确定重复性和再现性的指南
质量管理体系五种核心工具MSA

n
X
= i=1
Xi/n
5)计算重复性标准差(б重复性或称бr )
б重复性=
max(xi) – min(xi)
d*2
式中:d2* 可从d2* 表中查到,此时,g=1,m=n
6)计算偏倚
偏倚=观测到的平均测量值(x)– 参考值
7)计算平均值的标准误差бb
2024/7/21
бb = бr /
n
8)确定偏倚的t统计值 t = 偏倚/бb
d.确定对偏倚的统计t值
m : 子组客量
平均值的标准误差бb=бr / g g : 子组数量
2024/7/21
t=偏倚/бb e.确定置信度,一般要求为95%(即α=0.05)。
偏倚–d2〔бb(tv,1–α/2)〕/ d≤*20≤偏倚+d2〔бb(tv,1–α/2)〕/
பைடு நூலகம்
d*2
式中:d2,d2* ,v可在d*2 表中查到。
n
平均值X 标准差бr 平均值的标准误差бb
测量值 100
6.021
0.2048
0.0458
测量值
参考值=6.01,α=0.05,m=5,g=20, d2* =2.334,d2=2.326
统计的 t 值
df
显著的t值
偏倚
(2-有尾数的)
偏倚95%置信度区 间
下限 上限
0.2402
72. 7
1.993
再比如:当R&R为10%时,CP实为2, CP观为1.96 R&R为30%时,CP实为2, CP观为1.71 R&R为60%时,CP实为2, CP观为1.28
可以看出, CP观由1.96到1.28之间的区别就是由于测 量系统的不同所造成。 为此,我们要对测量系统进行分析,要识别测量系统 的普通原因和特殊原因,以便采取决策措施,使测量 系统的变差减小到最小程度,使得测量系统观测到的 过程变差值尽可能接近和真实地反映过程的变差值。 这就要求,测量系统的最大(最坏)的变差必须小于过 程变差或规范公差。
测量系统分析MSA--原理和通用方法

b= ∑y/n-a*(∑x/n)
R2=
[∑xy-∑x∑y/n]2 [∑x2-((∑x)2/n)]*[∑y2-((∑y)2/n)]
线性由最佳拟合直线的斜率而不是拟合优度(R2 )的值确定,斜率越低,线性越好。
分辨力对测量系统变差的影响
分 辨 力 合 适 的 控 制 图
0.145 0.144 0.143 0.142 0.141 0.14 0.139 0.138 0.137 0.136 0.135
0.02
0.015
0.01
0.005
0
0.14555(UCL) 控制上限
0.13571(LCL) 控制下限
0.1810(UCL) 控制上限
用规定的检测方式测量每个零件以确定其基准 值和确认包含了被检量具的工作范围;
让通常情况下使用该量具的操作人之一用该量 具测量每个零件12次;
计算每个零件平均值和偏移平均值; 计算回归直线和直线的拟合优度。
线性计算方法
Y=b+aX
其中:X=基准值;Y=偏倚;a=斜率
a=
∑xy-(∑x∑y/n) ∑x2-(∑x)2/n
再现性或评价人变差(AV或σo)由评价人的最 大平均差(XDIFF)乘以一个常数(K2)得出。 K2取决于量具分析中的评价人数量。评价人变 差包含设备变差,必须减去设备变差来校正。 AV=√[XDIFF×K2]2-(EV)2/n*r
n=零件数,r=试验次数
重复性和再现性——数据分析
测量系统变差重复性和再现性(R&R或σm)的 计算是将设备变差的平方与评价人变差的平方 相加并开方得出: R&R=√[(EV)2+(AV)2]
比较,确定测量系统的重复性是否适于应用。
测量系统分析(MSA)2

一.测量系统分析(MSA)21.定义:稳固性——测量系统在某连续时刻内测量同一基准或零件的单一特性时获得的测量值总变差。
2.使用均值和极差操纵图,该操纵图可提供方法以分离阻碍所有测量结果的缘故产生的变差〔一般变差〕和专门条件产生的变差〔专门缘故变差〕。
凡信号显现在操纵值外点均表现〝失控〞或〝不稳固〞。
3.研究:绘出标准〔样件〕重复读数X或R,图中失控信号即为需核准测量系统的标志。
4.操作要领:必须认真策划操纵图技术〔如取样时刻、环境等〕,以防样本容量、频率等导致失误信号。
5.稳固性改进①从过程中排除专门缘故——由超出的点反应。
②减少操纵限宽度——排除一般缘故造成的变差。
图2测量系统特性图二.偏倚1.定义:偏倚——测量结果的观看平均值与基准的差值。
2.操作方式:①对一件样件进行周密测量。
②由同一评判人用被评判单个量具测量同一零件至少十次。
③运算读数平均值。
④偏倚=基准值-平均值3.产生较大偏倚的缘故①基准误差②磨损的零件③制造的仪器尺寸不对④测量错误的特性⑤外表未正确校准⑥评判人使用仪器不正确。
三.重复性1.定义:重复性——由一个评判人采纳一种测量器具,多次测量同一零件的同一特性时获得的差值。
2.测量过程的重复性意味着测量系统自身的变异是一致的。
重复性可用极差图显示测量过程的一致性。
3.重复性或量具变差的估量:σe=5.15×R/d2d2——常数〔查表得〕与零件数量、试验次数有关。
5.15——代表正态分布的90%的测量结果。
四.再现性1.定义:再现性——由不同评判人采纳相同测量器具测量同一零件的同一特性时测量平均值的变差。
2.测量过程的再现性说明评判人的差异性是一致的。
假设评判人变异存在,那么每位评判人所有平均值将会不同,可采纳均值图来显示。
3.估量评判人标准偏差σo=5.15×R o/d2d2——常数〔查表得〕与零件数量、试验次数有关。
5.15——代表正态分布的90%的测量结果。
【MSA】确定重复性和再现性的指南-平均值和极差法

平均值和极差法(Xbar & R)是一种可同时对测量系统提供重复性和再现性的估计值的研究方法。
与单独的极差法不同,该方法允许将测量系统的变差分解成两个独立的部分:重复性和再现性,但不能确定它们两者的相互作用。
同时,基于评估者与零件/量具交互作用产生的变差也没有计入分析中。
进行研究尽管评价者的人数、测量次数及零件数量均可能会不同,但下面的讨论呈现进行研究的最佳情况。
参见图B6中的GRR数据表,详细的程序如下:1) 取得一个能代表过程变差实际或预期范围的样本,为n> 10个零件44的样本。
2) 给评价者编号为A、B、C等,并将零件从1到n进行编号,但零件编号不要让评价者看到。
3) 对量具进行校准,如果这是正常测量系统程序中的一部分的话。
让评价者A以随机顺序45测量n个零件,并将结果记录在第1行。
4) 让评价者B和C依次测量这些一样的n个零件,不要让他们知道别人的读值,然后将结果分别的记录在第6行和第11行。
5) 用不同的随机测量顺序重复以上循环,并将数据记录在第2、7和12行:注意将数据记录在适当的栏位中,例如:如果首先被测量的是零件7,然后将数据记录在标有零件7的字段中。
如果需要进行三次测量,则重复以上循环,并将数据记录在第3、8和13行中。
6) 当测量大型零件或不可能同时获得数个零件时,第4步到第5步将变更成以下顺序:让评价者A测量第一个零件并将读值记录在第1行;让评价者B测量第一个零件并将读值记录在第6行;让评价者C测量第一个零件并将读值记录在第11行。
让评价者A重新测量第一个零件并将读值记录在第2行;评价者B重新测量第一个零件并将读值记录在第7行;评价者C重复测量第一个零件并将读值记录在第12行。
如果需要进行三次测量,则重复以上循环,并将数值记录在第3、8和13行中。
7) 如果评价者处于不同的班次,可以使用一个替代的方法。
让评价者A 测量所有10个零件,并将读值记录在第1行;然后让评价者A按照不同的顺序重新测量,并把读值记录在第2行和第3行。
重复性和再现性分析
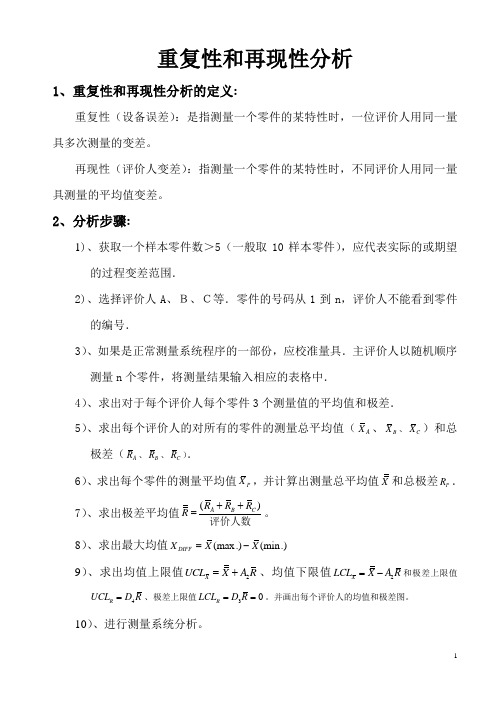
重复性和再现性分析1、重复性和再现性分析的定义:重复性(设备误差):是指测量一个零件的某特性时,一位评价人用同一量具多次测量的变差。
再现性(评价人变差):指测量一个零件的某特性时,不同评价人用同一量具测量的平均值变差。
2、分析步骤:1)、获取一个样本零件数>5(一般取10样本零件),应代表实际的或期望的过程变差范围.2)、选择评价人A 、B、C等.零件的号码从1到n ,评价人不能看到零件的编号.3)、如果是正常测量系统程序的一部份,应校准量具.主评价人以随机顺序测量n 个零件,将测量结果输入相应的表格中.4)、求出对于每个评价人每个零件3个测量值的平均值和极差.5)、求出每个评价人的对所有的零件的测量总平均值(A X 、B X 、C X )和总极差(A R 、B R 、C R ).6)、求出每个零件的测量平均值P X ,并计算出测量总平均值X 和总极差P R .7)、求出极差平均值()A B C R R R R ++=评价人数。
8)、求出最大均值(max.)(min.)DIFF X X X =-9)、求出均值上限值2X UCL X A R =+、均值下限值2X LCL X A R =-和极差上限值4R UCL D R =、极差上限值30R LCL D R ==。
并画出每个评价人的均值和极差图。
10)、进行测量系统分析。
①重复性—设备变差(EV ) 1EV R K =⨯②再现性—评价人变差(A V )AV =③重复性和再现性(R&R )&R R =④零件变差(PV )3p PV R K =⨯⑤总变差(TV )TV =⑥%总变差(TV )%100(/)EV EV TV =⨯%100(/)AV AV TV =⨯%&100(&/)R R R R TV =⨯%100(/)PV PV TV =⨯有效分辨率=1.41(PV / R&R )11)、量具重复性和再现性接收标准(之一)①低于10%误差——测量系统可接收。
量具测量值重复性与再现性的评定

量具测量值重复性与再现性的评定1、相关概念1、重复性:传统上把重复性看作“评价人内变异性”。
重复性是指由一个评价人,用同一种测量仪器,多次测量同一零件的同一特性时获得的测量变差。
它是设备本身固有的变差和性能,通常指设备变差,尽管这样容易使人误解。
但事实上,重复性是在确定的测量条件下连续试验得到的普通原因(随机变差)变差。
当测量环境固定和已定义时,即确定了-固定的零件、仪器、标准、方法、操作者、环境和假设条件时,对于重复性最佳的术语是系统内部变差。
除了设备内部变差以外,重复性也包括在特定测量误差模型下任何情况下的内部变差。
2、再现性:传统上把再现性看作“评价人之间”的变异。
再现性通常定义为由不同的评价人,采用相同的测量仪器,测量同一零件的同一特性时测量平均值的变差。
手动仪器受操作者技术影响常常是实际情况,然而,在测量过程(即自动操作系统)中操作者就不是主要的变差源了。
由于这个原因,为此,再现性被看作是测量系统之间或测量条件之间的平均变差。
2、数据来源本案例数据节选自深圳市佳宝隆科技有限公司《重复性与再现性分析报告》,为避免重复,笔者采取了其中的前两次测定,结果如下:2 32.00 31.99 31.99 32.00 31.98 31.99 32.00 31.99 31.99 32.00在该实验中,n=10,k=3,m=2。
完成测量任务后应有60个数据,下面将对这些数据进行分析。
3、测量系统评定1、均值极差法(1)软件操作:统计-质量工具-量具研究-量具R&R(交叉)研究(2)运用minitab软件绘制均值控制图与极差控制图结果:(3)结果分析从均值控制图中我们可以看到,30个均值点中有13个处在控制界限外面,达到了65%,大于50&,而从极差控制图中我们可以看到其是受控的,所以我们认为实验中的重复测量数据能用来做出零件间的标准差的估计,同时也说明该测量系统都能够很好的反应零件的区别。
重复性和再现性
量具重复性与再现性分析:GR&R 是用来检定检测产品的人员是否具备识别产品特性的能力,正常的产品是否会误判,不正常的产品是否会漏判,也就是检定“检测系统是否正常”的一个工具。
GR&R是研究重复性和再现性的,是计量型分析。
1.简称:重复性(EV)(equipment variance)设备偏差、(再现性AV)(appriser variance)人員偏差、产品偏差(PV)(products variance),2.重复性(Repeatability):重复性是用本方法在正常和正确操作情况下,由同一操作人员,在同一实验室内,使用同一仪器,并在短期内,对相同试样所作多个单次测试结果,在95%概率水平两个独立测试结果的最大差值。
在中国仪器中当测量条件是在以下4个状况下实验时,相同的待测量的测量结果有一致性的称为重复性,4个条件如下:a、相同的测量环境b、相同的测量仪器及在相同的条件下使用c、相同的位置d、在短时间内的重复3.再现性(Reproducibility)是指两个不同的实验室对同一物料进行测定两个分析结果接近的程度.再现性的值总是大于或等于重复性,因为再现性的测量结果把重复性引起的偏差考虑进去了。
在很多实际工作中,最重要的再现性指由不同操作者、采用相同的方法、仪器,在相同的环境条件下,检测同一被测物的重复检测结果之间的一致性,即检测条件的改变只限于操作者的改变。
也就是说别人用你说的方法和仪器也能做出同样的结果来,这就是试验的再现性。
当然,这样的试验就叫做再现性实验。
4.测量结果的重复性:是指“在相同测量条件下,对同一被测量进行连续多次测量所得结果之间的一致性”。
上述定义中的“一致性”是定量的,可以用重复性条件下对同一量进行多次测量所得结果的分散性来表示。
而表示测量结果分散性的量,最为常用的是实验标准。
重复性条件。
质言之,就是在尽量相同的条件下,包括程序、人员、仪器、环境等,以及尽量短的时间间隔内完成重复测量任务。
测量系统分析---5 重复性和再现性 GRR
EV---Equipment Variation 设备变差----重复性: AV---Appraiser Variation 评价者变差---再现性: PV---Part Variation 零件的变差--------产品偏差:
与评价人之间的交互作用和由于量具造成的重复误差。但 计算复杂,需掌握一定程度的统计学知识。
-7-
第五章
重复性和再现性
GRR分析方法---极差法
例:2个评价人对5个零件进行测量。在研究中,两个评价人各将每 个零件测量一次。每个零件的极差是评价人A获得测量值和B获得 测量值之间的绝对差值。计算极差的和与平均极差。通过将平均极 差均值乘以1/d2*得到标准偏差.
计算A评价者测试数据的平均值 计算B评价者测试数据的平均值
计算C评价者测试数据的平均值 计算全部评价者所测数据的平均值 计算单个零件的平均值 计算零件全距Rp 计算最大与最小量测值班的差异 计算零件全距的极差R的平均值
-12-
6 7
8 9 10 11
=Max(Xa,Xb, Xc)-Min(Xa,Xb,Xc) =( Ra + Rb + Rc ) / 3
第五章
重复性和再现性
GRR分析方法
● 极差法 (全距法) 特点:简单快捷,能提供整体大概概况 ● 均值极差法(全距及平均值法)(包括控制图法) 特点:可将测量系统的变差分成两个部分-----重复性和再
现性,而不是他们的交互作用
● ANOVE法--方差分析法(变异数分析法) 特点:是一种标准统计技术,可算出零件、评价人、零件
重复性和再现性汇总
GRR 75.5% 过程标准差
现在已确定了这测量系统的%GRR,就应该对这 结果进行解释。在表7中,%GRR被确定为75.7%, 于是结论是需对测量系统进行改进。
平均值和极差法
平均值和极差法(X&R)是一种可 同时对测量系统提供重复性和再现 性的估计值的研究方法。与极差法 不同,这方法允许将测量系统的变 差分解成两个独立的部分:重复性 和再现性,但不能确定它们两者的 相互作用。
7)如果评价人处于不同的班次,可以使用一个替代 的方法。让评价人A测量所有10个零件,将将读值记 录在第1行;然后让评价人A按照不同的顺序重新测 量,并把读值记录在第2行和第3行。评价人B和评价 人C也同样做。
量具重复性和再现性数据收集表
评价人/ 测量次数 1 2 3 A 1 2 3 零 1 0.29 0.41 0.64 2 -0.56 -0.68 -0.58 3 1.34 1.17 1.27 4 0.47 0.50 0.64 5 -0.80 -0.92 -0.84 件 6 0.02 -0.11 -0.21 7 0.59 0.75 0.66 8 -0.31 -0.20 -0.17 9 2.26 1.99 2.01 10 -1.36 -1.25 -1.31 平均值
4
5 6 7 8
平均值
极 差 B 1 2 3 0.08 0.25 0.07 -0.47 -1.22 -0.68 1.19 0.94 1.34 0.01 1.03 0.20 -0.56 -1.20 -1.28 -0.20 0.22 0.06 0.47 0.55 0.83 -0.63 -0.08 -0.34 1.80 2.12 2.19 -1.68 -1.62 -1.50
极差法
质量管理体系五种核心工具MSA培训课件
统计的t 值
显著的t值 df
偏倚
偏倚95%置信度区 间
(2-有尾数的)
下限 上限
测量值 0.1153 10.8
2 .206
0.0067 0.1215 0.1319
2.确定稳定性的指南
1) 取得一样件并建立其可追溯到相关标准的参考值。如 果无法取 得这样件,则选择一件落在生产测量范围中 间的生产零件,作为基准样件以进行稳定性分析。希 望拥有位于预期测量结果的下限,上限和中限位置的 三个基准件。要求对每种基准件单独的进行测量和画 控制图。
选取了生产过程输出范围中 接近中间值的一个零件.该零 6.0
件在计量测试室经n≥10测 5.7
量,并计算这n个读值的平均
值为6.01为其参考值。
1.0
小组每班测量该零件5次,共 0.5
测了四周(20个子组)。
0
数据收集,计算后,作 X -R控
制图。如:右图
稳定性 X -R控 制图
UCL 6.627
0
g为零件数量
9)对于已知的x0, α置信度区间为:
涵盖了这量具的工作量程。 3)让经常使用该量具的操作者测量每个零件m≥10次(盲测
法)。
结果分析—图示法
4)计算每个零件每次测量的偏倚,以及每个零件的偏倚平均 值。
偏倚ij= Xij –Xi
偏倚i =
m
jΣ=1偏倚ij
m
式中: Xi —第i个零件的参考值 Xij —第i个零件的第j次测量值
5)在线性图上画出相对于参考值的每个偏倚值及偏倚平均值
3.对测量系统的五性分析
位置变差
·偏倚 ·稳定性 ·线性
宽度变差 ·重复性 ·再现性
对测量系统研究分析可供: --接受新测量设备的标准 --两个测量装置的比较 --测量设备维修前后的比较,计算过程变差及生产过程 可接受 性的水平
- 1、下载文档前请自行甄别文档内容的完整性,平台不提供额外的编辑、内容补充、找答案等附加服务。
- 2、"仅部分预览"的文档,不可在线预览部分如存在完整性等问题,可反馈申请退款(可完整预览的文档不适用该条件!)。
- 3、如文档侵犯您的权益,请联系客服反馈,我们会尽快为您处理(人工客服工作时间:9:00-18:30)。
极差法
极差法是一种经修正的计量型量具研究方法, 它能对测量变差提供一个快速地的近似值。 这方法只能对测量系统提供变差的整体情况, 不能将变差分解成重复性和再现性。它通常 用来快速地检查以验证GRR是否有变化。 使用这方法能够潜在的检测出测量系统为不 可接受的概率是:对于抽样次数是 5 的情况下, 机率为80%;对于抽样次数为10的情况下, 机率为90%。
7)如果评价人处于不同的班次,可以使用一个替代 的方法。让评价人A测量所有10个零件,将将读值记 录在第1行;然后让评价人A按照不同的顺序重新测 量,并把读值记录在第2行和第3行。评价人B和评价 人C也同样做。
量具重复性和再现性数据收集表
评价人/ 测量次数 1 2 3 4 5 6 7 8 9 10 11 12 13 14 15 16 17 18 19 A 1 2 3 平均值 极 差 B 1 2 3 平均值 极 差 C 1 2 3 平均值 极 差 零件 平均值
确定重复性和再现性的指南
A
C GRR
B
可以使用不同的方法进行计量型量具的研究。 本节将详细讨论三种可接受的方法。它们是:
极差法(Range method)
均值—极差法(Average and Range method)
方差分析法(ANOVA method)
除极差法之外,其它方法所用的研究数据的设计
0 . 07 0 . 058 1 . 19
过程标准差
% GRR
0 . 0777 从之前的研究中取得
75 . 5 %
GRR 100 * 过程标准差
表7:量具研究(极差法)
为了确定测量变差占过程标准差的多少 百分比, 可通过把GRR乘以 100,再除以过程标准差, 即可将GRR转化成百分数。在以上范例中(参 见表 7 ),该特性的过程标准差为 0.0777 ,因 此:
% GRR GRR 100 * 过程标准差 75 . 5 %
现在已确定了这测量系统的%GRR,就应该对这 结果进行解释。在表7中,%GRR被确定为75.7%, 于是结论是需对测量系统进行改进。
平均值和极差法
平均值和极差法(X&R)是一种可 同时对测量系统提供重复性和再现 性的估计值的研究方法。与极差法 不同,这方法允许将测量系统的变 差分解成两个独立的部分:重复性 和再现性,但不能确定它们两者的 相互作用。
零件 1 2 3 4 5
评价人A 0.85 0.75 1.00 0.45 0.50
R
评价人B 0.80 0.70 0.95 0.55 0.60
极差(A,B) 0.05 0.05 0.05 0.10 0.10
极差平均值
5
Ri
0 . 35 5
0 . 07
GRR R R *源自 d 1 . 19 2
4)让评价人B和C依次测量这些一亲的n个零件, 不要让他们知道别人的读值;然后将结果分别 的记录在第6行和第11行。
5)用不同的随机测量顺序重复以上循环,并将数 据记录在第2、7和12行;注意将数据记录在适 当的栏位中,例如:如果首先被测量的是零件 7,然后将数据记录在标有零件7的栏位中。如 果需要进行三次测量,则重复以上循环,并将 数据记录在第3、8和13行中。 6)当测量大型零件或不可能同时获得数个零件时, 第3步到第5步将变更成以下顺序:
R
零 1 0.29 0.41 0.64 2 -0.56 -0.68 -0.58 3 1.34 1.17 1.27 4 0.47 0.50 0.64 5 -0.80 -0.92 -0.84
件 6 0.02 -0.11 -0.21 7 0.59 0.75 0.66 8 -0.31 -0.20 -0.17 9 2.26 1.99 2.01 10 -1.36 -1.25 -1.31 平均值
都很相似。如所呈现的,所有的方法在它们的分 析时均忽视了零件内部变差(如:在第四章,第A 节所讨论的圆度、锥度直径、平面度等。) 但是,整个测量系统不仅包括量具本身及其相关 的偏倚、重复性等,还包括被测零件之间的变差。 如何处理零件内部的变差,需要取决于对零件使 用意图以及测量目的的合理理解。 最后,本章节中的所有技术均以过程处于统计的 稳定状态这一前提条件。 尽管再现性通常被解释为评价者变差,但有些情 况下该变差会出其它原因造成。例如对重复性研 究是必要的,对于一些过程中没有人为评价人的 测量系统,如果所有的零件由相同的设备来搬运、 夹具及测量,则再现性为零。
X R
0.08 0.25 0.07 -0.47 -1.22 -0.68 1.19 0.94 1.34 0.01 1.03 0.20 -0.56 -1.20 -1.28 -0.20 0.22 0.06 0.47 0.55 0.83 -0.63 -0.08 -0.34 1.80 2.12 2.19 -1.68 -1.62 -1.50
用极差法进行研究时通常选用两个评价 人与五个零件。在这种研究中,两个评 价人测量每个零件一次。由评价人A测量 的每个零件的极差与由评价人B测量的每 个零件的极差是决然不同的。计算极差 之和以及极差的平均值(R):总测量变 差即为极差的平均值乘以1/d2*,d2*可在 附录 C 中查到,取 m=2 ,且 g= 零件的数 量。
进行研究 尽管评价人的人数、测量次数及零件数量 均可会不同,但下面的讨论呈现进行研究 的最佳情况。参见图12中的GRR数据表, 详细的程序如下: 1)取得一个能代表过程变差实际或预期范围的样 本,为n>5个零件的样本。 2)给评价人编号为A、B、C等,并将零件从1到 n进行编号,但零件编号不要让评价人看到。 3)对量具进行校准,如果这是正常测量系统程序 中的一部分的话。让评价人A以随机顺序测量 n个零件,并将结果记录在第1行。
让评价人A测量第一个零件并将读值记录在第1行; 让平价人B测量第一个零件并将读值记录在第6行; 让评价人C测量第一个零件并将读值记录在第11行。
让评价人A重新测量第一个零件并将读值记录在第2行; 评价人B重新测量第一个零件并将读值记录在第7行; 评价人C重复测量第一个零件并将读值记录在第12行。 如果需要进行三次测量,则重复以上循环,并将数值 记录在第3、8和13行中。