冷轧带钢主要板形缺陷
冷轧带钢浪形缺陷的成因和解决措施
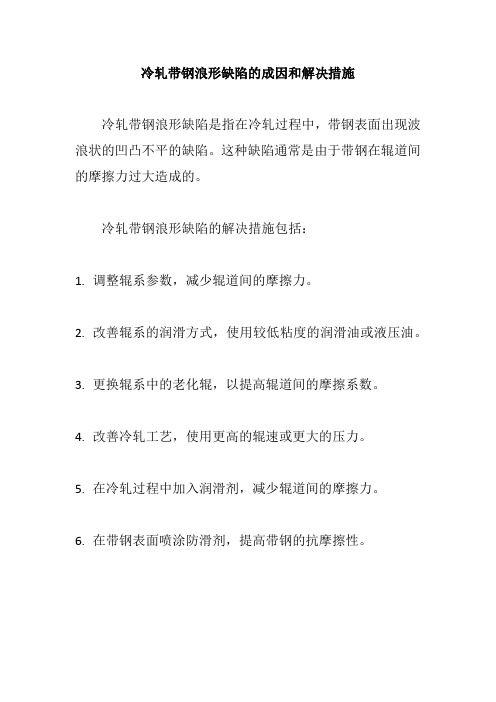
冷轧带钢浪形缺陷的成因和解决措施
冷轧带钢浪形缺陷是指在冷轧过程中,带钢表面出现波浪状的凹凸不平的缺陷。
这种缺陷通常是由于带钢在辊道间的摩擦力过大造成的。
冷轧带钢浪形缺陷的解决措施包括:
1.调整辊系参数,减少辊道间的摩擦力。
2.改善辊系的润滑方式,使用较低粘度的润滑油或液压油。
3.更换辊系中的老化辊,以提高辊道间的摩擦系数。
4.改善冷轧工艺,使用更高的辊速或更大的压力。
5.在冷轧过程中加入润滑剂,减少辊道间的摩擦力。
6.在带钢表面喷涂防滑剂,提高带钢的抗摩擦性。
冷轧缺陷图谱

精心整理目录冷轧卷缺陷辊印 (2)粘结 (3)咯伤 (4)边裂 (5)平整纹 (7)划伤 (8)05011.图例2.陷;②平整辊印与轧机辊印的区分:平整辊印伤疤处无粗糙度且发亮;轧机辊印伤疤处发暗,有一定的粗糙度。
3.产生原因及危害①轧钢辊表面受损;②轧辊表面粘有异物;③退火过程产生氧化皮后,脱落粘附在平整机轧辊上,平整时产生;④生产过程中其它辊面受损。
危害:①外观不良,加工(冲压)时易发生破裂;②影响镀层效果。
4.5.05021.图例2.②一般粘结分三种:月牙状、折皱状、以及牡丹花状,一般存在于罩式炉的生产中才会产生此缺陷3.产生原因及危害①板形不良②轧机卷取张力过大③退火冷却速度过快④退火前钢卷边部受冲击危害:外观不良,加工(冲压)时易发生破裂4.预防及消除方法①保证前工序板形良好;②退火工艺周期的适当调整;轧机的卷取张力的调整,以及根据轧钢过程中材质和5.05031.图例2.3.①生产过程中各辊上粘有凸起的异物引起;②钢卷摆放位置有异物,导致产生;③小车压痕;④行车吊钩撞击后产生对产品的影响。
危害:①外观不良,镀层后更加明显;②制造用面板无法使用。
4.预防及消除方法①生产过程中对辊面的检查,发现不良及时处理;②钢卷应搬运在适当的优越位置(放置位置环境良好);③对操作工教育,提高操作水平;5.05041.图例2.3.③在酸洗过程中,带钢跑偏或浪形严重导致边部与设备摩擦,边部间断轻折边,经冷轧后边部形成锯齿状;④带钢成分异常;危害:①对产品的外观有直接的影响;②边部无法镀层。
③后道工序生产过程中可能导致断带事故。
4.预防及消除方法①吊运的时候防止撞伤;②酸洗过程中,对中装置适当的调整避免跑偏事故;③严格控制带钢成分及原料卷形、板形缺陷。
5.05051.图例2.3.危害:①对产品的外观有直接的影响;②产品要冲压或深加工时很容易造成开裂。
4.预防及消除方法①应保持轧钢及平整压下量的均衡;②需保持工作辊的适当弯曲度及钢带的对中;③在酸洗过程中对钢带厚度实测,确认热轧的厚度是否均匀。
冷轧钢带表面缺陷的成因分析及预防措施
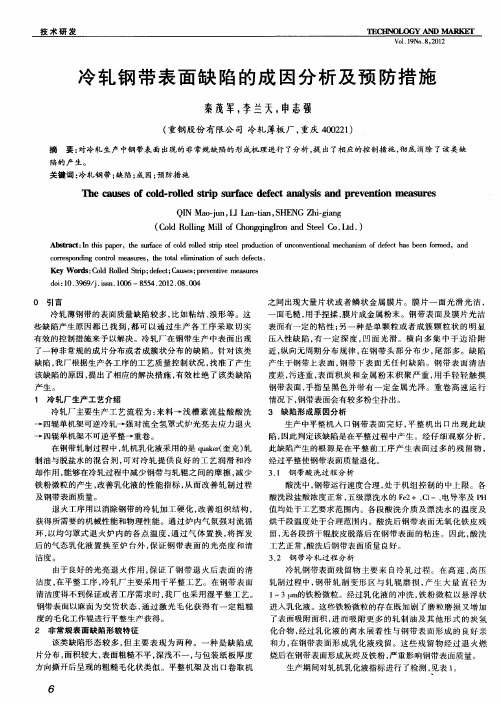
此缺 陷产生 的根 源是在平 整前 工序 产生表 面过 多 的残 留物 , 经过平整使钢带表 面质量退化 。
3 1 钢 带 酸 洗 过 程 分 析 .
制油与脱盐水 的混合剂 , 对冷轧 提供 良好 的工艺 润滑 和冷 可
却作用 , 能够在冷轧过程 中减少钢带 与轧辊之 间的摩擦 , 减少
该类缺陷形态 较多 , 主要 表现 为两种 。一种 是缺 陷成 但
片分布 , 面积较大 , 表面粗糙不平 , 深浅不 一 , 与包装纸 板厚度 方向撕 开后呈现 的粗糙 毛化 状类似 。平整机架 及 出 口卷取机
6
技 术 与 市 场
第 1 卷 第 8 21 年 9 期 02
技 术 研 发
1 冷 轧 厂 生产 工 艺 介 绍
冷轧厂主要生产工 艺流程 为 : 来料 一浅 槽紊 流盐 酸酸 洗
一 四辊 单 机 架 可 逆 冷 轧 一 强 对 流 全 氢 罩 式 炉 光 亮 去 应 力 退 火 一 四辊 单 机 架 不 可 逆 平 整 一 重 卷 。 在 钢 带 轧 制 过 程 中 , 机 乳 化 液 采 用 的 是 qae( 克 ) 轧 ukr奎 轧
表 1 轧 机 乳 化液 成 分 指 标 检 测 情 况
『 标 名 称 皂 化值 指 氯 离子 电 导 率 总铁 含 量 浓度 单 位 P H值 E. . SI
mg KOH/ g mg L / u / m sc mg L / %
常关键 的。比如用 于控制氢气流量 的炉 台氢气 管道重 锤阀能 及 时对乳化液挥 发后 炉 内压 力增 大到设定 值 而报警 泄压 , 使 新鲜氢气通过重锤 阀进入炉 内及 时置换炉 内氢气 和挥发 的乳 化液混合气氛 , 到达及时排除乳化液 的 目的。 因此 , 要求 重点 对退火过程 中氢 气介 质用量 重点监 护 , 每个退 火周期 的氢气 用消耗量必须控 制在 10—20m 9 0 3范围 内, 使退 火气 氛正 常 ,
冷轧薄带的时候出现的问题

冷轧薄带过程中可能出现的问题及其原因和解决方案可以包括以下方面:1. 厚度问题:厚度超差,这类问题出现的原因可能是轧辊磨损导致轧制压力分布不均匀,或是设备精度不够,导致轧制时张拉力不稳定。
解决方案包括定期更换轧辊,维护和检修设备以提高精度,或是采用高精度的人工修磨方式来保证张拉力的稳定性。
2. 板型问题:如波浪弯、镰刀弯、瓢曲度等板型问题,可能是由于轧机设计不科学、轧制力波动大、原料板形不好等原因导致的。
解决办法包括优化轧机设计,提高设备稳定性,以及使用合理的原料和工艺手段,同时加强带钢表面的检查和修磨工作。
3. 表面质量问题:冷轧带钢的表面质量不佳,可能是由于轧机调整中凸度过大、板形控制不当、来料表面缺陷较多等原因导致的。
解决方法包括调整凸度以控制带钢平直度,适当调整压下量、退火温度等因素以改善带钢表面质量,或是定期对表面检查和修磨设备进行维护。
4. 尺寸精度问题:冷轧薄带的尺寸精度问题可能是由于设备精度不够、操作不当、原料问题等原因导致的。
解决办法包括提高设备精度,优化操作工艺,选择合适的原料和处理方式等。
5. 生产效率问题:冷轧薄带的生产效率低下,可能是由于设备故障、操作不当、原料问题等原因导致的。
解决办法包括定期维护和检修设备,提高操作技能和工艺水平,选择合适的原料和处理方式等。
此外,还有一些其他可能出现的问题及其解决方案:1. 带钢跑偏:这可能是由于纠偏装置失灵、调整螺丝松动、导尺板磨损等原因导致的。
解决办法包括定期更换和修复纠偏装置,调整调整螺丝,更换或修复导尺板等。
2. 硬度超差:这可能是由于退火工艺不适当导致的。
解决办法是优化退火工艺,确保带钢的硬度达到要求。
3. 裂纹、划伤等严重缺陷:这可能是由于原料选择不当、检查不严格等原因导致的。
解决办法包括选择质量好的原料,加强带钢表面的检查和清理工作,以及发现缺陷时及时处理。
总之,要解决冷轧薄带过程中出现的问题,需要综合考虑设备精度、原料质量、工艺调整等多个因素,同时加强生产过程中的监控和管理,确保生产过程的稳定性和产品质量。
冷轧板带缺陷定义
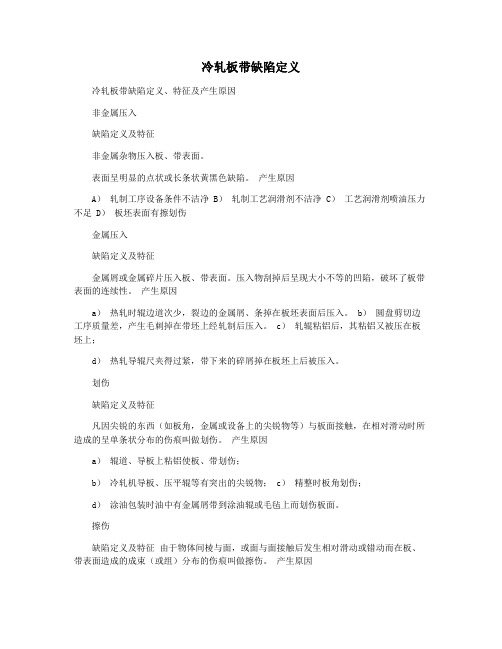
冷轧板带缺陷定义冷轧板带缺陷定义、特征及产生原因非金属压入缺陷定义及特征非金属杂物压入板、带表面。
表面呈明显的点状或长条状黄黑色缺陷。
产生原因A)轧制工序设备条件不洁净 B)轧制工艺润滑剂不洁净 C)工艺润滑剂喷油压力不足 D)板坯表面有擦划伤金属压入缺陷定义及特征金属屑或金属碎片压入板、带表面。
压入物刮掉后呈现大小不等的凹陷,破坏了板带表面的连续性。
产生原因a)热轧时辊边道次少,裂边的金属屑、条掉在板坯表面后压入。
b)圆盘剪切边工序质量差,产生毛刺掉在带坯上经轧制后压入。
c)轧辊粘铝后,其粘铝又被压在板坯上;d)热轧导辊尺夹得过紧,带下来的碎屑掉在板坯上后被压入。
划伤缺陷定义及特征凡因尖锐的东西(如板角,金属或设备上的尖锐物等)与板面接触,在相对滑动时所造成的呈单条状分布的伤痕叫做划伤。
产生原因a)辊道、导板上粘铝使板、带划伤;b)冷轧机导板、压平辊等有突出的尖锐物; c)精整时板角划伤;d)涂油包装时油中有金属屑带到涂油辊或毛毡上而划伤板面。
擦伤缺陷定义及特征由于物体间棱与面,或面与面接触后发生相对滑动或错动而在板、带表面造成的成束(或组)分布的伤痕叫做擦伤。
产生原因a)板带在加工生产过程中与导路、设备接触时,产生相对摩擦而造成擦伤; b)冷轧卷断面不齐正,在立式退火炉时产生错动、层与层之间长生擦伤; c)精整验收和包装操作不当产生板间滑动而造成擦伤; d)冷轧时张力不当,开卷时产生层间错动而产生擦伤。
碰伤(凹陷)缺陷定义及特征铝板、铝卷于其它物体碰撞后在板、带表面或断面产生的伤痕。
该缺陷发生在铝板、铝卷的表面或断面,且大多数在凹陷边际有被挤出的金属存在。
产生原因a)板、卷在搬运或存放过程中与其它物体相碰撞产生; b)板、卷在退火料架或底盘上有其他突出物顶撞而产生。
粘伤缺陷定义及特征因板间或带材卷层间压力过大造成板、带表面呈点状、片状或条状的伤痕。
粘伤产生时往往上下板片(或卷层)呈现对称性,有时呈周期性。
冷轧板常见表面缺陷特征及成因分析
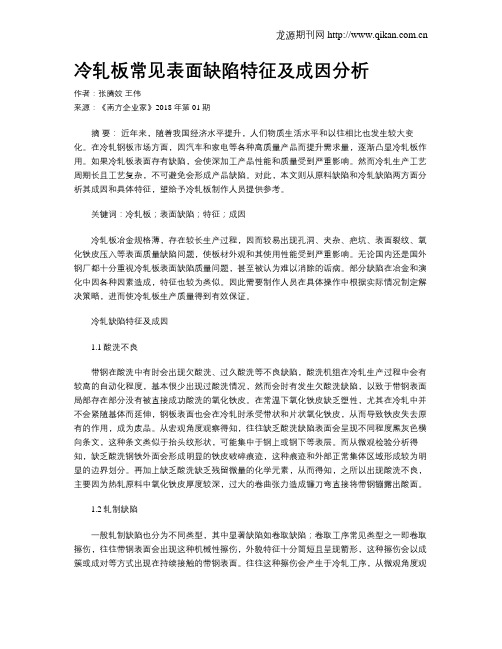
冷轧板常见表面缺陷特征及成因分析作者:张腾姣王伟来源:《南方企业家》2018年第01期摘要:近年来,随着我国经济水平提升,人们物质生活水平和以往相比也发生较大变化。
在冷轧钢板市场方面,因汽车和家电等各种高质量产品而提升需求量,逐渐凸显冷轧板作用。
如果冷轧板表面存有缺陷,会使深加工产品性能和质量受到严重影响。
然而冷轧生产工艺周期长且工艺复杂,不可避免会形成产品缺陷。
对此,本文则从原料缺陷和冷轧缺陷两方面分析其成因和具体特征,望给予冷轧板制作人员提供参考。
关键词:冷轧板;表面缺陷;特征;成因冷轧板冶金规格薄,存在较长生产过程,因而较易出现孔洞、夹杂、疤坑、表面裂纹、氧化铁皮压入等表面质量缺陷问题,使板材外观和其使用性能受到严重影响。
无论国内还是国外钢厂都十分重视冷轧板表面缺陷质量问题,甚至被认为难以消除的诟病。
部分缺陷在冶金和演化中因各种因素造成,特征也较为类似。
因此需要制作人员在具体操作中根据实际情况制定解决策略,进而使冷轧板生产质量得到有效保证。
冷轧缺陷特征及成因1.1酸洗不良带钢在酸洗中有时会出现欠酸洗、过久酸洗等不良缺陷,酸洗机组在冷轧生产过程中会有较高的自动化程度,基本很少出现过酸洗情况,然而会时有发生欠酸洗缺陷,以致于带钢表面局部存在部分没有被直接成功酸洗的氧化铁皮。
在常温下氧化铁皮缺乏塑性,尤其在冷轧中并不会紧随基体而延伸,钢板表面也会在冷轧时承受带状和片状氧化铁皮,从而导致铁皮失去原有的作用,成为废品。
从宏观角度观察得知,往往缺乏酸洗缺陷表面会呈现不同程度黑灰色横向条文,这种条文类似于抬头纹形状,可能集中于钢上或钢下等表层。
而从微观检验分析得知,缺乏酸洗钢铁外面会形成明显的铁皮破碎痕迹,这种痕迹和外部正常集体区域形成较为明显的边界划分。
再加上缺乏酸洗缺乏残留微量的化学元素,从而得知,之所以出现酸洗不良,主要因为热轧原料中氧化铁皮厚度较深,过大的卷曲张力造成镰刀弯直接将带钢镚露出酸面。
冷轧缺陷图谱教程PPT课件
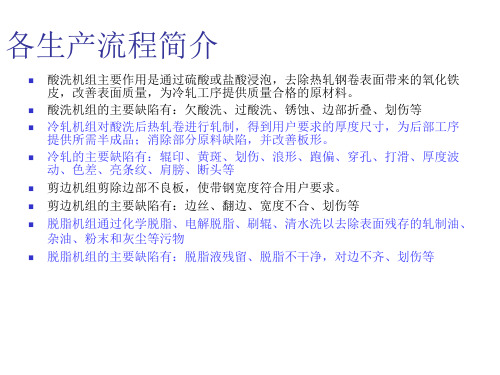
过酸洗
缺图片
过酸洗
【定义与特征】 钢带表面比正常酸洗后的钢板粗糙,颜
色是呈现暗黑色或棕黑色。 【原因分析】 在酸洗线上,如果酸温过高或带钢运行
在随后的冷轧中不能消除,因为带钢卷取时, 卷径增加会放大效果而变得越来越明显。 【鉴别与判定】 肉眼可以判定,尤其当带卷直径很大时,不易 与其他缺陷混淆。
夹杂
夹杂
【定义与特征】 钢板表面有明显的呈白色或黑色的点状、块状、
长条状缺陷,严重时表面起皮。 【原因分析】 表层夹杂是由连铸工艺中非金属夹杂导致,开
动、色差、亮条纹、肩膀、断头等
剪边机组剪除边部不良板,使带钢宽度符合用户要求。 剪边机组的主要缺陷有:边丝、翻边、宽度不合、划伤等
脱脂机组通过化学脱脂、电解脱脂、刷辊、清水洗以去除表面残存的轧制油、 杂油、粉末和灰尘等污物
脱脂机组的主要缺陷有:脱脂液残留、脱脂不干净,对边不齐、划伤等
各生产流程简介
退火机组用来消除冷轧带钢加工硬化和残余应力,软化金属 ,提高塑性,以便进一步进行冷轧。使冷轧带钢获得所需要 的硬度。
退火机组的主要缺陷有:硬度不合、粘钢、氧化等
平整机组用来消除带钢屈服平台,提高带钢成形性能,改善 板形,通过不同粗糙度的工作辊获得不同的粗糙度的钢带。
平整机组的主要质量缺陷有:辊印、太阳线、色差、浪形、 褶皱、压印等
穿孔
穿孔
【定义与特征】 钢带表面连续的或非连续的,贯穿钢带
上下表面的缺陷。 【原因分析】 多为原料穿孔,过酸洗会产生轧制中穿
带钢轧制常见缺陷原因分析
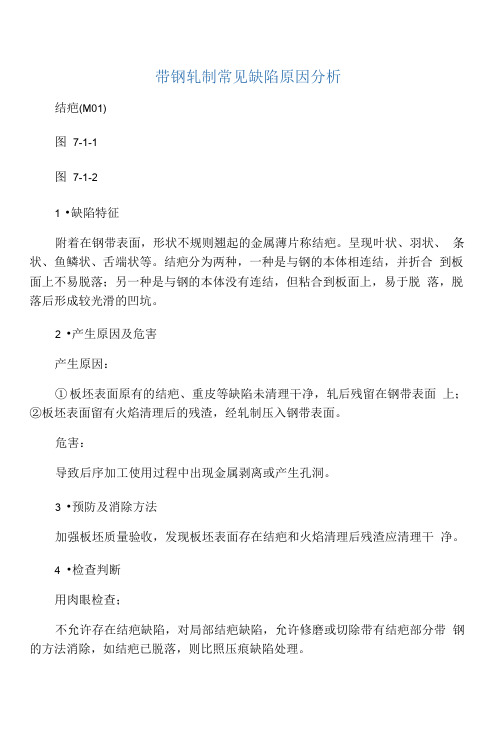
带钢轧制常见缺陷原因分析结疤(M01)图7-1-1图7-1-21•缺陷特征附着在钢带表面,形状不规则翘起的金属薄片称结疤。
呈现叶状、羽状、条状、鱼鳞状、舌端状等。
结疤分为两种,一种是与钢的本体相连结,并折合到板面上不易脱落;另一种是与钢的本体没有连结,但粘合到板面上,易于脱落,脱落后形成较光滑的凹坑。
2•产生原因及危害产生原因:①板坯表面原有的结疤、重皮等缺陷未清理干净,轧后残留在钢带表面上;②板坯表面留有火焰清理后的残渣,经轧制压入钢带表面。
危害:导致后序加工使用过程中出现金属剥离或产生孔洞。
3•预防及消除方法加强板坯质量验收,发现板坯表面存在结疤和火焰清理后残渣应清理干净。
4•检查判断用肉眼检查;不允许存在结疤缺陷,对局部结疤缺陷,允许修磨或切除带有结疤部分带钢的方法消除,如结疤已脱落,则比照压痕缺陷处理。
7.2 气泡(M02)图7-2-1闭合气泡图7-2-2 口气泡图7-2-3开口气泡1•缺陷特征钢带表面无规律分布的圆形或椭圆形凸包缺陷称气泡。
其外缘较光滑,气泡轧破后,钢带表面出现破裂或起皮。
某些气泡不凸起,经平整后,表面光亮,剪切断面呈分层状。
2•产生原因及危害产生原因:①因脱氧不良、吹氮不当等导致板坯内部聚集过多气体;②板坯在炉时间长,皮下气泡暴露或聚集长大。
危害:可能导致后序加工使用过程中产生分层或焊接不良。
3•预防及消除方法①加强板坯质量验收,不使用气泡缺陷暴露的板坯;②严格按规程加热板坯,避免板坯在炉时间过长。
4•检查判断用肉眼检查;不允许存在气泡缺陷。
7.3表面夹杂(M03)图7-3-1图7-3-21•缺陷特征板坯中的夹杂或夹渣经轧制后在钢带表面暴露的块状或长条状的夹杂缺陷称表面夹杂。
其颜色一般呈棕红色、黄褐色、灰白色或灰黑色。
2•产生原因及危害产生原因:板坯皮下夹杂轧后暴露或板坯原有的表面夹杂轧后残留在带钢表面。
危害:可能导致后序加工过程中产生孔洞、开裂、分层。
3•预防及消除方法加强板坯检查验收,不使用表面存在严重夹杂或夹渣的板坯。
- 1、下载文档前请自行甄别文档内容的完整性,平台不提供额外的编辑、内容补充、找答案等附加服务。
- 2、"仅部分预览"的文档,不可在线预览部分如存在完整性等问题,可反馈申请退款(可完整预览的文档不适用该条件!)。
- 3、如文档侵犯您的权益,请联系客服反馈,我们会尽快为您处理(人工客服工作时间:9:00-18:30)。
一、压痕 原因:1、因勒带或穿带甩尾不正常,带钢在工作辊表面造成堆焊或粘接 2、在轧机空转时预压力过小,造成工作辊与支撑辊点接触而使支撑辊周 长磨损,受损支撑辊反过来造成新更换工作辊表面压印而造成带钢表 面压痕 3、支撑辊掉肉造成工作辊表面压印,即在带钢表面产生压痕 措施: 1、轻微小面积压痕可对工作辊进行修磨(用砂石),严重压痕应更换工作辊 2、轧机空转时给一定轧制压力或采用正弯辊,以避免局部损伤轧辊,发现 支撑辊局部损伤,避免使用负弯辊,减轻轧辊表面压痕深度,勤换工作 辊,必要时及时更换支撑辊 二、压印 特征:带钢表面呈周期性凸状印痕 原因:工作辊表面产生裂纹或掉皮 措施: 1、更换新工作辊之前,严格检查轧辊表面质量,防止未磨净裂纹辊投入 使用(轧辊间应确保应有磨削量,特别是粘钢辊,以完全消除裂纹层)。 2、确保各机架工艺润滑良好,轧制液温度、浓度、压力在正常范围,防止喷嘴堵塞,避免轧辊局部温度过高 3、发现压印及时更换轧辊,更换新辊后,要进行一定预热,同时,开轧头几卷钢要严格控制升速制度 三、划伤 特征:带钢沿轧制方向的直线凹状缺陷 原因: 1、各种导辊与带钢速度不一样 2、带钢与辅助设备异常接触 3、生产线设备有异物 措施: 1、定期检查辅助传动辊是否转动灵活及表面状况 2、固定辅助设备与带钢应保持一定间隔 3、及时检查、清除生产线设备中的异物 4、发现带钢表面有划伤,应从后向前逐个检查,查出事故原因后,根据情况采 取的办法给予处理。 四、裂边 特征:带钢边部局部开裂或呈锯齿形裂口 五、原因: 1、酸洗剪切边部状况不好,造成轧后带钢裂边 2、热轧板本身边部裂口或龟裂 3、吊运中夹钳碰撞,使带钢边部碰损 措施: 1、酸洗剪切边剪刃间隙,应按剪切的不同厚度规格精确调节 2、热轧原板边部缺陷应在酸洗工序尽量切除(呈月牙形) 3、吊运钢卷时,夹钳应稳、准、轻,防止吊具将钢卷边部碰损 五、热划伤 特征:带钢表面沿轧制方向无规律的局部条状凹痕 原因: 1、轧辊和带钢温升过高 2、轧制薄规格时,在高速高压下,轧制油的油膜强度不够,使润滑不良所致 措施: 1正确选择轧制油浓度和轧制油类型,确保良好的润滑性能 2使各机架的负荷分配尽量均匀 3正确选择轧制液的温度、压力,确保良好的冷却性 4选择适当的轧制速度,在润滑和冷却不好的情况下,轧制速度不应超过 1000mpm 5、当已经发现有较严重的热划伤时,立即更换工作辊 六、轧穿 特征:带钢表面呈周期性孔洞 原因: 1、工作辊表面严重粘接 2、严重粘辊裂纹(一般前架板面产生压印,经后架轧钢延伸造成轧穿) 3、轧辊表面凹状缺陷 措施: 1、更换新工作辊 2、防止异物掉入轧机进入辊缝,避免轧辊表面损伤 七、板形缺陷 A、双边浪 特征:带钢两边呈可见波纹状 原因:轧辊凸度小,轧制压力过大,轧制温度低、正负弯辊使用不当 措施:减小轧制压力或加大后张力,合理控制好辊型,将工作辊中间部分轧制液流量尽量减小,增大正弯辊 B、单边浪 特征:带钢一边呈可见波浪状 原因:有浪一边轧制力过大,轧辊温度不均,工作辊水平未调好,来料厚度不均(楔形) 措施: 通过压下双摆,将有浪一边轧制力减小,严格要求原料同板厚差不超规定,头尾有镰刀弯在酸洗一定.要剪掉 C、中间浪 特征:带钢中部呈可见波浪状 原因:与双边浪相反 措施:与双边浪相反 D、二肋浪 特征:带钢沿宽度方向1/4、3/4处或部分区域呈可见波浪状 原因:轧制温度不均,局部过热与浪相对应的轧辊冷却液喷嘴堵塞 措施:加大二肋浪部位的轧制液流量,认真检查二肋浪部位喷嘴是否堵塞 八、厚度不均或不合 特征:带钢沿轧制方向厚度波动变化超出产品要求或轧制成品厚度与产品要求厚度不符 原因: 1、热轧原料本身厚度不均,材质硬度不均 2、AGC系统没有投入时,压下及速度调节不及时 3、各机架张力波动范围过大 4、测厚仪(特别是最后机架)不准 措施: 1、确保热轧原料厚度精度,对严重超厚或超薄部分应切除,轧制中发现原料厚度波动,应及时降速,待调节好后再升速,当厚度波动严重时,要停机,然后按实际厚度进行手设定计算,再启动设备进行轧制 2、AGC系统没有投入使用时,随速度的变化及时调节轧制力和张力,保证厚度精度正常 3、严格保证系统的张力稳定 4、定期检查测厚仪的精度,轧制时如发现异常状况,及时检查、核对成品实物厚度与测厚仪显示的一致性,否则立即通知计控人员进行处理 九、卷形 A、溢出边 特征:钢卷边部局部不齐 原因:酸洗来料溢出边,热轧板形较差,卷取张力过小及波动,轧制压力不稳定,入口无跑偏控制装置 措施:发现原料溢出边严重时,人工首先降速,及时采取手动对中调节,严格控制好板形,对带头板形不好的部分,应切除,严格控制卷取张力,确保压下稳定正常,尽快使人工跑偏控制装置投入使用,一旦出现严重溢边,在最后机架分卷 B、塔形 特征:钢卷边部呈弧形状 原因:酸洗卷塔形,带钢头部板形不良或卷心有废带头,卷取张力过小,卷心与卷取机卷筒之间有窜动,各架侧倒板间隙过大等因素,均可造成卷取时钢卷塔形 措施:轧制酸洗塔形卷时速度不能高,人工随时进行对中调节,当实在无法纠偏时,最后机架轧钢工根据情况进行分卷,严格控制好穿带头部倒板,当带头板形不好时,应及时切除,废带头一定不能卷入卷心,确保卷取张力正常,满足工艺制度的要求,无论在何种情况下,发现塔型应立即分卷 C、心形卷 特征:钢卷内径局部下凹 原因:带卷头部卷取张力过小,轧制规格薄 措施:提高头部卷取张力,一般应大于设定张力20~30%,适当增大带头厚度,必要时更换小直径卷筒 D、抽心 卸卷时,卷取机卷筒将卷心部分带出,或是热处理吊车在掉卷时,将卷心部分吊起,无法将钢卷吊走 特征:钢卷内径局部溢出 原因:带钢头部板形不好,卷心卷取张力过小,卷取机卷筒位移或钢卷小车上塑料垫磨损不均,造成钢卷中心与卷筒中心不一致 措施:确保带钢头部板形良好,特别是废带头不要卷入内径,手动方式加大头部卷取张力,将偏移的卷取机复位,同时更换已磨损的钢卷小车塑料垫块,经常检查吊具的表面状况及磨损程度 E、塌卷 特征:钢卷卧放时呈椭圆状 原因:在整个轧制过程中,卷取张力都小于设定张力,卸卷以后便暴露,尤其以薄规格产品为明显,经吊车吊运后会发生卷内孔径全塌,厚规格产品,经退火后平整机上料时暴露出来 措施:在张力调节系统或张力设定不正常时,要通过手动操作方式,将卷取张力升高,以保证带钢头部及整卷的卷取张力符合工艺的要求,避免质量和安全事故的发生 粘结、氧化色和性能不合格是冷轧薄板退火工序中存在的三大问题,尤其是粘结与氧化色这两种缺陷较为突出。 一、粘结 1、缺陷特征:退火钢卷层间互相粘在一起称粘结,粘结的形式有点状、线状和大块面粘合,粘结较严重时,手摸有突起感觉,多分布于带钢的边部或中间;严重的面粘结,开卷时被撕裂或出现孔洞,甚至无法开卷,成为“死卷”。 2、产生原因: (1)张力过大,张力是引起钢卷粘结的主要原因之一。张力包括轧机的轧制张力和卷取张力。张力过大时,会使保护气体的气流循环不好而产生热阻滞,使钢板发生粘结。 (2)板形不良,板形不好会使带钢在纵向上出现两边厚,中间薄或两边薄,中间厚或边浪、中间浪、多条浪及周边性的局部浪形等,经高温退火后,都能产生粘结。 (3)卷取时出现参差不齐的溢出边,带钢卷取不齐,特别是较薄的的板子,容易产生粘结。 (4)乳化液不纯,乳化液中有杂物,经退火蒸发后残留于钢板与钢板之间,如吹除不净,也会产生粘结。 (5)超温,不管是什么原因引起的,如果炉内出现严重超温时,也必然要引起粘结。 ( (6)气体循环不良,由于装炉堆垛不符合要求,致使保护气体在炉内循环不好,使炉温不均匀,个别部位形成热阻滞严重,温差大而产生粘结。 (7)带钢表面粗糙度太小。 (8)钢质太软,钢中碳、硅含量少,粘结倾向高。 3、预防及消除方法: (1)正确选择卷曲张力。 (2)控制工作辊粗糙度。 (3)控制好板形和卷形。 (4)按堆垛原则堆垛,将塔形卷,溢出边卷放置钢垛上部。 (5)遵守操作规程,控制退火温度和时间。 (6)保证退火设备的完整性,检测仪表准确,热电偶插放到位等。 4、检测判断: (1)用肉眼检查。 (2)普通冷轧板及钢带允许有局部的粘结痕迹,标准中有明确规定的不允许存在 (3)严重的粘结判废。 二、氧化色(氧化边) 1、缺陷特征:钢板及钢带表面被氧化,其颜色由边部的深蓝色逐步过渡到浅蓝色、淡黄色,统称氧化色。 2、产生原因: (1)退火时保护罩密封不严或漏气,发生化学反应。 (2)保护罩吊罩过早,高温出炉(钢卷温度大于110℃)钢卷边缘表面氧化。 (3)保护气体成分不纯,CO和CO2比例不和造成碳的沉积。 (4)加热前预吹洗时间不足,炉内存在残氧,钢卷在氧化性气氛中退火。 3、预防及消除方法: (1)带钢表面的乳化液应吹干净,减少进入炉内的水份和残渣。 (2)装炉盖罩后,必须进行密封性检查,发现密封不好,应及时处理。 (3)保证预吹洗时间,尽量吹净退火空间的空气,避免钢卷氧化。 (4)确保保护气体成份,露点 (5)严禁高温出炉。 (6)发现严重氧化时,必须重新退火除氧。 (7)经常检查控制仪表的工作状态及热电偶插放位置。 三、乳化液斑点 1、缺陷特征:经退火的钢板表面呈现不规则的或象小岛形状的黑色、褐色图形,常出现在带钢的头尾部;有时出现在带钢边部;有时带钢通长都有。 2、产生原因: (1)在轧机出口处乳化液未吹干净,残留在带钢表面上。 (2)穿带时风机未开,甩尾时风机关闭。 (3)装炉后预吹洗时间不足,加热时乳化液碳化形成斑点。 3、预防及消除方法 (1)吹风设备良好,风压达到工艺要求。 (2)发现吹不干净,应查找原因,及时处理。 (3)保证预吹洗时间。 四、性能不合格 产生原因: 1、工艺制度出现差错。在配料时如果将工艺制度下错了,则极易造成性能不合格。 2、装炉不正。钢卷在退火炉中,如果内径部队齐,相互错压,引起保护气体循环不畅,形成炉内温差大,加上循环风机的风量小,也会造成部分性能不合。 3、欠温。没有达到额定退火温度就加热结束了,容易出现性能不合,这主要是计控设备的故障影响的。 4、欠时。加热时间未达到或保温时间太短就加热结束了,同样也容易影响性能。 1.屈服点(σs) 钢材或试样在拉伸时,当应力超过弹性极限,即使应力不再增加,而钢材或试样仍继续发生明显的塑性变形,称此现象为屈服,而产生屈服现象时的最小应力值即为屈服点。 设Ps为屈服点s处的外力,Fo为试样断面积,则屈服点σs =Ps/Fo(MPa),MPa称为兆帕等于N(牛顿)/mm2,(MPa=106Pa,Pa:帕斯卡=N/m2) 2.屈服强度(σ0.2) 有的金属材料的屈服点极不明显,在测量上有困难,因此为了衡量材料的屈服特性,规定产生永久残余塑性变形等于一定值(一般为原长度的0.2%)时的应力,称为条件屈服强度或简称屈服强度σ0.2 。 3.抗拉强度(σb) 材料在拉伸过程中,从开始到发生断裂时所达到的最大应力值。它表示钢材抵抗断裂的能力大小。与抗拉强度相应的还有抗压强度、抗弯强度等。 设Pb为材料被拉断前达到的最大拉力,Fo为试样截面面积,则抗拉强度σb= Pb/Fo (MPa)。 4.伸长率(δs) 材料在拉断后,其塑性伸长的长