冷芯盒制芯技术及应用现状
冷芯盒工艺在单缸柴油机机体铸造上的应用

1 冷 芯 盒 法 制 芯
1 1 制芯设 备的选择 . 砂 芯 的 获 得 有 两 种 方 式 : 是 从 市 场 上 定 点 一
采 购 ; 一 种 就 是 自己 生 产 。 由于 单 缸 柴 油机 属 另
1 2 2 原砂 含 泥量 ..
在保证砂 芯强度 的情况 下 ,含泥量越 高 ,树
随 着 冷 芯 盒 制 芯 工 艺 的 日趋 成 熟 以及 制 造 成 本 的 不 断 下 降 , 使 其 从 过 去 以 高 档 铸 件 为 主 逐 步 扩 大 到 中 低 档 铸 件 的 生 产 。近 年 来 通 过 摸 索 ,将
只 要 控 制得 好 ,所 制砂 芯 品质 能 满足 使 用 要 求 。
强 度 的 影 响 要 严 重 得 多 。据 介 绍 , 即使 射 砂 和 清 洗 过 程 所 用 压 缩 空 气 只 含 有 中等 水 分 , 也 会 使 破
层 的厚 度 和 干 燥 时 间 。 3 2 内 跑 火 . 铸 件 在 浇 注 过 程 中 ,铁 水 从 砂 芯 分 型 面 处 钻
冷 芯盒工 艺在 单缸 柴油机机 体铸 造上 的应 用
董绍俊 ( 江苏江淮 动力股份有限公司 ,江苏 盐城 2 4 0 ) 20 1
摘要:在单缸柴油机机体 生产 中采用冷芯盒制芯工艺,分析 了冷芯盒工艺的关键 ,以及生产 中 常见的铸件缺 陷及 防止方法 ,并将其与合 脂砂 工艺的成本进行 了对比。
关键 词 :冷 芯 盒 法 ;制 芯 工 艺 ; 柴油机 机 体
中图分 类号 :T 2 2 7 文献标识码 :B G 4 .
文章编号 :1 7 - 3 0( 0 1 10 2 - 2 6 3 3 2 2 1 )0 - 0 8 0
水玻璃冷芯盒制芯技术的研究
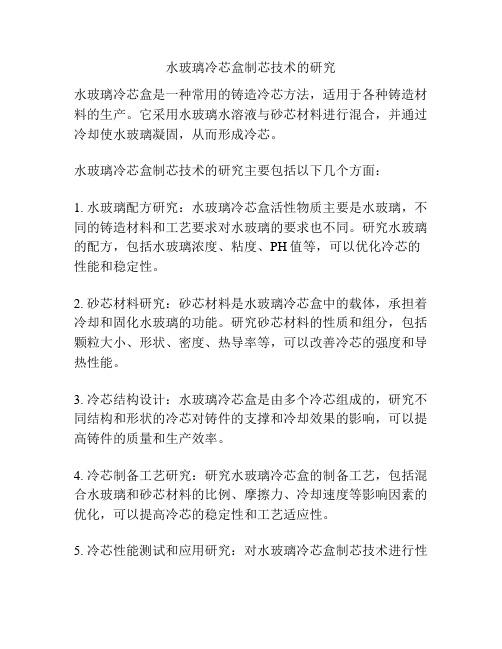
水玻璃冷芯盒制芯技术的研究
水玻璃冷芯盒是一种常用的铸造冷芯方法,适用于各种铸造材料的生产。
它采用水玻璃水溶液与砂芯材料进行混合,并通过冷却使水玻璃凝固,从而形成冷芯。
水玻璃冷芯盒制芯技术的研究主要包括以下几个方面:
1. 水玻璃配方研究:水玻璃冷芯盒活性物质主要是水玻璃,不同的铸造材料和工艺要求对水玻璃的要求也不同。
研究水玻璃的配方,包括水玻璃浓度、粘度、PH值等,可以优化冷芯的性能和稳定性。
2. 砂芯材料研究:砂芯材料是水玻璃冷芯盒中的载体,承担着冷却和固化水玻璃的功能。
研究砂芯材料的性质和组分,包括颗粒大小、形状、密度、热导率等,可以改善冷芯的强度和导热性能。
3. 冷芯结构设计:水玻璃冷芯盒是由多个冷芯组成的,研究不同结构和形状的冷芯对铸件的支撑和冷却效果的影响,可以提高铸件的质量和生产效率。
4. 冷芯制备工艺研究:研究水玻璃冷芯盒的制备工艺,包括混合水玻璃和砂芯材料的比例、摩擦力、冷却速度等影响因素的优化,可以提高冷芯的稳定性和工艺适应性。
5. 冷芯性能测试和应用研究:对水玻璃冷芯盒制芯技术进行性
能测试和应用研究,包括冷芯的强度、导热性能、生产效率和经济性等方面的考察和评价,可以为铸件生产提供参考和指导。
三乙胺冷芯盒制芯工艺的应用与探索

三 乙胺 法 对 石英 砂 、 锆砂 或 铬 砂 均适 应 , 必 须 但 注意 原砂 化学 成分 、 含水 量 、 砂温 和灰分 含量 。 中含 砂
水 量 多 , 会 降低砂 芯 的强度 和 减少 可用 时间 。 如 图 则 (
- 十 ” 十 ” + ” + ” + ” + “ + ” + “ +- - - - - - - - - - “ + “十 ” 十 ” +- + - ” ” + “ + “ +- - - - ” + ” - - - “ + ” +- - - + - + ・+・ ・ - -
三 乙胺 冷芯 盒制 芯 一般 采用 水 洗砂 与 擦洗 砂 , 也 可 以用锆砂 和铬矿砂 。 其含 泥量 ≤03 ,Hi7 角 度 . p < , % 系数 ≤1 , 度 为 5 / 0 。一般 可 以用 三筛 砂 , .粒 3 0 10 最好 采用 四筛 砂 。耐火 材料 技术要 求 见表 l表 2 、 。
表 1 铸 造 用 硅 砂 技术 要 求
名 称 产 地 O 灼 烧 减 量 粒 度 粒 度 集 中 S 2 i 含泥 ( ) ( )( ) ( 号) ( % 量 % % 筛 %) 性 擦 洗 砂 场 9 ≤O3 ≤ O3 5 / 0 ≥8 无 异 物 杂 质 芯 围 ≥ O - - 0 10 O 制 检 指 标 粒度 检 指 标 SO i: 粒 度 集 中性 灼 烧 减量 含泥 量 外 观 用 途
维普资讯
材 料 工 艺 M TR L E H O O Y A E I &T C N L G A
Байду номын сангаас
三乙胺冷芯盒制芯工艺的应用与探索
Te h o o yAp lc t n a d Ex l r t n o it y c n l g p ia i n p o a i fTre h l o o
射芯机冷芯盒制芯工艺

射芯机冷芯盒制芯工艺射芯机冷芯盒制芯工艺是一种常用的制芯方法。
这种方法通过使用冷芯盒来制作芯子,使芯子中心部位得到更好的冷却,实现了内部光洁度的提高和投产效率的提高,从而在制芯过程中克服了一些缺点。
本文将介绍射芯机冷芯盒制芯工艺的原理、设备要求、工艺流程和注意事项等方面的内容。
一、工艺原理射芯机冷芯盒制芯工艺是通过在制芯时使用冷芯盒,将冷却介质通过冷芯盒注入芯子中心部位,使其得到更好的冷却,从而提高芯子内部光洁度和投产效率。
制芯过程中,首先通过3D打印技术制作冷芯盒,然后将芯盒与冷芯盒固定,在射芯机上进行制芯。
二、设备要求射芯机冷芯盒制芯工艺的设备要求比较简单,包括射芯机、冷芯盒、冷却介质以及3D打印机等。
其中,射芯机是制芯的核心设备,具有稳定的性能和高精度的制芯能力,能够满足不同类型的芯子制造需求。
冷芯盒是制芯时所需的辅助设备,用于注入冷却介质,提高芯子内部光洁度和投产效率。
冷却介质是通过冷芯盒注入到芯子内部,实现芯子冷却;3D打印机用于制作冷芯盒,由于冷芯盒的型号不同,因此必须使用3D打印机来制作。
三、工艺流程射芯机冷芯盒制芯工艺的工艺流程如下:1、3D打印冷芯盒首先,使用3D打印技术制作冷芯盒,根据实际情况制作不同型号的冷芯盒。
2、制作芯盒使用芯盒制作设备制作芯盒,芯盒中心预留冷芯盒的活动空间,方便将冷芯盒放进去。
3、放入冷芯盒将冷芯盒放入芯盒中央的冷芯盒活动空间中,使其与芯盒紧密贴合,预留供冷却介质流通的孔。
4、连接冷却液路连接冷却液路的二级循环,使冷却介质可以流行到冷芯盒中心部位,实现芯子的冷却。
5、加热芯盒先预热芯盒,再向芯盒内注入熔融的铝合金材料,通过射芯机将熔融的铝合金材料挤压到芯盒中心,将冷却介质流入到冷芯盒中心部位。
6、芯子收集通过推出机和接料机收集芯子,完成固态铝制芯子的制造,实现集成芯片封装和电子设备制造过程中的芯子制造需求。
四、注意事项在射芯机冷芯盒制芯工艺中,需要注意以下事项:1、冷芯盒设计的尺寸应该在芯盒中预留一定的活动空间,使其能够完全嵌入到芯盒中,避免在制作过程中出现不必要的问题。
三乙胺法冷芯盒制芯工艺的应用及探讨

三乙胺法冷芯盒制芯工艺的应用及探讨潍坊柴油机有限责任公司邹化仲=摘要>为进一步推广应用三乙胺法冷芯盒制芯工艺,对在此工艺中存在的问题作了分析,并提出了改进措施。
1国内外三乙胺法冷芯盒工艺的发展应用三乙胺法冷芯盒工艺即酚醛氨基甲酸乙酯工艺,是冷芯盒制芯工艺方法中目前应用最广泛的一种,开发于1968年。
其制芯工艺过程是,在定量原砂中按工艺配比加入组分Ñ酚醛树脂和组分Ò聚异氰酸酯的双组分粘结剂,在混砂机中混均匀后得到冷芯砂,利用射芯机紧实到芯盒中,再藉助气体发生器,以干燥的压缩空气或氮气等为载体将定量的雾化或汽化的三乙胺催化剂通过吹气板吹入芯盒,将双组分粘结剂中的羟基和异氰酸催化变成尿烷而硬化,继而靠载体气体清洗出芯砂中残余的三乙胺,得到具有一定强度、满足工艺要求的砂芯。
冷芯盒法制芯工艺用的芯盒不需加热,免去了芯盒热变形,砂芯精度高,芯盒寿命长,芯盒材质可视生产批量大小等条件选用钢、铸铁、铝、塑料、木材等。
冷芯盒制芯工艺化学反应迅速,固化周期短,生产效率高,砂芯发气量较低,溃散性好,易清砂,铸件表面光洁,废品率低,综合成本低,易于组织自动化生产,经济效益显著。
因此,在近20年的发展中,日益取代油砂法、热芯盒法、壳芯法等传统制芯工艺。
在欧美等有些工厂采用三乙胺法冷芯盒制芯工艺生产的砂芯重量达砂芯总重量的70%以上。
为适应铸造工艺各方面的不同要求,特别是提高现行三乙胺法冷芯盒砂芯的热强度,防止在浇注金属高温作用下,砂芯过早溃散、变形、开裂造成废品,美国有关部门研究出高热强度三乙胺冷芯盒工艺,将现行三乙胺法冷芯盒工艺用的粘结剂组分Ñ酚醛树脂改为酚醛多元醇树脂,其他不变。
这样,溃散时间从不到100s延迟到400s。
另一方面,德国、美国、意大利、西班牙、日本等各国对三乙胺法冷芯盒工艺配套设备,射芯机、气体发生器、芯砂混砂机、空气干燥器、砂加热冷却器、废气净化装置等的研究逐步深入,不断采用新技术、新专利形成各具特色的系列化生产。
冷芯盒工艺优典型失效案例分析

冷芯盒工艺优典型失效案例分析随着科技的不断进步,冷芯盒工艺在铸造行业中得到了广泛应用。
冷芯盒是铸造过程中用于注入冷芯材料的容器,通过冷却机械的作用,实现铸件内部的凝固与冷却。
然而,在实际应用过程中,冷芯盒工艺也可能出现一些失效问题。
本文将针对冷芯盒工艺的优点和典型的失效案例进行分析。
冷芯盒工艺的优点主要体现在以下几个方面:1. 提高生产效率:冷芯盒工艺可以实现一次性注入多个冷芯,减少了工作人员的操作次数和时间。
相比传统的手工冷芯注入,冷芯盒工艺可以大大提高铸造生产的效率。
2. 提高铸件质量:通过冷却机械的作用,冷芯盒工艺可以快速冷却和固化铸件内部的冷芯材料,减少了铸件内部气孔和缩松的产生,提高了铸件的密实度和力学性能。
3. 降低工人劳动强度:传统的手工冷芯注入需要工人频繁操作,不仅操作复杂,还存在一定的安全隐患。
而冷芯盒工艺可以完全由机械自动化完成,减少了工人的劳动强度,提高了工作安全性。
然而,冷芯盒工艺在实际应用过程中也可能出现以下典型的失效案例:1. 冷芯材料破裂:冷芯盒工艺注入的冷芯材料通常为石膏或陶瓷等,这些材料在长时间的冷却过程中可能出现破裂的情况。
破裂的冷芯材料会导致铸件内部的冷却不均匀,影响铸件的质量。
2. 冷芯盒变形:冷芯盒在高温状态下长时间工作,容易受到热膨胀的影响而发生变形。
冷芯盒的变形会导致冷芯材料的不正常流动,进而影响铸件的成型。
3. 注入不均匀:冷芯盒工艺的注入过程需要保持一定的注入速度和压力,以确保冷芯材料均匀地注入到铸件内部。
如果注入速度和压力不均匀,容易导致冷芯材料的局部堆积或空洞,进而影响铸件的质量。
针对上述失效案例,我们可以采取以下措施进行改进:1. 选择高质量的冷芯材料:在冷芯盒工艺中,选择质量可靠、耐高温、不易破裂的冷芯材料,可以减少冷芯材料破裂引起的问题,并能够提高铸件的质量。
2. 加强冷芯盒的设计和制造:在冷芯盒的设计和制造过程中,要考虑到材料的热膨胀系数,合理设计冷芯盒的结构和尺寸,以减少冷芯盒的变形问题。
优质铸件生产中冷芯盒制芯的质量控制

优质铸件生产中冷芯盒制芯的质量控制摘要】冷芯盒工艺是一种节能、低污染、高效的造型及制芯工艺。
随着我国铸造业的快速发展,冷芯盒树脂砂工艺已经日益成熟,有逐步取代热芯盒成为铸造行业首选的趋势。
本文旨在分析探讨生产中使用酚醛尿烷树脂砂冷芯盒工艺制芯对铸钢件质量造成影响的因素,强调铸钢件制芯过程中的过程控制要点。
【关键词】冷芯;酚醛尿烷树脂砂;铸钢件质量;制芯一、冷芯工艺特点气硬冷芯盒工艺是指将树脂砂填充于芯盒,然后在室温下吹入气体或气雾催化或硬化而瞬时成型的树脂砂制芯工艺。
1.硬化速度快。
硬化反应几乎是在表面和内部同时进行,不受型腔形状或壁厚的限制,可有效提高生产效率,制得的砂芯可在1h内合型浇注。
2.芯砂可使用时间长。
可使用时间内树脂粘度变化几乎不可察觉,型砂的流动性良好。
一旦催化后,芯砂很快硬化。
可使用时间可在30s~200min范围内变化,能大范围适应生产需要。
3.砂芯抗热裂纹、脉纹等缺陷能力高。
4.含氮量低,发气量少,可降低气孔缺陷发生率。
5.气硬冷芯工艺设备密封性要求较高,必须配备尾气处理装置。
6.质量风险点。
制芯过程主要可能造成的铸件缺陷有气孔、夹砂、脉纹等,芯砂混砂是气硬冷芯工艺的最关键工序,混砂质量直接影响砂芯的强度质量,是质量管控的重点。
二、过程控制1.制芯原材料气硬冷芯工艺树脂砂制芯的原材料包括原砂、树脂粘结剂、冷铁、芯骨、涂料等。
1.1芯砂原砂1.1.1原砂的角形因数、颗粒度、含泥量。
在满足砂芯吊运的基础上,原砂的颗粒度、含泥量等的不同,树脂的加入量也要发生变化,相应影响铸件气孔和应力产生的倾向。
原砂颗粒度越小,含泥量越高,硅砂颗粒表面积越大,耗费的粘结剂量越多,铸件气孔和应力倾向越大。
生产过程常控制粘结剂量,对硅砂颗粒度应有所要求,建议优先选用满足下表1要求的擦洗硅砂,工艺控制过程可基本稳定控制树脂等粘结剂加入量,来保证砂芯使用强度。
1.1.2原砂含水量。
为保证砂芯成型强度满足要求,原砂必须干燥,原砂含水量超过0.1%就会减少芯砂的可使用时间,降低砂芯强度,也会增加铸件针孔产生的倾向,含水量最佳范围是<0.1%,允许范围≤0.2%。
冷芯盒的发展和应用

冷芯盒的发展和应用摘要:论述了目前使用较广泛的冷芯盒工艺的一些关键工序 ,参考德国铸造现状,着重从冷芯盒的树脂、原砂、混砂工艺、芯盒设计等方面进行了分析。
对一些常见的铸造缺陷(例如脉纹) ,以及混制后砂型输送、射芯机制芯个数、型砂存放时间控制等。
近年来,冷芯盒工艺在中国铸造工业得以蓬勃发展,很多铸造厂已经使用此项技术。
现对冷芯盒工艺的一些关键因素进行以下论述。
1冷芯盒树脂和活化剂的化学特征传统的酚尿烷基冷芯盒法,粘结剂由两部分组成,为含有机溶剂的聚醚酚醛和聚异氢酸酯溶液。
酚醛树脂和聚异氢酸酯通常用有机溶剂稀释。
然而聚异氢酸酯和酚醛树脂的极性不同,与这两组分匹配的有机溶剂的最佳加入量也不同。
其最佳加入量是既不能使反应进行彻底,也不能使粘结剂自行固化。
比如适用于酚醛树脂的溶剂不一定适用于聚异氢酸酯 ,这种情况确实如此 ,采用非极性溶剂结果恰恰相反。
非极性溶剂为高沸点的芳烃碳氢化合物(通常为其混合物) ,在常压下其沸点高于150 ℃,高沸点酯也可作为极性溶剂。
尽管聚异氢酸酯对铸造工业有许多优点,但与其配用的高沸点极性溶剂在制芯和造型过程中会产生很多挥发物,尤其在浇注以后,由此带来很多缺点。
在高温浇注情况下,由于粘结剂热分解产生新的、稳定的新组分。
由于芳烃碳氢化合物的存在,浇注过程中通常会产生苯、甲苯和二甲苯,这些化合物在高温下具有很高的热稳定性。
HA 研制的新型冷芯盒树脂的组成却与上述完全不同,在树脂和活化剂中,采用植物基的菜油甲酯代替高沸点的芳烃溶剂。
该溶剂具有沸点高、粘高低、环保、气味小、无污染等优点可以完全满足树脂的各种性能要求,特别是其为非易燃品 ,运输和贮存十分方便 ,大大降低了铸造车间的安全隐患 ! 所需的硬化气体为胺类,按其闪点可分为:DMEA 的闪点36~38 ℃;DMIA 的闪点65~68 ℃; TEA 的闪点 87~89 ℃。
2、制芯材料冷芯盒法多采用石英砂。
高质量的石英砂一般含有极少的矿物,该类矿物常为:长石 ,云母 ,高岭石 ,碱性金属氧化物和碳水化合物。
- 1、下载文档前请自行甄别文档内容的完整性,平台不提供额外的编辑、内容补充、找答案等附加服务。
- 2、"仅部分预览"的文档,不可在线预览部分如存在完整性等问题,可反馈申请退款(可完整预览的文档不适用该条件!)。
- 3、如文档侵犯您的权益,请联系客服反馈,我们会尽快为您处理(人工客服工作时间:9:00-18:30)。
冷芯盒制芯技术及应用现状前言自1968年美国的阿什兰公司发明并推广冷芯盒技术以来,冷芯盒制芯因其生产效率高、节能,砂芯尺寸精度高、发气量低,芯盒寿命长、变形量小,铸件表面光洁、尺寸精度高(可达到CT7级),浇注后砂芯溃散性好等特点而被广泛采用。
尽管冷芯盒法除了ISOCURE法(阿什兰法)外,后来还开发了SO2法(呋喃树脂/SO2法、环氧树脂/SO2法、酚醛树脂/SO2法、自由基硬化法)、低毒或无毒的气硬促硬法(钠水玻璃/CO2法、酚醛树脂/脂法、有机粘结剂/CO2法)、FRC法,但目前应用最多的仍是ISOCURE法。
ISOCURE法是在原砂中加入一定量的组分I(液态的酚醛树脂)和II组分(聚异氰酸脂),在混砂机中混匀后,用射芯机射砂或人工填砂制芯,用干燥的空气、CO2气体或氮气作载体,通入约5%浓度的催化剂气体,使组分I中的酚醛树脂的羟基和组分II中的异氰酸基在催化剂的作用下,发生聚合反应生成尿烷树脂而固化。
冷芯盒的适应性强,它可以应用于铸造所有种类的黑色和有色合金以及适用于大多数铸造用砂,冷芯盒砂芯可小到136g,大到840Kg,最大达到1000磅;砂芯壁厚从3mm到170mm。
在国内外,冷芯盒技术已成功的应用于汽车、拖拉机、飞机、机床、泵业等行业,但在实际生产中,冷芯盒制芯工艺受到许多因素的影响,包括原材料、工装、工艺参数等。
本文对冷芯盒技术的应用中应注意的问题作了一定的综述,并对国内应用冷芯盒技术的情况作了说明。
一、冷芯盒生产中应注意的问题:冷芯盒技术的本质是组分I(液态的酚醛树脂)和II组分(聚异氰酸脂)在催化剂的作用下,生成尿烷的过程,即:催化剂酚醛树脂+聚异氰酸脂尿烷组分I的酚醛树脂结构要求为苯醚型,组分II为4,4’二苯基甲烷二异氰酸酯(MDA)或多次甲基多苯基多异氰酸脂(PAPI)等,美国推荐使用MDA,我国主要用PAPI。
组分I和组分II通常用高沸点的酯或酮稀释,以增加树脂的流动性和可泵性,使树脂容易包覆在砂粒表面,也增加芯砂的流动性,使砂芯致密。
催化剂为叔胺,可使用三乙胺(TEA)、二甲基乙胺(DMEA)、异丙基乙胺或三甲胺(TMA),因为三乙胺便宜,通常采用三乙胺作催化剂。
该反应过程非常迅速,在催化剂的作用下,可以立即完成反应。
冷芯盒的生产过程通常为:尽管冷芯盒树脂的硬化过程很快,但在生产过程中,原砂、水分、温度及工装对制芯过程和砂芯质量有很大的影响。
1、原砂所有用树脂作黏结剂的原砂都要求粒形好,粒度适当,以减少树脂的加入量,降低浇注时的砂芯发气量。
冷芯盒树脂要求原砂最好是圆形的,这样,原砂表面积最小,可以减少树脂的用量,对砂芯强度也最为有利。
但次角形的砂对减少飞边或毛刺有利。
一般要求原砂的角形系数<1.3,AFS细度为50-60,并且分布不要过于集中,最好分布在相邻的5-6个筛号,以利用浇注时不同粒度砂的膨胀时间差异来防止铸件产生脉纹现象。
因为冷芯盒树脂在碱性情况下提早发生反应,所以,原砂吸酸值高则芯砂的可使用时间缩短。
原砂的吸酸值为0-5最好,5-20为可用范围。
同样,原砂的PH=6-8是最好的。
许多金属氧化物呈碱性,过多的氧化物也会降低芯砂的可使用时间,故原砂中的氧化物含量要求<0.3%。
原砂的含泥量要尽可能的小。
含泥量增加,不仅降低了砂芯强度,降低了透气性,还使铸件产生脉纹缺陷的倾向增加,一般要求含泥量<0.3%。
水分能够与冷芯盒树脂中的组分II发生反应,而且水分的存在还能降低芯砂的流动性,造成砂芯疏松,使砂芯质量大大降低。
所以,冷芯盒工艺中对原砂的水分要求严格,原砂的水分最好在0.1%以下。
随着水分的增加,砂芯强度下降(如图1),铸件产生脉纹的倾向加大。
原砂水分<0.25%的也可用,但水分>0.25%,则砂芯的品质大降。
图1:砂芯抗拉强度与原砂含水量的关系冷芯盒制芯对原砂和树脂的温度要求也较为严格。
尽管目前冷芯盒树脂的粘度较低(如苏州兴业的组分I≤300mpa.s,组分II≤100mpa.s;亚什兰(常州)的组分I=120-200mpa.s,组分II=10-30mpa.s (均在25℃时)),但如果温度太低(如低于10℃),因树脂中的组分I变得粘性增加而造成混碾不匀;相反,如果砂温过高,则树脂反应加快,混好的砂子存放期就会变短。
目前使用的树脂,要求原砂温度最好在21-27℃之间,10-40℃虽然也能使用,但对砂芯质量有一定的影响。
2、混砂虽然冷芯盒混砂可以使用任何类型的混砂机,但是,使用碗形快速混砂机最好,并且随用随混。
混砂时,一方面要使混砂时间短些,以便不影响芯砂的可使用时间(空气的湿度、混砂时的发热和溶剂的挥发都可以影响到芯砂的可使用时间);另一方面,又必须混匀,使树脂均匀的包覆在砂粒的表面,发挥最大的粘结强度。
混砂时一般为先加原砂,再加组分I,混碾一定时间后,再加组分II,混匀后出砂,即混碾混匀原砂+组分I 组分II 出砂其实,先加哪一组分并没有特别的优点,两组分同时加入也可以(但不可存放时混合)。
砂芯的强度随树脂的加入量增加而增加,但同时铸件产生脉纹的倾向加大,而且,树脂加入量过高,成本加大,发气量增加,因此,一般控制树脂加入量在2.0%以内(国外生产轻金属合金时树脂的加入量最低可至0.6%,国内黑色铸造一般为1.2-2.0%)。
在树脂加入量一定时,随着组分II的增加,砂芯终强度和抗吸湿性增加,在50:50时达到最高,之后,随着组分II的继续增加,砂芯终强度和抗吸湿性下降,在组分II的加入量为80%时,砂芯强度几乎完全丧失;随着组分II的减少,制芯时降低了粘模性,取芯变得容易,铸件产生脉纹的倾向减少,而且由于含氮量降低(组分II中含有3-4%的氮),铸件气孔缺陷减少,但对粘砂影响不大。
决定砂芯质量的是组分I的性能和加入量。
3、添加剂正常生产时一般不加添加剂,为解决铸件出现的某一缺陷,有时在混砂时加入某种添加剂。
添加剂有氧化铁、纤维素材料、耐火泥、硅粉、糖浆等。
氧化铁红的加入量在砂总量的0.25-3%之间,可以减少铸件皮下气孔和表面针孔的缺陷,也可以减少脉纹缺陷。
氧化铁黑也可以使用,并不需要多加树脂以弥补因砂中细粉过多而造成的强度下降。
还有加极细的干燥的木屑来防止脉纹的产生。
其原理可能是加入附加物后,能缓解石英砂在高温时的瞬时膨胀。
但附加物的加入,可能引起粘砂缺陷。
氧化铁的加入,还会使出砂性能变差。
有色金属用砂芯还常在树脂中加入0.1%-1.0%的氟硼酸钾或0.25-0.5%的硫磺作为抑制剂,以弥补由于树脂系统误差而引起的误差。
4、压缩空气压缩空气用做催化剂的载体和洗涤砂芯用,也有用CO2和N2用载体的(因为三乙胺易燃易爆,用CO2和N2用载体更加安全)。
所用的压缩空气如果含有水分,则对砂芯的质量影响很大,因为在射砂时或随后的吹气净化过程中,水分都可与树脂中的II组分发生反应而影响砂芯的强度。
分还降低了砂子的流动性而使砂芯疏松。
因此,冷芯盒所用的压缩空气必须是干燥的。
一般来说,生产薄的复杂砂芯时所用的空气的露点最好在大气压下为―50℉,生产厚大砂芯时所用的空气的露点在―10℉下也可以使用。
一般采用吸附法或冷冻法除水。
冷冻法比吸附法效果要好,而且稳定。
5、工装在冷芯盒制芯中,由于砂芯的硬化不是加热,而是靠三乙胺气体的催化来完成的,因此,芯盒可以使用任何材料制作,铸铁、钢、铝、塑料、树脂甚至木头都可以,芯盒不会因加热引起变形,砂芯精度非常高。
在制芯过程中,为了得到完好的砂芯,首先必须确保砂芯射得致密,其次,要确保催化剂均匀的达到砂芯的每一个地方,使砂芯硬化。
芯砂紧实一般利用压缩空气来完成,这在大量生产时非常必要。
也可以用震实、挤压、手椿或刮砂的方法来完成,但必须保证砂芯的紧实度。
如果利用压缩空气来完成射砂及紧实,射嘴的大小和位置是十分重要的,应该尽量选用口径大而直的射嘴,以降低吹砂压力即冲击速度,从而减少树脂残留在芯盒上,同时降低砂子与芯盒的磨损。
射砂时间非常短,通常在3-5s之间,射砂时气流的速度非常快,通常情况下,如果射砂时的空气压力为0.6Mpa,则在射嘴出口的气流速度可达235m/s。
如此高的冲击速度,极容易造成砂粒撞击芯盒内壁后回弹,使树脂粘在芯盒上,增加粘模性,不易脱模甚至砂芯损坏。
因此,要选用低的射砂压力和大的射嘴。
射嘴面积的选用,厚大的砂芯要保证0.2平方英寸/磅,复杂砂芯则要保证不小于0.35平方英寸/磅。
吹砂压力在0.25-0.3MPa是最好的,不要超过0.4MPa。
三乙胺发生器到芯盒的进气管路设计要根据砂芯的大小来决定,最好是大口径的管路,弯头尽可能的少,线路尽可能的短,保证催化剂气体迅速、畅通的进入芯盒。
推荐的进气管口径如表1。
表1:推荐的进气管口径而排气管路(芯盒排气到废气处理)的管径也要尽可能的大,最好设计排气量为进气量的3倍以上,尽量少用弯头和T型接头,保证排气畅通。
射砂嘴和排气塞的数量和布置既要保证射砂时能使整个砂芯致密,还要保证催化剂能均匀的到达砂芯的每一个部位。
进气面积要尽可能的大,可以保证在砂芯的一面迅速充满催化剂气体,排气面积比进气面积要小,一般为进气面积的60-80%,并且位置要适当。
如果催化剂气体不能到达,则该处就不能硬化,造成砂芯局部强度不够;如果要想使该部位硬化,只有延长硬化时间,这样就造成了催化剂的浪费,也降低了生产效率。
射嘴位置最好开在砂芯的最大面积处,以便砂子均匀的、畅通无阻的射满模腔各个角落。
射嘴方向、催化剂流动的方向和排气塞方向要一致,以保证催化剂能通畅的到达砂芯的每一个地方。
压缩空气管路口径太小、催化剂输送管路口径太小、催化剂混合气进气分布不好、射嘴、排气塞面积过小、催化剂在砂芯中流动有短路现象、排气管太长或太细都会导致催化剂用量过高或硬化速度过慢。
正常的砂芯硬化速率应是厚大砂芯高于10磅/秒,复杂砂芯高于3磅/秒。
就具体的三乙胺用量而言,厚大的砂芯每吨砂少于1磅(0.33ml/b),复杂砂芯少于1.6磅(0.5ml/b),说明工装设计的非常合理。
在实际生产中,平均催化剂消耗量要高一些,厚大的砂芯通常在1-2b/t、复杂砂芯在1.7-2.2b/t之间,超过了该范围,说明工装设计存在不合理的地方。
芯盒的密封也非常重要。
密封有芯盒与芯盒、芯盒与射腔,如图2所示,如果密封损坏,催化剂就会漏掉,造成硬化不良、硬化速度慢和催化剂浪费。
图2:硬化过程示意图硬化所用的三乙胺只是一种催化剂,加速两种树脂的聚合反应速度,使反应在几秒中内即可完成,而没有催化剂,反应则需要几个小时或几天的时间才能完成。
在反应过程中,胺只是某种电子的位移,反应结束后,三乙胺本身并没有发生改变。
因此,进入多少催化剂,就排出多少催化剂。
由于三乙胺有臭味,蒸汽刺激眼睛和呼吸系统,并且是极易燃易爆的危险品,因此,除了必须保证密封外,硬化反应过程中,必须抽风排出尾气;反应结束后,还必须清洗干净砂芯中和芯盒工装中的胺,保证工作环境良好。