电动汽车的总装生产线工艺
电动汽车总装配工艺的设计与施工
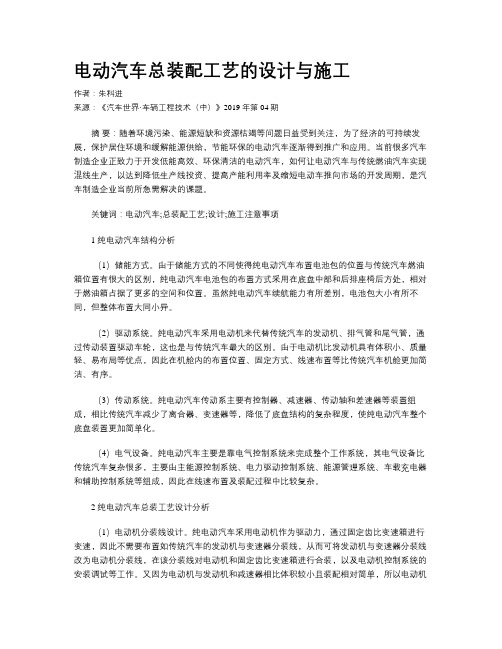
电动汽车总装配工艺的设计与施工作者:朱科进来源:《汽车世界·车辆工程技术(中)》2019年第04期摘要:随着环境污染、能源短缺和资源枯竭等问题日益受到关注,为了经济的可持续发展,保护居住环境和缓解能源供给,节能环保的电动汽车逐渐得到推广和应用。
当前很多汽车制造企业正致力于开发低能高效、环保清洁的电动汽车,如何让电动汽车与传统燃油汽车实现混线生产,以达到降低生产线投资、提高产能利用率及缩短电动车推向市场的开发周期,是汽车制造企业当前所急需解决的课题。
关键词:电动汽车;总装配工艺;设计;施工注意事项1 纯电动汽车结构分析(1)储能方式。
由于储能方式的不同使得纯电动汽车布置电池包的位置与传统汽车燃油箱位置有很大的区别,纯电动汽车电池包的布置方式采用在底盘中部和后排座椅后方处,相对于燃油箱占据了更多的空间和位置。
虽然纯电动汽车续航能力有所差别,电池包大小有所不同,但整体布置大同小异。
(2)驱动系统。
纯电动汽车采用电动机来代替传统汽车的发动机、排气管和尾气管,通过传动装置驱动车轮,这也是与传统汽车最大的区别。
由于电动机比发动机具有体积小、质量轻、易布局等优点,因此在机舱内的布置位置、固定方式、线速布置等比传统汽车机舱更加简洁、有序。
(3)传动系统。
纯电动汽车传动系主要有控制器、减速器、传动轴和差速器等装置组成,相比传统汽车减少了离合器、变速器等,降低了底盘结构的复杂程度,使纯电动汽车整个底盘装置更加简单化。
(4)电气设备。
纯电动汽车主要是靠电气控制系统来完成整个工作系统,其电气设备比传统汽车复杂很多,主要由主能源控制系统、电力驱动控制系统、能源管理系统、车载充电器和辅助控制系统等组成,因此在线速布置及装配过程中比较复杂。
2 纯电动汽车总装工艺设计分析(1)电动机分装线设计。
纯电动汽车采用电动机作为驱动力,通过固定齿比变速箱进行变速,因此不需要布置如传统汽车的发动机与变速器分装线,从而可将发动机与变速器分装线改为电动机分装线,在该分装线对电动机和固定齿比变速箱进行合装,以及电动机控制系统的安装调试等工作。
某新能源汽车总装车间工艺设计方案
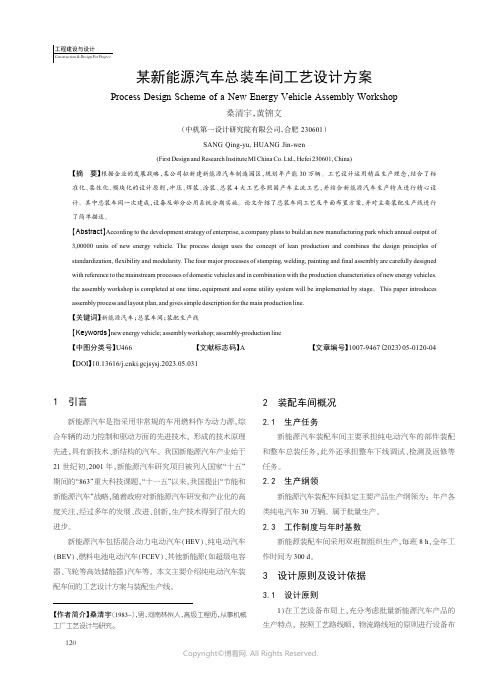
1引言新能源汽车是指采用非常规的车用燃料作为动力源,综合车辆的动力控制和驱动方面的先进技术,形成的技术原理先进,具有新技术、新结构的汽车。
我国新能源汽车产业始于21世纪初,2001年,新能源汽车研究项目被列入国家“十五”期间的“863”重大科技课题,“十一五”以来,我国提出“节能和新能源汽车”战略,随着政府对新能源汽车研发和产业化的高度关注,经过多年的发展、改进、创新,生产技术得到了很大的进步。
新能源汽车包括混合动力电动汽车(HEV)、纯电动汽车(BEV)、燃料电池电动汽车(FCEV)、其他新能源(如超级电容器、飞轮等高效储能器)汽车等。
本文主要介绍纯电动汽车装配车间的工艺设计方案与装配生产线。
2装配车间概况2.1生产任务新能源汽车装配车间主要承担纯电动汽车的部件装配和整车总装任务,此外还承担整车下线调试、检测及返修等任务。
2.2生产纲领新能源汽车装配车间拟定主要产品生产纲领为:年产各类纯电汽车30万辆。
属于批量生产。
2.3工作制度与年时基数新能源装配车间采用双班制组织生产,每班8h,全年工作时间为300d。
3设计原则及设计依据3.1设计原则1)在工艺设备布局上,充分考虑批量新能源汽车产品的生产特点,按照工艺路线顺,物流路线短的原则进行设备布某新能源汽车总装车间工艺设计方案Process Design Scheme of a New Energy Vehicle Assembly Workshop桑清宇,黄锦文(中机第一设计研究院有限公司,合肥230601)SANG Qing-yu,HUANG Jin-wen(First Design and Research Institute MI China Co.Ltd.,Hefei230601,China)【摘要】根据企业的发展战略,某公司拟新建新能源汽车制造园区,规划年产能30万辆。
工艺设计运用精益生产理念,结合了标准化、柔性化、模块化的设计原则,冲压、焊装、涂装、总装4大工艺参照国产车主流工艺,并结合新能源汽车生产特点进行精心设计。
新能源汽车和传统汽车的总装工艺比较分析
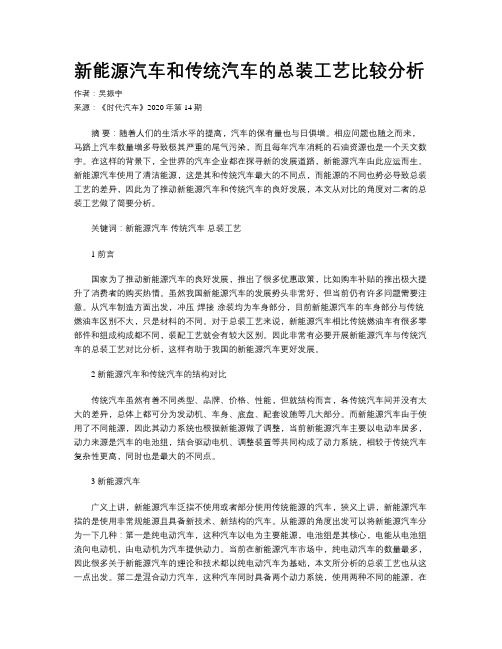
新能源汽车和传统汽车的总装工艺比较分析作者:吴振宇来源:《时代汽车》2020年第14期摘要:随着人们的生活水平的提高,汽车的保有量也与日俱增。
相应问题也随之而来,马路上汽车数量增多导致极其严重的尾气污染,而且每年汽车消耗的石油资源也是一个天文数字。
在这样的背景下,全世界的汽车企业都在探寻新的发展道路,新能源汽车由此应运而生。
新能源汽车使用了清洁能源,这是其和传统汽车最大的不同点,而能源的不同也势必导致总装工艺的差异,因此为了推动新能源汽车和传统汽车的良好发展,本文从对比的角度对二者的总装工艺做了简要分析。
关键词:新能源汽车传统汽车总装工艺1 前言国家为了推动新能源汽车的良好发展,推出了很多优惠政策,比如购车补贴的推出极大提升了消费者的购买热情。
虽然我国新能源汽车的发展势头非常好,但当前仍有许多问题需要注意。
从汽车制造方面出发,冲压-焊接-涂装均为车身部分,目前新能源汽车的车身部分与传统燃油车区别不大,只是材料的不同。
对于总装工艺来说,新能源汽车相比传统燃油车有很多零部件和组成构成都不同,装配工艺就会有较大区别。
因此非常有必要开展新能源汽车与传统汽车的总装工艺对比分析,这样有助于我国的新能源汽车更好发展。
2 新能源汽车和传统汽车的结构对比传统汽车虽然有着不同类型、品牌、价格、性能,但就结构而言,各传统汽车间并没有太大的差异,总体上都可分为发动机、车身、底盘、配套设施等几大部分。
而新能源汽车由于使用了不同能源,因此其动力系统也根据新能源做了调整,当前新能源汽车主要以电动车居多,动力来源是汽车的电池组,结合驱动电机、调整装置等共同构成了动力系统,相较于传统汽车复杂性更高,同时也是最大的不同点。
3 新能源汽车广义上讲,新能源汽车泛指不使用或者部分使用传统能源的汽车,狭义上讲,新能源汽车指的是使用非常规能源且具备新技术、新结构的汽车。
从能源的角度出发可以将新能源汽车分为一下几种:第一是纯电动汽车,这种汽车以电为主要能源,电池组是其核心,电能从电池组流向电动机,由电动机为汽车提供动力。
浅谈新能源汽车和传统汽车的总装工艺比较
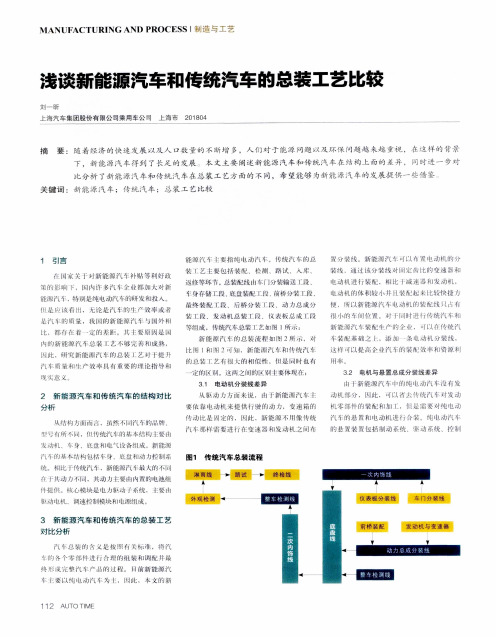
淋 雨线
▲
— 路试 '. 终检 线
i荔 划 蜀
分 装线。 新能源 汽 J‘以 f乜动机 的 分 装线 ,通 过 法分装 线埘 定 齿比的 变述 器币¨ 电动 机进 行装配 ,相 比十减 速 l 车I】发动机 , 电动 机的体 fjI较 小并 且装配 起 求比较伙 拄 方 便 , 所 以 新 能 源 汽 牟 电 动 机 的 装 线 I 自‘ 很 小 的 'i-Iil】f 置 。 对 i:同 时 进 行 传 统 } t车 I 新 能 源 1i装 配 牛 产的 企 Ik 一 j以 他统 汽 乍 装 配 越 础 之 添 加 ·条 电 动 机 分装 线 , 这 样 · 以提 高企 ,J 汽车 的装配 效率 和资源 利 川 牢 。
3 2 电机 与 悬 置 总 成 分 装 线 差 异 … 十 新 能 源 汽 车 巾 的 纯 I乜动 汽 没 有 发 动 机 部分, 此 , ur以 省 传统 j L‘i对发 动 机 零部 的装 配和 『Jf1 J:, I怂需 要埘纯 电动 汽 的 悬 和 电 动 机 进 合装 纯 f 动 汽 中 的 悬 置装 ’ 也 括 制 动 系统 、 动 系统 、 控 制
组 成 .传 统 汽 车 总 装 工 艺 如 l所 永 : 新 能 源 },L车 的 总 装 流 如 f{f 2所 示 , 对
比 l III !nJ‘知I,新 能 源 1i硐I传统 汽车 的 总 装 I 艺 仃 很 大的 车门似 , 似 怂 I叶也 有 一 定 的 圳 。 这 两 之 间 的 区 别 主要 体 现 :
是 J.:,=浚 出 , 无 论 是 汽 车 的 'I-f 效 率 或 者 址 ‘ 的 顷 量 , 我 困 的 新 能 源 4i j国 外 相 比 , 仃 l 着 ·定 的 差 距 。 』 { 受 蟓 因 是 I 内 的 新 能 源 汽 乍 总 装 1:岂 /f 够 完 和 成 熟 ,
汽车制造总装车间生产线的输送设备研究

汽车制造总装车间生产线的输送设备研究汽车在生产和制造的环节是非常复杂的,每个环节都要做好才可以保证汽车制造的质量。
每个环节都要进行物品的运输,而各个生产线中设备的选择是该行业比较重视的问题。
汽车总装是汽车生产制造中的最后一项工作,也是最重要的一环,在输送设备的选择时,不但要节约成本、减少各个方面的资金投入,还要满足汽车制造的实际需求。
因此,本文对汽车制造总装车间生产线的输送设备进行了研究。
關键词:汽车制造;总装车间;生产线输送设备一、汽车制造总装的工艺1、汽车制造总装工艺流程为了能够满足产能的需求,实现精确化生产,汽车制造总装车间都使用了模块化工艺流程,主线模块主要包括PBS 线、底盘线、调试线、内饰线等,分装模块主要包括动力总成、车门、座椅等。
模块化装配主要是实现汽车零件的分装,之后通过主线工位组装,以此实现整车的装配。
汽车制造总装工艺的流程为:车身PBS线→内饰线→底盘装配线→合成线→检测线→淋雨线→道路试验。
2、汽车制造总装的工艺参数工位之间的间距一般选择最大车型的长度加长700-1100mm,比如最大车长为4000mm,那么科学的工位间距就是5000mm。
在进行输送设备的选择和应用的过程中,需要考虑到不同生产线之间输送设备的应用间隔,不允许输送设备对车间生产的实际效率造成影响,要根据在汽车制造的实际情况来进行输送设备的选择。
二、汽车制造总装的输送设备1、积放链积放链运输设备在实际应用时,其内部空间是非常大的,可以将工件堆积在一起进行运输,可以进行多种物品的共同运输,提升整体应用效率。
积放链的组成结构是非常复杂的,由多种装置、设备和系统构成,通常被应用在底盘线的运输作业中。
在该运输系统中,可以将不同生产线之间的运输工作结合在一起整合成一个物流运输系统,可以对不同类型的物品进行放置、运输、管理和储存,实际应用效率比较高。
这种运输系统中所应用的技术是比较可靠的,并且在使用的过程中不同投入过多的成本,但是产生的噪音很大,需要消耗大量的能源资源才能完成相关的运输工作。
混动车型混线生产总装工艺规划方式的应用
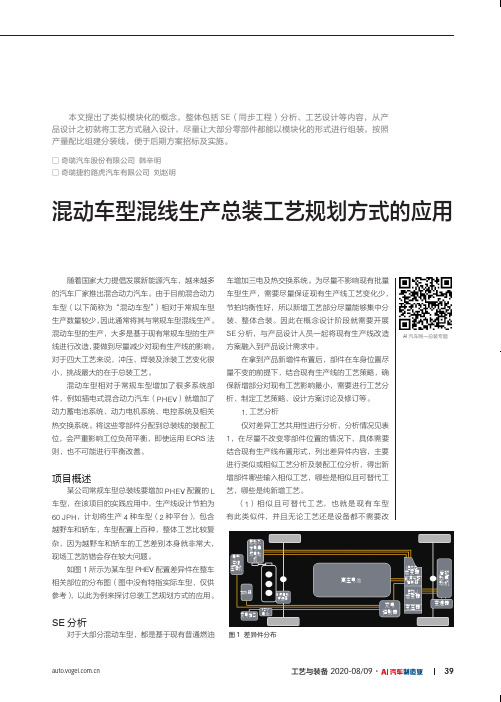
图1 差异件分布电子空调压缩机加热器充电插口起动及发电集成电动机12 V 电池高压电池充电控制器IBSG 逆变器能源分配控制器EDU逆变器变压器变速器后驱动电动机6速自动变速器AI 汽车网—总装专题四大工艺FOUR PROCESSES造就能够满足新部件装配的工艺内容。
比如电动空气压缩机(E-compressor),正常汽油车使用带驱动的空气压缩机,此为电驱动的空气压缩机,两者无论是装配内容还是装配位置都相差无几,并且工艺设备都不需要进行相关改造。
此类工艺不需要做特殊安排,实际生产时只需要进行配置区分即可。
(2)相似工艺,是现有车型也有类似件,并且装配工艺都基本相同,但是装配性不能完全进行替换或者工装设备不能完全覆盖,一般需要进行小范围的改造或优化。
比如起发电一体机(IBSG),正常汽油车都有发电机,IBSG与发电机装配位置相同,但是IBSG无法使用现有的机械臂,机械臂爪手需要进行改造才能融合纯汽油车和混动车。
对于此类工艺,需要输出工艺工装设备改造清单给设备部门。
(3)新增工艺是相对于基础车型新增加的、难以在生产线相关工位找到类似件,且工时难以进行配置替换。
比如PTC加热器,此件为在纯电动模式下加热冷却液给室内供热用的,为纯增加件。
2.工艺策略这里以新增工艺为分析重点,采取四种工艺策略。
工艺策略分析见表2。
(1)策略a:依托装配线体工艺排布形式,确认线体内在混动时相对于基础车型有无删除件,可以尽量在删除件装配工位将此排布进去。
(2)策略b:调整工艺路线以模块化或总成形式供货。
(3)策略c:将某些总成部件拆分成数个子件,便于安排到对应工位,减少对相应工位的冲击。
(4)策略d:组建新的分装线或分装工位,将新增部分统一分装,一起合装。
3.设计方案的讨论及修订将工艺策略完整版输入给产品部门,逐项达成共同结论,经过多次讨论、优化,特别是组建分装线的分装内容,要求合装至车身不应受到底盘合装的限制,形成最终的设计方案,产品部门修改完善数模及EBOM输出给工艺规划部门。
纯电动重卡总装工艺流程

纯电动重卡总装工艺流程【摘要】纯电动重卡总装工艺流程在当今汽车行业中扮演着重要的角色。
本文将详细介绍了纯电动重卡总装工艺流程的各个环节,包括零部件采购与入库流程、总装车间的布置与准备工作、车身吊装与焊接、电池组装与安装以及电控系统集成与调试。
通过对这些工艺流程的分析,我们可以了解到纯电动重卡的装配过程是如何进行的。
在结论部分也分析了纯电动重卡总装工艺流程的优势和未来发展方向,指出了其在节能环保、提升车辆性能等方面的潜力与前景。
通过本文的介绍,读者可以更加深入了解纯电动重卡总装工艺流程的重要性和发展趋势。
【关键词】纯电动重卡、总装工艺流程、零部件采购、车身焊接、电池组装、电控系统、优势、未来发展方向1. 引言1.1 纯电动重卡总装工艺流程的重要性纯电动重卡总装工艺流程的重要性体现在多个方面。
对于汽车制造企业来说,确立一套科学高效的总装工艺流程能够提高生产效率,降低生产成本,提升产品质量,从而增强企业竞争力。
纯电动重卡总装工艺流程的完善不仅关系到整车的性能表现,还关乎整车的安全性和可靠性,直接关系到用户的舒适性和使用体验。
纯电动重卡总装工艺流程的优化还能够减少资源浪费,推动节能减排,符合当前社会对绿色可持续发展的需求。
正因为如此,纯电动重卡总装工艺流程的重要性不容忽视,需要制定科学合理的流程,确保每个环节都能够顺畅高效地进行,以实现产品质量和工艺水平的提升,为车辆的使用者提供更加优质的产品和服务。
1.2 纯电动重卡总装工艺流程的背景背景中值得注意的是,纯电动重卡总装工艺流程的建立和发展并非一蹴而就,而是经过了长期的探索和实践。
在初期阶段,纯电动重卡总装工艺流程存在着诸多技术难题和挑战,如电池技术的不断进步、电控系统的稳定性等问题。
但是随着科技的不断进步和工艺的不断优化,纯电动重卡总装工艺流程逐渐成熟和完善。
通过不断地改进和创新,纯电动重卡总装工艺流程在提高生产效率、降低生产成本、保障产品质量等方面取得了显著的成果。
基于与传统汽车比较的纯电动汽车总装工艺分析
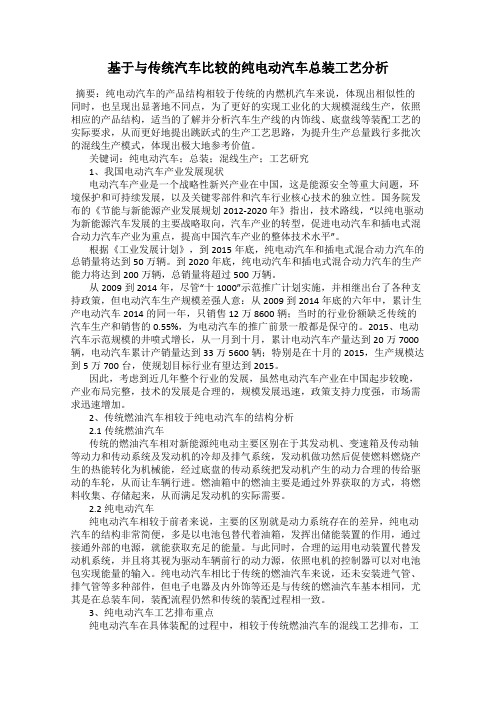
基于与传统汽车比较的纯电动汽车总装工艺分析摘要:纯电动汽车的产品结构相较于传统的内燃机汽车来说,体现出相似性的同时,也呈现出显著地不同点,为了更好的实现工业化的大规模混线生产,依照相应的产品结构,适当的了解并分析汽车生产线的内饰线、底盘线等装配工艺的实际要求,从而更好地提出跳跃式的生产工艺思路,为提升生产总量践行多批次的混线生产模式,体现出极大地参考价值。
关键词:纯电动汽车;总装;混线生产;工艺研究1、我国电动汽车产业发展现状电动汽车产业是一个战略性新兴产业在中国,这是能源安全等重大问题,环境保护和可持续发展,以及关键零部件和汽车行业核心技术的独立性。
国务院发布的《节能与新能源产业发展规划2012-2020年》指出,技术路线,“以纯电驱动为新能源汽车发展的主要战略取向,汽车产业的转型,促进电动汽车和插电式混合动力汽车产业为重点,提高中国汽车产业的整体技术水平”。
根据《工业发展计划》,到2015年底,纯电动汽车和插电式混合动力汽车的总销量将达到50万辆。
到2020年底,纯电动汽车和插电式混合动力汽车的生产能力将达到200万辆,总销量将超过500万辆。
从2009到2014年,尽管“十1000”示范推广计划实施,并相继出台了各种支持政策,但电动汽车生产规模差强人意:从2009到2014年底的六年中,累计生产电动汽车2014的同一年,只销售12万8600辆;当时的行业份额缺乏传统的汽车生产和销售的0.55%,为电动汽车的推广前景一般都是保守的。
2015、电动汽车示范规模的井喷式增长,从一月到十月,累计电动汽车产量达到20万7000辆,电动汽车累计产销量达到33万5600辆;特别是在十月的2015,生产规模达到5万700台,使规划目标行业有望达到2015。
因此,考虑到近几年整个行业的发展,虽然电动汽车产业在中国起步较晚,产业布局完整,技术的发展是合理的,规模发展迅速,政策支持力度强,市场需求迅速增加。
2、传统燃油汽车相较于纯电动汽车的结构分析2.1传统燃油汽车传统的燃油汽车相对新能源纯电动主要区别在于其发动机、变速箱及传动轴等动力和传动系统及发动机的冷却及排气系统,发动机做功然后促使燃料燃烧产生的热能转化为机械能,经过底盘的传动系统把发动机产生的动力合理的传给驱动的车轮,从而让车辆行进。
- 1、下载文档前请自行甄别文档内容的完整性,平台不提供额外的编辑、内容补充、找答案等附加服务。
- 2、"仅部分预览"的文档,不可在线预览部分如存在完整性等问题,可反馈申请退款(可完整预览的文档不适用该条件!)。
- 3、如文档侵犯您的权益,请联系客服反馈,我们会尽快为您处理(人工客服工作时间:9:00-18:30)。
电动汽车的总装生产线工艺
作者:张菊文章来源:奇瑞汽车股份有限公司点击数:3565 发布时间:2012-04-0904-09
新浪微博QQ空间人人网开心网更多
随着节能,环保等问题日益受到重视,电动汽车开始投入生产并推广应用.
图1 混合电动汽车工作原理
随着节能、环保等问题日益受到重视,电动汽车开始投入生产并推广应用。
与传统汽车生产的装配工艺相比,电动汽车既有其特殊性,又与传统汽车有共同之处,在新生产线规划阶段,企业应充分分析两者的工艺不同点,努力实现两种车型的混线生产。
如今人们的出行离不开汽车,然而,大规模汽车的应用引发的大气污染、全球变暖及资源迅速递减等成为全球关注的问题。
近10年来,人们致力于发展高效、清洁的代步工具,即电动汽车。
电动汽车完全由可充电电池(如铅酸电池、镍镉电池、镍氢电池或锂离子电池)提供动力源,大部分车辆直接采用电动机驱动,有一部分车辆把电动机装在发动机舱内,也有一部分直接以车轮作为4台电动机的转子,后者技术含量更高。
图2 动力蓄电池布置示意
电动汽车工作原理
电动汽车主要是应用电动机驱动装置和动力蓄电池组替换发动机与燃油系统以及发动机进排气系统等附件,图1重点描述了混合电动汽车串联工作原理。
纯电动汽车工作模式为:由外接电源通过BMS(电池管理单元监测和控制动力电池工作)对动力驱动电池充电,动力电池对整车逆变器提供低压二相电,再由逆变器将低压二相逆变成高压三相提供电力给驱动电动机,由MCU电动机控制器监测和控制驱动电动机工作产生动力,经差速器传给半轴带动车轮前进。
图3 动力总成夹具
燃油汽车工作模式为:由增程器燃烧燃料产生电力,对整车逆变器提供低压二相电源,再由逆变器将低压二相逆变成高压三相提供电力给驱动电动机,由MCU电动机控制器监测和控制驱动电动机工作产生动力,经差速器传给半轴带动车轮前进。
电动汽车与传统汽车装配工艺区别
在国内,电动汽车产业化生产装配线比起传统汽车生产线屈指可数,电动汽车与传统汽车有哪些工艺区别?如果电动汽车在传统车生产线通过会出现哪些与传统车工艺的不同点?下面我们通过对公司目前开发的两款电动车生产线内饰一底盘和内饰二检测的顺序,进行说明。
图4 电动汽车底板电池布置
总装车间内饰一装配生产线,主要完成电动汽车高压线束、动力蓄电池等零部件装配。
图2为电池结构,因每块电池质量在100kg左右,助力机械手装配电池过程中机械手与内饰一输送线同步运动,生产线节拍为120s,机械手负重从侧门与后背门进入油漆车身过程中要规避车身刮伤,与整车后底板紧固螺柱的导向配合,完成电池的紧固。
这种动力蓄电池的装配一般至少需要300s才能完成,此处为电动汽车装配的瓶颈工位,产品工程师在做电动汽车电池布置过程中一定要考虑电池重量。
同时,与车身螺栓孔对位置性差,应尽量设计成带导向的螺柱,电池孔位U形进入螺柱内,节约在线装配工时且降低装配难度。
图5 电池合装小车
底盘分装工位驱动电动机与减速器及悬置总成等,可在传统车动力总成分装线改造完成,发动机与变速器支撑销沿夹具四周布置,电动汽车驱动电动机减速器托块在夹具中间处(见图3),两种车型基本上无空间干扰因素。
图6 电动汽车高低电压工作原理
在底盘合装工位,电动汽车动力总成及后轴合装设备可与传统汽车共用。
电动汽车动力蓄电池布置在底板下部(见图4),重量约100kg以上,由10~12个螺栓或螺母紧固。
在底盘生产线新增电池合装小车1台,由机械手将动力蓄电池放置在电动合装小车夹具上(见图5),电动合装小车两侧夹爪卡在吊具上与吊具实行同步装配,两名操作员工完成电池与底板紧固后夹爪落下,电动合装小车自动返回至起始位置。
此种工艺的实现投资较少,在120s节拍内实现不了合装工艺,需要300s以上。
动力蓄电池合装占用生产线两工位,传统车底盘工位只占据整条生产线15%~20%工位数。
换句话说底盘工位数少,在新建生产线规划过程中需考虑的是,底盘电池合装工位数比传统车工位数多,此处需预留工位。
图7 电动汽车淋雨段设置装置
内饰二生产线主要完成前仓增程器装配,在整车进入CP7检测线前完成整车绝缘检测等工作,为提升整车产品质量,对整车高压电与低压电工作原理需理解(见图6)。
在保证整车装配完成后,使用绝缘表依照产品装配技术条件进行检测,保证整车是绝缘状态。
操作工人在检验过程中带绝缘手套,以保证人身安全。
电动汽车四轮定位仪、侧滑、制动试验、动态检测及最终检测与传统车型基本相同,淋雨试验因为产品构造问题在工艺上有所不同。
相比汽油车而言,出现后仓漏水后,电动车返工量极大,且需俩人拆卸及装配电池。
为杜绝此种情况,在产品设计阶段建议工程师预留后备箱电池处的底板出水孔,同时在淋雨工段末端设置一倾斜装置(见图7),让雨水从整车中漏出。
结语
不同企业电动汽车布置原理不尽相同,电动汽车工艺尚处在摸索成熟阶段,在以后新生产线规划阶段,要充分考虑电动汽车与传统汽车的工艺不同点,考虑到两种车型的混线生产。