丙烯酸酯液体改性环氧树脂胶粘剂
丙烯酸酯

丙烯酸酯丙烯酸酯,是丙烯酸及其同系物的酯类的总称,能自聚或和其他单体共聚,是制造胶粘剂、合成树脂、特种橡胶和塑料的单体。
比较重要的丙烯酸酯有丙烯酸甲酯、丙烯酸乙酯、2-甲基丙烯酸甲酯和2-甲基丙烯酸乙酯等。
基本信息∙中文名称丙烯酸酯∙外文名称acrylic ester;acrylate∙化学式CH2=CHCOOCH3∙性质橡胶等简介:名称:丙烯酸酯英文名称:acrylic ester;acrylate化学式:CH2=CHCOOR分类:商品牌号很多,根据其分子结构中所含的不同交联单体,加工时硫化体系也不相同,由此可将丙烯酸酯橡胶划分为含氯多胺交联型、不含氯多胺交联型、自交联型、羧酸铵盐交联型、皂交联型等五类。
此外,还有特种丙烯酸酯橡胶,如含氟型及热塑性丙烯酸酯橡胶等性能:丙烯酸酯橡胶的性能受其主要单体丙烯酸烷基酯中烷基碳原子数目的影响。
以丙烯酸酯为基础的橡胶,耐油、耐热性较好;而以丙烯酸丁酯为基础的橡胶,因烷基碳原子数目的增多,对酯基极性基的屏蔽效应增大,因此使耐水性有所改善,同时由于屏蔽效应,减弱了橡胶分子间力,增大了内部塑性,从而使脆性温度降低,耐寒性较好。
若通过上述两种单体并用,则可得到介于两者性能之间的橡胶。
特点:无论哪一种类型的丙烯酸酯橡胶,其分子结构的共同特点有两个:一是高极性;二是完全饱和性。
从而使其具有优越的耐矿物油和耐高温氧化性能。
其耐油性仅次于氟胶,而与一般中高丙烯晴含量的丁腈橡胶相似。
而耐热性介于通用橡胶和硅、氟橡胶之间,比丁腈橡胶使用温度高出30~60℃,最高使用温度180℃,断续和短时间使用可达200℃,在150℃热空气老化数年性能无明显变化。
此外,最重要的是其对含有硫、氯、磷等极压剂的极压型润滑油十分稳定,使用温度可达150℃,间断使用温度可更高些。
而带有双键的丁腈橡胶在含有极压剂的油中,当温度超过110℃时,即发生显著硬化与变脆。
丙烯酸酯橡胶还具有优良的抗臭氧性、气密性、耐屈挠和耐裂口增长性,以及抗紫外线变色性等。
含环氧和长氟碳链的丙烯酸酯的制备及其改性环氧树脂涂料性能研究

含环氧和长氟碳链的丙烯酸酯的制备及其改性环氧树脂涂料性能研究张晓伟【摘要】采用两步法合成了可聚合含氟丙烯酸酯预聚物(FM),并将其与甲基丙烯酸缩水甘油酯(GMA)共聚合成了含环氧和长氟碳链的丙烯酸酯共聚物(CFPA).采用GPC、1H NMR对该聚合物的结构进行表征.将CFPA与环氧树脂E51共混得到改性环氧树脂涂料.对涂膜的表面性能以及本体性能进行了研究.结果表明:加入少量CFPA(0.5%)便可使涂膜的疏水性大幅度提高(水接触角97.8°,二碘甲烷接触角66.0°,表面能25.16 mN/m).X射线光电子能谱(XPS)研究发现,含氟丙烯酸酯聚合物添加量为4%时,CFPA改性的环氧树脂涂膜表面氟原子含量是无规含氟含环氧丙烯酸酯(RFPA)改性的环氧树脂涂膜的8.39倍,氟原子富集于改性涂膜表面,使得材料疏水性得到提高.对改性涂膜的本体性能进行研究,结果表明:改性涂膜具有高凝胶含量、高硬度(4H)、优异的附着力(0级)和低吸水率.【期刊名称】《涂料工业》【年(卷),期】2016(046)012【总页数】6页(P16-21)【关键词】丙烯酸酯材料;长氟链;环氧树脂;低表面能;涂料【作者】张晓伟【作者单位】三友众泰化工涂料有限责任公司,内蒙古137500【正文语种】中文【中图分类】TQ630.4环氧树脂因具有优异的粘结性、热性能、机械性能以及化学稳定性等而被广泛应用于涂料、胶粘剂、电子封装等领域[1-3]。
然而,在固化过程中环氧基开环产生的羟基,会使材料的表面能升高,从而限制了环氧树脂在防污、防涂鸦涂料等方面的应用[4]。
含氟聚合物具有低表面能、优异的疏水疏油特性、优异的热稳定性以及化学稳定性,因此可用于疏水、防水涂料等[4-10]。
而在众多的含氟聚合物当中,含氟丙烯酸酯聚合物最为常用。
从结构上分析,利用含氟聚合物改善环氧树脂高表面能的问题,需要让尽可能多的氟原子迁移至表面以降低材料的表面能,赋予材料疏水疏油特性。
丙烯酸酯结构胶和环氧树脂结构胶

丙烯酸酯结构胶和环氧树脂结构胶
丙烯酸酯结构胶和环氧树脂结构胶是两种常见的结构胶类型,它们在性能和用途上有一些区别。
1. 丙烯酸酯结构胶:
-优点:丙烯酸酯结构胶具有较高的固化速度、良好的粘接强度、较高的抗冲击性和抗疲劳性。
它们在室温下可以快速固化,常用于快速固定和粘结各种材料。
-缺点:丙烯酸酯结构胶的耐高温性能和耐化学性相对较差,不适用于高温或化学腐蚀环境。
-应用:丙烯酸酯结构胶常用于汽车制造、航空航天、电子设备等领域的结构粘接和固定。
2. 环氧树脂结构胶:
-优点:环氧树脂结构胶具有优异的粘接强度、高耐温性、良好的耐化学性和电绝缘性能。
它们可以在广泛的温度范围内保持稳定的性能。
-缺点:环氧树脂结构胶的固化速度相对较慢,需要较长的固化时间。
-应用:环氧树脂结构胶常用于航空航天、汽车、电子、建筑等领域的结构粘接、封装和加固。
选择哪种类型的结构胶取决于具体的应用需求和工作条件。
如果需要快速固化和较高的抗冲击性,可以选择丙烯酸酯结构胶。
如果需要更高的耐温性和耐化学性,以及良好的粘接强度,那么环氧树脂结构胶可能更适合。
在选择结构胶时,还应考虑材料的兼容性、固化条件和所需的粘接强度等因素。
丙烯酸酯改性己二胺固化剂对环氧树脂性能的影响
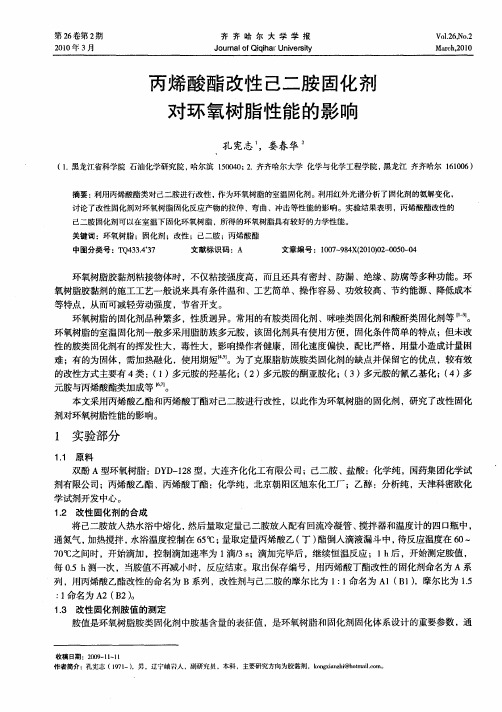
2 1 年 3月 00
齐 齐 哈 尔 大 学 报
J u n l f qh lUnv st o ra ia‘ ieri o Qi y
Vo. 6No2 1 , . 2 M, c ,0 0 a h2 1 r
丙 烯 酸 酯 改 性 己二胺 固化 剂
对 环 氧 树脂 性 能 的影 响
中图分类号 :T 4 343 Q 3. 7 ‘ 文献标识码 :A 文章 编号 :10 - 8X 2 1)20 5- 4 07 94 (0 00 - 0 0 0
环氧树脂胶黏剂粘接物体时 ,不仅粘接强度高 ,而且还具有密封 、防漏 、 绝缘 、防腐等多种功能。环
氧树脂胶黏剂的施工工艺一般说来具有条件温和、工艺简单 、操作容易、功效较高 、节约能源 、降低成本
第2 期
丙烯酸酯改性 已二胺 同化剂对环 氧树脂性能 的影响
・ 1・ 5
常用与中和 1 多胺 同化剂中胺基所需要的酸等 当量的氢氧化钾 K H的毫克数来表示 。 g O 可以用化学分析的
方 法来 测定 。
14 性 能测试 .
红外分析 ,采用 美 国 P 公 司的 F —R 型的红外光 谱仪进行测试 。拉伸 剪切强度按照 国家标准 E TI G /7 2—6 采用济南蓝光机电技术发展 中心 的 N W一 0 BT 14 8 , L 2 型拉伸剪切试验机测试 , 拉伸速度为 1 mm n 0 / i。 m 涂膜铅笔划痕硬度测试 , 按照国家标准 G /6 3— 96 采用天津市中亚材料试验机厂的 Q Q型涂膜铅笔 B 79 19 , T H
孔 宪志 ,娄春华
(. 1 黑龙江省科学院 石油化学研究院 , 哈尔滨 104 ; . 5 0 0 2 齐齐哈尔大学 化学与化学工程 学院 , 黑龙江 齐齐哈尔 1 10 ) 606
环氧树脂胶和丙烯酸酯胶

环氧树脂胶和丙烯酸酯胶环氧树脂胶和丙烯酸酯胶是两种常用的高分子材料,它们在结构和性能上有所不同,但都广泛应用于粘接、密封和涂层等领域。
环氧树脂胶:成分与结构环氧树脂是由双酚A和环氧氯丙烷通过缩聚反应制得的高分子化合物。
它由环氧基团(-CH-CH-)和芳香族基团(如苯环)组成。
固化剂通常为胺类或酸酐,与环氧树脂反应形成三维交联网络。
特性1. 高粘接强度:环氧树脂具有极强的粘接能力,能与多种材料形成牢固的结合。
2. 耐化学性:对油类、溶剂和多数酸碱有很好的抵抗力。
3. 耐热性:一般可在-50℃到150℃范围内使用,部分特殊配方可耐受更高温度。
4. 电气绝缘性:具有良好的电绝缘性能,适用于电气绝缘领域。
5. 低收缩率:固化过程中体积收缩小,减少应力产生。
应用环氧树脂胶常用于金属、塑料、陶瓷等材料的粘接,也用于电子行业的封装、电路板的保护、地面涂层等。
丙烯酸酯胶成分与结构丙烯酸酯胶是基于丙烯酸或甲基丙烯酸及其酯类单体的聚合物。
这些单体可以通过自由基聚合反应形成长链聚合物。
固化剂通常为过氧化物或其他引发剂。
特性1. 快速固化:丙烯酸酯胶固化速度快,适合需要快速修复或粘接的场合。
2. 透明性:固化后通常保持透明或半透明,适用于需要美观效果的场合。
3. 粘接性:对多种材料具有良好的粘接能力,尤其是玻璃和某些塑料。
4. 耐候性:对紫外线和气候变化有一定的抵抗力。
5. 柔韧性:相比环氧树脂,丙烯酸酯胶通常更加柔软和弹性。
应用丙烯酸酯胶主要用于玻璃粘接、塑料粘接、透明密封、装饰性涂层、光学元件的粘接等。
比较两者都具有优异的粘接性能,但在耐温性、硬度、耐化学品性等方面存在差异。
环氧树脂胶因其高强度、耐高温、低收缩率而适用于结构性粘接和重载环境;而丙烯酸酯胶则因其快速固化、透明性和良好的柔韧性而适用于需要快速处理和美观效果的场合。
选择哪一种胶粘剂取决于具体的应用需求和工作条件。
环氧丙烯酸酯的性能与用途

环氧丙烯酸酯的性能与用途环氧丙烯酸酯是一种重要的化学物质,具有优异的性能和广泛的用途。
本文将从环氧丙烯酸酯的性能特点、制备方法和常见的应用领域等方面进行探讨。
环氧丙烯酸酯的性能特点需要考虑。
作为一种双官能团化合物,环氧丙烯酸酯具有很高的反应活性和多种官能团的反应选择性,使其具备独特的化学特性。
环氧丙烯酸酯还具有出色的耐化学腐蚀性、耐候性和机械性能,以及优异的粘附性和耐磨性。
这些特点使得环氧丙烯酸酯在广泛的应用领域发挥着重要作用。
环氧丙烯酸酯的制备方法值得关注。
环氧丙烯酸酯的制备主要通过环氧树脂和丙烯酸酯的反应得到。
一种常见的制备方法是环氧树脂与丙烯酸酯在催化剂的作用下,通过环氧开环反应生成环氧丙烯酸酯。
也可以通过环氧树脂的缩聚反应、环氧树脂和酸酐的酯交换反应等方法制备环氧丙烯酸酯。
这些制备方法灵活多样,可根据不同的用途需求来选择合适的方法。
随后,我们需要了解环氧丙烯酸酯的常见用途。
环氧丙烯酸酯广泛应用于涂料、胶粘剂、电子封装材料、复合材料和油田化学品等领域。
在涂料方面,环氧丙烯酸酯作为一种优良的交联剂,能够提供高度的耐久性和保护性能,广泛应用于金属、混凝土和木材表面的防护涂层。
在胶粘剂领域,环氧丙烯酸酯可以作为粘接剂和封胶剂,具有粘附性强、强度高的特点,可用于汽车、航空航天、电子等行业。
在电子封装材料方面,环氧丙烯酸酯可以作为耐高温、耐化学腐蚀的封装材料,广泛应用于半导体封装和电子元器件的保护。
在复合材料领域,环氧丙烯酸酯可以作为增强剂与其他材料复合,提高材料的强度、硬度和耐久性。
在油田化学品方面,环氧丙烯酸酯常用于油井水泥浆稳定剂和封隔剂,能够提高油井的完井质量和产能。
综上所述,环氧丙烯酸酯作为一种重要的化学物质,具有独特的性能和广泛的用途。
其出色的化学特性、制备方法的灵活性以及广泛的应用领域使环氧丙烯酸酯成为许多行业中不可或缺的材料。
随着科技的不断进步,环氧丙烯酸酯的应用前景将继续拓展,为各行各业带来更多的创新和发展机会。
改性丙烯酸酯胶粘剂
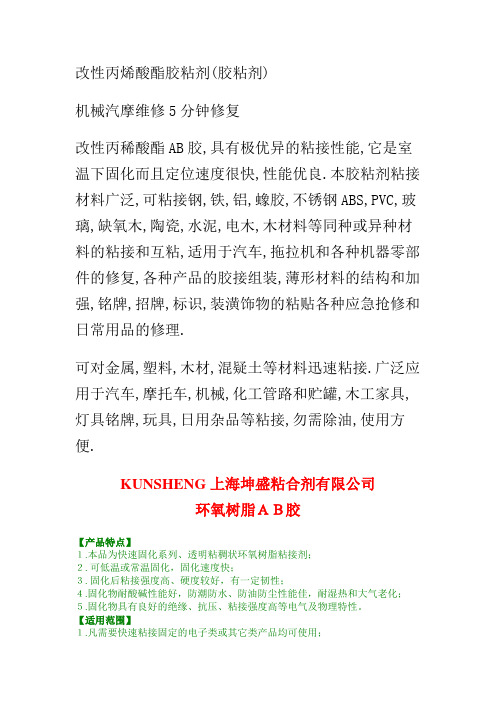
改性丙烯酸酯胶粘剂(胶粘剂)机械汽摩维修5分钟修复改性丙稀酸酯AB胶,具有极优异的粘接性能,它是室温下固化而且定位速度很快,性能优良.本胶粘剂粘接材料广泛,可粘接钢,铁,铝,蟓胶,不锈钢ABS,PVC,玻璃,缺氧木,陶瓷,水泥,电木,木材料等同种或异种材料的粘接和互粘,适用于汽车,拖拉机和各种机器零部件的修复,各种产品的胶接组装,薄形材料的结构和加强,铭牌,招牌,标识,装潢饰物的粘贴各种应急抢修和日常用品的修理.可对金属,塑料,木材,混疑土等材料迅速粘接.广泛应用于汽车,摩托车,机械,化工管路和贮罐,木工家具,灯具铭牌,玩具,日用杂品等粘接,勿需除油,使用方便.KUNSHENG上海坤盛粘合剂有限公司环氧树脂AB胶【产品特点】1.本品为快速固化系列、透明粘稠状环氧树脂粘接剂;2. 可低温或常温固化,固化速度快;3. 固化后粘接强度高、硬度较好,有一定韧性;4.固化物耐酸碱性能好,防潮防水、防油防尘性能佳,耐湿热和大气老化;5.固化物具有良好的绝缘、抗压、粘接强度高等电气及物理特性。
【适用范围】1.凡需要快速粘接固定的电子类或其它类产品均可使用;2. 广泛应用于电子元器件及工艺品、礼品的粘接固定,对于金属、陶瓷、木材、玻璃及硬质塑胶之间的封装粘接,有优异的粘接强度;3.不适用于有弹性或软质材料类产品的粘接。
1. 要粘接密封的部位需要保持干燥、清洁;2.按配比取量,A、B剂混合后需充分搅拌均匀,以避免固化不完全;3.搅拌均匀后请及时进行注胶,并尽量在可使用时间内使用完已混合的胶液;4.固化过程中,请及时清洁使用的容器及用具,以免胶水凝固在器具物品上。
【固化后特性】硬度Shore D ≥70吸水率25℃%24小时<0.15抗压强度kg/mm2 ≥50剪切强度(钢/钢)kg/mm2 ≥13拉伸强度(钢/钢)kg/mm2 ≥22介电常数1KHZ 3.8~4.2体积电阻25℃Ohm-cm ≥1.35 ×1015表面电阻25℃Ohm ≥1.2×1014耐电压25℃Kv/mm ≥16~18【注意事项】1.本品在混合后会开始固化,其粘稠度会很快上升,并会放出热量;2.注意:该产品固化速度很快,请尽可能减少一次配胶的量!混合在一起的胶量越多,其反应就越快,固化速度也会越快,并可能伴随放出大量的热量,请注意控制一次配胶的量,因为由于反应加快,其可使用的时间也会缩短,混合后的胶液尽量在短时间内使用完;3.有极少数人长时间接触胶液会产生轻度皮肤过敏,有轻度痒痛,建议使用时戴防护手套,粘到皮肤上请用丙酮或酒精擦去,并使用清洁剂清洗干净;4.在大量使用前,请先小量试用,掌握产品的使用技巧,以免差错。
丙烯酸酯改性双环戊二烯酚型环氧树脂及其性能研究

DP C D酚 型 环 氧树 脂 , 自制 ; 甲基 丙 烯 酸 甲 酯 ( MMA) 甲 基 六 氢 苯 酐 ( e P 、 烯 酸 丁 酯 、 I HH A) 丙 M l A 聚酰胺 均 为工业 品 ; )、 B 过氧 化苯 甲酰 ( P 、 B O) 偶 氮 二 异 丁 腈 ( [N) 4, 一 二 氨 基 二 苯 甲 烷 AB 、 4 (D 、 D M) 甲苯 、5 乙醇 、 酸 、 氧 化钠 、 酸钠 均 9% 盐 氢 碳 为化学纯 试剂 ; 实验 用水 为蒸 馏水 。
维普资讯
研 究 报告 及 专论
粘 接 20。 f 022 2 3
丙 烯 酸 酯 改 性 双 环 戊 二 烯 酚 型 环 氧 树 脂
及 其 性 能 研 究
孔振 武 黄 焕 孙光祥 一
( 中国林 业科学 研究疏林产 化学 工业 研究所 , 南京市 2 04 ) 10 2
收 稿 日期 :0 2—0 20 1一{ 5 作 者简舟 : 孔振武 男 , 6 1 5年生 . . 9 博: 中国#业科 学研究院# 产化学 工 业曰 究所副研究员。 f 江 苏 省 科 委 应 斤 基 础 研 究 基 金 资 助 坝 目 ( 目编 号: 】 项
B9 13 J7 4 )
3 结 果 与讨 论
④ 丙烯 酸酯改 性 D P C D酚 型环 氧 树  ̄/ D 体 DM
系 8 0℃ ×5 h+1 0 ℃ ×8 h; 2
⑤ E一 1环氧 树脂/ D 5 D M体 系 l0℃ × 。 2 8h
型 丌 一I 谱仪 上分 析 。 R光
2 6 漆膜 性 能测定 . 2 6 1 漆膜 的制 备 .. 按 2 2制成 试样 , 以溶 剂 ( 0 二 甲苯 + 0 7% 3 %正
- 1、下载文档前请自行甄别文档内容的完整性,平台不提供额外的编辑、内容补充、找答案等附加服务。
- 2、"仅部分预览"的文档,不可在线预览部分如存在完整性等问题,可反馈申请退款(可完整预览的文档不适用该条件!)。
- 3、如文档侵犯您的权益,请联系客服反馈,我们会尽快为您处理(人工客服工作时间:9:00-18:30)。
丙烯酸酯液体改性环氧树脂胶粘剂
3.2 胶粘剂力学性能
采用环氧基含量为1.2 mmol·g-1的丙烯酸酯液体橡胶增韧环氧树脂胶粘剂,其力学性能见表3。
由表3可见,环氧树脂胶粘剂对不同材料有不同的粘接性,但加入丙烯酸酯液体橡胶后拉伸剪切强度都有不同程度的提高,铝合金试片的拉剪强度提高了133%,复合材料试片提高了124%,45#钢试片提高了84%。
这是因为加入丙烯酸酯液体橡胶,改善了体系的韧性,降低了固化过程中产生的内应力,胶粘剂拉剪强度增大。
下面分别讨论液体橡胶添加量和环氧基含量对拉剪强度的影响。
表3 环氧树脂胶粘剂拉剪强度
拉剪强度每百份环氧树脂中液体橡胶的加入份数
/MPa 0 5 10 15 20
铝合金试片 12.1 20.1 28.2 26.1 22.3
玻璃钢试片 7.2 12.0 16.1 14.0(试片破坏) 14.1(试片破坏)
45#钢试片 9.2 11.2 16.8 16.6 13.2
由表3可见,随液体橡胶添加量的增加,胶粘剂的拉剪强度逐渐增大,当添加量为每百份环氧树脂加10份时,拉剪强度提高幅度最大,分别提高了约133%和124%。
这是因为加入液体橡胶,体系成两相结构,由于橡胶相变形和撕裂的阻力对基体开裂有阻碍和钉扎作用,消耗大量的能量,提高了韧性。
而这种阻碍作用与橡胶相的体积分数成线性关系,故随液体橡胶添加量的增加,基体的韧性增大,拉伸剪切强度逐渐增大。
又由于胶结件在受拉剪载荷时,胶粘剂与胶接件表面粘接作用和胶粘剂本身的强度不同,胶接件的破坏形式也不同。
但是若橡胶含量过大,胶粘剂内聚强度降低,试件呈内聚破坏,拉剪强度反而降低。
3.2.1 丙烯酸酯液体橡胶环氧基含量的影响
丙烯酸酯液体橡胶含有的反应性官能团为环氧基,不同环氧基含量的液体橡胶对胶粘剂拉剪强度的影响不同。
图4(图略)是体系中分别加入不同环氧基含量(每百份环氧树脂加入10份)的液体橡胶后,胶粘剂拉剪强度与液体橡胶环氧基含量的关系曲线。
由图4(图略)可见,在相同工艺条件下,随着液体橡胶环氧基含量的增加,拉剪强度增加,环氧基含量到一定程度后,拉剪强度又有减小的趋势。
环氧基含量为1.2 mmol·g-1的液体橡胶增韧效果最好,拉剪强度提高了133%。
由橡胶增韧环氧树脂的机理可知,要使丙烯酸酯液体橡胶有良好的增韧效果,橡胶和环氧树脂在反应前应有良好的相容性,在固化过程中,由于反应的进行分子量变大相容性变差产生分相,形成两相复合体系。
不同环氧基含量的丙烯酸酯液体橡胶与环氧树脂的相容性也不同。
环氧基含量过低,丙烯酸酯液体橡胶不易溶于环氧基体中;环氧基含量过高,橡胶与基体的的相容性太好,在反应的过程中不易分相,Tomio M.的研究也得出了这一结论。
由于相容性的不同,直接导致橡胶在反应分相过程中形成颗粒的粒径及分布的差异,而不同粒径的橡胶粒子,对环氧树脂增韧效果也有区别。
Riew的理论表明:小的颗粒主要对剪切变形起作用,大的颗粒能阻止裂纹的增长。
因此丙烯酸酯液体橡胶要有良好的增韧效果,环氧基含量要适当。
更重要的是,丙烯酸酯液体橡胶的环氧基团可通过固化剂反应接人环氧树脂固化网络中,可有效的在橡胶粒子与环氧基体之间形成化学连接,产生良好的增韧效果。
橡胶中环氧基含量低时,仅形成了两相体系,橡胶相和环氧基体无化学连接,橡胶粒子在受力变形时,易引起界面脱粘现象,不能有效的引起基体大量的剪切屈服和塑性变形而消耗大量的能量,因而韧性增加不明显。
加入环氧基含量为零的液体橡胶时,拉伸剪切强度只提高了30%左右;液体橡胶中环氧基含量太高时,橡胶粒子与环氧基体的界面连接太强,限制了橡胶粒子受力时的变形,拉伸剪切强度提高的幅度反而下降。
4 结论
(1) 以二乙烯三胺基甘油正丁基醚为固化剂,DMP—30为促进剂,丙烯酸缩水甘油酯—丙烯酸丁酯—丙烯酸乙酯三元共聚液体橡胶为增韧剂,制备了室温固化环氧树脂胶粘剂。
拉剪强度分别为28.0 MPa(铝合金试片)、16.1 MPa(复合材料试片)和16.8 MPa(45#钢试片)。
(2) 丙烯酸酯液体橡胶增韧环氧树脂的效果与橡胶中的环氧基含量和橡胶添加量有关。
添加量的大小影响基体开裂时的耗能大小;环氧基含量的大小影响液体橡胶与环氧树脂的相容性和两相间的化学界面连接,从而影响体系的韧性。
(3) 每100份环氧树脂加入10份环氧基含量为1.2 mmol·g-1的丙烯酸酯液体橡胶时,改性效果最好:铝合金、复合材料和45#钢试片拉剪强度分别提高了133%、124%和84%。