铝冷轧机边部板形缺陷的控制
冷轧半成品常见缺陷及改正措施专题

冷轧半成品常见缺陷及改正措施专题一、压痕特征:带钢表面呈周期性凹状印痕原因:1、因勒带或穿带甩尾不正常,带钢在工作辊表面造成堆焊或粘接2、在轧机空转时预压力过小,造成工作辊与支撑辊点接触而使支撑辊周长方磨损,受损支撑辊反过来造成新更换工作辊表面压印而造成带钢表面压痕3、支撑辊掉肉造成工作辊表面压印,即在带钢表面产生压痕措施:1、轻微小面积压痕可对工作辊进行修磨(用砂石),严重压痕应更换工作辊2、轧机空转时给一定轧制压力或采用正弯辊,以避免局部损伤轧辊,发现支撑辊局部损伤,避免使用负弯辊,减轻轧辊表面压痕深度,勤换工作辊,必要时及时更换支撑辊二、压印特征:带钢表面呈周期性凸状印痕原因:工作辊表面产生裂纹或掉皮措施:1、更换新工作辊之前,严格检查轧辊表面质量,防止未磨净裂纹辊投入使用,(轧辊间应确保应有磨削量,特别是粘钢辊,以完全消除裂纹层)2、确保各机架工艺润滑良好,轧制液温度、浓度、压力在正常范围,防止喷嘴堵塞,避免轧辊局部温度过高3、发现压印及时更换轧辊,更换新辊后,要进行一定预热,同时,开轧头几卷钢要严格控制升速制度三、划伤特征:带钢沿轧制方向的直线凹状缺陷原因:1、各种导辊与带钢速度不一样2、带钢与辅助设备异常接触3、生产线设备有异物措施:1、定期检查辅助传动辊是否转动灵活及表面状况2、固定辅助设备与带钢应保持一定间隔3、及时检查、清除生产线设备中的异物4、发现带钢表面有划伤,应从后向前逐个检查,查出事故原因后,根据情况采取的办法给予处理四、裂边特征:带钢边部局部开裂或呈锯齿形裂口原因:1、酸洗剪切边部状况不好,造成轧后带钢裂边2、热轧板本身边部裂口或龟裂3、吊运中夹钳碰撞,使带钢边部碰损措施:1、酸洗剪切边剪刃间隙,应按剪切的不同厚度规格精确调节2、热轧原板边部缺陷应在酸洗工序尽量切除(呈月牙形)3、吊运钢卷时,夹钳应稳、准、轻,防止吊具将钢卷边部碰损五、热划伤特征:带钢表面沿轧制方向无规律的局部条状凹痕原因:1、轧辊和带钢温升过高2、轧制薄规格时,在高速高压下,轧制油的油膜强度不够,使润滑不良所致措施:1、正确选择轧制油浓度和轧制油类型,确保良好的润滑性能2、使各机架的负荷分配尽量均匀3、正确选择轧制液的温度、压力,确保良好的冷却性4、选择适当的轧制速度,在润滑和冷却不好的情况下,轧制速度不应超过1000mpm5、当已经发现有较严重的热划伤时,立即更换工作辊六、轧穿特征:带钢表面呈周期性孔洞原因:1、工作辊表面严重粘接2、严重粘辊裂纹(一般前架板面产生压印,经后架轧钢延伸造成轧穿)3、轧辊表面凹状缺陷措施:1、更换新工作辊2、防止异物掉入轧机进入辊缝,避免轧辊表面损伤七、板形缺陷A、双边浪特征:带钢两边呈可见波纹状原因:轧辊凸度小,轧制压力过大,轧制温度低、正负弯辊使用不当措施:减小轧制压力或加大后张力,合理控制好辊型,将工作辊中间部分轧制液流量尽量减小,增大正弯辊B、单边浪特征:带钢一边呈可见波浪状原因:有浪一边轧制力过大,轧辊温度不均,工作辊水平未调好,来料厚度不均(楔形)措施:通过压下双摆,将有浪一边轧制力减小,严格要求原料同板厚差不超规定,头尾有镰刀弯在酸洗一定.要剪掉C、中间浪特征:带钢中部呈可见波浪状原因:与双边浪相反措施:与双边浪相反D、二肋浪特征:带钢沿宽度方向1/4、3/4处或部分区域呈可见波浪状原因:轧制温度不均,局部过热与浪相对应的轧辊冷却液喷嘴堵塞措施:加大二肋浪部位的轧制液流量,认真检查二肋浪部位喷嘴是否堵塞八、厚度不均或不合特征:带钢沿轧制方向厚度波动变化超出产品要求或轧制成品厚度与产品要求厚度不符原因:1、热轧原料本身厚度不均,材质硬度不均2、AGC系统没有投入时,压下及速度调节不及时3、各机架张力波动范围过大4、测厚仪(特别是最后机架)不准措施:1、确保热轧原料厚度精度,对严重超厚或超薄部分应切除,轧制中发现原料厚度波动,应及时降速,待调节好后再升速,当厚度波动严重时,要停机,然后按实际厚度进行手设定计算,再启动设备进行轧制2、AGC系统没有投入使用时,随速度的变化及时调节轧制力和张力,保证厚度精度正常3、严格保证系统的张力稳定4、定期检查测厚仪的精度,轧制时如发现异常状况,及时检查、核对成品实物厚度与测厚仪显示的一致性,否则立即通知计控人员进行处理九、卷形A、溢出边特征:钢卷边部局部不齐原因:酸洗来料溢出边,热轧板形较差,卷取张力过小及波动,轧制压力不稳定,入口无跑偏控制装置措施:发现原料溢出边严重时,人工首先降速,及时采取手动对中调节,严格控制好板形,对带头板形不好的部分,应切除,严格控制卷取张力,确保压下稳定正常,尽快使人工跑偏控制装置投入使用,一旦出现严重溢边,在最后机架分卷B、塔形特征:钢卷边部呈弧形状原因:酸洗卷塔形,带钢头部板形不良或卷心有废带头,卷取张力过小,卷心与卷取机卷筒之间有窜动,各架侧倒板间隙过大等因素,均可造成卷取时钢卷塔形措施:轧制酸洗塔形卷时速度不能高,人工随时进行对中调节,当实在无法纠偏时,最后机架轧钢工根据情况进行分卷,严格控制好穿带头部倒板,当带头板形不好时,应及时切除,废带头一定不能卷入卷心,确保卷取张力正常,满足工艺制度的要求,无论在何种情况下,发现塔型应立即分卷C、心形卷特征:钢卷内径局部下凹原因:带卷头部卷取张力过小,轧制规格薄措施:提高头部卷取张力,一般应大于设定张力20~30%,适当增大带头厚度,必要时更换小直径卷筒D、抽心卸卷时,卷取机卷筒将卷心部分带出,或是热处理吊车在掉卷时,将卷心部分吊起,无法将钢卷吊走特征:钢卷内径局部溢出原因:带钢头部板形不好,卷心卷取张力过小,卷取机卷筒位移或钢卷小车上塑料垫磨损不均,造成钢卷中心与卷筒中心不一致措施:确保带钢头部板形良好,特别是废带头不要卷入内径,手动方式加大头部卷取张力,将偏移的卷取机复位,同时更换已磨损的钢卷小车塑料垫块,经常检查吊具的表面状况及磨损程度E、塌卷特征:钢卷卧放时呈椭圆状原因:在整个轧制过程中,卷取张力都小于设定张力,卸卷以后便暴露,尤其以薄规格产品为明显,经吊车吊运后会发生卷内孔径全塌,厚规格产品,经退火后平整机上料时暴露出来措施:在张力调节系统或张力设定不正常时,要通过手动操作方式,将卷取张力升高,以保证带钢头部及整卷的卷取张力符合工艺的要求,避免质量和安全事故的发生冷轧带钢的质量指标中,带钢的尺寸偏差、板形以及表面粗糙度等要求是很主要的项目,消除产品在这些方面的缺陷是冷轧生产中质量提高的关键之一。
冷轧机常见板型控制问题分析与处理

图1
同样我们也通过修改Lubrication level参数来改变冷却控制的效果。
当然也可以通过增加固定部分流量来增加总的流量,从而将高热合金轧制时产生的高热量带走。
0~20%是ABB工程师在现场调试时设定的值,此参数经过现场验证可以给到30%甚至40%,不过问题也是一样,将参数设定大了以后会降低冷却控制的效果,这也是一对矛盾。
我们现场观察流量设定不宜超过75%,如果轧制热量太高,需要从轧制工艺去考虑,比如减小压下量或降低速度。
因为冷却的能力或者冷却对板形调整的能力满足不了原来的轧制工艺。
在实际生产中发现润滑等级的值调到40%以上B列就处于全喷的状态,这样的情况对于轧制热凸度的控制较好,但是对板型的控制能力又会不足。
因此这个一般不进行设定。
这个设定是指从冷却中拿出一部分出来当润滑用,在生产过程中我们冷却一般都能力不足,本来的冷却量就不大,不需要再从冷却当中分出来给润滑。
因此此参数一般设定为零。
2.在线和离线板型不一致的问题
带材轧制过程中的实时板型通过板型仪的操作画面可以直观的进行观察,但是往往会出现我们在轧制过程中板型仪画面显示的带材实时板型很好,轧制完毕在下游工序进行生产时却会发现带材的实际板型和实时的在线显示的
YAN JIU。
冷轧带钢产品板形质量缺陷的分析与控制

130管理及其他M anagement and other冷轧带钢产品板形质量缺陷的分析与控制刘 涛(邯钢品质部用户服务中心,河北 邯郸 056000)摘 要:在冷轧产品中,板形质量缺陷是比较显著,也是客户反映比较多的质量问题。
冷轧带钢常见的板形缺陷有褶皱、浪行、瓢曲等,其缺陷问题的产生与加工原料、轧制过程等都有密切的关系。
通过对缺陷产生原因的分析和对生产工艺的调整可以有效消除上述质量缺陷问题,提高客户对产品质量的满意度。
关键词:冷轧带钢;板形质量;缺陷问题;控制中图分类号:TG334.9 文献标识码:A 文章编号:11-5004(2021)12-0130-2收稿日期:2021-06作者简介:刘涛,男,生于1980年,宁夏中宁人,本科,研究方向:于冷轧产品的研发及售后。
随着我国加工制造业的快速发展,市场上对于各种规格高品质带钢产品的需求量越来越大。
冷轧板带及汽车板、家电板等深加工产品已成为钢铁企业当前主要的利润增长点,各钢铁企业围绕提高冷轧产品质量开展了一系列的技术研发和质量改进,以满足市场客户不断提高的要求。
冷轧带钢产品生产工序较多、工艺控制复杂、质量影响因素较多,任何一个环节出现问题都有可能导致产品的质量缺陷。
在冷轧产品中,板形质量缺陷是比较显著,也是客户反映比较多的质量问题。
冷轧带钢常见的板形缺陷有褶皱、浪行、瓢曲等,其缺陷问题的产生与加工原料、轧制过程等都有密切的关系。
通过对缺陷产生原因的分析和对生产工艺的调整可以有效消除上述质量缺陷问题,提高客户对产品质量的满意度。
本文对此进行了探讨。
1 冷轧带钢的板形控制冷轧是常温条件下,利用冷轧机按照一定的规格尺寸对钢板、热轧带钢等进行的轧制加工。
因此,作为一种物理式的加工方式,带钢的板形质量缺陷主要来自于轧件的机械性能,以及轧制加工的各项参数。
冷轧生产中由于各种原因造成的板带横断面形状和平直度不良问题,均可归结为带钢的板形缺陷。
板带横断面形状是指宽度方向上板带厚度的分布规律,由于冷轧时压扁变形远小于轧辊弯曲挠度,因此对于带钢横断面形状通常以凸度作为其描述特征和控制对象;平直度主要是指带钢翘曲,包括板带各种浪形,在轧制时应尽量排除。
铝轧机板形等质量问题分析及采取措施

铝轧机板形等质量问题分析及采取措施一、板形不良.1、冷轧机:(1)每三个月由钳工检查一次喷杆梁的减振喉是否损坏.及时更换(2)每两个月由操作手和电工一起检查喷嘴是否有堵塞或者在轧制时,操作手发现板形明显不良或者喷嘴喷油异常时,马上对喷嘴进行测试检查.(3)针对不同宽度,不同厚度,操作手及质检作好记录,并及时通知设备部进行一起分析,是否需要对板形目标曲线进行更改及试验(不同的板形目标曲线会对喷淋产生一定的影响). (4) 有些薄板,建议操作手可以进行手动喷淋干预,总结分析板形不良原因.(5)所有辊系检测每季度一次,由技术组完成,水平度及平行度。
2、粗轧机:(1)建议要求厂家增加手动调节喷淋功能(因为粗轧机不能对局部喷油进行手动干预,其不良板形只能通过弯辊,倾斜等手段进行辊型控制).(2)定期检查压平辊平行及水平度.1次/季度。
(3)每两个月由操作手和电工一起检查喷嘴是否有堵塞或者在轧制时,操作手发现板形明显不良或者喷嘴喷油异常时,马上对喷嘴进行测试检查.(4)工艺道次合理安排,张力合理使用,轧辊凸度建议尝试支承辊凸度0.02mm;工作辊凸度0.05-0.07mm.3、精轧机:(1)定期检查喷杆梁喷嘴.(2)定期检查压平辊平行及水平度.1次/季度(3)喷射梁及板型仪备品备件要尽快订货,因为膜片及滤芯都是消耗品需定期更换。
(4)工艺道次合理安排,张力合理使用,轧辊凸度建议尝试支承辊凸度0.02mm;工作辊凸度0.05-0.07mm.针对以上情况,将对三台轧机定期作以下的检查和测试:(1)定期对入口张紧辊进行检查辊系.(2)定期对板形辊平行度,水平度进行检查.(3)定期对工作辊辊隙进行检查.(4)定期对轧制线进行检查.(5)对薄板的局部板形不良,操作手是否可以采用手动调节喷淋,对相同的铝卷进行持续跟踪和比较.二、打底印.1、目前对部分变形的套筒进行车削,保证套筒的外圆一致。
2. 生产要加强套筒管理严格区分退火用套筒和非退火用套筒,决不能混用3、合理使用张力速度,匹配要合理.三、铝粉堆积1、入口可增加板面清洗装置.2,加强板式过滤器维护,确保过滤能力满足生产需求3,定期换纸,严格执行硅藻土及白土纤维素的添加工艺,搅拌箱内不能吸空4,每班要对轧制油透光率进行检测设备部2017-4-18。
铝薄板轧制中的板形控制

图 1 正弦波弯 曲
2 板形仪测量原理 . 2
△L 作为 板形 测量值 . 儿 假定 渡形 为正 弦波 , 其长 度差 与波高 破 长的关系式 为 :
现 代轧机生产板带材采用张力轧制 ,板带材横截
面上的单位张力不相等。这种张力差 . 虽然产生的原 因 很 多 ,但在很大程度上能明显表现 出板带材的板形好 出板 带材在线板形质 的变化 。板形仪是在生 产线 上测 量带 有张力的板带材 的板形 ,这种板形 与离线去掉 张 力 的板片还 是有一定差别 的。 英 国R Y A E C N公 司生产的空气支承式板形仪 是 由 很多测量辊 组成 , 每辊宽度为 7 r, 图 2 5Tl如 Il l 所示 , 测量 辊 受 的径 向 压 力 为 :
材内部的应力 。根据虎克定律 :
L
=
() 3
式中 : 一应力变量 ;—杨 氏横量 ( △ E 弹性模数 ) 。 如果能测量 出板带材横 向上的应 力变化 ( 也就是
潜在的板形 ) 我们就能确定 △ , , 板形的结果就可 以 显示 出来 。板形 仪是根据测量板材横 向应力 的原理 而 制成。 板带材经过板形辊 , 因板带材板形不够 良好 , 引起 板带材 内部张力不一致 , 对于板形 辊产 生不 同压力 , 该辊 就产 生压 力信号 , 这些压力信号可 能转换 成 0 5 -V 电压或 0 5 - V的模拟信号。 () 6 手动控制 系统 , 形 自动控制 中还备有 手动 板
姜 树 春
JANG h —c u I Su h n
( 北 铝 加 工厂 。 肃 陇西 西 甘
78 1 】 4 1 1
摘要 : 介绍铝薄板轧制中如何控制板形 . 用板形仪测量出板形误差 , 并送 到计算机数据库 . 由计 算机给 出指令进行调整
轧制缺陷及质量控制
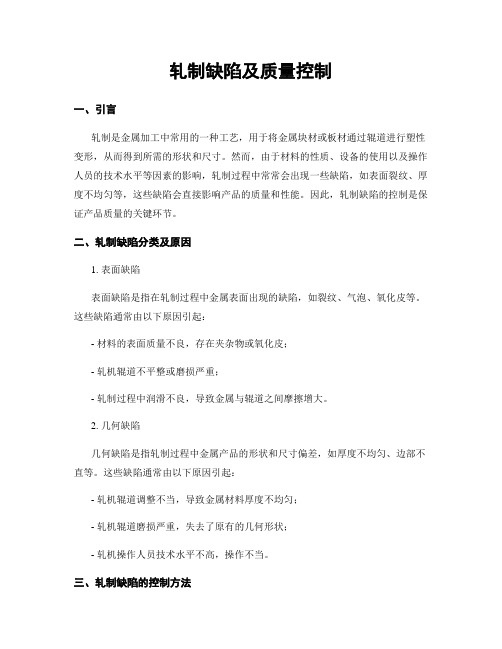
轧制缺陷及质量控制一、引言轧制是金属加工中常用的一种工艺,用于将金属块材或板材通过辊道进行塑性变形,从而得到所需的形状和尺寸。
然而,由于材料的性质、设备的使用以及操作人员的技术水平等因素的影响,轧制过程中常常会出现一些缺陷,如表面裂纹、厚度不均匀等,这些缺陷会直接影响产品的质量和性能。
因此,轧制缺陷的控制是保证产品质量的关键环节。
二、轧制缺陷分类及原因1. 表面缺陷表面缺陷是指在轧制过程中金属表面出现的缺陷,如裂纹、气泡、氧化皮等。
这些缺陷通常由以下原因引起:- 材料的表面质量不良,存在夹杂物或氧化皮;- 轧机辊道不平整或磨损严重;- 轧制过程中润滑不良,导致金属与辊道之间摩擦增大。
2. 几何缺陷几何缺陷是指轧制过程中金属产品的形状和尺寸偏差,如厚度不均匀、边部不直等。
这些缺陷通常由以下原因引起:- 轧机辊道调整不当,导致金属材料厚度不均匀;- 轧机辊道磨损严重,失去了原有的几何形状;- 轧机操作人员技术水平不高,操作不当。
三、轧制缺陷的控制方法为了控制轧制过程中的缺陷,提高产品的质量和性能,可以采取以下措施:1. 材料预处理在轧制之前,对原材料进行预处理是非常重要的。
首先,对材料的表面进行清洁,去除氧化皮和夹杂物。
其次,对材料进行退火处理,以提高其塑性和可加工性。
最后,对材料进行表面润滑处理,减少与辊道的摩擦。
2. 轧机设备维护保持轧机设备的良好状态对于控制缺陷至关重要。
定期检查和维护轧机辊道,确保其平整度和几何形状的精确性。
同时,及时更换磨损严重的辊道,以保证轧制过程的稳定性和一致性。
3. 润滑控制在轧制过程中,适当的润滑是减少摩擦、防止表面缺陷的关键。
选择合适的润滑剂,并确保润滑剂的供应充足、均匀。
同时,及时清洗辊道和润滑系统,避免杂质对产品质量的影响。
4. 操作人员培训轧制过程需要经验丰富的操作人员进行操作和监控。
因此,对轧机操作人员进行培训,提高其技术水平和操作规范性是非常重要的。
操作人员应熟悉轧机设备的使用方法和调整技巧,能够及时发现和解决轧制过程中的问题。
板形缺陷及预防措施
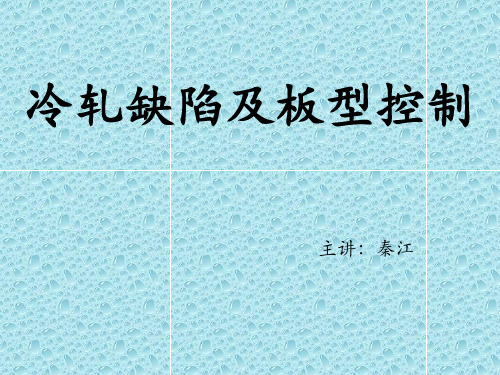
原因:带卷头部卷取张力过小,轧制规格薄。
措施:提高头部卷取张力,一般应大于设定张力20~30%, 适当增大带头厚度,必要时更换小直径卷筒。
4.抽心 卸卷时,卷取机卷筒将卷心部分带出,或是热处理吊车在 掉卷时,将卷心部分吊起,无法将钢卷吊走
特征:钢卷内径局部溢出
原因:带钢头部板形不好,卷心卷取张力过小,卷取机卷 筒位移或钢卷小车上塑料垫磨损不均,造成钢卷中心与卷 筒中心不一致
3.金属碎末压入
带钢表面粘附着金属碎末,无规则,有大有小,有块状、 也有条状,压入深度亦有深浅之别。
产生原因:轧辊表面不干净或金属碎末(如铁屑、钢丝等) 落于带钢表面轧入,金属碎末轧入一般也只存在表面,有 时可用小刀清除掉,甚至将带钢轻轻弯曲就可掉落。
4.辊印
带钢表面呈凸起或凹陷的印痕, 但没有明显的凸凹感觉,印痕部 位较亮。
产生原因:轧机的导卫装置安装不正确,或导板等粗糙不 平,有凸起的锐边。另外,在轧制、卷取中,带钢与异物 摩擦也可引起划痕。
措施:1、定期检查辅助传动辊是否转动灵活及表面状况 2、固定辅助设备与带钢应保持一定间隔 3、及时检查、清除生产线设备中的异物 4、发现带钢表面有划伤,应从后向前逐个检查,
查出事故原因后,根据情况采取办法给予处理。
复合浪是在板中部和边部同时出现浪形缺陷。
复合浪形成的主要原因: 1.轧制吨位过大,磨损不均匀 ; 2.没有预热轧辊,轧辊局部冷却不好。
(二)控制板型缺陷的主要措施
1.选择合适的轧辊凸度值
带钢在轧后其横断面上的厚度形状是由轧 辊实际辊缝的形状所决定的。如果轧辊是平辊, 在轧制力作用下,轧辊产生弹性变形,使轧件 通过轧辊时的实际辊缝呈现中间开口度大,而 两边开口度小的辊型,这种辊缝轧出的带钢, 横断面必是中间厚,两边薄。为克服此种缺陷, 轧辊原始辊型应具有一定的凸度。
轧制缺陷及质量控制

轧制缺陷及质量控制一、引言轧制是金属加工过程中的重要环节,对于金属产品的质量和性能具有重要影响。
轧制缺陷是指在轧制过程中产生的各种不良现象,如裂纹、夹杂物、不均匀变形等。
为了保证轧制产品的质量,需要进行有效的质量控制和缺陷检测。
本文将详细介绍轧制缺陷的分类、检测方法以及质量控制措施。
二、轧制缺陷的分类1. 表面缺陷:包括划痕、氧化皮、凹陷等。
2. 内部缺陷:包括夹杂物、气泡、裂纹等。
3. 形状缺陷:包括厚度不均匀、宽度不均匀、边缘不平整等。
三、轧制缺陷的检测方法1. 目视检测:通过人眼观察轧制产品的表面和断面,判断是否存在明显的缺陷。
2. 磁粉检测:利用磁性粉末吸附在轧制产品表面的磁性缺陷上,通过观察磁粉的分布情况来判断是否存在缺陷。
3. 超声波检测:利用超声波的传播特性,通过检测超声波的反射和传播时间来判断轧制产品内部是否存在缺陷。
4. X射线检测:利用X射线的穿透性,通过观察X射线照片来判断轧制产品内部是否存在缺陷。
5. 红外热像检测:利用红外热像仪记录轧制产品表面的热分布情况,通过观察热图来判断是否存在缺陷。
四、轧制缺陷的质量控制措施1. 原材料控制:选择质量良好的原材料,确保原材料的化学成份和物理性能符合要求。
2. 轧制工艺控制:合理控制轧制温度、轧制速度和轧制压力,避免轧制过程中的过热和过冷现象。
3. 设备维护控制:定期对轧机设备进行检修和维护,确保设备的正常运行和精确度。
4. 操作工艺控制:培训操作人员,提高其对轧制工艺的理解和操作技能,减少人为操作引起的缺陷。
5. 缺陷修复控制:对于轧制产品中的一些小缺陷,可以采取修复措施,如打磨、热处理等,以提高产品的外观和性能。
五、案例分析以某钢厂的冷轧钢板生产线为例,该生产线采用磁粉检测和超声波检测相结合的方式进行轧制缺陷的检测。
经过对轧制产品的检测分析,发现存在少量的夹杂物和裂纹缺陷。
针对这些缺陷,钢厂采取了以下措施:首先,加强原材料的筛选和质量控制,确保原材料的纯净度和均匀性;其次,优化轧制工艺参数,减少轧制过程中的应力和变形;最后,对于存在的缺陷,进行修复处理,并进行再次检测,确保产品的质量符合要求。
- 1、下载文档前请自行甄别文档内容的完整性,平台不提供额外的编辑、内容补充、找答案等附加服务。
- 2、"仅部分预览"的文档,不可在线预览部分如存在完整性等问题,可反馈申请退款(可完整预览的文档不适用该条件!)。
- 3、如文档侵犯您的权益,请联系客服反馈,我们会尽快为您处理(人工客服工作时间:9:00-18:30)。
铝冷轧机边部板形缺陷的控制
加拿大赫氏工业自动化服务有限公司马建军
随着最终用户对产品质量越来越严格的要求,国内的铝板带生产厂家也越来越严格的关注板形,对产品的在线和离线板形都提出了严格的要求。
以国内某厂家的2300姗的六辊轧机为例,对于在线板形的偏差已经要求达到小于+/一6 I单位的要求,同时对于在其后部拉矫机工序上,也要求产品的离线板形没有出现可以观察到的板形缺陷。
对于目前的板形控制,一般是首先通过轧机出口侧的板形测量辊测量得到沿带坯宽度方向上的张力分布曲线,然后将得到的曲线与预先设定的板形目标曲线进行比较,并将得到的偏差值进行解析。
偏差解析时~般按以下三类进行:直线板形偏差、对称板形偏差、无规律板形偏差,并分别采取工作辊倾斜、工作辊弯辊和调节对应区域的喷淋流量进行控制。
以上三种板形控制方式对于大多数的冷轧机工况基本上可以满足板形控制的要求,但是对于由于工作辊二侧和轧辊中心轧制区域温度不同,而造成的轧辊热凸度引起的边部板形缺陷(俗称“紧边’’),则很难得到理想的控制。
本文针对高速轧机(轧制速度在1000m/min.以上)、在轧制厚度小于1.0姗的产品时经常出现的“紧边”现象进行分析,并探讨不同的解决办法,以及其效果和优、缺点。
1.“紧边"缺陷的成因:
对于铝冷轧机,在正常轧制过程中,由于材料压缩形变和摩擦会造大量的轧制热,这些轧制热中的一部分被离开的带坯以及轧制冷却油带走,但是大部分热量会传递给上、下工作辊,并造成工作辊的温度的升高。
图1所示即是轧辊和带坯间热量的传递示意图。
图1轧制过程中轧辊区域热量图
但是由于工作辊的边部二侧是轧机牌坊的侧向开口,二侧和空气会有大量的对流换热冷却,散热条件明显比轧辊的中间区域好,因此经过~段时间的轧制后,工作辊中心区域的辊面温度要明显高于二侧的辊面温度,从而造成轧辊的热凸度,如图2所示。
轧辊热凸发(mm)
沿辊丽距离(mm)
图2沿轧辊辊面的典型热凸度分布曲线
对于目前的高速轧机,如果轧制速度高于1000m/min.,带材的厚度小于
1.0mm,在正常轧制后,工作辊中间的温度大约高于二侧温度5’10oC,特别是在轧制带材的边部,正好处于处于无料区交界处,在无料区轧辊无从得到轧制变形热和摩擦热,同时由于工作辊高速旋转带来的空气却通过对流的作用带走大量的热,这样的状况会造成沿工作辊辊面轴向的温度和直径尺寸造成差异,这也就是我们所说的轧辊热凸度。
在轧辊二侧的带材边缘区域,工作辊由于温降快,温度低,轧辊直径膨胀小,造成此区域的实际有载辊缝加大,因而此区域的带材出口厚度变厚,形成俗称的“紧边”,操作工如果观察带材的上表面,可以看到有一个明显的色差条。
“紧边’’的宽度一般发生在距离带材边部’15胁的范围区域,从上述成因分析可以看出,一旦形成“紧边”后,该区域带材厚度增加,造成铝金属的“聚集”。
但是,对于冷轧而言,由于在该温度下,铝金属难以发生延展,因此,该区域的“聚集”
74
的金属相对于相邻的区域形成一种“外端拉应力”,造成该相邻区域的带材被拉薄变松,操作工一般俗称“肋浪”,因此“紧边”发生后,和“紧边”区域相邻的区域也一般会出现变松的“肋浪’’,造成板形缺陷更难以纠正。
2.搿紧边乃缺陷的检测由于边部“紧边"只是发生在距离带材边部“15姗的位置上,而对于目前常用的
各类板形测量辊,其检测环的宽度一般是52啪,这样即便发生了“紧边",在15舳宽条上出现了对板形辊检测环压力的明显增高,但是由于其分布的宽度只是相当于检测环宽度的20%’30%,对整个环面宽度52咖上压力的影响不是很明显,因此,对于边部配置52咖检测环的板形测量辊,一般很难检测到“紧边”情况的发生。
如果希望板形辊能自动检测带材边部是否出现了“紧边”,在带材最窄宽度到最宽宽度之间的板形辊,应配置为26咖宽的检测环,这样,才可以检测到边部的“紧边”。
3.“紧边弦的控制方法和优缺点比较
根据“紧边"的成因,如有要想进行有效的控制,就需要减少带材边部由于工作辊直径热凸度减少而造成的有载辊缝相对变大的问题,对应的控制方法有二类,一种是加大工作辊的负弯,用负弯辊减少带材边部出现的过大的有载辊缝;另外一种是加大工作辊在带材边部的热凸度,使得工作辊在该区域的辊直径变大,从而消除“紧边”现象。
利用加大工作辊负弯来消除“紧边”,不需要增加额外的控制执行机构,只需要利用原有的弯辊液压缸即可以完成。
但是,利用工作的负弯来消除“紧边’’同时会带来以下二个方面的问题:一是在加大工作辊负弯的同时,由于工作辊辊径一般较小,在辊的二端作用负弯辊力时,同时会使靠近带材边部的二肋区域的工作辊向上翘起,这样一来,又会使得肋部的有载辊缝发生改变;二是考虑对工作辊寿命的的影响,加大负弯本身会造成对工作辊使用寿命的影响,因此一些厂家在使用负弯时,都不希望用到很大的负弯力。
利用向外推延轧辊的热凸度来消除“紧边”是目前常用的手段,向外推延工作辊边部热凸度的方式也有二种,一种是采用是热的轧制油进行带材边部附近工作辊的热喷淋,来增加轧辊的热凸度,使得轧辊的热凸度曲线向外延伸,覆盖整个带材宽度,这样使得带材边部的有载辊缝和其他区域相一致,消除“紧边”。
其原理如下3所示。
轧辊热凸度(mm)
徽一梦觥
图4边部油热喷系统组成
热油喷嘴布置在工作辊的二端的冷却喷射梁的上部,一般是从所轧制带材的最窄宽度开始布置,直到布置到每侧带材最大宽度以外再增加二个喷嘴的位置。
热油喷嘴块的间距要与对应区域所选择的板形辊的辊环宽度相匹配,如果边部的板型辊的辊环宽度是26mm,那么热油喷嘴的间距也应为26mm。
热油喷嘴的控制同样也是采用脉冲时间对单位时间内喷出的热油总量进行控制。
油加热和循环系统,目前有电阻直接加热和水乙二醇间接加热二种方式。
使用电阻棒对轧制油直接进行加热时,在电阻棒和轧制油的界面,容易形成碳黑沉积,
一旦形成后会阻止热量的传递,长期使用加热效率会降低;同时考虑到轧制油的燃
76
点温度,加热温度从安全考虑不会太高,目前使用的直接油加热系统的热油温度一般为’85℃。
另外的一种加热方式是采用电阻棒先直接加热水乙二醇,同时为了防止水乙二醇的沸腾,在水乙二醇储液罐的顶部加高压氮气进行密封,在这样的条件下,先将水乙二醇加热到大约130度,然后通过一个一次管式热交换器,进行换热,将轧制油加热到’98oC,换热器的换热量可以通过安装在水乙二醇管路上的电控阀和安装在热油管路上的温度传感器实现闭环控制,这样可以保证喷出了热油达到要求的。
98 oC。
同时,该系统还考虑在不需要热喷情况下,热油本身热量的循环利用,在不进行热喷时,轧机二侧的热油管路中的热油通过一个旁通系统相连接,然后进入另外一个二次管式换热器,在二次管式换热器中,不需要使用的热油将本身的热量换热给即将进入一次换热器的冷油,这样冷油在被二次加热后再被水乙二醇进行一次加热,而排到污油箱中的油也不会因为太高的温度而影响冷却油的温度。
图5即为国内某厂常用的带有循环换热的油间接加热和循环系统设备图。
图5带有循环预热的间接油加热和循环系统
在控制方面,如果没有配置26咖分区板形测量辊,一般是依靠操作工的观察,在出现“紧边”的情况下,手动打开和关闭热喷系统。
对于加热功率为500Kw的油热喷系统,在2分钟内可以对薄规格的带材边部板
形进行25I单位的改变,图6即为油热喷系统在国外某厂的应用实例,从图中可以看出在打开油热喷后,边部的张力测量值在很短的时间内降低到正常水平。
nq-,·。
¨c西uEⅡt_¨r曙u5碍x-Mq庀pIE5日l口田c■EnlIa no●田口E砷●z驴
图6边部油热喷改善“紧边”效果
5.边部电感应加热和边部热油喷相比,采用边部电感应加热,也可以同样起到对工作辊边部进行
加热,从而将轧辊热凸度推移到整个带材宽度范围,消除“紧边”现象。
电感应加热使用电感应线圈对工作辊的表面进行感应加热,电感应线圈布置在
工作辊的二侧,而且随着所轧制的带材,从最窄的带材宽度到最宽的带材宽度之间进行游走定位。
电感应线圈块距离工作辊表面的距离一般在5m左右,并且有开进和退出机构。
工作辊每次磨辊后,电感应线圈块在液压控制机构的带动下,会先和工作辊表面进行轻压靠,随后开出5姗进行定位;在宽度方向上一般开到轧制带材边缘外端10nun的位置。
在轧机进行换辊前,电感应块会在液压控制机构的带动下会全部缩回,不影响换辊。
图7为国内某厂常用的工作辊感应加热头和控制器。
图7国内某厂使用的工作辊电感应加热头和控制器
相对热油喷方式,电感应加热使用的电功率较低,系统占地面积小,效果显著。
以国内某厂安装的边部电感应边部加热器,每侧使用6KW的电感应线圈,在2分钟内,对板形的控制效果可以达到大约15I单位,图7即为该厂使用边部电感应加热器后,关闭和打开情况下对边部“紧边”的改善效果:
78
图8采用电感应加热控制“紧边”的效果
6.结论
本文分析了板带冷轧机在高速轧制时由于工作辊热凸度而造成的边部板形缺陷一“紧边”,分析了其形成的原因、检测方法、以及消除“紧边”的二大类策略一工作辊负弯和推延工作辊热凸度,随后分析了这二大类解决策略的优、缺点,并针对边部热油喷和电感应加热二种技术的原理和使用效果进行论述。
参考文献1.秦官林,卢文平.铝带冷轧机板型控制中的一种热喷淋技术介绍[J].科技风,2012,(6):9
2.张俊芳,李卫国,董春阳,张洁.,冷轧机热喷系统原理机构及应用[J].,有色金属加工,2013,(2):44—46。