焦炉气制合成氨尿素(18-30规模)全厂工艺指标
利用焦炉气生产合成氨工艺路线探讨

利用焦炉气生产合成氨工艺路线探讨焦炉气是指高炉冶金过程中产生的含有一氧化碳、二氧化碳、氮气等成分的气体。
合成氨是一种重要的化工原料,广泛用于制备尿素、硝酸等产品。
本文将探讨利用焦炉气生产合成氨的工艺路线。
合成氨工艺主要分为两个步骤:制氢和合成氨。
首先是制氢步骤。
焦炉气中的一氧化碳可通过水煤气变换反应(WGS)转化为二氧化碳和氢气。
该反应的化学方程式为:CO+H2O⇌CO2+H2在该反应中,需要加入一定的催化剂,常用的催化剂有铁、铬、镍等。
此步骤可以通过加热焦炉气到一定温度,然后与适量的水蒸气混合后通过催化反应器进行反应,生成含有一定量的氢气和二氧化碳的气体。
制氢后,接下来是合成氨步骤。
合成氨的反应是一种低温高压的反应,一般需要在200-300摄氏度和高达200-350巴的压力下进行。
合成氨的化学方程式为:3H2+N2⇌2NH3在该反应中,需要选择合适的催化剂。
目前常用的催化剂是铁-镁体系或铁-钛体系。
合成氨反应是一个放热反应,通过加热实现放热反应的平衡。
此步骤需要在固定反应器中进行,反应结束后,得到合成氨气体。
在整个合成氨工艺过程中,还需要考虑到气体的净化和循环利用。
由于焦炉气中可能含有硫化氢、氰化氢等有毒成分,需要进行净化处理。
一般可以采用吸收、吸附等方法去除有害成分,确保气体的纯净度。
此外,在环保方面也需要关注工艺过程中的能源利用和废物处理。
合成氨工艺需要大量的能源供应,常用的能源供应方式包括天然气、煤炭等,需要考虑能源的有效利用和减少二氧化碳等污染物的排放。
同时,在合成氨工艺中,也会产生一定的废水和废气,需要采取相应的处理措施。
综上所述,利用焦炉气生产合成氨工艺路线涉及到制氢和合成氨两个步骤。
制氢通过焦炉气和水蒸气的反应产生氢气和二氧化碳;合成氨则通过在合适的温度和压力下,氢气和氮气进行反应生成合成氨。
整个工艺过程需要考虑到气体的净化和循环利用,以及能源利用和废物处理等方面的问题。
通过科学的工艺设计和环保措施的采取,能够实现高效率、低污染的焦炉气合成氨生产工艺路线。
合成氨生产各岗位工艺操作指标
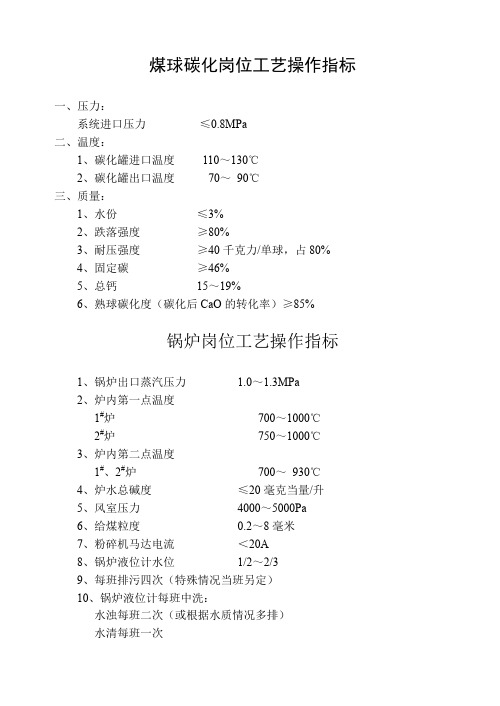
煤球碳化岗位工艺操作指标一、压力:系统进口压力≤0.8MPa二、温度:1、碳化罐进口温度110~130℃2、碳化罐出口温度70~90℃三、质量:1、水份≤3%2、跌落强度≥80%3、耐压强度≥40千克力/单球,占80%4、固定碳≥46%5、总钙15~19%6、熟球碳化度(碳化后CaO的转化率)≥85%锅炉岗位工艺操作指标1、锅炉出口蒸汽压力 1.0~1.3MPa2、炉内第一点温度1#炉700~1000℃2#炉750~1000℃3、炉内第二点温度1#、2#炉700~930℃4、炉水总碱度≤20毫克当量/升5、风室压力4000~5000Pa6、给煤粒度0.2~8毫米7、粉碎机马达电流<20A8、锅炉液位计水位1/2~2/39、每班排污四次(特殊情况当班另定)10、锅炉液位计每班中洗:水浊每班二次(或根据水质情况多排)水清每班一次11、排烟温度150~200℃12、鼓风机电流70~85A13、引风机电流50~80A14、喂煤机电流0.2~3.0A15、每小时巡回检查一次16、除尘器每班排灰:1#炉每两小时一次2#炉每小时一次造气微机岗位工艺操作指标一、压力:1、减压前蒸汽压力>0.9MPa2、减压后蒸汽压力0.08~0.12MPa3、入炉蒸汽压力0.05~0.07MPa4、鼓风机风压1800~2400mm水柱5、微机油压 4.0~6.0MPa6、汽泡压力<0.2MPa二、循环时间(150秒):1、二次上吹5~10秒2、吹净6~7秒3、吹风24~32秒4、上吹30~43秒5、下吹50~60秒三、温度:1、炉上温度350~400℃2、炉下温度180~250℃3、水夹套温度<135℃4、洗气塔≤50℃四、风机风量:吹风时风机电流≤340A五、蒸汽入炉流量:上吹 1.8~2.5吨/时下吹 1.6~2.5吨/时六、炉内炭层高度(空程)Φ2260 2.2~2.5mΦ2400 2.3~2.6m七、出渣次数块煤3次/班炉煤球5次/班炉八、气体成份:半水煤气中CO2≤13%O2≤0.5%CO ≥25%(H2+CO)>68%循环气中H250~60%H2/N2 2.0~2.8九、液位:汽泡液位1/3~1/2脱硫再生岗位工艺操作指标1、脱硫后半水煤气H2S含量<0.2g/m32、再生氨水中脱硫剂催化剂含量0.1~0.3g/L3、再生氨水浓度10~20tt4、再生效率≥65%5、再生泵出口压力≥0.36MPa6、电动机电流及温升按铭牌规定7、液位控制:脱硫塔1/3~1/28、再生氨水槽(按现标尺刻度)23~24注:再生氨水槽液位一定按规定值来控制液位过低将会引起硫泡沫排重新沉淀,过高则排出带走过多的脱硫氨水。
以焦炉煤气制合成氨的主要工艺分析与选择
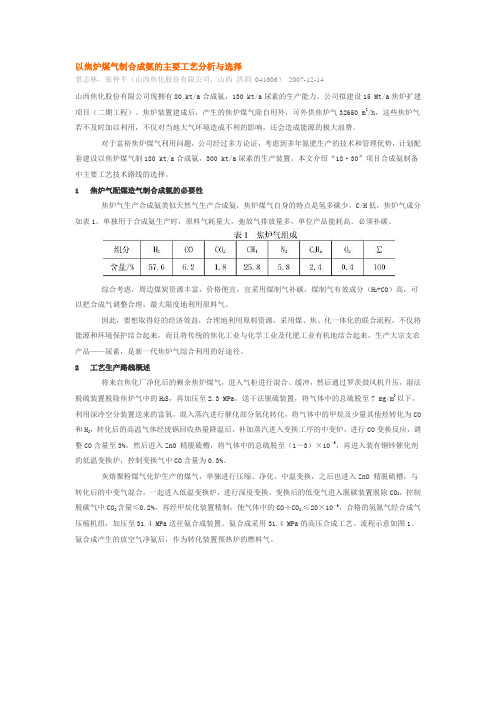
以焦炉煤气制合成氨的主要工艺分析与选择景志林,张仲平(山西焦化股份有限公司,山西洪洞041606)2007-12-14山西焦化股份有限公司现拥有80 kt/a合成氨,130 kt/a尿素的生产能力。
公司拟建设15 Mt/a焦炉扩建项目(二期工程)。
焦炉装置建成后,产生的焦炉煤气除自用外,可外供焦炉气32650 m3/h,这些焦炉气若不及时加以利用,不仅对当地大气环境造成不利的影响,还会造成能源的极大浪费。
对于富裕焦炉煤气利用问题,公司经过多方论证,考虑到多年氮肥生产的技术和管理优势,计划配套建设以焦炉煤气制180 kt/a合成氨,300 kt/a尿素的生产装置。
本文介绍“18·30”项目合成氨制备中主要工艺技术路线的选择。
1 焦炉气配煤造气制合成氨的必要性焦炉气生产合成氨类似天然气生产合成氨,焦炉煤气自身的特点是氢多碳少,C/H低,焦炉气成分如表1。
单独用于合成氨生产时,原料气耗量大,弛放气排放量多,单位产品能耗高。
必须补碳。
综合考虑,周边煤炭资源丰富,价格便宜,宜采用煤制气补碳,煤制气有效成分(H2+CO)高,可以把合成气调整合理,最大限度地利用原料气。
因此,要想取得好的经济效益,合理地利用原料资源,采用煤、焦、化一体化的联合流程,不仅将能源和环境保护结合起来,而且将传统的焦化工业与化学工业及化肥工业有机地结合起来,生产大宗支农产品——尿素,是新一代焦炉气综合利用的好途径。
2 工艺生产路线概述将来自焦化厂净化后的剩余焦炉煤气,进入气柜进行混合、缓冲,然后通过罗茨鼓风机升压,湿法脱硫装置脱除焦炉气中的H2S,再加压至2.3 MPa,送干法脱硫装置,将气体中的总硫脱至7 mg/m3以下,利用深冷空分装置送来的富氧,混入蒸汽进行催化部分氧化转化,将气体中的甲烷及少量其他烃转化为CO 和H2,转化后的高温气体经废锅回收热量降温后,补加蒸汽进入变换工序的中变炉,进行CO变换反应,调整CO含量至3%,然后进入ZnO 精脱硫槽,将气体中的总硫脱至(1~3)×10-6,再进入装有铜锌催化剂的低温变换炉,控制变换气中CO含量为0.3%。
“1830”工程尿素装置建设及运行

“18.30”工程尿素装置建设及运行前言天脊晋城化工股份有限公司(原晋城第二化肥厂)为发挥原料无烟煤得天独厚的地域优势,实施晋城200×104t/a高浓度氮肥基地项目的目标,进一步把企业做大做强,继2001年气化分公司改产尿素成功后,2002年3月在现在化工分公司(原解放军6013厂址处)开工建设“18.30”(18×104tNH3/a,30×104t Ur/a,)工程。
该工程采用了目前氮肥行业成熟可靠的多项先进技术和成果。
整个工程总决算投资3.6亿元,分二期建设,首期12×104tNH3/a配套工程于2002年12月投运。
30×104t Ur/a装置2002年11月开工建设,2003年11月装置开始试车,12月26日产出合格的大颗粒尿素,投产42天即达到设计生产能力,到2004年12月25日止,整套装置生产安全稳定,全年生产合成氨19.99×104t,尿素32×104t,分别达到设计能力的111.06%和106.6%,并联产甲醇1.435×104t,甲醛0.543×104t,实现销售收入4.53亿元,利税1.5亿元,创出了国内“18.30”装置的最佳效益,达到了较好的投入产出比。
现将30×104t/a尿素装置的建设和生产情况小结如下。
1 尿素装置生产工艺的选择工业生产中CO2与氨是在合成塔中合成尿素的。
实际生产中,每次反应仅有2/3左右CO2转化为尿素,因此从尿素合成塔出来的物料中除得到合成的尿素外,还有CO2与氨留在反应液中。
为了回收利用这部分未反应的CO2和氨,同时能顺利的进行尿液的浓缩以得到尿素产品,必须将CO2与氨从反应液中分离出来。
围绕着如何回收处理尿素合成塔出来的物料,形成了各种尿素工业生产方法。
归纳起来可分为两大类:一是水溶液全循环法,二是汽提全循环法。
针对如何确定30×104t/a尿素生产工艺,我们作了分析和比较。
年产18万吨合成氨和30万吨尿素项目建议书修改版
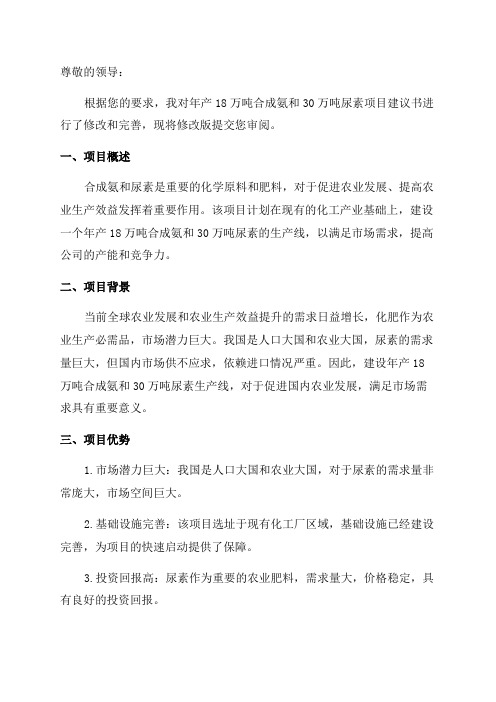
尊敬的领导:根据您的要求,我对年产18万吨合成氨和30万吨尿素项目建议书进行了修改和完善,现将修改版提交您审阅。
一、项目概述合成氨和尿素是重要的化学原料和肥料,对于促进农业发展、提高农业生产效益发挥着重要作用。
该项目计划在现有的化工产业基础上,建设一个年产18万吨合成氨和30万吨尿素的生产线,以满足市场需求,提高公司的产能和竞争力。
二、项目背景当前全球农业发展和农业生产效益提升的需求日益增长,化肥作为农业生产必需品,市场潜力巨大。
我国是人口大国和农业大国,尿素的需求量巨大,但国内市场供不应求,依赖进口情况严重。
因此,建设年产18万吨合成氨和30万吨尿素生产线,对于促进国内农业发展,满足市场需求具有重要意义。
三、项目优势1.市场潜力巨大:我国是人口大国和农业大国,对于尿素的需求量非常庞大,市场空间巨大。
2.基础设施完善:该项目选址于现有化工厂区域,基础设施已经建设完善,为项目的快速启动提供了保障。
3.投资回报高:尿素作为重要的农业肥料,需求量大,价格稳定,具有良好的投资回报。
4.技术优势明显:公司具备丰富的化工生产经验和技术优势,可以在项目建设和运营中发挥重要作用。
四、项目目标及实施方案1.项目目标:年产18万吨合成氨和30万吨尿素生产线的建设和运营。
2.实施方案:(1)项目规模:合成氨年产18万吨,尿素年产30万吨。
(2)项目投资:预计总投资10亿元。
(3)项目建设周期:预计3年。
(4)项目运营:建设完成后,逐步投入生产,开始为市场提供产品。
五、项目经济效益预测该项目的年产18万吨合成氨和30万吨尿素生产线建成后,预计年销售收入为6亿元,年利润为2亿元,投资回收期为5年。
项目具有良好的经济效益和市场前景。
六、风险分析1.市场风险:尿素市场价格受多种因素影响,价格波动较大,可能对项目的经济效益造成不利影响。
2.技术风险:生产合成氨和尿素涉及复杂的化学反应过程,技术要求较高,存在一定的技术风险。
3.环保风险:化学工业对环境的污染较大,项目需要与周边环境协调,确保环境保护工作的顺利开展。
年产18万吨合成氨、30万吨尿素项目建议书

年产18万吨合成氨、30万吨尿素项目建议书年产18万吨合成氨、30万吨尿素项目建议书一、项目概况1、项目名称:年产18万吨合成氨、30万吨尿素项目2、合作方式:独资、合资、合作、贷款等均可3、建设单位:XX煤业有限责任公司及合作单位4、建设性质:新建5、建设范围:内蒙古自治区XX自治旗XX矿区6、建设内容及规模:以XX矿区丰富的褐煤资源为依托,建设年产合成氨18万吨、尿素 30 万吨的项目。
可联产轻质油4752吨/年、煤焦油 14454吨/年,氨水(16%)27720吨/年、粗酚1980吨/年7、建设期限:项目建设期为4年,即2005年4月-2008年9月。
8、投资估算及资金筹措:投资规模:总投资为147215万元,其中建设投资 138703万元,流动资金8512万元。
本项目资金来源可以是贷款、风险投资等。
9、经济评价经济评价一览表序号项目单位指标备注1 项目总投资万元147215 建设投资万元1387032 铺底流动资金万元85123 年销售收入万元649064 年成本费用万元474285 税金万元26226 利润万元174787 投资利润率% 11.878 投资回收期年8.4二、项目区基本情况1.地理位置XX矿区位于内蒙古自治区呼伦贝尔市XX自治旗境内的东北部,地处大兴安岭西麓。
其地理坐标是东经120°24′~120°38′、北纬49°09′~49°16′。
矿区西连海拉尔区,东接牙克石市,南临巴彦嵯岗苏木,北至海拉尔河,与陈巴尔虎旗隔河相望,南北宽约13.7Km,东西长约46.1Km,总面积385.7Km2。
XX火车站东距牙克石18Km,西距呼伦贝尔市64Km,滨州铁路线由东向西穿过XX矿区,北有301国道,铁路经过牙克石可达齐齐哈尔,哈尔滨乃至全国各地,经海拉尔可达满州里市,民航经海拉尔机场可达北京、呼和浩特等地,交通十分方便。
2.煤炭资源及煤质情况⑴资源情况XX煤业公司拥有XX矿区、扎尼河矿区、伊敏河东区、陈旗巴彦哈达矿区、莫达木吉矿区五大矿区。
合成氨工艺指标

4.工艺控制指标(1)脱硫工序铁锰脱硫出口: S≤5ppm 氧化锌出口硫含量:≤0.1ppm加氢量: 2~5% 进口温度TIC-111: 380±5℃氧化锌出口温度:≤360℃进脱硫系统压力:≤4.1 MPa(2)转化工序水碳比: 3.2~3.5 一段炉出口甲烷:≤12.84%一段炉进口压力:≤3.82 MPa 燃料气压力PI-811:≤0.35 MPa对流段出口烟压:-2000 Pa 排烟温度:≤170℃炉膛负压:-100 Pa 混合气盘管出口温度:≤610℃工艺空气盘管温度:≤615℃过热蒸汽盘管NO.3:≤360℃原料天然气盘管NO.4:≤400℃原料天然气盘管NO.7:≤295℃燃料天然气预热盘管:≤200℃一段炉出口温度:≤801℃一段炉阻力:≤0.35 MPa 二段炉阻力:≤92 KPa二段炉出口温度:≤997℃二段炉水夹套温度:≤100℃二段炉出口甲烷:≤0.5% 中压汽包蒸汽压力:≤4.2 MPa脱氧槽液位:80%以上脱氧槽压力:≤20KPa中压汽包液位:1/3~2/3 锅炉给水PH值: 8.8~9.3 含量:≤0.007ppm 二段炉出口甲烷≤ 0.5%锅炉给水O2(3)变换工序高变进口温度: TIC-157 370±5℃高变出口温度:≤436℃高变出口CO:≤3 % 高变汽包液位: 1/3~2/3 高变汽包蒸汽压力:≤2.5 MPa 低变进口温度TIC-220 :200±5℃低变出口温度:≤228℃低变出口CO:≤0.3 %(4)脱碳工序(碳酸钾溶液)吸收嗒入气温度: 81℃±5℃吸收塔出气温度: 70℃±5℃吸收塔进贫液温度:70℃±5℃吸收塔进半贫液温度: 112℃±5℃再生气温度:<40℃再生塔出口贫液温度: 120℃±5℃吸收塔压差:<45KPa 再生塔压差:<20KPa再生塔出再生气压力:<75KPa 低变废锅蒸汽压力: 0.40~0.50MPa 吸收塔出二氧化碳含量:≤0.1% 再生气纯度:≥98.5 %汽提塔出口水中电导率:≤10μs/cm吸收塔液位: 1/2~2/3 闪蒸槽液位: 1/2~2/3低水分液位: 1/3~2/3 低变废锅液位: 1/3~2/3净水分液位: 1/3~2/3 铁离子含量:<100ppm汽提塔液位: 1/2~2/3 再生塔上部液位:≥30 %再生塔中部液位: 1/3~2/3 再生塔下部液位: 1/2~2/3贫液流量:≤ 96 t / h 半贫液流量:≤ 778 t / h总碱度: 25~30% 贫液再生度: 1.15~1.25半贫液再生度: 1.35~1.45 DEA : 2~3%)V5+/V4+:≥0.5 总矾: 0.7~1.0%(以KVO3(5)甲烷化工序甲烷化进口温度: 310℃±5℃甲烷化床层温度:≤350℃甲水分出口温度:<40℃甲烷化出口CO+CO:≤10ppm2甲水分液位:≤10 %。
合成氨工艺指标[修改版]
![合成氨工艺指标[修改版]](https://img.taocdn.com/s3/m/b99f020af61fb7360a4c6552.png)
第一篇:合成氨工艺指标4.工艺控制指标(1)脱硫工序铁锰脱硫出口:S≤5ppm 氧化锌出口硫含量:≤0.1ppm 加氢量:2~5% 进口温度TIC-111:380±5℃氧化锌出口温度:≤360℃进脱硫系统压力:≤4.1 MPa (2)转化工序水碳比:3.2~3.5 一段炉进口压力:≤3.82 MPa 对流段出口烟压:-2000 Pa 炉膛负压:-100 Pa 工艺空气盘管温度:≤615℃原料天然气盘管NO.4:≤400℃燃料天然气预热盘管:≤200℃一段炉阻力:≤0.35 MPa 二段炉出口温度:≤997℃二段炉出口甲烷:≤0.5% 脱氧槽液位:80%以上中压汽包液位:1/3~2/3 锅炉给水O2含量:≤0.007ppm (3)变换工序高变进口温度:TIC-157 370±5℃高变出口CO:≤3 % 高变汽包蒸汽压力:≤2.5 MPa 低变出口温度:≤228℃(4)脱碳工序(碳酸钾溶液)吸收嗒入气温度:81℃±5℃吸收塔进贫液温度:70℃±5℃再生气温度:<40℃吸收塔压差:<45KPa 一段炉出口甲烷:≤12.84% 燃料气压力PI-811:≤0.35 MPa 排烟温度:≤170℃混合气盘管出口温度:≤610℃过热蒸汽盘管NO.3:≤360℃原料天然气盘管NO.7:≤295℃一段炉出口温度:≤801℃二段炉阻力:≤92 KPa 二段炉水夹套温度:≤100℃中压汽包蒸汽压力:≤4.2 MPa 脱氧槽压力:≤20KPa锅炉给水PH值:8.8~9.3 二段炉出口甲烷≤0.5% 高变出口温度:≤436℃高变汽包液位:1/3~2/3 低变进口温度TIC-220 :200±5℃低变出口CO:≤0.3 % 吸收塔出气温度:70℃±5℃吸收塔进半贫液温度:112℃±5℃再生塔出口贫液温度:120℃±5℃再生塔压差:<20KPa再生塔出再生气压力:<75KPa 低变废锅蒸汽压力:0.40~0.50MPa 吸收塔出二氧化碳含量:≤0.1% 再生气纯度:≥98.5 % 汽提塔出口水中电导率:≤10μs/cm 吸收塔液位:1/2~2/3 闪蒸槽液位:1/2~2/3 低水分液位:1/3~2/3 低变废锅液位:1/3~2/3 净水分液位:1/3~2/3 铁离子含量:<100ppm 汽提塔液位:1/2~2/3 再生塔中部液位:1/3~2/3 贫液流量:≤96 t / h 总碱度:25~30% 半贫液再生度:1.35~1.45 DEA V5+/V4+:≥0.5 甲烷化工序甲烷化进口温度:310℃±5℃甲水分出口温度:<40℃甲水分液位:≤10 %再生塔上部液位:≥30 % 再生塔下部液位:1/2~2/3 半贫液流量:≤778 t / h 贫液再生度:1.15~1.25 :2~3% 总矾:0.7~1.0%(以KVO3) 甲烷化床层温度:≤350℃甲烷化出口CO+CO2:≤10ppm (5)第二篇:合成氨工艺合成氨工艺陈昶君化九三20090118921.合成氨生产工艺流程图(1)煤为源头工艺路线:以无烟煤为原料生成合成氨常见过程是:造气->半水煤气脱硫->压缩机1,2工段->变换->变换气脱硫->压缩机3段->脱硫->压缩机4,5工段->铜洗->压缩机6段->氨合成->产品NH3造气过程为以煤为原料,用间歇式固定层常压气化法,反应方程为煤+氧气→二氧化碳二氧化碳+煤→一氧化碳煤+水蒸气→一氧化碳+氢气(2)天然气为源头采用天然气、焦化千气力原料的合成氨生产工艺流程包括:脱硫、转化、变换、脱碳、甲烷化、氨的合成、吸收制冷及输入氨库和氨吸收八个工序(一)脱琉原料气进入后,首先进入三段脱硫塔.第一、二段分别采用5—6%Na0H和10。
- 1、下载文档前请自行甄别文档内容的完整性,平台不提供额外的编辑、内容补充、找答案等附加服务。
- 2、"仅部分预览"的文档,不可在线预览部分如存在完整性等问题,可反馈申请退款(可完整预览的文档不适用该条件!)。
- 3、如文档侵犯您的权益,请联系客服反馈,我们会尽快为您处理(人工客服工作时间:9:00-18:30)。
供汽车间35T循环流化床锅炉工艺指标炉温:880~950℃中压压力:2.5~2.8 Mpa低压压力:0.6 Mpa 汽包液位:40%~60%除氧器液位:70%~90% 炉膛负压:-20~ -70pa风室静压:7.5~8.5Kpa 给水泵压力:≥4.5Mpa给水水质指标:PH:8.8~9.2 溶解氧:≤15μg/L氯根:5mg/l 硬度: ≤2.0μmol/L油含量:<1.0mg/ L炉水水质指标:磷酸根:5~15mg/ LPH:9~11(25℃)氯根:给水氯根的12倍总碱度:6~16mmol/ L溶解固形物:<3000 mg/ L工艺主任审核:车间主任审核:供水车间合成循环水工艺指标:电机电流:≤28.5A液位:1/2~2/3.风机电流:≤168A供水总管压力:0.25~0.4Mpa尿素循环水工艺指标:1.风机电流: ≤246A2.电机电流: ≤31.1A3.水位:1/2~2/3.4.供水压力:0.25~0.4Mpa.脱盐水工艺指标:1.机械过滤器压力:0.3~0.5Mpa2.精密过滤器压力:0.25~0.3Mpa3.高压泵前压力:>0.1Mpa4.膜前压力:<1.3Mpa5.段间压力:<0.9Mpa6.浓水压力: <0.7 Mpa7.硬度= 0 mmol/L8.电导率:≤20μs/cm9.PH: 7~9一次水泵房工艺指标:一次水泵电机电流:<150A.消防泵电机电流:<260A.稳压泵电机电流:<22A.一次水总管压力:0.3~0.5Mpa.消防泵总管压力:0.8~1.2Mpa.工艺主任审核:车间主任审核:合成车间冰机岗位工艺指标1、压力进口:0.05~0.25MPa出口:≤1.6MPa油压:高于排气压力0.25~0.3MPa氨贮槽:1.6MPa循环水:≥0.25Mpa2、温度出口温度:≤105℃冷凝温度≤45℃油温温度:≤65℃电机温度:≤65℃循环水温度:≤25℃3、液位油液位:1/2~2/3氨槽高限:≤槽容积80%氨槽低限:≥槽容积13%4、电流KA31.5----1型机≤110A氨库岗位工艺指标1、去尿素液氨压力 2.3MPa2、液氨球罐压力<2.4MPa3、液氨球罐温度-5~30℃4、液氨球罐液位10~80%(夏天最高控制70%)等压岗位工艺指标等压吸收塔压力控制在2.3~2.5MPa柱塞泵压力大于塔内压力0.2~0.5MPa冷却水压力≥0.25MPa等压塔液位保持在1/2~1/3软水槽液位1/2~1/3等压塔出口氨水滴度保持在150~200tt合成压力(MPa)补充气≤31.4系统压差≤2.5合成塔压差≤0.8气氨总管压力≤0.3放氨压力2.5~2.9合成废锅压力<2.52、温度(℃)触媒层温度:初期465±5,后期490±5塔壁温度≤140塔二出口温度300~350水冷前气体温度80水冷后气体温度40NH3冷温度0~-103、成分精炼气(CO+CO2)≤20ppm入塔氨含量2.5~2.8% 出塔氨含量11~15%新鲜气中惰性气体含量≤2.0%循环气惰性气体含量15.0~21.0%循环气H2/N2 2.2~2.84、液位冷交氨分1/2~2/3废锅40-70%5、电炉电流≤2KA透平机:进气压力≤29.2MPa出气压力≤31.4MPa压差≤2.2MPa进气温度≤30℃打气量620m3/h电机转速2970r/min电机功率680KW电机电压380V电机运行电流≤1062A电机非负荷端轴承温度≤75℃电机负荷轴承温度≤75℃透平机进口轴承温度≤75℃透平机出口轴承温度≤75℃电机定子温度≤100℃电机绝缘电阻值≥0.5MΩ氨冷器保护器进口温度≤35℃氨冷器保护气出口温度5~15℃压缩岗位工艺指标(1)气体压力一段进口压力≈1.5Mpa 一段出口压力≈3.4Mpa 二段进口压力≈3.3 Mpa 二段出口压力≈7.2Mpa 三段进口压力≈7.2 Mpa 三段出口压力≈14.11 Mpa 四段进口压力≈12 Mpa 四段出口压力≈31.4 Mpa (2)气体温度一段进口温度<40℃一段出口温度<130℃二段进口温度<40℃二段出口温度<130℃三段进口温度<40℃三段出口温度<130℃四段进口温度<40℃四段出口温度<130℃(3)循环冷却水工作压力0.4 Mpa(4)润滑油型号:L-DAB150, 工作温度<50℃(5)曲轴箱油位:1/2-2/3 注油器油位:1/2~2/3 (6)循环油压<0.2 Mpa时,压缩机联锁停车。
工艺主任审核:车间主任审核:化产车间硫铵工段饱和器岗位泵岗位干燥机岗位洗脱苯工段终冷岗位工艺指标:1、电机温度<55℃,轴承温度≤65℃。
2、终冷煤气进口温度50~65℃。
3、终冷塔煤气出口温度27℃(夏季≤27℃,冬季≥20℃)。
4、终冷塔阻力≤1KPa。
5、冷凝液泵:额定电流:2.6A洗苯油泵岗位工艺指标:1、入洗苯塔贫油温度27~30℃。
(冬季比煤气高3~6℃,夏季比煤气高0~2℃)。
2、洗苯塔后煤气含苯量≤5g/Nm3。
3、富油含苯2~3%,含水<1%。
4、洗苯塔阻力<2.0KPa。
5、二段贫油冷却器后贫油出口温度≤30℃。
6、泵TRG表指示在绿区。
7、新洗油质量:比重1.04~1.07,粘度E20≤2;水分≤1%;230℃前馏出量≤15%。
270℃前馏出量≥60%,300℃前馏出量≥85%;含萘≤15%;含酚≤0.5%;在15℃时无沉淀物。
贫富油泵:额定电流:39A粗笨回流泵:额定电流:15.3A粗笨输送泵:额定电流:11.0/6.4A新洗油槽液下泵:额定电流:11.0/6.4A蒸馏岗位工艺指标:1.管式炉后富油温度:180~190℃。
2.再生器顶部温度:≥190℃。
3.脱苯塔底贫油温度:175~180℃。
4.脱苯塔顶温度:77~82℃。
5. 粗苯冷凝冷却后,粗苯温度≤30℃。
6. 过热蒸汽温度:400℃。
7. 粗苯180℃前馏出量:≥93%8. 贫油含苯<0.35%。
9. 入再生器洗油占循环量的1~1.5%。
10.脱苯塔底部压力30KPa。
11.再生器顶部压力30KPa。
12.脱苯塔顶部回流比4~5。
13. 萘扬液槽操作压力≤0.4MPa制冷岗位工艺指标:1.溴化锂机组蒸汽压力:0.6MPa2.溴化锂机组冷却水进出口温度:32~40℃3. 凝结水回收器工作压力≤0.6MPa4. 冷水泵:额定电流:55.5A5. 凝结水泵:额定电流:8.1A工艺主任审核:车间主任审核:净化车间半水煤气系统岗位操作规程正常工艺指标1、温度氧化锌脱硫槽床层温度220~280℃变换炉入口半水煤气300~330℃变换炉第一层触媒床层350~435℃变换炉第二层触媒床层380~470℃变换炉上段气体出口421℃变换炉下段气体出口400℃变换炉第三层触媒床层400~410℃变换炉出口气体405℃2、压力半水煤气入系统2.06MPa出系统变换气1.76MPa入系统饱和蒸汽2.45MPa3、分析入工段半水煤气中总硫≤150mg/Nm3氧化锌脱硫槽出口气体总硫含量<5mg/Nm3进变换炉半水煤气中CO 28~30%(干基)出变换炉变换气CO≤3%水汽比(体积比)0.7~0.9:1干法脱硫岗位操作规程正常工艺指标入工段焦炉气压力<2.3MPa入工段焦炉气温度25℃铁钼转化器入口温度300℃铁钼触媒层热点温度350~420℃氧化锰触媒层热点温度350~450℃干法脱硫出口总硫≦20mg/Nm3(一般<5mg/Nm3)转化岗位正常工艺指标1、温度(1)初预热器出口焦炉气温度300~350℃(2)出蒸焦预热器混合气温度≤500℃(3)出富氧预热炉富氧温度480~500℃(4)转化炉出口温度880~960℃(5)转化炉触媒热点≤1050℃(6)出转化废热锅炉转化气温度≤615℃(7)出蒸焦预热器转化气温度≤450℃(8)进中变炉转化气温度330~390℃(9)出中变炉中变气温度350~450℃(10)中变炉触媒层温度≤460℃(11)出中变换热器中变气温度300~450℃(12)出中变废热锅炉中变气温度260~300℃(13)氧化锌触媒层热点温度250~280℃(14)出淬冷器中变气温度180~200℃(15)低变触媒层热点温度180~230℃(16)出低变炉低变气温度180~240℃(17)蒸焦预热炉出口气体温度正常650±10℃升温期间≤700℃(2小时)(18)入预热炉脱氧软水温度104℃(19)出预热炉脱氧软水温度≤180℃(20)间断排污缸温度80℃(21)夹套冷却水进口温度≤40℃(22)夹套冷却水出口温度≤70℃(23)富氧预热炉炉膛温度<700℃(投料时850℃2小时)(24)蒸焦预热炉炉膛温度800℃(投料时900℃2小时)压力(23)进工段焦炉气压力2.25MPa(24)正常生产时富氧空气压力2.3MPa(25)废热锅炉出口蒸汽压力2.45MPa(26)进淬冷器水压≥2.20MPa(27)新鲜氮气压力≤0.78MPa(28)进工段脱氧软水压力2.5 MPa(29)蒸汽管网压力2.45 MPa(30)汽包压力2.45 MPa2、分析(1)化炉出口CH4≤0.8%(2)中变炉出口CO≤3%(3)低变炉出口CO≤0.3%(4)氧化锌出口总硫<0.1ppm3、烧嘴工艺指标:4、转化联锁(1)转化炉出口转化气温度≥1050℃,系统停车联锁启动(2)富氧空气流量/焦炉气流量≥0.73系统停车联锁启动(3)入转化炉富氧空气与蒸焦气压差≤0.05MPa系统停车联锁启动(4)转化废锅汽包液位≤-350mm系统停车联锁启动脱碳岗位正常工艺指标1、温度(1)入第一低变气煮沸器150~180℃(2)入第二低变气煮沸器120~135℃(3)入吸收塔低变气≤110℃(4)出吸收塔碱洗气≤80℃(5)甲烷化换热器出口碱洗气250~270℃(6)甲烷化炉入口碱洗气270~320℃(7)甲烷化炉触媒层热点280~380℃(8)出工段净化气<30℃(9)甲烷化换热器出口净化气≤146℃(10)出加压再生塔CO2 98~100℃(11)出常压再生塔CO2 <104℃(12)出富液闪蒸槽CO2 92~101℃(13)出“三合一”CO2 <80℃(14)冷却器出口CO2 <40℃(15)入吸收塔上塔冷贫液75~85℃(16)入吸收塔上塔热贫液85~110℃(17)入吸收塔中部半贫液95~110℃(18)出吸收塔底富液95~120℃(19)入CO2冷却器软水≤40℃2、压力(1)入吸收塔低变气 1.60MPa (2)入甲烷化炉碱洗气 1.52MPa (3)出工段净化气 1.47MPa (4)加压再生塔顶部CO2 60KPa (5)加压再生塔底部气相80KPa (6)常压再生塔顶部CO2 10KPa (7)常压再生塔底部气相30KPa (8)贫液闪蒸槽出口溶液80KPa (9)吸收塔压差<30Kpa (10)甲烷化炉压差<30Kpa (11)CO2冷却器出口>12Kpa 3、流量(1)入吸收塔低变气108864 Nm3/h (2)出吸收塔碱洗气86978 Nm3/h (3)出工段净化气84700 Nm3/h (4)出工段CO2气21886 Nm3/h (5)冷贫液150 Nm3/h (6)热贫液200 Nm3/h (7)半贫液900 Nm3/h 4、液位(1)吸收塔液位50~60% (2)加压再生塔液位60~80%(3)常压再生塔液位60~80%(5)贫液闪蒸槽液位60~75%(6)低变气煮沸器后分离器液位50~60%(7)碱洗气分离器液位≤20%(8)净化气分离器液位20~30%(9)CO2分离器液位≤50%5、分析(1)吸收塔出口碱洗气CO2 ≤0.3%(2)甲烷化炉出口CO+CO2 ≤20×10-6(3)再生气CO2纯度≥98%(4)溶液分析K2O 180—200g/L;KVO3 5—7g/L;DETA 10—20g/L;V5+≥1g/L(以KVO3计);Fe3+≤50mg/h;泡高<50cm;消泡时间≤8s;再生度:贫液≤1.25 ;半贫液≤1.42。