冷轧带钢产品的质量缺陷
冷轧带钢表面白色缺陷成因与控制

Total No.299总第299期2020年第11期HEBEI METALLURGY2020,Numbrr11冷轧带钢表面白色缺陷成因与控制王田惠,吕超杰,王风强,程帅(河钢集团邯钢公司技术中心,河北邯郸05601)摘要:利用电镜和能谱分析手段对I带钢退火后表面出现的白色缺陷的位置分布、微观形貌及成分进行了分析,并根据分析结果,将白色缺陷分为点、线、面3类。
详细分析了每类缺陷产生的工序及原因,并提出了相应的控制措施。
实施后,因表面白色缺陷而降级的冷轧带钢明显减少。
关键词:冷轧;I钢;带钢表面;白色缺陷;点状;线状;片状中图分类号:TG142.2文献标识码:B文章编号:1006-5008(2020)11-0062-05doi:10.23630/ki.13-112.2020.2115CAUSES AND CONTROL OFSURFACE WHIZE DEFECTS OF COLD ROLLED STRIZWang Tia/hui,Lv Chaojie,Wang Fecgqia/g,Checg Shuai(Technical Cectar of HBIS Group Hansteai Company,Handan,Hebei,056015) Abstract:The position distriVution,micro morphology and composition of white defects on the serfacc of IFstrip after annealing was analyzeC by SEM and ecerpy disyersive seactroscopy.AccorPing to the analysis re-selts,the white defects were diviVeC into three tyyas:point,line and serfacc.The process and censes of va-Pety defects are analyzeC in detail,and the correseonding control measeras are put forwarP.After the implementation,the degcdation number of cold rolled strip due to white serfacc defects is significebtly reduced.Key Word::cold rolling;IF steel;strip serfacc;white defect;seot;linear;sheet0引言随着家电和汽车工业的发展,对钢板表面质量的要求也越来越高[-3]。
冷轧带钢浪形缺陷的成因和解决措施
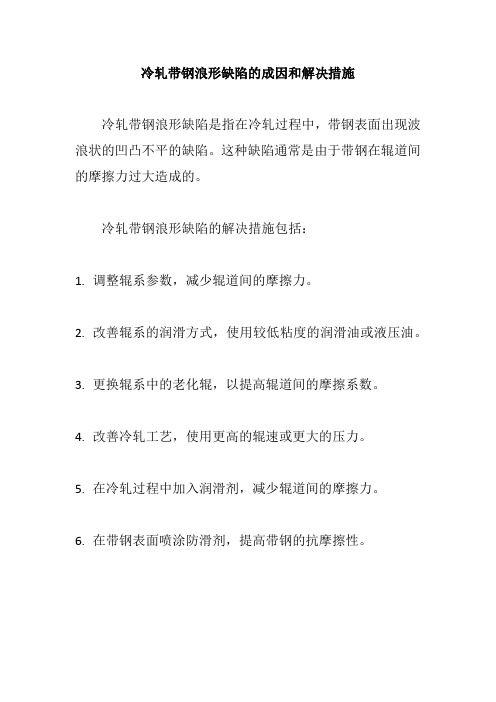
冷轧带钢浪形缺陷的成因和解决措施
冷轧带钢浪形缺陷是指在冷轧过程中,带钢表面出现波浪状的凹凸不平的缺陷。
这种缺陷通常是由于带钢在辊道间的摩擦力过大造成的。
冷轧带钢浪形缺陷的解决措施包括:
1.调整辊系参数,减少辊道间的摩擦力。
2.改善辊系的润滑方式,使用较低粘度的润滑油或液压油。
3.更换辊系中的老化辊,以提高辊道间的摩擦系数。
4.改善冷轧工艺,使用更高的辊速或更大的压力。
5.在冷轧过程中加入润滑剂,减少辊道间的摩擦力。
6.在带钢表面喷涂防滑剂,提高带钢的抗摩擦性。
冷轧常见缺陷
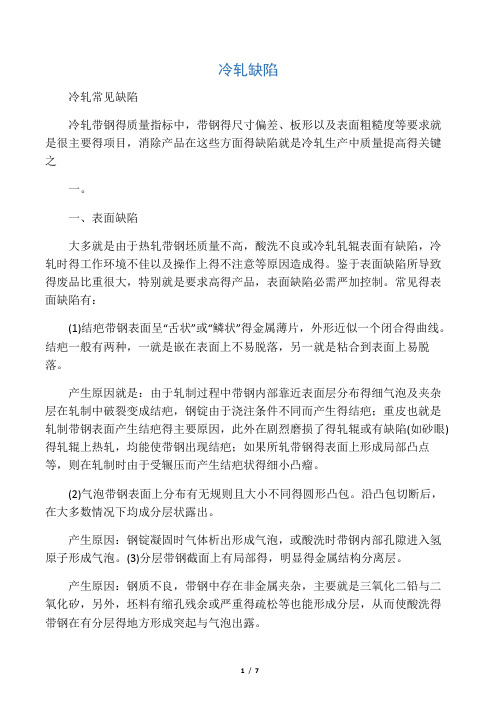
冷轧缺陷冷轧常见缺陷冷轧带钢得质量指标中,带钢得尺寸偏差、板形以及表面粗糙度等要求就是很主要得项目,消除产品在这些方面得缺陷就是冷轧生产中质量提高得关键之一。
一、表面缺陷大多就是由于热轧带钢坯质量不高,酸洗不良或冷轧轧辊表面有缺陷,冷轧时得工作环境不佳以及操作上得不注意等原因造成得。
鉴于表面缺陷所导致得废品比重很大,特别就是要求高得产品,表面缺陷必需严加控制。
常见得表面缺陷有:(1)结疤带钢表面呈“舌状”或“鳞状”得金属薄片,外形近似一个闭合得曲线。
结疤一般有两种,一就是嵌在表面上不易脱落,另一就是粘合到表面上易脱落。
产生原因就是:由于轧制过程中带钢内部靠近表面层分布得细气泡及夹杂层在轧制中破裂变成结疤,钢锭由于浇注条件不同而产生得结疤;重皮也就是轧制带钢表面产生结疤得主要原因,此外在剧烈磨损了得轧辊或有缺陷(如砂眼)得轧辊上热轧,均能使带钢出现结疤;如果所轧带钢得表面上形成局部凸点等,则在轧制时由于受辗压而产生结疤状得细小凸瘤。
(2)气泡带钢表面上分布有无规则且大小不同得圆形凸包。
沿凸包切断后,在大多数情况下均成分层状露出。
产生原因:钢锭凝固时气体析出形成气泡,或酸洗时带钢内部孔隙进入氢原子形成气泡。
(3)分层带钢截面上有局部得,明显得金属结构分离层。
产生原因:钢质不良,带钢中存在非金属夹杂,主要就是三氧化二铅与二氧化矽,另外,坯料有缩孔残余或严重得疏松等也能形成分层,从而使酸洗得带钢在有分层得地方形成突起与气泡出露。
(4)裂纹带钢表面完整性比较严重得破裂,它就是以纵向、横向或一定角度得形式出现得裂缝。
产生原因:轧制前带钢不均匀加热或过热,轧制时带钢不均匀延伸,或带钢表面有缺陷清除不彻底,以及带钢上有非金属夹杂及皮下气泡,另外,冷轧时不正确地调整轧辊与不正确得设计辊型,同样会产生裂纹,再有,用落槽得轧辊轧制带钢,张力太大,化学成分不合适等也可能会出现裂纹。
(4)表面夹杂带钢表面上具有轧制方向上伸长得红棕色,淡黄色,灰白色得点状,条状与块状得非金属夹杂物。
冷轧带钢边鼓缺陷产生原因与控制措施

冷轧带钢边鼓缺陷产生原因与控制措施全文共四篇示例,供读者参考第一篇示例:冷轧带钢是一种重要的金属材料,广泛应用于建筑、汽车、机械制造等领域。
在生产过程中,冷轧带钢常常会出现边鼓缺陷,影响产品质量。
本文将从冷轧带钢边鼓缺陷的产生原因和控制措施两方面进行探讨。
一、冷轧带钢边鼓缺陷产生原因:1. 轧辊质量不良:轧辊表面粗糙度大、硬度不足或不均匀,会导致轧件表面质量不良,进而引起边鼓缺陷的产生。
2. 轧辊边缘磨损严重:轧辊边缘磨损加剧,造成轧件边部挤压不平整,易产生边鼓缺陷。
3. 轧件冷却不均匀:冷却水量不足或水压不稳定会导致轧件温度分布不均匀,使得边部冷却速度不一致,进而引发边鼓缺陷。
4. 锯切不准确:如果在冷轧带钢的切割过程中,锯切位置不准确或锯切刀具损坏,容易导致边部挤压变形,产生边鼓缺陷。
5. 压下力控制不好:在轧制过程中,如果压下力控制不好,会造成轧辊与轧件之间的挤压不均匀,容易形成边鼓缺陷。
1. 提高轧辊质量:选用优质的轧辊材料,确保轧辊表面光滑、硬度均匀,减少轧辊对轧件表面的损伤。
2. 加强轧辊维护:定期检查轧辊边缘磨损情况,及时更换或修复磨损严重的轧辊,确保轧辊边缘的平整度。
3. 控制冷却工艺:合理设置冷却水量和水压,确保轧件冷却均匀,避免轧件边部出现温差过大的情况。
4. 加强锯切管理:对切割设备进行定期维护保养,确保切割精度和品质,避免因切割不准确导致的边鼓缺陷。
冷轧带钢边鼓缺陷的产生原因复杂多样,需要生产企业在生产过程中严格控制各项工艺参数,加强设备维护保养,提高操作技术水平,才能有效避免边鼓缺陷的产生,确保产品质量。
希望通过本文的介绍,能够对冷轧带钢生产企业提供一定的参考和帮助。
【以上内容仅供参考】。
第二篇示例:冷轧带钢是一种重要的金属材料,广泛应用于各种领域。
但是在生产过程中,冷轧带钢边鼓缺陷是经常出现的一种质量问题,给生产造成了一定的影响。
本文将从边鼓缺陷的产生原因和相应的控制措施进行探讨,希望对相关行业提供一些参考。
冷轧带钢表面黑斑缺陷的成因及控制
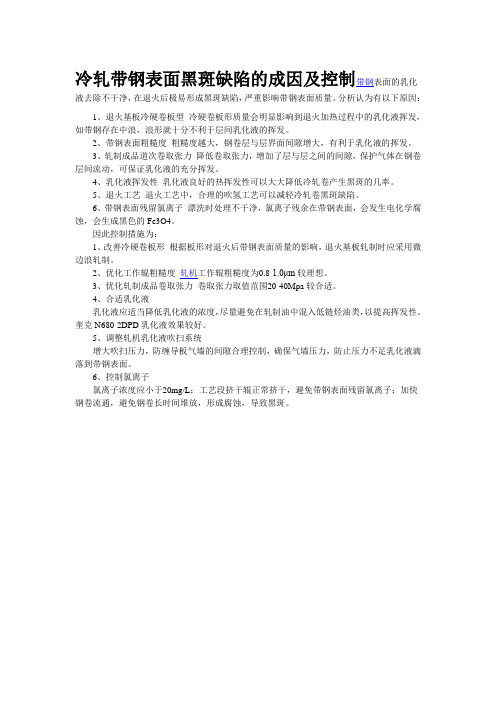
冷轧带钢表面黑斑缺陷的成因及控制带钢表面的乳化液去除不干净,在退火后极易形成黑斑缺陷,严重影响带钢表面质量。
分析认为有以下原因:
1、退火基板冷硬卷板型冷硬卷板形质量会明显影响到退火加热过程中的乳化液挥发,如带钢存在中浪,浪形就十分不利于层间乳化液的挥发。
2、带钢表面粗糙度粗糙度越大,钢卷层与层界面间隙增大,有利于乳化液的挥发。
3、轧制成品道次卷取张力降低卷取张力,增加了层与层之间的间隙,保护气体在钢卷层间流动,可保证乳化液的充分挥发。
4、乳化液挥发性乳化液良好的热挥发性可以大大降低冷轧卷产生黑斑的几率。
5、退火工艺退火工艺中,合理的吹氢工艺可以减轻冷轧卷黑斑缺陷。
6、带钢表面残留氯离子漂洗时处理不干净,氯离子残余在带钢表面,会发生电化学腐蚀,会生成黑色的Fe3O4。
因此控制措施为:
1、改善冷硬卷板形根据板形对退火后带钢表面质量的影响,退火基板轧制时应采用微边浪轧制。
2、优化工作辊粗糙度轧机工作辊粗糙度为0.8-1.0μm较理想。
3、优化轧制成品卷取张力卷取张力取值范围20-40Mpa较合适。
4、合适乳化液
乳化液应适当降低乳化液的浓度,尽量避免在轧制油中混入低链烃油类,以提高挥发性。
奎克N680-2DPD乳化液效果较好。
5、调整轧机乳化液吹扫系统
增大吹扫压力,防缠导板气墙的间隙合理控制,确保气墙压力,防止压力不足乳化液滴落到带钢表面。
6、控制氯离子
氯离子浓度应小于20mg/L;工艺段挤干辊正常挤干,避免带钢表面残留氯离子;加快钢卷流通,避免钢卷长时间堆放,形成腐蚀,导致黑斑。
常见冷轧质量缺陷
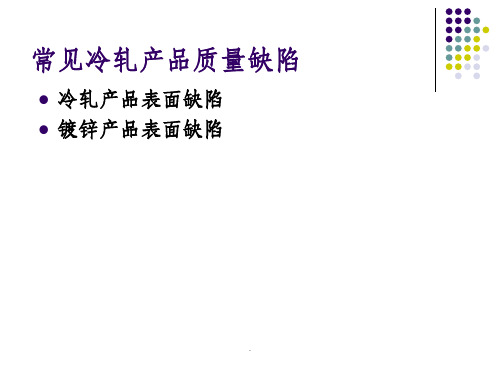
大面积残留
点状残留
.
冷轧产品表面缺陷——平整液残留
缺陷原因: 1)平整机平整液流量过大,平整机出口侧排 烟系统故障导致平整液蒸汽结露后掉落在钢板 表面; 2)平整机吹扫系统出现故障,未吹扫完全;
控制措施: 1)调整平整液喷射流量; 2)检查吹扫系统压力、过滤器等;
.
冷轧产品表面缺陷——油斑
缺陷特征:带钢表面点状周期性出现,呈现黄 色或黑色;
缺陷特征:带钢表面呈现黄白相间的分布状况, 板面发花;
.
冷轧产品表面缺陷——黄斑
缺陷原因: 1)来料冷硬卷表面存在锈蚀; 2)炉子出口水淬槽水质较脏; 3)带钢在水淬槽内与脱盐水发生化学反应;
控制措施: 1)加强对来料冷硬卷的表面质量检查,发现来料严 重存在锈蚀缺陷时及时甩卷; 2)定期检测炉子水淬槽内水质状况,根据电导率、 浊度等进行排放并补充新水; 3)水淬槽内添加缓蚀剂;
.
冷轧产品表面缺陷——擦划伤
缺陷原因: 1)机组某个辊子表面有划伤,导致带钢表面被划伤; 2)机组中某个辊子转速与带钢速度不同步; 3)平整机板形仪高度不当造成带钢下表面划伤; 4)冷硬卷表面存在划伤;
控制措施: 1)快速确认擦划伤产生的位置,若是辊子表面有划 伤则需要停车修磨辊子表面; 2)由于板形仪导致的划伤则需要增加板形仪与带钢 之间的距离;
控制措施: 1)带钢经过平整机出现浪形时关闭板形仪自动控制人工调整弯辊 力; 2)生产薄宽规格产品时要时事观察炉子出口带钢板形状况,出现 浪形及时调整炉区速度、温度及张力等参数;
.
冷轧产品表面缺陷——辊印
缺陷特征:带钢表面有轧机或平整机工作辊印 痕,一般无手感
.
冷轧产品表面缺陷——辊印
缺陷原因: 1)轧辊磨削或毛化不良,辊面粗糙度不均等 使得带钢表面局部区域粗糙度不均形成辊印; 2)冷硬卷横截面上厚度分布不均,存在局部 高点,导致平整后带钢局部高点处发亮; 3)生产过程中轧辊被带钢损伤,传递到带钢 表面后形成辊印;
冷轧产品常见缺陷图谱与判断(doc40页).doc

冷轧产品常见缺陷图谱与判断目录结疤(4)表面夹杂(5)分层(6)氧化铁皮压入(7)辊印(8)压痕(压印、压坑)(9)扁卷 (10)瓢曲 (11)镰刀弯 (12)折迭(13)边裂(14)气泡(15)折皱(16)刮伤(17)擦伤(划伤、划痕)(18)撞伤(19)切斜(20)欠酸洗(21)过酸洗(22)停车斑(23)浪形(24)氧化色(25)振动纹(26)平整斑(27)粘结(28)塔形(29)溢出边(30)卷取擦伤(31)锈蚀(32)松卷(33)凸包(起筋、隆起、鼓包)(34)厚度不合(35)长度不合(36)平整纹(37)孔洞(38)黄斑(39)黑斑(40)1.缺陷名称:结疤定义与外观:附着在钢带表面,形状不规则翘起的金属薄片称结疤。
呈现叶状、羽状、条状、鱼鳞状、舌端状等。
结疤分为两种,一种是与钢的本体相连结,并折合到板面上不易脱落叫闭口结疤;另一种是与钢的本体没有连结,但粘合在板面上,易于脱落,脱落后形成较光滑的凹坑称为开口结疤。
成因:●冷轧基板表面原有的结疤、翘皮等缺陷未挑出,经冷轧后残留在钢带表面上;●冷轧时钢板表面粘附异物,经轧制压入钢带表面。
危害:导致后续加工使用过程中出现金属剥离或产生孔洞。
预防及消除方法:加强冷轧基板的检查,检查判断:●用肉眼检查;●不允许存在结疤缺陷,一般判利用品或以下等级,对局部结疤缺陷,允许切除带有结疤部分带钢的方法清除。
如结疤已脱落,则比照压痕缺陷处理,若深度没有超出相关标准规定,可以参照相应标准进行判定。
2.缺陷名称:表面夹杂定义与外观:冷轧基板皮下或表面非金属夹杂、夹渣在冷轧加工过程中破裂而暴露在钢带表面,一般呈点状、块状、线状或长条状无规律的分布在薄板的表面。
其颜色一般呈棕红色、黄褐色、灰白色或灰黑色。
成因:冷轧基板皮下夹杂轧后暴露或基板的表面原有夹杂轧后残留在带钢表面(炼钢浇铸原因)。
危害:可能导致后续加工过程中产生孔洞、开裂、分层。
预防及消除方法:●严格遵守浇铸制度●加强冷轧基板表面质量检查。
浅析冷轧带钢表面缺陷成因及控制措施
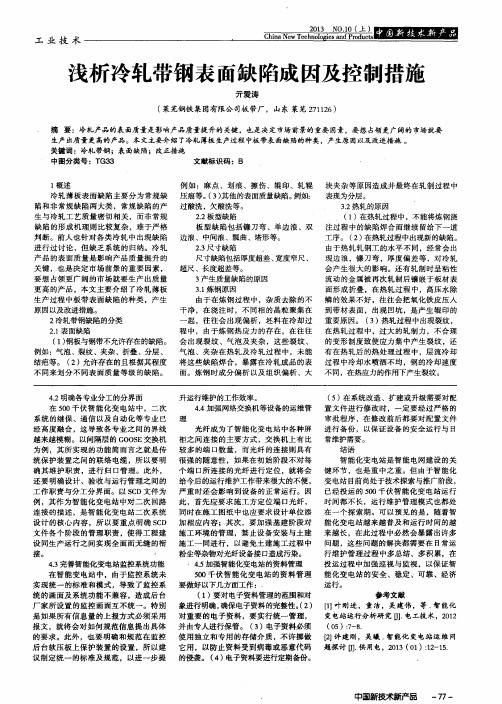
1概 述
冷轧 薄板表 面缺陷主要分为常规缺 陷和非常规缺 陷两大类 ,常规缺陷的产 生 与 冷 轧 工 艺 质 量 密 切 相 关 ,而 非 常 规 缺 陷 的形 成 机 理 则 比较 复 杂 ,难 于 严 格 判 断 。 前 人 也 针 对 各 类 冷 轧 中 出 现 缺 陷 进 行 过 讨 论 ,但 缺 乏 系 统 的 归 纳 。 冷 轧 产 品 的表 面 质 量 是 影 响 产 品 质 量 提 升 的 关 键 ,也 是 决 定 市 场 前 景 的 重 要 因素 , 要 想 占领 更 广 阔 的 市 场 就 要 生 产 出 质 量 更高 的产品 ,本 文主要介 绍了冷轧薄板 生 产 过 程 中板 带 表 面 缺 陷 的 种 类 ,产 生 原 因 以及 改 进措施 。 2 冷 轧带 钢缺 陷 的分 类 2 . 1 表 面缺 陷 ( 1 ) 钢板与钢带不允许存在 的缺陷。 例如 :气泡 、裂 纹 、夹 杂 、折 叠 、分 层 、 结疤等。 ( 2 )允许存在的且根据其程度 不 同来 划分 不 同 表 面 质量 等级 的缺 陷 。
亓 爱 涛
( 莱芜钢铁 集 团有限公 司板带厂 ,山 东 莱芜 2 7 1 1 2 6 )
摘 要 :冷 轧 产 品 的表 面质 量是 影 响产 品质 量提 升 的 关键 ,也是 决定 市 场前 景 的重要 因素 。要 想 占领 更广 阔 的 市场就 要
生产出质量更高的产品。本文主要介绍了冷轧薄板生产过程 中板 带表 面缺陷的种类,产生原因以及改进措施 。 关键词 :冷轧带钢;表面缺陷;改正措施
4 . 2明确各 专业 分工 的分 界 面 在5 0 0 千 伏 智 能 化 变 电 站 中 ,二 次 系统 的继保 、通信以及 自动化等专业 已 经 高 度 融 合 ,这 导致 各 专 业 之 间 的 界 线 越 来越 模 糊 。 以间 隔层 的 G O O S E交 换 机 为例 ,其所实现的功能简而言之就是传 统 保 护 装 置 之 间 的联 络 电缆 ,所 以 要 明 确其维护职 责,进行归 口管理 。此外 , 还 要 明确 设 计 、 验 收 与 运 行 管 理 之 间 的 工作职责与分工分界 面。以 S C D文件为 例 ,其 作 为智 能 化变 电站 中对 二次 回路 连 接 的 描 述 ,是 智 能 化 变 电 站 二 次 系 统 设 计 的 核 心 内容 ,所 以 要 重 点 明确 S C D 文件各个阶段的管理职责 ,使得工程建 设 同生 产 运 行 之 间 实 现全 面 而无 缝 的衔 接。 ・ 4 . 3 完善智能化变电站监控系统功能 在智能变电站中 ,由于监控 系统未 实 现 统 一 的 标 准 和 模 式 ,导 致 了监 控 系 统 的 画 面及 系 统 功 能 不兼 容 ,造 成 后 台 厂家所设 置的监 控画面互 不统一。特别 是 如果 所有 信息量 的上报方式必须采用 报文 ,就将会对如何规范信息提 出具体 的要 求 。此 外 ,也 要 明 确 和 规 范 在 监 控 后 台软压板 上保 护装 置的设 置,所 以建 议制定统一 的标准及规范 ,以进一步提
- 1、下载文档前请自行甄别文档内容的完整性,平台不提供额外的编辑、内容补充、找答案等附加服务。
- 2、"仅部分预览"的文档,不可在线预览部分如存在完整性等问题,可反馈申请退款(可完整预览的文档不适用该条件!)。
- 3、如文档侵犯您的权益,请联系客服反馈,我们会尽快为您处理(人工客服工作时间:9:00-18:30)。
冷轧带钢产品的质量缺陷1.原料缺陷对冷轧产品质量的影响。
冷轧所使用的各种形式的原料,最常见的缺陷是表面铁皮压下边部裂纹、表面麻坑、凸泡过大、纵条状划伤、沿横向厚度偏差过大、沿纵向是镰刀弯或S弯、钢卷塔形、浪形扁卷、长舌头、冷松卷等。
由于这些原料质量缺陷,大大降低了产品质量的成材率,使产品成本提高。
2.酸洗产生的缺陷对冷轧产品质量的影响带钢经酸洗、水洗和干燥后,其表面应成灰白色或银白色。
但因操作不当,洗工艺制度和某些设备的不良影响,往会造成带钢的不同缺陷。
这些缺陷主要有:酸洗气泡、过酸洗、欠酸洗、锈蚀、夹杂划伤和压痕等。
这些缺陷占冷轧产品缺陷的2%左右,其中主要是欠酸洗,过酸洗和酸洗气泡等。
下面简述一下这些缺陷产生的原因几防止措施:(1)酸洗气泡。
酸洗气泡是由于酸与带钢作用生成氧气所造成的。
它在冷轧时会发生噼啪的爆炸声,他的外观特征是呈条状的小鼓泡,破裂后呈黑色细裂纹,经过轧制后,气泡裂缝会延伸扩大,致使产品的力学性能降低。
防止产生气泡的措施是:调整酸液的浓度,控制酸洗时溶液的温度和带钢表面平直状态等。
(2)过酸洗。
金属在酸溶液中停留时间过长,使其在酸溶液的作用下表面逐渐变成粗糙麻面的现象称为过酸洗。
过酸洗的带钢延伸性大大降低,在轧制过程中很容易断裂和破碎,并且造成粘辊。
过酸洗的带钢即使轧制成材也不能作为成品,因为他的力学性能大大降低了。
产生过酸洗的原因是:机组连续作业中断,使酸洗失去连续性,或因带钢断带处理时间过长、酸液浓度过高、酸液温度过高、酸洗速度过低等。
防止措施是尽量密切全机组的操作配合,保证生产正常运行。
严格按照工艺规程控制好酸液浓度、温度、工艺速度。
(3)欠酸洗。
钢带酸洗之后表面残留未洗掉的氧化铁皮时称为欠酸洗。
欠酸洗的带钢,轻者在轧制之后产品表面是暗色或花脸状;严重时氧化铁皮被压入到黑斑。
造成欠酸洗的原因是:氧化铁皮厚度不匀,较厚部分的氧化铁皮需要较长酸洗时间,酸洗工艺不适当、酸浓度偏低、温度低、酸液中亚铁成分高或速度太快所导致。
带钢波浪度和镰刀弯较大,在酸洗过程中起浪部分或弯起部分没有浸泡在酸液中通过,造成漏酸洗。
实际生产中欠酸洗多出现在带钢的头尾段和两侧边缘,因此处理欠酸洗的方法是预先平整好板形,对于铁皮较厚而面积又不大的带钢可采用先局部酸洗涤一次,而后再过酸洗线的方法去锈。
按照工艺规程控制好酸浓度、温度和酸洗速度也能提高酸洗质量。
(4)锈蚀。
原料酸洗后表面重新出现锈层的现象称为锈蚀。
锈蚀形成的原因是:带钢酸洗后表面残留少许的酸溶液,或带钢清洗后没有达到完全干燥而使表面重新生锈。
此外带钢在酸洗后在高温的清洗水中停留过长也会产生锈蚀现象。
带钢锈蚀处的钢板在轧制后表面呈暗色,他促使成品在库存时再次锈蚀,从而降低成品材的表面质量,严重时使产品报废。
防止锈蚀的措施是严格执行酸洗、清洗操作规程及时给表面涂油,并应堆放在干燥的地方。
(5)夹杂。
带钢在酸洗后表面出现深陷的星罗棋布的黑点疵病称为夹杂。
它是由于热轧时氧化铁皮被压下所形成的。
这样的缺陷不可能采取酸洗法除去。
当它经过冷轧后,黑点便会扩展延伸呈黑色条状,大大降低了成品钢板的冲击性能。
(6)划伤。
带钢在机组运行过程中新出现的划伤,是由于卷取辊的表面出现硬质的异物,或带钢的波浪急折棱与导板成线接触,或带钢在拆卷过程中拍打折头刮板等,使表面划出新的伤痕。
另外也有部分伤痕出现在热轧和卷取的过程中。
(7)带钢的划伤可分为上表面划伤和下表面划伤。
划伤的原料经冷轧后,在成品带钢表面,将形成宽而长的黑条。
带钢划伤深度超过带钢允许公差一半时,轧制后不能消除。
防止措施是经常检查机组的滚动部件和导板,维护好设备。
(8)压痕。
压痕是指带钢表面凹下去的压迹,压痕形成的原因是:焊接时焊渣没有吹净,被带钢带到张力辊上,而后在带钢表面压出了痕,张力辊在带钢表面滑动造成粘辊,使带钢表面造成压痕。
防止压痕的措施是及时清扫带钢表面的残留硬物和及时清理拉辊表面粘住的铁屑及硬物。
总之,上述带钢表面缺陷只要精心操作,严格执行酸洗工艺制度和操作规程,及时检修和维修设备是可以避免和减少的。
3.冷连轧机组对冷轧产品质量的影响。
带钢经过冷连轧机组后,因操作不当冷连轧工艺制度和其他一些设备的不良影响,往往会造成冷轧产品的不同缺陷。
这些缺陷主要有划伤、单边浪、双边浪、中间鼓、超薄、超厚、薄厚不匀、硌伤、辊伤、辊印和漏洞。
其中常见的缺陷主要是:辊伤、辊印、单边浪、中间鼓。
下面简述一下这些缺陷的产生原因及预防措施。
(1)划伤。
带钢在冷连轧机组运行过程中由于带钢表面与设备成线接触或带钢表面经过张力辊时,由于张力辊轴承故障,张力辊不能转动,致使带钢表面出现划伤,另外也有部分由于卷取机上料卷内圈没有卷紧,在轧制时会使带钢表面与表面产生摩擦,从而导致划伤。
防止措施是经常检查机组的滚动部件,时刻注意轧制时带钢是否与设备接触。
(2)辊伤辊印。
带钢在冷连轧机组运行过程中,由于操作员的操作不当或某些设备原因造成带钢在机架内跑偏断带,轻者使工作辊生成辊印,严重时造成工作辊粘钢,有时由于操作员在穿带时铁管碰到工作辊,也会造成工作辊的辊伤。
辊伤辊印表现在带钢表面是有周期性的,从而可以判断是哪个机架工作辊产生的。
防止措施是立即更换新的工作辊,方可轧制。
(3)硌伤。
带钢在冷连轧机组运行过程中,由于张力辊上有铁屑或其他硬物,从而使带钢产生硌窝。
防止措施是及时清擦张力辊。
(4)孔洞。
在带钢表面任意部位有带钢表面穿透现象(局部材料断裂)。
造成轧制成品无法正常使用销售,造成公司直接经济损失。
其主要原因是由于浇铸中夹杂、气泡、缩孔等,在以后的轧制过程中随着厚度的减薄使带钢局部破裂;还有就是由于轧制不均而导致局部周期性韧性撕裂;还有就是由于工作辊发生严重的辊伤辊印,在轧制时带钢经过其机架时使带钢内部组织发生变化,再经过后机架轧制时使带钢产生空洞,有时由于在轧制时卷取上的钢卷中掉入硬物,致使带钢硌漏。
防治措施:首先应查明原因,若是热轧问题,应及时换料轧制,将自身损失降到最低;并且联系厂家通知他们现场情况,让他们对生产过程进行严查改进;若是由于轧制不均而导致局部周期性韧性撕裂,应及时查找轧制不均的原因及机架,及时做压下率进行调整;若是最后一种,应立即停车更换工作辊和将钢卷中的硬物取出方可轧制。
(5)单边浪带钢在冷连轧机组运行过程中,由于工作辊的辊缝位置偏差大、成品机架的辊缝与来料断面吻合不好,造成延伸率大、轧辊局部过热或来料同板差较大,从而使带钢产生单边浪,单边浪严重时将使带钢跑偏使工作辊产生辊印辊伤。
防止措施是及时调整工作辊的辊缝偏差来调整带钢的板型、经常清理乳化液喷嘴、根据来料品质合理设计轧辊凸度。
(6)双边浪带钢在冷连轧机组运行过程中,由于机架轧制力压的过大或前张力较小工作辊弯辊力较小或工作辊的弧度较小,从而使带钢产生双边浪,双边浪严重时,工作辊可以将带钢轧漏,从而时工作辊产生辊印辊伤。
防止措施是将机架轧制力减小或加大前张力,或将机架工作辊的弯辊力加大,或更换弧度较大的工作辊,可以减小其双边浪。
(7)中间鼓。
带钢在冷连轧机组运行过程中,由于机架轧制力压的过小或前张力较大或工作辊的弯辊力较大或工作辊的弧度较大,从而使带钢产生中间鼓。
中间鼓较大时容易使正在运行的带钢发生断带。
防止措施是:将机架轧制力加大或减小前张力或合理使用轧机的正负弯辊或更换弧度较小的工作辊,可以减小其中间鼓。
即成品实际厚度或大于或小于目标厚度。
是由于测厚仪测量不准造成的。
防止措施是:定期校准测厚仪,及时清理测厚仪射源孔的异物。
(9)薄厚不匀。
即成品厚度的纵向波动较大。
是由于钢带在冷连轧机组运行过程中其机架间的张力波动,从而影响成品厚度的波动造成薄厚不均。
有时也由于酸洗来料的厚度的薄厚不均,从而影响冷轧成品的厚度不均。
防止措施是:控制好机架间的张力,严格把握来料质量(10)乳化液斑。
带钢表面呈灰色黑色或黄褐色打大小不等的痕迹。
出现在边部情况比较多,大多由于乳化液中含杂油量过多、轧机出口乳化液吹扫装置效果不良、出口设备不干净压缩空气质量比较低等因素造成。
防止措施是:控制设备漏油、改进吹扫装置以提高吹扫效果、提高压缩空气质量(降低露点、降低含油量)。
(11)夹杂。
夹杂有明显点状、块状、长条状或柳叶状且无规律性。
夹杂极容易引起轧机高速断带,其主要原因是热轧浇铸时混入非金属杂物或连铸保护渣进入钢中。
防止措施:及时换料轧制,将自身损失降到最低;并且联系厂家通知他们现场情况,让他们对生产过程进行严查改进。
氧化铁皮是带钢表面粘附着一层鱼鳞状、细条状、块状或弥散型点状的棕色或黑色物。
极容易引起轧机高速断带。
形成氧化铁皮的原因是由于热轧前面机架的高压水嘴堵塞、氧化铁皮等未吹扫干净而被轧入、高温卷取料时在酸洗拉矫时破鳞不够。
防止措施:及时换料轧制,将自身损失降到最低;并且联系厂家通知他们现场情况,让他们对生产过程进行严查改进。
(13)油泥。
油泥是在轧制过程中,长时间积留在牌坊顶部的油性沉积物落在运行的带钢上表面,经过轧制,基本粘贴在带钢的上板面。
防止措施:定期清理轧机牌坊及周边沉积物质。
(14)热划伤。
正常生产时,突然出项在带钢表面任意位置条状斑迹,无手感,造成其主要原因有可能是乳化液喷射不均匀,或长时间使用的轧辊表面老化造成。
防止措施:定期对乳化液喷嘴进行清理和对喷射梁角度或找出哪个机架的轧辊及时更换轧辊。
总之,上述冷轧带钢表面的缺陷,严重影响到冷轧产品的成材率,只要精心操作,严格按照冷轧工艺制度和操作规程,及时检修和维护好设备,是可以避免和减少的,从而提高冷轧产品的成材率,争取更大的利益。