基于ANSYS的桥式起重机主梁优化设计(2021版)
用ANSYS 软件进行变截面翼板主梁优化设计

用ANSYS 软件进行变截面翼板主梁优化设计3.4.1 参数化建模在双梁箱形龙门起重机结构设计时应选择最佳结构参数,使产品达到最佳经济和技术性能指标,降低自重,提高产品的性能价格比,使梁的强度和刚度都达到许用值。
由第4 章ANSYS 分析梁的截面尺寸过程可知在梁全长范围内有时刚度有富余,有时强度有富余,因此有必要进一步优化。
3.4.2. 设定模型参数上下翼板厚度:A=30主腹板厚度:C =24主梁宽度:B = 3500主梁高度:H = 8500主梁长度:L = 120000翼板厚度变化幅值:M = 2主梁长度变化次数:N =203.4.3. 编制翼板厚度离散化的语句因为工艺制造的原因,主梁翼板变化是离散的,因此生成的关键点这一步骤必须实现参数化。
ANSYS 的参数化设计语言(APDL )中有分支和循环的功能,利用这一功能,将关键点的标号与其坐标关联起来,实现参数化。
这一过程如下:I =20*DO,l,1,4* N + l,1* IF,MOD ( 1,2 ),NE,0,THEN //分支语言设定关键点的Z坐标。
Z =0ELSEIF,MOD ( l,4 ),EQ ,0Z =MELSE,Z =-MEND IFK,I ( I-l ) *L ( 4*10 ),O,ZEND DOFLST,3,4*N + 1,3DO,I,l,4*N + 1,lFITEM,3,IEND DOBSPLIN, PSlX在语句K,I,( I-1 ) * L / ( 4*N ),O,Z 中,K 表示关键点,I 表示关键点的标号,(I-1 ) * L / ( 4*N )表示关键点的X 坐标,Y 坐标为零,Z 坐标为Z 。
用上面的这一程序就能自动画出一系列的关键点,如果需要改变翼板的形状的时候,只需要改变参数N 和M 就行了。
这一程序虽然小,却是非常关键的一步,它直接关系到优化设计能否进行。
因为模型的所有尺寸都己经在建模开始前设计了ANSYS 的参数,因此在建模中涉及模型的尺寸必须用这些参数而不能数字,在设定的梁单元常数时候就必须用参数表示,建模的其它方面与前面分析主梁时完全一致。
基于有限元分析的单梁桥式起重机优化设计

基于有限元分析的单梁桥式起重机优化设计摘要:利用ANSYS9.0分析单梁桥式起重机钢结构的力学特性,并结合分析结果咯实际经验提出了相应的结构优化方案,其正确性和合理性得到验证,并为同类产品优化设计提供有益参考。
关键字:桥式起重机;钢结构;优化设计;FEM目前广泛应用于机械制作、冶金、钢铁、码头的桥式起重机占具我国起重机的40%左右。
原有起重机设计方法多为传统的设计方法,设计效率低下,设计起重机安全系数大、消耗原料多、结构不尽合理。
亟待对其钢结构进行优化设计。
通常的优化设计是利用数学规划的方法,将机械工程的设计问题转化为由目标函授与约束条件描述额度最优化问题。
该方法对于解决较典型的优化问题可以得到较好的优化结果,但对于工程实际中经常出现的多目标、多约束条件优化问题则存在着数学模型难以建立及计算复杂,难于推广应用等问题。
鉴于此,本文利用有限元分析软件对可能的结构设计方案快速进行虚拟试验,并通过分析FEM虚拟试验的结果,作相应的结构优化。
以LX型单梁桥式起重机主梁钢结构为例,利用ANSYS模拟其在最恶劣工况下的应力分布和变形情况,提出并检验了优化方案。
1.LX型5t电动悬挂单梁桥式起重机钢结构特点LX型5t电动悬挂单梁桥式起重机由主梁和两条端梁、电动葫芦、大车运行机构、电气设备等主要部件组成。
车轮组倒挂在车间的H 型轨下运行。
主梁中部由工字梁I32a和箱型梁焊接而成;两端悬臂部分则由工字钢I32a与槽钢[28a焊接而成;端梁由两根槽钢[18与钢板焊接而成,主梁通过箱型梁两侧的吊耳实现与端梁的连接,如图1 所示。
2.有限元建模和分析方案2.1单元的选择与网格划分LX型5t电动悬挂单梁桥式起重机钢结构中的工字钢、槽钢和箱型梁的主尺寸均为其厚度的10倍以上,故选定壳单元(shall 63)对该桥式起重机进行有限元分析[1]。
此外,选用壳单元便于模型的优化修改。
2.2确定最恶劣工况相关理论表明:小车位于跨中并制动,大车行径轨道接头并制动;小车位于悬臂梁极限位置并制动,大车行径轨道接头并发生偏斜为最恶劣的2中工况[2]。
基于ANSYS吊车支撑梁的分析设计及优化研究

基于ANSYS吊车支撑梁的分析设计及优化研究ANSYS是基于有限元理论的大型通用有限元分析软件。
它广泛应用于工程设计、结构仿真、材料分析、热力学分析等领域。
在工程设计中,吊车支撑梁作为一个承受重载的重要结构零件,需要经过分析设计及优化研究,确保其高效、安全、可靠。
通过ANSYS分析,在进行吊车支撑梁设计时,需要首先建立模型。
模拟吊车支撑梁几何尺寸、材料性质以及负荷情况等,生成三维有限元模型。
同时,需要确定边界条件,包括支撑条件、连接方式、边缘约束等。
然后通过加工工艺处理模型进行悬挂,获得吊车支撑梁的负荷合理分布。
在分析设计和优化研究方面,ANSYS提供了多种解决方案。
其中,结构力学分析是最常用的分析方法。
它能够模拟材料弹性、塑性、损伤和破坏等现象,并计算出各种应力、位移、变形等物理量。
通过仿真分析,可以评估吊车支撑梁的强度、刚度、稳定性等性能指标,为后续优化研究提供基础。
优化研究的目标是通过改变设计参数,提高吊车支撑梁的性能,降低成本,减少材料浪费等。
ANSYS提供了一系列的优化工具,包括灵敏度分析、优化算法、参数化设计等。
在吊车支撑梁的设计优化中,可以利用其中的优化算法,通过最大化性能、最小化成本等目标函数,自动寻找最优解。
同时,可以通过参数化设计,设置设计变量进行批量优化研究,以寻找全局最优解。
在吊车支撑梁的分析设计及优化研究中,ANSYS是重要的工具。
它不仅提供了准确的仿真分析,而且提供了强大的优化研究功能,为用户节约了时间和成本,帮助设计者更好的实现优化设计。
数据分析是管理和决策过程中的重要工具。
在日常生活和商业领域中,收集和分析数据可以帮助我们获得有关趋势、模式和行为的深入理解。
以下是一些相关数据及其分析。
1. 消费者调查数据消费者调查数据是管理营销战略的关键工具。
其中最重要的指标是消费者满意度。
通过分析这些数据,可以了解顾客对产品或服务的评价,可以帮助商家制定改善产品或服务的策略。
另外,还可以了解产品或服务所占市场份额,这可以为商家的营销战略提供依据。
桥式起重机主梁的有限元分析及优化设计武建华

桥式起重机主梁的有限元分析及优化设计武建华发布时间:2021-10-27T06:54:26.359Z 来源:《建筑学研究前沿》2021年15期作者:武建华[导读] 本文针对16 t×22.5 m的双梁桥式起重机当前的工况和具体的载荷进行分析,合理的确认了对于金属结构重量产生影响的相关因子——设计变量,同时针对这一重机主梁展开了针对MeshFree软件平台进行的一种有限元分析以及优化,最后使其重机力学性能可以获得要求。
河南东起机械有限公司河南省新乡 453400摘要:本文针对16 t×22.5 m的双梁桥式起重机当前的工况和具体的载荷进行分析,合理的确认了对于金属结构重量产生影响的相关因子——设计变量,同时针对这一重机主梁展开了针对MeshFree软件平台进行的一种有限元分析以及优化,最后使其重机力学性能可以获得要求。
关键词:桥式起重机;结构分析;有限元优化引言桥式起重机器本身是工程进行施工中能够提升作业效率和降低工人劳动强度的一种大型的起重设备。
当前应用的一些起重机其自身的金属结构全部都是选择型钢以及板材去完成焊接形成。
按照相关统计,通常桥式起重机器本身重量里的金属结构大概占到了改为汉字数字之下,针对一些跨度比较大的起重机器能够占到百分之85 之上,所以,有效降低本身的重量是减少起重机在制造上消耗成本的一种切实科学的方式。
当前,起重机金属结构在设计上的计算,通常都是使用理论以及类比计算去展开。
其中有非常多的经验估算以及简化算法,这样的一种情况就使得起重机自身的金属结构其自身的力学性能出现富余同时材料上的利用率相对较低等情况出现。
本文先首先基于16 t×22.5 m桥式起重机具原型去展开适当的力学分析,并适当的对其完成优化,最后有效地降低了这一起重机本身的自重。
1.双梁桥式起重机整体布局和核心技术参数当前桥架整体的金属结构件主要包含了:主梁和端梁,以及小车和走台栏杆等。
基于ANSYS的桥式起重机主梁优化设计.doc
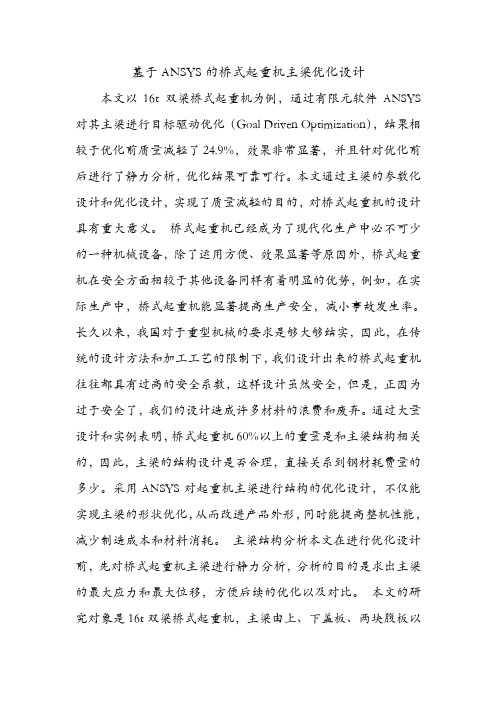
基于ANSYS的桥式起重机主梁优化设计本文以16t双梁桥式起重机为例,通过有限元软件ANSYS 对其主梁进行目标驱动优化(Goal Driven Optimization),结果相较于优化前质量减轻了24.9%,效果非常显著,并且针对优化前后进行了静力分析,优化结果可靠可行。
本文通过主梁的参数化设计和优化设计,实现了质量减轻的目的,对桥式起重机的设计具有重大意义。
桥式起重机已经成为了现代化生产中必不可少的一种机械设备,除了运用方便、效果显著等原因外,桥式起重机在安全方面相较于其他设备同样有着明显的优势,例如,在实际生产中,桥式起重机能显著提高生产安全,减小事故发生率。
长久以来,我国对于重型机械的要求是够大够结实,因此,在传统的设计方法和加工工艺的限制下,我们设计出来的桥式起重机往往都具有过高的安全系数,这样设计虽然安全,但是,正因为过于安全了,我们的设计造成许多材料的浪费和废弃。
通过大量设计和实例表明,桥式起重机60%以上的重量是和主梁结构相关的,因此,主梁的结构设计是否合理,直接关系到钢材耗费量的多少。
采用ANSYS对起重机主梁进行结构的优化设计,不仅能实现主梁的形状优化,从而改进产品外形,同时能提高整机性能,减少制造成本和材料消耗。
主梁结构分析本文在进行优化设计前,先对桥式起重机主梁进行静力分析,分析的目的是求出主梁的最大应力和最大位移,方便后续的优化以及对比。
本文的研究对象是16t双梁桥式起重机,主梁由上、下盖板、两块腹板以及隔板组成,同时,为了分析更为准确,本文对端梁也进行了建模。
1.1 参数化建模优化设计就是讲设定的参数不断优化,最终在众多方案中寻找最佳方案的过程,因此,在建模时,需要实施参数化建模。
本文采取PROE建模,并且设定了8个优化参数。
1.2 有限元的前处理本文选取solid45单元,材料全部采用Q235,材料密度,弹性模量,泊松比。
网格划分以四边形单元为主,同时在个别部位采用三角形单元。
基于Ansys Workbench的桥式起重机主梁优化设计
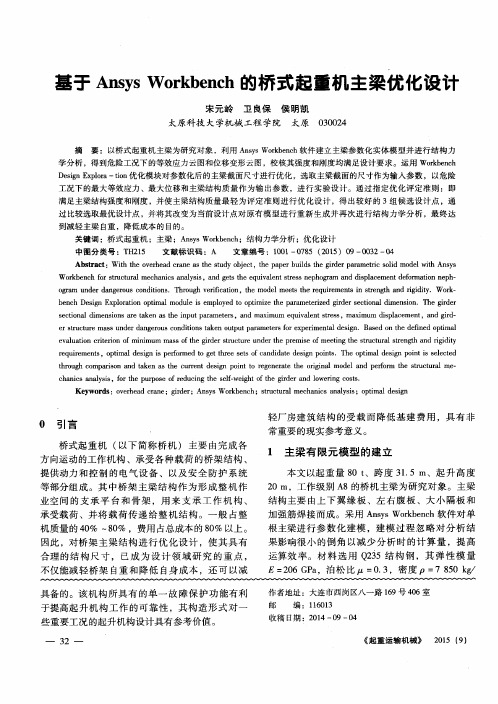
e v a l u a t i o n c r i t e i r o n o f mi n i mu m ma s s o f t h e g i r d e r s t r u c t u r e u n d e r t h e p r e mi s e o f me e t i n g t h e s t uc r t u r a l s t r e n th g a n d i r g i d i t y
学分析 ,得到危险工况下 的等效应力 云图和位移变形 云图 ,校核其强度和刚度均满足设计要求 。运 用 Wo r k b e n c h D e s i g n E x p l o r a—t i o n 优化模块对参 数化 后的主梁截面尺寸进行优化 ,选取主梁截面 的尺寸作为输入参 数 ,以危 险
基于 A n s y s Wo r k b e n c h的桥 式起 重机 主梁优 化设计
基于ANSYS的起重机结构设计优化
基于ANSYS的起重机结构设计优化作者:李聪张亚鹏连冬晓来源:《时代汽车》2021年第12期摘要:在随车起重机的前期設计论证阶段,需进行详细的结构设计及强度校核计算,结构设计包括整机外形的布置、技战术指标的实现及三维模型的建立等方面,在初步确定三维模型结构后,可对整体结构进行有限元分析计算,加入强度及刚度有限元计算后,可有效模拟实际工作状况中部件的受力状况,从而对危险受力点及截面进行预判,根据分析结果对结构进行改变并重新分析直至受力状况优化,从而能对结构优化及实际生产起到有效的指导作用。
正确的有限元分析常常会有效的提高产品质量,以致减小实际生产的成本,对于从设计到生产都能起到极大的促进作用。
关键词:随车起重机三维模型有限元分析结构优化Study on the Performance of Lithium-ion Battery in Electric Vehicle during Cycling TestLi Cong Zhang Yapeng Lian dongXiaoAbstract:In the preliminary design demonstration stage of the truck-mounted crane, detailed structural design and strength check calculations are required. The structural design includes thelayout of the overall machine shape, the realization of technical and tactical indicators, and the establishment of three-dimensional models. The three-dimensional model structure is initially determined After that, finite element analysis and calculation of the overall structure can be carried out. After adding the finite element calculation of strength and stiffness, it can effectively simulate the force status of the components in actual working conditions, so as to predict the dangerous force points and cross-sections. According to the analysis results The structure is changed and re-analyzed until the stress condition is optimized, which can effectively guide the structure optimization and actual production. Correct finite element analysis can often effectively improve product quality, so as to reduce the actual production cost, which can greatly promote the process from design to production.Key words:Truck mounted crane, 3D model, Finite element analysis,Structure optimization1 引言随车起重机是指安装在汽车底盘上,在一定范围内垂直提升和水平搬运重物的起重机械,又称随车吊,属于物料搬运机械,是众多起重运输机械中的一个分支。
基于ANSYS的起重机新型弧弦主梁力学分析论文
基于ANSYS的起重机新型弧弦主梁力学分析论文基于ANSYS的起重机新型弧弦主梁力学分析论文0 引言门式起重机是一种搬运大型物料的起重设备,广泛用于国民经济的各个部门,在现代化生产中占有重要地位。
随着门式起重机的使用范围越来越广,对其安全性能和力学性能也越来越重视。
目前市场上的门式起重机中主梁大多采用平直主梁结构,很少采用其他新型主梁结构形式。
下承式拱桥随处可见,因为这种梁-拱组合体系同时具备受弯和承压的特点而广泛应用。
其结构的主要优点是利用梁的受拉,来抵消拱在竖向载荷下产生的水平推力。
本文依据下承式拱桥的受力特点,参照该桥梁的结构形式,提出了一种新型弧弦主梁结构,并利用ANSYS 对改进后的主梁进行力学分析。
1 新型弧弦主梁的结构模型新型弧弦主梁(以下简称新型主梁)的结构设计,就是在原来传统主梁的基础上,加设一弧形梁,中间通过焊接连杆与平直梁连接。
理论上,这种新型主梁可以利用平直梁的受拉来抵消弧在小车竖向载荷作用下产生的水平力,与传统主梁相比,减小了在竖向载荷的作用下产生的最大应力和应变。
2 有限元建模 2.1 主要参数该门式起重机的跨度为22.5m,额定起升量Pg=30t,小车的轮距3.6m,两相邻大隔板的间距1.5m,隔板厚度0.006m。
腹板的高度H=1.3m,两腹板的间距B=0.5m,腹板的厚度t3=0.006m,上下盖板的厚度t1=t2=0.016m。
2.2 模型建立与网格划分在ANSYS前处理模块中分别设置分析类型、单元种类、实常数以及材料参数。
在本文中主要采用SHELL63单元和BEAM188单元。
SHELL63具有弯曲和薄膜能力,且该平直梁板材的长度不小于其厚度的10倍,应选用SHELL63单元。
弧形梁和起连接用作的连杆采用BEAM188单元,该单元适用于应力强化部分,符合弧形梁和接连杆的实际受载情况。
建模过程中采用自下而上的方法,通过依次创建关键点、线、面等单元达到最终的建模效果。
桥式起重机桥架箱形主梁的优化设计
桥式起重机桥架箱形主梁的优化设计田德雨;舒大文;宋婷婷;张朝喜【摘要】桥式起重机桥架箱形主梁的传统设计一般采用偏于保守的简化计算方法,并且选用比较大的安全系数,所设计出的箱形主梁往往在一定程度上存在结构笨重、部分材料浪费和造价过高等问题,导致整机的性价比降低。
本文应用 ANSYS 软件的优化设计模块,对起重机桥架的箱形主梁结构进行了优化设计分析。
应用ANSYS 软件的 APDL 语言,建立箱形主梁的参数化有限元模型,选取其截面尺寸作为设计变量,对其截面参数进行寻优,在满足其强度和刚度要求的前提下,使其质量减小,性价比提高。
%The traditional design of main girder of bridge cranes generally uses conservative and simplified method to de-sign and uses a large safety factor.The main girder design exists a certain extent problems such like bulky structure,mate-rial waste and high costs,which leads to the reduces of the whole cost-effective.This paper used ANSYS software optimized design modules to conduct a optimal design for the main girder of crane bridge structure.By using the internal command and ANSYS APDL language,established the parameterized finite element model of the main beam.The sectional dimensions of the main beam were selected as the design variables to optimize the main beam cross-section parameters.Under the premise of meeting the strength and stiffness of the main girder,minimized total weight and improved cost performance.【期刊名称】《新技术新工艺》【年(卷),期】2013(000)011【总页数】3页(P60-62)【关键词】桥式起重机;优化设计;参数化;ANSYS【作者】田德雨;舒大文;宋婷婷;张朝喜【作者单位】昆明理工大学机电工程学院,云南昆明 650500;昆明理工大学机电工程学院,云南昆明 650500;三一重工股份有限公司,湖南长沙 410100;昆明理工大学机电工程学院,云南昆明 650500【正文语种】中文【中图分类】TH21随着市场经济的发展,桥式起重机的性价比较以往更显重要。
基于ANSYS平台桥式双梁起重机主梁模态分析
阵, 还需 要 提前 设定 好 弹性 模 量 和 材 料 密度 等 参
数.
1 . 2 加 载 与 求 解
学 分析 等过 程 中 , 首先 也要 进行模 态 分析 , 所 以模
用 ANS Y S Wo r k b e n c h进 行 模 态 分 析 首 先
需 要建 立有 限元 模 型. 可以在 D M 模 块 中建 立 也
收 稿 日期 : 2 0 1 7 — 0 6 — 1 5
电动 双梁起 重机 为 研 究 对 象. 该 起 重 机 的 主要 结
作者简介 : 喻 永巽 ( 1 9 8 4 一 ) , 男, 福 建 莆 田人 , 讲 师, 硕士 , 主要 研 究 方 向 为机 械 工 程 . E - ma i l : k l 6 6 9 9 @1 2 6 . c o m.
第 3 1卷 第 6期
2 O 1 7年 l 1月
兰 州 文理 学 院 学报 ( 自然 科 学版 )
J o u r n a l o f L a n z h o u Un i v e r s i t y o f Ar t s a n d S c i e n c e( Na t u r a l S c i e n c e s )
态 分析 也是 多种 动 力 学 分 析 的前 提 和 基 础. 本 文
通 过商 用 有 限元 软 件 AN S YS Wo r k b e n c h , 对 桥 式 双梁 起重 机 的箱 型 主 梁模 型进 行 了模 态 分 析 ,
主要 包 括对 连接 主梁 的两 条端梁 的 四个端 面施 加
- 1、下载文档前请自行甄别文档内容的完整性,平台不提供额外的编辑、内容补充、找答案等附加服务。
- 2、"仅部分预览"的文档,不可在线预览部分如存在完整性等问题,可反馈申请退款(可完整预览的文档不适用该条件!)。
- 3、如文档侵犯您的权益,请联系客服反馈,我们会尽快为您处理(人工客服工作时间:9:00-18:30)。
基于ANSYS的桥式起重机主梁优化设计(2021版)
Safety management is an important part of enterprise production management. The object is the state management and control of all people, objects and environments in production.
( 安全管理 )
单位:______________________
姓名:______________________
日期:______________________
编号:AQ-SN-0478
基于ANSYS的桥式起重机主梁优化设计
(2021版)
本文以16t双梁桥式起重机为例,通过有限元软件ANSYS对其主梁进行目标驱动优化(GoalDrivenOptimization),结果相较于优化前质量减轻了24.9%,效果非常显著,并且针对优化前后进行了静力分析,优化结果可靠可行。
本文通过主梁的参数化设计和优化设计,实现了质量减轻的目的,对桥式起重机的设计具有重大意义。
桥式起重机已经成为了现代化生产中必不可少的一种机械设备,除了运用方便、效果显著等原因外,桥式起重机在安全方面相较于其他设备同样有着明显的优势,例如,在实际生产中,桥式起重机能显著提高生产安全,减小事故发生率。
长久以来,我国对于重型机械的要求是够大够结实,因此,在传统的设计方法和加工工
艺的限制下,我们设计出来的桥式起重机往往都具有过高的安全系数,这样设计虽然安全,但是,正因为过于安全了,我们的设计造成许多材料的浪费和废弃。
通过大量设计和实例表明,桥式起重机60%以上的重量是和主梁结构相关的,因此,主梁的结构设计是否合理,直接关系到钢材耗费量的多少。
采用ANSYS对起重机主梁进行结构的优化设计,不仅能实现主梁的形状优化,从而改进产品外形,同时能提高整机性能,减少制造成本和材料消耗。
主梁结构分析
本文在进行优化设计前,先对桥式起重机主梁进行静力分析,分析的目的是求出主梁的最大应力和最大位移,方便后续的优化以及对比。
本文的研究对象是16t双梁桥式起重机,主梁由上、下盖板、两块腹板以及隔板组成,同时,为了分析更为准确,本文对端梁也进行了建模。
1.1参数化建模
优化设计就是讲设定的参数不断优化,最终在众多方案中寻找
最佳方案的过程,因此,在建模时,需要实施参数化建模。
本文采取PROE建模,并且设定了8个优化参数。
1.2有限元的前处理
本文选取solid45单元,材料全部采用Q235,材料密度,弹性模量,泊松比。
网格划分以四边形单元为主,同时在个别部位采用三角形单元。
在有限元中,为了确保结果的正确性,需要依据实际情况对模型施加约束。
对于本文来说,分析的是桥式起重机主梁,约束的对象就在端梁的支撑面,即端梁大车轮处。
需要约束的四个支撑面,均拥有6个自由度,即X、Y、Z方向的平移自由度和X、Y、Z方向的旋转自由度,依据实际情况,采取全约束。
当起重机小车满载处于主梁跨中位置时,主梁的应力和变形是最大的,因此,本文的研究工况为小车满载处于主梁跨中处。
1.3求解
当完成主梁的建模以及选取单元、定义材料属性、网格划分、施加约束和施加载荷以后,即可对主梁进行求解,得出主梁的应力
云图和位移云图,如下图所示:
优化设计
优化设计的过程就是分析、评估、修整的循环过程,当用户输入设计参数,ANSYS会对参数进行分析,然后按照用户要求对分析结果进行评估,最后按照算法进行修整。
循环过程会不断重复,一直到满足用户要求打止。
2.1设计变量
优化设计中,对于变量的数目需要严格控制,变量过多,所求问题就会过于复杂,虽然会得到很好的优化结果,但是无形中增大了计算量和计算难度,以至于得不偿失。
因此,在确定变量数目前,需要对研究的结构进行仔细分析,对于设计中几乎没有影响甚至是完全没有影响的参数可以进行忽略,或者以作为给定条件或转化成约束条件的方式来进行处理,尽量减少设计变量的个数,以达到控制变量个数的目的。
本文设计了8个变量,如表2.1所示:表2.1设计变量表
Table2.1Designvariablestable
优化变量的名称
对应Workbench的名称
主梁上盖板宽度
主梁上盖板厚度
端梁高度
主梁腹板高度
主梁下盖板厚度
主梁腹板厚度
端梁内壁间距
端梁盖板长度
本文对16t双梁桥式起重机的主梁进行了参数化建模,然后通过无缝连接导入ANSYSWorkbench进行了静力分析,得出结构符合要求的结论。
在此基础上,对主梁进行了优化,优化得出81组优化数据,经过筛选得出最优解,相比优化前减轻了24.9%,并且进行了优化后的应力、位移的云图对比,得出优化满足要求的结果。
本文结论为桥式起重机主梁的设计和改善提供了有益的指导,具有一定的
参考价值。
XXX图文设计
本文档文字均可以自由修改。