棒材生产线自动控制系统改造设计与实现
棒材打包机自动控制系统的设计及应用
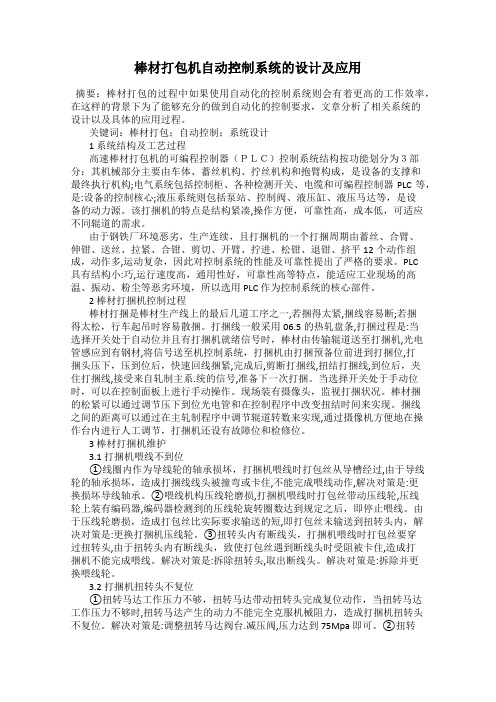
棒材打包机自动控制系统的设计及应用摘要:棒材打包的过程中如果使用自动化的控制系统则会有着更高的工作效率,在这样的背景下为了能够充分的做到自动化的控制要求,文章分析了相关系统的设计以及具体的应用过程。
关键词:棒材打包;自动控制;系统设计1 系统结构及工艺过程高速棒材打包机的可编程控制器(PLC)控制系统结构按功能划分为3部分:其机械部分主要由车体、蓄丝机构、拧丝机构和抱臂构成,是设备的支撑和最终执行机构;电气系统包括控制柜、各种检测开关、电缆和可编程控制器PLC等,是:设备的控制核心;液压系统则包括泵站、控制阀、液压缸、液压马达等,是设备的动力源。
该打捆机的特点是结构紧凑,操作方便,可靠性高,成本低,可适应不同辊道的需求。
由于钢铁厂环境恶劣,生产连续,且打捆机的一个打捆周期由蓄丝、合臂、伸钳、送丝、拉紧、合钳、剪切、开臂、拧进、松钳、退钳、挤平12个动作组成,动作多,运动复杂,因此对控制系统的性能及可靠性提出了严格的要求。
PLC具有结构小:巧,运行速度高,通用性好,可靠性高等特点,能适应工业现场的高温、振动、粉尘等恶劣环境,所以选用PLC作为控制系统的核心部件。
2 棒材打捆机控制过程棒材打捆是棒材生产线上的最后几道工序之一,若捆得太紧,捆线容易断;若捆得太松,行车起吊时容易散捆。
打捆线一般采用06.5的热轧盘条,打捆过程是:当选择开关处于自动位并且有打捆机就绪信号时,棒材由传输辊道送至打捆机,光电管感应到有钢材,将信号送至机控制系统,打捆机由打捆预备位前进到打捆位,打捆头压下,压到位后,快速回线捆紧,完成后,剪断打捆线,扭结打捆线,到位后,夹住打捆线,接受来自轧制主系.统的信号,准备下一次打捆。
当选择开关处于手动位时,可以在控制面板上进行手动操作。
现场装有摄像头,监视打捆状况。
棒材捆的松紧可以通过调节压下到位光电管和在控制程序中改变扭结时间来实现。
捆线之间的距离可以通过在主轧制程序中调节辊道转数来实现,通过摄像机方便地在操作台内进行人工调节,打捆机还设有故障位和检修位。
涟钢棒材倍尺飞剪自动控制系统
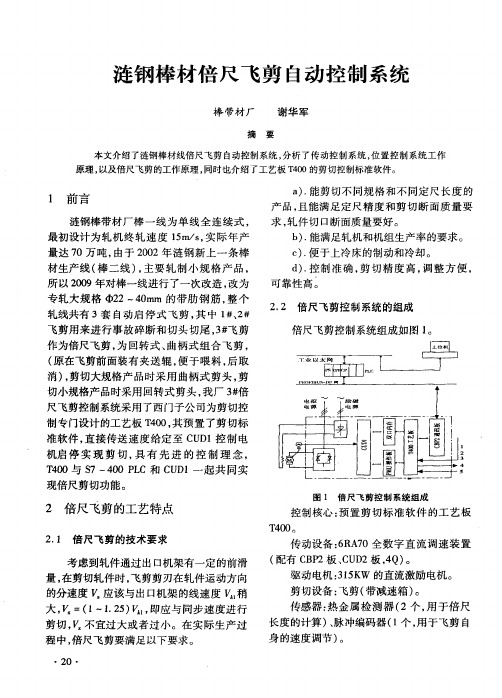
图 2 飞 剪 控 制 系统 框 图
3 倍尺长度的控制及飞剪位置的控制
近年来 , 尺 飞 剪 在 国 内外 已被 广 泛 应 倍 用, 传统 的做 法是 用 P C去控 制倍 尺 飞 剪 的 L
剪切 , 原理 是 : 机在 得 到上 游方 向热 金属 其 剪 检 测器 的 轧件 头 部 信 号 时 , 预 定 剪 切 长 度 按 要 求 , 一定 的计 算 , 延 时 启 动 飞剪 , 始 经 并 起 位置 由轴 向定 位 系统 确 定 , 可 调 节 并
( 在飞剪前 面装 有 夹送 辊 , 于 喂 料 , 原 便 后取 消 ) 剪切大规 格 产 品时 采用 曲柄式 剪 头 , , 剪
倍 尺飞剪 控制 系统 组成 如 图 l 。
切小 规格产 品时采用 回转式 剪 头 , 我厂 3 倍 #
尺飞剪 控制 系统采用门设计 的工艺板 T 0 , 预置 了剪 切 标 40其 准 软件 , 接 传送 速 度 给定 至 C D 直 U 1控 制 电 机启停 实 现剪 切 , 有 先 进 的控 制 理 念, 具 T0 4o与 s 4 0P C和 C D1一起 共 同 实 7— 0 L U
求, 轧件切 口断 面质量 要好 。
b. ) 能满足 轧机 和机 组生 产率 的要求 。 c . 于上冷床 的制动 和冷却 。 )便 d . 制准确 , 切精度高 , 整方便, )控 剪 调 可靠性 高 。
2 2 倍 尺飞 剪控 制系统 的组成 .
飞剪用 来进 行 事故 碎 断和 切 头切尾 ,# 3 飞剪 作 为倍尺 飞剪 , 回转 式 、 为 曲柄 式组 合 飞 剪 ,
、 、
固定 的 2次关 系 , 切完后 由再 生制 动减 速 剪
棒材生产的自动控制(DOC)
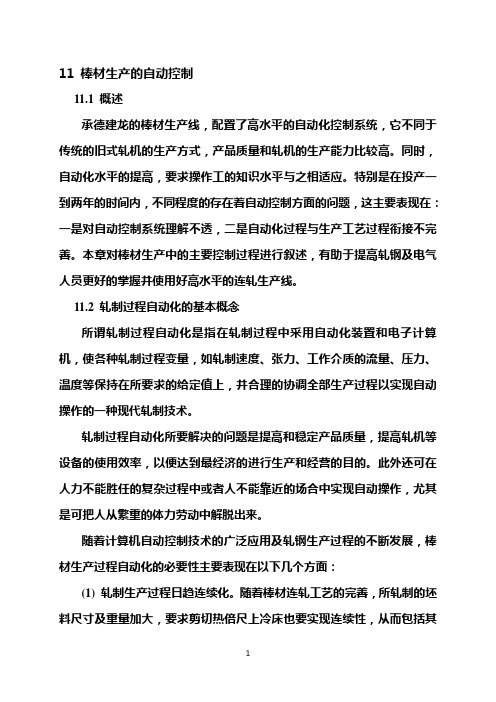
11 棒材生产的自动控制11.1 概述承德建龙的棒材生产线,配置了高水平的自动化控制系统,它不同于传统的旧式轧机的生产方式,产品质量和轧机的生产能力比较高。
同时,自动化水平的提高,要求操作工的知识水平与之相适应。
特别是在投产一到两年的时间内,不同程度的存在着自动控制方面的问题,这主要表现在:一是对自动控制系统理解不透,二是自动化过程与生产工艺过程衔接不完善。
本章对棒材生产中的主要控制过程进行叙述,有助于提高轧钢及电气人员更好的掌握并使用好高水平的连轧生产线。
11.2 轧制过程自动化的基本概念所谓轧制过程自动化是指在轧制过程中采用自动化装置和电子计算机,使各种轧制过程变量,如轧制速度、张力、工作介质的流量、压力、温度等保持在所要求的给定值上,并合理的协调全部生产过程以实现自动操作的一种现代轧制技术。
轧制过程自动化所要解决的问题是提高和稳定产品质量,提高轧机等设备的使用效率,以便达到最经济的进行生产和经营的目的。
此外还可在人力不能胜任的复杂过程中或者人不能靠近的场合中实现自动操作,尤其是可把人从繁重的体力劳动中解脱出来。
随着计算机自动控制技术的广泛应用及轧钢生产过程的不断发展,棒材生产过程自动化的必要性主要表现在以下几个方面:(1) 轧制生产过程日趋连续化。
随着棒材连轧工艺的完善,所轧制的坯料尺寸及重量加大,要求剪切热倍尺上冷床也要实现连续性,从而包括其他一些连续性生产过程在内,使得连轧棒材生产的加热、轧制及后部精整剪切、包装等生产过程全部实现了连续化。
人本身很难在较短的时间内完成各个连续性的生产环节,而计算机自动控制过程解决了这一难点,使连续化生产得以实现,从而大大提高了生产效率,提高了轧钢车间的机时产量,使得生产规模越来越大。
(2) 轧制速度不断提高。
轧制过程的连续化为轧制速度的提高创造了条件,机加工的精度的提高也为连续高速度生产创造了机械条件。
目前传统工艺棒材生产轧制速度达20m/s左右,高速棒材生产速度突破了40m/s,大大超过了老式轧机的轧制速度,这样对轧件在线跟踪控制提出了更高的要求,而计算机快速反应及高灵敏度的跟踪控制恰恰满足了这一点。
棒线厂一棒自动控制系统改造
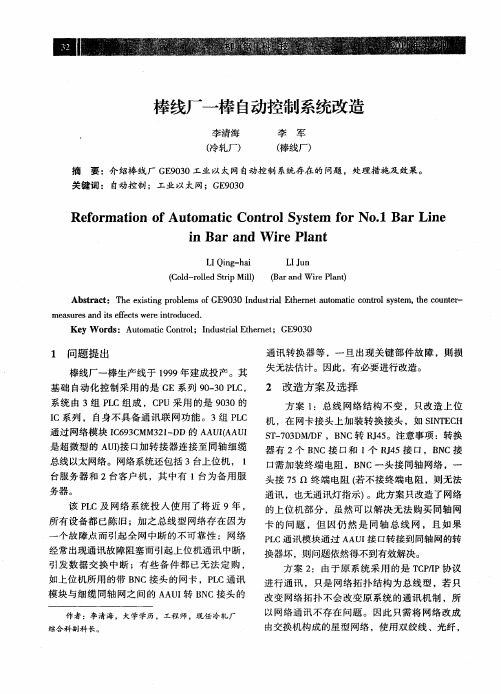
I c系列 ,自身不具备通讯联 网功能。3 P C 组 L
通过 网络模 块 I 6 3 MM3 1 D C9C 2 一 D的 A I AU AU ( I A 是超 微 型 的 A I 口加 转 接 器连 接至 同轴 细缆 U) 接
总线 以太 网络 。 网络 系统还 包括 3台上 位机 , 1 台服 务器 和 2台 客户 机 ,其 中有 1台 为备 用 服
L i - a I n hi Q g
(od rl dSr l C l-o e tpMi) l i 1
L u I n J
(a dWi l t B r n r Pa ) a e n
Ab ta t T ee i i g p o lmso E9 3 n u tilE h m e u o t o t ls se te c u tr sr c : h xs n r b e fG 0 0 I d s r t e t tmai c n r y tm, h o n e - t a a c o
一
的上 位机 部 分 ,虽然 可 以解 决无 法 购 买 同轴 网 卡 的 问 题 ,但 因仍 然 是 同轴 总 线 网 ,且 如 果
P C通讯 模块通 过 A U 接 口转 接 到同轴 网的转 L A I
个 故 障点 而 引起 全 网 中断 的不 可 靠 性 ;网络
经常 出现通讯 故 障阻 塞而 引起上 位 机通 讯 中断 ,
■
更 换 带 R 4 的 P C 通 讯 模 块 (由 J5 L I 6 3 MM3 1 D 改 为 I 6 3 MM3 1J),并 C9C 2一 D C 9C 2 -J 更 换所 有 的上 位 机 、服 务 器及 客 户 机 ,网 卡采
用 R4 J 5型 即可 彻底解 决 上述存 在 问题 。 spo ar 的帮 助里找 到 缺省 的密码 为 :n t i e t ,用 户 ul 可 以更 改此 密码 。 f 进 人 到 通 讯组 态 的组 态 窗 口 ,呈 现 出 缺 3 ) 省 的组 态 例 程 和 旧 的 组 态 。可 以对 存 在 的 组态 连接进 行编 辑或删 除 ,也可 以新 建 自定 义连接 。
棒材生产线二级过程控制系统的设计和应用
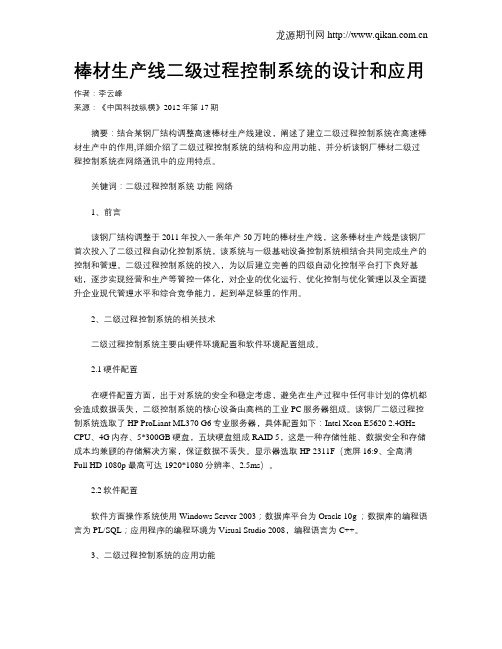
棒材生产线二级过程控制系统的设计和应用作者:李云峰来源:《中国科技纵横》2012年第17期摘要:结合某钢厂结构调整高速棒材生产线建设,阐述了建立二级过程控制系统在高速棒材生产中的作用,详细介绍了二级过程控制系统的结构和应用功能,并分析该钢厂棒材二级过程控制系统在网络通讯中的应用特点。
关键词:二级过程控制系统功能网络1、前言该钢厂结构调整于2011年投入一条年产50万吨的棒材生产线,这条棒材生产线是该钢厂首次投入了二级过程自动化控制系统,该系统与一级基础设备控制系统相结合共同完成生产的控制和管理。
二级过程控制系统的投入,为以后建立完善的四级自动化控制平台打下良好基础,逐步实现经营和生产等管控一体化,对企业的优化运行、优化控制与优化管理以及全面提升企业现代管理水平和综合竞争能力,起到举足轻重的作用。
2、二级过程控制系统的相关技术二级过程控制系统主要由硬件环境配置和软件环境配置组成。
2.1硬件配置在硬件配置方面,出于对系统的安全和稳定考虑,避免在生产过程中任何非计划的停机都会造成数据丢失,二级控制系统的核心设备由高档的工业PC服务器组成。
该钢厂二级过程控制系统选取了HP ProLiant ML370 G6专业服务器,具体配置如下:Intel Xeon E5620 2.4GHz CPU、4G内存、5*300GB硬盘,五块硬盘组成RAID 5,这是一种存储性能、数据安全和存储成本均兼顾的存储解决方案,保证数据不丢失。
显示器选取HP 2311F(宽屏16:9、全高清Full HD 1080p 最高可达1920*1080分辨率、2.5ms)。
2.2软件配置软件方面操作系统使用Windows Server 2003;数据库平台为Oracle 10g ;数据库的编程语言为PL/SQL;应用程序的编程环境为Visual Studio 2008,编程语言为C++。
3、二级过程控制系统的应用功能结合该钢厂棒材生产线的需求和现场的实际情况,棒材生产线的二级过程控制系统具备了生产计划、物料跟踪、设定值下发、轧制参数查询、报表等功能,同时实现了轧机状态监控、HMD和CMD信号监控、飞剪的剪切长度和状态信号等有效数据的记录和处理。
棒材生产线自动控制系统改造设计与实现

在 轧 线 自动 化 系 统 中 , 除 可 编 程 续 控 的 单 调量 时, 下 游 机 架及 本 机 架 的延 伸率 都 制器 ( P L C) 外, 还 配 置 了工业 P C机作 为 工 会 发 生 变化 。 这 种 调 节 方法 主 要 用 于 本 机
作 站, 为 此 选 用 著名 的 美 国M i c r o s o f t ( 微 架 速 度不 适合 于上游 和 下 游机 架 的情 况 。 正
文章编 号: 1 6 7 4 - 0 9 S X ( 2 0 1 3 ) 0 6 ( c ) 一 0 0 6 9 — 0 2
山西 中阳 钢 铁 集 团 有 限 公 司 的 棒 材 生 冷 床 区的 自动 控 制 其 中P LC1 选 用 了2 个
Vl ;Vi +1 /E i +1
产线 是一 条年产4 0 万t 热 轧棒 材 的 全 连 轧 C P U4 1 6 - 2 D P , P LC 2 选 用 了1 个C P U 4 1 6 — 在 实际 中, 也是设定出口 机 架 的 速 度 和 生产 线, 主 要 产 品规 格 为 1 2 ~ 4 0 mm 2 DP , P L C3 选用了1 个C PU3 l 5 - 2 D P 进 行 各 机 架 的延 伸 率 来 计 算 各 机 架 的 基 准 速度 圆 钢 和 螺 纹 钢 。由于 生 产 线 自动 化 程 度 落 数 据 处 理 与 通 讯 。 在各 操 作点 、 操 作 台 设 给 定 还 有 就 是 各机 架 附 加 的速 度 给 定 , 包
1 棒 材 生产 线 的 主要设 备组 成
软) 公司的服务器/ 客 户 机 操 作 系统 , 系 统 常 情 况 下 因为 单 调 量 调 节会 同时 影 响 两 个 相邻机架的延伸率即秒流量相等的平衡,
基于PLC的棒材打捆机控制系统的设计
基于PLC的棒材打捆机控制系统的设计摘要本文介绍了基于PLC的棒材打捆机控制系统的设计。
通过对棒材打捆机的工作原理、动作流程进行分析,确定了打捆机的控制方式、控制器型号及其输入输出模块。
在设计控制程序时,采用了Ladder图的编程方式,实现了棒材打捆机的顺序控制、循环控制以及报警保护等功能。
最后,通过现场实验验证了控制系统的可靠性和稳定性。
关键词:棒材打捆机,PLC,控制系统,Ladder图,顺序控制,循环控制AbstractThis paper describes the design of a PLC-based control system for a rod bundling machine. By analyzing the working principle and action process of the rod bundling machine, the control mode, controller model, and its input and output modules of the bundling machine are determined. In the design of the control program, the programming method of Ladder diagram is adopted to realize the function of sequential control, loop control, and alarm protection of the rod bundling machine. Finally, the reliability and stability of the control system were verified through on-site experiments.Keywords: rod bundling machine, PLC, control system, Ladder diagram, sequential control, loop control1.引言随着工业化生产的不断发展,越来越多的机械设备被应用于工业生产中。
棒材生产线自动控制系统优化与应用
后极 限运 行 ,那 坯 料 是不会 准 确运 送 到 出炉辊 道 上 的,所 以必 须 改 变推 钢机 的前极 限,来 使它 满足 步进 梁 为2 8 0 mm步距 ,同时 也能 将 坯料 准确 的送到 出炉 辊道 上 。 通过 查 阅 资料 ,计 算 出推 钢机 的 前极 限 ,把 表达 式 写入程 序 。 步进 梁 的步 距 写入 程序 的 时候 ,将 它 当做 一个 变 量来 写 , 以后 不 论 改什 么 步距 , 只要将 所 要 步距 输入 这个 变 量 ,推钢 机 就会 计算 出一 个与 之 匹配 的前 极 限 ,使 得 坯料 能准 确 的从 出炉辊 道 出去 。 3 . 2 P 1 主操 台增  ̄ I D A S曲线显 示 的改造 在P 1 台安 装 一 台客户 机 ,放置 到P 1 操 作 工所 正对 的粗 轧位 置 。 通过 网线和 网 卡接 入 到三 级 网络拓 扑 结构 中 。该 客户 机装 有 英文 版 的DAS 系统 ( 实时 数 据 采集 系 统 )软 件 ,C H0 . c H7 八个 开 关 量 用 于检 测 粗轧 前及 粗 轧各 架 次 的咬钢 信 号 ,八个 模 拟量 用于 检测 粗 轧 各架 次 的 电流情 况 。正 常过 钢过 程 中P 1 操 作工 通 过方 便 的观 察粗 轧 机组 各架 次 电流 情 况便 可 准确 的判 断 各架 轧机 的运 行 情况 。该系 统 还具 有 历史 记录 功 能 ,每个 班 次接 班后 可 以将 自己 的作业 时 间进 行 保存 ,一旦 有 故障 发生 了意外 堆钢 ,可 以调 出历 史 曲线分 析 故障 原 因 ,为查 明故障 和设 备维 护 提供 了解 决方 向 。 3 . 3 三号 剪的 剪切 程序 优化 改造 ( 1 )原 三 号剪 程 序 只 能设 五 根倍 尺 ,第 五剪 后 倍尺 长度 自动 按第 五 剪设 定 的剪 切长 度剪 切 ,满 足 不 了生产 要 求 ,使得 最后 一 支 倍尺 切成 定 尺后 必将 出现 小 齐尺 。 ( 2 )每 根钢 坯 的长 度 都不 一 样 ,有 误 差 ,细 小 的误 差造 成 最 后 一支 倍尺 出现 小 齐尺 ,尤其 在轧 制 中2 5 以下螺 纹钢 和 圆钢 时 , 由 于 原料 长度 的较 小 波动 ,造 成 最后 倍尺 波 动较 大 ,最 后一 支倍 尺 长 度不 稳 定 ,出现 小齐 尺 的几 率很 大 。 ( 3 )料 型 的变 化 ,随着 料 型 的变 化 ,尤其 生 产 中2 5 以 下螺 纹 钢和 圆钢 ,有时 也会 使得 最 后一 支倍 尺 出现 小齐尺 。 综 上所 述如 果 将倍 尺 设定 根数 由五剪 增加 到 八剪 ,即对 三 号剪 倍尺 优化 可 解决 以上 问题 。
基于棒材生产线的电气传动及自动化控制系统探究
&('交流变频调速传动系统# 在棒材生产线中用到交流变 频调速传动系统主要是为了节约能源的损耗"因为交流的设备 非常多"所以"中天钢铁就采用了逆变器加上直流母线系统# 在这一过程中采用矢量控制变频器"其中它的过载能力极强且 进行的是低速运行# 在基本速度的范围内是恒转矩系统"与此 同时"这一系统中配置的是 :FL通讯板"然后与 LA:系统的数 据通讯#
&('速度级联# 在棒材自动化控制系统的过程中"速度级 联控制起着非常重要的作用# 它主要的作用是对棒材生产过 程中机架之间所存在的速度问题进行级联方式的调整"从而使 得整个的棒材生产过程可以更加稳定并且效率较高# 这一调 整可以分为两个控制过程"第一个过程就是机架的初速度进行 设定"只要设置了机架的初速度"机架就可以按照所设定的速 度进行生产"当这一生产过程中出现一些拉钢与堆钢的现象" 上下机架之间就会利用微张力和活套自动控制联合起来进行 生产"从而保证棒材的生产过程更加的顺利-(. # 另一种生产过 程的控制就是速度级联的控制方式"它可以在这一生产过程中 实现不同轧区的速度联动"使得棒材生产线更加安全"棒材的 生产质量得以提高"提升其中的生产效益# 这样不仅提高了棒 材质量"而且还可以使施工人员更加安心"同时也可以使人们 运用上更加安全放心的棒材#
&)'活套自动控制# 从整个棒材的连轧线的生产情况来讲" 棒材从粗轧区和中轧区出来之后就会进行到下一个精轧区"但 是精轧区对于钢材的生产条件是非常高的"要求钢材的截面要 更加小"同时"棒材的生产速度就更加快了# 相关的工作人员为 了提高棒材的生产质量"减少能源的消耗以及不必要的钢材的 浪费"就要在精轧区生产过程加上活套自动控制系统# 把活套 设置在相邻的机架之间"这样就会对相邻机架的速度进行检测 与控制"利用活套的角度来实现钢材的轧制# 在活套自动控制 的这一过程中"基本的功能实现包括活套器控制和起套辊控制# 因为在棒材生产过程中"存在着温度高以及尺寸变化非常明显 的问题"相关的工作人员就需要结合实际情况"进一步检测出活 套的起套量"然后在该系统中设置出相应的活套调节器# 其中 活套自动控制系统的主要目的是通过对活套进行速度方面的调 整来检测出活套的高度"从而实现活套的灵活使用# 相关的工 作人员通过相关的调节与检测"使得机架之间可以进行很好的 配合"从而使得棒材生产质量和生产效率都得到提高#
180棒材生产线精整区自动控制系统改造
180棒材生产线精整区自动控制系统改造发布时间:2022-11-13T09:32:36.853Z 来源:《科学与技术》2022年14期7月作者:张浩[导读] 本文主要针对180棒材的生产线的精加工设备存在的问题张浩宝武杰富意特殊钢有限公司广东省韶关市 512000摘要:本文主要针对180棒材的生产线的精加工设备存在的问题,提出一种改进的自动化控制系统,本方案既能降低工人操作失误,又能保障人员和设备的安全,同时还能有效地提高工作效率。
关键词:180棒材生产线;精整区;自动控制引言钢铁工业是我国国民经济的重要支柱产业,而钢筋又是建筑业不可缺少的重要原料,随着建筑业的发展,钢材的需求量也在快速增加,传统的钢筋生产线已不能满足日益增加的需求。
采用全自动化的棒料生产线,能够使生产效率得到极大的提升,从原来的几米/秒的加工速度提升到40多米/秒。
此外,自动化控制也使人员和设备的安全得到很大的改善。
目前,全自动生产已成为棒材生产线的一个重要组成部分,而自动化控制技术则是整条生产线的关键所在。
1 精整设备存在的主要问题 180棒材生产线的精加工设备主要包括:上料、冷床、冷剪、三组检验台、下料以及包装等系统。
精加工设备的电气控制很简单,各工序的电气控制不能互相联系,不能实现自动控制,而且故障率高,严重地影响生产的正常生产。
180棒材机组是根据当前的轧制需求,与国内同类轧机进行比较的,其主要问题如下:第一,上卸钢结构落后,电动机牵引装置失效频发,技术事故多,严重影响生产指标。
第二,冷床对钢的加工能力不强、电动机控制简单、制动器性能差、事故频发、弯头现象多,造成成材率、定尺率等经济技术指标落后于国外同行。
第三,检查台收集结构落后,轧辊道堆钢频繁出现,对生产速度造成很大的影响。
第四,裁剪机容量严重不足、电器及控制系统陈旧、故障率高、维修保养难度大。
第五,采集包装质量不佳、劳动强度大。
2 棒材自动化控制的整体布局 180棒材生产线可划分为加热炉区、轧线区和精加工区3个相对独立的控制区。
- 1、下载文档前请自行甄别文档内容的完整性,平台不提供额外的编辑、内容补充、找答案等附加服务。
- 2、"仅部分预览"的文档,不可在线预览部分如存在完整性等问题,可反馈申请退款(可完整预览的文档不适用该条件!)。
- 3、如文档侵犯您的权益,请联系客服反馈,我们会尽快为您处理(人工客服工作时间:9:00-18:30)。
棒材生产线自动控制系统改造设计与实现
摘要:该文主要介绍了山西中阳钢铁集团有限公司棒材生产线改造后的自动控制系统的软硬件组成和PLC系统及操作站、工程师站的主要控制功能。
关键词:棒材生产线PLC系统自动控制
山西中阳钢铁集团有限公司的棒材生产线是一条年产40万t热轧棒材的全连轧生产线,主要产品规格为φ12~φ40?mm圆钢和螺纹钢。
由于生产线自动化程度落后,为了提高生产线自动化程度,提高产品精度和增加产品产量,由北京钢研新冶电气股份有限公司进行改造,改造后自动化程度明显提高,实现了生产线全连续轧制,产品精度达到了φ12~φ20.0?mm±0.05?mmφ22~φ40.0?mm±0.1?mm,椭圆度不大于尺寸总偏差的80%,精轧机最高速度为15.5?m/s,精轧机保证速度为13.5?m/s (Φ12?mm)。
1 棒材生产线的主要设备组成
(1)加热炉区。
包括热装辊道、装钢辊道、炉内装钢辊道、推钢机、步进梁、炉内出钢辊道、炉外出钢辊道等。
(2)轧机区。
包括卡断剪、粗轧机(1#—7#机架)、1#飞剪、中轧机(8#—13#机架)、2#飞剪、预精轧精轧机(14#—18#机架)、10#~18#机架替代辊道、3#飞剪等。
(3)精整区。
包括裙板辊道、制动裙板、冷床、冷床齐头辊道、冷床输出小车、冷床输出辊道、冷剪、剪后输出辊道、移送齐头辊道、打
包辊道、打包机、成捆器等。
2 轧线自动控制系统
在本系统中通讯网络配置主要是由工业以太网(INDUSTRIAL ETHERNET)和Profibus-DP网,组成两层通讯网络系统。
系统配置如图1所示。
工业以太网(INDUSTRIAL ETHERNET)主要是完成操作站同PLC设备和工厂管理机的数据、信息通讯功能;留有同上级工厂管理机之间的工业以太网通讯接口;操作站、工程师站、PLC之间的工业以太网通讯速率100Mbit/s;工业以太网通讯介质采用工业用光纤;
Profibus-DP网主要是完成PLC设备同传动设备和远程I/O装置之间的数据、信息通讯功能。
Profibus-DP网通讯介质采用工业屏蔽双绞线,其通讯速率可达12Mbit/s。
(如图1)
轧线基础自动化共配置了3套西门子公司的系列pLC(PLC1、PLC2、PLC3),分别完成轧线自动控制、飞剪自动控制和冷床区的自动控制。
其中PLC1选用了2个CPU416-2DP,PLC2选用了1个CPU416-2DP,PLC3选用了1个CPU315-2DP进行数据处理与通讯。
在各操作点、操作台设远程I/O站,采用西门子ET200系列。
PLC 与ET200远程站之间采用PROFIBUS-DP网络通讯。
传动系统采用西门子6R70、6SE70系列装置,PLC与传动设备通过PROFIBUS-DP 网络进行通讯,通讯格式为PPO4,通讯速率为12?Mb/s,各PLC之间采用ETHERNET进行数据交换。
在轧线自动化系统中,除可编程续控制器(PLC)外,还配置了工业PC机作为工作站,为此选用著名的美国Microsoft(微软)公司的服务器/客户机操作系统,系统软件为Windows XP Professional。
HMI/SCADA软件采用SIEMENS公司的WinCC6.2中文版。
PLC系统的编程软件采用STEP 7 Ver 5.4。
3 主轧线自动化系统主要控制功能
3.1 PLC系统主要控制功能
3.1.1 速度设定与速度级联
速度设定级联即通过确定出口轧机基准速度和各机架延伸率来确定各机架的设定速度。
自动调节级联是指定用活套调节器或微张力调节器产生的速度修正率,通过级联的方式对各机架的速度进行修正。
为保证精轧出口速度的稳定,系统的级联方向为逆轧制方向即从精轧机开始向轧线上游级联。
由速度设定级联和自动调节级联综合产生各机架线速度给定,在根据对应机架的工作辊径及减速机速比等折算为速度给定信号,通过网络由PLC送给主传动速度调节系统。
一旦某个机架的速度因操作工在操作台上手动调整,或控制系统根据微张力控制计算程序,需要调节某机架的速度时,为保证机架间的秒流量相等,上游各个机架的电机速度也随之相应地调整。
在棒线材轧机中,第i机架的延伸率等于该机架的出口速度与入口速度之比:
Ei=Vi/Vi-1
在采用逆调的系统中,只要给出末架的出口速度和各个机架的延
伸率,就可求得各个机架的速度:
Vi=Vi+1/E i+1
在实际中,也是设定出口机架的速度和各机架的延伸率来计算各机架的基准速度给定。
还有就是各机架附加的速度给定,包括本机架单调量、本机架联调量、本机架Pi调节量和本机架的动态补偿量。
所有这些量加起来就是本机架的实际设定速度。
本机架单调量。
所谓单调量就是只为本机架自己所附加的调节量,它只调节本机架自身的速度而不会影响其它机架的速度,当调节本机架的单调量时,下游机架及本机架的延伸率都会发生变化。
这种调节方法主要用于本机架速度不适合于上游和下游机架的情况。
正常情况下因为单调量调节会同时影响两个相邻机架的延伸率即秒流量相等的平衡,所以使用时要非常慎重,不要调节好了下游机架的延伸率又打破了本机架的延伸率。
正常使用时单调量调节非常少用。
本机架联调量。
所谓联调量就是不仅调节本机架的速度,还把调节量级联至上游机架,使本机架和上游机架的平衡关系保持不变,也就是说只调节下游机架的延伸率。
因为这种调节方式只调节一个机架的延伸率即本机架和下游机架的平衡关系,所以控制起来非常方便,正常使用中常用
联调量调节方式。
本机架Pi调节量。
本机架Pi调节量是由本机架和下游机架间的平衡关系不匹配而自动调节所产生的调节量,一般情况下这种调节量是由Pi调节器输出的,所以叫Pi调节量。
Pi调节量一般是由微张或活套调节所引起的。
Pi调节量和联调量相同,都要把调节量级联至上游机架。
动态补偿量。
所谓动态补偿量是指补偿咬钢速降所设置的调节量,主要是用于防止机架间的堆钢。
动态补偿量和单调量相同,只调节本机架。
综合以上的各种调节量,本机架的实际速度给定为:
Vi=(Vji+1/Ei+1)*(1+Vpii+Vji)+(Vji+1/Ei+1)*(Vdi+Vbi)(1)
Vji=(Vji+1/Ei+1)*(1+Vpii+Vji)(2)
其中:
Vi表示本机架速度设定
Vji+1表示下游机架级联速度
Ei+1表示下游机架延伸率
Vpii表示本机架Pi调节量
Vdi表示本机架单调量
Vbi表示本机架动态补偿量
Vji表示至上游机架级联速度
上述(1)式和(2)式是整个速度设定的经典公式,不管采取什么控制方法,最终的速度给定都是通过它们给出去的。
只有使用上述公式,才能保证向上游速度调节的一致性,即不会影响上游各个机架间的平衡关系。
计算出本机架的速度给定后,并不是直接把速度送出去,而是经过斜坡函数发生器走斜率送出,这样就避免了速度突变所引起的电流冲击。
斜坡函数发生器的斜率是变化的:正常起停车用一个比较缓的斜率,当发生危险或事故时启用快速斜率停车,使机架快速停下来,减小危险系数。
速度设定与速度级联控制是棒线材主轧线自动化系统功能中很特殊的一个功能组,相对来说它比较固定,但又非常重要,一旦这个功能出现编程上的错误,那么整个系统的稳定就不可能实现。
3.1.2 轧件跟踪
轧件跟踪是棒材连轧计算机控制系统的主要功能之一。
在轧制生
产过程中,同一时刻往往有多根轧件在生产线上的不同工序中加工处理。
为了对整个轧制生产过程进行自动控制,必须区分每根轧件所在的位置,针对它们在生产线上的不同位置,及时地进行相应的自动控制。
PLC是根据生产线上各个区段的活套扫描器、高温计及热金属检测器的状态变化来跟踪轧件的位置。
本系统配置的用于轧线跟踪的在线检测仪表为:
活套扫描器5台,选用潞城传感厂产品。
分别安装于FA11、FA12、FA14、FA16、FA17活套附近。
高温计4台,选用潞城传感厂产品。
分别安装于加热炉出口、16#机架前、18#机架出口位置、冷床入口。
热金属检测器8台,选用潞城传感厂产品。
分别安装于加热炉出口、1#飞剪前、1#飞剪后、2#飞剪前、2#飞剪后、15#机架出口、18#机架出口、3飞剪后。
3.2 操作站、工程师站主要控制功能
轧线速度和参数设定;活套高度设定;轧制规程管理;轧线监控动态画面状态显示;显示系统起停条件;故障报警、显示、存储;飞剪切头、切尾长度设定;模拟轧钢,检查各系统准备情况;多种采集量的柱状图或数字显示;故障报警、显示、记录;同工厂二级自动化系统通讯。
轧线监控动态画面状态显示如图2所示
4 结语
控制系统改造后,棒材生产线运行稳定,产品的数量和质量都得
到了显著的提高,效果良好,获得了客户的一致好评。
参考文献
[1] 房新亮.小型棒材生产线控制系统改造[J].设备管理与维修,2010(7).
[2] 王桂芳.涟钢棒材生产线自动控制系统[J].冶金自动化,2002(2).
[3] 王丰.棒材生产线自动控制系统改造设计[J].机床与液压,2010(14).
[3] 赵恒.棒材轧线速度控制过程[J].冶金动力,2007(1):119.。