失效分析基本常识及操作流程培训
失效分析基本常识及操作计划流程培训
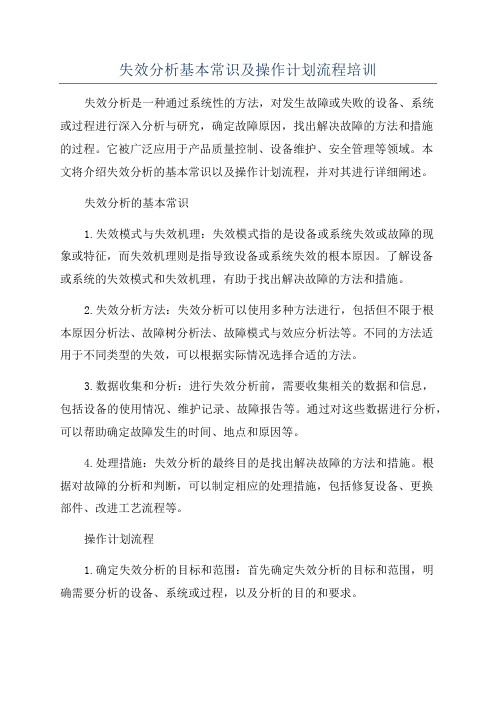
失效分析基本常识及操作计划流程培训失效分析是一种通过系统性的方法,对发生故障或失败的设备、系统或过程进行深入分析与研究,确定故障原因,找出解决故障的方法和措施的过程。
它被广泛应用于产品质量控制、设备维护、安全管理等领域。
本文将介绍失效分析的基本常识以及操作计划流程,并对其进行详细阐述。
失效分析的基本常识1.失效模式与失效机理:失效模式指的是设备或系统失效或故障的现象或特征,而失效机理则是指导致设备或系统失效的根本原因。
了解设备或系统的失效模式和失效机理,有助于找出解决故障的方法和措施。
2.失效分析方法:失效分析可以使用多种方法进行,包括但不限于根本原因分析法、故障树分析法、故障模式与效应分析法等。
不同的方法适用于不同类型的失效,可以根据实际情况选择合适的方法。
3.数据收集和分析:进行失效分析前,需要收集相关的数据和信息,包括设备的使用情况、维护记录、故障报告等。
通过对这些数据进行分析,可以帮助确定故障发生的时间、地点和原因等。
4.处理措施:失效分析的最终目的是找出解决故障的方法和措施。
根据对故障的分析和判断,可以制定相应的处理措施,包括修复设备、更换部件、改进工艺流程等。
操作计划流程1.确定失效分析的目标和范围:首先确定失效分析的目标和范围,明确需要分析的设备、系统或过程,以及分析的目的和要求。
2.收集故障数据和信息:收集与故障相关的数据和信息,包括设备的使用情况、维护记录、故障报告等。
通过对这些数据进行分析,可以帮助确定故障发生的时间、地点和原因等。
4.分析故障机理和模式:根据调查和观察的结果,对故障机理和模式进行分析,找出导致设备或系统失效的根本原因。
5.制定处理措施:根据对故障的分析和判断,制定相应的处理措施,包括修复设备、更换部件、改进工艺流程等。
同时,给出预防措施,以避免类似故障再次发生。
6.实施处理措施:根据制定的处理措施,组织实施修复、更换等工作。
同时,对工作结果进行检查和验证,确保故障得到彻底解决。
FA失效模式分析

2021/4/14
1.0 基本概念
1.2 什么是“失效模式” ? --- 失效模式是指由失效机理所引起的可观察到的物理 或化学变化(如开路、短路或器件参数的变化)。
通俗讲就是失效的表现形式。 失效模式通常从技术角度可按失效机制、失效零件 类型、引起失效的工艺环节等分类。从质量管理和可靠性 工程角度可按产品使用过程分类。
(FA)失效分析基本常识 及操作流程
—— 建立失效分析管理程序
2021/4/14
1.0 基本概念
1.1 什么是“失效分析” 、“FA”? 失效分析:
--- 是指产品失效后,通过对产品及其结构、使用和技 术文件的系统研究,从而鉴别失效模式、确定失效机理 和失效演变的过程。 FA: --- Failure Analysis
案例
2021/4/14
4.0 分析方法
4.2 半破坏性分析
修复参数,提取能够 使其参数回复的条件,
从而总结失效机理
案例
2021/4/14
4.0 分析方法
4.3 破坏性分析 排除A处的因素
案例
2021/4/14
4.0 分析方法
4.3 破坏性分析
分解器件观察 对比
2021/4/14
5.0 主要程序
失效情况调查
器件相关信息 使用信息 环境信息
失效现象
失效过程
鉴别失效模式 失效特征描述
2021/4/14
光电特性测试 结构特征鉴定
形状 颜色
大小 机械结构
位置 物理特性
5.0 主要程序
失效机理分析
参考相关标准 综合分析 还原现象 观测失效样品 实验对比
提交分析报告
任务来源 分析过程
零件失效分析失效分析基础知识

表3 在一般工业工程中调查的失效原因的比例
起
因
材料选择不恰当 装配错误 错误的热处理 机械设计错误 未预见的操作条件 环境控制不够充分 不恰当的或缺少监测与质量控制 材料混杂
(%)
38 15 15 11 8 6 5
2
表4 航空零件失效原因的比例
起
因
保养不恰当 安装错误 设计缺陷 不正确的维修损坏 材料缺陷 未定原因
❖ 氢腐蚀(高温氢侵蚀)引起的蒸汽管道爆管事故
氢腐蚀是蒸汽管道、锅炉管与石油化工临氢高温装备中较常见的 失效模式。 这种失效模式可能没有明显的腐蚀现象,但是材料性能严重退化, 事故的隐患已经存在。在氢处理、重整、加氢裂化等装置中,温 度超过260℃,氢的分压大于689kPa,就有可能发生氢分子在钢 的表面分解为原子氢而发生腐蚀。氢腐蚀是原子氢进入钢铁材料, 并与碳化物反应生成甲烷(Fe3C+4H→3Fe+CH4),由于甲烷的分 子尺寸大而不易扩散,会使甲烷在晶界或相界面等处聚集产生局 部高压,形成微裂纹,进而材料脆化。
❖ 催化裂化装置再生器的硝酸盐应力腐蚀失效
➢ 裂纹均从内表面开始向外表面扩展,裂纹发生部位未见明显塑 性变形,裂纹宽度较窄,向纵深发展并多数穿透壁厚;
➢ 裂纹呈树枝状,断口有典型的沿晶特征; ➢ 腐蚀产物的水溶液PH值在5~6,呈现酸性; ➢ 断口表面腐蚀产物中的氮含量均明显高于基体金属中的氮含量; ➢ 结论是NO3-引起的应力腐蚀开裂。
上海汽车锻造总厂生产的汽车钢板弹簧产生早期失效,综合 分析发现:表面存在较多较深的弹坑及局部脱碳。
应力状态:弯曲疲劳
缺陷:
➢ 降低应力集中的措施
强化材料,降低应力集中的作用
整体强化 局部强化
第2章 失效分析基础知识-最终版
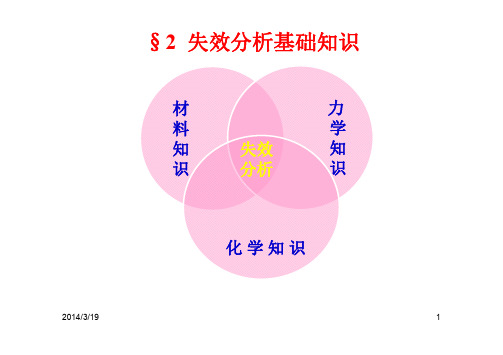
§ 2.2 应力集中与零件失效
§ 2.2.1 应力集中与应力集中系数
应力集中:零件截面有急剧变化,引起局部地区的应力 高于受力体的平均应力。 应力集中处往往是构件破坏的起始点,应力集中是引起 构件破坏的主要因素。 应力集中系数:表示应力集中程度大小的系数。 构件中产生应力集中的原因主要有:
z a r cos ir sin y r sin
r远小于a,将上式按r/a的升幂次展开,只保留随r的减小而 增大的主项,略去其中的次项
2a cos y z q r 2 2a 3 3 2014/3/19 2i sin cos (sin i cos ) y z xy q r 2 2 2 2
iz y z 2q Re 2 z a2 2 2 2 2i q Re ia z iz( 2 z 3a ) y z xy ( z 2 a 2 )3 / 2
KI a 在裂纹线上, =0,其应力 x = y =0, xy =q = 2014/3/19 21 2r 2 r
max a Kt 1 2 ( a ) 平均
2014/3/19
椭圆孔长轴顶 端的曲率半径
曲率半径小的尖角处Kt大,将尖角改 为圆角,或流线形变化的截面能有效 15 5 地缓和应力集中程度
§ 2.2 应力集中与零件失效
2014/3/19
16 5
§ 2.2 应力集中与零件失效
上式表明拉应力与1/ r成比例,即r 0, x, y, xy
KI a 在裂纹线上, =0,其应力 x = y =q = , xy =0 2014/3/19 19 5 2r 2 r
失效分析基本常识以及操作流程

失效分析基本常识以及操作流程失效分析是一种通过分析和探究事物、系统或过程发生失效的原因和机制的方法。
它可以帮助我们识别并改进潜在的问题,以提高系统的可靠性和性能。
以下是关于失效分析的基本常识与操作流程。
一、失效分析的基本常识1.失效模式与效应分析(FMEA):FMEA是一种通过分析预测和评估失效模式及其严重性、发生概率和检测能力的方法。
它可以在设计、生产和使用阶段预防或减少失效。
2.失效树分析(FTA):FTA是一种通过将失效进行因果关系的图形化表示来分析系统失效的方法。
它能够帮助确定导致一些具体失效的事件链。
3.事故树分析(ETA):ETA是一种通过将事故及其后果进行因果关系的图形化表示来分析事故发生的方法。
它可以帮助识别和评估事故的潜在原因及其对系统的影响。
4.失效模式、原因和影响分析(FMEDA):FMEDA是一种通过分析失效模式、失效原因和失效影响的方法来评估系统的可靠性。
它通常用于评估硬件系统。
5.人因分析:人因分析是一种通过分析人因相关的错误、失误和措施来评估和改进工作系统和流程的方法。
它可以帮助减少人为失误和提高操作效率。
二、失效分析的操作流程1.确定分析目标:确定需要进行失效分析的系统、产品或过程,并明确分析的目标和范围。
例如,是为了解决一个特定的问题,还是为了提高整体系统的可靠性等。
2.收集相关数据:收集和整理与失效有关的数据和信息,包括过去的失效记录、测量数据、使用情况等。
这些数据将为后续的分析提供基础。
3.选择适当的工具和方法:根据分析的目标和需要,选择适合的失效分析方法和工具,如FMEA、FTA、ETA等。
有时需要结合多种方法进行分析。
4.定义失效模式与效应:识别和描述可能的失效模式及其对系统的影响。
这包括对失效模式的描述和分类,以及对失效的严重性进行评估。
5.分析失效原因:通过追溯失效模式,分析导致失效发生的可能原因和机制。
这包括对失效原因的分类和评估,以及确定潜在缺陷和改进点。
fmea培训内容

fmea培训内容FMEA(失效模式和影响分析)培训内容FMEA(失效模式和影响分析)是一种常用的风险管理工具,用于识别、评估和减少潜在的失效模式及其对系统或过程的影响。
FMEA培训旨在帮助参与者掌握FMEA方法和技巧,以有效地应用于实际工作中,提高风险管理能力和工作效率。
一、什么是FMEA?FMEA是一种系统性的方法,通过分析失效模式、评估其影响和确定风险等级,以提前识别和减少潜在的问题。
FMEA可以应用于各个领域,例如制造业、医疗保健、汽车工业等,帮助组织识别潜在的问题并采取相应的改进措施。
二、FMEA的基本步骤1. 确定分析范围:确定需要进行FMEA分析的系统、过程或产品,并明确分析的目的和范围。
2. 建立团队:组建一个跨职能的团队,包括相关的专业人员和利益相关者,以确保全面的分析和有效的决策。
3. 收集相关信息:收集系统、过程或产品的相关信息,包括设计、工艺、操作手册、历史数据等。
4. 识别失效模式:通过头脑风暴、经验分享等方法,识别可能的失效模式,并记录在FMEA表格中。
5. 评估影响:对每个失效模式进行影响评估,包括对安全、质量、生产效率等方面的影响进行定量或定性评估。
6. 确定原因和控制措施:确定导致失效模式的原因,并提出相应的控制措施,以减少或消除潜在的问题。
7. 评估风险等级:根据失效的严重性、发生频率和检测能力,评估风险等级,以确定优先处理的失效模式。
8. 制定改进计划:根据风险等级和控制措施的效果,制定相应的改进计划,并明确责任人和时间表。
9. 实施改进:按照改进计划的要求,实施所需的改进措施,并监控其效果。
三、FMEA的优势和应用1. 优势:- 提前识别潜在的问题,减少风险;- 增加对系统或过程的了解,改进设计和工艺;- 提高团队协作和沟通;- 降低成本,减少不良事件和事故的发生。
2. 应用:- 新产品开发:在产品设计阶段,通过FMEA识别潜在的问题,并采取相应措施,确保产品质量和安全性。
失效分析操作指南
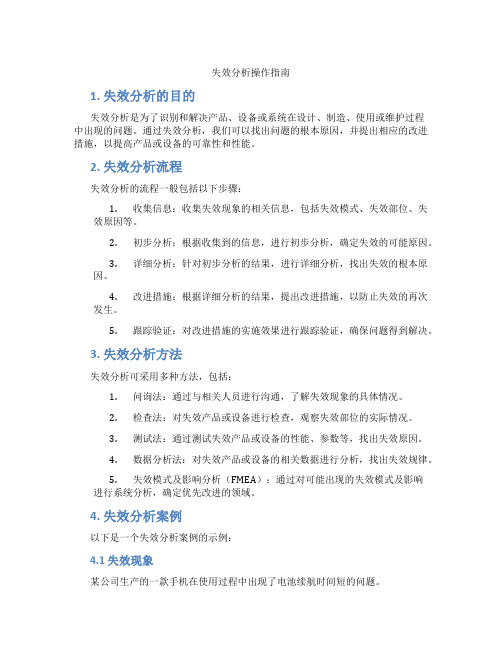
失效分析操作指南1. 失效分析的目的失效分析是为了识别和解决产品、设备或系统在设计、制造、使用或维护过程中出现的问题。
通过失效分析,我们可以找出问题的根本原因,并提出相应的改进措施,以提高产品或设备的可靠性和性能。
2. 失效分析流程失效分析的流程一般包括以下步骤:1.收集信息:收集失效现象的相关信息,包括失效模式、失效部位、失效原因等。
2.初步分析:根据收集到的信息,进行初步分析,确定失效的可能原因。
3.详细分析:针对初步分析的结果,进行详细分析,找出失效的根本原因。
4.改进措施:根据详细分析的结果,提出改进措施,以防止失效的再次发生。
5.跟踪验证:对改进措施的实施效果进行跟踪验证,确保问题得到解决。
3. 失效分析方法失效分析可采用多种方法,包括:1.问询法:通过与相关人员进行沟通,了解失效现象的具体情况。
2.检查法:对失效产品或设备进行检查,观察失效部位的实际情况。
3.测试法:通过测试失效产品或设备的性能、参数等,找出失效原因。
4.数据分析法:对失效产品或设备的相关数据进行分析,找出失效规律。
5.失效模式及影响分析(FMEA):通过对可能出现的失效模式及影响进行系统分析,确定优先改进的领域。
4. 失效分析案例以下是一个失效分析案例的示例:4.1 失效现象某公司生产的一款手机在使用过程中出现了电池续航时间短的问题。
4.2 初步分析初步分析认为,电池续航时间短可能是由以下原因导致的:1.电池本身质量问题2.软件优化不足3.硬件设计不合理4.3 详细分析针对初步分析的结果,进行详细分析:1.电池质量问题:对电池进行检测,发现电池的容量低于标准值,确认电池质量问题。
2.软件优化不足:对手机软件进行监测,发现存在后台应用耗电量较高的问题,优化软件后台耗电策略。
3.硬件设计不合理:对手机硬件进行拆解,发现电池与手机壳之间的间隙过大,导致电池散热不良,优化电池与手机壳之间的结构设计。
4.4 改进措施根据详细分析的结果,提出以下改进措施:1.更换质量合格的电池2.优化软件后台耗电策略3.优化电池与手机壳之间的结构设计,提高散热效果4.5 跟踪验证对改进措施的实施效果进行跟踪验证,确认问题已得到解决。
失效分析基本常识以及操作流程概要
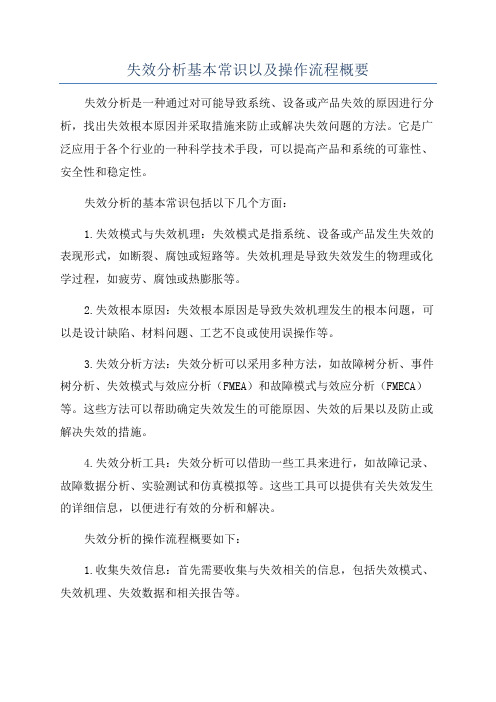
失效分析基本常识以及操作流程概要失效分析是一种通过对可能导致系统、设备或产品失效的原因进行分析,找出失效根本原因并采取措施来防止或解决失效问题的方法。
它是广泛应用于各个行业的一种科学技术手段,可以提高产品和系统的可靠性、安全性和稳定性。
失效分析的基本常识包括以下几个方面:1.失效模式与失效机理:失效模式是指系统、设备或产品发生失效的表现形式,如断裂、腐蚀或短路等。
失效机理是导致失效发生的物理或化学过程,如疲劳、腐蚀或热膨胀等。
2.失效根本原因:失效根本原因是导致失效机理发生的根本问题,可以是设计缺陷、材料问题、工艺不良或使用误操作等。
3.失效分析方法:失效分析可以采用多种方法,如故障树分析、事件树分析、失效模式与效应分析(FMEA)和故障模式与效应分析(FMECA)等。
这些方法可以帮助确定失效发生的可能原因、失效的后果以及防止或解决失效的措施。
4.失效分析工具:失效分析可以借助一些工具来进行,如故障记录、故障数据分析、实验测试和仿真模拟等。
这些工具可以提供有关失效发生的详细信息,以便进行有效的分析和解决。
失效分析的操作流程概要如下:1.收集失效信息:首先需要收集与失效相关的信息,包括失效模式、失效机理、失效数据和相关报告等。
2.确定失效根本原因:通过对失效信息进行分析,确定失效的根本原因。
可以采用故障树分析等方法来帮助确定可能的失效原因。
3.评估失效后果:评估失效的后果,包括人员伤害、财产损失和环境影响等。
可以采用FMEA和FMECA等方法来评估失效的后果。
4.制定措施:根据失效的根本原因和后果,制定相应的措施来防止或解决失效问题。
这些措施可以包括改进设计、优化工艺、更换材料或提供培训等。
5.实施措施:根据制定的措施,进行实施。
这可能涉及到产品的改进、工艺的优化或操作人员的培训等。
6.监控效果:监控实施措施的效果,以确保达到预期的目标。
如果发现新的失效问题,需要重新进行失效分析并制定相应的措施。
- 1、下载文档前请自行甄别文档内容的完整性,平台不提供额外的编辑、内容补充、找答案等附加服务。
- 2、"仅部分预览"的文档,不可在线预览部分如存在完整性等问题,可反馈申请退款(可完整预览的文档不适用该条件!)。
- 3、如文档侵犯您的权益,请联系客服反馈,我们会尽快为您处理(人工客服工作时间:9:00-18:30)。
11/26/2020
10
3.0 意义和价值
3.2 质量管理闭环系统中的重要环节。
无论是”PDCA”循环还是”6σ”理念中”DMAIC” 管理模型,缺少失效分析就不能形成闭环系统。
11/26/2020
11
根据改善 效果建立
标准
3.0 意义和价值
分析原因并提 出改善措施, 制定改善计划
存在的问
题进行失 效分析
•
好的事情马上就会到来,一切都是最 好的安 排。上 午7时54 分21秒 上午7 时54分0 7:54:21 20.11.2 6
•
每天都是美好的一天,新的一天开启 。20.11. 2620.1 1.2607: 5407:54 :2107:5 4:21Nov-20
•
务实,奋斗,成就,成功。2020年11 月26日 星期四7 时54分 21秒Thursday, November 26, 2020
4.1 非破坏性分析 4.2 半破坏性分析 4.3 破坏性分析
11/26/2020
14
4.0 分析方法
4.1 非破坏性分析
外观确 认
案例
11/26/2020
15
4.0 分析方法
4.2 半破坏性分析
确认失效机理
案例
11/26/2020
16
4.0 分析方法
4.2 半破坏性分析
修复参数,提取能够 使其参数回复的条件,
•
重于泰山,轻于鸿毛。07:54:2107:54:2 107:54 Thursda y, November 26, 2020
•
不可麻痹大意,要防微杜渐。20.11.26 20.11.2 607:54: 2107:5 4:21November 26, 2020
•
加强自身建设,增强个人的休养。202 0年11 月26日 上午7时 54分20 .11.262 0.11.26
外观鉴定
结构特征鉴定
形状 颜色
大小 机械结构
位置 物理特性
11/26/2020
20
5.0 主要程序
失效机理分析
参考相关标准 综合分析 还原现象 观测失效样品 实验对比
提交分析报告
任务来源 分析过程
背景描述
分析结果
记录和图片 综合评审
分析实质原因 提出纠正措施
11/26/2020
工艺
设计结构 材料
测试方法 使用条件 质量控制
……
1.0 基本概念
1.3 什么是“失效机理”? --- 失效机理是指导致器件失效的物理、化学、电和 机械应力的过程,通俗地讲就是怎么坏的。 常见的失效机理有:
表面劣化
Cell被划伤
材料缺陷
Cell来料超厚
体内劣化
cell foil分层 swelling
设计缺陷
金手指偏位
零部件损坏
Breaker 破损
•
抓住每一次机会不能轻易流失,这样 我们才 能真正 强大。2 0.11.26 2020年 11月26 日星期 四7时5 4分21 秒20.11. 26
谢谢大家!
11/26/2020
8
2.0 研究对象和要求
案例分析:
跌落后电池头 部出现凹陷
失效分析
注胶量不足
失效模式
11/26/2020
失效机理
9
3.0 意义和价值
3.1 为提高产品可靠性提供科学依据。
通过失效分析,得到失效模式,准确判定失效机理, 为产品可靠性设计、材料选型、工艺制造和使用维护提 供科学依据,从而提高产品可靠性。
即失效\故障\损坏\失败分析
11/26/2020
2
1.0 基本概念
1.2 什么是“失效模式” ? --- 失效模式是指由失效机理所引起的可观察到的物理 或化学变化(如开路、短路或器件参数的变化)。
通俗讲就是失效的表现形式,失效导致的结果。 失效模式通常从技术角度可按失效机制、失效零件 类型、引起失效的工艺环节等分类。从质量管理和可靠性 工程角度可按产品使用过程分类。 按失效表象可以分为外观、结构以及功能参数失效。
先检查整体外观和功能, 再检查局部外观与功能。
先简单再复杂
先做简单的项目分析,再 进行复杂的项目分析。
先静态后动态 先恢复再分解
11/26/2020
先做空载和常温等常规测 试,再模拟使用条件测试。
先进行模拟实验,尽力恢 复失效功能或参数,再做 分层解剖检查分析。
28
7.0 注意事项
失效样品有时是唯一的,十分宝贵。 在分析时应严格按程序进行。样品 的保管、运输、拆装、分解等过程 要注意ESD\EOS\机械应力\温湿度环 境不当损伤样品,造成新的失效, 从而无法找到原来失效的真正原因。
➢ ……
11/26/2020
7
2.0 研究对象和要求
2.2 失效分析层次要求
任一产品或系统的构成都是有层次的,失效原因也 具有层次性,如系统-单机-部件(组件)-零件(元 件)-材料。
上一层次的失效原因即是下一层次的失效现象。 凭我们现有资源和技术能力,结合产品特性,失效 分析对内适宜以器件为单元建立失效模式。分析机理达到零 件(如cell\IC\PCB\FUSE等)层次即可。对外则因需求而异。
11/26/2020
32
•
踏实,奋斗,坚持,专业,努力成就 未来。2 0.11.26 20.11.2 6Thurs day, November 26, 2020
•
弄虚作假要不得,踏实肯干第一名。0 7:54:21 07:54:2 107:54 11/26/2 020 7:54:21 AM
•
安全象只弓,不拉它就松,要想保安 全,常 把弓弦 绷。20. 11.2607 :54:210 7:54Nov-2026-Nov-20
先了解准确、详尽的使用 信息,通常需要使用方配 合。
根据失效现象,制定方案 后再进行分析。检查分析 过程中可以修订分析方案。
失效分析的基本原则。先 确认所有无损检验完成后, 在进行半破坏和破坏分析。
先观察后测试
先进行外观检查再做参数 测试和功能测试。
11/26/2020
27
7.0 注意事项
先宏观再微观
3 11/26/2020
1.0 基本概念
结合行业特征,归纳常见的失效模式有:
A、外观失效
Label气泡、脏污 B、功能参数失效
……
无电压输出 IR out spec
Swelling
Charger/discharge capacity not enough
C、结构失效 超厚 … …
4 11/26/2020
21
6.0 操作流程-1 *这个流程还在完善
11/26/2020
22
6.0 操作流程-2
11/26/2020
23
6.0 操作流程-3
11/26/2020
24
6.0 操作流程-4
11/26/2020
25
6.0 操作流程-6
11/26/2020
上传到OA存档/供查阅
26
7.0 注意事项
先了解再鉴定 先方案再操作 先无损再破坏
使用不当
使用环境温度60℃
11/26/2020
5
1.0 基本概念
1.4 结合我们的产品例举常见的失效模式 和失效机理
失效模式
失效机理
11/26/2020
6
2.0 研究对象和要求
2.1 需要做失效分析的对象
➢ 现场使用的失效样品(客诉样品) ➢ 可靠性试验失效样品 ➢ 生产筛选失效样品(特大异常样品)
备很熟悉,甚至还有测试设备要玩的转。 6. 做过测试,对光电参数方面分析有深入理解。
11/26/2020
31
8.0 FA工程师因该具备的能力
7. 搞过项目管理,会引导团队达成目标。 8. 可靠性有投入,能做风险验证和拍板,对产品
的发货负责。 9. 了解器件应用、对应用分析有一定的经验。 10. 较强的推动能力、勇于挑战。
11/26/2020
8.0 FA工程师因该具备的能力
1. 要懂基础的物理科学,对物理对电路都要有 一定的基础,否则无法解释一些本质现象, 思路也不宽。
2. 要熟悉产品封装工艺,这个是失效分析的基 础,不然没法给结论。
11/26/2020
30
8.0 FA工程师因该具备的能力
3. 要懂电路和机械装配图。 4. 熟悉材料科学,会分析各种材料的相关问题。 5. 要对业界的所有失效分析设备,材料分析设
•
追求卓越,让自己更好,向上而生。2 020年1 1月26 日星期 四上午7 时54分 21秒07 :54:212 0.11.26
•
严格把控质量关,让生产更加有保障 。2020 年11月 上午7时 54分20 .11.260 7:54November 26, 2020
•
重规矩,严要求,少危险。2020年11 月26日 星期四7 时54分 21秒07 :54:212 6 November 2020
11/26/2020
12
3.0 意义和价值
3.3 通过建立反馈系统,共享技术信息,推动技 术革新。
失效分析的反馈系统可与技术开发和市场部门、甚至 与国家的质量管理部门、可靠性研究中心、数据中心及数 据交换网相结合。转化为各类技术文献,减少失效发生几 率,增加经济效益。
11/26/2020
13
4.0 分析方法
从而总结失效机理
案例
11/26/2020
17
4.0 分析方法
4.3 破坏性分析 排除A处的因素
案例
11/26/2020
18
案例
4.0 分析方法
4.3 破坏性分析