生产运作系统设计和分析
生产运作决策支持系统的设计与开发
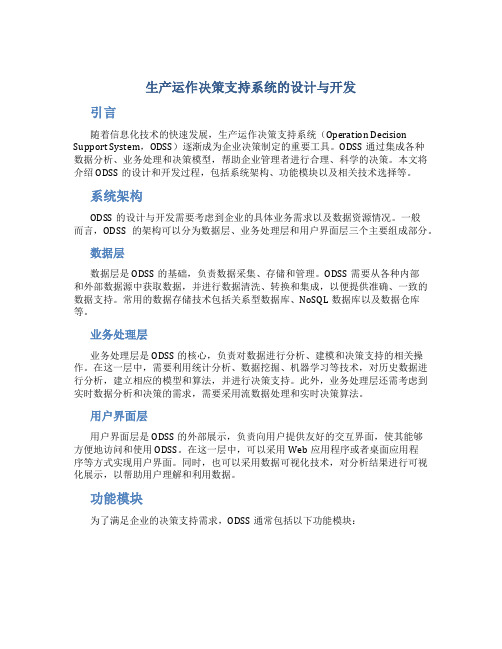
生产运作决策支持系统的设计与开发引言随着信息化技术的快速发展,生产运作决策支持系统(Operation Decision Support System,ODSS)逐渐成为企业决策制定的重要工具。
ODSS通过集成各种数据分析、业务处理和决策模型,帮助企业管理者进行合理、科学的决策。
本文将介绍ODSS的设计和开发过程,包括系统架构、功能模块以及相关技术选择等。
系统架构ODSS的设计与开发需要考虑到企业的具体业务需求以及数据资源情况。
一般而言,ODSS的架构可以分为数据层、业务处理层和用户界面层三个主要组成部分。
数据层数据层是ODSS的基础,负责数据采集、存储和管理。
ODSS需要从各种内部和外部数据源中获取数据,并进行数据清洗、转换和集成,以便提供准确、一致的数据支持。
常用的数据存储技术包括关系型数据库、NoSQL数据库以及数据仓库等。
业务处理层业务处理层是ODSS的核心,负责对数据进行分析、建模和决策支持的相关操作。
在这一层中,需要利用统计分析、数据挖掘、机器学习等技术,对历史数据进行分析,建立相应的模型和算法,并进行决策支持。
此外,业务处理层还需考虑到实时数据分析和决策的需求,需要采用流数据处理和实时决策算法。
用户界面层用户界面层是ODSS的外部展示,负责向用户提供友好的交互界面,使其能够方便地访问和使用ODSS。
在这一层中,可以采用Web应用程序或者桌面应用程序等方式实现用户界面。
同时,也可以采用数据可视化技术,对分析结果进行可视化展示,以帮助用户理解和利用数据。
功能模块为了满足企业的决策支持需求,ODSS通常包括以下功能模块:数据采集与预处理该模块负责从各种数据源中获取数据,并进行数据清洗、转换和集成,以保证数据的准确性和一致性。
常用的数据采集方式包括批量导入、实时采集和数据集成等。
数据分析与建模该模块利用统计分析、数据挖掘、机器学习等技术,对历史数据进行分析,并建立相应的模型和算法。
通过对数据的挖掘和分析,可以发现数据中隐藏的规律和关联,从而为决策提供支持。
生产运作管理系统设计
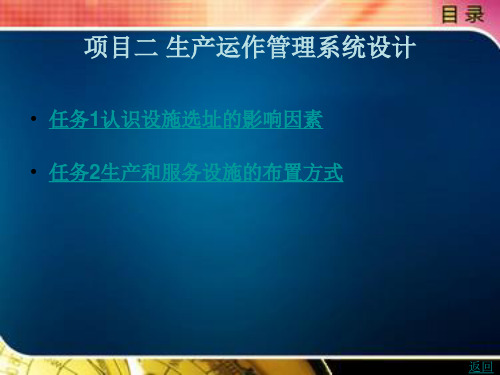
第一节 会计等式
应付账款一10实收资本+10 (8)以银行存款偿还东方公司剩余货款5万元。
资产=负债+所有者权益 银行存款一5应付账款一5 6月末该公司的资产负债表见表2-1。 通过以上几个经济业务的发生,证明会计等式是恒成立的。虽然一个 企业在生产经营中发生的经济业务是多种多样的,内容不一,但从它们 引起会计主体的资产、负债、所有者权益的增减变动来看,只有以下四 种类型。 (1)一项经济业务的发生,引起资产和权益,即会计等式两边同时
资产=债权人权益+所有者权益 债权人的权益则是企业的负债,那么这个公式就变为
资产=负债+所有者权益
上一页 下一页
第一节 会计等式
这一公式称为会计等式(或会计恒等式、基本等式、静态等式),是设置 账户、复式记账、试算平衡、编制资产负债表的理论依据。
(二)收入、费用、利润之间的关系 随着企业的经营活动,企业要获取收入,实现赢利。在企业取得收入 的同时,必然会发生相应的费用。企业只有通过收入与费用的比较,才 能计算确定一定会计期间的赢利水平,确定当期的利润。把它们的关系 用公式表示出来 收入一费用=利润 这一公式从动态方面反映了经营成果的形成,称为动态会计等式,是 编制利润表的理论依据。
资产=负债+所有者权益 固定资产+40实收资本+40 (2)向银行借入资金20万元,存入银行。 资产=负债+所有者权益
上一页 下一页
第一节 会计等式
银行存款+20短期借款+20 (3)购买材料一批8万元,以存款支付。 资产=负债+所有者权益 原材料+8 银行存款一8
(4)企业按法定程序报经批准减少注册资本2万元,以存款支付。 资产=负债+所有者权益 银行存款一2实收资本一2
生产与运作管理 第五章 生产系统设计.ppt

5.3.5 选址的方法
–量本利分析法 –分级加权评分法
量本利分析法
选址方案都有一定的固定成本和变动成本 可用于多个选址方案的比较
量本利分析法(续)
收入
利润
TC2
TC1
FC1 FC2
0 盈亏平衡点 Vo
V1
V2 产(销)量
评分法
全面比较不同选址方案,是一个多目标或多准 则的决策问题
5.2 生产能力概述
假定产品的计算
首先,计算假定产品的台时定额:
–tpj=(50×20+100×30+125×40+25×80)÷300
=36.67(台时) 然后,将各产品的计划产量折算成假定产品产量
–A:50×20/36.67= 27 –B:100×30/36.67=82 –C:125×40/36.67= 136 –D :25×80/36.67 = 55
4
2
6
5
联系簇
相对关系布置法
第三步,考虑其他“A”关系部门,如能加在主 联系簇上就尽量加上去,否则画出了分离的子 联系簇。本例中,所有的部门都能加到主联系 簇上去。
单元1
L
D
D
G
L 车床
原
单元2
材
L
G
料
单元3
L
L
G
P
成组生产单元布置示意图
成 D 钻床
品 库
G
磨床
5.4.4 几种典型的布置
形式(续)
按C形制造单元布置
机器2
机器3
机器1
机器4
入口 出口
机器6
机器5
C形制造单元布置示意图
5.4.4 几种典型的布置
生产系统规划与设计

生产系统规划与设计第一节厂址选择一、厂址选择的重要性厂址选择是生产运作系统规划和设计的重点内容。
任何一个生产运作系统都是由建筑物、设施、设备等各种物质要素构成的,是生产运作系统的空间实体形态的具体表现。
生产运作系统的规划与设计,就是运用科学的方法和手段对生产运作系统的各种物质要素进行合理的选择和布置,使其形成一个有机系统,能够用最经济的方式和最高的效率生产产品或提供服务。
其中,厂址选择是生产系统规划和设计的第一步,也是十分重要的一步。
厂址选择是指如何确定工厂设施的地理位置,它不仅对新建一个企业尤为重要,也是老厂因经济、技术原因而需要改扩建或搬迁必需解决的一个首要问题。
厂址选择的重要性表现在以下几个方面:第一,厂址一旦选定,就要投入大量的资金进行设施建设,许多资金就会沉淀为固定成本,很难加以改变,若选择厂址发生错误,必然造成巨大的经济损失和人力、物力的大量浪费。
我国过去在这方面的教训颇多,六十年代到七十年代,由于受到种种主观和客观因素的影响,把许多大型制[]造企业建设在偏僻山区,由于交通不便,信息闭塞,长期经济效益低下,职工不安心。
为了救活这些企业,国家又不得不在八十年代投入大量资金进行搬迁。
原有的厂址设施闲置或折价变卖,新搬迁需要的大量资金又给国民经济带来沉重负担。
第二,厂址选址对于工厂建成后的生产经营费用,产品和服务质量以及成本都有极大而长久的影响,一旦选择不当,带来的不良后果往往是难以消除的。
例如选址不当可能导致增加过多的运输费用,人力资源缺乏,原材料、燃料、动力供应困难,丧失竞争优势等问题,这些都不利企业生产经营,更说不上提高经济效益了。
对于服务业,一个不良的位置可能导致顾客丧失或付出很高的经营成本。
如果要在选定的厂址改善上述不利状况,往往十分困难,因为许多不利因素不是通过企业自身加强或改善管理等其他措施所能弥补的,除非迁移到另外一个条件合适的新厂址,但这要付出相当大的代价。
因此,在进行厂址选择时,必须充分考虑多方面因素的影晌,慎重地进行决策,绝不能草率行事。
生产运作管理之生产运作系统的设计
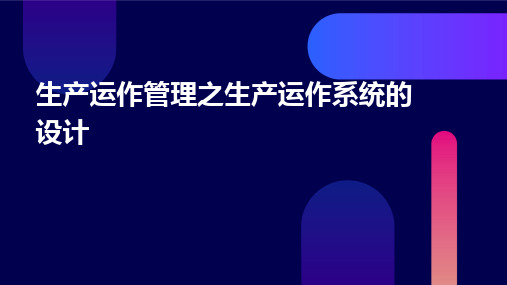
案例二:某机械制造企业的设备管理实践
总结词
强化设备管理,保障生产安全
详细描述
某机械制造企业重视设备管理,通过制定严格的设备维护和检修制度,确保设备的正常运行。该企业还采用了状 态监测和故障诊断技术,及时发现并解决设备故障,有效降低了生产事故的发生率。
案例三:某化工企业的安全与环保设计
总结词
注重安全与环保,实现可持续发展
生产运作管理之生产运作系统的 设计
目录
• 生产运作系统设计概述 • 产品开发与设计 • 生产流程设计 • 设备与设施管理 • 生产运作系统的安全与环保设计 • 生产运作系统设计的实践案例
01
生产运作系统设计概述
定义与目标
定义
生产运作系统的设计是指根据市场需求、企业战略和资源条件,对生产运作系 统的整体架构、设施布局、设备配置、工艺流程等方面进行规划和安排的过程。
目标
提高生产效率、降低生产成本、优化资源配置、提升产品质量、满足客户需求, 以及实现可持续发展。
设计原则与流程
整体性原则
将生产运作系统视为一个整体, 综合考虑各要素之间的关系,实 现整体最优。
适应性原则
根据市场需求、企业战略和资源 条件的变化,灵活调整生产运作 系统的设计。
设计原则与流程
• 可持续性原则:在追求经济效益的同时,注重环境友好和 社会责任,实现可持续发展。
详细描述
某化工企业在生产运作系统的设计中,充分考虑了安全与环保因素。通过采用先进的工 艺技术和设备,降低生产过程中的危险和污染。同时,该企业还建立了完善的环境管理 体系,确保废弃物的妥善处理和资源的循环利用,实现了经济效益和环境效益的双重提
升。
THANK YOU
人机工程学原理
生产运作流程的分析与改进

生产运作流程的分析与改进一、引言生产运作是企业核心活动之一,其流程的高效与优化对企业的业务运作和成本控制起着至关重要的作用。
本文将重点分析生产运作流程的现状和问题,并提出改进措施以提升生产效率和质量。
二、生产运作流程分析1.原材料准备在生产运作流程中,原材料的准备是关键环节。
分析原材料的采购渠道、供应商合作情况以及存储管理,确保原材料的质量和供应稳定性,避免因原材料问题导致生产延误或产品质量问题。
2.生产计划制定生产计划制定应根据市场需求和企业资源状况,合理安排生产订单和计划排产。
通过对生产工序的优化与分析,合理安排生产顺序和生产线辅助设备,提高生产效率和经济性。
3.生产过程控制生产过程控制是保障产品质量和生产效率的关键环节。
要建立完善的质量控制标准和流程,确保产品符合设计和用户需求。
同时,对生产过程进行监控和数据分析,及时发现问题并采取有效措施进行改进和纠正。
4.生产设备维护生产设备的正常运行对生产效率和产品质量至关重要。
定期对生产设备进行维护、保养和检修,及时处理设备故障,减少停机时间,提高生产连续性和稳定性。
5.物流和仓储管理物流和仓储管理对整个生产运作流程有着直接影响。
合理规划物流运输路线,减少物流成本和时间;优化仓储布局,提高仓储效率和物资调配能力。
三、改进措施1.引入信息化系统通过引入先进的信息化系统,如企业资源计划(ERP)系统,实现生产过程的全面监控和数据实时分析。
同时,可以优化生产计划、物流配送等环节,提高生产运作效率和准确性。
2.精益生产方法采用精益生产方法,通过流程优化、减少浪费和缩短周期时间来提高生产效率和质量。
例如,采用价值流分析方法,找出生产过程中的瓶颈和浪费环节,并持续改进以追求生产过程的最大价值。
3.培训和激励加强员工培训,提高员工的专业技能和操作能力,使其更好地适应生产运作的要求。
同时,建立激励机制,通过奖惩制度激发员工的积极性和主动性,推动流程改进和工作效率的提升。
某公司生产计划系统数据与数据流程分析
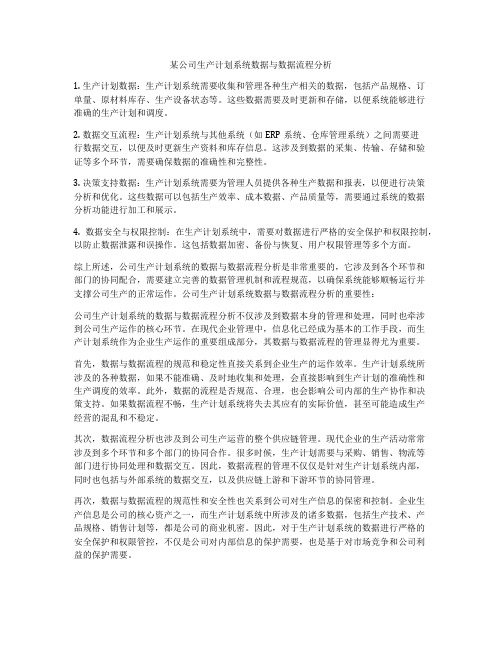
某公司生产计划系统数据与数据流程分析1. 生产计划数据:生产计划系统需要收集和管理各种生产相关的数据,包括产品规格、订单量、原材料库存、生产设备状态等。
这些数据需要及时更新和存储,以便系统能够进行准确的生产计划和调度。
2. 数据交互流程:生产计划系统与其他系统(如ERP系统、仓库管理系统)之间需要进行数据交互,以便及时更新生产资料和库存信息。
这涉及到数据的采集、传输、存储和验证等多个环节,需要确保数据的准确性和完整性。
3. 决策支持数据:生产计划系统需要为管理人员提供各种生产数据和报表,以便进行决策分析和优化。
这些数据可以包括生产效率、成本数据、产品质量等,需要通过系统的数据分析功能进行加工和展示。
4. 数据安全与权限控制:在生产计划系统中,需要对数据进行严格的安全保护和权限控制,以防止数据泄露和误操作。
这包括数据加密、备份与恢复、用户权限管理等多个方面。
综上所述,公司生产计划系统的数据与数据流程分析是非常重要的,它涉及到各个环节和部门的协同配合,需要建立完善的数据管理机制和流程规范,以确保系统能够顺畅运行并支撑公司生产的正常运作。
公司生产计划系统数据与数据流程分析的重要性:公司生产计划系统的数据与数据流程分析不仅涉及到数据本身的管理和处理,同时也牵涉到公司生产运作的核心环节。
在现代企业管理中,信息化已经成为基本的工作手段,而生产计划系统作为企业生产运作的重要组成部分,其数据与数据流程的管理显得尤为重要。
首先,数据与数据流程的规范和稳定性直接关系到企业生产的运作效率。
生产计划系统所涉及的各种数据,如果不能准确、及时地收集和处理,会直接影响到生产计划的准确性和生产调度的效率。
此外,数据的流程是否规范、合理,也会影响公司内部的生产协作和决策支持。
如果数据流程不畅,生产计划系统将失去其应有的实际价值,甚至可能造成生产经营的混乱和不稳定。
其次,数据流程分析也涉及到公司生产运营的整个供应链管理。
现代企业的生产活动常常涉及到多个环节和多个部门的协同合作。
生产运作系统的设计和分析

生产运作系统的设计和分析一、引言生产运作系统(Production and Operation System,简称POS)是指一个组织或企业用于实现产品或服务的生产和交付的系统。
一个高效的POS能够提高企业的生产效率、降低成本、提升产品质量,并满足客户需求。
因此,本文将重点讨论生产运作系统的设计和分析,以帮助企业在竞争激烈的市场中获得竞争优势。
二、设计生产运作系统的关键要素1.产品设计与开发产品设计与开发是POS的基础。
企业需要根据市场需求和竞争情况确定产品的规格、功能和外观设计。
同时,应考虑产品的可制造性,以便在生产过程中实现高效率和高质量。
2.设备与工艺设备和工艺决定了生产过程的效率和产品质量。
企业应选择合适的设备和工艺,确保生产线的平稳运行,并通过持续改进来提升生产效率和产品质量。
3.人员管理与培训人员是POS中不可或缺的关键要素。
企业应该建立科学的人员管理制度,激励员工的积极性和创造力,并提供必要的培训以提升员工的技能水平。
只有具备高素质的员工才能保证POS的稳定运行。
4.供应链管理供应链管理涉及到原材料和零部件的采购、库存控制以及与供应商的合作。
企业应建立高效的供应链管理系统,确保物料的及时供应,降低库存成本,并与供应商建立长期稳定的合作关系。
5.质量控制与检测质量控制和检测是确保产品质量的关键环节。
企业应制定科学的质量控制流程,并进行严格的质量检测,以确保产品符合设计规格,并满足客户需求。
三、分析生产运作系统的关键指标1.生产效率生产效率是衡量POS运行效果的重要指标。
可以通过衡量单位时间内生产的产品数量、设备利用率、人力利用率等指标来评估生产效率,并通过持续改进来提高生产效率。
2.产品质量产品质量是企业赢得客户信赖的关键要素。
可以通过衡量产品的不良品率、售后服务问题率等指标来评估产品质量,并通过质量控制和改进来提升产品质量。
3.生产成本生产成本是影响企业盈利能力的重要因素。
可以通过衡量单位产品的生产成本、原材料利用率、能源消耗等指标来评估生产成本,并采取相应的措施降低生产成本。
- 1、下载文档前请自行甄别文档内容的完整性,平台不提供额外的编辑、内容补充、找答案等附加服务。
- 2、"仅部分预览"的文档,不可在线预览部分如存在完整性等问题,可反馈申请退款(可完整预览的文档不适用该条件!)。
- 3、如文档侵犯您的权益,请联系客服反馈,我们会尽快为您处理(人工客服工作时间:9:00-18:30)。
§3.1运作系统的布置及其分析
一、选址 1 2 设施网络选址 二、布置原则 1 满足生产过程要求 2 追求高效率和合理的设备利用率 3 保持生产的柔性
生产运作系统设计和分析
三、布置分析及其改进
工艺原则布置:如何使物流有序 对象原则布置:如何使每个单元的操作时间大致相等 混合原则布置:物流有序,瓶颈的解决
仓库及堆放地的位置。 ·辅助服务部门S:生产系统的生产支持系统部分 ·时间T:什么时候、用多少时间生产出产品,包括各工序的操作
时间、更换批量的次数
生产运作系统设计和分析
·准备原始资料:明确基本要素P、Q、R、S、T ·物流分析与作业单位相互关系分析
-产品制造费用的20%-50%用作物料搬运,有效的布置能减少搬
45-80
不希望接近 X
酌情而定
生产运作系统设计和分析
·作业单位占地面积计算 ·绘制作业单位面积相关图 ·修正:修正因素包括物料搬运方式、操作方式、存 储周期等。 ·方案评价与择优
-选择方案评价因素,如物料搬运效率及方便 性、扩建可能性、生产管理的方便性、安全生产、辅 助服务方便性等。
将所有作业分配到各工作站 向第一工作站分配作业,逐项增加,直至作业 完成时间等于节拍。 5)平衡后的效率:
完成作业的总工作时间/(实际工作站数目*节拍C)
生产运作系统设计和分析
装配线平衡例 J型玩具马车要在一个传送带上组装,每天需生产500辆。每天的生产时间为420分钟。
。 根据节拍和作业次序的限制,求工作站最少的平衡方式
生产运作系统设计和分析
四、装配线的柔性分析
直线型: U型: 环型: 人的柔性调节装配线
生产运作系统设计和分析
五、装配线的平衡
节拍:相邻两产品通过装配线尾端的间隔时间
工作站:操作者传递零件或完成装配作业
作业基本单元:工作站的操作组成
一个工作站要完成的工作总量与分配到工作站的基本作业单元总 数是一致的。
作业 A B C D E F G H I J K
时间/秒 描述
必须提前的作业
45 安装后轮支架,拧紧四个螺母 -
11 插入后轴
A
9 拧紧后轴支架螺栓
B
50 安装前轴,拧紧四个螺母
-
15 拧紧前轴螺栓
D
12 安装1#后车轮,拧紧轮轴盖
C
12 安装2#后车轮,拧紧轮轴盖
C
12 安装1#前车轮,拧紧轮轴盖
规则,可得到更好的平衡方案
生产运作系统设计和分析
六、作业分解
最长的作业时间决定了生产线上节拍的最小可能值 一种作业的时间为40秒,大于节拍36秒,此作业如何
处理? 可能的方法有:
作业分解:使一个作业分解到两个工作站 作业共享:作业能不能在相邻工作站(协助)进行一点共享 设立平行工作站: 聘用操作技巧高的工人 加班:以每40秒生产1件的速度进行生产 重新设计 工作团队
从至表:方阵,方阵的行-物料移动的源,从 方阵的列-物料移动的目的地,至 行列交叉点标明由源到目的地的物流量。
生产运作系统设计和分析
一般物流强度
O
可忽略搬运
U
40
10
·绘制作业单位位置相关图
作业单位相互关系等级
含义
符号
比例
绝对重要
A
2-5
特别重要
E
3-10
重要
I
5-15
一般密切
O
10-25
不重要
U
生产运作系统设计和分析
效率计算: 效率=T/(N*C)=195/(5*50.4)=0.77
评价平衡方案:装配线不平衡,闲置时间为23% 更好的方案: 規則2平衡装配线,规则1作为第二
规则,可得到更好的平衡方案
生产运作系统设计和分析
混合装配线的平衡
混合装配线的平衡要解决产品的生产排 序问题,从而使同一生产线在指定的日 期内生产不同型号的产品,实现多种产 品循环生产。
12 38.4 H,I
Байду номын сангаас
H,I
F,G,H,I H,I
H 12 26.4 I
I
I 12 14.4 J
J
8 6.4 无
工作站5 K 9 41.4 无
生产运作系统设计和分析
效率计算: 效率=T/(N*C)=195/(5*50.4)=0.77
评价平衡方案:装配线不平衡,闲置时间为23% 更好的方案: 規則2平衡装配线,规则1作为第二
作业 作业 剩余的 可安排的 紧后作业 时间 时间 紧后作业 最多的作业
工作站1 A 45 5.4 无 工作站2 D 50 0.4 无 工作站3 B 11 39.4 C,E C,E
时间最长 的作业
E
E C F 工作站4 G
15 24.4 C,H,I C
9 15.4 F,G,H,I F,G,H,I
12 3.4 无
2 S-L物P流程运分费析序用方的法步30骤%左右。
工艺流程图:在工艺过程图上注明各工序间的物流量, 适用大批量,产品品种单一的生产。工艺布置
多种产品工艺过程表:将各产品的生产工艺流程汇总在一起。 多品种,批量较大的生产。(10种左右)
成组方法:分组,再用工艺过程图或多种产品工艺过程表分析。 中、小批量生产,品种达到数十种时。
生产运作系统设计和分析
七、工艺原则布置
生产运作系统设计和分析
SLP法(系统布置法)
1 系统布置基本要素P、Q、R、S、T
·产品P:影响生产系统的组成及其作业单位间的相互关系、生产 设备的类型、物料搬运方式。
·产量Q:影响生产系统的规模、设备数量、运输量、建筑物面积 ·生产路线R:工艺流程,影响作业单位间的关系、物料搬运路线、
平衡
:将基本工作单元分配到各个工作站,使每个工作站在节
拍内都处于繁忙状态,使各工作站的闲置时间最小。
生产运作系统设计和分析
装配线平衡的步骤
1)流程图表示作业先后关系 2)求节拍C=每天的工作时间/每天的计划产量 3)满足节拍最少的工作站
理论值=完成作业的总工作时间/节拍C 4)选择作业分配原则-安排多后续作业或持续时间很长的作业)
E
12 安装2#前车轮,拧紧轮轴盖
E
8 安装前轴上的车把手,拧紧螺栓和螺钉 F,G,H,I
9
上紧全部螺栓和螺钉
195
生产运作系统设计和分析
J型玩具马车的流程图
A 45
B 11 C 9
F 12 G 12
J8
D 50
H 12
E 15
I 12
生产运作系统设计和分析
K9
计算节拍: C=60*420/500=50.4(秒/辆) 工作站数量的理论最小值:N=T/C=190/50.4=3.87=4 选择作业分配规则: 按后续作业数量的多少; 2)按作业时间最长 根据后续作业最多规则平衡装配线