湿硫化氢环境腐蚀与防护
ISO15156腐蚀介绍酸性环境选材

硫化氢引起氢损伤的腐蚀类型
硫化氢应力腐蚀和氢致开裂是一种低应力破坏,甚至 在很低的拉应力下都可能发生开裂。一般说来,随着钢材强 度(硬度)的提高,硫化氢应力腐蚀开裂越容易发生,甚至在 百分之几屈服强度时也会发生开裂。
硫化物应力腐蚀和氢致开裂均属于延迟破坏,开裂可 能在钢材接触H2S后很短时间内(几小时、几天)发生,也可 能在数周、数月或几年后发生,但无论破坏发生迟早,往 往事先无明显预兆。
硫化氢引起氢损伤的腐蚀类型
(3) 硫化物应力腐蚀开裂(SSCC)
湿H2S环境中腐蚀产生的氢原子渗入钢的内部固溶于晶 格中,使钢的脆性增加,在外加拉应力或残余应力作用下 形成的开裂,叫做硫化物应力腐蚀开裂。工程上有时也把 受拉应力的钢及合金在湿H2S及其它硫化物腐蚀环境中产生 的脆性开裂统称为硫化物应力腐蚀开裂。SSCC通常发生在 中高强度钢中或焊缝及其热影响区等硬度较高的区域。
5. 选择性腐蚀:合金在腐蚀过程中,腐蚀介质不 是按合金的比例侵蚀,而是发生了其中某种成分的 选择性溶解,使合金的机械强度下降,这种腐蚀形 态称之为成分选择腐蚀,或称为选择性腐蚀。
灰口铸铁石Байду номын сангаас化和黄铜脱锌。
常见的局部腐蚀形态
6. 应力腐蚀开裂(SCC, 简称应力腐蚀):它是在 拉应力和特定的腐蚀介质共同作用下发生的金属材 料的破断现象。
硫化氢(H2S)的特性及来源
H2S在石油工业中的来源
油气中硫化氢的来源除了来自地层以外,滋长的硫酸 盐还原菌转化地层中和化学添加剂中的硫酸盐时,也会释放 出硫化氢。
H2S在石化工业中的来源
石油加工过程中的硫化氢主要来源于含硫原油中的有 机硫化物如硫醇和硫醚等,这些有机硫化物在原油加工过程 进行中受热会转化分解出相应的硫化氢。
硫化氢腐蚀与防护相关知识

硫化氢腐蚀与防护相关知识1. 硫化氢腐蚀的预防措施1.1. 选用抗硫化氢材料抗硫化氢材料主要是指对硫化氢应力腐蚀开裂和氢损伤有一定抗力或对这种开裂不敏感的材料。
同时采用低硬度(强度)和“完全淬火+回火”处理工艺对材料抗硫化氢腐蚀是有利的。
美国国家腐蚀工程师学会(NACE)标准MR-01-75(1980年修订)中规定:含硫化氢环境中使用的钻杆、钻杆接头、钻铤和其它管材的最大硬度不许高于HRC22;钻杆接头与钻杆的焊接及热影响区应进行“淬火+595℃以上温度的回火”处理;对于最小屈服强度大于655MPa的钢材应进行“淬火+回火”处理,以获得抗硫化物应力腐蚀开裂的最佳能力。
1.2. 抗H2S腐蚀钢材的基本要求⑴成分设计合理:材料的抗H2S应力断裂性能主要与材料的晶界强度有关,因此常常加入Cr、Mo、Nb、Ti、Cu等合金元素细化原始奥氏体晶粒度。
超细晶粒原始奥氏体经淬火后,形成超细晶粒铁素体和分布良好的超细碳化物组织,是开发抗硫化物应力腐蚀的高强度钢最有效的途径。
⑵采用有害元素(包括氢,氧,氮等)含量很低纯净钢;⑶良好的淬透性和均匀细小的回火组织,硬度波动尽可能小;⑷回火稳定性好,回火温度高(>600℃);⑸良好的韧性;⑹消除残余拉应力。
1.3. 添加缓蚀剂实践证明合理添加缓蚀剂是防止含H2S酸性油气对碳钢和低合金钢设施腐蚀的一种有效方法。
缓蚀剂对应用条件的选择性要求很高,针对性很强。
不同介质或材料往往要求的缓蚀剂也不同,甚至同一种介质,当操作条件(如温度、压力、浓度、流速等)改变时,所采用的缓蚀剂可能也需要改变。
用于含H2S酸性环境中的缓蚀剂,通常为含氧的有机缓蚀剂(成膜型缓蚀剂),有胺类、米唑啉、酰胺类和季胺盐,也包括含硫、磷的化合物。
如四川石油管理局天然气研究所研制的CT2-l和CT2-4油气井缓蚀剂及CT2—2输送管道缓蚀剂,在四川及其他含硫化氢油气田上应用均取得良好的效果。
1.4. 控制溶液pH值提高溶液pH值降低溶液中H+含量可提高钢材对硫化氢的耐蚀能力,维持pH值在9~11之间,这样不仅可有效预防硫化氢腐蚀,又可同时提高钢材疲劳寿命。
硫化氢基本知识与防护
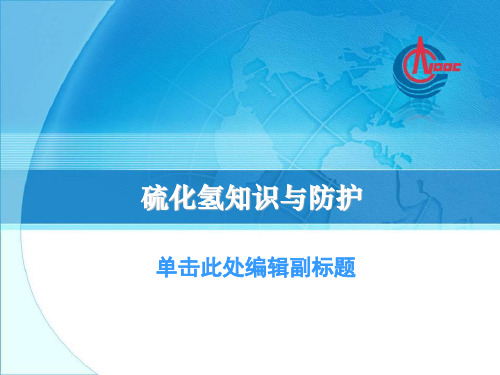
四、应急与急救
应急措施
启动油气泄漏及防硫化氢应急程序 。
寻源堵漏人员佩戴好呼吸器或防毒面具。 应急集合区:1、2号救生艇旁集合区。必要时,进生活楼内部集合。
集合地点两大特点:高处、上风处。
谢
谢 !
13
易燃,与空气混合能形成爆炸性混合物,遇明火、高热能引起燃烧爆炸。
一、硫化氢知识
硫化氢的危害
浓度百万分率 (PPM) 0.13-4.6 健康危害 可闻到一种令人讨厌的 臭皮蛋气味 对人有毒;需要带防护 面罩或呼吸器 眼部呼吸区域有明显刺 激感 很快使人失去嗅觉 浓度百万分率 (PPM) ﹥300 健康危害 可立刻威胁生命和健 康 破坏人体大脑呼吸中 心,15分钟内导致失 去知觉 迅速失去知觉,停止 呼吸,如不立即抢救 ,将导致死亡 如不迅速抢救的话会 立刻失去知觉并死亡
三、硫化氢防护与安全控制
油田防硫化氢措施
配备呼吸器、防硫化氢防毒面具。 防硫化氢应急程序。 针对硫化氢中毒的急救药品。 对可能含有硫化氢的地点进行定点检测。 硫化氢探测系统。
四、应急与急救
急救处理
现场抢救极为重要,因空气中含极高硫化氢浓度时常在现场引起 多人电击样死亡 。 应立即使患者脱离现场至空气新鲜处。有条件时立即给予吸氧。现场抢 救人员应有自救互救知识,以防抢救者进入现场后自身中毒。 维持生命体征。对呼吸或心脏聚停者应立即施行 心肺脑复苏术。对在事 故现场发生呼吸骤停者如能及时施行工呼吸,则可避免随之而发生心脏 骤停。 以对症、支持治疗为主。高压氧治疗对加速昏迷的复苏和防治脑水种有 重要作用,凡昏迷患者,不论是否已复苏,均应尽快给予高压氧治疗, 但需配合综合治疗。
口腔吸入、皮肤接触
硫化氢进入人体,与血液中的溶解氧发生作用,使人体器官失氧
柴油加氢装置的低温湿硫化氢腐蚀与防护
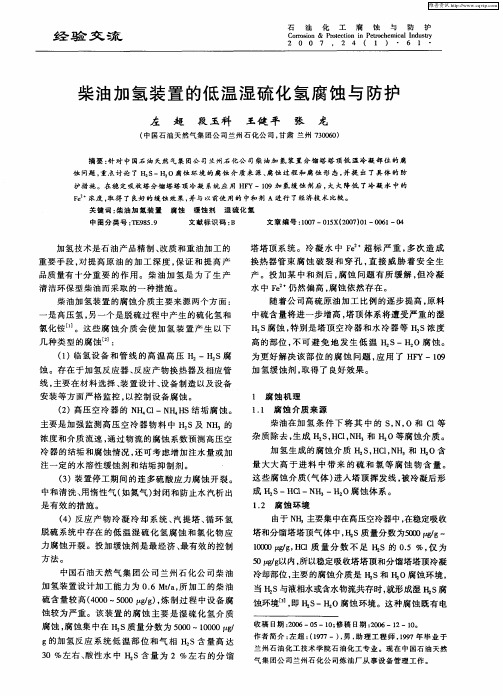
塔塔 顶 系统 。冷 凝 水 中 F2 超 标 严 重 , e’ 多次 造 成
换热 器管 束 腐 蚀 破 裂 和 穿 孔 , 接 威 胁 着 安 全 生 直 产 。投 加 某 中 和剂 后 , 腐蚀 问题 有 所缓 解 , 冷 凝 但 水 中 ’ 仍然 偏高 , 腐蚀 依然 存在 。 随着 公 司高 硫原 油加 工 比例 的逐步 提高 , 原料 中硫含 量 将进 一步增 高 , 塔顶 体系 将遭受 严重 的湿 Hs 蚀 , '腐 特别 是塔 顶 空冷 器 和水 冷器 等 H s浓度 ' 高 的部位 , 可避 免 地 发 生 低 温 H s—H 0腐 蚀 。 不 , ,
脱硫 系统 中存在 的低 温 湿 硫 化 氢腐 蚀 和 氯化 物 应 力腐 蚀 开裂 。投 加缓蚀 剂是 最经 济 、 最有效 的控制
方法。
中国石油 天然 气集 团公 司兰 州 石化 公 司柴 油
冷却部位 , 的腐蚀介 质是 s和 0腐 蚀环境 , 主要 当 s与液相水或含水物流共存时 , 成湿 H s 就形 2 腐
柴油 加 氢 装 置 的低 温 湿 化 氢 腐 蚀 与 防护 硫
左 超 段 玉科 王健 平 张 龙
( 国石 油 天然 气 集 团 公 司 兰 州 石 化 公 司 , 肃 兰 州 706 ) 中 甘 300
摘 要 : 对 中 国石 油 天然 气集 团公 司兰 州石 化 公 司 柴 油 加 氢 装 置 分 馏 塔 塔 顶 低 温 冷 凝 部 位 的 腐 针 蚀 问题 , 点讨 论 了 H S ’ 重 , —H O腐蚀 环 境 的 腐 蚀 介 质 来 源 、 蚀 过 程 和 腐 蚀 形 态 , 提 出 了具 体 的 防 腐 并 护措 施 。在 稳 定 吸 收 塔 分 馏 塔 塔 顶 冷 凝 系统 应 用 H Y一19加 氢缓 蚀 剂 后 , 大 降 低 了冷 凝 水 中 的 F 0 大 F2 e 浓度 , 得 了 良好 的 缓 蚀 效 果 , 与 以前使 用 的 中和 剂 A进 行 了经 济 技 术 比较 。 取 并
湿硫化氢环境中设备应力腐蚀分析及控制
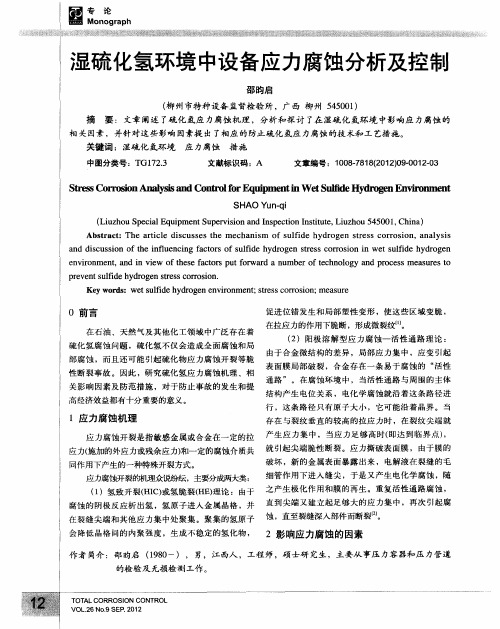
物 力 蚀 裂 利 元 有i nPs 。 当 料 受 超 屈 极 值 , 会 腐 应 腐 开 不 的 素 N M、和 等 因 材 所 譬 值 过 服 限 时 才 对 蚀 、
e v r n n , d i i w ft e e f c o s p t o wa d a n m b ro c n l g n r c s a u e o n io me t a v e o s a t r u r r u e ft h o o y a d p o e s me s r st n n h f e
全面 腐 蚀 控 制
第2 卷第9 0 月 6 期2 1 年9 2
豳 豹
3 1材 料控 制 _ 要严格控制工作环境中的H S 含量 ,按 照有关标
( )选择 合适强度和硬度的材料 。随着材料强 准的规定 ,使硫化氢分压小 于30 a 1 5 P ,另外也可以加
度 的提 高 ,应力 腐蚀破 裂的敏感 性也提 高 ,破 裂临 入一定的缓蚀剂来延缓其腐蚀速率。
会 造成 其化学成 分 、显 微组织 、强度 、硬度 、韧性 在水 中的H s z溶解度大于等于1 0 ; 0×1~ 等不 同 ,因此 ,影响硫 化氢应 力腐蚀 的程 度也会 不 同。硫化氢应 力腐蚀开裂的影响因素主要有 :
, ( )冶金 因素 :金相组织 、化学成分 、强度、 1 硬度 、夹杂和缺 陷 ;
a d d s u so fte i f e c n a t r fs l d y r g n sr s or so n we u fd y r g n n ic si n o h n l n ig fco so u f e h d o e te sc ro i n i ts l e h d o e u i i
部分炼油装置湿硫化氢的腐蚀与工艺防腐蚀

素和腐蚀 的控制措施等方 面进行 了较为详 细的介绍。
关 键词 : 硫 化 氢 湿 腐蚀 腐蚀机理 防 腐 蚀措 施
中图分类号 :E 8 . T 95 9
王菁辉 赵文轸 ’
( .西安交通大学材料科学与工程学院 , 1 陕西 西安 7 04 ; 10 9
2 .中国石化集 团洛 阳石油化工工程公 司, 河南 洛ห้องสมุดไป่ตู้ 4 10 ) 7 0 3
摘 要: 文章主要就 H 1 2 C 一H s—H O, C 2 H N—H2 s—H O, 2 2 H S—H2 O和 C 2 O 一H2 s—H O等湿硫化 2
F + c Fc + 2为控制性的腐蚀反应) e H l eI H ( 2
F + 2一 Fs’ + C Fc2 2( e H s ÷ e L H l e l+H s 为加速
腐蚀的反应 )
13 腐蚀部 位 .
H 1 H S H O腐蚀体系发生 的部位主要在 C一 — 低温部位( 初馏塔顶及其冷凝冷却系统 、 常压塔顶 部的 5 层塔盘、 塔体和挥发线及冷凝冷却系统 、 减 压塔 顶及 其冷凝 冷 却 系统 ) 催化 重 整 的加 氢 预处 ;
理 的低温 系统 ; 柴油加 氢 和加氢 裂化 的低 温系统 等
原 油 中的杂质 包括 硫 、 、 氮 氧和无 机盐 、 环烷酸 等一 系列物质 。其 中 的无 机盐 由于 炼 油工 艺 过程 中加入 的水 而使无 机盐包 括氯 化钠 、 氯化钙 和氯化
镁等在较高温度下发生水解而产生氯化氢 以及原 油中的有机氯化物加热分解产生氯化氢 , 原油中本
湿硫化氢腐蚀简介
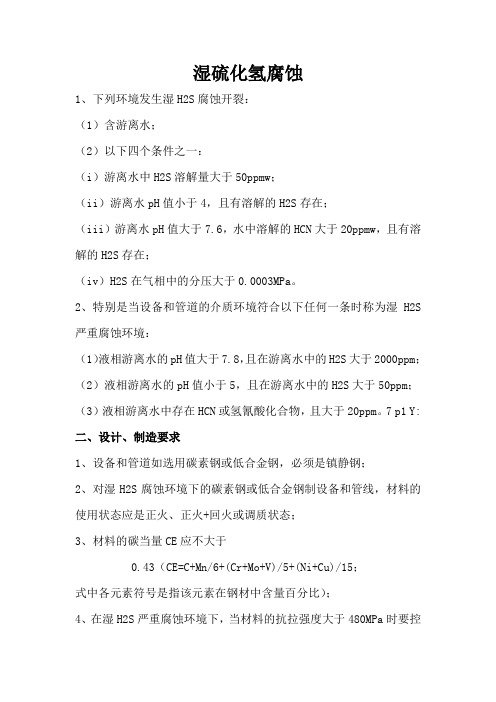
湿硫化氢腐蚀1、下列环境发生湿H2S腐蚀开裂:(1)含游离水;(2)以下四个条件之一:(i)游离水中H2S溶解量大于50ppmw;(ii)游离水pH值小于4,且有溶解的H2S存在;(iii)游离水pH值大于7.6,水中溶解的HCN大于20ppmw,且有溶解的H2S存在;(iv)H2S在气相中的分压大于0.0003MPa。
2、特别是当设备和管道的介质环境符合以下任何一条时称为湿H2S 严重腐蚀环境:(1)液相游离水的pH值大于7.8,且在游离水中的H2S大于2000ppm;(2)液相游离水的pH值小于5,且在游离水中的H2S大于50ppm;(3)液相游离水中存在HCN或氢氰酸化合物,且大于20ppm。
7 p1 Y:二、设计、制造要求1、设备和管道如选用碳素钢或低合金钢,必须是镇静钢;2、对湿H2S腐蚀环境下的碳素钢或低合金钢制设备和管线,材料的使用状态应是正火、正火+回火或调质状态;3、材料的碳当量CE应不大于0.43(CE=C+Mn/6+(Cr+Mo+V)/5+(Ni+Cu)/15;式中各元素符号是指该元素在钢材中含量百分比);4、在湿H2S严重腐蚀环境下,当材料的抗拉强度大于480MPa时要控制其S含量不大于0.002%,P含量不大于0.008%,Mn含量不大于1.30%,且应进行抗HIC性能试验或恒负荷拉伸试验。
5、在湿H2S环境下,应尽量少选择焊接。
如采取焊接,原则上应进行焊后消除应力热处理,热处理温度应按标准要求取上限。
6、热处理后碳素钢或碳锰钢焊接接头的硬度应不大于HB200,其它低合金钢母材和焊接接头的硬度应不大于HB237;7、热加工成形的碳素钢或低合金钢制管道元件,成形后应进行恢复力学性能热处理,且其硬度不大于HB225;8、冷加工成形的碳素钢或低合金钢制设备和管道元件,当冷变形量大于5%时,成形后应进行消除应力热处理,且其硬度不大于HB200。
但对于冷变形量不大于15%且硬度不大于HB190时,可不进行消除应力热处理;9、接触湿硫化氢环境碳素钢螺栓的硬度应不大于HB200,合金钢螺栓的硬度应不大于HB225;10、铬钼钢制设备和管道热处理后母材和焊接接头的硬度应不大于HB225(1Cr-0.5Mo、1.25Cr-0.5Mo)、HB235(2.25Cr-1Mo、5Cr-1Mo)和HB248(9Cr-1Mo);11、铁素体不锈钢、马氏体不锈钢和奥氏体不锈钢的母材和焊接接头的硬度应不大于HRC22,其中奥氏体不锈钢的碳含量不大于0.10%,且经过固溶处理或稳定化处理;12、双相不锈钢的母材和焊接接头的硬度应不大于HRC28,其铁素体含量应在35-65%的范围内;.13、容器内在焊接接头两侧50mm范围内的表面进行防护,可在表面喷锌、喷铝并用非金属涂料封闭的方法;14、不使用承插焊形式的管件;15、结构上应尽量避免应力集中;16、设备壳体或卷制管道用钢板厚度大于12mm时,应按JB/T4730进行超声波检测,符合Ⅱ级要求。
硫化氢金属腐蚀

精选ppt
14
A、金相组织
索氏体中碳化物呈均匀球形分布者,抗H2S腐 蚀好,珠光体的抗硫性能次之,马氏体最差;
焊接处金属组织呈马氏体,缺陷多,易聚集氢
分子,造成严重氢脆。
因此,在H2S环境的钢材设备要尽量避免损伤 表面或对设备进行冷加工,尽量减少残余应力。
• 氢脆和硫化氢应力腐蚀破裂是呈脆性破坏,在形式 上的特点是产生裂纹,且裂纹的纵深比宽度大几个 数量级,裂纹有穿晶裂纹和晶间裂纹。
精选ppt
7
• 它的发生一般要具备三个基本条件:
• 一定的拉应力、敏感材料和特定的环境
• 这种破坏有如下特点:
• ⑴破裂断口平整无塑性变形;
• ⑵在拉应力时才产生,且主裂纹的方向一般 总是和拉应力方向垂直;
精选ppt
20
2、加入缓蚀剂
原理:金属表面氧化生成钝化膜或改变 金属腐蚀电位起保护作用。
精选ppt
21
• 3、控制溶液的PH值
提高溶液PH值降低溶液中H+含量,可提 高钢材对硫化氢的耐腐蚀能力,维持PH 值在9~11之间,不仅可有效预防硫化氢 腐蚀,又可同时提高钢材疲劳寿命。
• 4、减少硫化氢溶液有管材的接触时间
精选ppt
12
3、硫化氢浓度 腐
蚀
一般浓度越高腐蚀速度
速 度
越快,但高于某一浓度
温度=26。7 ℃
时变慢300-500ppm。
硫化氢的体积分数低于
2× 10-3~5× 10-3mL/L 时,对材料的硬度要求 可以从HRC22放宽一些。 0 300 600 1200
- 1、下载文档前请自行甄别文档内容的完整性,平台不提供额外的编辑、内容补充、找答案等附加服务。
- 2、"仅部分预览"的文档,不可在线预览部分如存在完整性等问题,可反馈申请退款(可完整预览的文档不适用该条件!)。
- 3、如文档侵犯您的权益,请联系客服反馈,我们会尽快为您处理(人工客服工作时间:9:00-18:30)。
湿硫化氢环境腐蚀与防护第一章总则1.1 为规湿硫化氢环境腐蚀与防护工作,防止发生安全事故,依据国家有关法规、标准,制定本指导意见。
1.2石油化工装置在湿硫化氢环境(含有气相或溶解在液相水中,不论是否有氢气存在的酸性工艺环境)使用的静设备,为抵抗硫化物应力腐蚀开裂(SSC)、氢诱导开裂(HIC)和应力导向氢诱导开裂(SOHIC),在设计、材料、试验、制造、检验等方面的要求。
生产、技术、设计、工程、检修、科研等部门应积极参与和配合设备管理部门做好相关工作。
1.3对处于湿硫化氢腐蚀环境中的设备抗 SSC、HIC/SWC 和 SOHIC 损伤的最低要求,其中包括碳钢和低合金钢,以及碳钢及低合金钢加不锈钢的复合钢板制造的设备。
但不包括采用在金属表面(接触介质侧)增加涂层(如喷铝等)防止基体材料腐蚀开裂的设备。
1.4凡处于湿硫化氢环境中的设备在材料选择、设备制造与检验均应满足本标准的要求,否则可能导致设备 SSC、HIC/SWC 和 SOHIC 的破坏。
1.5不包括湿硫化氢引起的电化学失重腐蚀和其他类型的开裂。
1.7 湿硫化氢腐蚀环境的定义与分类:1.7.1 介质在液相中存在游离水,且具备下列条件之一时称为湿硫化氢腐蚀环境:(1)在液相水中总硫化物含量大于 50ppmw;或(2)液相水中 PH 小于 4 且总硫化物含量大于等于 1ppmw;或(3)液相水中 PH 大于 7.6 及氢氰酸(HCN)大于等于 20ppmw,且总硫化物含量大于等于 1ppmw;或(4)气相中含有硫化氢分压大于 0.0003MPa(0.05psia)。
1.7.2 根据湿硫化氢腐蚀环境引起碳钢和低合金钢材料开裂的严重程度以及对设备安全性影响的大小,把湿硫化氢腐蚀环境分为 2 类,在第I 类环境中主要关注 SSC,而在第Ⅱ类环境中,除关注 SSC 外,还要关注HIC 和 SOHIC 等损伤。
具体划分类别如下:第 I 类环境(1)操作介质温度≤ 120℃;(2)游离水中硫化氢含量大于 50ppmw;或(3)游离水的 PH < 4,且含有少量的硫化氢;或(4)气相中硫化氢分压大于 0.0003MPa(绝压);或(5)游离水中含有少量硫化氢,溶解的 HCN 小于 20ppmw,且 PH >7.6。
第Ⅱ类环境(1)操作介质温度≤ 120℃;(2)水溶液中硫化氢含量大于 50ppmw,且 PH < 4;或(3)气相中硫化氢分压大于 0.0003MPa(绝压),且水中总硫化物含量大于 2000ppmw,PH < 4;或(4)水溶液中总硫化物 [ 注 ] 含量大于 2000ppmw,HCN 含量大于20ppmw,且 PH > 7.6;或(5)水溶液中含有硫氢化胺(NH4HS)浓度大于 2%(wt%)。
1.8 湿硫化氢环境下的腐蚀与损伤主要包括:酸性水腐蚀、湿 H2S 损伤(HB/HIC/SOHIC/SSC)、胺腐蚀、碱式酸性水腐蚀(硫氢化氨腐蚀)等几类。
1.9 湿硫化氢环境下装置设计选材与制造应严格执行国家、行业及中国石油相应标准规,同时应参照以下标准规:(1)GB/T4340.1 金属维氏硬度试验第一部分:试验方法法(2)GB/T6394 金属平均晶粒度测定方法(3)GB/T10561 钢中非金属夹杂物含量的测定 / 标准评级图显微检验法(4)GB150 固定式压力容器(5)TSG R0004 固定式压力容器安全技术监察规程(6)SH/T 3074 石油化工钢制压力容器(7)GB151 管壳式换热器(8)SH/T3075 石油化工钢制压力容器材料选用规(9)GB/T8165 不锈钢复合钢板和钢带(10)GB/T699 优质碳素结构钢(11)GB713 锅炉和压力容器用钢板(12)NB/T47002 压力容器用爆炸焊接复合板(13)NB/T47008 承压设备用碳素钢和合金钢锻件(14)GB24511 承压设备用不锈钢钢板和钢带(15)JB 4708 钢制压力容器焊接工艺评定(16)JB/T 4711 压力容器涂敷与运输包装(17)其它适应于湿硫化氢环境设计选材与制造相关标准规。
(18)GB/T4157 金属在硫化氢环境中抗特殊形式环境开裂实验室实验(19)GB/T8650 管线钢和压力容器钢抗氢致开裂评定方法(20)NACE MR0103 Materials Resistant to sulfide StressCracking in Corrosive Petroleum Refining Environments (21)NACE SP0472 Methods and Controls to Prevent In-ServiceEnvironmental of Carbon Steel Weldments in Corrosive PetroleumRefining Environments(22)NACE TM0177 Laboratory Testing of metals for Resistanceto Sulfide Stress Cracking and Stress Corrosive Cracking In H2SEnvironments(23)NACE TM0284 Evaluation of pipeline and Pressure VesselSteels for Resistance to Hydrogen-Induced Cracking (24)NACE RP0296 Guidelines for Detection, Repair, andMitigation of Cracking of Existing Petroleum Refinery PressureVessels in Wet Hydrogen Sulfide Environments(25)API 945(RP)Avoiding Environmental Cracking in AmineUnits (26) API-571 Damage Mechanisms Affecting Fixed Equipment inthe Refining Industry (中文版)(27) NACE RP0103 炼厂腐蚀性原油环境中抗硫化物应力开裂材料;1.10 发生部位:(1)在炼油厂有湿 H2S 环境存在的部位都能发生 HB、HIC、SOHIC、SSC 损伤。
(2)在加氢装置中,NH4HS 浓度增大到超过 2% 会增加发生鼓泡、HIC和 SOHIC 的可能性。
(3)氰化物会明显增加 HB、HIC、SOHIC 损伤的可能性和严重程度。
对于流体催化裂化和延迟焦化装置的汽相回收单元尤为明显。
典型的部位包括分馏塔塔顶罐,分离塔,吸收塔和汽提塔,压缩机级间分离器和缓冲罐,各种换热器、冷却器和空冷器。
酸性水汽提塔和胺再生塔顶系统尤其容易发生湿 H2S 损伤,因为此处存在氰化物,NH4HS 浓度也很高。
(4)SSC 最有可能在硬焊缝和热影响区及高强度部件中发现。
高强度部件包括螺栓,安全阀弹簧,400 系列不锈钢阀芯,压缩机轴、套管和弹簧。
1.11 各炼化企业在遵循本指导意见的基础上,应加强湿硫化氢环境腐蚀防护新技术的引进与推广,如各种涂层、镀层技术等。
第二章湿硫化氢环境设备的材料选择2.1 处于湿硫化氢腐蚀环境下的设备承压件应选用表 2.1 中的材料:表 2.1 湿硫化氢腐蚀环境下的设备承压件推荐材料2.2 材料选择原则2.2.1 在第 I 类环境下操作的设备承压件应选用表 2.1 中的普通碳钢和低合金钢。
2.2.2 在第Ⅱ类环境下操作的设备承压件应选用表 2.1 中的抗 HIC 碳钢和低合金钢,以及表 2.1 中的复合材料。
2.3 材料附加要求2.3.1 碳钢和低合金钢2.3.1.1 在湿硫氢腐蚀环境下操作的设备用碳钢和低合金钢除符合相应的材料标准及相关规和规程的规定外还应符合下列附加要求:a)化学成分(熔炼分析):硫(S)含量≤ 0.08%,磷(P)≤ 0.12%成品分析偏差应符合 GB/T 222 的规定。
b)碳当量 CE:对普通碳素钢 CE ≤ 0.40,对低合金钢 CE ≤ 0.45。
元素以重量百分比代入(Wt%)c)力学性能(试样须经模拟焊后热处理)材料标准规定的屈服强度下限 ReL ≤ 355MPa材料最高抗拉强度 Rm ≤ 600MPa-20℃冲击功合格指标为:三个试样平均值 KV2 ≥ 34J,允许其中一个 KV2 ≥ 25J;d)使用状态:正火或正火 + 回火e)无损检测:钢板厚度超过 12mm 时,按 JB/T4730.3 进行 100% 超声检测,气质量等级按下列要求:钢板厚度 12 ~ 60mm 质量等级不低于Ⅱ级为合格钢板厚度大于 60mm 质量等级低于 I 级为合格2.3.1.2 钢板和锻件应逐(件)进行布氏硬度试验,硬度值应小于等于 200HBW。
2.3.1.3 处于湿硫化氢环境的锻焊设备壳体、接管、法兰及接管法兰的锻件级别按设计文件的要求。
2.3.2 抗 HIC 碳钢和低合金钢2.3.2.1 钢板除符合 GB/T 713、SA516-65/70 和 NB/T47008 的规定外,还应满足 2.3.1.2 条及以下要求:a)冶炼方法:应采用电炉 + 炉外精炼方法(或其他高质量的冶炼方法),应为本质细晶粒钢b)化学成分(熔炼分析 wt%):P ≤ 0.010;S ≤ 0.003;Ti ≤ 0.01;B ≤ 0.0005;Nb+V ≤ 0.05。
成品分析偏差应符合 GB/T 222 的规定。
C)碳当量 CE:钢材厚度≤ 50mm 时;CE ≤ 0.43;钢材厚度> 50mm 时;CE ≤ 0.45。
d)无损检测(同 5.3.1.1 e);e)使用状态:正火或正火 + 回火;2.3.2.2 钢板和锻件的晶粒度应符合 GB/T6394 的要求,晶粒度不粗于 5 级。
2.3.2.3 锻件和厚度大于 20mm 的钢板应按照 GB10561 规定的 B 法进行非金属夹杂物评定,硫化物类(A 类)、氧化铝类(B 类)、硅酸盐类(C 类)及球状氧化物类(D 类)、单颗粒球状类(DS 类)均不得大于 1.5级,且应满足 A+C ≤ 2.0,B+D ≤ 2.0,A+B+C+D+DS ≤ 4.5 级。
2.3.2.4 钢板和锻件应在正火状态交货,经模拟热处理后的力学性能除应符合 GB713、NB47008 的规定外,还应满足以下要求,推荐模拟热处理为 610℃±10℃,保温时间不小于 2.5min/ 每 1mm 厚度×预期热处理次数,且最小为 2h,或者供需双方协商。
a)厚度大于 20mm 的钢板应进行厚度方向的性能试验,其Ψz 三个试样平均值大于等于 35%,单个试样最低值大于等于 25%。