FORD流程介绍
福特业务流程分析
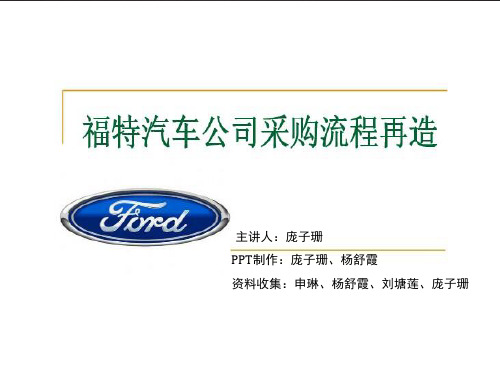
0 但是参观了Mazda之后,他们震惊了,Mazda是家小公司,
其在福特公司占有22%的股份,而马自达汽车公司做同样 工作的人只有五人。
部门人数
600 500 400 300 200 100 0 福特 马自达 部门人数
0 尽管两个公司在规模上存在一定的差距,但是5:500
的差距却让福特公司震惊。。
新流程采用的是 “无发票”制 度,大大简化工 作环节
带来的结果
1.以往应付款部门需在订单、验收报告和 发票中核查14项内客,而如今只需3项——零 件名称、数量和供货商代码; 2.实现裁员75%,而非原定的20%;
3.由于订单和验收单的自然吻合,使得付 款也必然及时而准确,从而简化了物料管理 工作,并使得财务信息更加准确。
第一组:庞子珊、杨舒霞、刘塘莲、申琳
于是他们推翻了第一组方案,决定对其公司及与 应付账款部门相关的整个业务流程进行彻底重组。
新的业务流程是这样的: 1.采购部门发出订单,同时将订单内容输入联机数 据库; 2.供货商发货,验收部门核查来货是否与数据库中 的内容相吻合,如果吻合就收货,并在终端上按键通 知数据库,计算机会自动按时付款。
1、采购部门向订货商发出订单,并将订单的复印件送往应付款部 门; 2、供货商发货,福特的验收部门收检,并将验收报告送到应付款 部门(验收部门自己无权处理验收信息) 3、同时,供货商将产品发票送至应付款部门,当且仅当“订 单”,“验收报告”以及“发票”三者一致时,应付款部门才能付 款而往往,该部门的大部分时间都花费在处理这三者的不吻合上, 从而造成了人员,资金和时间的浪费
福特汽车公司原先的原材料、零部件采购流程显然是 按常规办事的。流程一开始,由采购部门向供应商发出购 货订单,并将一份副本送交应付账款部门。供应商发货, 货物运到福特汽车公司的收货点后,点上的办事人员填写 一份表格,说明收到货物的情况,并将表格发交给应付账 款部门。与此同时,供应商向福特汽车公司的应付账款部 门送去发票。 现在,福特汽车公司的应付账款部门关于 这批货物有三种凭证——购货订单、收货凭证和发票。如 果这三种凭证上的数据互相吻合,应付账款部门的办事人 员就签字同意付款。
福特质量体系 ppt课件 (2)
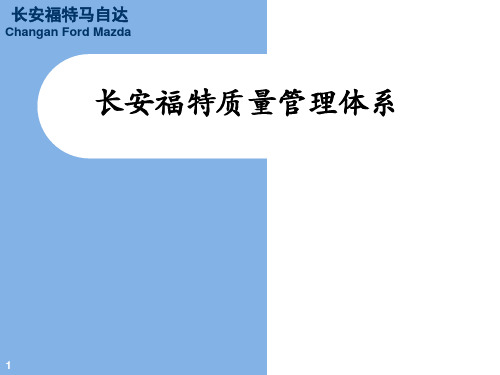
Consumer Magazine Information (e.g.
Consumer Reports, ADAC, Quatro Rodas, What Car?)
GQRS: 3 MIS TGW/1000
Trend
Other Survey Data (e.g. IQS, APEAL, VQS,
NCBS)
Exte外rna部l I信nd息icators D
(市场调研和三包信息)
市M场ar分ke析t A Analysis
I+C+R
产品和E制ngi造ne工erin程g 标准
对顾客抱怨Pri的ori问tiz题e Is进su行es优th先at 度do排no序t
M&A
✓ 平衡质量单议程(BSAQ)顾客柏拉图 – 每月更新
Trend
Warranty: 1 MIS R/1000
Trend
Warranty: 12 MIS R/1000
TreWndarranty: 3 MIS R/1000
Trend Warranty: R/1000 Best In Ford
Warranty: 0 MIS CPU
Trend
Warranty: 1 MIS CPU
VRT RYG Chart
BSAQ / VRT Action Matrix /
Roadmap
BSAQ Leadtime Current
VOME Health Charts NEW
Indicates Charts are stacked on top of each other
Work Group Board
0 MIS R/1000 Trend
0 MIS CPU Trend
Ford汽车公司采购应付账款部门的业务流程再造案例

Ford汽车公司采购应付账款部门的业务流程重组案例分析网络营销2班 3101167029 陈慧一、案例背景福特汽车公司是美国三大汽车巨头之一,但是到了20世纪80年代初,福特像许多美国大企业一样面临着日本竞争对手的挑战,正想方设法削减管理费和各种行政开支。
北美福特汽车公司2/3的汽车部件需要从外部供应商购进,为此需要有相当多的雇员从事应付账款管理工作,当时,公司财会部有500多名员工,负责审核并签发供应商供货账单的应付款项。
按照传统观念,这么大一家汽车公司,业务量如此之大,有500多个员工处理应付账款是合情合理的。
促使福特公司认真考虑“应付账款”工作的是日本马自达汽车公司。
这是一家福特公司占股22%的参股公司,有5位职员负责应付账款工作。
尽管两个公司在规模上存在一定的差距,但按公司规模进行数据调整后,福特公司仍多雇佣了5倍的员工,5:500这个比例让福特公司的经理再也无法泰然处之了。
福特公司决定对与应付账款相关的整个业务流程进行彻底重组。
进行业务重组之前,管理人员计划通过业务流程重组和应用计算机系统,将员工裁减到最多不超过400人,实现裁员20%的目标。
Ford公司应付账款部门原来的业务流程: 财会部门接受采购部门送来的采购订单副本、仓库的验货单和供应商的发票,然后将三张票据在一起进行核对,查看其中的14项数据是否相符,核对相符后,财会部门才予以付款。
财会部门要花费大量的时间核对三张单据上14项数据是否相符。
原付款业务处理流程如图1示。
图1 重组前的业务流程第一,采购部门向供应商发出订单,并将订单的副本送往应付款部门;第二,供应商发货,福特的验收部门收检,并将验收报告送到财会部;第三,供应商同时将产品发票送至财会部。
可以看出从采购部门向供应商发出订单到最后的付款有许多环节,尤其是“订单”、“验收单”和“发票”三者一致时才能付款的条件引出了大量的单证核对,这不仅耗费了财务和仓库的大量人力、时间和资金,而且还常发生差错和延误付款的事件。
福特问题解决之8D报告

福特问题解决之8D流程8D又称团队导向问题解决方法,8D问题求解法(Eight Disciplines Problem Solving)是福特公司处理问题的一种方法,亦适用于制程能力指数低於其应有值时有关问题的解决。
它提供了一套符合逻辑的解决问题的方法,同时对於统计制程管制与实际的品质提升架起了一座桥梁。
二战期间,美国政府率先采用一种类似8D的流程——“军事标准1520”,又称之为“不合格品的修正行动及部署系统”。
1987年,福特汽车公司首次用书面记录下8D法,在其一份课程手册中这一方法被命名为“团队导向的问题解决法”(Team Oriented Problem Solving)。
当时,福特的动力系统部门正被一些经年累月、反复出现的生产问题搞得焦头烂额,因此其管理层提请福特集团提供指导课程,帮助解决难题。
8D主要用于汽车及类似加工行业的问题解决方法。
原始是由Ford公司,全球化品质管制及改善的特殊必备方法,之后已成为QS9000/ TS16949、福特公司的特殊要求。
该方法适用于解决各类可能遇到的简单或复杂的问题;8D方法就是要建立一个体系,让整个团队共享信息,努力达成目标。
8D本身不提供成功解决问题的方法或途径,但它是解决问题的一个很有用的工具;亦适用于过程能力指数低于其应有值时有关问题的解决;面对顾客投诉及重大不良时,提供解决问题的方法。
8D法是美国福特公司解决产品质量问题的一种方法,曾在供应商中广泛推行,现已成为国际汽车行业(特别是汽车零部件产家)广泛采用来解决产品质量问题最好的、有效的方法。
D0:征兆紧急反应措施目的:主要是为了看此类问题是否需要用8D来解决,如果问题太小,或是不适合用8D来解决的问题,例如价格,经费等等,这一步是针对问题发生时候的紧急反应。
关键要点:判断问题的类型、大小、范畴等等。
与D3不同,D0是针对问题发生的反应,而D3是针对产品或服务问题本身的暂时应对措施。
D1:小组成立目的:成立一个小组,小组成员具备工艺/产品的知识,有配给的时间并授予了权限,同时应具有所要求的能解决问题和实施纠正措施的技术素质。
业务流程重组(BPR)

13
BPR的定义
业务流程重组(BPR)
BPR:Business Process Reengineering
1
案例:福特北美汽车公司付款流程重组
福特北美公司预付款部门雇佣员工500余人,冗员严重, 效率低下。他们最初制定的改革方案是:运用信息技术,减少
信息传递,以达到裁员20%的目标。
但是参观了Mazda(马自达)之后,他们震惊了,Mazda 是家小公司,其应付款部门仅有5人,就算按公司规模进行数 据调整之后,福特公司也多雇佣了5倍的员工,于是他们推翻 了第一种方案,决定彻底重建其流程。
17
BPR的主要思想与原则 顾客与企业的联系不是单点方式 (Single Point of Contact),如一个顾客要想 查询发票信息,必须与企业的财务部门联系,与 之打交道的销售部门只知道有关销售方面的信息。 此外,由于部门边界限制,很多工作只是为了满 足企业内部管理结构的需要而完成,从而存在很 多无效的工作。
戏剧性改善表明业务流程重组追求的不是一 般意义上的业绩提升或略有改善、稍有好转等, 而是要使企业业绩有显著的增长、极大的飞跃和 产生戏剧性变化。这也是业务流程重组工作的特 点和取得成功的标志。
14
BPR的定义 业务流程重组关注的要点是企业的业务处理 流程,一切“重组”工作全部是围绕业务流程展开 的。“业务流程”是指一组共同为顾客创造价值而 又相互关联的活动。哈佛商学院的Michael Porter 教授将企业的业务流程描绘为一个价值链 (Value Chain),竞争不是发生在企业与企业之间, 而是发生在企业各自的价值链之间。只有对价值链 的各个环节(业务流程)进行有效管理的企业,才 有可能真正获得市场上的竞争优势。
福特公司的流程再造

一、企业流程再造的概念企业流程再造(Business Process Reengineering,简称BPR)这一概念最初于1990年由美国麻省理工学院的哈默(Michael Hammer)在“Reengineering Work:Don't Automate,But Obliterate”一文中提出。
接着哈默(Michael Hammer)和钱辟(James Champy)于1993年合著的“Reengineering the Corporation——A Manifesto for Business Revolution”一书,全面提出BPR概念。
在书中,他们将“企业流程再造”定义为“从根本上重新思考、彻底改造业务流程,以便在衡量企业绩效的关键指标上取得显著性的改善”,其中衡量绩效的指标包括产品和服务客户满意度、成本、工作效率等。
这个定义包括了四个关键词:根本的(Fundamental),彻底的(Radical),显著性(Dramatic)和流程(Process)。
这就是企业再造的四个核心内容:第一,所谓根本的,是指企业再造需要从根本上重新思考,对长期以来企业在经营中所遵循的分工思想,等级制度和官僚体制等进行重新审视,这需要打破原有的思维定势,进行创造性思维。
第二,所谓彻底的,是指企业再造工程不是对企业进行肤浅的改变或调整修补,而是要追根溯源,进行脱胎换骨式的彻底改造,抛弃现有的业务流程和组织结构以及陈规陋习,另起炉灶,对企业进行重新构造,不是对企业进行改良,增强或调整。
第三,所谓显著性,是指企业再造的目标不是要取得小的改善,而是要取得业绩上的突飞猛进,如大幅度降低成本,缩短研发生产周期,提高质量等。
不是缓和的,渐进式的改善,而是大幅度的跳跃,渐进式的变革只需要精细微调旧系统,而业绩上的巨大飞跃则需要以新的系统取代旧的系统。
第四,所谓企业流程(Business Process),就是企业将多种资源输入转换成对客户有价值的输出的一连串活动集合。
福特APQP学习教程
J1
FS
CFMEA
50 41
36 33.5
25.5
14.5
8
4.5 3.5
0
-6
25
3 – 设计FMEA (续)
可交付性:
开发DFMEA, PFMEA, 和机器FMEA计划和时间安排
DFMEA的RPN在<PA> 100%完成 每月评审DFMEAs状态和质量 控制计划中的SC和CC在FMEAs中被识别出来
PR
CP
CC LR LS
J1
FS
19
14.5
8
4.5 3.5
0
-6
28
5 – 设计验证计划
定义:
列出工程评估和试验的文件,以确定设计适合预 期的环境
SI 50 41
SC PH PA ST 36 33.5 30 25.5
PR
CP
CC LR LS
J1
FS
19
14.5
8
4.5 3.5
0
-6
29
5 – 设计验证计划 (续)
DFMEA中推荐的措施在<PR> 得到100%实施
SI
SC PH PA ST
PR
CP
CC LR LS
J1
FS
CFMEA
50 41
36 33.5
25.5
14.5
8
4.5 3.5
0
-6
26
4 – 设计评审
定义:
定期安排会议验证设计,并与管理层监控 计划进度
SI 50 41
SC PH PA ST 36 33.5 30 25.5
可交付性:
制定样件制造控制计划开发的工作计划
FORD福特汽车研发流程的介绍
27MBJ1
供应商选 点开始
M1 25MBJ1
PA
FDJ
20.5MBJ1 17MBJ1
VP 13MBJ1
高影响供 应商选择
跨功能小组形成
解决问题
交运制造
PEC 8MBJ1
LR/ FEC
5.5MBJ1
TT 5MBJ1
PP 2.5MBJ1
MP1 0MBJ1
启动会议 开始
第一次现场 评审
第二次现场 评审
决定: 是否进 行试生 产?
团队
利用福特跨功能团队与供应商一起在现场工作 (4次拜访)
标准化
采用唯一的,全球通用到,有纪律的流程 尽量减少返工和重复。
管理/汇报
使用共同的,明确的交付报告和结构化的 管理评审模式
GPDS 供应商管理过程-总览
Unit
Unit
PTC
PA
34MBJ1
27.5MBJ1
PTCC
PTC/ M1DJ
33.5MBJ1 (655/654)
Required Inputs
START
INPUTS Released design [#1,2,3 & 4]
Trained supplier production operators
Sub-supplier(s) material status
from Tier-x R@R
Quantity of parts required as defined by
[#5,6 & 7]
Production Tools, Facilities
& Gauging [#8,16 & 17]
Planned production cycle times required to support Daily Production
福特经典8D报告模板
舍得,放下,参与,尊重(电话,时间)
充分利用 休息时间:
2
培训目标 培训目标:
培养问题意识和开放的心态; 了解8D的精神和原则; 掌握8D的实施流程; 掌握实施8D各环节的要领; 掌握PDCA、脑力风暴、因果图等必要的技法; 能够编写专业的8D报告;
团队导向问题解决对策
TOPS (Team Oriented Problem Solving)
导入:构建学习心态
NGSCC
充分的投入 开放的心态
投入多少,收获多少!
没有人靠节约成功!
经验往往是进一步成功的障碍!
大家都是井底蛙,只是井口位置和大小有所不同!
改变的决心
郑重的承诺
不是想,不是要,是一定要改变
人 material Man 机 六大 生产要素 法 测量 环
NGSCC
料
machine
method
environment
measurement
七大任务法
1. Q — 品质 2. C — 成本 3. D — 交期
组合 应用
不 合 理 不 均 衡 浪 费
人
机
料
法
环
测量
4. S — 服务
5. S — 安全 6. P — 效率 7. M — 士气
1886年管理学诞生,泰罗在此年加入美国的机械工程师学会 (ASME); 1908年哈佛大学创立了著名的哈佛商学院(HBS,Harvard Business chool),并于同年开设了MBA课程;
毛泽东曾经说过:
‚我们不但要提出任务,而且要解决完成任务的方法问题。我们的任务是过河,但是没有 桥或没有船就不能过。不解决桥或船的问题,过河就是一句空话。不解决方法问题,任务 也只是瞎说一顿。‛
Ford Service简介
Ford Service服务体系及特色服务简介“Ford Service”是福特全球统一的高标准服务体系,其核心支柱包括:全球统一的汽车服务流程改善体系──Quality Care、遍布全国的经销商网络、专业化的技术队伍建设、个性化的客户关系管理,以及优质高效的零件供应体系。
这五大支柱充分保证了标准化流程和专业、人性化的服务所带来的高效率与高质量。
福特Quality Care服务流程改善体系福特Quality Care是福特全球高标准服务体系“Ford Service”的核心之一,形成于1987年,其诞生的初衷是与客户建立良好关系,提高客户满意度。
2002年起,Quality Care在中国市场推行。
经销商通常要花费7-16个月的时间对客户服务的软硬件进行彻底改善,以达到Quality Care的严格标准。
到2010年9月,长安福特的167家经销商通过了此Quality Care认证,认证率超过66%。
在每家授有“Quality Care”标志的福特经销商,客户都将享受到“精准、友善、专业”的服务。
Quality Care作为福特汽车品牌所特有的、经销商服务流程改善项目,包括三个组成部分:12个关键流程,5S和经销商客户关系中心DCRC。
已经在全球超过34个国家得到全面推广。
12个关键流程:12个关键步骤的先进服务流程,涵盖了长安福特服务过程中的每个关键细节,用标准化的操作提高服务质量和效率。
12个关键流程包括:主动与客户接触、客户预约制度、个性化接待流程、菜单式报价/价格承诺、客户关怀、明确车间工作流程、预先检料、维修订单处理和工作质量保证、完工/出票、提供客户信息/交车、服务后客户跟踪、问题解决和预防。
每一个步骤,都有详实的工作内容描述作为依据,切实可行地保证了全国长安福特车主都能享受到全球统一的服务质量。
5S现场管理:包括整理、整顿、清扫、清洁和素养,充分保证了经销商现场运作的准确高效和整洁有序。
- 1、下载文档前请自行甄别文档内容的完整性,平台不提供额外的编辑、内容补充、找答案等附加服务。
- 2、"仅部分预览"的文档,不可在线预览部分如存在完整性等问题,可反馈申请退款(可完整预览的文档不适用该条件!)。
- 3、如文档侵犯您的权益,请联系客服反馈,我们会尽快为您处理(人工客服工作时间:9:00-18:30)。
2020/11/1
FORD流程介绍
GPDS 全球产品开发体系
GPDS( Global Product Development System)
—是FORD公司全球产品开发体系,替代原FPDS福特产品开发体系
早期参与
在产品开发过程早期,与供应商更融洽地合作
团队
利用福特跨功能团队与供应商一起在现场工作 (4次拜访)
START
INPUTS Released design [#1,2,3 & 4]
Trained supplier production operators
Sub-supplier(s) material status
from Tier-x R@R
Quantity of parts required as defined by
STATUS:
Phase 0
1
Completed
Capacity Analysis Worksheet
Submit to Customer
Status Tracking Database
4
Phase 0 Run-at-Rate
1 - 设计记录 2 - 工程变更文件 3 – 顾客工程批准 4 - 设计FMEA 5 - 过程流程图 6 - 过程FMEA 7 - 控制计划 8 - 测量系统分析 16 – 检查辅具 17 – 顾客特殊要求 产能分析报告
图 6. Process FMEA过程FMEA 7. Control Plans控制计划 8. Measurement System Analysis
Studies测量系统分析研究 9. Dimensional Results尺寸报告
10. Records of Material / Performance
- Performance Tests [#12]
- Appearance criteria [#13]
- Sample parts [#14]
- Master samples [#15]
- Customer Specific Requirements[#17]
- as defined by PPAP
告 11 - 初始过程能力研究 12 - 有资格的实验室文
件 13 – 外观批准报告 14 – 生产样件 15 – 标准样件 18 – 零件提交保证书
phase1 PSW
All personnel for all shifts,
trained
Are the CVR input requirements in place
15. Master Sample标准样件
16. Checking Aids检查辅具
17. Customer-Specific Requirements顾
客特殊要求
18. Production Part Approval Process
Submission Warrant (PSW)零件提交
保证书
FORD流程介绍
[#5,6 & 7]
Production Tools, Facilities
& Gauging [#8,16 & 17]
Planned production cycle times required to support Daily Production
Volume
Are the Run@Rate input requirements in place for the production
produced?
Phase 3
Warrant
No
Yes
[#18]
Phase 2
& Capacity
Warrant
Analysis
Report
Phase 2 Warrant
[#18]
Submit to Customer
Status Tracking Database
Scheduled down time defined (TPM, change over, Breaks etc.)
Important note: For suppliers with only one production stream completion of Phase 1 & 2 occur at the same time
4
Have the
Yes
STATUS:
PPAP elements been satisfied?
第三次现场 评审
第四次现场 评审
更新供应商 APQP/PPAP 准备状态评估报告 (A表)
FORD流程介绍
项目节点(里程碑)
• PTC-Program Target Compatibility 项目目标整合
• PA-Program Approval 项目批准
• FDJ-Final Data Judgement 工程数据发布 • VP-Verification Prototype (OTS)样件验证 • PEC-Preliminary Engineering Completion 工程数据冻结
改善工作流程
1. 简化 2. 稳定化 3. 标准化 4. 节奏化 5. 持续性
FORD流程介绍
供应商阶段性PPAP过程图
Required Inputs Proceed to next page
Proceed to next page Proceed to next page
Required Inputs
FORD流程介绍
项目节点(里程碑)
• LR-Launch Readiness 生产准备就绪(可生产) • TT-Tooling Trial 工装样件 (PSW1) • PP-Pilot Production 试生产(可售)(PSW2) • MP1-Mass Production 1 量产 (PSW3) • Job #1— 整车投产
for all production streams?
EVENT:
Yes
Conduct
Capacity
Verification Run
STATUS:
Phase 3
END
Have Run-at-Rates (Phase 0)
Completed
been conducted and Quality
2
Verifications (Phase 1) been
FORD流程介绍
FORD项目跟踪(装车)节点
Unit
Unit
PTC
PA
34MBJ1
27.5MBJ1
PTCC
PTC/ M1DJ
33.5MBJ1 (655/654)
27MBJ1
项目批准 工程数 据发布
M1
PA
FDJ
25MBJ1
20.5MBJ1 17MBJ1
手工样 件OTS
VP 13MBJ1
PEC 8MBJ1
FORD项目开发节点
FORD流程介绍
PPAP 的18项
1. Design Records设计记录 2. Engineering Change Documents
工程变更文件 3. Engineering Approval 工程批准 4. Design FMEA设计FMEA 5. Process Flow Diagrams过程流程
Continue Production Part Approval Process (PPAP) using parts from Phase 0
- Dimensional measurements [#9]
- Material Tests [#10]
1
- Statistical process package [#11]
标准化
采用唯一的,全球通用到,有纪律的流程 尽量减少返工和重复。
管理/汇报
使用共同的,明确的交付报告和结构化的 管理评审模式
FORD流程介绍
GPDS 供应商管理过程-总览
Unit
Unit
PTC
PA
34MBJ1
27.5MBJ1
PTCC
PTC/ M1DJ
33.5MBJ1 (655/654)
27MBJ1
Yes
satisfied for ALL production
streams?
STATUS: Phase 2 Completed
3
3
Quantity required is
customer DPV
for one full day
Was the No control plan followed
& acceptable parts
Action
Status Tracking Database
Important note: Phase 2 and Phase 3 can happen concurrently if all Inputs and Outputs are satisfied
customer (default 300 consecutive
parts)
Job 1 Location (final site & line)
Production process including
control plan, flow diagram instructions &
Process parameters
产能验证
Phase 2 Production Verification
生产验证
加强沟通
1. 一至性的沟通 2. 关注少数重要的优先点。 3. 言简意赅 4. 帮助使用者区分优先级 5. 去除障碍