胺法冷芯盒制芯工艺研究
三乙胺法冷芯盒制芯工艺的应用及探讨

三乙胺法冷芯盒制芯工艺的应用及探讨潍坊柴油机有限责任公司邹化仲=摘要>为进一步推广应用三乙胺法冷芯盒制芯工艺,对在此工艺中存在的问题作了分析,并提出了改进措施。
1国内外三乙胺法冷芯盒工艺的发展应用三乙胺法冷芯盒工艺即酚醛氨基甲酸乙酯工艺,是冷芯盒制芯工艺方法中目前应用最广泛的一种,开发于1968年。
其制芯工艺过程是,在定量原砂中按工艺配比加入组分Ñ酚醛树脂和组分Ò聚异氰酸酯的双组分粘结剂,在混砂机中混均匀后得到冷芯砂,利用射芯机紧实到芯盒中,再藉助气体发生器,以干燥的压缩空气或氮气等为载体将定量的雾化或汽化的三乙胺催化剂通过吹气板吹入芯盒,将双组分粘结剂中的羟基和异氰酸催化变成尿烷而硬化,继而靠载体气体清洗出芯砂中残余的三乙胺,得到具有一定强度、满足工艺要求的砂芯。
冷芯盒法制芯工艺用的芯盒不需加热,免去了芯盒热变形,砂芯精度高,芯盒寿命长,芯盒材质可视生产批量大小等条件选用钢、铸铁、铝、塑料、木材等。
冷芯盒制芯工艺化学反应迅速,固化周期短,生产效率高,砂芯发气量较低,溃散性好,易清砂,铸件表面光洁,废品率低,综合成本低,易于组织自动化生产,经济效益显著。
因此,在近20年的发展中,日益取代油砂法、热芯盒法、壳芯法等传统制芯工艺。
在欧美等有些工厂采用三乙胺法冷芯盒制芯工艺生产的砂芯重量达砂芯总重量的70%以上。
为适应铸造工艺各方面的不同要求,特别是提高现行三乙胺法冷芯盒砂芯的热强度,防止在浇注金属高温作用下,砂芯过早溃散、变形、开裂造成废品,美国有关部门研究出高热强度三乙胺冷芯盒工艺,将现行三乙胺法冷芯盒工艺用的粘结剂组分Ñ酚醛树脂改为酚醛多元醇树脂,其他不变。
这样,溃散时间从不到100s延迟到400s。
另一方面,德国、美国、意大利、西班牙、日本等各国对三乙胺法冷芯盒工艺配套设备,射芯机、气体发生器、芯砂混砂机、空气干燥器、砂加热冷却器、废气净化装置等的研究逐步深入,不断采用新技术、新专利形成各具特色的系列化生产。
行业标准铸造用三乙胺冷芯盒法树脂解读

行业标准《铸造用三乙胺冷芯盒法树脂》解读1 标准概况三乙胺冷芯盒法树脂工艺由于其具有生产效率高、节约能源、芯(型)强度高、尺寸精确、芯(型)砂溃散性好等优点,已经得到了铸造业的广泛使用。
根据2011年中国机械工业联合会下发的2011年行业标准制修订计划,《铸造用三乙胺冷芯盒法树脂》行业标准由苏州兴业材料科股份有限公司负责起草,全国铸造标准化技术委员会归口管理。
在2011年第三批行业标准制修订计划中,标准名称为《铸造用三乙胺法冷芯盒树脂》,在标准征求意见时,经标准起草小组一致同意,将标准名称确定为《铸造用三乙胺冷芯盒法树脂》。
2 标准的主要内容2.1 范围本标准适用于铸造用三乙胺冷芯盒法制芯(型)用树脂。
2.2 术语和定义参照GB/T 5611《铸造术语》“铸造用三乙胺冷芯盒法树脂 TEA cured cold-box resin for foundry”,将铸造用三乙胺冷芯盒法树脂定义为“在室温下吹入三乙胺等叔胺类催化剂气体,使双组分粘结剂的酚醛树脂和聚异氰酸酯交联成固态的氨基甲酸酯,从而使砂芯(型)硬化的冷芯盒用树脂。
”2.3 分类和牌号铸造用三乙胺冷芯盒法树脂是目前广泛使用的制芯、造型用有机粘结剂,在用户现场使用时主要根据强度判断产品优良,因此标准以强度等级分级为普通型、抗湿型和高强度型。
铸造用三乙胺冷芯盒法树脂按使用条件不同分类及分类代号见表1。
铸造用三乙胺冷芯盒法树脂的牌号表示方法如下:示例SLⅠ-G:表示铸造用三乙胺冷芯盒法树脂组分Ⅰ高强度型树脂。
2.4 技术要求2.4.1 铸造用三乙胺冷芯盒法树脂的理化性能应符合表2的规定。
因为组分Ⅰ刚生产出来时为淡黄色,遇光易变棕红色,但不影响性能,所以本标准规定组分Ⅰ为淡黄色至棕红色透明液体。
为促进技术进步,出于对职业健康和环境保护的需要,同时考虑到国内有代表性厂家的现状,对组分Ⅰ中的游离甲醛进行了分级规定,≤0.5%为合格品,≤0.3%为优级品。
冷芯盒制芯技术及应用现状

冷芯盒制芯技术及应用现状前言自1968年美国的阿什兰公司发明并推广冷芯盒技术以来,冷芯盒制芯因其生产效率高、节能,砂芯尺寸精度高、发气量低,芯盒寿命长、变形量小,铸件表面光洁、尺寸精度高(可达到CT7级),浇注后砂芯溃散性好等特点而被广泛采用。
尽管冷芯盒法除了ISOCURE法(阿什兰法)外,后来还开发了SO2法(呋喃树脂/SO2法、环氧树脂/SO2法、酚醛树脂/SO2法、自由基硬化法)、低毒或无毒的气硬促硬法(钠水玻璃/CO2法、酚醛树脂/脂法、有机粘结剂/CO2法)、FRC法,但目前应用最多的仍是ISOCURE法。
ISOCURE法是在原砂中加入一定量的组分I(液态的酚醛树脂)和II组分(聚异氰酸脂),在混砂机中混匀后,用射芯机射砂或人工填砂制芯,用干燥的空气、CO2气体或氮气作载体,通入约5%浓度的催化剂气体,使组分I中的酚醛树脂的羟基和组分II中的异氰酸基在催化剂的作用下,发生聚合反应生成尿烷树脂而固化。
冷芯盒的适应性强,它可以应用于铸造所有种类的黑色和有色合金以及适用于大多数铸造用砂,冷芯盒砂芯可小到136g,大到840Kg,最大达到1000磅;砂芯壁厚从3mm到170mm。
在国内外,冷芯盒技术已成功的应用于汽车、拖拉机、飞机、机床、泵业等行业,但在实际生产中,冷芯盒制芯工艺受到许多因素的影响,包括原材料、工装、工艺参数等。
本文对冷芯盒技术的应用中应注意的问题作了一定的综述,并对国内应用冷芯盒技术的情况作了说明。
一、冷芯盒生产中应注意的问题:冷芯盒技术的本质是组分I(液态的酚醛树脂)和II组分(聚异氰酸脂)在催化剂的作用下,生成尿烷的过程,即:催化剂酚醛树脂+聚异氰酸脂尿烷组分I的酚醛树脂结构要求为苯醚型,组分II为4,4’二苯基甲烷二异氰酸酯(MDA)或多次甲基多苯基多异氰酸脂(PAPI)等,美国推荐使用MDA,我国主要用PAPI。
组分I和组分II通常用高沸点的酯或酮稀释,以增加树脂的流动性和可泵性,使树脂容易包覆在砂粒表面,也增加芯砂的流动性,使砂芯致密。
胺法冷芯盒树脂砂射芯技术装备及应用

( 2 ) 水 玻璃 石 灰 石砂 表 面 涂刷 醇 基 锆英 粉 涂 料 是 导致铸 件产 生气 孑 L 的原 因之一 。 ( 3 ) 发热 保温 冒 口的应 用有 利于铸 件 质量 控制 。
I m pr o v e me nt o n Ca s t i ng Te c h n o l o g y o f Ce r t a i n Co u pl e r Yo k e s
YU S h u J i , F U Do n g Ya , HUANG o
( C S R Q I S HU Y AN C o . L t d . , C h a n g z h o u 2 1 3 0 1 1 , J i a n g s u C h i n a )
1 工 艺流程 和 工艺硬 化原 理 1 . 1 工艺 流程
的冷 芯盒 射 芯机 , 将 北 奔重 汽 球铁 件 基数 和批 量 大 的产 品呋 喃 自硬 树 脂 砂 制 芯 工 艺 改进 为胺 法 冷 芯
收稿 日期 : 2 0 1 3 — 3 — 1 4
胺 法冷芯 盒树 脂砂 射 芯是将 聚苄 醚 酚醛 树脂 组 分、 聚 异氰 酸酯组 分 与原砂 混合后 射 入冷 芯 盒 , 然 后 以压缩 空气 为载 体 ,将 液 态三 乙胺 升温雾 化 后 吹入
生产 技术 P r o d u c t i o n T e c h n i q u e s
胺法冷芯盒树脂 砂射 芯技术装 备及应 用
郭 利云 、 ,程 坚 ,武 玉平 、 ,于 大威 ,王利 华 、 ,高 磊 ( 1 . 内蒙古第 一 机械 集 团有 限公司 , 内蒙 古包 头 0 1 4 0 3 2 ;
件质 量 , 减 少铸 造缺 陷 的产生 。
优质铸件生产中冷芯盒制芯的质量控制

优质铸件生产中冷芯盒制芯的质量控制摘要】冷芯盒工艺是一种节能、低污染、高效的造型及制芯工艺。
随着我国铸造业的快速发展,冷芯盒树脂砂工艺已经日益成熟,有逐步取代热芯盒成为铸造行业首选的趋势。
本文旨在分析探讨生产中使用酚醛尿烷树脂砂冷芯盒工艺制芯对铸钢件质量造成影响的因素,强调铸钢件制芯过程中的过程控制要点。
【关键词】冷芯;酚醛尿烷树脂砂;铸钢件质量;制芯一、冷芯工艺特点气硬冷芯盒工艺是指将树脂砂填充于芯盒,然后在室温下吹入气体或气雾催化或硬化而瞬时成型的树脂砂制芯工艺。
1.硬化速度快。
硬化反应几乎是在表面和内部同时进行,不受型腔形状或壁厚的限制,可有效提高生产效率,制得的砂芯可在1h内合型浇注。
2.芯砂可使用时间长。
可使用时间内树脂粘度变化几乎不可察觉,型砂的流动性良好。
一旦催化后,芯砂很快硬化。
可使用时间可在30s~200min范围内变化,能大范围适应生产需要。
3.砂芯抗热裂纹、脉纹等缺陷能力高。
4.含氮量低,发气量少,可降低气孔缺陷发生率。
5.气硬冷芯工艺设备密封性要求较高,必须配备尾气处理装置。
6.质量风险点。
制芯过程主要可能造成的铸件缺陷有气孔、夹砂、脉纹等,芯砂混砂是气硬冷芯工艺的最关键工序,混砂质量直接影响砂芯的强度质量,是质量管控的重点。
二、过程控制1.制芯原材料气硬冷芯工艺树脂砂制芯的原材料包括原砂、树脂粘结剂、冷铁、芯骨、涂料等。
1.1芯砂原砂1.1.1原砂的角形因数、颗粒度、含泥量。
在满足砂芯吊运的基础上,原砂的颗粒度、含泥量等的不同,树脂的加入量也要发生变化,相应影响铸件气孔和应力产生的倾向。
原砂颗粒度越小,含泥量越高,硅砂颗粒表面积越大,耗费的粘结剂量越多,铸件气孔和应力倾向越大。
生产过程常控制粘结剂量,对硅砂颗粒度应有所要求,建议优先选用满足下表1要求的擦洗硅砂,工艺控制过程可基本稳定控制树脂等粘结剂加入量,来保证砂芯使用强度。
1.1.2原砂含水量。
为保证砂芯成型强度满足要求,原砂必须干燥,原砂含水量超过0.1%就会减少芯砂的可使用时间,降低砂芯强度,也会增加铸件针孔产生的倾向,含水量最佳范围是<0.1%,允许范围≤0.2%。
冷芯盒工艺优典型失效案例分析

冷芯盒工艺典型失效案例分析--苏州兴业材料科技股份有限公司:吉祖明王骏康胺法冷芯盒工艺自1968年在美国铸造学会举办的展览会上展示以来,以其极高的生产率,较低的单位能耗,倍受关注。
在汽车、拖拉机、内燃机等大批大量生产行业得到了极其广泛的发展和应用。
据权威部门统计,从本世纪初叶开始,国内冷芯盒树脂消费量呈快速上升态势,到2011年己占铸造合成树脂总量的10%,已成为仅次于呋喃树脂砂的主流树脂砂制芯造型工艺。
但冷芯盒工艺在实际应用中,如工艺控制不当,常会出现不少质量问题。
下面我们列出一些常见失效典型案例,与大家共同讨论。
1制芯过程沾模1.1. 失效原因我们将沾模失效归纳总结为如下四种:能量型沾模:大家都知道,所谓能量沾模就是原包覆在原砂表面的树脂膜在射砂过程中,有一部份液态树脂膜由于动能势能的作用而转移至芯盒表面,在吹胺吹气以后,固化以后的树脂膜会留在芯盒表面,这种沾模主要和射砂压力有关,射砂压力愈大,沾模会愈严重。
在通常情况下射砂大于0.3MPa,几率会极剧放大。
排气塞堵塞型沾模:排气塞的位置和大小是获得合格砂芯充分而必要的条件,在日常制芯过程中排气面积会因沾附树脂和砂粒而逐渐缩小,伴随而至的将是砂芯射不紧,吹不实。
有些操作人试图用提高射砂压力,提高吹胺量和吹胺压力的方法来纠正这种缺陷,其结果,不但射不紧,吹不实沒得到解决,而且又出现了严重的沾模问题。
我们称这种失效为排气塞堵塞沾模。
水份型沾模:混合料与芯盒之间温差大,空气中的水份会在芯盒表面结露。
另外如脱模剂中水较多,喷雾过量,汽化以后残余水份也会停留芯盒表面,这些微量水份既大大增加了脱膜阻力,又严重削弱了砂芯表面强度,致使芯盒表面沾附树脂夹砂层。
混砂型沾模:在冬天树脂粘度相对变大,混砂工艺又沒做动态调控。
或混砂机刮刀、护板磨损间隙过大而未及时更换,都会导致混和料中树脂未均匀包覆在砂粒表面,存在树脂部分集中现象,混合料射入芯盒后,就会导致沾模,如沾模呈点多、面小、膜厚大多属混砂不匀型沾模。
三乙胺法冷芯盒工艺技术
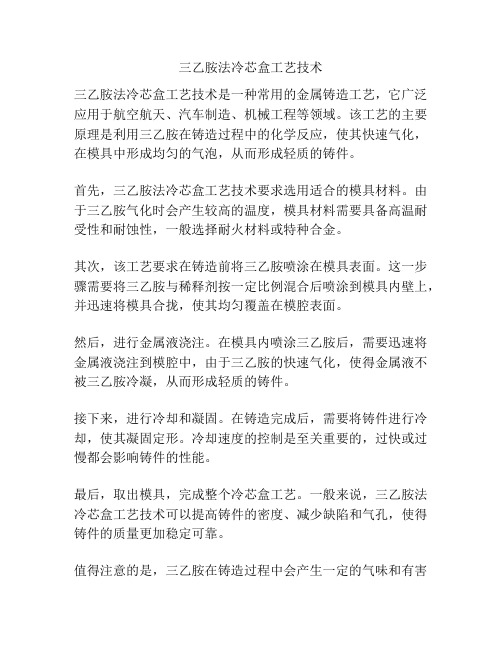
三乙胺法冷芯盒工艺技术三乙胺法冷芯盒工艺技术是一种常用的金属铸造工艺,它广泛应用于航空航天、汽车制造、机械工程等领域。
该工艺的主要原理是利用三乙胺在铸造过程中的化学反应,使其快速气化,在模具中形成均匀的气泡,从而形成轻质的铸件。
首先,三乙胺法冷芯盒工艺技术要求选用适合的模具材料。
由于三乙胺气化时会产生较高的温度,模具材料需要具备高温耐受性和耐蚀性,一般选择耐火材料或特种合金。
其次,该工艺要求在铸造前将三乙胺喷涂在模具表面。
这一步骤需要将三乙胺与稀释剂按一定比例混合后喷涂到模具内壁上,并迅速将模具合拢,使其均匀覆盖在模腔表面。
然后,进行金属液浇注。
在模具内喷涂三乙胺后,需要迅速将金属液浇注到模腔中,由于三乙胺的快速气化,使得金属液不被三乙胺冷凝,从而形成轻质的铸件。
接下来,进行冷却和凝固。
在铸造完成后,需要将铸件进行冷却,使其凝固定形。
冷却速度的控制是至关重要的,过快或过慢都会影响铸件的性能。
最后,取出模具,完成整个冷芯盒工艺。
一般来说,三乙胺法冷芯盒工艺技术可以提高铸件的密度、减少缺陷和气孔,使得铸件的质量更加稳定可靠。
值得注意的是,三乙胺在铸造过程中会产生一定的气味和有害气体,因此在操作过程中需要保持良好的通风条件并使用适当的个人防护设备,确保工人的安全。
总的来说,三乙胺法冷芯盒工艺技术是一种重要的铸造工艺,具有较高的效率和质量优势。
通过合理的应用和控制,可以实现高质量的铸件生产,并满足不同领域的需求。
三乙胺法冷芯盒工艺技术是一种常用的金属铸造工艺,它在各个领域中广泛应用。
下面将详细介绍该工艺技术的相关内容。
首先,三乙胺法冷芯盒工艺技术的基本原理是利用三乙胺在铸造过程中的化学反应。
三乙胺,也被称为N,N-二乙基甲酸酰胺,是一种液体化合物。
当在铸造过程中,将三乙胺喷涂在模具表面后,它会快速气化,形成大量气泡,进而形成轻质的芯盒。
该工艺的第一步是选择适合的模具材料。
由于三乙胺在气化时会产生高温,因此模具材料需要具备耐高温和耐蚀性。
三乙胺法冷芯盒制芯工艺影响因素的研究

三乙胺法冷芯盒制芯工艺影响因素的研究引言三乙胺法冷芯盒制芯作为一种常用的铸造工艺,广泛应用于金属铸造行业。
在该工艺中,冷芯盒起到加固砂芯的作用,从而保证砂芯能够在铸造过程中保持形状稳定。
然而,冷芯盒制芯工艺中存在许多影响因素,这些因素会直接影响到制芯质量和生产效率。
因此,对冷芯盒制芯工艺影响因素的研究具有重要的理论和实际意义。
影响因素1. 砂芯配合比砂芯配合比是指砂芯制备过程中砂与粘结剂的比例关系。
砂芯配合比的变化会直接影响到砂芯的强度和形状稳定性。
过高或过低的配合比会导致砂芯变形或者失去强度,影响到铸件的质量。
因此,在冷芯盒制芯过程中,合理选择砂芯配合比十分重要。
2. 砂芯固化条件砂芯固化条件是指砂芯在制备过程中固化所需的温度和时间。
砂芯固化条件的设置不仅会影响到砂芯的强度和稳定性,还会对铸件的缩孔和热裂纹等缺陷产生影响。
因此,对砂芯固化条件的优化研究可以有效提高制芯质量和减少铸件缺陷。
3. 冷芯盒结构设计冷芯盒的结构设计直接影响到砂芯的形状和支撑力。
合理的冷芯盒结构设计可以保证砂芯在铸造过程中不发生变形或裂纹。
对于复杂形状的砂芯,冷芯盒结构设计的合理性尤为重要。
因此,冷芯盒结构设计应根据具体的砂芯形状和尺寸进行优化。
4. 三乙胺溶剂配置三乙胺是冷芯盒制芯工艺中常用的一种粘结剂,它可以使砂芯具备一定的强度和稳定性。
三乙胺溶剂配置的不同会直接影响到砂芯的粘结效果。
过高或过低的三乙胺溶剂配比会导致砂芯粘结不牢或者溶剂残留在砂芯中,影响到铸件质量。
因此,三乙胺溶剂配比的合理选择对于冷芯盒制芯工艺影响很大。
结论三乙胺法冷芯盒制芯工艺是常用的铸造工艺之一,影响因素的研究对于提高制芯质量和生产效率具有重要意义。
砂芯配合比、砂芯固化条件、冷芯盒结构设计以及三乙胺溶剂配置是冷芯盒制芯工艺的主要影响因素。
合理选择和优化这些影响因素可以有效提高制芯质量、减少缺陷产生,从而提高铸件的质量和生产效益。
因此,在实际生产中,应对这些影响因素进行细致的研究和优化,以提高冷芯盒制芯工艺的可靠性和稳定性。
- 1、下载文档前请自行甄别文档内容的完整性,平台不提供额外的编辑、内容补充、找答案等附加服务。
- 2、"仅部分预览"的文档,不可在线预览部分如存在完整性等问题,可反馈申请退款(可完整预览的文档不适用该条件!)。
- 3、如文档侵犯您的权益,请联系客服反馈,我们会尽快为您处理(人工客服工作时间:9:00-18:30)。
胺法冷芯盒制芯工艺研究三乙胺冷芯盒工艺自1968年在美国铸造学会举办的展览会上展出以来,因其很高的生产率颇具竞争性和实用性,而且在此基础上出现了制芯中心,型芯的尺寸精度进一步提高,受到了铸造业内人士的普遍关注,尤其是在汽车、拖拉机、内燃机等大批大量生产行业得到了极其广泛的发展和应用。
据报道,美国铸造行业所用的各类铸造粘结剂中,冷芯盒树脂的年用量最大,约占粘结剂总量的44%。
我国七十年代初,一拖工艺材料研究所和安阳塑料厂率先开始了胺法冷芯盒制芯树脂及工艺的研究,但当时国内无专用设备及配套材料供应,使该工艺无法推广。
1985年,常州有机化工厂从美国Ashland公司引进了胺法冷芯树脂生产技术,一汽铸造一厂从美国B﹠P公司引进了全套冷芯盒制芯设备,接着一拖、上柴又分别从德国、美国引进了两套冷芯盒制芯专用装备,使胺法冷芯技术在国内获得生产性应用。
到目前为止,国内已形成了冷芯盒全套设备、工艺装备、树脂及配套辅料等近百家设计、制造单位的年产值数十亿元的产业链。
1.冷芯盒树脂砂的工作原理和化学特性1.1冷芯盒树脂砂工作原理冷芯盒树脂有二个组份,即:Ⅰ组份是宽分布线性酚醛树脂。
它是用苯酚、甲醛经过化学反应获得的含有羟甲基(-CH2OH)与醚键(R-O-R)的线性聚合体。
适量的羟甲基数,可保证型芯获得必要的初强度,适当的醚键可保证充分的终强度。
Ⅱ组份是用高沸点的相溶性优良的溶剂而改性的含有适量(—N=C=O)基团的聚异氰酸酯。
冷芯盒工艺的固化原理是酚醛树脂中的羟甲基(-CH2OH)和聚异氰酸酯中的(—N=C=O)基团在三乙胺的催化作用下,数秒内反应生成固态的尿烷树脂。
实际使用时,需要混砂和制芯两个过程:首先是树脂的两种组分通过混砂过程均匀地包覆在砂粒表面;然后将混好的混合料射入芯盒,再吹入三乙胺气体,使均匀包覆在砂粒表面的树脂膜从液态变成固态,在砂粒与砂粒之间建立粘结桥,形成强度。
1.2冷芯盒树脂砂的化学特性1.2.1 Ⅱ组份聚异氰酸酯中—N=C=O基团在碱性或微碱性环境中容易水解,放出CO2生成胺化合物,其反应活性受浓度、温度、催化剂的影响。
水份浓度和反应温度增加可使水解反应速率增大。
三乙胺在催化羟甲基与—N=C=O基团反应的同时,也使—N=C=O基团的水解反应加速,在无三乙胺的条件下水解相对速率为1.1,在吹三乙胺以后,水解相对速率则提高到47。
因此,整个工艺过程中对水份须进行严格控制。
1.2.2 Ⅰ组份和Ⅱ组份树脂一旦混合后,即会发生缓慢的聚合化学反应。
但在胺、铁、钙、镁等碱性化合物的催化作用下,反应速率极快。
催化效果取决于催化剂的种类、浓度、温度、压力、时间等参数。
1.2.3 Ⅰ组份和Ⅱ组份树脂的聚合反应过程存在前、后两期固化,在催化剂作用下快速固化形成的初强度仅占整个终强度的50~75%,还有25~50%的强度需在后期形成,为保证已成型型芯不被破坏和终强度顺利形成,须对上涂料的时间、烘干温度、仓储时间、温度、湿度进行控制。
1.2.4 冷芯盒树脂砂的室温、高温强度随树脂加入量增加而增加,但并非始终是呈线性增加,一般树脂加入量都<2%。
1.2.5 冷芯盒树脂组份Ⅰ增加,初强度上升,韧性下降。
组份Ⅱ增加,终强度上升,发气量增加。
组份Ⅰ∶组份Ⅱ在(60~40)%∶(40~60)%之间变动。
2.冷芯盒树脂砂工艺控制冷芯盒工艺过程控制的总体要求是:以控制水份危害为主线;选择符合冷芯要求的工艺设备、原材料;正确把握温度、压力、时间主参数;注意工装的气路和配合尺寸。
“水份”主要是指硅砂、压缩空气、三乙胺、涂料、大气及型砂中的水份。
“温度”主要是指硅砂、树脂、压缩空气(射砂和吹胺)、三乙胺、涂料烘干时的温度。
“压力” 主要是指射砂、吹胺、清洗时的压力。
“时间” 主要是指树脂仓储、混砂、可使用、射砂、吹胺、清洗、上涂料、烘干、型芯仓储及型芯落入铸型后所经历的时间。
2.1水份控制:由于Ⅱ组份聚异氰酸酯中—N=C=O基团在碱性或微碱性环境中容易水解,如果在制芯过程中,某一工序受到水的浸害都将导致某种缺陷,有时,这种缺陷将会非常严重。
这是因为水份将消耗大量的Ⅱ组分聚异氰酸酯中—N=C=O基团,从理论上计算,1摩耳的水将消耗2摩尔的—N=C=O基团。
而Ⅱ组分聚异氰酸酯中含有—N=C=O基团一般在20%左右,也就是说,每克水与—N=C=O基团完全反应将消耗10克左右的聚异氰酸酯,这不仅严重削弱了型芯强度,其反应生成的胺化合物降低了型芯的高温塑性和发气量,而且使生产成本大幅度提高。
因此,冷芯盒工艺的优化控制应以控制水份的破坏作用为主线,从原辅材料(硅砂、树脂、三乙胺)的准备、混合料的配制、制芯、加工涂料、仓储、下芯、浇注等整个工艺过程都须对水份进行监控。
2.1.1 硅砂水份控制硅砂水份对冷芯盒型芯的强度有着重要影响。
如果水份高,不仅降低芯砂强度和缩短芯砂可使用时间,降低型芯本身的质量,而且会使铸件产生气孔、起皮等由水份而导致的缺陷,因此须有效地将硅砂含水量控制在0.15%以内为宜。
经试验,含水量为0.15%左右的硅砂所制型芯初强度比含水量为0.05%左右的硅砂所制型芯初强度略低0.2Mpa,水份的影响与温度还有密切关系,当在高温、高湿环境中,水份对强度的破坏程度将成倍增加,当水份达到0.30%时, 强度下降30% , 当水份达到0.50%时, 强度下降近60% , 且存放性大大降低。
2.1.2 压缩空气中的水份控制控制射砂和清洗过程所用压缩空气中的水份是冷芯盒工艺以控制水份为主线的又一个关键问题。
众所周知,冷芯盒所用三乙胺催化剂在常温下是液体,吹胺时,以压缩空气为载体,加热汽化。
如果压缩空气中水份含量高,其后果比硅砂中水份高还要严重得多,如前所述,三乙胺在催化两个组份树脂高速反应的同时,也是水与—N=C=O基团的反应速率提高了47倍。
据介绍,即使射砂和清洗过程所用压缩空气只含有中等含量的水份,就会使破坏型芯树脂粘结力所需的应力降为正常状态下打破树脂粘结桥所需应力的50~80%,型芯在存储、搬运过程中的破损率和浇注过程中的报废率将明显上升。
另外,含有水份的射砂用压缩空气作用于混制好的芯砂时,大量的水份会聚集在射砂网上,将会减少射砂循环后压缩空气从此处排除的流量,就增加了维护工作量。
为避免类似问题产生,需要对射砂和清洗用压缩空气进行去湿处理,使常压下压缩空气的露点应按型芯的种类、复杂程度来选择,薄壁高强度复杂型芯露点应尽量低,一般应≤-40℃,简单厚大型芯露点可以高一些,一般应≤-15℃。
2.1.3 涂料水份控制刚起模的冷芯盒型芯初强度一般为终强度的60~70%,此时树脂膜中憎水的溶剂开始从砂粒间隙中向外挥发,在挥发的过程中,可以有效地阻止水份向型芯内部渗透,但是,这种挥发过程所经历的时间一般小于2小时。
所以如需要上水基涂料的冷芯盒型芯应尽快涂覆,涂覆越快,憎水溶剂的阻碍效应越明显。
如在憎水溶剂基本挥发完毕以后上水基涂料,涂料中的水份会通过型芯的毛细管间隙渗透到内部,损伤树脂粘接桥,与未反应的二组分聚异氰酸酯发生水解而失效。
使用水基涂料,型芯就需要烘干,尽可能使型芯残余水份降至最低。
型芯烘干温度也是影响型芯最终质量和铸件质量的一个重要因素,一般原则是在保证型芯烘干的前提下,温度越低越好。
尤其是烘干初期,因为水份浓度高,蒸发快,水蒸气饱和后,会形成饱和蒸气膜,不易于型芯内层水份烘干。
所以初期温度不宜过高,适当减缓水份蒸发,避免形成饱和蒸气膜。
如使用醇基涂料,则与水基涂料相反,不宜型芯出盒后立即涂覆,这是因为冷芯盒溶剂憎水但可溶于醇类有机物,醇基涂料常用溶剂为异丙醇或工业用乙醇,它们对型芯的渗透能力非常强,每秒钟渗透深度可达10毫米,渗入型芯的醇类有机物将树脂已经交联的缩聚物阻塞在体形结构中,使大量活性基不能参与反应破坏后期固化,所以上醇基涂料应在树脂溶剂基本挥发完毕后进行,涂好后需立刻点燃。
2.1.4 下芯以后的水份控制冷芯盒型芯落入湿型后,往往会由于铸型、型芯之间的温差发生水份迁移,在型芯表面发生水份结露,损伤树脂粘接桥。
使型芯表面水份增大,强度下降,而水份的发气量大约是冷芯树脂的100倍。
所以如果将冷芯盒型芯落入湿型铸型后,数小时不浇注,将特别容易使铸件产生冲砂、砂孔、气孔、粘砂等缺陷,存放时间越长,产生上述缺陷的机率就越大。
2.2 温度、压力和时间的优化控制:冷芯盒工艺的过程实际是一种化学、物理过程,其中化学过程起着决定性的作用。
研究和分析其过程的影响参数,进行优化组合,达到预定的工艺目标。
冷芯盒工艺吹气固化是整个工艺过程中最主要的工艺过程,也即是在一定的温度、压力条件下,使催化剂“雾化”,历经一定的时间,充满并均布整个型腔,使型腔中的砂粒和树脂之间形成粘结力,即型芯固化成型。
这一过程可以再细分成“射砂”和“吹气”二个过程,合理设置这两个过程工艺参数将有助于使制芯生产平稳,废品率维持在最低水平,并使生产环境改善。
2.2.1硅砂温度控制砂温和大气温度对生产率和型芯成品率会产生很大的影响。
温度低,树脂粘度反而高,不易使树脂包覆在砂粒表面,导致混砂效率降低、混砂时间延长。
砂温影响遵循“10℃”原则,即砂温每增加10℃,将使树脂的反应速度加快1倍,同样砂温每降低10℃,将使树脂反应速度减慢1倍。
尤其是在高湿环境中,当砂温低于环境温度时,水份更易于聚集在砂粒表面,破坏树脂与砂粒建立粘结力。
但砂温过高,一方面加剧其中溶剂挥发恶化环境,一方面缩短混合料可使用时间。
所以必须采用砂温调节装置使砂温控制在20~30℃之间为宜。
2.2.2 射砂压力和时间的控制射砂,即将混制好的芯砂充填射砂筒、密封射砂筒(射砂头和芯盒间的通道除外)、使射砂筒充满压力后将芯砂射入芯盒中。
设计良好的射砂机构应该在较低的压力下使芯砂平稳充填型腔而不“沸腾”翻转。
较低的射砂压力不仅可以减少压缩空气用量,减少芯盒磨损,延长芯盒使用寿命;而且可以适当减少芯盒所需排气塞数量,降低芯盒制造费用和维护费用。
芯砂平稳充填型腔不仅可以使型芯密度及尺寸保持一致,而且可以适当延长芯砂的可使用时间。
当然,射砂压力的选取还与砂子的密度有关,对硅砂而言,通常的射砂压力取0.2~0.3Mpa即可。
增加射砂压力相当于增加了砂子从射砂筒射入芯盒中的速度,增加砂子的速度会使树脂“脱离”砂子而沉积在芯盒壁和排气塞处,这将加速粘模和影响排气,直接影响型芯质量。
所以,通常的经验是用较低的压力获取致密的型芯,这样就减少粘模、减少清理、延长模具寿命。
在实践中,采用低压射砂时,对于一些较难充型的复杂模型,或者是因为工作面要求,无法开设较多排气塞的模型,往往易出现射不满的情形,此时往往采用“二次射砂”进行补偿,结果却造成型芯表面射口附近凹凸不平。
经实践,在此情况下将射砂时间及排气时间从常规的3~5秒再延长3~5秒,即可获得表面良好的型芯。