垫圈冲压模具设计说明
垫圈-冲压模具课程设计说明书
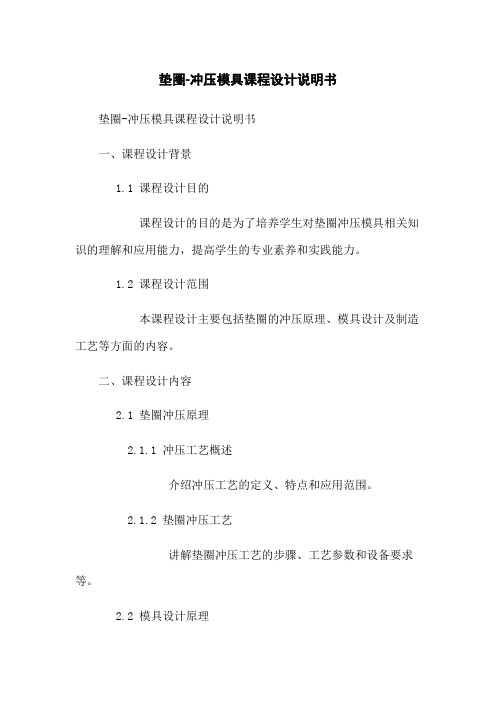
垫圈-冲压模具课程设计说明书垫圈-冲压模具课程设计说明书一、课程设计背景1.1 课程设计目的课程设计的目的是为了培养学生对垫圈冲压模具相关知识的理解和应用能力,提高学生的专业素养和实践能力。
1.2 课程设计范围本课程设计主要包括垫圈的冲压原理、模具设计及制造工艺等方面的内容。
二、课程设计内容2.1 垫圈冲压原理2.1.1 冲压工艺概述介绍冲压工艺的定义、特点和应用范围。
2.1.2 垫圈冲压工艺讲解垫圈冲压工艺的步骤、工艺参数和设备要求等。
2.2 模具设计原理2.2.1 模具设计概述概述模具设计的定义、分类和基本原理等。
2.2.2 垫圈冲压模具设计详细说明垫圈冲压模具的结构、功能和设计要点。
2.3 模具制造工艺2.3.1 模具制造工艺概述介绍模具制造工艺的基本流程和要求。
2.3.2 垫圈冲压模具制造工艺详细说明垫圈冲压模具制造的步骤、工艺和注意事项。
三、课程设计实施3.1 教学方法结合理论和实践,采用讲授、实验、案例分析等多种教学方法。
3.2 教材选用推荐教材:《冲压技术与模具设计》3.3 实践任务安排学生参与垫圈冲压模具制造过程的实际操作,提高实践能力。
四、课程设计评价4.1 评价指标根据学生的实际表现,评价其对垫圈冲压模具知识理解和应用能力的程度。
4.2 评价方法采用考试、实验报告、实践操作和互动讨论等方式进行评价。
五、附件本文档中涉及以下附件,请参阅:2.垫圈冲压模具设计图纸3.相关案例分析资料六、法律名词及注释1.冲压工艺:指将板材或带材通过冲压模具的冲压动作,加工成所需形状的工艺。
2.模具设计:指根据工件要求,设计模具的结构和尺寸,以实现对工件的加工。
3.模具制造工艺:模具制造过程中的工艺流程,包括铣削、钳工、研磨、电火花等工艺环节。
垫圈冲孔冷冲压模具设计与制作指导书-零件名称:垫圈-材料Q235-厚度-...知识交流

*垫圈冲孔冷冲压模具设计与制作指导书零件名称:垫圈,材料Q235,厚度1.0mm,小批量生产。
一、零件工艺分析,确定工艺方案该零件为形状简单,规则,需经过落料、冲孔两道工序。
该零件形状简单,精度要求不高,冲压工艺性良好。
工艺方案一:采用落料、冲孔两副单工序模,能满足零件精度要求,模具制造简单,模具成本低,缺点工序多,占用冲床多,生产率低,适合小批量生产。
工艺方案二:采用落料冲孔复合模生产,能满足精度要求,落料冲孔复合模制造比单工序模稍复杂,模具成本稍高,生产率比方案一高,适合中批生产。
根据这些特点考虑是小批量生产,为降低模具成本,确定采用方案一。
二、工艺计算1、冲孔尺寸计算Do=D-2(H-0.43r-0.72t)=43-2X(8-0.43X1-0.72X1)=29.3mm2、计算冲压力对材料Q235,b=450Mpa冲孔力:F孔=Ltb=29.3X X1X450=41Kn衬套冲孔卸料力:F卸=K卸F=0.05X41=2.1Kn衬套冲孔推料力:F卸=nK卸F=4X0.05X41=8.2kN衬套冲孔总冲压力为:F总=F+F卸+F推=41+2.1+8.2=51.3Kn3、确定凸、凹模刃口尺寸零件精度要求不高,对自由公差尺寸,冲孔凸模按工件孔公差尺寸,对有公差要求的孔,冲孔凸模按工件孔最大极限尺寸。
冲孔凸模尺寸为29.3mm,冲孔凹模尺寸为冲孔凸模尺寸加冲孔间隙,为29.38mm。
凸、凹模型和销孔采用线割加工,凸模和凹模线割公差取0.01mm。
4、确定凸、凹模结构尺寸刃口高度一般为5—6mm,取刃口高度5mm。
凹模厚度一般为15—50mm,取35mm。
凹模壁厚一般为20—50mm,落料凹模尺寸取180X 35,冲孔凹模尺寸取150X35。
选M8螺钉和8mm销钉。
凸模高度取60mm,小凸模采用抬肩结构,固定板固定,大凸模采用螺钉、销钉固定。
5、定位方式落料模条料用导料销和固定挡料钉定位,弹性卸料板卸料。
方形垫圈冲压复合模具设计

方形垫圈冲压复合模具设计
设计一个方形垫圈冲压复合模具需要考虑以下几个方面:模具结构设计、材料选择、工艺流程和模具加工。
1.模具结构设计:
上模由切割机构、冲头和定位销组成。
切割机构用于切割板材成为合
适的尺寸,冲头用于将板材冲击成为方形形状,定位销用于确保上模位于
恰当的位置。
下模由定位销、导向柱和冲头组成。
定位销用于将下模固定在机床上,导向柱用于保证上模和下模的准确对位,冲头用于将板材冲击成为带有孔
的方形形状。
背模由切割机构、冲头和导向柱组成。
切割机构用于将垫圈从板材中
切割出来,冲头用于将垫圈从板材上弹出,导向柱用于保持背模和上下模
的准确对位。
2.材料选择:
考虑到垫圈需要具有一定的弹性和耐用性,一般选择具有良好塑性和
高强度的金属材料,如不锈钢、铜等。
3.工艺流程:
在制造方形垫圈的过程中,首先需要将适当尺寸的板材切割成相应的
形状,然后使用上模和下模将板材冲压成为带有孔的方形形状。
最后,使
用背模将垫圈从板材上切割出来。
4.模具加工:
根据设计需求和材料选择,可以采用车削、铣削、线切割、磨削等工艺进行模具的加工。
同时,需要考虑加工精度和模具的寿命,以确保模具的可靠性和稳定性。
在设计方形垫圈冲压复合模具时,还需要考虑到其使用环境和应用要求,例如垫圈的尺寸、材料厚度、产量要求等。
通过综合考虑以上因素,可以设计出适合生产方形垫圈的冲压复合模具。
圆形带孔垫片的冲压模具设计

圆形带孔垫片的冲压模具设计冲压模具是一种用于加工金属材料的重要工具,广泛应用于各种工业领域。
在设计圆形带孔垫片的冲压模具时,需要考虑材料选择、结构设计、强度分析、工艺参数等因素。
1.材料选择:在选择材料时需要考虑垫片的使用条件和要求,如工作温度、压力等。
一般来说,常用的材料包括不锈钢、碳钢、铝合金等。
根据具体要求选择合适的材料,确保垫片的使用寿命和性能。
2.结构设计:根据垫片的形状和孔洞要求,设计适合的结构。
垫片一般为圆形,孔洞可能为单孔或多孔。
通过制定合理的结构设计,可以提高冲压效率和产品质量。
3.垫片强度分析:在设计中需要考虑垫片的强度,确保能够承受外部压力和变形。
通过有限元分析等方法,确定垫片的受力分布和强度要求,选择适当的材料和加工工艺。
4.工艺参数确定:根据垫片的形状和要求,确定冲压过程中的工艺参数。
包括模具结构尺寸、冲床压力、模具开合高度、冲头直径等。
通过试模和实际应用,不断优化工艺参数,提高冲压效率和产品质量。
5.模具制造:根据设计要求,制造冲压模具。
主要包括模具底座、上下模、冲头等。
在制造过程中,需要确保模具的精度和质量,避免出现偏差和故障。
6.模具调试和试模:在模具制造完成后,进行模具调试和试模工作。
通过逐步调整模具的参数,如开合高度、冲头直径,确保模具的正常运行和垫片的加工质量。
总之,设计圆形带孔垫片的冲压模具需要综合考虑材料选择、结构设计、强度分析、工艺参数等多个因素。
在设计过程中,需要通过模拟分析和试模实验,不断优化设计方案,确保模具运行稳定和垫片加工质量。
垫圈冲压模课程设计说明书

湖南涉外经济学院机械工程学部冲压成型工艺及模具设计课程设计任务书机械工程学院材料成型及控制工程专业题目垫圈冲压模具设计任务起止日期:2012 年9 月18 日至2012 年11 月20 日止学生姓名:王曦明班级:材料0902班指导老师:何雅槐日期:系主任:日期:审查学部主任:日期:批准冲压模具课程设计一、题目垫圈二、原始数据冲裁制件如图2-1所示。
材料为Q235,材料厚度0.8mm,生产批量为10万件,属中大批量生产。
三、冲裁件工艺分析此工件既有冲孔,又有落料两个工序。
材料为Q235、t=0.8mm 的碳素钢,具有良好的冲压性能,适合冲裁,工件结构简单,内有一个直径为 12mm的圆孔。
此工件满足冲裁的加工要求,工件尺寸未标注公差,按IT14级计算。
尺寸精度较低,普通冲裁完全能够满足要求。
四、冲裁工艺方案的确定(一)方案种类该工件包括落料、冲孔两个基本工序,有以下三种工艺方案。
方案一:先冲孔,后落料。
采用单工序模生产。
方案二:冲孔-落料级进冲压。
采用级进模生产。
方案三:采用冲孔-落料同时进行的复合模生产。
(二)方案的比较各方案的特点及比较如下。
方案一:模具结构简单,制造方便,但需要两道工序,两副模具,成本相对较高,生产效率低,且更重要的是在第一道工序完成后,进入第二道工序必然会增大误差,使工件精度、质量大打折扣,达不到所需要的要求,难以满足生产需要。
故不选此方案。
方案二:级进模是一种多工位、效率高的加工方法。
但级进模轮廓尺寸较大,制造复杂,成本较高,因而也排除此方案。
方案三:只需要一套模具,工件的精度及生产效率要求都能满足,模具轮廓尺寸较小、模具的制造成本不高。
故本方案用先冲孔后落料的方法。
(三)方案的确定综上所诉,本套模具采用冲孔-落料复合模。
五、模具结构形式的确定复合模有两种结构形式,正装式复合模和倒装式复合模。
分析该工件成形后脱模方便性,正装式复合模成形后工件留在下模,需向上推出工件,取件不方便。
垫圈冲压课程设计说明书

课程设计说明书 杯盖冲压工艺及模具设计材控0704班郭豪杰U200711329目录设计任务 (3)冲压工艺分析 (4)冲压方案设计 (5)模具结构设计 (7)计算压力及选择冲压设备 (19)参考文献 (20)设计任务如图所示的杯盖,材料为08F,料厚0.5mm, 大批量生产,试设计该零件的冲压生产工艺及模具.图 1零件二维图图 2零件三维模型冲压工艺分析冲压件的冲压工艺性是指其冲压加工的难易程度。
从技术方面看,根据产品图纸,主要分析该冲压件的形状特点、尺寸大小、精度要求和材料性能等因素是否符合冲压工艺的要求。
在经济方面,主要根据冲压件的生产批量,分析产品成本,阐明采用冲压生产可以取得的经济效益。
一般说来,工艺性良好的冲压件,可保证材料消耗少,工序数目少,模具结构简单,产品质量稳定,成本低,还能使技术准备工作和生产的组织管理做到经济合理。
冲压工艺性分析的目的就是了解冲件加工的难易,为制定冲压工艺方案奠定基础。
(1)从经济方面分析,此零件的生产批量为大批量生产,采用冲压生产可以取得好的经济效益。
(2)从技术方面分析,此零件为无凸缘圆筒形件,结构相对简单,尺寸小,只有落料、拉深和切边三个工序。
零件材料为08F,板料厚度为0.5mm,成型性能好。
另外该零件的尺寸精度要求不高,适合采用冲压方式生产。
同时工件底部圆角半径r=2mm >(3~5)t, t=0.5mm,满足拉深圆角半径要求。
通过以上分析,该零件具有良好的冲压工艺性,适合采用冲压生产。
冲压方案设计由于板厚t<1mm,所以可以直接用零件图标注的尺寸进行计算,不必用工件材料厚度中心尺寸计算1.确定修边余量该件H0=20mm H0/d=20/50=0.4查[2]表4.2.1得△h=1.2 则拉伸高度H=20+1.2=21.2mm 2.毛坯展开计算展开直径D根据面积相等原则D===81mm3.确定拉深次数根据毛坯相对厚度t/Dx100=0.5/81x100=0.62,查[2]得,有压边圈时第一次拉深极限拉深系数m1=0.53~0.55;又总拉深系数m总=d/D=50/81=0.617> m1。
圆形双孔垫片冲压模具设计
圆形双孔垫片冲压模具设计引言:圆形双孔垫片常用于密封应用中,用于填充接合面和填充随机的孔洞,以防止液体、气体或粉尘的泄漏。
为了生产高质量的圆形双孔垫片,需要设计合适的冲压模具。
本文将对圆形双孔垫片冲压模具进行设计,并介绍设计过程。
设计步骤:1.模具材料选择:模具材料应具有良好的耐磨性和耐腐蚀性。
常见的模具材料有H13、SKD11等。
在选择模具材料时,需要考虑其机械性能和使用寿命。
2.模具结构设计:圆形双孔垫片冲压模具主要由上下模块、定位部件、导向部件和冲头组成。
上下模块通过螺纹螺栓连接,以便于更换和维修。
定位部件用于确保上下模块的位置准确。
导向部件用于引导冲头在冲压过程中的移动。
3.模具尺寸设计:根据产品要求和机械特性,确定垫片的直径、孔的尺寸和间距等参数。
圆形双孔垫片通常具有对称性,可以简化模具结构和设计。
4.冲头设计:冲头是模具的核心部件,直接与材料接触。
冲头的设计应考虑到材料的性质和厚度,以确保冲压过程中的顺利进行。
常见的冲头形状有圆形、方形和倒角形状。
5.导向机构设计:导向机构用于引导冲头在冲压过程中的移动,以确保冲压位置的准确性和一致性。
导向机构一般由导柱和导套组成,导柱安装在上模块上,导套安装在下模块上。
6.模具制造和调试:根据设计图纸进行模具制造,并进行试模和调试。
在试模和调试过程中,需要确保冲压过程的平稳和垫片的质量。
结论:通过以上的设计步骤,可以设计出适用于生产圆形双孔垫片的冲压模具。
模具设计的关键是考虑材料的性质、模具结构的合理性和冲头形状的选择。
在实际生产中,还需进行模具的制造和调试,以确保生产出高质量的圆形双孔垫片。
总结:。
冲压垫圈设计
冲压垫圈设计冲压⼯艺模具课程设计说明书(垫圈)学校:院系:班级:姓名学号指导教师:《冲压⼯艺模具学实训》说明书摘要本次的课程设计是⼀个简单的防滑垫圈及其复合模设计,此副模具是采⽤落料—冲孔两道⼯序相结合的复合模,本⼈经查阅相关书籍、资料以及对设计此副模具所要⽤到的相关公式、数据作出了⼀个准确的依据。
本次课程设计⼀共分为两部分,和其他模具的设计⼀样,第⼀部是对零件进⾏⼯艺分析,接着对⼯艺⽅案进⾏⽐较,最终确定选⽤复合模加⼯制件的⼯艺⽅案。
然后画⼯序图、排样图以及对材料利⽤率的计算,计算冲压⼒,选择冲压机。
然后填写冲压⼯艺规程卡。
第⼆部分是冲压模具的设计,选择冲模类型以及结构形式,定位⽅式,卸料⽅式,模具设计计算(主要计算各类主要零件的外形尺⼨),最后确定凸凹模⼯作部分尺⼨。
关键词:垫圈落料冲孔前⾔在现代⼯业⽣产中,模具是重要的⼯艺装备之⼀,它在铸造、锻造、冲压橡胶等⽣产⾏业中得到了⼴泛应⽤。
由于采⽤模具进⾏⽣产能够提⾼⽣产效率,节约原材料,降低成本,并可保证⼀定的加⼯质量要求。
所以,汽车、飞机、拖拉机、电器、仪表、玩具等的零部件很多采⽤模具来加⼯。
随着科学技术的发展,产品的更新换代加快,对产品质量外观不断提出新要求,对模具质量要求也越来越⾼。
模具的设计、制造⼯业部门肩负着为相关企业和部门提供产品的重任。
如果模具设计及制造⽔平落后,产品质量低劣,制造周期长,必将影响产品的更新换代,使产品失去竞争能⼒,阻碍⽣产和经济的发展。
因此,模具设计及制造技术在国民经济中的地位是显⽽易见的。
⾦属板料冲压是模具在⼯业⽣产中应⽤⼴泛的加⼯形式之⼀,随着市场竞争⽇趋加剧,产品质量不断提⾼,对⽣产的安全性,操作的⽅便性等要求也⽇益提⾼。
模具作为冲压⽣产的基本要素,其设计制造技术受到普遍重视。
因此学习模具课程,进⾏模具设计也是适应现代化⼯业要求的。
这次课程设计的内容是利⽤CAD等系列软件设计材料为H62-M的黄铜垫圈冲压模具,说明书有四部分内容,叙述了整个设计的过程。
圆形垫片冲压模具设计
圆形垫片冲压模具设计
1.需求分析:确定设计目标和模具使用条件。
了解需要生产的圆形垫
片的规格、要求和使用环境等信息。
2.材料选择:根据圆形垫片的要求选择合适的材料。
不同材料的硬度、韧性和导热性等性质对模具设计和生产工艺有直接影响。
3.模具结构设计:根据圆形垫片的形状和尺寸,设计模具的整体结构。
一般情况下,圆形垫片冲压模具包括上模板、下模板、导向柱和导向套等
组成部分。
各部分的尺寸和位置需要精确计算和确定。
4.模具零件设计:根据整体结构设计的要求,设计模具中的各个零部件。
例如,设计合适的模具底座、护板、抓取装置等零件。
模具零件的尺
寸和材料选择需要经过计算和评估。
5.模具分型设计:将整个模具分为上下模板,并设计合适的导向装置
和分型机构。
分型准确、顺畅的设计可以提高工作效率和模具使用寿命。
6.模具加工制造:根据设计要求制造模具的各个零部件。
使用先进的
数控加工设备和精密测量工具,确保模具的高精度和质量。
7.模具装配调试:将制造好的模具各部分进行装配,并进行调试和测试。
调试包括模具的尺寸精度、分型准确性、导向性能等方面的检查。
8.生产应用:经过调试确认无误后,将模具投入实际生产使用。
不断
进行观察和评估,对模具进行维护和保养,以确保其长期稳定工作。
总体来说,圆形垫片冲压模具设计涉及到多个方面的工程知识,需要
设计师具备丰富的经验和专业技能。
准确的模具设计和制造将直接影响生
产效率和产品质量,因此对模具的设计和加工过程需要高度的重视和专业性处理。
304不锈钢垫圈冲孔冲压模具设计说明书
304不锈钢垫圈冲孔冲压模具设计说明书一、项目背景:随着工业的发展,垫圈已成为各种机械设备以及建筑等领域中常用的配件。
为了提高生产效率和产品质量,设计制造一种304不锈钢垫圈冲孔冲压模具,可以满足市场需求。
二、产品要求:1.材料选择:模具材料要求为优质的304不锈钢,具有耐腐蚀、高强度和良好的塑性。
2.冲孔尺寸:模具设计要求能够满足常见的垫圈规格,包括内径、外径和厚度等尺寸要求。
3.冲压效果:模具设计要求能够实现高效的冲压过程,确保冲压出的垫圈质量良好、尺寸精确。
4.模具寿命:要求模具寿命长,能够满足大批量生产的需求。
三、模具设计方案:1.模具结构:本模具采用上冲式结构,即上模向下冲压,下模固定,以提高冲压效率。
2.模具材料选择:上模和下模采用优质的304不锈钢,确保模具耐腐蚀性能和强度。
3.模具组成:模具由上模、下模和导向系统组成。
上模具有冲孔凸模和导向柱,下模具有导向套筒和冲孔模口。
4.冲孔设计:上模和下模分别设计为圆形冲孔,在模具的设计中,要确保冲孔尺寸准确、位置精确。
5.模具寿命:通过表面处理的方式,提高模具的耐磨性和抗腐蚀性,延长模具的使用寿命。
四、模具制造工艺:1.模具制造工艺:模具采用数控机床进行精确加工和装配。
如上模、下模和导向系统的加工,采用车、铣、钻等工艺完成。
2.表面处理工艺:模具的表面进行抛光处理,提高模具的表面光洁度和耐腐蚀性能。
3.模具装配工艺:将上模、下模、导向系统按设计要求进行装配,确保模具的配合精度和可靠性。
4.模具试产及修改:完成模具后,进行试产,根据实际情况不断进行修改和优化,确保模具的冲压效果和寿命。
五、模具使用和维护:1.模具使用:在使用模具时,要根据实际需要选择适当的冲压速度和冲压参数,以确保冲压过程的稳定性和垫圈质量。
2.模具维护:定期对模具进行清洁和润滑,避免模具表面生锈和机械部件的磨损。
在模具存放时要注意防潮、防尘等。
六、总结:本设计说明书详细介绍了304不锈钢垫圈冲孔冲压模具的设计要求、方案以及制造、使用和维护等相关内容。
- 1、下载文档前请自行甄别文档内容的完整性,平台不提供额外的编辑、内容补充、找答案等附加服务。
- 2、"仅部分预览"的文档,不可在线预览部分如存在完整性等问题,可反馈申请退款(可完整预览的文档不适用该条件!)。
- 3、如文档侵犯您的权益,请联系客服反馈,我们会尽快为您处理(人工客服工作时间:9:00-18:30)。
实验实训(设计)报告项目名称:________ 垫圈冲压工艺及模具设计_________________ 专业:模具设计与制造班级:模具⑷企业指导老师:校指导老师:邓老师学号:201401091 姓名:江峰地点:职业技术学院时间:2016.7二。
一六年七月十三日职业技术学院实验实训(设计)进度检查及成绩评定表摘要本次的课程设计是一个简单的防滑垫圈及其复合模设计,此副模具是采用落料一冲孔两道工序相结合的复合模,本人经查阅相关书籍、资料以及对设计此副模具所要用到的相关公式、数据作出了一个准确的依据。
本次课程设计一共分为两部分,和其他模具的设计一样,第一部是对零件进行工艺分析,接着对工艺方案进行比较,最终确定选用复合模加工制件的工艺方案。
然后画工序图、排样图以及对材料利用率的计算,计算冲压力,选择冲压机。
然后填写冲压工艺规程卡。
第二部分是冲压模具的设计,选择冲模类型以及结构形式,定位方式,卸料方式,模具设计计算(主要计算各类主要零件的外形尺寸),最后确定凸凹模工作部分尺寸。
前言在现代工业生产中,模具是重要的工艺装备之一,它在铸造、傲造、冲压橡胶等生产行业中得到了广泛应用。
由于采用模具进行生产能够提高生产效率,节约原材料,降低成本,并可保证一定的加工质量要求。
所以,汽车、飞机、拖拉机、电器、仪表、玩具等的零部件很多采用模具来加工。
随着科学技术的发展,产品的更新换代加快,对产品质量外观不断提出新要求,对模具质量要求也越来越高。
模具的设计、制造工业部门肩负着为相关企业和部门提供产品的重任。
如果模具设计及制造水平落后,产品质量低劣,制造周期长,必将影响产品的更新换代,使产品失去竞争能力,阻碍生产和经济的发展。
因此,模具设计及制造技术在国民经济中的地位是显而易见的。
金属板料冲压是模具在工业生产中应用广泛的加工形式之一,随着市场竞争日趋加剧,产品质量不断提高,对生产的安全性,操作的方便性等要求也日益提高。
模具作为冲压生产的基本要素,其设计制造技术受到普遍重视。
因此学习模具课程,进行模具设计也是适应现代化工业要求的。
这次课程设计的容是利用CAD等系列软件设计材料为H62-M的黄铜垫圈冲压模具,说明书有四部分容,叙述了整个设计的过程。
分析了零件的工艺性,经济性,确定零件的冲压工艺方案及其模具的结构。
然后进行模具零件的设计计算。
计算出零件尺寸后,通过CAD 软件做出各个零件的实体,最后完成模具装配。
由于时间比较仓促,有的地方考虑不足,希望老师予以指导。
目录1、冲栽件工艺分析 (1)1.1冲裁件的结构工艺性.............................................. . (1)1.2尺寸精度和断面粗糙.............................................. . (1)2、冲压工艺方案的确定 .............................................. (2)3、冲压工艺计算 .................................................... . (4)3.1排样图设计,材料利用率计算...................................... .. (4)3.2计算凹凸模尺寸 ................................................. . (5)4、冲载力计算及压力中心计算,初选压力机 ............................•••• 64.1冲裁力计算及初选压力机 .......................................... . (6)4.2压力中心的计算.................................................. . (7)5、模具结构型式的确定 .............................................. (8)5.1模具结构型式 .................................................... . (8)5.2定位装置........................................................ (8)5.3推件装置........................................................ (8)5.4卸料装置........................................................ .. (9)5.5导向装置 ........................................................ (9)6、模具零部件设计 .................................................. .. (10)6.1落料凹模........................................................ . (10)7.2冲孔凸模........................................................ . (10)6.3凸凹模 ......................................................... . (11)6.4其他主要零件结构•••••••••••••••••••••••••117、零件及压力机校核 ................................................ .. (12)7.1垫板的校核...................................................... .. (12)7.2压力机的校核 ................................................... .. (12)总结 ............................................................... . (13)参考文献 ........................................................... .. (14)设计任务书如图垫图零件冲裁图,材料H62铜片,料厚t=L 5mm,大批量生产,试确定冲裁工艺性, 设计冲裁模。
06.5图1-1零件图L1冲裁件的结构工艺性L2尺寸精度与断面粗糙度尺寸精度:该制件所有尺寸都未标注公差,按IT14级确定工件的公差。
一般的冲压均能满足其尺寸精度要求。
经查公差表,各尺寸公差分别为:22.3 _;52. 6-0.3. ®14-0,43. 06.5+ 产,,,表面粗糙度:零件图上所有未标注表面粗糙度,考虑为12.5um。
适合冲裁。
结论:该制件符合冲裁工艺性,适合冷冲裁加工,其加工工艺性好。
该零件包括冲孔和落料两个基本工序,有以下三种方案可以采用 方案一:先冲孔,后落料,采用单工序模生产。
方案二:冲孔一落料复合冲压,采用复合模生产。
方案三:冲孔落料连续冲压,采用级进模生产。
项目 方案一方案二 方案三 模具结构 简单 复杂 复杂 模具数量 二套 一套 一套 模具寿命 低 较高 不高 制件质量精度低 精度高 精度不高生产率低高较高根据表确定方案二倒装复合模,冲孔废料由下模漏出,工件落在下模表面,需要及时清理°安全性相对较 低。
但工图2-1方案一件精度较高,同轴度,对称度及位置度误差较小,生产效率较高,对材料要求不严,可用边角料.正装复合模,冲孔废料和工件都落在下模表面,安全性更差。
综合以上分析比较结果说明,本零件采用倒装复合模最为合适。
3、冲压工艺计算3.1排样图设计,材料利用率计算(1)为了提高材料利用率选用直排查表6-1-9工件间搭边值%=1.8,边缘搭边值a=2.2, 条料宽度偏差查表6-1-11,取A=0. 5,导料板与条料之间的最小间隙,查表6-1-13,取Z=0. 5 (2)计算送料步距A:经计算求得A=14+ai=15.8mm(3)计算料条宽度B:经计算求得8% ⑺2+ 2a + Z) \=(22.3 + 4.4 + 0.5).屋27.2 3导料板间的距离Bo =B+Z=27. 2+0. 5=27. 8mm以上式中:B一条料的宽度,单位mmAnax一冲裁件垂直于送料方向的最大尺寸,单位mma一侧搭边值Z一导料板于最宽条料之间的间障△一条料宽度的单向(负向)公差查表7-3-1选择板料规则为2000 X 1000 X 1.5纵裁:A 1000下条料数:"叵|=及'=36(条)”一■2000 - 1.8单个条料制件数:m= E7^] = [ 14 + 1-8 J = 126 (个)n.AAA/ 36 X 126 X 173.202 .材料利用率:〃纵二-2000 Xsoo —X 100为=39.3%横裁:A 2000下条料数:n=回二笳=73(条)"-4 1000 - 1.8单个条料制件数:m=[, + a i] = [ 14+18 ]=63 (个)“小/。
dccw 73 X 63 X 173.202 .材料利用率:9纵二丁厂x 10%=200G xlooo x 10°念39.8%由于纵裁与横裁利用率相差不大,优先选用纵裁(1)凹模磨损后变大的尺寸:%、42、A3查表3-5得:*1二丫2二万3二0.5、4- X 0.3 4. n QQC(6 - 05X0.3) % 诃二5・85 + 即加(22.3 - 0.5 X0.52)“产2mm二22.04 +4-X 0.43 4- D 10ft(14 -0.5X0.43) % mm J3.785 +V°8mm凹模磨损后变小的尺寸:/查表3-5得:々=0.5n (6. 5 + 0.5 X 0.36),、标rrQ 0位二 F xo. 36nl m= 6.68 .o.o91nm 查表6-1-1 得4nm = 0.090 Z min = 0.120 图3-2排样图3.2计算凹凸模尺寸A2=力3=pnn 图3-1纵裁凸模刃口尺寸按凹模实际刃口尺寸配制,保证最小合理间隙值4RE =°♦0904、冲裁力计算及压力中心计算,初选压力机4.1冲裁力计算及初选压力机该制件厚度t=1.5nun,初步考虑采用弹性性卸料装置,因此完成本制件所需的冲压力有冲载力、顶件力、卸料力。