长输管道下向焊接通用工艺2
管道通用工艺规程
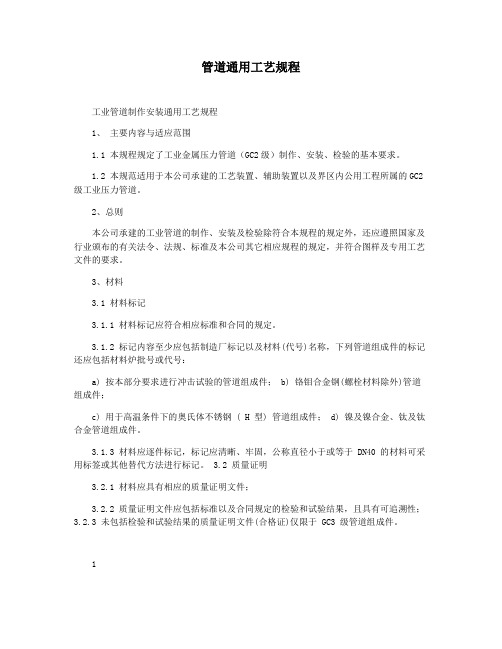
管道通用工艺规程工业管道制作安装通用工艺规程1、主要内容与适应范围1.1 本规程规定了工业金属压力管道(GC2级)制作、安装、检验的基本要求。
1.2 本规范适用于本公司承建的工艺装置、辅助装置以及界区内公用工程所属的GC2级工业压力管道。
2、总则本公司承建的工业管道的制作、安装及检验除符合本规程的规定外,还应遵照国家及行业颁布的有关法令、法规、标准及本公司其它相应规程的规定,并符合图样及专用工艺文件的要求。
3、材料3.1 材料标记3.1.1 材料标记应符合相应标准和合同的规定。
3.1.2 标记内容至少应包括制造厂标记以及材料(代号)名称,下列管道组成件的标记还应包括材料炉批号或代号:a) 按本部分要求进行冲击试验的管道组成件; b) 铬钼合金钢(螺栓材料除外)管道组成件;c) 用于高温条件下的奥氏体不锈钢 ( H 型) 管道组成件; d) 镍及镍合金、钛及钛合金管道组成件。
3.1.3 材料应逐件标记,标记应清晰、牢固,公称直径小于或等于 DN40 的材料可采用标签或其他替代方法进行标记。
3.2 质量证明3.2.1 材料应具有相应的质量证明文件;3.2.2 质量证明文件应包括标准以及合同规定的检验和试验结果,且具有可追溯性;3.2.3 未包括检验和试验结果的质量证明文件(合格证)仅限于 GC3 级管道组成件。
13.3 外观检查管道组成件及管道支承件的材料牌号、规格、外观质量应按相应标准进行目视检查和几何尺寸抽查,不合格者不得使用。
3.4 材质检查对于合金钢、含镍低温钢、含钼奥氏体不锈钢以及镍基合金、钛和钛合金材料的管道组成件,应采用光谱分析或其它方法进行材质抽样检查,抽样数量取每批(同炉批号、同规格,下同)的5%且不少于一个管道组成件。
3.5 阀门试验阀门应按标准要求进行壳体压力试验和密封试验: a) 用于GC2 级管道的阀门应每批抽查10%,且不得少于一个。
b) 用于GC3 级管道的阀门应每批抽查5%,且不少于一个。
工艺管道安装通用规范及注意事项(PPT37张)
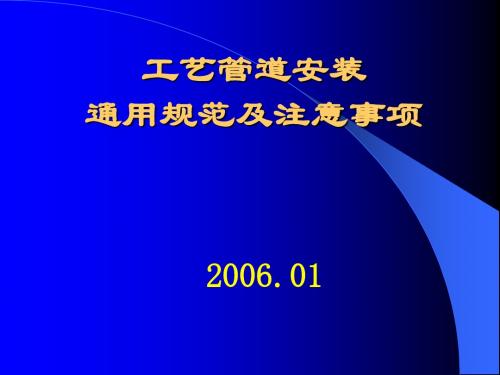
3-4管道预制
1管道预制应按系统单线图进行,按单线图的尺寸要求切割及组 对,并留有调整尺寸。 2切割及坡口加工:钢管切割应采用机械方法,用自动或半自动切 割机进行;不锈钢管可用等离子或砂轮切割机进行切割,切口端 面倾斜偏差不应大于管外径的1%,且不大于3mm。坡口加工采用 角向磨光机,不锈钢管采用专用的角向磨光机。坡口型式按焊接 工程师给出的型式及要求加工。 3 管道预制应遵守下列规定 (1) 为保证配管工程质量和方便安装,应按单线图将管线分段 预制,合理的选择自由段和封闭段,其允许的尺寸偏差见下表: (2) 在预制好的管线上要标记管道系统号,管线号和焊缝号,即 和单线图的标记要一致,管线预制的方向与现场安装方向一致, 在预制段上做出安装方向标记和材料标识; (3) 管道组成件焊口的组对,应做到内壁平齐,内壁错边量不应 超过壁厚的10%,且不大于2mm; (4) 预制的管子要留有50mm的现场调整余量以利安装时调整长度。
3 符合下列条件之一的GC2级工业管道划分为GC3级: a 输送可燃流体介质、无毒流体介质,设计压力<1.0MPa,并且设计温度<400℃的管道; b 输送非可燃流体介质、无毒流体介质,设计压力<4.0MPa,并且设计温度<400℃的管道 。
二
材料验收
管道组成件的检验 阀门试验的管理规定
2-1管道组成件的检验
1 输送剧毒流体、有毒流体、可燃流体管道的阀门;设计压力大于1MPa或设 计压力小于等于1MPa且设计温度小于-29℃或大于186℃的非可燃流体、无毒 流体管道的阀门。必须逐个进行壳体压力试验和密封试验。 2 输送设计压力小于等于1Mpa且设计温度为-29~186°C的非可燃流体,无 毒流体管道的阀门,应从每批中抽查10%,且不少于1个,进行壳体压力试验 和密封试验。当不合格时,应加倍抽查,,仍不合格时,该批阀门不得使用。 3 阀门的壳体试验压力不得小于公称压力的1.5倍,试验时间不得少于5min, 以壳体填料无渗漏为合格;密封试验以公称压力进行,以阀瓣密封面不漏为 合格。 4 试验合格的阀门,要及时排尽内部积水,并吹干。除需要脱脂的阀门外, 密封面上应涂防绣油,关闭阀门,封闭出入口,作出明显标记,并应填写 “阀门试验记录”。 5 公称压力小于1Mpa,且公称直径≥600mm的闸阀,可不单独进行壳体压力 试验和闸阀密封试验。壳体压力试验宜在系统试验时按管道系统的压力试验 进行试验,闸阀密封试验可采用色印等方法进行检验,接合面上的色印应连 续。 6 安全阀应按设计文件规定的开启压力进行试调。试调时压力应稳定,每个 安全阀启闭试验不得少于3次。试调后填写“安全阀最初调试记录”。
长输管道下向焊通用工艺规程
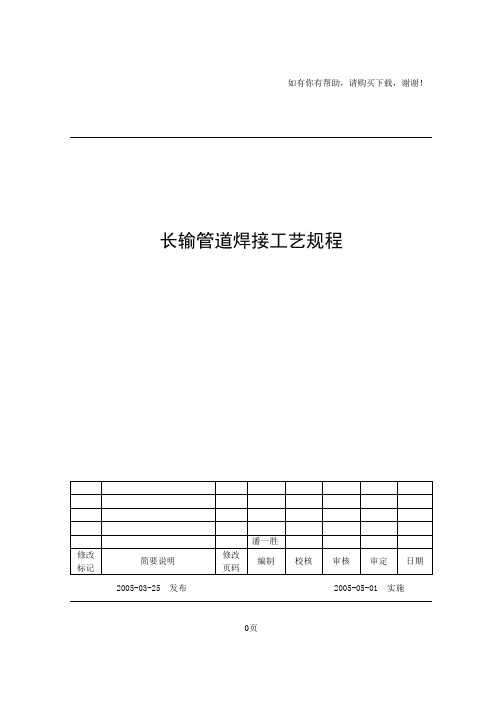
如有你有帮助,请购买下载,谢谢!
长输管道焊接工艺规程
2005-03-25 发布2005-05-01 实施
0页
目次1 总则
1.1 目的
1.2 适用范围
1.3 引用标准
2 施工工艺流程
3 施工准备
3.1 技术准备
3.2工装准备
4设备(材料)验收
4.1出厂技术文件
4.2外观检查
4.3复验批次及质量要求
4.4保管
5施工工艺及技术要求
6交工验收
6.1检查验收内容
6.2交工技术表格
6.3需归档的质量记录
7施工质量管理
7.1质量控制措施
7.2质量控制点划分
8HSE管理
8.1HSE保证措施
8.2JHA工作危险分析
9劳动力组织
10施工机具及手段用料
11施工进度计划
附录A 交工技术表格
附录B 质量控制点划分
附录C JHA工作危险性分析
1 总则
1.1 目的
为了明确长输管道焊接技术管理的工作内容、工作流程、工作方法,保证施工工艺方案的编制质量,推行规范化项目管理,特制定本通用工艺规程。
1.2 适用范围
1.2.1 本工艺规程适用的主要范围为: 本标准适用于直径≥φ159mm,材质为碳素钢及普通低合金钢的输油、输气管道手工电弧焊和药芯焊丝半自动下向对接焊施工。
1.2.2 本工艺规程是长输管道焊接的施工通用工艺文件,各单位在工程施工中,应结合项目具体情况,编制相应的施工技术方案。
1.3 引用标准
2 焊接施工工艺流程
3 施工准备
3.1 技术准备
3.1.1。
50235-2010工业金属管道工程施工规范[9]
![50235-2010工业金属管道工程施工规范[9]](https://img.taocdn.com/s3/m/81d8ec1e59fb770bf78a6529647d27284b733781.png)
50235-2010工业金属管道工程施工规范1. 前言本规范是根据国家标准化管理委员会《关于发布国家标准计划项目的通知》(国标委[2007]第176号)的要求,按照《中华人民共和国国家标准制修订工作规定》(GB/T 1.1-2009)的规定,对原《工业金属管道工程施工及验收规范》(GB 50235-1997)进行了修订。
本规范适用于设计压力不大于42MPa,设计温度不超过材料允许使用温度的工业金属管道工程的施工。
本规范不适用于下列工业金属管道的施工:1. 石油、天然气、地热等勘探和采掘装置的管道;2. 长输管道;3. 核能装置的专用管道;4. 海上设施和矿井的管道;5. 采暖通风与空气调节的管道及非圆形截面的管道。
本规范中第1.0.5、8.6.1 (2)、8.6.6 (1)条(款)为强制性条文,必须严格执行。
本规范自2011年6月1日起实施。
原《工业金属管道工程施工及验收规范》(GB 50235-1997)同时废止。
2. 引用标准GB/T 699-1999 高质量碳素结构钢技术条件GB/T 700-2006 碳素结构钢GB/T 711-2008 碳素结构钢热轧厚钢板和钢带GB/T 713-2008 锅炉及压力容器用钢板GB/T 714-2008 桥梁用结构钢GB/T 8162-2008 结构用无缝钢管GB/T 8163-2008 输送流体用无缝钢管GB/T 9711.1-1997 石油天然气工业输送钢管第1部分:A级钢GB/T 9711.2-1999 石油天然气工业输送钢管第2部分:B级钢GB/T 9711.3-2005 石油天然气工业输送钢管第3部分:C级钢GB/T 12224-2005常压容器用锻制或轧制钢制法兰、锻件及承插件通用技术条件GB/T 12228-2006常压容器用锻制或轧制奥氏体不锈钢法兰、锻件及承插件通用技术条件GB/T 12229-2005常压容器用锻制或轧制低温钢法兰、锻件及承插件通用技术条件GB/T 12230-2005常压容器用锻制或轧制铁素体不锈钢法兰、锻件及承插件通用技术条件GB/T 12771-2008 流体输送用不锈钢焊接钢管GB/T 12777-2008 热交换器用钢管壳体GB/T 13296-2007 锅炉、热交换器和冷凝器用无缝不锈钢管GB/T 13793-2008 直缝电焊钢管GB/T 14975-2002 不锈钢无缝管GB/T 14976-2002 不锈钢无缝管(流体输送用)GB/T 150.1-2011 压力容器第1部分:一般规定GB/T 150.2-2011 压力容器第2部分:材料GB/T 150.3-2011 压力容器第3部分:设计GB/T 150.4-2011 压力容器第4部分:制造GB/T 17395-2008 钢管尺寸、形状、重量及允许偏差GB/T 20801.1-2006 压力管道第1部分:一般要求GB/T 20801.2-2006 压力管道第2部分:材料GB/T 20801.3-2006 压力管道第3部分:设计GB/T 20801.4-2006 压力管道第4部分:制造安装GB/T 20801.5-2006 压力管道第5部分:检验试验GB/T 20801.6-2006 压力管道第6部分:运行维护GB/T 21237-2007 宽厚钢板用高强度低合金结构钢JB/T 4730.1~5-2005 压力设备无损检测第1~5部分:通用要求、超声波检测、射线检测、磁粉检测、渗透检测JB/T 4730.6~7-2005 压力设备无损检测第6~7部分:涡流检测、声发射检测JB/T 4747-1994石油化工设备用奥氏体不锈钢焊接接头的超声波探伤方法JB/T 4748-1994石油化工设备用奥氏体不锈钢焊接接头的射线探伤方法石油化工设备用奥氏体不锈钢焊接接头的磁粉探伤方法JB/T 4751-1994石油化工设备用奥氏体不锈钢焊接接头的渗透探伤方法JB/T 4752-1994石油化工设备用奥氏体不锈钢焊接接头的涡流探伤方法JB/T 4753-1994石油化工设备用奥氏体不锈钢焊接接头的声发射探伤方法JB/T 7928.1~3-1999 工业过程测量和控制系统安装工程第1~3部分:通用要求、仪表安装、电气安装SH/T 3009-1999 石油化工设备安装工程质量验收规范(试行)SH/T 3010-1999 石油化工设备安装工程质量验收规范(试行)SH/T 3011-1999 石油化工设备安装工程施工规范(试行)SH/T 3012-1999石油化工设备安装工程施工组织设计规范(试行)SH/T 3013-1999 石油化工设备安装工程施工管理规范(试行)石油化工设备安装工程施工技术文件编制规范(试行)SH/T 3015-1999石油化工设备安装工程施工图纸编制规范(试行)SH/T 3016-1999石油化工设备安装工程施工图纸审查规范(试行)SH/T 3017-1999石油化工设备安装工程施工图纸变更管理规范(试行)SH/T 3018-1999石油化工设备安装工程施工图纸管理规范(试行)SH/T 3020-1999石油化工设备安装工程施工质量控制规范(试行)SH/T 3021-1999石油化工设备安装工程施工质量检验规范(试行)SH/T 3022-1999石油化工设备安装工程施工质量评定规范(试行)SH/T 3023-1999石油化工设备安装工程施工质量记录规范(试行)石油化工设备安装工程施工质量分析与改进规范(试行)SH/T 3025-1999石油化工设备安装工程施工质量保证体系建立与运行规范(试行)SH/T 3026-1999石油化工设备安装工程施工质量审核规范(试行)SH/T 3027-1999 石油化工设备安装过程中的环境保护与节能措施3. 术语和定义本规范采用下列术语和定义:3.1 工业金属管道指在设计压力不大于42MPa,设计温度不超过材料允许使用温度的条件下,用于输送气体、液体、蒸汽、泥浆等介质的金属管道。
第二章管道穿跨越工程使用说明.

第⼆章管道穿跨越⼯程使⽤说明.第⼆章管道穿跨越⼯程使⽤说明⼀、本章适⽤于长距离输送管道⼯程穿跨越公路、铁路、河流、管道、电缆、光缆及其它穿跨越⼯程。
⼆、本章包括:穿跨越直管段安装⼯程(通⽤)、公路穿越、河流穿越(开挖)、管道跨越、地下建、构筑物穿越、定向钻穿越等⼯程。
三、穿跨越⼯程的场地平整、⼟⽯⽅⼯程套⽤本册相应⼦⽬;⽔⼯保护、便道、便桥等项⽬可执⾏⼯程所在地建筑、市政⼯程定额。
四、穿跨越管道安装1、隧道内管道安装⑴、⼭体隧道内管道安装a、本定额是按隧道坡度⼩于10°、隧道主体施⼯完成、隧道内墙、底板的平直度、坡度达到管道施⼯条件情况下考虑的,坡度⼤于10°的⼭体隧道安装,按施⼯⽅案另计。
b、卷扬机牵引有轨⾃制⼩车运布管按隧道长度500m取定,隧道长度每增减100m时,⼈、机增减1.1系数。
c、牵引车牵引⽆轨⾃制⼩车运布管的牵引设备已综合考虑,使⽤时不再调整。
d、牵引车牵引⽆轨⾃制⼩车运布管按隧道长度1000m取定,从隧道⼀侧往另⼀侧全线布管考虑的,隧道长度每增减100m时,⼈、机增减1.04系数。
e、⼭体隧道内的管道布管按单线施⼯取定,设计为双线施⼯时,第⼆条管线的⼈、机调增系数见下表:f、⼭体隧道内的管道安装按单线施⼯取定,设计为双线施⼯时,第⼆条管线的⼈、机调增系数见下表:g、隧道内的吊管龙门架、焊接⾏⾛⼩车、牵引车带的⽆轨⾃制⼩车已在定额型钢⽀架⽤量中摊销计⼊。
h、⼭体隧道内管道安装不包括的内容:(a)、⼭体隧道外的临时堆管场平整、卷扬机安装及基础施⼯固定等。
(b)、坡度⼤于10°的隧道运布管、焊接施⼯措施费。
(c)、⼭体隧道内的轨道安拆、通风、照明等安装施⼯措施。
(d)、⼭体隧道内的管道⽀墩上的管道⽀架的制作安装。
(2)、盾构隧道管道安装a、隧道运布管(a)、运布管是按单线施⼯编制的,双线施⼯时,第⼆条管线按第⼀条管线⼈⼯机械乘1.7倍系数。
(b)、隧道内吊管⽀架、临时管⽀敦已在型钢⽀架消耗量中摊销计⼊。
压力管道设计与审批人员考试题电子版---5

考试题电子版(部分试题)1.根据《特种设备生产单位许可目录》的要求,压力管道用阀门是压力管道元件。
(0.5分)[法规、规范题]A.对B.错2.根据《特种设备生产单位许可目录》的要求,某空气管道最高工作压力1.2ma、最高工作温度50℃、公称直径100mn,按照《特种设备生产单位许可目2录》(国家市场监督管理总局公告[2021]第41号),该管道属于压力管道。
(0.5分)[法规、规范题]Â.对 B.错3.制冷管道属于《特种设备生产单位许可目录》中的公用管道。
(0.5分)[法规、规范题A.对B.错4.根据TSG2F003《爆破片装置安全技术监察规程》的要求,爆破片更换周期应当根据设备使用条件、介质性质等具体影响因素,或者设计预期使用年限合理确定,一般情况下爆破片装置更换周期为4年。
对于腐蚀性、毒性介质以及苛刻条件下使用的爆破片装置应当缩短更换周期。
(0.5分)[法规、规范题A.对B.错5.三通焊缝的射线检测试验是管道无损检验的方法之一。
(0.5分)[通用知识题]A.对B.错6.根据现行国家标准《防止静电事故通用导则》GB12158规定,可燃物的温度比常温低的环境更易发生引燃、引爆等静电危害。
(0.5分)[通用知识题)A.对B.错4.3在下列环境下,更易发生引燃、引爆等静电危害。
-可燃物的温度比常温高;--局部环境氧含量(或其他助燃气含量)比正常空气中高:-爆炸性气体的压力比常压高;--相对逐度较低。
7.现行国家标准《建筑灭火器配置设计规范》(B50140规定,工业建筑灭火器配置场所的危险等级应根据其使用性质,人员密集程度,用电用火情况,可燃物数量,火灾蔓延速度,扑救难易程度等因素划分为严重危险级、中危险级和轻危险级。
(0.5分)[通用知识题1Â.对 B.错8.现行国家标准《管道支吊架》B/T 17116规定,在管道支吊架设计时,不应计入管道或管道绝热层外表面温度<20℃的室外管道受到的雪荷载。
管道工程质量控制点等级划分表

工程质量控制点等级划分表
管道工程
注:A级:关键过程或工序质量控制点,由业主项目组、监理(EPCM承包商)、工程建设承包商专业技术人员共同参加的质量检查、检测或见证。
B级:重要过程或工序质量控制点,由监理(EPCM承包商)、EPC承包商、施工承包商专业技术人员共同参加的质量检查、检测或见证。
C级:一般过程或工序质量控制点,由EPC承包商、施工承包商专业技术人员自行实施的质量检查、检测。
H点:既质量停检控制点。
表示未经业主专业人员见证或参加检查通过,承包商不得以任何理由进行下步工序。
若因此业主原因造成承包商工期延误或费用增加,承包商有权向业主索赔。
FH点:既首件样板质量停检控制点。
表示承包商在多人次、多部位重复发生的工序或应用新材料、新技术的工序时,必须策划首件样板工程,待通过业主项目组、监理(EPCM承包商)、工程建设承包商专业技术人员共同参加的质量检查、检测后,后续重复工作方可全面开展。
详见《首件样板施工管理规定》(SHEC-P07-10)。
W点:既质量观察控制点。
表示若业主专业人员未按事先约定或承包商通知时间到场参加检查验证,承包商有权继续进行下步工序,业主专业人员事后应对承包商质量检查、检测结果予以认可。
压力管道焊接工艺规程完整

压力管道焊接工艺规程1 合用范围本规程合用于工业管道或公用管道中材质为碳素钢、低合金钢、耐热钢、不锈钢和异种钢等压力管道的焊条电弧焊、钨极氩弧焊以及二氧化碳气体保护焊的焊接施工。
2 重要编制依据2.1 GB50236-2023《现场设备、工业管道焊接工程施工及验收规范》;2.2 GB/T20801-2023《压力管道规范-工业管道》;2.3 SH3501-2023《石油化工剧毒、可燃介质管道工程施工及验收规范》;2.4 GB50235-2023《工业金属管道工程施工及验收规范》;2.5 CJJ28-2023《城市供热管网工程施工及验收规范》;2.6 CJJ33-2023 《城乡燃气输配工程施工及验收规范》;2.7 GB/T5117-2023 《碳钢焊条》;2.8 GB/T5118-2023 《热强钢焊条》;2.9 GB/T983-2023 《不锈钢焊条》;2.10 YB/T5092-2023《焊接用不锈钢丝》;2.11 GB14957-1994《焊接用钢丝》;2.12 其他现行有关标准、规范、技术文献。
3 施工准备3.1 技术准备3.1.1 3.2 对材料的规定3.4 焊接人员3.4.2 3.5 施焊环境4.1 压力管道焊接施工流程图(见图1 )图1 焊 接 施 工 流 程 图 4.2 焊前准备及接头组对4.2.1 4.2.2 b )异种钢管子焊接时, 焊条或焊丝的选用一般应符合下列规定: 表1 常用钢号推荐选用的焊接材料焊前准备焊机性能确认 焊口组对质量评估正式施焊 焊接检查焊缝无损探伤结果评估焊后热解决硬度测试水压实验焊接坡口制备及清理 焊条烘干及焊丝清理焊缝外观检查是表2 不同钢号相焊推荐选用的焊接材料表3 常用钢号分类分组4.2.4 a)按SH3501-2023《石油化工剧毒、可燃介质管道工程施工及验收规范》分为SHA级的压力管道、中高合金钢及不锈钢管道的坡口应采用机械方法加工。
b)其他管道坡口宜采用机械方法加工, 当采用热加工方法时, 切割后必须去除影响焊接质量的表面层。
- 1、下载文档前请自行甄别文档内容的完整性,平台不提供额外的编辑、内容补充、找答案等附加服务。
- 2、"仅部分预览"的文档,不可在线预览部分如存在完整性等问题,可反馈申请退款(可完整预览的文档不适用该条件!)。
- 3、如文档侵犯您的权益,请联系客服反馈,我们会尽快为您处理(人工客服工作时间:9:00-18:30)。
长输管道下向焊通用工艺1适用范围本通用工艺标准适用于大口径长距离输油(气)管道工程的下向焊焊接施工。
2引用(依据)文件2.1《输油输气管道线路工程施工及验收规范》................................................ S Y/T0401--1998 2.2《石油和天然气管道穿越工程施工及验收规范》..................................... S Y/T0479—1995 2.3《石油天然气管道焊接工艺评定》................................................................. S Y4052—20022.4《管道下向焊接工艺规程》 ........................................................................... S Y/T4071-932.5《钢质管道焊接及验收》.................................................................................. S Y/T4103-952.6《石油工程建设质量检验标准输油输气管道线路工程》 .......................... S Y/T4029--2000 2.7《石油工程建设质量检验标准管道穿跨越工程》 ....................................... S Y/T4104--1995 2.8《石油天然气钢制管道对接焊缝射线照相及质量分级》 .......................... S Y4056--932.9《石油天然气钢制管道对接焊缝超声波探伤及质量分级》 ...................... S Y4065--932.10《锅炉压力容器焊工考试规则》3施工准备3.1材料要求3.1.1管材、管件(弯管、弯头、阀门等)应有出厂质量证明书或材质复验报告。
3.1.2 焊材应有质量证明书或产品合格证。
焊条的规格型号应符合设计要求。
3.1.3 原则上纤维素下向焊焊条不需进行烘干,若受潮或长期暴露在空气中,烘干温度为70~80℃,不得超过100℃,恒温时间0.5 ~ 1 h。
3.2主要设备及机具3.2.1主要设备:移动电站、逆变焊机、半自动焊机、吊管机、内(外)对口器、环形加热器、烘干箱、恒温箱。
3.2.2工具:焊条保温筒、角向磨光机、电子测温计、电流表、风速仪、干湿温度计、焊缝检验尺、钢丝刷、砂轮片等。
3.3作业条件3.3.1管材、焊材及其他材料、设备机具均已齐全到位,各类仪表及检测器具均已检验合格。
3.3.2防风、防雨棚按要求制作好,且在施工现场。
3.3.3焊接工艺规程已按《石油天然气管道焊接工艺评定》的要求完成,并编制好焊接作业指导书。
3.3.4焊工的培训、考试和管理,按《锅炉压力容器焊工考试规则》的要求执行。
4施工工艺4.1施工流程图4.1 下向焊工艺流程图4.2坡口型式及组对要求:4.2.1 接头形式:对接 坡口形式:V 型 钝边:2.0±0.5 坡口角度60±5 对口间隙2.0~3.0mm 错边≤1.5mm垫板:无 盖面焊缝宽度:两侧每侧比坡口外表面宽1.0-2.0mm余高:0-1.6 mm ,局部不充许大于3.0 mm4.2.2组对时,当采用外对口器对口时,必须在根焊至少完成50%以上时方可将对口器撤离;当采用内对口器对口时,必须在根焊全部完成时方可将对口器撤离。
4.2.3组对前应将坡口表面及边缘不小于20mm 范围内的油污、铁锈、毛刺清除干净,直至露出金属光泽,坡口表面不得有裂纹和夹层等缺陷。
4.2.4.两管口螺旋焊缝间距应错开至少100 mm 以上。
4.2.5错口等于或小于1.5mm 沿圆周均匀分布,个别处可使用铜锤校正。
4.2.6钢管短节长度大于管径且不小于0.5m ,管子的组对偏差小于或等于3°,不允许割斜口。
4.3焊接4.3.1焊接方法采用手工电弧焊或手工电弧焊打底+半自动焊填充盖面。
焊条采用纤维素下向焊焊条,焊丝采用半自动用药芯焊丝。
4.3.2定位焊与正式焊接工艺相同。
采用外对口器对口,定位焊缝长度不得小于100mm ,每道口定位焊不少于6点,且应基本均匀分布。
4.3.3需要预热时在定位焊前进行,预热要求如表4.3.2或符合相关标准。
不合格4.3.4管口预热采用氧乙炔焰加热,当用内对口器对口时用环形加热器加热,当采用外对口器对口时用烤把加热的方法,加热温度为100℃左右。
预热范围应不小于焊道两侧各100mm。
4.3.5焊接采用对称焊流水作业,每道焊口均分为两侧各半个焊口,分别由两名焊工负责从根焊到盖面焊的施焊;采用多层单道焊。
4.3.6不同壁厚的焊接层数应符合表4.3.12-1的规定。
4.3.7根焊时,起弧点基本在12点处,应保证熔透,后起弧的焊工要将接头处打磨,避免产生夹渣等缺陷。
4.3.8管道焊接时,每层焊道必须连续一次焊完,相邻两层焊道的接头应错开20 ~30mm,热焊与根焊的时间不宜超过5min。
4.3.9每道焊缝焊完后应将表面的飞溅物、熔渣清除干净,如无特殊的规定,一般情况下在管道介质流向的下方0.5m-1.0m处标出焊口编号,并做好组对、焊接等记录。
4.3.10管道焊接时,应采取措施防止管内成为风道,必要时应封闭管道两端。
4.3.11管段焊接完待无损检测合格后,要将两端即时封堵,避免异物进入。
4.3.12焊接规范:1.焊接层数:一般情况下,不同管壁厚的焊接层数可参考表4.3.12-1的规定。
2.焊接参数:纤维素型焊条下向焊参数见表4.3.12-2注:DC-指直流电源、焊条接负极。
4.4焊缝检验4.4.1 外观质量应符合《管道下向焊接工艺规程》SY/T4071-93的要求。
主要有以下几点:a表面不得有裂纹、未熔合气孔和夹渣等缺陷。
b咬边深度不得大于0.5mm,在任何300mm长焊缝中,两侧累计咬边长度不大于50mm。
c焊缝余高一般为0.5~1.6mm,特殊部位管底不得超过3mm,且长度不超过50mm。
4.4.2.管道无损检测a. 外观检查合格后按设计图纸要求进行无损检测,一般情况下,管道焊口进行100%超声波探伤和10%射线检验。
b.对主要的穿跨越以放大图为准的管道焊口、钢管与弯头连接的焊口及试压后接头的碰口进行100%超声波探伤外加100%射线检验。
c.射线检验应达到《石油天然气钢质管道对接焊缝射线照相及质量分级》SY4056-93中Ⅱ级焊缝标准的要求;超声波探伤应达到《石油天然气钢质管道对接焊缝超声波探伤及质量分级》SY4065-93中Ⅰ级焊缝标准的要求。
4.5焊缝返修4.5.1经检验不合格的焊缝应进行返修。
4.5.2返修前应由无损检测人员在焊逢上准确标明缺陷具体位置和大小。
4.5.3缺陷采用直接用磨光机清除。
焊缝返修最少长度不小于50mm。
4.5.4返修焊接工艺详见其相关的返修工艺规程。
4.5.5焊缝返修不得超过两次。
4.6注意事项4.6.1焊接用二次线要制作成长输管道专用卡具型,焊接时不允许直接在母材上引弧,并要采取措施保护母材,防止被飞溅灼伤母材。
4.6.2 焊接场所应采取防风、防雨、防雪、防寒。
在下列焊接环境下,如不采取有效防护措施,应停止焊接作业。
1.雨天、雪天。
2.风速超过8m/s。
3.相对湿度大于90%以上。
5质量标准5.1 外观质量5.1.1焊缝表面应无裂纹、夹渣、未熔合、气孔等缺陷。
5.1.2 焊缝咬边深度≤0.5mm,在焊缝300mm连续长度中咬边长度≤50mm。
5.1.3 余高:应为0-1.6mm,局部不得大于3mm,累积长度不得大于50mm。
5.1.4错边量:应≤0.15δ(δ为管壁厚),局部最大错边量应≤2mm。
5.1.5整条焊缝宽度比每侧坡口增宽1.0- 2.0mm为宜。
5.2焊缝无损检测见4.4.2所述。
6成品保护6.1施焊完的管段应封住端口,免进入杂物。
6.2焊机的电缆线不得随意搭放在管子上,以免电弧划伤管材表面。
6.3防腐管装卸应使用专用吊具,严禁野蛮装卸作业并应特别注意管口保护。
运输弯头、弯管应采取有效的固定措施。
车辆的栏杆要用橡胶包扎,避免钢铁直接接触碰伤管材。
6.4管材堆放时下面设置管堆,管堆要用草袋装土堆置而成。
6.5现场使用的耙犁上要放置胶皮做好对管材的保护。
7施工注意事项7.1 电焊机开机前要做好设备的例行安全检查。
7.2 焊工必须穿戴齐全劳保用品且持证方可上岗。
7.3 工作场地附近不得堆放易燃易爆物品。
7.4 焊接现场有积水或潮湿时,应采取垫放干燥木板或橡胶等隔水隔潮措施,焊工应穿胶质鞋作业。
7.5不允许将通电的焊把或裸露的把线随意搭在管上。
7.6电焊把线尽量不要有接头,有接头处应连接良好,绝缘可靠,把线破损严重时应及时更新。
7.7施工现场所用电气设备及电源开关应有良好的防风、防火和防盗性能,电源开关的保险规格要符合使用要求。
8质量记录技术交底记录合格焊工登记表施工过程工序交接记录管道组对及坡口检查记录管道焊接工作记录焊缝无损检测委托单焊缝射线探伤报告焊缝超声波探伤报告。