乘用车,系数取2.0。
m axeT j=2.0x392N·m=784N·m2)扭转刚度kϕ(N·m/rad)由经验公式初选 kϕ13≤T j=10192N·m/rad3)阻尼摩擦转矩Tμ可按公式初选Tμ,Tμ=(0.06~0.17)T选取系数=0.12em axTμ=0.12⨯392 N·m=47.04 N·m4)预紧转矩T n减振弹簧在安装时都有一定的预紧。
T n 满足以下关系: T n =(0.05~0.15)m ax e T , 且T n ≤T μ 选取系数0.1T n =0.1⨯392N ·m=39.2N ·m 5) 减振弹簧的位置半径R 0R 0的尺寸应尽可能大些,一般取 R 0=(0.60~0.75)d/2 选取系数0.7 R 0=0.7⨯d/2 =66.5m 6) 减振弹簧个数Z j表2 减振弹簧个数的选取摩擦片外径D /mm225~250 250~325 325~350 >350 Zj4~66~88~10>10根据摩擦片外径D=325mm 选取Zj =8 7) 减振弹簧总压力F ∑当减振弹簧传递的转矩达到最大值T j 时,减振弹簧受到的压力F ∑为F ∑=T j /R 0 =11789.5N 8) 极限转角减振器从预紧转矩增加到极限转矩时,从动片相对从动盘毂的极限转角为2arcsin2R lj ∆=ϕ式中,△l为减振弹簧的工作变形量。
jϕ通常取3-12º,对汽车平顺性要求高或发动机工作不均匀时,jϕ取上限。
具体见参考书目1 选取jϕ =12o(7)从动盘毂的设计计算从动盘毂是离合器中承受载荷最大的零件,它几乎承受由发动机传来的全部转矩。
从动盘毂的花键孔与变速器第一轴的花键轴配合,目前大都采用齿侧定心的矩形花键,花键副之间为间隙配合。
花键结构尺寸的选择可依据从动盘外径D和发动机最大转矩T emax,按表3选取从动盘毂花键尺寸。
表3 从动盘毂花键尺寸系列摩擦片外径D/mm 发动机最大转矩Temax/(N·m)花键尺寸挤压应力cσ/MPa 齿数n外径D’/mm内径d’/mm齿厚t/mm有效尺长l/mm250 200 10 35 28 4 35 10.4 280 280 10 35 32 4 40 12.7 300 310 10 40 32 5 40 10.7 325 380 10 40 32 5 45 11.6 350 480 10 40 32 5 50 13.2 380 600 10 40 32 5 55 15.2 410 720 10 45 36 5 60 13.1 1)根据摩擦片外径D=325mm 选取从动盘毂花键尺寸n =10mm D'=28mm d'=24mm t=5mm l=45mmcσ=11.6MPa2)花键毂轴向工作长度应满足以下两项要求:a. 导向要求。
为了保证从动盘毂在变速器第一轴上滑动时不产生自锁,花键毂的轴向长度不宜过小,一般应与花键外径大小相同,对于工作条件恶劣的离合器,其盘毂的长度更大,可达花键外径的1.4倍。
b. 强度要求。
花键尺寸选定后应进行挤压应力强度校核。
2/)()(2m axdD hZ dD TFnhlFejy'-'='+'==βσF为花键的齿侧面压力;Dd'',分别为花键的内外直径;Z为从动盘毂的数目;T emax为发动机最大转矩392N·m;n为花键齿数;h为花键齿工作高度2mm;l为花键有效长度45mm。