多线切割工艺断线问题的分析
线切割总断丝原因及解决办法
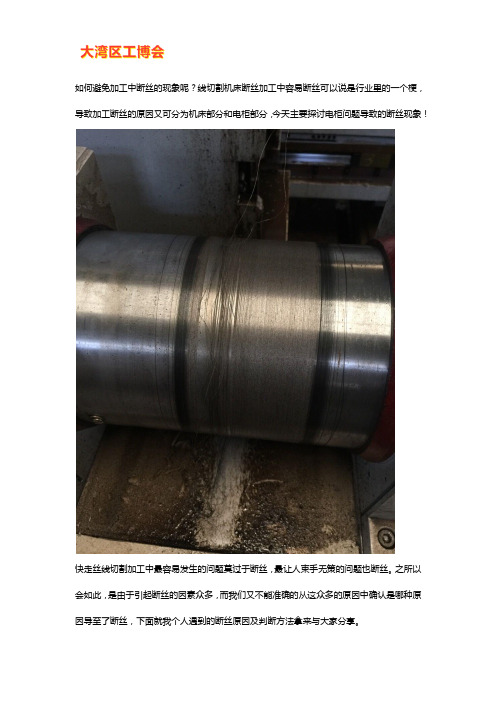
如何避免加工中断丝的现象呢?线切割机床断丝加工中容易断丝可以说是行业里的一个梗,导致加工断丝的原因又可分为机床部分和电柜部分,今天主要探讨电柜问题导致的断丝现象!
快走丝线切割加工中最容易发生的问题莫过于断丝,最让人束手无策的问题也断丝。
之所以会如此,是由于引起断丝的因素众多,而我们又不能准确的从这众多的原因中确认是哪种原因导至了断丝,下面就我个人遇到的断丝原因及判断方法拿来与大家分享。
1.最容易忽视的原因:高频电源性能
电源能正常加工一般就认为电柜是好的,其实有两项性能对断丝影响很大,一是输出脉冲含有直流分量,二是有负向脉冲。
这两项性能简单的测量是无法发现的,只能用专业的测试仪才能检查出来;
2.输出的脉冲含有直流分量会使脉间时间内放电间隙不能有效的恢复绝缘状态,导致加工不稳定而断丝;
3.输出脉冲中有负向脉冲会使钼丝损耗加快而发生断丝;
在线切割加工电流不大、工件也不厚,又没有其它明显的断丝原因,断丝又频繁发生,基本就可以判断高频电源性能有问题了。
切割的一般异常情况分析
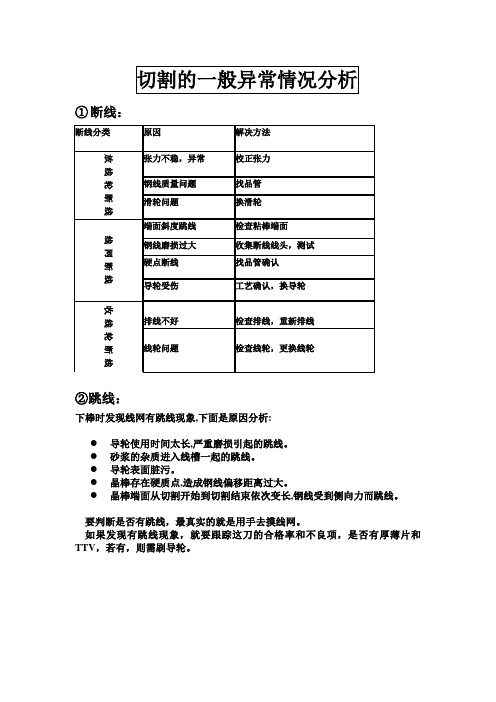
① 断线:
断线分类 放 线 轮 断 线 原因 张力不稳,异常 钢线质量问题 滑轮问题 端面斜度跳线 线 网 断 线 钢线磨损过大 硬点断线 导轮受伤 解决方法 校正张力 找品管 换滑轮 检查粘棒端面 收集断线线头,测试 找品管确认 工艺确认,换导轮
②跳线:
下棒时发现线网有跳线现象,下面是原因分析: 导轮使用时间太长,严重磨损引起的跳线。 砂浆的杂质进入线槽一起的跳线。 导轮表面脏污。 晶棒存在硬质点,造成钢线偏移距离过大。 晶棒端面从切割开始到切割结束依次变长,钢线受到侧向力而跳线。
要判断是否有跳线,最真实的就是用手去摸线网。 如果发现有跳线现象,就要跟踪这刀的合格率和不良项,是否有厚薄片和 TTV,若有,则需刷导轮。
收 线 轮 断 线
排线不好 线轮问题
检查排线,重新排线 检查线轮,更换线轮
线切割机床常见的断丝原因汇总

对于在机床加工行业里,线切割的断丝故障是一件非常令劳动者不愉快的事情,它既影响到工作人员的工作热情,还会降低工作的效率。
谈起断丝故障,大多数的人认为与钼丝的粗细,钼丝的松紧度以及导丝解构的运行有关系。
不可否认,这些问题的存在是容易导致线切割断丝的发生,但除此之外还有其他的一些故障的存在会导致断丝的发生:
一、与工件相关的断丝
例如工件铸造机性能的好坏,工件本身的应力的大小,工件的位置发生的变动等。
其中,在使用工件时,建议使用铸造机能较好的,那样的话其淬透性比较好,变形幅度比较小,经常的锻造淬火也不容易导致断丝发生,工件铸造机能茶,不经常锻造淬火的工件在加工前建议经过一番高温归火,这样更容易消除它本身的应力,减少断丝的发生。
二、与电流相关的断丝
线切割的运行过程中,电源处的电流量突然变大变小或者脉冲电流过大时容易造成断丝的发生。
其中短道电流峰值过大容易导致电极丝变暖造成收缩而烧断,高频脉冲负波的增大容易造成电极丝的腐蚀,影响到钼丝的寿命;故此,为了保证线切割减少断丝的发生,在设备运行时建议使用调节器确保电流电压的稳定性。
三、与工作操作相关的断丝
工作人员在线切割机床的应用中,采取的不适当操作也容易引起断丝的发生,例如换挡不迭时的逼迫高频电流接通,半途突然停机时没有提前堵截高频电源,或者更换定位块时压持不准引发的钼丝需求不足等,这些操作中的不当都是造成设备发生断丝并停工的直接原因。
此外,在工作台的挪动过程中,速度的不稳定或者不均匀也是容易造成断丝情况发生的。
这
是因为工件的线切割依靠丝杆来保证,而丝杆与螺母间的间隙考的是弹簧来排除,当丝杠滑行不畅或者弹簧力较差时都会造成工作台的挪动,工作台的不规则挪动势必引起高频电流的短路以及断丝的发生。
线切割加工中常见工艺问题分析与解决办法

2007年3月第35卷第3期机床与液压M A C H I N ET O O LSH Y D R A U L I C SM a r.2007V o l.35N o.3线切割加工中常见工艺问题分析与解决办法鲍中美"湖北汽车工业学院!湖北十堰442002#摘要!针对线切割加工中断丝与频繁短路切割速度慢及加工表面粗糙度差硬质合金类材料加工效果差铝材加工效果差等常见工艺问题经过分析并结合生产实践给出科学有效的解决办法关键词!线切割工艺问题中图分类号!T G66 文献标识码!B文章编号!1001-3881"2007#3-225-10 引言目前国内外的线切割机床已占电加工机床的60%以上在线切割加工中因为各种因素的影响常常会带来一些工艺问题直接影响加工质量和加工效率通过对线切割加工中常见工艺问题的分析找到实际有效的解决办法对保证加工质量和提高加工效率极其重要必将引起人们越来越多的关注1 断丝与频繁短路1电极丝质量差电极丝粗细不匀强度差打弯易折过了有效期限解决办法是选购质量好的电极丝2导轮磨损导轮V形槽的圆角半径超过电极丝半径造成电极丝抖动易造成频繁短路储丝筒换向瞬间更易造成断丝解决办法是更换新导轮新轴承3电参数过大应根据加工对象选择合理的电参数如脉冲间隔过小脉冲宽度又过大就易造成断丝和频繁短路解决办法是合理选择电参数4工件变形因工件变形造成夹丝短路引起断丝解决办法工件尽量使用热处理淬透性好变形小的合金钢毛坯件需要锻造避免夹层含有杂质的工件5进给速度选择不合理过跟踪时短路电压波型浓工件蚀除速度低于进给速度间隙接近于短路易造成断丝频繁短路欠跟踪时工件蚀除速度大于进给速度间隙近于开路造成电极丝抖动也易造成断丝频繁短路解决办法是选择最佳跟踪速度调节合理的变频进给速度6工作液脏工作液太脏悬浮的加工屑太多间隙消电离变差洗涤性也变差不利于排屑间隙状态也变差对放电加工不利也易造成断丝频繁短路解决办法是更换新的工作液按操作工艺合理配制导电块本身磨出深沟造成断丝解决办法是更换新的导电块或将导电块转一角度使用8储丝筒跳动往往是因储丝筒轴承磨损或损坏造成储丝筒跳动引起电极丝叠丝断丝解决办法是更换轴承从新校验储丝筒精度9脉冲电源有故障脉冲电源有晶体管损坏漏电负波太大及各项电参数改变都会造成断丝频繁短路解决办法是更换晶体管维修好脉冲电源10机械故障x7坐标丝杠的磨损储丝筒丝杠的磨损及传动齿轮的磨损不但影响加工质量精度也易造成断丝和频繁短路解决办法是更换丝杠或传动齿轮维修好机械保证机械正常运转2 切割速度慢$加工表面粗糙度差1切割速度和表面粗糙度是成反比的两个工艺指标所以必须在满足表面粗糙度的前提下再追求高的切割速度必须根据不同的加工对象选择合理的电参数是非常重要的2切割速度慢表面粗糙度差与进给速度有很大关系进给速度调整得过快超过工件的蚀除速度会频繁地出现短路造成加工不稳定使实际切割速度降低加工表面也会发焦而呈褐色工件上下端面处有过烧现象进给速度调整得太慢低于工件的蚀除速度偏开路脉冲利用率低切割速度慢加工表面质量也不好出现不稳定条纹或出现烧蚀现象所以进给速度必须调整得适宜加工稳定切割速度高加工表面细而亮丝纺均匀可获得较好的表面粗糙度和较高的切割速度3 硬质合金类材料加工效果差1硬质合金类材料由于含高熔点的碳化钨碳化钛成分因此加工速度低且易于产生表面微裂纹解决办法是使用专用脉冲电源2根据在用设备选择合理的电参数例如选择窄脉宽大峰值电流提高峰值电压使硬质合金大部分在汽化状态下汽化爆炸抛出熔化而又冷凝图3 折向器调节单元液压原理图折向器调节单元可采用图3所示的液在折向器控制单元中不设微动调节功能,采用微机发出指令直接控制先导阀(一组电磁球阀>,再由先导阀操纵大通径插装阀实现液压放大,从而对关闭等操作O得电时,插装阀A和B的控压力油经阀A注入接力器右腔,推。
线切割断丝问题浅析
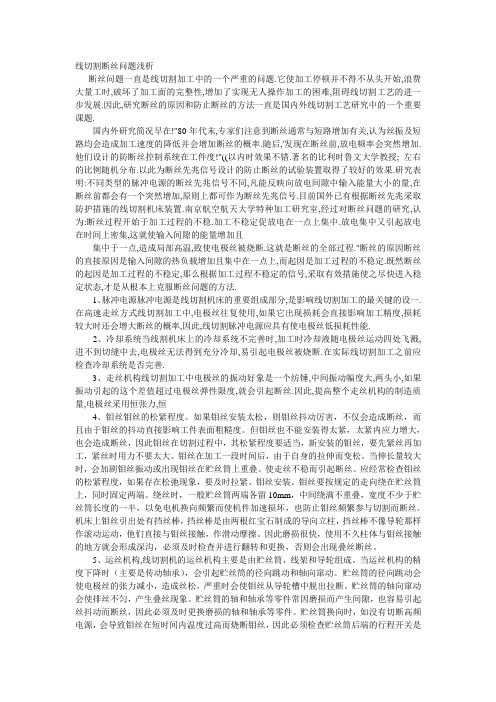
线切割断丝问题浅析断丝问题一直是线切割加工中的一个严重的问题.它使加工停顿并不得不从头开始,浪费大量工时,破坏了加工面的完整性,增加了实现无人操作加工的困难,阻碍线切割工艺的进一步发展.因此,研究断丝的原因和防止断丝的方法一直是国内外线切割工艺研究中的一个重要课题.国内外研究简况早在!"80年代末,专家们注意到断丝通常与短路增加有关,认为丝振及短路均会造成加工速度的降低并会增加断丝的概率.随后,'发现在断丝前,放电频率会突然增加.他们设计的防断丝控制系统在工件度!"((以内时效果不错.著名的比利时鲁文大学教授; 左右的比例随机分布.以此为断丝先兆信号设计的防止断丝的试验装置取得了较好的效果.研究表明:不同类型的脉冲电源的断丝先兆信号不同,凡能反映向放电间隙中输入能量大小的量,在断丝前都会有一个突然增加,原则上都可作为断丝先兆信号.目前国外已有根据断丝先兆采取防护措施的线切割机床装置.南京航空航天大学特种加工研究室,经过对断丝问题的研究,认为:断丝过程开始于加工过程的不稳.加工不稳定促放电在一点上集中.放电集中又引起放电在时间上密集,这就使输入间隙的能量增加且集中于一点,造成局部高温,致使电极丝被烧断.这就是断丝的全部过程."断丝的原因断丝的直接原因是输入间隙的热负载增加且集中在一点上,而起因是加工过程的不稳定.既然断丝的起因是加工过程的不稳定,那么根据加工过程不稳定的信号,采取有效措施使之尽快进入稳定状态,才是从根本上克服断丝问题的方法.1、脉冲电源脉冲电源是线切割机床的重要组成部分,是影响线切割加工的最关键的设一.在高速走丝方式线切割加工中,电极丝往复使用,如果它出现损耗会直接影响加工精度,损耗较大时还会增大断丝的概率,因此,线切割脉冲电源应具有使电极丝低损耗性能.2、冷却系统当线割机床上的冷却系统不完善时,加工时冷却液随电极丝运动四处飞溅,进不到切缝中去,电极丝无法得到充分冷却,易引起电极丝被烧断.在实际线切割加工之前应检查冷却系统是否完善.3、走丝机构线切割加工中电极丝的振动好象是一个纺锤,中间振动幅度大,两头小,如果振动引起的这个差值超过电极丝弹性限度,就会引起断丝.因此,提高整个走丝机构的制造质量,电极丝采用恒张力,恒4、钼丝钼丝的松紧程度。
断线分析
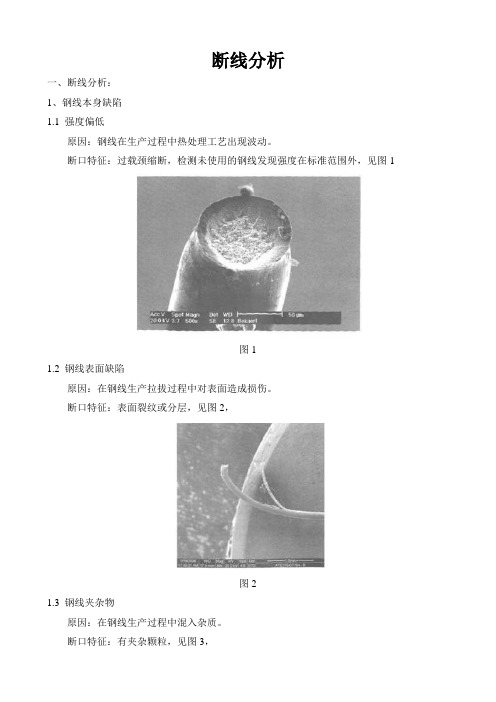
断线分析一、断线分析:1、钢线本身缺陷1.1 强度偏低原因:钢线在生产过程中热处理工艺出现波动。
断口特征:过载颈缩断,检测未使用的钢线发现强度在标准范围外,见图1图11.2 钢线表面缺陷原因:在钢线生产拉拔过程中对表面造成损伤。
断口特征:表面裂纹或分层,见图2,图21.3 钢线夹杂物原因:在钢线生产过程中混入杂质。
断口特征:有夹杂颗粒,见图3,图32、切片设备或其他原因2.1 工字轮变形引起排线松动或夹线原因:工字轮强度不足以支撑钢线压力引起变形,并造成钢线排线松动或夹线。
断口特征:过载颈缩断,放线侧工字轮靠近法兰边外排线松动,严重时工字轮明显变形。
见图5,图5解决方案:在切割前仔细检查工字轮是否变形,切割过程中要注意跟踪钢线的跳动是否有异常。
2.2 压线:原因:操作不慎线头松动并重新抬起时钢线线头从下一圈钢线中穿过造成放线压线断线。
断口特征:过载颈缩断或竹节状,通常容易伴随切割线痕,切割后废线呈卷曲状。
见图6,图6解决方案:建议在一次断线后将放线轮上的钢线转掉几百米,可以有效防止出现因操作失误造成压线。
2.3 工字轮毛刺原因:工字轮上有凿伤痕迹或毛刺,放线时钢线挂到其上造成断线(收线轮有毛刺则会造成收线侧断线)。
断口特征:过载颈缩断或表面损伤。
见图7,图72.4 切割设备影响原因:收线轮导线轮摩擦过大或切透,放线轮和收线轮随动性不佳(控制系统故障);张力检测设备故障(张力臂摆动异常)。
断口特征:过载颈缩断或不规则断口。
见图8,图8解决方案:消耗性物品应在切割前检查是否需要更换,定期检查测试收放线轮随动性,切前检查压缩空气是否正常,织完线网后加上张力,正反转动几圈,查看是否异常;定期检查各个传感器是否异常。
2.5 收线轮排线质量原因:收线轮排线成桶形,引起收线张力急剧跳动。
断口特征:过载颈缩断或不规则断口。
见图9,图9解决方案:调整收线排线器的工艺参数,检查排线器是否出现机械故障(排线器丝杠要定期检查是否磨损过大)。
多线切割机断线原因分析及解决办法【妙】
1.收线口断线处理:(1)发生断线故障时首先做好记录:测量断线处线的直径、断线位置等,一般收线处发生断线有以下几个原因:①线损过大:造成线损过大的原因有进线量偏少、刀口进砂少、碳化硅磨损过大(更换新液)。
②检查有无掉料。
③导轮磨损严重:如果导轮磨损过大也会造成断线,而且这个原因的可能性非常大,实际工作中注意判断导轮的磨损情况具体判断。
④排线问题: 检查收线轮两端是否出现塌陷或凸起的状态,如果有则为排线设置不合适,调整方法咨询烟台力凯电子科技有限公司技术人员。
⑤收线轮问题:判断线轮是否锁紧、收线轮是否变形过大造成运转中摆动过大。
(2)线网断线处线头和缠绕到线导轮上的钢线清理干净,如果切割产品中间有钢线要及时清理干净,防止钢线缠绕造成其他部位断线和误报警发生;(3)在断线处抽取最外边的一根钢线连接到收线轴,低速低张力运行,待转多圈后再增加到工作使用的张力;2.放线口断线处理(1)一般放线处发生断线有以下几个原因:①导轮磨损严重:如果导轮磨损过大也会造成断线,而且这个原因的可能性非常大,实际工作中注意判断导轮的磨损情况具体判断情况。
②检查有无掉料现象。
③排线问题: 检查收线轮两端是否出现塌陷或凸起的状态,如果有则为排线设置不合适,调整方法咨询烟台力凯电子科技有限公司技术人员。
④压线造成断线:如果出现此种状态有可能为上次接线时线头没有处理好⑤放线轮:放线轮是否锁紧、放线轮是否变形造成摆动过大。
(2)放线断线处理:退刀,清洗干净罗拉,整理好断线出现的线头。
(3)将断线后出现的线头打好结接好,低速低张力运行,将线头部分带入到收线轮后,此时增加收放线张力到工作值,将产品上升到断线位置,对好刀口继续工作即可。
3.线网断线处理(1)一般线网处发生断线有以下几个原因:①检查有无掉料现象;②刀口进砂少:检查出液口有无堵塞、是否能覆盖全部产品;③砂液粘度:如果粘度过大会造成切割能力减弱,形成线弓过大以至于断线;④放线轮:放线轮是否锁紧、放线轮是否变形造成摆动过大(2)处理方法:退刀并将卷绕在罗拉上的线去掉,重新绕线。
线切割断丝原因和参数设置
线切割断丝原因分析:1.快走丝机床加工中断丝的主要原因若在刚开始加工阶段就断丝,则可能的原因有:(1) 加工电流过大(2) 钼丝抖动厉害。
(3) 工件表面有毛刺或氧化皮。
若在加工中间阶段断丝,则可能的原因有:(1) 电参数不当,电流过大。
(2) 进给调节不当,忽快忽慢,开路短路频繁。
(3) 工作液太脏。
(4) 导电块未与钼丝接触或被拉出凹痕。
(5) 切割厚件时,脉冲过小。
(6) 丝筒转速太慢。
(7)管道堵塞,工作液流量大减若在加工最后阶段出现断丝,则可能的原因有:(1) 工件材料变形,夹断钼丝。
(2) 工件跌落,撞落钼丝。
解决办法:1、加工参数:跟踪不要太紧,否则易出现短路,而短路会造成钼丝电流过大,局部产生高温,加速钼丝老化、脆化,易折。
短路电流应设在2a以下为好。
2、将脉宽挡调小,将间隙挡调大,或减少功率管个数3、贮丝筒换向时,未能及时切断高频电源,使钼丝烧断4、检测机床电路部分,要保证先关高频再换向5、工作液使用不当(如错误使用普通机床乳化液),乳化液太稀,使用时间长,太脏6、脉冲电源削波二极管性能变差,加工中负波加大,使钼丝短时间内损耗加大脉宽、脉间参数设置脉宽:线切割脉冲宽度越宽,单个脉冲的能量就月大。
切割得就越快,由于放电时间长,所以加工比较稳定。
但光洁度就越不好。
你要想光洁度好就要把脉宽调小。
脉间:说简单的就是给脏东西排出来的通道大小。
由于厚度大的工件排渣困难,所以就要加大脉间,给排渣有充裕的时间,另一方面减少生成腐蚀物。
使得加工稳定,少断丝脉冲:调整参数:脉宽越大,电流越大,加工越快,不过光洁度越差。
脉间越大,电流越小,加工速度慢,光洁度好。
一般加工厚度100以下的,可以用脉宽30us,脉间150us。
这个参数比较常用脉冲宽度操作方法:旋转“脉宽选择”旋钮,可选择8μs~80μs脉冲宽度,分五档,分别为1档为8μs,二档为20μs,三档为40μs,四档为60μs,五档为80μs选择原则说明:脉冲宽度宽时,放电时间长,单个脉冲的能量大,加工稳定,切割效率高,但表面粗糙度较差。
浅析线切割常见断丝原因及处理方法
网 络
( 未见 尚 实际应 用于汽 用) 车和航空 领域
表 1TCN lxa 和 TP TA 、FeRy T 三种协议在其它方面 的比较 三 、 结 束 语 未来若干年问C N A 总线将继续充当在汽车业 电子网 络架 构 的统治 角色 。汽 车工 业将 慢 慢 改变 它 的 电子 架 构 。最有 可能 的是 ,采用 一种 L N A I 、C N和 F e R y混 lx a 合的协议方 案 。 另一种 方式 是 , 多数汽 车工程 师认识 到 他们将需要 一个 比较大 的 “ 数据 管道 ” ,这 时 M tr l o oo a
传输 速率( p) Ms b
1
1 0
5
传输 效率
平均每 包数据 (b e ) 8y s t
有5y s 余数据 bt 冗 e
平均每包 数据
(5b e)有 24 ts y
平均每 包数据
( 0ye) b e 2 bts 有4y s 4 t
参考 文献 :
[] w . n e r p r . o . 1 w wha s n e o t c m
h a er C O e d R
cl+ a( H C f k /^ K O
其 议服务 他协
主 机时fN . 步 - J
分布时间 同步; 分布时 总线 问同步; 总 节点 监视器. 线冗余 线监 双 视器;网 络成员 检 查,双 线冗余
[ ] h r e .M r a ,S n o e h i a d — 4 C a l sJ u r y e ir T c n c l E i
CN A
小于lbtsc 动力传输、 M /e i 底盘、车载电子 现在
浅谈线切割机床断丝的原因及解决方法
非常普及 的高精 度特 种加 工技 术 , 在 机械 制 造业 得到
广泛 的应用 , 尤其 是在模 具制造 方面 , 几 乎成为 必不可 少 的加 工方 法 。在 一 定条 件 下 可 以 实现 无 人 监 控加
善; ( 9 ) 储丝筒转 速太 慢 , 使 钼丝 在工 件 区停 留 时间 过
解 决方法 : 选 择 合适 的切 割路 线和 材料 及 热 处理
工艺 , 使变形影 响尽量减少。
6 、 工件割完 , 落下时断丝
原 因: 工 件跌落时撞断钼丝 。 解决方法 : 快割完时 , 用小磁铁 吸 紧或 用铁 夹夹 紧
( 3 ) 用工作液 或试 割时调低 电压档 ; ( 4 ) 调整轴 承 间隙 或更换导 轮 、 轴承 ; ( 5 ) 清除氧化皮 、 毛刺。
5 、 工件 接近切完时断丝 原因: 工件材 料变 形 , 夹断 钼丝 ( 断前 多会 出 现短 路) 。
方向移动, 再上紧螺钉, 使高频断开后储丝筒再换向。
2 、 刚开始切割时 即断丝
原 因是 : ( 1 ) 电流过 大 ; ( 2 ) 进 给不 稳 , 切入 速度过 快; ( 3 ) 试割时 不用工作 液 ; ( 4 ) 钼丝抖 动厉 害; ( 5 ) 工 件表面有毛刺 、 氧化皮或锐边 。 那 么针对上述情 况可以采用 以下解 决方法 : ( 1 ) 调 整 电参数 , 减小电流 ; ( 2 ) 刚切入时应 将进 给速 度调慢 ;
1 2 6
江
西
化
工
2 0 1 4年第 2期
浅 谈 线 切 割 机 床 断 丝 的原 因及 解 决 方 法
张 美 兰
( 江西旅游商贸职业学院 , 江西 南 昌 3 3 0 1 0 0 )
- 1、下载文档前请自行甄别文档内容的完整性,平台不提供额外的编辑、内容补充、找答案等附加服务。
- 2、"仅部分预览"的文档,不可在线预览部分如存在完整性等问题,可反馈申请退款(可完整预览的文档不适用该条件!)。
- 3、如文档侵犯您的权益,请联系客服反馈,我们会尽快为您处理(人工客服工作时间:9:00-18:30)。
多线切割工艺断线问题的分析
摘要:在多线切割工艺中,镀铜金属线对硅单晶切割片的质量有着重要影响,成为多线切割工艺需要控制的重要辅料。
断线问题一直是困扰多线切割工艺人员的主要问题之一,一直得不到有效的解决,本文从材料、设备、工艺以及人员等多个视角对断线问题进行了分析,并给出相应的解决措施。
关键词:硅钢线断线多线切割钢线破断力
多线切割工艺的基本原理是通过镀铜金属线携带砂浆按一定的速度对硅单晶进行切割。
在切割过程中,断线问题是困扰多线切割工艺技术人员的主要问题之一,该问题的解决对硅片的质量和成品率有着非常重要的意义[1-3]。
随着硅单晶尺寸逐步增大以及硅片向越来越薄的方向发展,断线问题对设备有效运行时间以及成本控制等带来的影响日趋显著,因此断线问题成为多线切割工艺丞待解决的主要技术问题之一。
在多线切割工艺领域,鲜有关于断线问题的文献报道。
本文从材料、设备、工艺以及人员等多个视角对断线问题进行了分析,以期给出相应的解决措施,为多线切割工艺人员解决断线问题提供一些解决方案。
1 断线问题的原因分析及解决措施
断线问题是多线切割工艺中的常见问题之一,本文从材料、设备、
工艺以及操作人员等角度进行了分析,具体如下。
1.1 镀铜金属线质量缺陷导致的断线问题及解决措施
在多线切割工艺中,镀铜金属线是在一定的张力条件下以一定的速度与硅单晶之间相互作用,从而实现对硅单晶的切割。
在切割过程中,镀铜金属线需要承受一定的拉力,从而镀铜金属线需要具有一定的强度,并且表面应无瑕疵、无杂质。
镀铜金属线的质量缺陷是造成断线问题的一个主要因素,可以从镀铜金属线的质量控制入手,严格控制镀铜金属线的强度值、外观质量,必要时可以采取复验强度、外观检验等措施,以防止镀铜金属线在多线切割过程中出现断线问题。
(1)断线原因:钢线生产过程中制造工艺出现问题,造成镀铜金属线的强度偏低。
(2)断线原因:在钢线生产过程中混入杂质,形成镀铜金属线夹杂物。
(3)断线原因:在钢线生产拉拔过程中对钢线表面的损伤,形成镀铜金属线表面缺陷。
1.2 设备异常以及人员操作不当
多线切割设备异常与人员操作不当也是形成断线问题的因素之一,二者往往交织在一起,难以完全区分开,本文将这两个因素放到一起进行讨论。
1.2.1 工字轮变形引起排线松动或夹丝
工字轮强度不足以支撑钢丝压力引起变形,并造成钢线排线松动或夹丝,从而造成切割过程中过载颈缩断,放线侧工字轮靠近法兰边处排线松动,严重时工字轮明显变形。
该问题可采取事前检查、事中监控的措施进行控制,即在切割前仔细检查工字轮是否变形,切割过程中要注意跟踪钢线的跳动是否有异常。
1.2.2 工字轮毛刺
工字轮上有凿伤痕迹或有毛刺,会出现钢线被刮在其上而在放线端或收线端造成断线。
其具体表现为过载颈缩断或表面损伤。
工字轮的质量问题可以通过工字轮外观检查加以控制,从而防止有缺陷的工字轮带病工作。
1.2.3 压线
在穿线操作的过程中,由于操作人员的操作不慎导致线头松掉并重新拾起时钢线线头从下一圈钢线中穿过造成放线压线断线,其断口特征为过载颈缩断或竹节状,通常容易伴随切割线痕,切割后废线呈卷曲状。
该问题通常在一次断线后出现,可以将放线轮上的钢线转掉几百米,可有效预防因操作失误而造成的压线现象。
1.2.4 切割设备影响
多线切割设备本身的精度出现问题也会导致断线问题,如收放线
轮导线轮磨损过大或被切透、放线轮和收线轮随动性不佳、控制系统故障、张力检测设备以及张力臂摆动异常等。
这类设备问题所造成的断口特征表现为过载颈缩断或不规则断口。
这类设备问题可通过采取设备的点检、日常维护保养以及事前检查等措施加以解决,如消耗性物品应在每刀切割前检查是否需要更换、定期检查测试收放线轮随动性以及切割前检查压缩空气是否正常。
1.3 工艺条件不匹配
多线切割工序是一个系统性较强的工序,涉及工艺环节较多,只有各环节之间良好匹配,才能在保证工序正常流转并得到各项性能具佳的硅片。
切割工序的胶、砂浆、洁净程序等均会对金属线的性能产生不同程度的影响,以下给出了因工艺条件不匹配而造成的断线问题,并给出了相应的解决措施。
(1)断线原因:砂浆配比或者质量影响到钢线携带砂浆量及切削能力,或直接对钢线造成损伤。
该问题归结为砂浆原因造成磨损量过大断线。
解决措施:严格按照规定配制砂浆如烘制金刚砂,砂浆配制室清洁等。
(2)断线原因:粘胶不当,四周去胶不干净,硅棒对接垂直度。
该问题归结为粘胶或硅棒对接质量问题。
解决措施:将晶棒四周残余的胶水去除干净,晶棒粘完后检查对接是否平行。
(3)断线原因:钢线在线网上因导轮槽磨损、导轮槽中有杂质、硅棒拼接等原因跳线,导致某些导轮槽内有多根钢线互相压住引起断线。
该问题归结为跳线问题。
解决措施:切割前完全清理导轮槽、压缩空气吹,钢丝刷刷等,检查导线滑轮是否需要更换。
(4)断线原因:砂浆中混人硬质异物如碎片等,或者在导线槽导轮槽内有未清理干净的碎硅渣等,对钢线造成刮伤。
该问题归结为导轮槽或导线槽有异物。
解决措施:切割前仔细清理设备包括导轮槽、各挡板、线网等,严格按照规定清洗导轮槽。
2 结论
断线问题是多线切割工艺的主要问题之一,本文通过从材料、设备、工艺以及人员等四个角度进行分析,得出如下的初步结论。
(1)镀铜金属线的自身质量是造成断线问题的主要因素,需要密切关注镀铜金属线的强度以及外观质量。
(2)设备维护保养以及事前检查是预防断线问题的有效措施,需要将这些措施落到实处。
(3)人员因素是造成断线问题不容忽视的因素,需要从制度上规范人员操作,杜绝
因人员因素造成的断线问题。
(4)多线切割工艺是一个综合性较强的工艺,各环节匹配是切割工艺人员需要考虑的首要问题。
参考文献
[1] 檀柏梅,牛新环,赵青云,等.单晶硅线切割技术及切削液的分析研究[C]//第十四届全国半导体集成电路、硅材料学术年会论文集珠海,2005:385-387.
[2] 王小军,孙振亚,硅片切割技术的现状和发展趋势[J].超硬材料工程,2011,23(6):19-23.
[3] 种宝春,靳永吉,罗嘉辉,多线切割机的切割运动分析[J].电子工业专用设备,2010,40(181):31-34.。