金属零件激光增材制造技术及其应用
金属材料激光增材制造技术

金属材料激光增材制造技术孙峰、李广生金属材料增材制造技术是通过对CAD模型进行离散处理,以金属粉末、颗粒、金属丝材等为原材料,采用高功率激光束熔化/快速凝固逐层堆积生长,直接从零件数模完成高性能零件的近终成形制造。
金属材料增材制造技术,可分为以送粉为技术特征的激光沉积制造(Laser Deposition Melting,LDM)技术和以粉床铺粉为技术特征的选区激光熔化(Selective Laser Melting,SLM)技术。
LDM技术是快速成形技术和激光熔覆技术的有机结合,是以金属粉末为原材料,以高能束的激光作为热源,根据成形零件CAD模型分层切片信息规划的扫描路径,将送给的金属粉末进行逐层熔化、快速凝固、逐层沉积,从而实现整个金属零件的直接制造。
LDM系统主要包括:激光器及光路系统、水冷机及冷却系统、数控机床系统、送粉器及送粉系统、惰性气体保护系统、激光熔化沉积腔及工艺监控系统等。
图1LDM激光沉积制造技术LDM技术集成了快速成形技术和激光熔覆技术的特点,具有以下优点:(1)无需大型设备与模具,零件近净成形,材料利用率高;工艺流程、制造周期短,制造成本低;(2)零件无宏观偏析,组织细小、致密,力学性能达到锻件水平;(3)成形尺寸不受限制,可实现大尺寸零件的制造;(4)激光束能量密度高,可实现难熔、难加工材料的近净成形;(5)可对失效和受损零件实现快速修复,并可实现定向组织的修复与制造。
主要缺点:(1)制造成本较高;(2)制造效率较低;(3)制造精度较差,悬臂结构需要添加相应的支撑结构。
SLM技术是以快速原型制造技术为基本原理发展起来的先进激光增材制造技术。
通过专用软件对零件三维数模进行切片分层,获得各截面的轮廓数据后,利用高能激光束根据轮廓数据逐层选择性地熔化金属粉末,通过逐层铺粉,逐层熔化凝固堆积的方式,实现三维实体金属零件制造。
SLM系统主要由激光器及光路系统、气体净化系统、铺粉系统、控制系统4部分组成。
金属材料激光增材制造技术

金属材料激光增材制造技术孙峰、李广生金属材料增材制造技术是通过对CAD模型进行离散处理,以金属粉末、颗粒、金属丝材等为原材料,采用高功率激光束熔化/快速凝固逐层堆积生长,直接从零件数模完成高性能零件的近终成形制造。
金属材料增材制造技术,可分为以送粉为技术特征的激光沉积制造(Laser Deposition Melting,LDM)技术和以粉床铺粉为技术特征的选区激光熔化(Selective Laser Melting,SLM)技术。
LDM技术是快速成形技术和激光熔覆技术的有机结合,是以金属粉末为原材料,以高能束的激光作为热源,根据成形零件CAD模型分层切片信息规划的扫描路径,将送给的金属粉末进行逐层熔化、快速凝固、逐层沉积,从而实现整个金属零件的直接制造。
LDM系统主要包括:激光器及光路系统、水冷机及冷却系统、数控机床系统、送粉器及送粉系统、惰性气体保护系统、激光熔化沉积腔及工艺监控系统等。
图1LDM激光沉积制造技术LDM技术集成了快速成形技术和激光熔覆技术的特点,具有以下优点:(1)无需大型设备与模具,零件近净成形,材料利用率高;工艺流程、制造周期短,制造成本低;(2)零件无宏观偏析,组织细小、致密,力学性能达到锻件水平;(3)成形尺寸不受限制,可实现大尺寸零件的制造;(4)激光束能量密度高,可实现难熔、难加工材料的近净成形;(5)可对失效和受损零件实现快速修复,并可实现定向组织的修复与制造。
主要缺点:(1)制造成本较高;(2)制造效率较低;(3)制造精度较差,悬臂结构需要添加相应的支撑结构。
SLM技术是以快速原型制造技术为基本原理发展起来的先进激光增材制造技术。
通过专用软件对零件三维数模进行切片分层,获得各截面的轮廓数据后,利用高能激光束根据轮廓数据逐层选择性地熔化金属粉末,通过逐层铺粉,逐层熔化凝固堆积的方式,实现三维实体金属零件制造。
SLM系统主要由激光器及光路系统、气体净化系统、铺粉系统、控制系统4部分组成。
增材制造技术的应用与发展

增材制造技术的应用与发展一、引言增材制造技术(Additive Manufacturing,AM)是指通过逐层堆积材料来制造产品的一种先进制造技术。
它采用计算机辅助设计和控制系统,根据三维模型数据逐层堆积材料,逐渐形成成品。
与传统的减材制造技术(Subtractive Manufacturing)相比,增材制造技术具有很多优势,如材料利用率高、制造周期短、几何形状复杂等。
本文将介绍增材制造技术的应用与发展,分别从金属增材制造、塑料增材制造和生物医疗领域进行探讨。
二、金属增材制造的应用与发展1. 概述金属增材制造技术是目前应用最为广泛的增材制造技术之一。
它可以通过激光熔化、电弧熔化等方式将金属粉末熔化,并在特定位置进行堆积,形成金属零件。
这种技术在航空航天、汽车制造、机械制造等领域具有广泛的应用前景。
2. 应用领域金属增材制造技术在航空航天领域得到了广泛应用。
例如,飞机零部件的制造可以使用增材制造技术,既可以满足零部件的高强度和高性能要求,又能够大幅降低零部件的重量。
此外,金属增材制造技术还可以用于制造航天器的推进系统和传感器等。
3. 技术发展随着材料科学和制造工艺的发展,金属增材制造技术也在不断进步。
目前已经出现了多种金属增材制造技术,如选择性激光熔化、电弧增材制造等。
这些技术在金属材料的选择、成型精度和制造效率等方面都有了显著的提升。
三、塑料增材制造的应用与发展1. 概述塑料增材制造技术是一种利用高温喷嘴或喷头将塑料线材加热至熔化,并通过控制喷嘴或喷头的运动轨迹来制造产品的技术。
这种技术在模具制造、个性化定制、家居装饰等领域有着广泛的应用。
2. 应用领域在模具制造领域,塑料增材制造技术可以快速制造模具,从而大大缩短了产品的开发周期。
此外,这种技术还可以用于制造复杂形状的家居装饰品、个性化的艺术品等。
3. 技术发展随着对材料性能要求的提高,塑料增材制造技术的发展也变得越来越重要。
目前,塑料增材制造技术已经可以使用多种高性能塑料材料,如聚酰亚胺、尼龙等。
金属粉床激光增材制造技术

金属粉床激光增材制造技术金属粉床激光增材制造技术是一种新型的金属加工技术,该技术采用激光为能源源,将金属粉末焊接成形,可以直接制造复杂零部件、金属零件及高性能金属材料等。
随着3D 打印技术的快速发展,金属粉床激光增材制造技术被广泛应用于航空、航天、船舶、汽车、医疗和电子等领域。
金属粉床激光增材制造技术具有多项优势。
首先,该技术可以实现大量小批量订单定制生产,无需加工模具,开销大幅降低。
其次,该技术具有很好的制造复杂形状产品的能力,能够制造出传统加工难以完成的零部件。
例如,内孔、空腔、薄壁等特殊形状产品,同时还能实现多材料复合加工。
第三,该技术制造出的产品质量高、精度高,产品表面光洁度好,并且产品材质硬度等物理性能优良。
第四,该技术具有环保优势,无需削减、磨削、切割等操作,对环境和人体健康无害。
金属粉床激光增材制造技术主要包括以下步骤:首先,设定产品三维数字模型;其次,将金属粉末在加热激光束下熔化,并将其固化成物体的一层,通过不断重复该过程,最终形成完整的三维物体。
在这个过程中,需要根据物体的形状、几何结构和材质特性选择适当的处理参数,使该技术的加工效率和加工质量达到最优化状态。
随着3D打印技术的不断创新和改进,金属粉床激光增材制造技术的应用前景非常广阔。
首先,航空、航天领域可以采用该技术制造轻量化和高强度材料的结构件和航空发动机。
其次,汽车行业可以生产轻量化汽车零部件,提高汽车性能。
第三,医疗领域可以生产人造骨、人造器官等高性能医疗器械。
第四,电子行业可以生产高性能散热器、导热板、触控传感器等电子元器件。
总之,金属粉床激光增材制造技术在未来的制造工业中将会发挥重要作用。
激光定向能量沉积增材制造技术及应用

激光定向能量沉积增材制造技术及应用1.引言1.1 概述概述激光定向能量沉积增材制造技术是一种先进的三维打印技术,它通过激光束将金属粉末熔化并逐层积累,从而实现对复杂形状零件的快速制造。
该技术具有高效、精确、可塑性强等特点,在制造业领域引起了广泛的关注和应用。
本文将深入探讨激光定向能量沉积增材制造技术的原理和应用,并展望其在未来的发展前景。
随着科技的发展和制造业的进步,零件的制造需求日益增加,特别是那些具有复杂形状和特殊功能要求的零件。
传统的加工方法往往会遇到制造困难和高成本的问题,因此需要一种新的制造技术来满足这些需求。
激光定向能量沉积增材制造技术的出现正是为了解决这些问题。
激光定向能量沉积增材制造技术与传统的加工方法相比,具有许多独特的优势。
首先,它可以根据设计要求实现高度个性化的制造,对于小批量生产和定制化生产非常适用。
其次,该技术能够实现快速、高效的制造过程,大大节约了制造时间和成本。
此外,激光定向能量沉积增材制造技术还具有高精度、材料利用率高、具备较好的机械性能等特点,能够满足各类零件的制造要求。
该技术的原理是通过激光束在金属粉末上进行选区熔化,将熔化的金属逐层积累成为固态零件。
在这个过程中,激光束的能量被准确地控制和定向,以实现精确的制造。
同时,激光束的使用还可以避免了传统加工方式中可能产生的机械损伤和变形问题。
激光定向能量沉积增材制造技术在许多领域都得到了成功应用。
例如航空航天领域,该技术可以制造出轻量化、高强度的零件,提高了飞行器的性能和燃油利用率。
同时在医疗领域,激光定向能量沉积增材制造技术也可以制造出个性化的医疗器械和假肢等,为患者提供更好的治疗和生活质量。
展望未来,激光定向能量沉积增材制造技术将会在更多领域得到应用和发展。
随着材料科学和激光技术的不断进步,该技术的制造速度和精度将进一步提高,为制造业带来更多的机遇和挑战。
同时,随着3D打印技术逐渐普及和成熟,激光定向能量沉积增材制造技术也将成为未来制造业的重要发展方向和趋势。
金属增材制造技术及其应用前景

金属增材制造技术及其应用前景金属增材制造是一种新型的制造技术,它是通过三维打印和激光堆焊等技术,在金属原材料上一层一层地构建出所需要的金属构件。
相比传统的金属制造方法,金属增材制造具有较高的精度、较短的制造周期和灵活的生产方式等优点。
近年来,随着金属增材制造技术的不断发展和成熟,它已经被广泛应用于航空航天、汽车制造、医疗器械等领域。
金属增材制造技术有着广泛的应用前景,可以满足汽车制造、医疗、军工、航空等各个领域的需求。
一、金属增材制造的技术方法金属增材制造技术有许多种方法,其中比较常见的有三维打印和激光堆焊技术。
1.三维打印技术三维打印技术是将金属原材料分层逐层地积累形成构件的制造方法。
首先根据需要建立数字模型,然后将该数字模型输入到三维打印机中,通过熔融、粉末、光束等不同的方式,将金属层层打印出来,直到构建出所需的形状。
三维打印技术不但可以生产出各种形状的构件,而且具有高精度、复杂度大、生产效率高等优点。
2.激光堆焊技术激光堆焊技术利用激光束瞄准工作面进行熔化,熔化过的金属材料很容易将下一层的粉末焊接在一起。
激光焊接过程中,熔化的金属材料可以很好地与下一层的金属粉末融合在一起,这样就可以形成精确的金属构件。
激光堆焊技术具有极高的焊接精度和摆放自由度,几乎可以将任何一件被设计的零件完整焊接。
二、金属增材制造技术的优势金属增材制造技术的出现很大程度上改变了传统的金属制造方式,它具有以下的优势:1.制造周期短传统金属制造,需要制造,加工,精加工等多个步骤,而且每一步都需要特定的设备和时间。
然而,在金属增材制造中,因为是逐层构建出构件,所以制造周期大大缩短。
例如,在三维打印中,利用打印机可以在数小时之内迅速制造出由数百至数千层构成的金属构件。
2.制造精度高相比传统的加工方式,金属增材制造技术具有更高的制造精度。
因为增材制造技术利用数字模型进行工作,它可以准确地控制每一层的厚度和形状,从而达到更高的制造精度。
金属零件激光增材制造技术的发展及应用
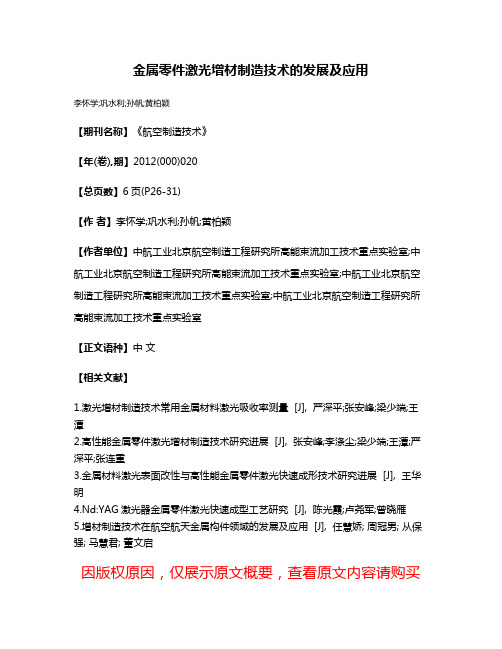
金属零件激光增材制造技术的发展及应用
李怀学;巩水利;孙帆;黄柏颖
【期刊名称】《航空制造技术》
【年(卷),期】2012(000)020
【总页数】6页(P26-31)
【作者】李怀学;巩水利;孙帆;黄柏颖
【作者单位】中航工业北京航空制造工程研究所高能束流加工技术重点实验室;中航工业北京航空制造工程研究所高能束流加工技术重点实验室;中航工业北京航空制造工程研究所高能束流加工技术重点实验室;中航工业北京航空制造工程研究所高能束流加工技术重点实验室
【正文语种】中文
【相关文献】
1.激光增材制造技术常用金属材料激光吸收率测量 [J], 严深平;张安峰;梁少端;王潭
2.高性能金属零件激光增材制造技术研究进展 [J], 张安峰;李涤尘;梁少端;王潭;严深平;张连重
3.金属材料激光表面改性与高性能金属零件激光快速成形技术研究进展 [J], 王华明
4.Nd:YAG激光器金属零件激光快速成型工艺研究 [J], 陈光霞;卢尧军;曾晓雁
5.增材制造技术在航空航天金属构件领域的发展及应用 [J], 任慧娇; 周冠男; 从保强; 马慧君; 董文启
因版权原因,仅展示原文概要,查看原文内容请购买。
解析金属增材制造技术在航空领域的发展与应用

解析金属增材制造技术在航空领域的发展与应用航空工业在上个世纪80年代就开始使用增材制造技术,之前增材制造在航空制造业只扮演了做快速原型的小角色。
最近的发展趋势是,这一技术将在整个航空航天产业链占据战略性的地位。
包括波音、空客、LockheedMartin,霍尼韦尔以及普惠都做出了表率行动。
新一代飞行器不断向高性能、高可靠性、长寿命、低成本方向发展,越来越多地采用整体结构,零件趋向复杂化、大型化,从而推动了增材制造技术的发展与应用。
增材制造技术从零件的三维CAD模型出发,无需模具,直接制造零件,可以大大降低成本,缩短研制周期,是满足现代飞行器快速低成本研制的重要手段,同时也是满足航空航天超规格、复杂金属结构制造的关键技术之一。
电子束熔丝沉积成形电子束熔丝沉积技术又称为电子束自由成形制造技术(ElectronBeamFreeformFabrication,EBF3)。
在真空环境中,高能量密度的电子束轰击金属表面形成熔池,金属丝材通过送丝装置送入熔池并熔化,同时熔池按照预先规划的路径运动,金属材料逐层凝固堆积,形成致密的冶金结合,直至制造出金属零件或毛坯。
电子束熔丝沉积快速成形技术具有一些独特的优点,主要表现在以下几个方面:(1)沉积效率高。
电子束可以很容易实现数10kW大功率输出,可以在较高功率下达到很高的沉积速率(15kg/h),对于大型金属结构的成形,电子束熔丝沉积成形速度优势十分明显。
(2)真空环境有利于零件的保护。
电子束熔丝沉积成形在10-3Pa真空坏境中进行,能有效避免空气中有害杂质(氧、氮、氢等)在高温状态下混入金属零件,非常适合钛、铝等活性金属的加工。
(3)内部质量好。
电子束是“体”热源,熔池相对较深,能够消除层间未熔合现象;同时,利用电子束扫描对熔池进行旋转搅拌,可以明显减少气孔等缺陷。
电子束熔丝沉积成形的钛合金零件,其超声波探伤内部质量可以达到AA级。
(4)可实现多功能加工。
电子束输出功率可在较宽的范围内调整,并可通过电磁场实现对束流运动方式及聚焦的灵活控制,可实现高频率复杂扫描运动。
- 1、下载文档前请自行甄别文档内容的完整性,平台不提供额外的编辑、内容补充、找答案等附加服务。
- 2、"仅部分预览"的文档,不可在线预览部分如存在完整性等问题,可反馈申请退款(可完整预览的文档不适用该条件!)。
- 3、如文档侵犯您的权益,请联系客服反馈,我们会尽快为您处理(人工客服工作时间:9:00-18:30)。
内容来源网络,由“深圳机械展(11万㎡,1100多家展商,超10万观众)”收集整理!
更多cnc加工中心、车铣磨钻床、线切割、数控刀具工具、工业机器人、非标自动化、数字化无人工厂、精密测量、3D打印、激光切割、钣金冲压折弯、精密零件加工等展示,就在深圳机械展.
传统零件制备工艺主要是减材制造。
从一块原材料开始,通过切割、钻、铣削等机械工艺方式去除部分材料,从而获得一个三维物体形态,这个过程中材料的利用率较低。
而增材制造通过极小单位的原材料的叠加产生三维物体形态,虽然后期也可能通过再加工产生废料,但总体来说对材料的浪费是很少的。
这在原型制作以及小批量生产上明显优于传统减材技术。
激光增材制造技术是一种基于离散/ 堆积成形思想的新型制造技术,是集成计算机、数控、激光和新材料等新技术而发展起来的先进产品研究与开发技术。
其基本过程是将三维模型沿一定方向离散成一系列有序的二维层片;根据每层轮廓信息,进行工艺规划,选择加工参数,自动生成数控代码;成形机制造一系列层片并自动通过激光熔敷、烧结、沉积等将它们联接起来,得到三维物理实体。
这样将一个物理实体的复杂三维加工离散成一系列层片的加工,大大降低了加工难度,且成形过程的难度与待成形的物理实体形状和结构的复杂程度无关。
该技术的主要特点有:高柔性,可以制造任意复杂形状的三维实体;CAD模型直接驱动,设计制造高度一体化;成形过程无需专用夹具或工具;无需人员干预或只需较少干预,是一种自动化的成形过程;成形全过程的快速响应,适合现代激烈的产品市场。
尤其是金属零件,其主要采用激光增材制造技术,以高功率或高亮度激光为热源,逐层熔化金属粉末,直接制造出任意复杂形状的零件。
其主要方法有:
1、激光直接沉积增材制造技
该技术可追溯到20 世纪70 年代末期的激光多层熔覆研究,但直到20世纪90年代,国内外众多研究机构才开始对同轴送粉激光快速成形技术的原理、成形工艺、熔凝组织、零件的几何形状和力学性能等基础性问题开展大量的研究工作。
激光直接沉积技术为航空航天大型整体钛合金结构制造提供一种短周期、高柔性、低成本手段。
为了提高结构效率、减轻结构重量、简化制造工艺,国内外飞行器越来越多地采用了大型整体钛合金结构。
与锻压- 机械加工传统制造技术相比,激光直接沉积增材制造技术具有以下特点:无需零件毛坯制备,无需锻压模具加工,无需大型或超大型锻铸工业基础设施及相关配套设施;材料利用率高,机加工量小,数控机加工时间短;生产制造周期短;工序少,工艺简单,具有高度的柔性与快速反应能力;采用该技术还可根据零件不同部位的工作条件与特殊性能要求实现梯度材料高性能金属零件的直接制造。
激光直接沉积技术还可以为航空航天、工模具等领域高附加值金属零部件的修复提供一种高性能、高柔性技术。
由于工作环境恶劣,飞机结构件、发动机零部件、金属模具等高附加值零部件往往因磨损、高温气体冲刷烧蚀、高低周疲劳、外力破坏等因素导致局部破坏而失效。
另外,零件制造过程中误加工损伤是其被迫失效的另一重要原因。
若这些零部件被迫报废,将使制造厂方蒙受巨大的经济损失。
与传统热源修复技术相比,激光直接沉积技术因激光的能量可控性、位置可达性高等特点逐渐成为其关键修复技术。
2、激光选区熔化增材制造技术
激光选区熔化技术是由德国Frauhofer研究所于1995年提出,在金属粉末选择性烧结基础上发展起来的。
2002年该研究所在激光选区熔化技术方面取得巨大成就,可一次性地直接制造出完全致密性的零件。
随着高亮度光纤激光的出现,国外金属粉末选区熔化激光精密增材成形技术发展突飞猛进。
譬如,德国EOS GmbH 公司新开发的激光选区熔化设备EOSINT M280 采用束源质量高的Yb 光纤激光器,将激光束光斑直径聚焦到100μm,大幅提高激光扫描的速度,减少成形时间,其成形零件性能与锻件相当。
激光选区熔化技术可直接制成终端金属产品,省掉中间过渡环节;零件具有很高的尺寸精度以及好的表面粗糙度(Ra 为10~30μm);适合各种复杂形状的工件,尤其适合内部有复杂异型结构、用传统方法无法制造的复杂工件;适合单件和小批量复杂结构件无模、快速响应制造。
2009 年以来,中航工业北京航空制造工程研究所通过与国际著名激光粉末烧结设备制造商——德国EOS 公司的技术交流,自主开发建立激光选区熔化增材制造技术平台,研制出一些典型金属结构件,其TC4 钛合金力学性能与锻件相当,但仍受到层片扫描轨迹优化设计、应力及变形协调控制等基础问题制约。
激光增材制造其实质就是CAD软件驱动下的激光三维熔覆过程。
所以其不仅可实现激光熔覆制备耐磨涂层和功能梯度材料,而且可修复高附加值的金属件和直接制造任意复杂结构的金属零部件。
随着其成形工艺和装备不断地成熟和提高,成形材料从钛合金、镍基合金、不锈钢、钴铬合金等成熟材料种类,不断推出新材料。
通过拓扑优化设计结构,激光选区熔化技术可制造出大幅减轻重量的航空航天金属结构件。
目前,金属零件激光增材技术面临的主要挑战包括成形过程应力及变形、材料组织及性能控制、质量检测及标准建立等。
产品创新是我国制造行业可持续发展的基础,而金属零件的激光快速成形技术对新产品的开发速度和重要零部件的再制造将起到十分重要作用。
金属零件激光增材制造技术开创了一个崭新的设计、制造概念。
它以相对低的成本、高速造型、可修改性强的特点,独特的工艺过程,为提高产品的设计质量、降低成本、缩短设计及制造周期,为将产品尽快推向市场提供了有效的方法,尤其适合于形状复杂的零件。
内容来源网络,由深圳机械展收集整理!
更多激光钣金及冲压自动化工艺展示,就在深圳机械展.金属板材加工展区/激光精密加工应用展区。