复合材料风电辅材及工艺
风电叶片基础知识之复合材料篇三

2) 热固性玻璃钢 它是由60%~70%玻璃纤维(或玻璃布)和30%~40%热固性树脂 (环氧、聚酯树脂等)组成。 主要优点:密度小、强度高,耐蚀性、绝缘性、绝热性好;吸 水性、防磁、微波穿透性好,易于加工成型。 缺点:弹性模量低,热稳定性不高,只能在300℃以下工作。
(2)碳纤维―树脂复合材料 最常用的是碳纤维与聚酯、酚醛、环氧、聚四氟乙烯等树脂组 成的复合材料,具有高强度、高弹性模量、高比强度和比模量,还 具有优良的抗疲劳性能、耐冲击性能、自润滑性、减摩耐磨性、耐 蚀性及耐热性。缺点是纤维与基体结合力低。 (3)硼纤维―树脂复合材料 主要由硼纤维与环氧、聚酰亚胺等树脂组成。具有高的比强度、 比模量,良好的耐热性。其缺点是各向异性明显。 (4)碳化硅纤维树脂复合材料 由碳化硅纤维与环氧树脂组成的复合材料,具有高的比强度、 比模量。 (5)Kevlar纤维树脂复合材料 由Kevlar纤维与环氧、聚乙烯、聚碳酸酯、聚酯等树脂组成。 主要性能特点是抗拉强度大于玻璃钢,而与碳纤维―环氧树脂复合 材料相似;延性好,与金属相当;其耐冲击性超过碳纤维增强塑料; 其疲劳抗力高于玻璃钢和铝合金;减振能力为钢的8倍。
风电叶片基础知识之复合材料 篇三
6.3
1.常用增强纤维
常用的复合材料
一、纤维增强复合材料
主要有玻璃纤维、碳纤维、硼纤维、碳化硅纤维、Kevlar有机 物纤维等。
玻璃纤维布
玻璃纤维绳
玻璃纤维绳
纳 米 碳 管 纤 维 玻璃纤维纸
碳 纤 维 绳
(1)玻璃纤维 按玻璃纤维中 Na2O 和 K2O 的含量不同,可将其分为无碱纤维 (碱的质量分数<2%)、中碱纤维(碱的质量分数为2%~12%)、高 碱纤维(碱的质量分数>12%)。随着碱量的增加,玻璃纤维的强度、 绝缘性、耐蚀性降低。 特点:强度高,抗拉强度可达 1000 ~3000MPa ;弹性模量比金 属低得多,为( 3 ~ 5 )×104MPa ;密度小,为 2.5 ~ 2.7g/cm3 ;化 学稳定性好;不吸水、不燃烧、尺寸稳定、隔热、吸声、绝缘等。 缺点:脆性较大、耐热性低,250℃以上开始软化。 优点:价格便宜、制作方便
碳纤维复合材料与新能源(风力发电、核能)

碳纤维复合材料与新能源(风力发电、核能)
一、风能发电
在风力发电领域,经编复合材料是制造风力发电叶片及其它重要结构部件的主要材料,叶片90%以上重量由复合材料组成。
采用碳纤维NCF 织物制备的复合材料风机叶片,具有质量轻、强度高、刚性好的优点,能够满足开发大型化、轻量化、高性能、低成本的发电叶片的要求。
图5.21 采用碳纤维NCF 织物制造的复合材料风机叶片
碳纤维高强度、高模量、耐腐蚀、抗疲劳等性能,可以有效地提高叶片刚度,减轻叶片重量,增长叶片使用寿命,提高风能利用率。
随着大丝束碳纤维的广泛应用,碳纤维价格的不断降低,碳纤维在大型叶片中的应用已成为一种趋势。
未来风力发电叶片制造中,碳纤维代替部分玻璃纤维应用于叶片、且用量逐步增加是高性能碳纤维复合材料发展的必然结果。
图5.22 碳纤维在风能发电方面的应用
这项最新设计需要1203 根“风力茎杆”,每根茎杆高60米,带有一个直径11-22米混凝土底基,风力茎杆最顶端直径仅5厘米。
它采用碳纤维材料制成,使用树脂进行加固,茎杆状碳纤维底部直径大约是0.33米。
对于风力茎杆,当它们受到摇摆风流的压缩作用,进而形成电流。
图5.23 碳纤维“风力茎杆”发电机
二、核能
碳纤维复合材料已用于核能高温气体冷却内炉的内部结构材料,等离子体直接变换器的栅极和集电极等。
2MW风机复合材料叶片材料及工艺研究

3 满足性能要求的材料种类及特点
3 1 增强材料 玻璃纤维增强叶片的受力特点是在玻璃纤维方 向能承受很高的拉应力 , 而其它方向承受的力相对 较小。叶片结构是由蒙皮和腹板组成 , 蒙皮采用夹 芯结构, 中间层是轻木, 上下面层为玻璃纤维增强材 料。面层由单向层和 , 45 − 层组成。单向层可选用 单向织物或单向玻璃纤维铺设 , 一般用 7 .1 或 4 .1 玻璃纤维布, 以承受由离心力和气动弯矩产生的轴 向应力。为简化成型工艺 , 可不用 , 45− 玻璃纤维布 层, 而采用 1 .1 玻璃纤维布, 均沿轴向铺设, 以承受 主要由扭矩产生的剪切应力, 一般铺放在单向层外 侧。腹板的结构形式也是夹芯结构。但是, 在蒙皮 与腹板的结合部位 , 即梁帽处必须是实心玻璃纤维 增强结构。这是因为此部分腹板与蒙皮相互作用, 应力较大 , 必须保证蒙皮的强度和刚度。 经过对长度为 10~ 60m 的叶片进行的统计表 明, 叶片质量按长度的三次方增加。叶片轻量化对 运行、 疲劳寿命、 能量输出有重要的影响。同时为了 保证在极端风载下叶尖不碰塔架, 叶片必须具有足 够的刚度。既要减轻叶片的质量, 又要满足强度与 刚度要求 , 有效的办法是采用碳纤维增强材料。碳 纤维增强材料的拉伸弹性模量是玻璃纤维增强材料 的 2~ 3 倍。 2 MW 叶片采用碳纤维增强可充分发挥 其高弹轻质的优点。经过分析 , 采用碳纤维 /玻璃纤 维混杂增强的方案, 叶片可减重 20 % ~ 40 % 。因此 采用碳纤维 /玻 璃纤维混杂增强对抑制质量的增大 是必要的 , 同时降低了风能成本, 叶片也可具有足够 刚性和长度
风力机复合材料叶片是风力机自主研发的核心 设备之一, 其价值达 到整机价值的 20 % 左右 , 其中 叶片的设计、 材料选择、 制造工艺选取对复合材料叶 片性能和成本起决定性作用。随着风力机组容量增 大 , 风力机叶片的尺寸随之增大 , 兆瓦级大型风力机 叶片已成为风力机国产化发展的主要瓶颈。 当前, 复合材料叶片追求容量大、 重量轻、 结构 强度高、 生产制造成本低、 运行安全可靠、 安装和维 护方便 , 整个风力机组单位千瓦时成本低 , 经济收益 高。复合材料叶片基本上是由聚酯树脂、 乙烯基树 脂和环氧树脂等热固性基体树脂与 E 玻璃纤维、 S 玻璃纤维、 碳纤维等增强材料, 通过手工铺放或树脂 注入等成型工艺复合而成。在自主研发 2MW 风力 机复合材料叶片的基础上, 综合考虑性能、 成本、 可 靠性等因素 , 选取合适的原材料及制造工艺是复合 材料叶片研制的关键。
叶片腹板操作流程

叶片腹板操作流程
叶片腹板操作流程一般指风电叶片制造中的复合材料腹板制作过程,简要描述如下:
1. 材料准备:裁剪玻璃纤维织物、碳纤维等增强材料,准备树脂、脱模布等其他辅材。
2. 工装铺设:在专用工装模具上铺设真空袋膜,然后按照设计要求精确摆放腹板增强材料。
3. 注入树脂:通过注射或刷涂等方式将树脂均匀覆盖于增强材料上,确保浸润充分。
4. 真空导入:密封真空袋,启动真空泵抽真空,排除空气,促使树脂均匀分布并完全渗透增强材料。
5. 固化成型:将腹板置于恒温环境中,按照规定的固化时间进行加热或常温固化。
6. 后处理:固化完成后,拆除真空袋,进行修边打磨,检查腹板质量和尺寸精度。
7. 组件装配:将成型的腹板与其他部件(如梁帽、壳体等)进行粘接或机械固定,形成完整的风电叶片结构。
我国复合材料风机叶片的几种制造工艺与发展前景

第2期12200r7年6月纤维复合材料FⅡlER咖SⅡESNo.2Jun..20∞我国复合材料风机叶片的几种制造工艺与发展前景何东晓1,黄力刚1,杨松1,安庆升2(1.哈尔滨玻璃钢研究院,哈尔滨15(1036)(2.上海复合材料科技有限公司,上海201206)摘要本文综合叙述了复合材料风机叶片的优势与发展前景,重点介绍了复合材料叶片的几种生产工艺方法和关键制造技术。
关键词复合材料;叶片;制造工艺;结构设计TheOutlookandManufacturingProcessofCompositeTurbineRotorBladesHEDong—xia01,HUANGLi—gan91,YANGSon91,ANQing—Shen92(1.HarbinH啦Institute,Harbin150036)(2.ShanghaiCompositeMateriatCompany,Shanghai201206)ABSTRACTThispaperstatestheoutlookandmanufacturingprocessofChinesecompositewindturbinerotorblades.andintroducesemphaticallyseveralmanufacturingprocessesandthekeytechnology.KEYWORDSComposites;Blades;Manufacturingprocess;Structuraldesign1前言中国幅员辽阔,风力资源极其丰富,作为刚刚起步发展风电的国家具有很大的市场潜力。
随着《可再生能源法》的颁布和《京都协议书》的生效,中国把可再生能源中的风能利用放在首要位置,使得风力发电面临着前所未有的发展形势。
风力发电有着如下显著优点:①风力发电是一种绿色能源。
用矿物燃料发电每千瓦要产生0.681公斤C02,风力发电不会产生C02。
②风力发电机技术成熟,故障率低,可用率高达98%。
风电叶片生产流程
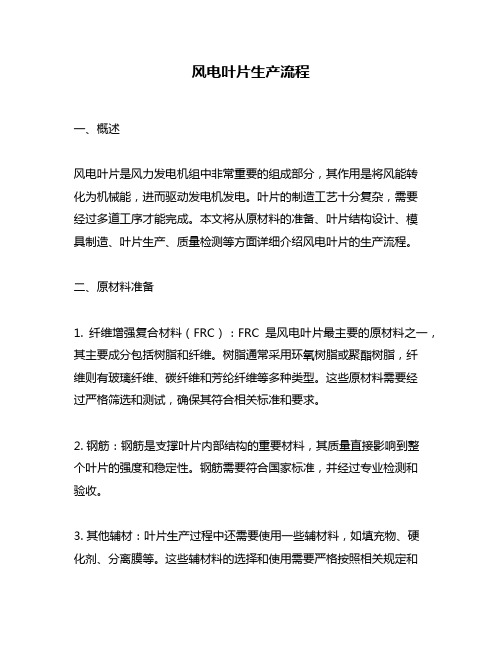
风电叶片生产流程一、概述风电叶片是风力发电机组中非常重要的组成部分,其作用是将风能转化为机械能,进而驱动发电机发电。
叶片的制造工艺十分复杂,需要经过多道工序才能完成。
本文将从原材料的准备、叶片结构设计、模具制造、叶片生产、质量检测等方面详细介绍风电叶片的生产流程。
二、原材料准备1. 纤维增强复合材料(FRC):FRC是风电叶片最主要的原材料之一,其主要成分包括树脂和纤维。
树脂通常采用环氧树脂或聚酯树脂,纤维则有玻璃纤维、碳纤维和芳纶纤维等多种类型。
这些原材料需要经过严格筛选和测试,确保其符合相关标准和要求。
2. 钢筋:钢筋是支撑叶片内部结构的重要材料,其质量直接影响到整个叶片的强度和稳定性。
钢筋需要符合国家标准,并经过专业检测和验收。
3. 其他辅材:叶片生产过程中还需要使用一些辅材料,如填充物、硬化剂、分离膜等。
这些辅材料的选择和使用需要严格按照相关规定和要求进行。
三、叶片结构设计1. 叶片结构设计是风电叶片生产的重要环节,其目的是确定叶片的形状、尺寸、材料以及内部结构等。
设计过程需要考虑多种因素,如气动性能、强度要求、制造工艺等。
通常采用计算机辅助设计软件进行设计,并经过多轮模拟和优化。
2. 叶片结构主要包括叶片表面和内部结构两个部分。
表面主要由纤维增强复合材料制成,内部结构则由钢筋和其他材料组成。
内部结构的形状和布局对叶片的强度和稳定性有着重要影响。
四、模具制造1. 模具制造是风电叶片生产中不可或缺的一环,其目的是为了将叶片原型复制出来。
模具通常采用玻璃钢或金属材料制成,需要具备高精度和高强度的特点。
模具制造需要经过多道工序,包括设计、加工、组装等。
2. 模具的设计需要根据叶片结构进行,通常采用CAD软件进行设计,并经过多轮模拟和优化。
加工过程中需要使用各种机床和工具,如数控车床、铣床、钻床等,确保模具的精度和质量。
五、叶片生产1. 叶片生产是风电叶片生产的核心环节,其目的是将纤维增强复合材料和钢筋等材料按照一定比例混合后注入模具中进行成型。
W9复合材料风电叶片技术研究-PPT课件
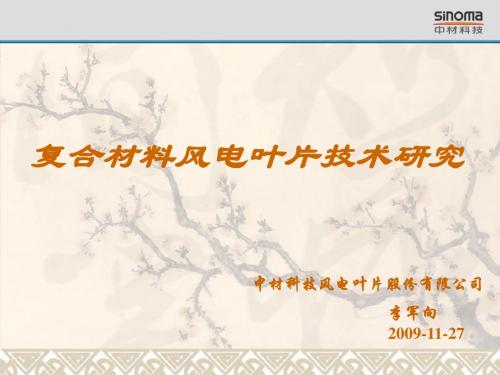
疲劳分析
计算单位载荷应变 利用Markov矩阵求解均值与幅值 求解许用循环次数 求解疲劳寿命 求解疲劳剩余安全系数
1MW叶片某纤维布的疲劳剩余安全系数
截面编号 剩余安全系数
1 2 3 4 5 6 7 8 9 10 11 12 13 14 15 16 17 18 19 20 21
叶片局部失稳图(L=27.9m,屈曲因子=2.738)
叶根螺栓连接分析
叶根螺栓连接分析包括连接螺栓的静强度分析和叶片根部玻璃钢强度分析,采 用工程算法和ABAQUS有限元算法对叶根螺栓连接强度进行分析。
叶根连接的有限元模型
十字头螺栓的应力变化图
*叶片根部最小剩余强度系数表
部 件 双头螺柱 计算部位 光杆拉伸 弯曲 剩余系数 1.56 1.1 失效系数 / /
1MW叶片三维模型
6.实例2:2.5MW叶片气动外形设计
设计尖速比的选择:9.5
叶片长度:48.8m
7.实例2:2.5MW叶片气动外形设计
二、复合材料叶片材料设计
材料、结构与工艺
材料设计
纤维/树脂/芯材
结构设计
蒙皮/主梁/腹板 叶根
生产工艺
灌注/预侵料
1 原材料选择与复合材料性能
A 原材料选择原则 结构、工艺、成本 B 纤维选择 玻璃纤维、碳纤维 C 芯材选择 PVC、BALSA D 树脂选择(热固性) 环氧树脂、不饱和聚酯
分析类型
模态分析:固有频率与预应力模态分析
变形分析:叶尖最大挠度分析
静强度分析:应力-应变分析 纤维失效分析:纤维方向和纤维层间失效分析 稳定性分析:叶片整体与局部稳定性分析 叶根螺栓连接分析:螺栓强度与螺栓寿命分析 疲劳分析:叶片寿命分析
风电叶片大梁板用复合材料及其制备方法与流程

风电叶片大梁板用复合材料及其制备方法与流程随着能源问题日益突显和可持续发展意识的加强,风能作为一种清洁、可再生能源得到了越来越多的关注和发展。
而作为风力发电的核心部件之一,风电叶片的优化和改进也成为了业内关注的重点。
在传统的风电叶片结构设计中,常常采用钢铁、铝合金等金属材料进行加固,但这些材料容易腐蚀、重量大、成本高等缺点,因此逐渐被复合材料所替代。
接下来,本文就介绍一种用于风电叶片大梁板的复合材料及其制备方法与流程。
一、复合材料的基本概念复合材料是指由两种或两种以上不同材料的组合形成一种新材料,其性能和性能的各种组合方式要远远优于单一材料。
这种“混搭”的方式,可以兼顾各种材料强度和耐用性的优势,实现综合材料性能的提升。
因此,在重量轻、强度高、耐腐蚀、耐热、隔音等性能方面具有很高的研究价值和实用性。
二、复合材料在风电领域的应用风电叶片作为风力发电机的关键零部件,需要具备一定的刚度和强度,同时又要轻量化,以增加输出功率。
因此,如何选用材料及其制备技术的优化,就成为提高风电叶片效率的关键。
复合材料的轻、强、硬、耐腐蚀和防电磁干扰等性能优点,使其在风电叶片的制造过程中被广泛应用,其中大梁板作为叶片的主梁骨架构件,需要具备较高的强度、刚度和耐久性。
通常与复合材料相结合制成。
常用的大梁板复合材料,由于其较好的性能和可塑性,主要采用树脂基复合材料(如环氧树脂、聚酯树脂),结合玻璃纤维、碳纤维等增强材料进行加固。
三、复合材料制备工艺流程1.材料预处理:复合材料的预处理包括采购、理化性能测试以及及时的贮存与保管等。
其中,材料采购需要注意材料来源、材料的保质期、含水率等各类因素。
2.材料切割:根据铺放图样按成品尺寸先在预制模具规定范围内用模板切割出相应的布料。
3.模具制作:将大梁板的形状和尺寸通过CAD技术和修模等方式进行设计,然后进行木质模具的制作。
4.胶液注入:制作好的木质模具表面用脱模剂喷涂处理后,制备胶液,按设计好的样板尺寸将其涂抹在木质模具表面上,并排气,待固化。
- 1、下载文档前请自行甄别文档内容的完整性,平台不提供额外的编辑、内容补充、找答案等附加服务。
- 2、"仅部分预览"的文档,不可在线预览部分如存在完整性等问题,可反馈申请退款(可完整预览的文档不适用该条件!)。
- 3、如文档侵犯您的权益,请联系客服反馈,我们会尽快为您处理(人工客服工作时间:9:00-18:30)。
复合材料风电叶片辅材及工艺
By
2010年,可以说是我国海上风电开始有序发展的“元年”。
对于当前业界高度关注的海上风电特许权招标问题,国家能源局可再生能源司副司长史立山对记者表示,加快海上风电建设的条件已基本具备,海上风电将是今后风电发展的重点之一。
由此可见,未来风电项目对风电叶片的要求将会更高,更轻质的大型复合材料叶片将会受到市场的青睐。
复合材料的市场机遇
风机叶片用主要材料体系包括各种增强材料、基体材料、夹层泡沫、胶粘剂和各种辅助材料等。
增强材料
对于同一种基体树脂来讲,采用玻璃纤维增强的复合材料制造的叶片的强度和刚度的性能要差于采用碳纤维增强的复合材料制造的叶片的性能。
但是,碳纤维的价格目前是玻璃纤维的10倍左右。
由于价格的因素,目前的叶片制造采用的增强材料主要以玻璃纤维为主。
因此玻璃纤维仍是风机叶片制造未来主要的增强材料。
随着叶片长度不断增加,叶片对增强材料的强度和刚性等性能也提出了新的要求,玻璃纤维在大型复合材料叶片制造中逐渐出现性能方面的不足。
为了保证叶片能够安全的承担风温度等外界载荷,风机叶片可以采用玻璃纤维/碳纤维混
杂复合材料结构,尤其是在翼缘等对材料强度和刚度要求较高的部位,则使用碳纤维作为增强材料。
这样,不仅可以提高叶片的承载能力,由于碳纤维具有导电性,也可以有效地避免雷击对叶片造成的损伤。
因此碳纤维在中国无法突破技术瓶颈的前提下,这种与玻璃纤维混搭增强也是一个重要市场。
其他增强材料方面,我国竹纤维增强风电叶片已经实现批量生产,因此天然纤维也将分得风电叶片市场的一杯羹。
基体材料
目前的风力发电机叶片基本上是由聚酯树脂、乙烯基树脂和环氧树脂等热固性基体树脂与玻璃纤维、碳纤维等增强材料,通过手工铺放或树脂注入等成型工艺复合而成。
为了提高复合材料叶片的承担载荷、耐腐蚀和耐冲刷等性能,必须对树脂基体系统进行精心设计和改进,采用性能优异的环氧树脂代替不饱和聚酯树脂,改善玻璃纤维/树脂界面的粘结性能,提高叶片的承载能力,扩大玻璃纤维在大型叶片中的应用范围。
同时,为了提高复合材料叶片在恶劣工作环境中长期使用性能,可以更多地采用耐紫外线辐射的新型环氧树脂系统。
夹层泡沫
夹芯材料成本约占叶片材料总成本的20%。
在风电叶片设计中,夹层结构芯材的选择主要考虑三个方面的因素:力学性能(强度、刚度和密度)要求、工艺条件(承受的温度、制品形状、芯材的加工等)要求和价格。
做好叶片夹层结构设计和芯材选择的前提是要充分了解各类芯材的性能特点,同时,一般要根据最终产品的性能和工艺方法进行特定的试验来减小风险。
在产品设计的初期就与芯材供应商进行充分的探讨则会取得事半功倍的效果。
可挤压糊状泥制作风叶阳模及风叶复合材料模具(涂敷胶衣)
胶粘剂等其他辅助材料
胶粘剂的作用是把叶片芯材与壳体,以及上、下半叶片壳体互相粘结,并将壳体缝隙填实从而构成牢固的整体。
在中国胶粘剂剂市场,多数通用型产品供大于求的局面没有改变,而部分高性能、高品质胶黏剂及胶黏制品需求量增加,如用于电子电气、精密仪器仪表、
汽车、航天航空等行业的产品。
由于市场需求量的快速增长和环保节能法规的强制执行,今后一些水基型、热熔型、生物降解型、光固化型、室温和低温固化型及无溶剂和高固含量型等环保节能产品,部分改性型、反应型、多功能型等高新技术产品,将会有较大发展,增长率将高于一般产品。
另外胶黏剂最大的需求将来自木工和建筑业,装配和运输业则是需求增长最快的领域。
随着专业化程度的不断增升,中国胶黏剂产品的质量和水平将会显著提高,生产将更趋集中。
真空灌注成型工艺适宜大型风机叶片批量生产
风机叶片是体现风能技术进步的关键风力机组部件,风机叶片产业是伴随着风电产业及风电设备产业的发展而迅速飙升的。
随着国内企业和科研院所的共同努力,中国风机叶片产业的供给能力迅速提升。
风电叶片是一种高性能的复合材料产品,制造条件要求高,温度要求16℃~25℃,空气湿度要求低于70%。
传统复合材料风力发电机叶片多采用手糊工艺制造。
目前,随着人们对环境保护意识的提高,风能作为清洁可再生的能源得到了社会各界高度的重视,风电产业飞速发展,从而对风力发电机叶片的需求也迅速增加,在风机叶片的批量生产上要求的技术水平也不断提升。
真空灌注成型工艺的出现解决了大型风机叶片批量生产的难题,目前这种工艺已被很多大型叶片制造商所看好,如:中材科技、中复连众、中航惠腾、东方电气等。
风机叶片用真空灌注成型工艺(Vacuum infusion process)的主要原理简单介绍如下:
首先在模腔中铺放好按性能和结构要求设计好的增强材料预成型体,采用注射设备将专用低粘度注射树脂体系注入闭合模腔,模具具有周边密封和紧固以及注射及排气系统,以保证树脂流动顺畅,并排出模腔中的全部气体和彻底浸润纤维,并且模具有加热系统,可进行加热固化而成型复合材料构件,属于半机械化的复合材料成型工艺。
工人只需将设计好的干纤维预成型体放到模具中合模,随后的工艺则完全靠模具和注射系统来完成和保障,没有任何树脂的暴露,因而对工人的技术和环境的要求远远低于手糊工艺,并可有效地控制产品质量。
同时由于采用了低粘
度树脂浸润纤维以及采用加温固化工艺,大大提高了复合材料质量和生产效率。
风机叶片真空吸塑成型(VRAM)工艺
在树脂传递模塑(RTM)工艺和真空辅助RTM工艺(VARTM)发展过程中,真空吸塑成型(VRAM)工艺的开发成功可谓具有里程碑的意义。
这一技术的应用不仅增加了树脂的传递动力,而且排除了模具及树脂中的气泡和水分,并且为树脂在模腔中的流动打工了通道,形成了完整的通路;更重要的是VRAM工艺完全利用真空,从而有效避免了在RTM和VARTM工艺中因注射产和的强大压力所引起的冲刷纤维现。