第1章 凝固过程的传热
2.凝固过程传热

1)凝固速度对铸件凝固组织、性能与凝固缺陷的产生有重要影响,试分析可以通过哪些工艺措施来改变或控制凝固速度?解:①改变铸件的浇注温度、浇铸方式与浇铸速度;②选用适当的铸型材料和起始(预热)温度;③在铸型中适当布置冷铁、冒口与浇口;④在铸型型腔内表面涂敷适当厚度与性能的涂料。
2)影响铸件凝固方式的因素有哪些?答:(1)金属本身的凝固特点(凝固温度范围):金属或合金的成分,液相线与固相线的凝固动态曲线;(2)外界条件:决定凝固体的断面温度分布的因素。
3液体的粘度:粘度越大,表示液体越粘稠,4 液体层间的内摩擦力越大,相对运动也越困难,原子无法迁移排成晶体。
2 )液体的冷却速度:冷却速度越大,阻止金属材料中原子的迁移。
(1)合金凝固温度范围的影响合金的液相线和固相交叉在一起,或间距很小,则金属趋于逐层凝固;如两条相线之间的距离很大,则趋于糊状凝固;如两条相线间距离较小,则趋于中间凝固方式。
(2)铸件温度梯度的影响增大温度梯度,可以使合金的凝固方式向逐层凝固转化;反之,铸件的凝固方式向糊状凝固转化。
3)何为凝固动态曲线?有何意义?答:(1)凝固动态曲线:根据凝固体断面上实际测得的温度随时间变化曲线上(T-t),在同一时间坐标下,制作凝固体断面上不同位置与时间框图,将实际测得的(T-t)曲线上确定的温度点投影到凝固体断面上不同位置与时间的框图中,把不同时间、不同位置的同一温度点(液相温度、固相温度)连接起来,即得到金属凝固动态曲线;即在凝固体断面上,不同时间、不同位置达到同一温度的连线。
(2)动态曲线意义:凝固动态曲线用于判断金属在凝固过程中两相区(凝固区)的宽窄;由两相区(凝固区)的宽窄判断凝固断面的凝固方式。
4)凝固方式分为几种?对铸件质量有何影响?答:(1)凝固方式分为逐层凝固方式、体积凝固方式、中间凝固方式三种;(2)对铸件质量的影响:○1.逐层凝固方式:流动性能好,容易获得健全的凝固体;液体补缩好,凝固体的组织致密,形成集中缩孔的倾向大;热裂倾向小;气孔倾向小,应力大,宏观偏析严重;○2.体积凝固方式:流动性能不好,不容易获得健全的凝固体;液体补缩不好,凝固体的组织不致密,形成集中缩孔的倾向小;热裂倾向大,气孔倾向大;应力小,宏观偏析不严重;○3.中间凝固方式:介于逐层凝固与体积凝固方式二者之间。
液态金属凝固过程中的传热与传质
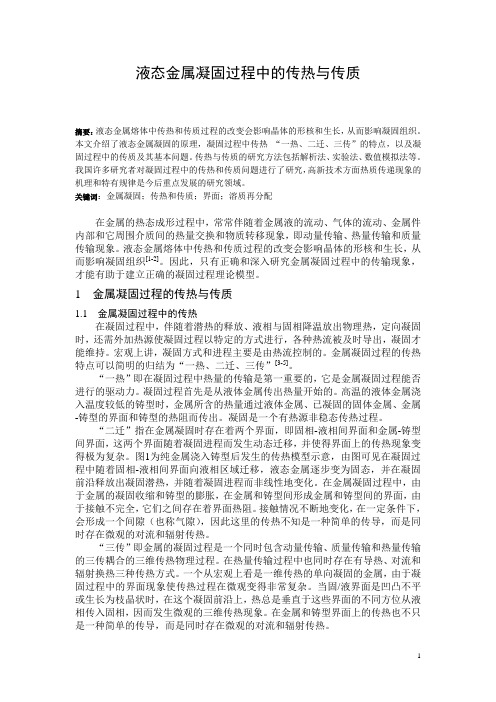
液态金属凝固过程中的传热与传质摘要:液态金属熔体中传热和传质过程的改变会影响晶体的形核和生长,从而影响凝固组织。
本文介绍了液态金属凝固的原理,凝固过程中传热“一热、二迁、三传”的特点,以及凝固过程中的传质及其基本问题。
传热与传质的研究方法包括解析法、实验法、数值模拟法等。
我国许多研究者对凝固过程中的传热和传质问题进行了研究,高新技术方面热质传递现象的机理和特有规律是今后重点发展的研究领域。
关键词:金属凝固;传热和传质;界面;溶质再分配在金属的热态成形过程中,常常伴随着金属液的流动、气体的流动、金属件内部和它周围介质间的热量交换和物质转移现象,即动量传输、热量传输和质量传输现象。
液态金属熔体中传热和传质过程的改变会影响晶体的形核和生长,从而影响凝固组织[1-2]。
因此,只有正确和深入研究金属凝固过程中的传输现象,才能有助于建立正确的凝固过程理论模型。
1 金属凝固过程的传热与传质1.1 金属凝固过程中的传热在凝固过程中,伴随着潜热的释放、液相与固相降温放出物理热,定向凝固时,还需外加热源使凝固过程以特定的方式进行,各种热流被及时导出,凝固才能维持。
宏观上讲,凝固方式和进程主要是由热流控制的。
金属凝固过程的传热特点可以简明的归结为“一热、二迁、三传”[3-5]。
“一热”即在凝固过程中热量的传输是第一重要的,它是金属凝固过程能否进行的驱动力。
凝固过程首先是从液体金属传出热量开始的。
高温的液体金属浇入温度较低的铸型时,金属所含的热量通过液体金属、已凝固的固体金属、金属-铸型的界面和铸型的热阻而传出。
凝固是一个有热源非稳态传热过程。
“二迁”指在金属凝固时存在着两个界面,即固相-液相间界面和金属-铸型间界面,这两个界面随着凝固进程而发生动态迁移,并使得界面上的传热现象变得极为复杂。
图1为纯金属浇入铸型后发生的传热模型示意,由图可见在凝固过程中随着固相-液相间界面向液相区域迁移,液态金属逐步变为固态,并在凝固前沿释放出凝固潜热,并随着凝固进程而非线性地变化。
传输原理第十二章 材料加工中的热量传输
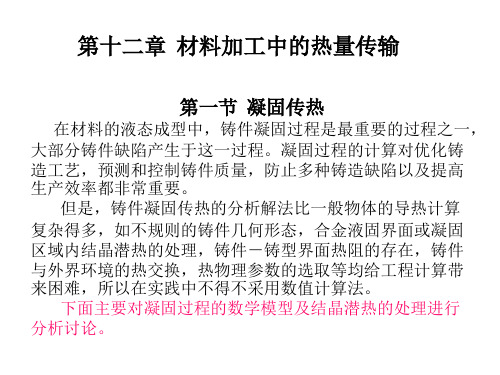
第三节 焊接热过程计算
熔焊时,被焊金属在热源的作用下被加热并发生局部熔化, 当热源离开后,金属开始冷却。这种加热和冷却的过程被称为 焊接热过程。它是影响焊接质量和生产率的主要因素之一。对 焊接热过程进行准确的计算和测定是进行焊接冶金分析、焊接 应力应变分析和对焊接热过程进行控制的前提。然而,焊接过 程的传热问题却十分复杂,给研究工作带来许多困难,具体体 现在以下四个方面:①加热过程的局部性,②加热的瞬时性, ③焊接热源是移动的;④焊接传热是复合传热过程。
进行求解.并且假定工件的初始温度均匀为0℃,同时不考 虑表面散热问题。
第三节 焊接热过程计算
把上述的具体条件代入后所求得的特解为:
式中 Q—热源在瞬时提供给工件的热能; R—距热源的坐标距离,R=(x2+y2+z2)1/2 t—传热时间 a—材质的热扩散率
由上式可以看出,在这种情况下所形成的温度场,是以R为半 径的一个个等温球面。但在熔焊的条件下,热源传给焊件的 热能是通过焊件表面进行的,故常称为半无限体。这时应对 上式进行修正,即认为全部的热能被半无限体所获得,则
通解为:
在铸件一侧,当x=0时,T=Ti,x=∞时,T=Tp 。分别代 入上式可得: A=Ti,B=Tp-Ti
在铸型一侧,当x=∞时, T=T0 ,x=0时,T=Ti。分别代 人上式可得: A=Ai,B=Ti-T0
TM、Tm铸件和铸型温度,αM、 αm铸件和铸型的热扩散率
第一节 凝固传热
在界面上应有: 因为
第一节 凝固传热
由于合金材质不同,潜热释放的形式也不同,在数值计算中 也应采取不同的潜热处理方法。 (一)温度补偿法 纯金属或共晶合金都是在同一温度上发生凝固,也是在该温 度上将所有的凝固潜热释放完毕。用有限差分对这类合金的 铸件进行计算时,应把握住其恒温凝固的特点,为此需做如 下处理: 铸件内任一单元i,设其初始温度高于凝固点Ts。计算时要 满足条件为: 即将潜热的释放折合成等效温度区间ΔT*内显热的释放,并 保持计算温度为常数Ts ,只有当所有的补偿温度之和大于或 等于等效温度区间ΔT*时才意味着凝固结束,温度才可能继 续下降。
第1章 凝固过程的传热

和铸件的凝固动态曲线。
第三节 凝固区域的结构 和液态金属的凝固方式
一、凝固动态曲线
图6为凝固动态曲线,它是根据直接测量的温度— 时间曲线绘
制的。首先在图6a上给出合金的液相线tl和固相线温度ts,把二 直线与温度—时间相交的各点分别标注在图6b的(x/R ,τ)坐标 系上,再将各点连接起来,即得凝固动态曲线。 纵坐标x是铸件表面向中心方向的距离,R是铸件壁厚之半或圆 柱体和球体的半径。由于凝固是从铸件壁两侧同时向中心进行, 所以当x / R=1时表示已凝固至铸件中心。 图6c为根据凝固动态曲线绘制的自测温度开始后2分20秒的凝固 状况。根据凝固动态曲线可以获得任一时刻的凝固状态。
如果合金(图8b)。的结晶温度范围很小,或断面温度梯度
很大时,铸件断面的凝固区域则很窄,也属于逐层凝固方式
纯金属或 共晶合金
合金
体积凝固方式或称糊状凝固方式
如果因铸件断面温度场较平坦(图9a),或合金的结晶温度范 围很宽(图9b),铸件凝固的某一段时间内,其凝固区域几乎 贯穿整个铸件断面时,则在凝固区域里既有已结晶的晶体,也 有未凝固的液体。
的结晶温度范围很小或断面温度梯度很大时铸件断面的凝固区域则很窄也属于逐层凝固方式纯金属或共晶合金合金体积凝固方式或称糊状凝固方式如果因铸件断面温度场较平坦图9a或合金的结晶温度范围很宽图9b铸件凝固的某一段时间内其凝固区域几乎贯穿整个铸件断面时则在凝固区域里既有已结晶的晶体也有未凝固的液体
内容简介
(6) 激冷法(液淬法)
方法:将多个一定尺寸的试样,隔一定时间淬入水中,然后在金相显微镜 下观察其凝固组织 。 优点:既可得到某一时刻凝固区域的大小,又可得到组织、界面形貌。 缺点:固相在液淬时也会发生异常相变。在液淬过程中,凝固还在进行。 不能研究大体积金属的凝固过程。
凝固过程中的传热

一、凝固过程中的传热 二、凝固过程中的传质 三、凝固过程中的液体流动
1
一、凝固过程中的传热
在凝固过程中,伴随着潜热的释放、液相与固相降温放出物理热,定向凝 固时,还需外加热源使凝固过程以特定的方式进行,各种热流被及时导 出,凝固才能维持。 宏观上讲,凝固方式和进程主要是由热流控制的。
10
4. 温度场与凝固过程的分析 铸件凝固时间的确定:
对温度场研究的目的是进行凝固过程分析。 以无限大平板铸件为例,由铸件放热与铸型吸热相等 Q1=Q2,可得
铸件凝固层厚度:? ? K ? , K为常数
Chvorinov 根据大量实验结果的分析,创造性地引入铸件模数的概念,
得出了著名的平方根定律: M ? K ? c
7
(1)解析法
直接从传热微分方程出发,在给定的
定解条件下,求出温度场的解析解
,实际条件下很少、只有引入许多假设
的条件下。
大平板铸件:
图中:S、L、M分别表示固相、液相和铸型的参数, Tk为凝固界面温度
根据界面上的热平衡:
?
S
? ? ?
?TS ?x
? ? ?x??
?
?
L
? ? ?
? TL ?x
? ? ?x??
边界条件相似 k s
按傅里叶导热微分方程可得相似条件:
k? k?
? ,? ,
即: l , 2
?
? ?,, ,,
l ,,2
?
??? ?
??
l2
k
2 l
Fo= ? ?
l2
?1
----定义为傅里叶数是
两个过程相似的必要条件是 Fo相等。
金属凝固原理复习大纲

金属凝固原理复习大纲绪论1、凝固定义宏观上:物质从液态转变成固态的过程.微观上:激烈运动的液体原子回复到规则排列的过程。
2、液态金属凝固的实质:原子由近程有序状态过渡为长程有序状态的过程液态金属的结构特征:“近程有序”、“远程无序”组成:液态金属是由游动的原子团、空穴或裂纹构成3、液态金属的性质:粘度和表面张力粘度的物理意义:单位接触面积,单位速度梯度下两层液体间的内摩擦力粘度的本质上是原子间的结合力影响液体金属粘度的主要因素是:化学成分、温度和夹杂物表面张力的物理意义:作用于表面单位长度上与表面相切的力,单位N/m影响液体金属表面张力的主要因素是:熔点、温度和溶质元素。
取决于质点间的作用力4、液体结构的特性:近程有序和远程无序晶体:凡是原子在空间呈规则的周期性重复排列的物质称为晶体。
单晶体:在晶体中所有原子排列位向相同者称为单晶体多晶体:大多数金属通常是由位向不同的小单晶(晶粒)组成,属于多晶体。
吸附是液体或气体中某种物质在相界面上产生浓度增高或降低的现象。
金属从液态过渡为固体晶态的转变称为一次结晶金属从一种固态过渡为另一种固体晶态的转变称为二次结晶当向溶液中加入某种溶质后,使溶液表面自由能降低,并且表面层溶质的浓度大于溶液内部深度,则称该溶质为表面活性物质(或表面活性剂),这样的吸附称为正吸附.反之,如果加入溶质后,使溶液的表面自由能升高,并且表面层的溶质浓度小于液体内部的浓度,则称该溶质为非表面活性物质(或非表面活性剂),这样的吸附为负吸附第一章凝固过程的传热1、凝固过程的传热特点:“一热、二迁、三传”“一热”指热量的传输是第一重要;“二迁”指存在两个界面,即固-液相间界面和金属-铸型间界面。
“三传”指动量传输、质量传输和热量传输的三传耦合的三维热物理过程。
2、金属型特点:具有很高的导热性能;非金属型铸造特点:与金属相比具有非常小热导率,故凝固速度主要取决于铸型的传热性能。
铸型外表面温度变化不大,故可把铸型看成是半无限厚的。
液态金属凝固中的传热、传质及液体流动

t R2 K2
K为凝固系数。
在实际的生产中,通常不需计算出铸件的凝固时间, 只需通过比较它们的相对厚度或模数就可制定生产工艺。
铸件温度场及凝固时间的精确计算——计算机数值模拟
4、焊接温度场
准稳定温度场的概念
图4-4 “厚板”表面运动点热源的温度场
图4-5 薄板焊接时的温度场分布
(图b是否有误?)
3.数值计算法 数值计算法是把所研究的物体从时间和位置上分割成许多小
单元,对于这些小单元用差分方程式近似地代替微分方程式, 给出初始条件和边界条件,逐个计算各单元温度的一种方法。 即使铸件形状很复杂,也只是计算式和程序烦杂而已,在原则 上都是可以计算的。
数值计算法比其它近似计算法准确性高,当单元选得足够小
无限长圆棒试样 测温及结果处理
2.铸件的两种凝固方式
图4-3 合金成分和温度梯度对凝固方式的影响 a)、b)为层状凝固,c)、d)为体积凝固 影响因素:(1)化学成分(液-固相线距离)
(2)温度梯度
层状凝固过程 层状凝固缩孔特点
体积凝固过程 体积凝固方式的缩松
3、铸件凝固时间计算
——与铸件厚度及温度场(凝固速度)相关
1)铸型的蓄热系数 铸型的蓄热系数越大,对铸 件的冷却能力就越大,铸件是的温度梯度就越大。 铸型的导热系数越大,能把铸型内表面吸收的热迅 速传至外表面,使铸型内表面保持强的吸热能力, 铸件内的温度梯度也就大。如金属型、涂料等的影 响。
2)铸型的预热温度的影响 铸型预热温度越高,对铸件的冷却作用就越小,铸件断面上的温度梯度也 就越小。 3.浇注条件的影响 过热热量加热了铸型,所以过热度越大,相当于铸型预热温度越高。铸件 内的温度场越平坦。 4.铸件结构的影响 1)铸件的壁厚 厚壁铸件比薄壁铸件含有更多的热量,当凝固层向中心推 进时,把铸型加热到更高温度,所以铸件内温度场较平坦。 2)铸件的形状 铸件的棱角和弯曲表面,与平面的散热条件不同,向外凸 出的部分,散出的热量为较大何种的铸型所吸收,铸件的冷速较大,如果铸 件内凹的表面,则相反。
【材料成型原理--铸造】第4章 液态金属凝固过程中的传热与传质
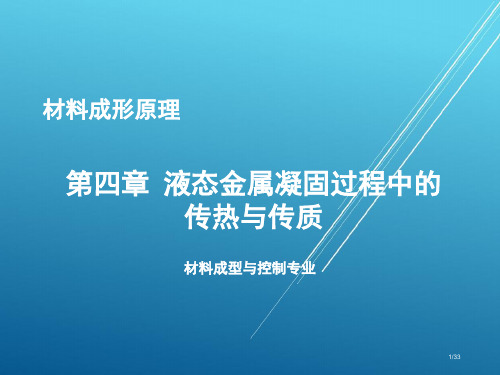
• 2、模型建立
• 温度TL时,开始凝固: • 固 度k相0C:0。百分数dfS;溶质浓
• 液相:溶质浓度几乎不变, 为C0。 • 温度降到T*时,
• 固 数f相S;:溶质浓度C*S;百分
•
液相:溶质浓 数fL。
度
C*L;百
分
28/33
• 当dfSf)S界,溶面这质处些浓固溶度相质增增将加加均d百C匀*L分扩,量散则为到:d整fS个时液,相排中出,溶使质剩量余为液(相C*(L-C1*S-) • (C*L-C*S)dfS=(1-fS)dC*L
30/33
31/33
32/33
33/33
34/33
35/33
• (二)固相无扩散,液相只有有限扩散(无对流或搅拌) 的溶质再分配
• 1、假设: • (1)合金单相凝固; • (2)固相无扩散(接近实际情况); • (3)液相有限扩散(无对流、搅拌); • (4)固液相线为直线,k0为常数; • (5)试样很长,单向放热,平面推进。
• 该两式为平衡凝固时溶质再分配的数学模型。
19/33
CS
1
C0k0 f S (1 k0 )
CL
k0
C0 f L (1 k0 )
• 3、验证 (1)开始凝固时 • 初始条件:fS0,fL1 • 则:CS=k0C0;CL=C0 (2)凝固结束时 • 初始条件:fS1,fL0 • 则:CS=C0;CL=C0/k0
凝固时间与凝固层厚度的平方成正比。
计算结果与实际接近。
适合大平板和结晶间隔小的铸件。
14/33
• 3、“折算厚度”法则
R2 t
K2
R V1 为铸件折算厚度或铸件模数。
A1
- 1、下载文档前请自行甄别文档内容的完整性,平台不提供额外的编辑、内容补充、找答案等附加服务。
- 2、"仅部分预览"的文档,不可在线预览部分如存在完整性等问题,可反馈申请退款(可完整预览的文档不适用该条件!)。
- 3、如文档侵犯您的权益,请联系客服反馈,我们会尽快为您处理(人工客服工作时间:9:00-18:30)。
即铸件和铸型的温度场数学模型并加以求解。
凝固是一个相当复杂的过程,涉及到传热、传质、相变等各
种复杂的初始和边界条件。要建立一个符合实际情况的微分方
程式很困难,即使建立了微分方程式也未必能够求解。因此, 用数学分析法研究凝固过程时,必须对过程进行合理的简化。
(2) 数学解析法
理论根据:压力恒定时,金属状态是温度的函数。 方法:建立数学解析式直接求解。是用数值计算法分析热流 传递规律,预测凝固过程。 优点:能得出温度场、凝固区域及变化规律。 缺点:计算复杂,只对形状简单的铸坯有效;需要做大量假 设,影响其精确性;需要有关热物性参数;难以直观反映固-液
界面的形貌。
第一章 凝固过程的传热
第一节 凝固过程的传热特点 第二节 非金属型、金属型铸造的凝固传热
第三节 凝固区域的结构和液态金属的凝固方式
第四节 凝固方式与铸件宏观组织
第一节 凝固过程的传热特点
合金从液态转变成固态的过程,称为一次结晶或凝固。
一次结晶和“凝固”这两个术语虽然指的是同一个状态变化
过程,但它们的含意是有区别的。
一次结晶是从物理化学观点出发,研究液态金属的生核、长
大、结晶组织的形成规律。 凝固则是从传热学观点出发,研究铸件和铸型的传热过程、 铸件断面上凝固区域的变化规律、凝固方式与铸件质量的关 系、凝固缺陷形成机制等。
凝固过程的传热特点:“一热、二迁、三传”
“一热”指热量的传输是第一重要;
“二迁”指存在两个界面,即固-液相间界 面和金属-铸型间界面。 “三传”动量传输、质量传输和热量传输的 三传耦合的三维热物理过程。
二、凝固区域的结构
铸件在凝固过程中,除纯
Ⅲ区 Ⅱ区 Ⅰ区
金属和共晶成分合金外,断面
上一般都存在三个区域,即固 相区,凝固区和液相区。铸件 的质量与凝固区域有密切的关 系。
图7是凝固区域结构示意图,
其中凝固区域由倾出边界和补 缩边界又分割成三个区域。
Ⅰ区(从液相边界到倾出边界)。这个区的特征为固相处 于悬浮状态而未连成一片,液相可以自由移动,用倾出法做试 验时,固体能够随液态金属一起被倾出。 Ⅱ区(从倾出边界到补缩边界),这个区的特征为固相已 经连成骨架,但液相还能在固相骨架间自由移动,这时某一部 位的体积收缩能够得到其它部位液体的补充,而不至于产生缩 孔或缩松。 Ⅲ区(从补缩边界到固相边界)这个区的特征为固相不但 连成骨架而且已经充分长大,存在于固相间隙中的少量液体被 分割成一个个互不沟通的小“溶池”。这时液体再发生凝固收 缩,不能得到其它液体的补缩。 根据以上的分析可以看出,对铸坯质量影响最大的是Ⅲ区 的宽度。可以推断凝固区域越宽,则Ⅲ区的宽度也就越宽。
边界元法等,这些方法各有特点。
以有限差分法为例,介绍如下:
微分方程转变为差分方程
向前差分
网格傅立叶数
温度对时间向后差分
凝固潜热
铸件-铸型界面模型
边界条件
初始条件
轴对称问题的差分方程
单元热平衡法建Βιβλιοθήκη 差分方程3、温度场的实测法
铸件温度场实测法的示意图如图4所示。 将一组热电偶的热端固定在型腔中的不同位置,利用多点自 动记录电子电位计作为温度测量和记录装置,即可记录自金属液 注入型腔起至任意时刻铸件断面上各测温点的温度-时间曲线(图 5a)。根据该曲线可绘制出铸件断面上不同时刻的温度场(图5b)
和铸件的凝固动态曲线。
第三节 凝固区域的结构 和液态金属的凝固方式
一、凝固动态曲线
图6为凝固动态曲线,它是根据直接测量的温度— 时间曲线绘
制的。首先在图6a上给出合金的液相线tl和固相线温度ts,把二 直线与温度—时间相交的各点分别标注在图6b的(x/R ,τ)坐标 系上,再将各点连接起来,即得凝固动态曲线。 纵坐标x是铸件表面向中心方向的距离,R是铸件壁厚之半或圆 柱体和球体的半径。由于凝固是从铸件壁两侧同时向中心进行, 所以当x / R=1时表示已凝固至铸件中心。 图6c为根据凝固动态曲线绘制的自测温度开始后2分20秒的凝固 状况。根据凝固动态曲线可以获得任一时刻的凝固状态。
(6) 激冷法(液淬法)
方法:将多个一定尺寸的试样,隔一定时间淬入水中,然后在金相显微镜 下观察其凝固组织 。 优点:既可得到某一时刻凝固区域的大小,又可得到组织、界面形貌。 缺点:固相在液淬时也会发生异常相变。在液淬过程中,凝固还在进行。 不能研究大体积金属的凝固过程。
(7) 模拟物质法
方法:用蛋白质、盐溶液等模拟金属凝固过程,直接观察。 优点:信息量大,研究方便。 缺点:模拟物质是否能全面真实反映金属凝固过程还需要认证。
金属凝固方式与金属化学成分及外部条件的 关系如图11所示:
第四节 凝固方式与铸件宏观组织
从凝固区域的结构分析可知,铸件的致密性 和健全性与合金的凝固方式密切相关,而影
响凝固方式的因素为结晶温度范围和铸件断
面的温度梯度。
一、化学成分、结晶温度范围与铸件质量的关系
化学成分决定了合金结晶的温度范围。纯金属和共晶成
三、界面温度Ti
四、凝固系数φ
五、虚拟凝固层厚度S0
换热系数hi ,通过实验测得:
s,t
β
hi
s0
φ
Ti
Ts
Tm
2、 数值计算法
计算机的出现为解决数值计算法计算量大的问题提供了有力 的工具。因此近十年来,凝固过程的数值模拟有了很大的进展。 金属凝固过程传热、传质及流动的耦合模拟,已经能够作为 预测和控制铸件质量的依据。 导热微分方程的数值解法主要有有限差分法、有限单元法、
(8) 彩色金相法
方法:利用凝固层推进过程中位置不同,成分也不同的特点,用彩色金相 对已经凝固的合金做特种处理,可得到其凝固过程的动态描述。 优点:可视形貌 。 缺点:由于找不到合适的处理方法,不总是有效。
第二节
非金属型、金属型铸造的凝固传热
1.数学解析法(mathematical analysis method)
(3) 数值模拟法
方法:将数学解析方程离散为差分方程,进行求解。近年
来随着计算机的普及而发展较快。 优点:能得出温度场、凝固区域及其变化规律。相对于数 学解析法,可解更复杂的函数式。 缺点:需要做大量假设,影响其精确性。需要有关热物性 参数。难以直观反映固-液界面形貌。
(4) 多点热分析法——凝固曲线法
分合金在凝固时,由于结晶温度范围是零,因此没有液固共存
的凝固区,以逐层方式凝固,其凝固前沿直接与液态金属接触。
当液态凝固成为固体而发生体积收缩时,可以不断地得到液体 的补充,所以产生分散性缩松的倾向性很小,而是在铸件最后
三、凝固方式
一般将金属的凝固方式分为三种类型; 逐层凝固方式; 体积凝固方式或称糊状凝固方式; 中间凝固方式; 凝固方式取决于凝固区域的宽度,而凝固区域的宽 度取决于合金的结晶温度范围和冷却强度。
逐层凝固方式
图8a为恒温下结晶的纯金属或共晶成分合金(图8a)。某瞬 间的凝固情况。tC是结晶温度,T1和T2 是铸件断面上两个不 同时刻的温度场。从图中可观察到,恒温下结晶的金属,在凝 固过程中其铸件断面上的凝固区域宽度为零。断面上的固体和 液体由一条界线(凝固前沿)清楚地分开。随着温度的下降, 固体层不断加厚,逐步达到铸件中心。
内容提要
第一章:凝固过程的传热 第二章:凝固热力学 第三章:凝固动力学 第四章:单相合金的凝固
第五章:多相合金凝固
第六章:金属凝固组织的控制 第七章:凝固过程中液态金属的流动 第八章:金属中的气体与气孔 第九章:缩孔和缩松
第十章:铸造应力
参考书
1. 金属凝固原理(第2版),胡汉起主编,北京:机械工业出版社,2000 2. Merton C. Flemings, Solidification processing, New York : McGraw-Hill, 1974. 凝固过程 (美) 弗莱明斯 著 关玉龙 等译,北京 : 冶金工业出版社, 1981 3. Fundamentals of solidification / W. Kurz, D.J. Fisher. Rockport, MA : Trans Tech Pub., 1986. 库尔. 费希尔 著 毛协民 等译,凝固原理,西安 : 西北工业大学出版社, 1987 4. I. Minkoff., Solidification and cast structure, Chichester : Wiley, c1986. 5. 周尧和、胡壮麒、介万奇编著,凝固技术,北京 : 机械工业出版社, 1998 6. (日) 大野笃美 著 唐彦斌, 张正德,金属凝固学,北京 : 机械工业出版社, 1983 7. Davies, G. J. , Solidification and casting , London : Applied Science Publishers Ltd., 1973. (英)戴维斯 著 陈邦迪, 舒震 译,凝固与铸造,北京 : 机械工业出版社, 1981 8.Tiller, William A., The science of crystallization : microscopic interfacial phenomena, Cambridge [England] : Cambridge University Press, 1991.
方法:实测不同部位铸坯温度随时间变化的曲线,据 此得到凝固动态曲线、温度场等。 优点:结果可靠。 缺点:不能反映固-液界面组织、界面形貌。有些情况 下实测困难。
(5) X-射线衍射法
方法:用X-射线直接观察、记录凝固过程。 优点:将不透明的金属透视,可直接观察其形貌。 缺点:只有固、液两相对X-射线的减弱系数有较大差 别时才有效。对金属厚度有限制。
如果合金(图8b)。的结晶温度范围很小,或断面温度梯度