船舶推进装置设计
船舶动力装置课程设计轴系计算说明书

华中科技大学船舶与海洋工程学院轮机工程专业民用船舶动力装置课程设计轴系计算说明书一、轴系计算(一)、概述本船为内河船,设单机单桨。
主机经减速齿轮箱减速后将扭矩通过中间短轴传给螺旋桨轴和螺旋桨。
考虑到长江水质较差,泥沙较多,若采用水润滑,则污物可能进入艉轴装置造成堵塞,故润滑方式采用油润滑。
本计算按《CCS钢质内河船舶建造规范》(2009年)(简称《钢内规》)进行。
(二)、已知条件(三)、轴直径的确定根据《钢内规》8.2.2进行计算,计算列表4.1如下:表4.1轴直径计算根据计算结果,取螺旋桨轴直径为 350 mm,中间轴直径为 280 mm。
二、强度校核1.尾轴强度验算轴设计过程中艉轴承、密封装置、联轴节的选型如下:a.艉轴轴承选自东台市有铭船舶配件厂,规格如下:b.油润滑艉轴密封装置选自东台市有铭船舶配件厂,规格如下:c.联轴节采用船厂自制。
尾轴危险段面的确定根据图4-1计算如下:图4-1尾轴管结构简图(1)相关尺寸确定已知L=880mm,L b=440mm,R=350mma螺旋桨轴尾部锥长l=(1.6~3.3)R=2.2*R=780mm,z对于白合金轴承,支撑点到后端面的距离u=0.5L=0.5*880=440mm。
而后密封装置的长度为215mm,再加上适当间距约为60mm,则:螺旋桨轴尾部锥面中心至后轴承中心距离a为:a=780/2+440+215+60=1105mm螺旋桨轴尾部锥面后端面至后轴承中心距离b为:b=1105+780/2=1495mm由布置总图得后轴承的后端面距前轴承中心约为4739mm,则:前后轴承支撑点距离l为:l=4739-440=4299mm因为后轴承后端面距齿轮箱有约7130mm,考虑到齿轮箱的周和联轴节等,法兰端面到前轴承支撑点距离为:d=7130-4299-440-769=2391mm因为联轴节长845mm ,则法兰重心到前轴承支撑点距离为: c=2391-845=1546mm(2)双支承轴承负荷计算: a .后轴承压力= 15873.21 N式中:g —9.81N/kg 1—前后轴承支撑点距离,4.299ma---螺旋桨中心至后轴承中心距离,1.105m b —桨毂后端面到后轴承支撑点距离,1.495m c —法兰重心到前轴承支撑点距离,1.546md —法兰端面到前轴承支撑点距离,2.391m G 0—法兰重量,1180kgQ B —螺旋桨及附件重量,4079.51kgq c —轴本身重量产生的均布负荷 ,q c=0.00622c d =0.0062×3502=759.5kg/mb .前轴承总压力⎥⎦⎤⎢⎣⎡--+++=l a Q l 2b q l c)(l G l 2d l q g B 2c 02c)(B R = 4596.65 N 式中:g —9.81N/kg 1—前后轴承支撑点距离,4.299ma---螺旋桨中心至后轴承中心距离,1.105m b —桨毂后端面到后轴承支撑点距离,1.495m c —法兰重心到前轴承支撑点距离,1.546md —法兰端面到前轴承支撑点距离,2.391m G 0—法兰重量,1180kgQ B —螺旋桨及附件重量,4079.51kgq c —轴本身重量产生的均布负荷 ,q c=0.00622c d =0.0062×3502=759.5kg/m1.截面E —E 的弯矩/2a 2L q g 2L R 2L a g Q M 2A cA A AB EE ⎪⎭⎫⎝⎛+⋅⋅-⋅+⎪⎭⎫ ⎝⎛+⋅-=- = —63745.48N ·m式中:g —9.81N/kgQ B —螺旋桨及附件重量,4079.51kg a —螺旋桨中心至后轴承中心距离,1.105m R A —后轴承支反力,15873.21 N L A —后轴承长度,0.88m q c —轴本身重量产生的均布负荷q c=0.00622c d =0.0062×3502=759.5kg/m其中d c 为尾轴直径,350mm 2.截面K -K 的弯矩c2B A B KK 2gq )Q -(R a g Q M g ⋅+⋅⋅-=-= —5093.61N ·m式中:g —9.81N/kgQ B —螺旋桨及附件重量,4079.51kg a —螺旋桨中心至后轴承中心距离,1.105m R A —后轴承支反力,15873.21 N q c —轴本身重量产生的均布负荷q c=0.00622c d =0.0062×3502=759.5kg/m其中d c 为尾轴直径,350mmK K E E M M -->,取E E M -=—63745.48N ·m 作为计算弯曲力矩。
船舶动力装置课程设计

船舶动力装置课程设计一、课程目标知识目标:1. 让学生掌握船舶动力装置的基本概念、分类及其工作原理;2. 使学生了解船舶动力装置的组成部分,包括主机、辅机、传动装置等;3. 帮助学生理解船舶动力装置的性能指标及其对船舶性能的影响。
技能目标:1. 培养学生运用所学知识分析船舶动力装置的优缺点,并能够提出改进措施;2. 培养学生具备船舶动力装置操作、维护及故障排除的基本能力;3. 提高学生的团队协作和沟通能力,能够就船舶动力装置相关技术问题进行讨论和交流。
情感态度价值观目标:1. 激发学生对船舶动力装置的兴趣,培养其探索精神和创新意识;2. 培养学生热爱航海事业,树立正确的职业观念;3. 培养学生关注能源、环保等问题,提高其社会责任感和使命感。
分析课程性质、学生特点和教学要求:本课程为船舶工程专业核心课程,具有较强的理论性和实践性。
学生为高中毕业生,具备一定的物理和数学基础,但对船舶动力装置的了解较少。
教学要求注重理论联系实际,强调实践操作能力的培养。
根据以上分析,将课程目标分解为以下具体学习成果:1. 学生能够准确描述船舶动力装置的基本概念、分类和工作原理;2. 学生能够列出船舶动力装置的主要组成部分,并解释其作用;3. 学生能够分析船舶动力装置的性能指标,并评价其对船舶性能的影响;4. 学生能够针对特定船舶动力装置,提出改进措施,并进行操作、维护和故障排除;5. 学生能够积极参与团队讨论,就船舶动力装置相关技术问题进行有效沟通;6. 学生能够关注船舶动力装置的能源、环保问题,并提出自己的见解。
二、教学内容根据课程目标,教学内容分为以下五个部分:1. 船舶动力装置概述- 教材章节:第一章 船舶动力装置概述- 内容:动力装置的概念、分类、发展历程及其在船舶中的作用。
2. 船舶动力装置的组成部分- 教材章节:第二章 船舶动力装置的组成部分- 内容:主机、辅机、传动装置、推进装置、控制系统等组成部分的结构、原理及功能。
船舶推进轴系锁紧装置的设计与应用
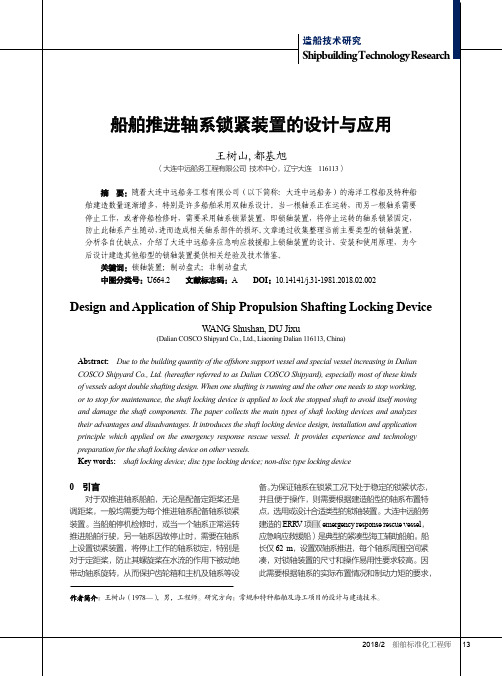
设计合适有效的锁轴装置。
1 锁轴装置类型及比较目前在实际的船舶应用中,锁轴装置[1]主要分两种:制动盘式锁轴装置和非制动盘式锁轴装置。
1.1 制动盘式锁轴装置制动盘式锁轴装置分为盘式锁轴装置和销式锁轴装置。
盘式锁轴装置是指在轴系上安装较大制动盘,通过刹车带动抱紧制动盘,进而锁紧螺旋桨轴系,常应用于调距桨船舶。
销式锁轴装置同样是在轴系上设置较大的制动盘,盘上在圆周方向加工有若干销孔,当要锁轴时,将制动销插入制动盘上的销孔中,进行轴系锁紧。
制动盘式锁轴装置加工制作相对复杂,成本较高,安装时占用空间较大,使用及安装不便,锁轴装置工作状态信号不易输出等[2]。
因此,为克服上述缺点,现在船舶采用的锁轴装置大部分使用螺旋桨法兰锁轴装置。
1.2 非制动盘式锁轴装置非制动盘式锁轴装置包括轴系法兰钻孔式和法兰开槽式。
轴系法兰锁轴装置(钻孔式)固定轴系,如图1所示,即采用锁轴销卡入法兰钻孔的方式来实现螺旋桨轴系的锁定,其优点是与制动盘式锁轴以及销式锁轴相比,螺旋桨轴系法兰代替制动盘,体积较小,制造成本低,结构简单,安装及维修方便,锁紧力较大,对轴系的锁定牢固,在外力作用下不易脱开。
缺点是法兰钻孔会影响法兰强度,因此设计此锁轴装置时应考虑到法兰强度计算,而且制动法兰需要加大尺寸。
1-锁轴盘;2-锁轴销;3-行程挡板;4-行程开关;5-丝杆;6-旋转手柄;7-支架;8-前行程开关;9-后行程开关图1 轴系法兰锁轴装置(钻孔式)示意图法兰开槽式锁轴装置,如图2所示,锁紧块和底座用固定螺栓固定在船体上,并将底座和船体焊接在一起。
锁紧销和左、右固定板通过两个锁紧螺栓连接在一起,限制锁紧销的轴向位置。
(a) 机构图(b) 实景图图2 锁轴装置安装图法兰开槽式锁轴装置的工作原理是:当锁紧销的上部分插入到中间轴法兰开口,下部分卡到锁紧块的槽中时,限制了轴法兰的旋转,从而实现了轴系的止动;当把锁紧螺栓拆卸下来,把锁紧销从中间轴法兰开口和锁紧块槽中抽出来后,主机才能起动,轴系才能旋转。
船舶推进系统的设计与优化
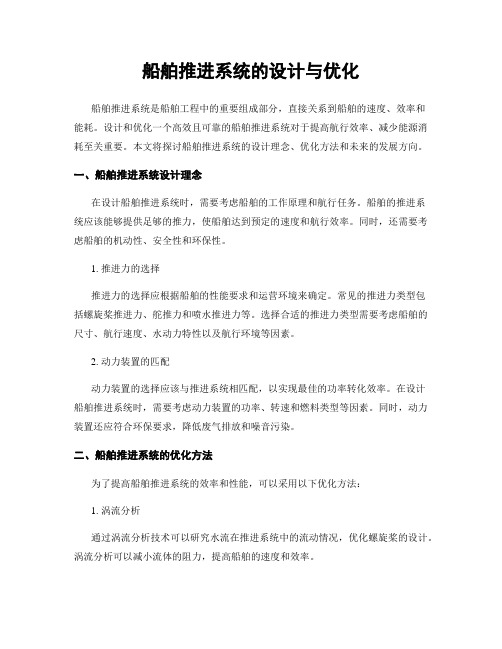
船舶推进系统的设计与优化船舶推进系统是船舶工程中的重要组成部分,直接关系到船舶的速度、效率和能耗。
设计和优化一个高效且可靠的船舶推进系统对于提高航行效率、减少能源消耗至关重要。
本文将探讨船舶推进系统的设计理念、优化方法和未来的发展方向。
一、船舶推进系统设计理念在设计船舶推进系统时,需要考虑船舶的工作原理和航行任务。
船舶的推进系统应该能够提供足够的推力,使船舶达到预定的速度和航行效率。
同时,还需要考虑船舶的机动性、安全性和环保性。
1. 推进力的选择推进力的选择应根据船舶的性能要求和运营环境来确定。
常见的推进力类型包括螺旋桨推进力、舵推力和喷水推进力等。
选择合适的推进力类型需要考虑船舶的尺寸、航行速度、水动力特性以及航行环境等因素。
2. 动力装置的匹配动力装置的选择应该与推进系统相匹配,以实现最佳的功率转化效率。
在设计船舶推进系统时,需要考虑动力装置的功率、转速和燃料类型等因素。
同时,动力装置还应符合环保要求,降低废气排放和噪音污染。
二、船舶推进系统的优化方法为了提高船舶推进系统的效率和性能,可以采用以下优化方法:1. 涡流分析通过涡流分析技术可以研究水流在推进系统中的流动情况,优化螺旋桨的设计。
涡流分析可以减小流体的阻力,提高船舶的速度和效率。
2. 燃油优化优化燃油的使用可以降低船舶的能源消耗,减少碳排放。
可以通过改进燃烧系统、提高燃油的燃烧效率,或者采用更加清洁的燃料替代传统燃油。
3. 自动控制系统采用自动控制系统可以提高船舶的航行稳定性和推进系统的效率。
自动控制系统可以根据船舶的航行状态和运营环境自动调整推进力和动力输出,实现最佳的船舶性能和能源利用效率。
三、船舶推进系统的未来发展方向随着科技的不断进步和创新,船舶推进系统也将面临新的发展方向。
1. 新材料的应用新材料的应用可以提高船舶推进系统的轻量化和耐用性。
例如,采用碳纤维复合材料可以减轻船舶的自重,提高推进效率;使用耐腐蚀材料可以提高推进系统的寿命和可靠性。
船舶动力装置课程设计说明书
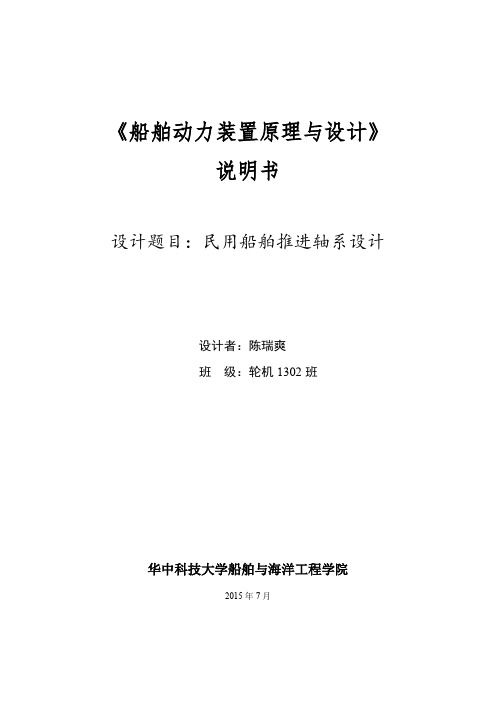
《船舶动力装置原理与设计》说明书设计题目:民用船舶推进轴系设计设计者:陈瑞爽班级:轮机1302班华中科技大学船舶与海洋工程学院2015年7月一.设计目的主机与传动设备、轴系和推进器以及附属系统,构成船舶推进装置。
因此,推进装置是动力装置的主体,其技术性能直接代表动力装置的特点。
推进装置的设计包括轴系布置、结构设计、强度校核以及传动附件的设计与选型等,而尾轴管装置的作用是支承尾轴及螺旋浆轴,不使舷外水漏人船内,也不能使尾轴管中的润滑油外泄,因此,尾轴管在推进系统设计中意义重大。
本设计是根据指导老师给出的条件,对船舶动力装置进行设计,既是对课程更深入的理解,也是对自身专业能力的锻炼。
二,设计详述2.1:布置设计本船为单机单桨。
主机经减速齿轮箱减速后将扭矩通过中间短轴传给螺旋桨轴和螺旋桨。
本计算是按《钢质海船入级规范》(2006年)(简称《海规》)进行。
因此,我们将轴系布置在船舶纵中剖面上,其中,轴的总长为9000mm,轴系布置草图及相关尺寸,见图1。
图12.2:轴系计算(一):已知条件:1.主机:型号:8PC2-6型式:四冲程,直列,不可逆转,涡轮增压,空冷船用柴油机缸数:8缸径/行程:400/460mm最大功率(MCR):4400kW×520rpm持续服务功率:3960kW×520rpm燃油消耗率:186g/kW·h+5%滑油消耗率:1.4g/kW·h起动方式:压缩空气3~1.2MPa生产厂:陕西柴油机厂2.齿轮箱:型号300,减速比3:1。
3.轴:材料35#钢,抗拉强度530MPa,屈服强度315MPa。
4.键:材料45#钢,抗拉强度600MPa,屈服强度355MPa。
5.螺栓:材料35#钢,抗拉强度530MPa,屈服强度315MPa(二):轴直径的确定根据已知条件和“海规”,我们可以计算出轴的相关数据,计算列表见表3.1:表3.1轴直径计算考虑到航行余量,轴径应在计算的基础上增大10%。
一种船用无轴轮缘推进器的设计研究

一种船用无轴轮缘推进器的设计研究设计研究报告:船用无轴轮缘推进器一、引言船舶推进器是船舶动力系统中的重要组成部分,直接影响船舶的航行性能,特别是在船舶的速度、操纵性和节能性方面具有重要的作用。
无轴轮缘推进器是一种新型的船舶推进器,能够有效减少水流对轮缘的阻力,提高推进效率,减小船舶耗能,因此备受关注。
本文将对船用无轴轮缘推进器的设计研究进行详细讨论。
二、传统轮缘推进器的缺陷及无轴轮缘推进器的优势传统的轮缘推进器存在一些缺陷,例如轮缘表面存在船体表面阻力、漩涡损失和压力波损失等问题,导致推进效率低下。
而无轴轮缘推进器采用了全新的推进原理,能够减少水流对轮缘的阻力,提高推进效率,降低能耗,具有较大的优势。
三、无轴轮缘推进器的结构和工作原理无轴轮缘推进器由轮缘、扁平薄壁等组成。
其工作原理是利用薄壁的特性,在扁平薄壁的阻挡面上产生对水流的引导作用,从而达到推进的目的。
该设计有效减少了水流对轮缘的阻力,提高了推进效率。
四、无轴轮缘推进器的设计要点1.轮缘的形状设计:要设计适合水流流动的轮缘形状,减小水流对轮缘的阻力;2.薄壁的选择:要选择适合的薄壁材料,既要保证薄壁的强度,又要保证轻盈的特性;3.轮缘与扁平薄壁的组合设计:要充分考虑轮缘与扁平薄壁之间的结合方式,确保结构牢固、无漏水;4.推进效率的优化设计:要通过有效的流体动力学分析与计算,优化推进器的设计,提高推进效率。
五、实验验证通过实验验证,无轴轮缘推进器的推进效率明显优于传统轮缘推进器,在不同船速下,无轴轮缘推进器的能耗明显减小,推进效率提高。
六、结论无轴轮缘推进器是一种具有较大发展潜力的船舶推进器,其推进原理新颖、推进效率显著提高。
通过合理的设计和优化,可以进一步提高无轴轮缘推进器的性能,为船舶的节能减排提供重要支持。
综上所述,船用无轴轮缘推进器的设计研究具有重要的意义和价值,有望成为未来船舶推进器的重要发展方向。
希望本文能够对相关领域的研究者和工程师们有所启发,激发更多创新思路,推动该领域的发展和进步。
柴油机主推进动力装置船舶余热利用系统优化设计
针对以上问题,本次演示提出以下优化设计方案:
1、能量回收利用
为了提高能量的回收利用率,我们提出一种新型的能量回收系统——多级能 量回收系统(MERS)。该系统将废热分为多个等级进行回收,根据不同等级废热 的特性,分别用于船舶动力装置、加热、制冷等多个方面。同时,该系统还采用 了先进的热能存储技术,确保在废热不足时,能够通过存储的热量进行补充。
2、设备优化设计
在设备方面,我们针对传统的换热器、冷却装置进行优化设计。首先,换热 器采用高性能材料,提高换热效率;其次,冷却装置采用新型的多级冷却系统 (MCS),将废热在不同温度等级下进行冷却,提高冷却效果。此外,我们还引 入了先进的存储装置,该装置采用新型的相变材料(PCM),能够在不同的温度 下吸收和释放热量,进一步提高能量的利用效率。
柴油机主推进动力装置船舶余 热利用系2 文献综述
03 系统优化设计
04 结论
05 参考内容
引言
随着全球能源需求的持续增长,船舶作为长途运输的重要工具,其节能减排 的重要性日益凸显。柴油机作为船舶主推进动力装置的核心部件,其在运转过程 中会释放大量余热。如何有效利用这些余热,提高船舶能源利用效率,成为当前 研究的热点问题。本次演示将对柴油机主推进动力装置船舶余热利用系统的优化 设计进行探讨。
参考内容
一、引言
随着全球船舶运输的快速发展,船舶在航行过程中需要大量的淡水资源。然 而,海上航行时,淡水储备往往受到限制。因此,开发一种能够利用船舶余热进 行海水淡化的装置具有重要意义。本次演示将介绍一种船舶余热低温蒸馏海水淡 化装置的设计方案及其实验验证。
二、设计思路
该船舶余热低温蒸馏海水淡化装置主要包括以下几个部分:热交换器、蒸发 器、冷凝器以及淡水储罐。其工作原理是利用船舶主发动机运转过程中产生的余 热,将加热后的海水引入蒸发器,随后在蒸发器内加热蒸发产生水蒸气。水蒸气 上升至冷凝器,遇到较低温度的冷凝管,形成液态水流入淡水储罐,最终得到淡 水。
iSIGHT在船舶推进器设计方面的运用
iSIGHT在船舶推进器设计方面的运用丁恩宝何凌中船重工集团第702研究所iSIGHT在船舶推进器设计方面的运用----螺旋桨敞水性能优化丁恩宝何凌中船重工集团第702研究所摘要:本文基于iSIGHT优化平台建立了螺旋桨敞水性能优化方法,调用的程序有MATLAB、Unigraphics、GAMBIT、FLUENT等,敞水性能预报采用的是CFD方法,优化设计的对象仅包括螺距分布,优化目标是敞水效率和最小压力系数,通过对计算结果的分析,螺距分布对效率和最小压力系数的影响趋势是合理的,通过优化敞水效率比常规螺距分布提高了约0.3%,而最小压力系数也有提高,优化的效果达到了预期目的。
关键词: 螺旋桨敞水性能效率优化1引言随着世界经济一体化的进展,国际航运业的竞争日趋激烈,也给世界造船业带来了机遇与挑战。
为了适应这种新的世界经济格局,我国政府提出了成为世界造船第一大国的目标。
近十年来民用船舶的生产正朝着大型化和高性能化方向发展,船舶的吨位和功率不断加大,同时船舶航速也不断提高,这造成了船舶螺旋桨设计条件的复杂化,使设计性能良好的螺旋桨变得更为困难。
如果说使螺旋桨具有最高效率为唯一设计目标的做法已成为历史,那么作为现代螺旋桨设计要追求的目标,还应包括减小螺旋桨对船体的诱导脉动压力和轴承力,消除桨叶空泡发展带来的有害后果(振动、噪声以及桨叶和舵的剥蚀)等要求。
随着民用船舶向大型化、超大型化方向发展,带来的必然后果是使船用螺旋桨盘面处伴流场不均匀程度越来越高,从而恶化了螺旋桨工作环境;另外主机功率的增加,使螺旋桨单位面积上负荷加大,同时螺旋桨叶梢流动线速度也大大增加,这些影响促使螺旋桨的空泡和激振问题变得十分突出。
因此在现代民用船舶螺旋桨的设计过程中,必须对螺旋桨的效率、空泡与空泡剥蚀、振动和噪声性能进行全面的权衡,设计者应该有足够可靠的设计计算方法,根据总体性能的要求,确定螺旋桨的最佳几何参数。
为此长期以来,国际上螺旋桨设计商对工作在不均匀伴流场中的螺旋桨设计技术的研究和开发作了大量的投入,螺旋桨理论设计技术和试验验证技术日趋完善,高效率、低激振、安静型螺旋桨设计方法已得到广泛应用,如叶梢卸载、中、大侧斜外形和新型抗空泡叶剖面等螺旋桨设计技术,在抑制螺旋桨空泡、降低激振力和噪声方面取得了很好的效果。
吊舱式船舶电力推进实验系统的设计
简单 , 安装 方便 , 易于维护 , 选择范 围广等优 点 , 适合 远距离
数据传输 , 因此系统利用 其作 为传输指令 和信号 的通道 。
3 实 验 系统 控 制方 案
吊舱式 电力推进实验系统 的控制方案主要 由推进控制 子 系统 和回转控 制 子系 统两 部分 组 成。其结 构 如 图 2所
l 操作面板 l T 0 M l lE 2 0 图 1 吊舱 式 电 力推 进 实 验 系统 布 局 图
万 钟 睦 志 剑
面
睦 . I 剑 控 制
I言 L 型 / 号
馗
l操作面板 I l 73 0 L - P Cl s 0
_ 1 鳖
回转控制
性能和处理故障 的能力 。
系统 的设计应该满足 以下性能指标 : 1 )远程操作 与就地 操作之 间 的无扰 切换 。能够及 时 响应操作 台切换命令 , 完成功能移交和功能切 除。 2 )港 内航行模 式 的选择 。航 行模 式主要 有港 内航 行 模式 、 正常航行模式和 紧急停船 模式 。每 种航行 模式 对应 不同的航行 工况 , 系统 能够根 据 工况 的变 化 , 切换 航行 模
吊舱式船舶 电力推进实 验系统 , 整个 系统 硬件结 构 由驾 控
台、 机旁 台和船体模 型组成 , 主要 控制 系统 有推进控制子 系
统 和 回转 控 制 子 系 统 。
2 系统结构与主要功能
本实验系统主要由驾控 台、 机旁台和船体模 型构成 , 如
图 1 示。 所
于船舶动力系统 的简化和布局 , 优化船 舶总体设计 , 改善操
8 6
朱
楼等 : 吊舱式船 舶电力推进实验 系统 的设计
船舶动力装置原理与设计_第1章
Tips:汽轮机推进装置主要采用的是汽轮机+减速齿轮箱+定距桨的形式;少数采 用汽轮机电力传动形式。
2019年3月30日星期六
17
燃气轮机推进动力装置
• • • • • 优点: a. 重量尺寸小; b. 操纵方便,备车迅速; c. 自巡航到全速工况加速迅速; d. 具有多机组并车的可靠性; • 缺点: • a. 必须配备不同燃料及相应的 管路及贮存设备; • b. 主减速器的小齿轮数目多, 结构复杂; • c. 在减速器周围布置有难度。
• e. 管理与检修费较低。
• 潜艇蓄电池也是一种电力推进装置
2019年3月30日星期六
26
目前舰艇电力推进装置的发展动向
• 以交流(交流发电机和交流电动机)电力推进装置取代 直流(直流发电机和直流电动机)电力推进和交直流 (交流整流发电机和直流电动机)电力推进装置
– 交流电力推进装置具有极限功率大,效率高和可靠性好的优点, 根据推进电机的类型,可分为异步电动机和同步电动机交流推 进装置;而根据电流交换器的结构形式不同分为晶闸管变频交 流电力推进装置、电力晶体管和可关断晶闸管交流电力推进装 置. – 是以超导电机(超导发电机和超导电动机)为功率元件的电力 推进装置,与普通电力推进相比,具有重量轻、体积小、效率 高、噪声低的特点。由于超导材料必须工作在相应的临界温度 以下,要有一套复杂的液氮设备,所以在一定程度上制约了它 的广泛应用。近年来,随着低温技术的迅速发展,特别是低温 技术的小型化,为超导电力推进在舰艇上的应用提供了良好的 条件。。
2019年3月30日星期六
- 1、下载文档前请自行甄别文档内容的完整性,平台不提供额外的编辑、内容补充、找答案等附加服务。
- 2、"仅部分预览"的文档,不可在线预览部分如存在完整性等问题,可反馈申请退款(可完整预览的文档不适用该条件!)。
- 3、如文档侵犯您的权益,请联系客服反馈,我们会尽快为您处理(人工客服工作时间:9:00-18:30)。
⒈初步匹配设计
已知船体主尺度、船体的有效功率曲线、船舶要求 的航速,螺旋桨的直径D或转速n、确定螺旋桨的效 率、螺距比p/D、螺旋桨的最佳直径及所需主机的 功率,便于主机与传动设备的选型。
初步匹配设计有两种方案,一种是已知螺旋桨直径
D求转速n;一种是已知螺旋桨转速n求直径D。
由图2-3和图2-4可以得出螺旋桨的效率、螺距比p/D、螺 旋桨的最佳直径(或转速)及所需主机的功率和转速等参数, 我们可以根据这些数据来选定主机。在选择主机时还要考虑 其它一些因素,如:功率储备问题;传动型式是直接还是间 接传动或特殊传动;是否需要减速,速比为多少等。
主机
减速器/离合器 螺旋桨 轴系
轴带发电机(Shaft generator)
⒊特殊传动推进装置
特殊传动通常是指电力传动、可调螺距螺旋桨传动、 液压马达传动、Z型推进和同轴对转螺旋桨传动等。
⑴可调螺距螺旋桨推进装置
通过改变螺旋桨螺距来改变船舶航速和正倒航向。 在这种装置中,螺旋桨的桨叶是可以转动的,只要 转动桨叶,便可改变螺旋桨的螺距,从而改变桨的 推力大小及方向。
㈣主机的选型分析
主机选型是根据设计任务书中的技术要求以及船体 设计所提供的资料来进行的,与螺旋桨的设计密切 相关。推进装置的选型是通过船、机、桨匹配计算
和分析选定螺旋桨参数和主机功率、转速等参数,
在满足设计的技术要求基础上,同时考虑重量和尺 寸、油耗、造价、可靠性、可维度、使用寿命、等 因素,选择一套从主机到螺旋桨的最佳方案。 图谱法。 机桨匹配计算可分为初步匹配和终结匹配两阶段。
以上是针对某一盘面比的 桨进行计算的,在实际匹 配设计中还要选择若干盘 面比的梁来进行比较,得 出不同盘面比所能达到的 航速和螺旋桨要素,然后 进行螺旋桨的空泡计算校 核,得出其不发生空泡的 最小盘面比的螺旋桨及所 对应的最大航速和螺旋桨 参数。
⑶Z型传动(Z type transmission)
主机经万向轴和轴 系带动螺旋桨、螺 旋桨轴可360回转, 船舶不设舵。
特点:省舵、尾轴 管,船尾形状简单, 阻力小;操纵性能 好,可原地回转;
与中高速机连用, 1-主机 2-联轴器 3-离合器 4-万向轴 5-滑动轴承 6-弹性联轴节 7-滚动轴承 8-上水平
其主要特点是:在部分负荷下能有较好的经济性; 能适应船舶阻力的变化,充分利用主机的功率;机 构比较复杂、造价高。
⑵电力传动推进装置
电力传动是主机驱动发电机组发电,然后并网,再 由电网供电给电动机驱动螺旋桨的一种传动型式。
其主要特点是:机组配置和布置比较灵活、方便, 舱室利用率高;改变直流电动机的电流方向可使螺 旋桨转向改变,便于遥控,机动性与操纵性好;发 电机转速不受螺旋桨转速限制;正倒车具有相同功 率和运转性能,具有良好的拖动性能;传动效率低; 增加了发电机和电动机,装置总的重量和尺寸较大, 造价和维修费用较贵。
推进装置的型式除了传动方式外,还涉及到轴系的 数目、推进器的型式和螺旋桨的类型等。
⒈直接传动
直接传动是主机直接通过轴系把功率传给螺旋桨,在主机与 轴系中间无其它传动设备,在任何工况下,螺旋桨与主机具 有相同的转速与转向。
直接传动一般应用于选用大型低速柴油机作为主机的船舶。 特点:传动效率高;燃料费用低,经济性好;结构简单,维
㈠概述
推进装置是船舶动力装置的重要组成部分, 它包括主机、传动设备、轴系和推进器等。 其作用是由主机发出功率,并通过传动设备 和轴系将功率传递给推进器,以推进船舶。
推进装置的设计是根据船舶设计任务书的要 求,设计出一套经济、可靠、机动性及操纵 性好的推进装置。具体的内容一般包括推进
装置型式确定,主机的选型,轴系的设计
⒉终结匹配设计
按照初步匹配设计所确定的主机功率与转速所选 用的主机与传动设备,其功率与转速与初步匹配 设计时不完全相同,还需要进行终结匹配设计。 终结匹配设计即是根据选定主机的功率和转速、 传动设备与轴系的传送效率,算得桨的收到功率、 桨的功率、船身效率等,计算船船舶所能达到的 航速和螺旋桨的最佳要素。终结匹配设计由表2- 3所列步骤计算,结果由作图2-55确定。
轴 9-上部螺旋锥齿轮 10-涡轮蜗杆装置 11-齿式联轴器 12-垂直轴 13-螺旋桨 14-下部
且装不置设 ;单 主独 机的 不减 用速 换 螺旋锥齿轮 15-下水平轴 16-旋转套筒 17-支架 向,寿命延长;
[9]
㈢选择传动方式的四个原则
⒈按船舶用途、种类与要求 ⑴航行工况稳定的船舶,推进装置大多数是单机单机桨直接
修保养方便;重量与尺寸大;机动性差;非设计工况下运转 时的经济性差;低速和微速航行受柴油机最低稳定转速的限 制。
主机
轴系
螺旋桨
⒉间接传动
间接传动是通过传动设备将主机与轴系连接在一起的一种传 动方式。在这种传动装置中,主机转速与螺旋桨转速有差别 或保持一定的速比。
间接传动一般应用于选用中、高速柴油机作主机的船舶,其 特点是:重量与尺寸小;主机的转速不受螺旋桨转速限制; 轴系布置方便;带倒顺车离合器时可选用不可逆转的主机; 有利于采用多机并车、单机分车与轴带发电机的布置;结构 相对复杂;传动效率较低。
传动,螺旋桨使用定距桨,在设计工况下推进效率较高。 ⑵客船要求较高的航速,吃水相对较浅,同时考虑其安全性
能、机动性和操纵性要求较高,因此,其推进装置多采用双 机双桨。如果主机采用中、高速机,则必须采用间接传动。 ⑶工况变化频繁的船舶,机动性要求高,而且机舱尺寸有限, 故采用中、高速机,多机多桨,并采用间接传动或调距桨。 对于特殊的工程船可采用电力传动装置。 ⒉按主机总功率的大小:主机总功率若要求过大,则采用多 机多桨,多机单桨等形式。 ⒊按船舶航区的吃水深度:吃水深度影响螺旋桨的直径。 ⒋按推进装置的经济性:初始投资、运输成本等等。
以及传动设备的计算与选型。
㈡舰船推进装置的传动方式
推进装置是由主机、传动设备、轴系及推进器所组 成。由于船舶的用途、航区和性能的不同,使主机 的类型与数目、传动方式、轴系的数目、推进器的 类型与数目必然不一,构成了具有不同特点的推进 装置。
推进装置的传动方式一般可分为直接传动,间接传 动和特殊传动三类 。