动力电池失效模式分析
0070.解析动力电池系统的各种失效模式
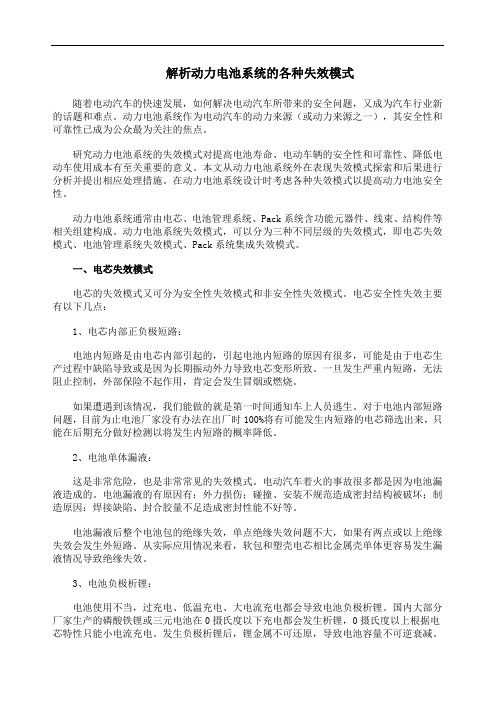
解析动力电池系统的各种失效模式随着电动汽车的快速发展,如何解决电动汽车所带来的安全问题,又成为汽车行业新的话题和难点。
动力电池系统作为电动汽车的动力来源(或动力来源之一),其安全性和可靠性已成为公众最为关注的焦点。
研究动力电池系统的失效模式对提高电池寿命、电动车辆的安全性和可靠性、降低电动车使用成本有至关重要的意义。
本文从动力电池系统外在表现失效模式探索和后果进行分析并提出相应处理措施。
在动力电池系统设计时考虑各种失效模式以提高动力电池安全性。
动力电池系统通常由电芯、电池管理系统、Pack系统含功能元器件、线束、结构件等相关组建构成。
动力电池系统失效模式,可以分为三种不同层级的失效模式,即电芯失效模式、电池管理系统失效模式、Pack系统集成失效模式。
一、电芯失效模式电芯的失效模式又可分为安全性失效模式和非安全性失效模式。
电芯安全性失效主要有以下几点:1、电芯内部正负极短路:电池内短路是由电芯内部引起的,引起电池内短路的原因有很多,可能是由于电芯生产过程中缺陷导致或是因为长期振动外力导致电芯变形所致。
一旦发生严重内短路,无法阻止控制,外部保险不起作用,肯定会发生冒烟或燃烧。
如果遭遇到该情况,我们能做的就是第一时间通知车上人员逃生。
对于电池内部短路问题,目前为止电池厂家没有办法在出厂时100%将有可能发生内短路的电芯筛选出来,只能在后期充分做好检测以将发生内短路的概率降低。
2、电池单体漏液:这是非常危险,也是非常常见的失效模式。
电动汽车着火的事故很多都是因为电池漏液造成的。
电池漏液的有原因有:外力损伤;碰撞、安装不规范造成密封结构被破坏;制造原因:焊接缺陷、封合胶量不足造成密封性能不好等。
电池漏液后整个电池包的绝缘失效,单点绝缘失效问题不大,如果有两点或以上绝缘失效会发生外短路。
从实际应用情况来看,软包和塑壳电芯相比金属壳单体更容易发生漏液情况导致绝缘失效。
3、电池负极析锂:电池使用不当,过充电、低温充电、大电流充电都会导致电池负极析锂。
电动汽车动力电池防水性失效模式分析
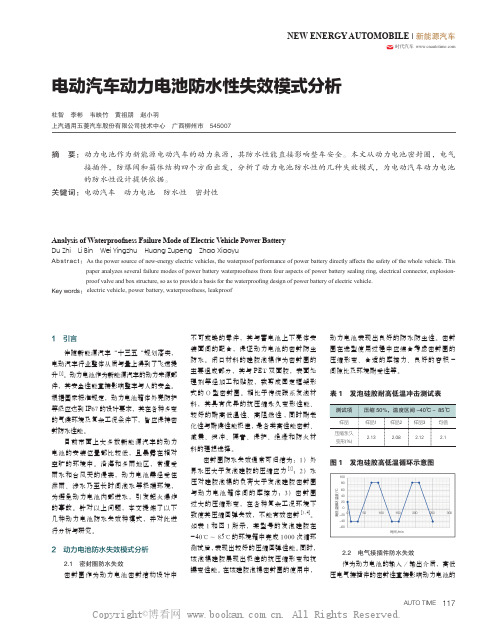
动力电池表现出良好的防水防尘性。密封 圈在选型使用过程中应综合考虑密封圈的 压缩形变、合适的摩擦力、良好的容积 间隙比及环境耐受性等。
表 1 发泡硅胶耐高低温冲击测试表
测试项
样品 压缩永久 变形(%)
压缩 50%,温度区间 -40℃~ 85℃
样品1
样品2 样品3
均值
2.13
2.08
2.12
2.1
图 1 发泡硅胶高低温循环示意图
关键词:电动汽车 动力电池 防水性 密封性
Analysis of Waterproofness Failure Mode of Electric Vehicle Power Battery Du Zhi Li Bin Wei Yingzhu Huang Zupeng Zhao Xiaoyu
A b s t r a c t :As the power source of new-energy electric vehicles, the waterproof performance of power battery directly affects the safety of the whole vehicle. This paper analyzes several failure modes of power battery waterproofness from four aspects of power battery sealing ring, electrical connector, explosionproof valve and box structure, so as to provide a basis for the waterproofing design of power battery of electric vehicle.
电池管理系统BMS潜在失效模式及后果分析(DFMEA)

外部供电低于系统供电最 小电压
系统供电不足无法运行
5 ☆ 电源输入范围不满足指标要求
在指标范围内,选择宽范围输入 的电源模块
3
老化试验
3
45
23 BMS数据存储
数据存储
无法正常存储历史数据
历史数据无法正常保存和 分析
2 ☆ 存储芯片损坏
采用汽车级元器件设计 老化测试
3 老化试验 2 12
24
电源模块 符合技术要求
10
设计验证
1
70
34
绝缘电阻检测 功能
在充电、放电状态下对车 身与电池负极之间的电阻 进行实时检测
在充电、放电状态下,绝 缘采样值跳变
绝缘电阻检测阻值不准,造 成漏电检测误报,影响车 辆行驶
7
☆
平衡桥式绝缘方案设计中绝缘采集 回路滤波电容容值100NF偏小
新电路修改为10UF,功能要充分 进行环境实验验证,包括充电、 放电、高低温实验等
BMS温度采集电路分压电阻损坏或
温度传感器损坏
高低温测试
1 温度采集功能 温度进行实时检测,并且
7☆
精度符合技术要求
温度采集显示温度一直保 持不变,且显示数值与实 际不符
温度采集功能失效,导致 BMS无法检测到温度
BMS与温度传感器接触不良
老化测试 震动测试
2 震动试验 3 42
对电池总电压进行实时检 电池电压采集不到
对接触器失去部分控制, 导致其闭合后不能断开
电源系统一直和负载连 接,使电池一直处于放电 状态
6
高压回路接触器 对接触器实现完全控制, 对接触器失去部分控制导 电源系统和负载失去连
控制功能
包括闭合与断开
动力电池的故障诊断方法与故障模式预测

动力电池的故障诊断方法与故障模式预测动力电池是电动汽车的重要组成部分,其性能和可靠性直接影响整车的使用寿命和安全性。
然而,长期以来,动力电池存在着故障风险,这不仅会导致车辆行驶不稳定,还可能引发火灾等严重后果。
因此,为了确保电动汽车的安全运行和使用,及时的故障诊断和模式预测变得至关重要。
一、动力电池故障诊断方法1.1 电池管理系统(BMS)电池管理系统(Battery Management System,BMS)是电动汽车中常用的故障诊断方法之一,其主要功能是监测电池的状态和性能。
BMS通过对电池电压、温度、电流等参数的实时监测,可以判断电池是否存在故障,并提供相应的故障代码或警告信息。
1.2 模型预测方法模型预测方法是一种基于电池数学模型的故障诊断方法。
通过建立电池系统的动力学模型,利用电池的状态估计技术,可以预测电池的容量衰减、内阻增加等故障模式,并及时采取相应的维修或更换措施。
1.3 数据挖掘与机器学习方法数据挖掘与机器学习方法是一种基于历史数据的故障诊断方法。
通过对大量的电池运行数据进行分析和挖掘,可以发现电池的故障模式和规律,并建立相应的故障诊断模型。
二、动力电池故障模式预测2.1 容量衰减容量衰减是动力电池常见的故障模式之一,主要表现为电池存储的能量逐渐减少。
容量衰减的原因有很多,如电池材料老化、循环次数增加等。
通过对电池容量的实时监测和历史数据的分析,可以预测电池的容量衰减趋势,提前采取措施进行维护或更换。
2.2 内阻增加内阻增加是另一种常见的动力电池故障模式,它会导致电池的放电性能下降和温升增加。
通过对电池的放电特性进行分析和建模,可以预测电池的内阻增加趋势,提前警示并采取相应的修复措施,以保证电池的正常工作和使用寿命。
2.3 温度异常温度异常是动力电池故障的一个重要指标,当电池温度过高或过低时,都会影响电池的性能和寿命。
通过对电池温度的实时监测和历史数据的比对分析,可以预测电池温度的异常情况,并及时采取散热或加热等措施,防止电池的故障和损坏。
动力电池的故障诊断方法与故障模式分析
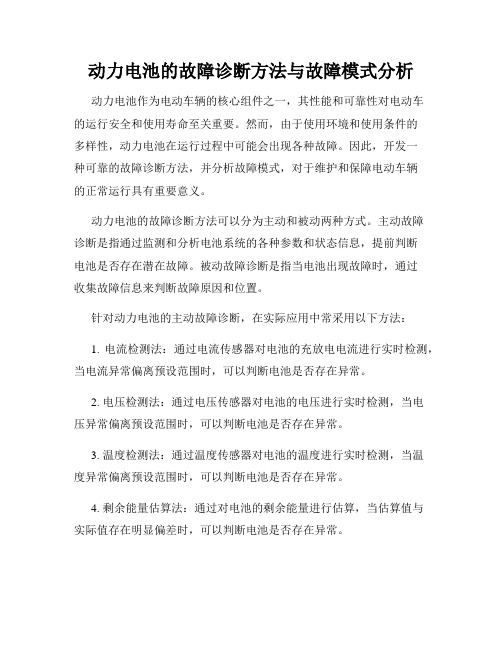
动力电池的故障诊断方法与故障模式分析动力电池作为电动车辆的核心组件之一,其性能和可靠性对电动车的运行安全和使用寿命至关重要。
然而,由于使用环境和使用条件的多样性,动力电池在运行过程中可能会出现各种故障。
因此,开发一种可靠的故障诊断方法,并分析故障模式,对于维护和保障电动车辆的正常运行具有重要意义。
动力电池的故障诊断方法可以分为主动和被动两种方式。
主动故障诊断是指通过监测和分析电池系统的各种参数和状态信息,提前判断电池是否存在潜在故障。
被动故障诊断是指当电池出现故障时,通过收集故障信息来判断故障原因和位置。
针对动力电池的主动故障诊断,在实际应用中常采用以下方法:1. 电流检测法:通过电流传感器对电池的充放电电流进行实时检测,当电流异常偏离预设范围时,可以判断电池是否存在异常。
2. 电压检测法:通过电压传感器对电池的电压进行实时检测,当电压异常偏离预设范围时,可以判断电池是否存在异常。
3. 温度检测法:通过温度传感器对电池的温度进行实时检测,当温度异常偏离预设范围时,可以判断电池是否存在异常。
4. 剩余能量估算法:通过对电池的剩余能量进行估算,当估算值与实际值存在明显偏差时,可以判断电池是否存在异常。
与主动故障诊断相对应的是被动故障诊断。
在电动车辆实际运行中,常常会发现电池不良的现象,例如:充电时间延长、续航里程缩短等。
这些故障需要通过故障模式分析来判断故障原因和位置。
常见的故障模式包括:1. 电池容量衰减:长时间使用导致电池容量下降,无法满足车辆行驶需求。
2. 电池内部短路:电池内部出现短路现象,导致充电和放电过程中电压异常。
3. 电池极化速度加快:电池放电速度加快,导致充电时间延长。
4. 电池自放电增加:电池长时间停放后,自放电速度增加,导致续航里程缩短。
针对上述故障模式,可以通过分析电池的工作特性和历史数据,结合电池管理系统的故障判别算法,快速诊断故障原因和位置。
综上所述,动力电池的故障诊断方法与故障模式分析对于电动车辆的可靠性和安全性至关重要。
动力电池失效模式分析
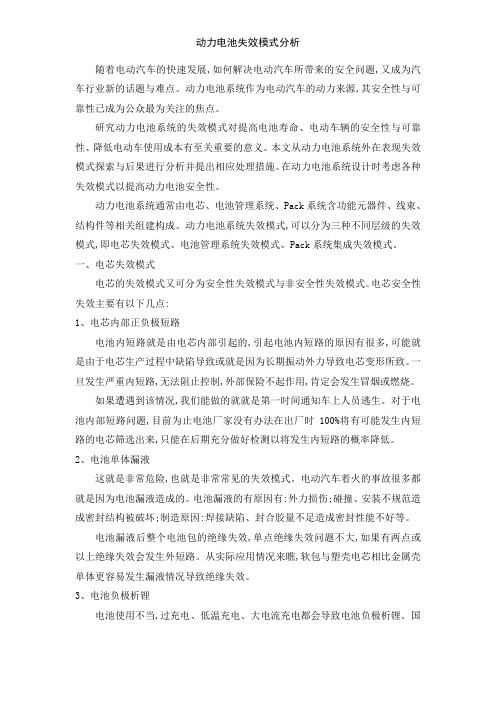
随着电动汽车的快速发展,如何解决电动汽车所带来的安全问题,又成为汽车行业新的话题与难点。
动力电池系统作为电动汽车的动力来源,其安全性与可靠性已成为公众最为关注的焦点。
研究动力电池系统的失效模式对提高电池寿命、电动车辆的安全性与可靠性、降低电动车使用成本有至关重要的意义。
本文从动力电池系统外在表现失效模式探索与后果进行分析并提出相应处理措施。
在动力电池系统设计时考虑各种失效模式以提高动力电池安全性。
动力电池系统通常由电芯、电池管理系统、Pack系统含功能元器件、线束、结构件等相关组建构成。
动力电池系统失效模式,可以分为三种不同层级的失效模式,即电芯失效模式、电池管理系统失效模式、Pack系统集成失效模式。
一、电芯失效模式电芯的失效模式又可分为安全性失效模式与非安全性失效模式。
电芯安全性失效主要有以下几点:1、电芯内部正负极短路电池内短路就是由电芯内部引起的,引起电池内短路的原因有很多,可能就是由于电芯生产过程中缺陷导致或就是因为长期振动外力导致电芯变形所致。
一旦发生严重内短路,无法阻止控制,外部保险不起作用,肯定会发生冒烟或燃烧。
如果遭遇到该情况,我们能做的就就是第一时间通知车上人员逃生。
对于电池内部短路问题,目前为止电池厂家没有办法在出厂时100%将有可能发生内短路的电芯筛选出来,只能在后期充分做好检测以将发生内短路的概率降低。
2、电池单体漏液这就是非常危险,也就是非常常见的失效模式。
电动汽车着火的事故很多都就是因为电池漏液造成的。
电池漏液的有原因有:外力损伤;碰撞、安装不规范造成密封结构被破坏;制造原因:焊接缺陷、封合胶量不足造成密封性能不好等。
电池漏液后整个电池包的绝缘失效,单点绝缘失效问题不大,如果有两点或以上绝缘失效会发生外短路。
从实际应用情况来瞧,软包与塑壳电芯相比金属壳单体更容易发生漏液情况导致绝缘失效。
3、电池负极析锂电池使用不当,过充电、低温充电、大电流充电都会导致电池负极析锂。
动力电池的故障诊断方法与故障模式精确预测

动力电池的故障诊断方法与故障模式精确预测随着电动车的普及,动力电池作为其重要组成部分,也备受关注。
然而,动力电池存在一定的故障风险,因此掌握故障诊断方法和故障模式的精确预测对于保障电池的性能和安全至关重要。
本文将介绍一些常见的动力电池故障诊断方法,并探讨故障模式的精确预测技术。
一、故障诊断方法1. 终端电压检测法:终端电压检测法是一种简单有效的故障诊断方法。
通过监测电池终端电压的变化,可以判断电池的工作状态和容量衰减情况。
当出现电压异常或不稳定的情况时,可能存在故障。
2. 内阻测量法:内阻测量法是一种常用的故障诊断方法。
通过测量电池内部电阻的大小,可以判断电池的性能和健康状况。
当电池内阻过大或不均匀分布时,可能存在故障。
3. 温度监测法:温度监测法是一种常见的动力电池故障诊断方法。
通过监测电池温度的变化,可以判断电池充放电过程中是否存在过热或过冷现象。
当电池温度异常升高或降低时,可能存在故障。
4. SOC估算法:SOC(State of Charge)估算法是一种基于电池电荷状态的故障诊断方法。
通过估算电池的充放电状态,可以判断电池的健康状况和容量衰减情况。
当估算的SOC与实际SOC存在较大差异时,可能存在故障。
二、故障模式精确预测技术1. 数据驱动的预测方法:数据驱动的预测方法通过收集大量的动力电池工作数据,并利用机器学习和数据挖掘技术来建立故障模式的预测模型。
通过分析历史数据中的故障模式和特征,可以预测未来电池可能出现的故障模式,为故障预防和维护提供指导。
2. 物理模型的预测方法:物理模型的预测方法基于对动力电池内部物理过程的建模和仿真,通过模拟不同的工作条件和故障情况,预测电池的故障模式。
这种方法具有较高的精确度和实时性,但对于模型的建立和参数的确定要求较高。
3. 统计分析的预测方法:统计分析的预测方法通过对大量电池故障数据的统计和分析,寻找故障模式之间的关系和规律,并建立故障发生的概率模型。
汽车动力电池的可靠性分析与测试方法研究

汽车动力电池的可靠性分析与测试方法研究随着国家政策的不断推动和市场需求的增长,汽车电动化已经成为汽车产业的趋势和方向。
而作为电动汽车的核心组件之一,动力电池的可靠性和安全性显得尤为重要。
因此,本文将就汽车动力电池的可靠性分析和测试方法进行研究和探讨。
一、动力电池的可靠性分析1.1 动力电池的失效模式电动车动力电池作为整个车辆的动力源和储能装置,一旦出现较大的失效,很可能引起严重的后果。
因此,首先需要对动力电池的失效模式进行分析。
根据目前已有的研究和实验,电池系统的失效模式主要包括以下几种:(1)电池单体失效:由单个电池单体引起的故障,如容量下降、内阻增大、短路等。
(2)模块化失效:由电池模块中的电池单体故障引起的故障,如模块崩坏、模块故障等。
(3)系统性失效:由电池系统中的多个模块或其他组件故障引起的故障,如整个电池组系统故障、BMS故障等。
1.2 可靠性评估方法在电池系统研发和生产过程中,需要对其可靠性进行评估和测试。
可靠性评估方法可以大致分为以下两种:(1)实验测试法:通过实验和测试,对电池系统进行可靠性评估。
该方法包括:温度循环试验、振动试验、容量保持试验、充放电试验等。
(2)预测模型法:采用数学统计和物理模型等方法,对电池系统进行可靠性评估。
该方法包括:有限元分析、热稳定性分析、寿命预测等。
二、动力电池的测试方法在电池系统的实验测试中,需要选择合适的测试方法和测试设备,以确保测试数据的准确性和可靠性。
下面介绍几种比较常见的动力电池测试方法。
2.1 组装测试方法该方法将电池单体按照一定的组装结构组成电池组,进行测试。
组装方法一般分为串联、并联和混联三种,具体的方法根据电池结构和性能而定。
组装测试时需要模拟电池使用过程,如充放电、温度循环等,以获取其可靠性数据。
2.2 压缩测试方法该方法是通过压缩电池组,来模拟电池失效时的状态,评估电池系统的可靠性。
压缩测试方法中包括静态和动态两种,即分别应用静态和动态荷载对电池组进行测试。
- 1、下载文档前请自行甄别文档内容的完整性,平台不提供额外的编辑、内容补充、找答案等附加服务。
- 2、"仅部分预览"的文档,不可在线预览部分如存在完整性等问题,可反馈申请退款(可完整预览的文档不适用该条件!)。
- 3、如文档侵犯您的权益,请联系客服反馈,我们会尽快为您处理(人工客服工作时间:9:00-18:30)。
随着电动汽车的快速发展,如何解决电动汽车所带来的安全问题,又成为汽车行业新的话题和难点。
动力电池系统作为电动汽车的动力来源,其安全性和可靠性已成为公众最为关注的焦点。
研究动力电池系统的失效模式对提高电池寿命、电动车辆的安全性和可靠性、降低电动车使用成本有至关重要的意义。
本文从动力电池系统外在表现失效模式探索和后果进行分析并提出相应处理措施。
在动力电池系统设计时考虑各种失效模式以提高动力电池安全性。
动力电池系统通常由电芯、电池管理系统、Pack系统含功能元器件、线束、结构件等相关组建构成。
动力电池系统失效模式,可以分为三种不同层级的失效模式,即电芯失效模式、电池管理系统失效模式、Pack系统集成失效模式。
一、电芯失效模式
电芯的失效模式又可分为安全性失效模式和非安全性失效模式。
电芯安全性失效主要有以下几点:
1、电芯内部正负极短路
电池内短路是由电芯内部引起的,引起电池内短路的原因有很多,可能是由于电芯生产过程中缺陷导致或是因为长期振动外力导致电芯变形所致。
一旦发生严重内短路,无法阻止控制,外部保险不起作用,肯定会发生冒烟或燃烧。
如果遭遇到该情况,我们能做的就是第一时间通知车上人员逃生。
对于电池内部短路问题,目前为止电池厂家没有办法在出厂时100%将有可能发生内短路的电芯筛选出来,只能在后期充分做好检测以将发生内短路的概率降低。
2、电池单体漏液
这是非常危险,也是非常常见的失效模式。
电动汽车着火的事故很多都是因为电池漏液造成的。
电池漏液的有原因有:外力损伤;碰撞、安装不规范造成密封结构被破坏;制造原因:焊接缺陷、封合胶量不足造成密封性能不好等。
电池漏液后整个电池包的绝缘失效,单点绝缘失效问题不大,如果有两点或以上绝缘失效会发生外短路。
从实际应用情况来看,软包和塑壳电芯相比金属壳单体更容易发生漏液情况导致绝缘失效。
3、电池负极析锂
电池使用不当,过充电、低温充电、大电流充电都会导致电池负极析锂。
国
内大部分厂家生产的磷酸铁锂或三元电池在0摄氏度以下充电都会发生析锂,0摄氏度以上根据电芯特性只能小电流充电。
发生负极析锂后,锂金属不可还原,导致电池容量不可逆衰减。
析锂达到一定严重程度,形成锂枝晶,刺穿隔膜发生内短路。
所以动力电池在使用时应该严禁低温下进行充电。
4、电芯胀气鼓胀
产生胀气的原因很多,主要是因为电池内部发生副反应产生气体,最为典型的是与水发生副反应。
胀气问题可以通过在电芯生产过程严格控制水分可以避免。
一旦发生电池胀气就会发生漏液等情况。
以上几种失效模式是非常严重的问题,可能会造成人员伤亡。
即使一个电芯使用1、2年没有问题,并不代表这个电芯以后没有问题,使用越久的电池失效的风险越大。
电芯的非安全性失效只是影响使用性能,主要有以下几点:
a)容量一致性差
动力电池的不一致性通常是指一组电池内电池的剩余容量差异过大、电压差异过大,引起电池续航能力变差。
引起电池间一致性变差的原因是多个方面的,包括电池的生产制造工艺,电池的存放时间长短,电池组充放电期间的的温度差异,充放电电流大小等。
目前解决方法主要是提高电池的生产制造工艺控制水平,从生产关尽可能保证电池的一致性,使用同一批次电池进行配组。
这种方法有一定效果,但无法根治,电池组使用一段时间后一致性差的问题还会出现,电池组发生不一致性问题后,如果不能及时处理,问题会愈加严重,甚至会发生危险。
b)自放电过大
电池制造时杂质造成的微短路所引起的不可逆反应是造成个别电池自放电偏大的最主要原因。
在大多电池生产厂家对电池的自放电微小时都可忽略,由于电池在长时间的充放电及搁置过程中,随环境条件发生化学反应,引起电池大自放电现象,这使电池电量降低,性能低下,不能满足使用需求。
c)低温放电容量减少
随着温度的降低,电解液低温性能不好,参与反应不够,电解液电导率降低而导致电池电阻增大,电压平台降低,容量也降低。
目前各厂家电池-20度下的
放电容量基本在额定容量的70%~75%。
低温下电池放电容量减少,且放电性能差,影响电动汽车的使用性能和续驶里程。
d)电池容量衰减
电池容置衰减主要来自于活性锂离子的损失以及电极活性材料的损失。
正极活性材料层状结构规整度下降,负极活性材料上沉积钝化膜,石墨化程度降低,隔膜孔隙率下降,导致电池电荷传递阻抗增大。
脱嵌锂能力下降,从而导致容量的损失。
电池容量衰减是电池不可避免的问题。
但是目前电池厂家应该首要解决前面安全性失效问题和电池一致性问题,在这个基础上再考虑延长电池的循环寿命。
二、BMS失效模式
电池的单体失效不仅和电池本身有关,也和电池管理系统BMS失效有关。
BMS 失效模式也会造成严重的事故有以下几类:
1、BMS电压检测失效导致电池过充电或过放电
连接、压线过程或接触不良导致电压检测线失效,BMS没有电压信息,充电时该停止时没有停止。
电池过充会着火、爆炸,磷酸铁锂过充至5V以上大部分只是冒烟,但是三元电池一旦过充,会发生爆炸。
而且,过充电容易导致锂离子电池中的电解液分解释放出气体,从而导致电池鼓胀,严重的话甚至会冒烟起火;电池过放电会导致电池正极材料分子结构损坏,从而导致充不进去电;同时电池电压过低造成电解液分解,干涸发生析锂,回到电池内短路问题。
在系统设计时应该选用可靠的电压采集线,在生产过程中严格管控,杜绝电压采集线的失效。
2、BMS电流检测失效
霍尔传感器失效,BMS采集不到电流,SOC无法计算,偏差大。
电流检测失效可能导致充电电流过大。
充电电流大,电芯内部发热大,温度超过一定温度,会使隔膜固化容量衰减,严重影响电池寿命。
3、BMS温度检测失效
温度检测失效导致电池工作使用温度过高,电池发生不可逆反应,对电池容量、内阻有很大影响。
电芯日历寿命跟温度直接相关,45度时的循环次数是25度时的一半,另外温度过高电池易发生鼓胀、漏液,爆炸等问题,因此在电池使
用过程中要严格控制电池的温度在20-45摄氏度之间,除能有效提高电池的使用寿命和可靠性之外还能有效避免电池低温充电析锂造成的短路以及高温热失控。
4、绝缘监测失效
在动力电池系统发生变形或漏液的情况下都会发生绝缘失效,如果BMS没有被检测出来,有可能发生人员触电。
因此BMS系统对监测的传感器要求应该是最高的,避免监测系统失效可以极大地提高动力电池的安全性。
5、电磁兼容问题通讯失效
对BMS系统来说,电磁兼容主要考核它抗电磁干扰能力。
电磁干扰会导致BMS通讯失效,引发以上几个问题。
6、SOC估算偏差大
目前所有BMS厂家普遍存在的问题,只偏差大小的差别。
基本上目前的检验标准要求都是5%以内,大部分厂家BMS应该都很难达到,因为实际使用中SOC 误差会越来越大,因为使用环境更加的复杂,影响精度的条件更多。
三、Pack系统集成失效模式
1、汇流排的失效
如果是螺栓连接,在后期使用过程中,螺栓氧化脱落或振动导致螺栓松了都会导致导体连接处产生大量的热,极端情况下会导致动力电池着火。
因此绝大部分动力电池系统生产厂家在Pack设计时电芯与电芯连接或模块与模块连接处采用激光焊接,或在连接处增加温度传感器通过检测的手段避免汇流排的失效。
2、动力电池系统主回路连接器失效
动力电池系统高压线通过连接器与外部高压系统相连。
连接器性能不可靠,在振动下发生虚接,产生高温烧蚀连接器。
一般来说连接器温度超过90度就会发生连接失效。
因此在系统设计时连接器需要增加高压互锁功能,或在连接器附进加温度传感器,时刻监测连接器的温度以防止连接器的失效。
3、高压接触器粘黏
接触器有一定次数的带载断开,大部分接触器在大电流带载闭合时烧蚀。
在系统设计一般采用双继电器方案,按照先后顺序闭合控制以避免高压接触器粘黏。
4、熔断器过流保护失效
高压系统部件中的熔断器的选型匹配,梯度先断哪个后断哪个需要综合考虑。
振动或外部受到碰撞挤压导致动力电池发生形变,密封失效,IP等级降低,因此在系统设计时需要考率电池箱结构的碰撞防护。
根据以上动力电池系统的各种失效模式,科研人员和电池厂商需要通过不断改进工艺和技术提高锂电池电芯的安全性,BMS系统厂商要充分了解电池的性能,基于动力电池的安全设计原则,设计出安全可靠的电池系统,同时正确的使用是保障电池安全性的最终屏障。
使用者要正确使用动力电池系统,杜绝机械滥用、
热滥用和电滥用,切实提高电动汽车的安全性和可靠性。