冷镦挤变形工艺冷镦工艺与模具设计24页PPT
合集下载
冷镦知识和工艺讲解课件
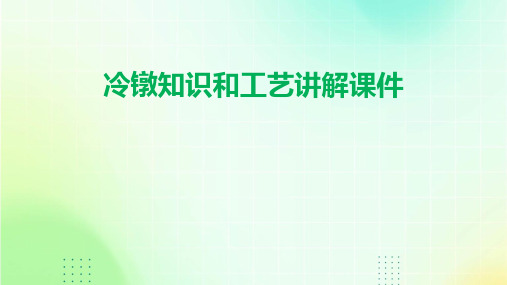
毛坯尺寸
根据产品需求,确定毛坯的尺寸 和形状,确保满足成型要求。
毛坯表面处理
对毛坯进行清洗、除锈等表面处 理,以提高成型质量和模具寿命
。
模具选择与安装
模具类型
根据产品形状和尺寸选择合适的模具类型,如开 式、闭式等。
模具设计
根据产品要求,进行模具结构设计,确保成型稳 定、生产效率高。
模具安装
将选定的模具安装到冷镦机上,确保安装位置准 确、稳定。
冷镦知识和工艺讲解课件
目录
• 冷镦工艺简介 • 冷镦设备与工具 • 冷镦材料 • 冷镦工艺流程 • 冷镦工艺质量控制 • 冷镦工艺的发展趋势与展望
01
冷镦工艺简介
冷镦工艺定义
01
冷镦工艺是一种金属塑性加工技 术,利用金属的塑性变形来制造 螺栓、螺母等紧固件。
02
在冷镦过程中,金属材料在模具 的挤压下发生塑性变形,从而获 得所需形状和尺寸的零件。
根据产品用途选择具有相应特性的材料以满 足使用要求。
考虑成本与性能平衡
在满足性能要求的前提下,尽量选择成本较 低的材料。
考虑工艺适应性
选择易于加工和处理的材料以提高生产效率 和降低成本。
符合环保要求
优先选择可回收、可再利用的材料,减少对 环境的污染。
04
冷镦工艺流程
毛坯准备
毛坯材料
选择适合冷镦工艺的材料,如低 碳钢、不锈钢等。
冷镦工艺的特点
01
02
03
高效率
冷镦工艺可以实现连续、 自动化生产,提高生产效 率。
优质产品
冷镦工艺可以获得高精度 、高表面质量的紧固件。
节能环保
冷镦工艺采用金属塑性加 工技术,相比切削加工可 以节约能源和减少废弃物 排放。
冷镦工艺与模具设计

2. 变形力的简单计算
冷镦加工与冷镦变形力有着密切的关系。冷镦变形力是确定工艺参数、 模具设计、设备设计和选择设备的重要依据。在正常生产中,一般不需经 常进行变形力的计算,但对于非标零件与几何形状复杂零件加工时,为便 于合理地选用设备、设计工艺和模具等,必要时需要进行变形力计算,所 以必须掌握变形力的计算方法。
形过程中,随着变形的增大,由于冷作硬化
变形抗力 (N/mm2)
作用使金属的硬度和强度随之增大, 变形抗力也大大增加,而塑性却有所降 低,这将给后道工序带来变形的困难。
电工纯铁
金属材料冷作硬化后实际变形抗力如
图1.1-1所示,材料的含碳量越高,其变
形抗力越大。所以,在冷加工过程中需
适当增加中间热处理工序,以消除冷作硬 化和内应力。
4.冷镦变形力计算方法 F=KσT A 式种: F — 冷镦变形力 (MPa)
K — 镦锻头部的形状系数, 一般螺钉、螺栓取 2~2.4 σT — 考虑到冷作硬化后的变形抗力
σT = σbIn (A/A0) (MPa) σb — 金属材料的强度极限 (MPa)
A — 镦锻后头部的最大投影面积 (mm2) A0 —镦锻前坯的断面积 (mm2)
冷镦工艺与模具设计
一、冷镦变形工艺一些基本概念
1. 金属变形的基本概念
a. 金属的结构 一切金属的组织是由许多小晶体组成的,这些小晶体称为“晶粒” 。 常用冷镦材料的晶体结构:体心立方晶格、面心立方晶格和密排六方 晶格 。
b. 金属变形的基本概念 金属材料在外力作用下,所引起尺寸和形状的变化称为“变形”。
表面润滑要求
冷镦材料的改制过程
材料热处理—低温去应力退火、完全退火、球化退火(对于C>0.25% 中碳钢,为了满足冷变形工艺要求,常需要进行球化退火。)、固溶 处理(对于冷镦用的1Cr18Ni9Ti等奥氏体不锈钢,需采用固溶处理方 法,实现钢材软化。)
冷镦加工与冷镦变形力有着密切的关系。冷镦变形力是确定工艺参数、 模具设计、设备设计和选择设备的重要依据。在正常生产中,一般不需经 常进行变形力的计算,但对于非标零件与几何形状复杂零件加工时,为便 于合理地选用设备、设计工艺和模具等,必要时需要进行变形力计算,所 以必须掌握变形力的计算方法。
形过程中,随着变形的增大,由于冷作硬化
变形抗力 (N/mm2)
作用使金属的硬度和强度随之增大, 变形抗力也大大增加,而塑性却有所降 低,这将给后道工序带来变形的困难。
电工纯铁
金属材料冷作硬化后实际变形抗力如
图1.1-1所示,材料的含碳量越高,其变
形抗力越大。所以,在冷加工过程中需
适当增加中间热处理工序,以消除冷作硬 化和内应力。
4.冷镦变形力计算方法 F=KσT A 式种: F — 冷镦变形力 (MPa)
K — 镦锻头部的形状系数, 一般螺钉、螺栓取 2~2.4 σT — 考虑到冷作硬化后的变形抗力
σT = σbIn (A/A0) (MPa) σb — 金属材料的强度极限 (MPa)
A — 镦锻后头部的最大投影面积 (mm2) A0 —镦锻前坯的断面积 (mm2)
冷镦工艺与模具设计
一、冷镦变形工艺一些基本概念
1. 金属变形的基本概念
a. 金属的结构 一切金属的组织是由许多小晶体组成的,这些小晶体称为“晶粒” 。 常用冷镦材料的晶体结构:体心立方晶格、面心立方晶格和密排六方 晶格 。
b. 金属变形的基本概念 金属材料在外力作用下,所引起尺寸和形状的变化称为“变形”。
表面润滑要求
冷镦材料的改制过程
材料热处理—低温去应力退火、完全退火、球化退火(对于C>0.25% 中碳钢,为了满足冷变形工艺要求,常需要进行球化退火。)、固溶 处理(对于冷镦用的1Cr18Ni9Ti等奥氏体不锈钢,需采用固溶处理方 法,实现钢材软化。)
最新.冷镦材料基础知识培训幻灯片
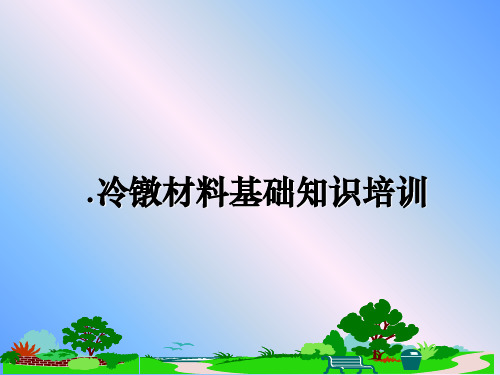
1.拉伸试样
2.拉伸曲线
❖ 拉伸曲线表示试样拉伸过程中力和变形关系,可用应力-延伸率曲线表 示,纵坐标为应力σ,σ=F/S0,横坐标为延伸率δ,δ=Δl/l0。
拉伸曲线的形状与材料有关, 由图可见,在载荷小的oa阶 段,试样在载荷F的作用下 均匀伸长,伸长量与载荷的 增加成正比。如果此时卸除 载荷,试样立即回复原状, 即试样产生的变形为弹性变 形。当载荷超过b点以后, 试样会进一步产生变形,此 时若卸除载荷,试样的弹性 变形消失,而另一部分变形 则保留下来,这种不能恢复 的变形称为塑性变形。
❖ 化学成分:C、Si、Mn、Ni、Cr、P、S等; ❖ 热处理状态:退火、淬火、回火、固溶处理、
时效处理等; ❖ 机HR械C性等能;:σb、σs、δ5、ψ、αk、HB、
了解、熟悉和理解这些信息,对我们合理选用 和使用冷镦材料,会有极大的帮助。
二、金属材料的力学性能
❖ 力学性能是指金属材料在外力作用下,所表现出来的抵抗变形 和破坏的能力以及接受变形的能力。
1.布氏硬度(HB)
HB F(kgf/m2m) S
SπD(D D2d2)
压头的材质有淬火钢球或硬质合金两种,当压头材质为淬火钢球时, 布氏硬度用HBS表示,适用于测量布氏硬度≤450的材料;当压头材质 为硬质合金时,布氏硬度用HBW表示,适用于测量布氏硬度在450~ 650范围内的材料。
2.洛氏硬度(HR)
用一定载荷将压头压入材料表面,根据压痕深度表示硬度值。根据压头和载 荷的不同,洛氏硬度分HRA,HRB和HRC,试验规范见表3-1 。
试验规范
3.维氏硬度(HV) 维氏硬度是用一定的载荷将锥面夹角为136°的正四棱锥金刚石压头压入试 样表面,保持一定时间后卸除载荷,试样表面就留下压痕,测量压痕对角线 的长度,计算压痕表面积,载荷F除以压痕面积S所得值即为维氏硬度。维氏 硬度用符号HV表示,计算公式如下:
冷镦挤变形工艺冷镦工艺与模具设计

和最小阻力定律。
体积不变定律 — 冷镦加工时,变形前金属坯料的体积等于变形后工件的体 积。 最小阻力定律 — 金属受到外力作用发生塑性变形,金属晶粒有向各个不 同方向移动的可能时,总是沿着阻里最小的方向移动。
最小阻力定律应用很广泛,在设计冷镦模具时,怎样才能使金属流动阻力 减小和合理地控制金属的流动,这是设计人员必须考虑的问题。
➢ 变形力的简单计算 冷镦加工与冷镦变形力有着密切的关系。冷镦变形力是确定工艺参数、
模具设计、设备设计和选择设备的重要依据。在正常生产中,一般不需经 常进行变形力的计算,但对于非标零件与几何形状复杂零件加工时,为便 于合理地选用设备、设计工艺和模具等,必要时需要进行变形力计算,所 以必须掌握变形力的计算方法。
4.冷镦变形力计算方法 F=KσT A 式种: F — 冷镦变形力 (MPa)
K — 镦锻头部的形状系数, 一般螺钉、螺栓取 2~2.4 σT — 考虑到冷作硬化后的变形抗力
σT = σbIn (A/A0) (MPa) σb — 金属材料的强度极限 (MPa)
试样裂纹的出现,是由于侧表面处附加拉应力作用的结果 。工具 与试 样接触表面的摩擦力、散热条件、试样几何尺寸等因素,都会 影响到附加拉应力的大小。因此,用镦粗法测定塑性指标时,为使 所得结果可进行比较,必须制定相应的规程,说明试验条件。在冷 镦生产中,常采用与工件变形条件相近的试验规程,以测定材料对 于冷镦工艺的适合性。 c. 塑性变形的基本定律 在冷镦加工中广泛应用的塑性变形的基本定律是:体积不变定律
镦粗试验在冷镦加工中常被采用。它是将试验材料制成圆 柱形试样,高度Ho一般为直径Do的1.5倍,然后在压力机或落 锤上进行镦粗,直至试样表面出现第一条肉眼可见的裂纹为止, 此时的压缩比ε即为塑性指标。
体积不变定律 — 冷镦加工时,变形前金属坯料的体积等于变形后工件的体 积。 最小阻力定律 — 金属受到外力作用发生塑性变形,金属晶粒有向各个不 同方向移动的可能时,总是沿着阻里最小的方向移动。
最小阻力定律应用很广泛,在设计冷镦模具时,怎样才能使金属流动阻力 减小和合理地控制金属的流动,这是设计人员必须考虑的问题。
➢ 变形力的简单计算 冷镦加工与冷镦变形力有着密切的关系。冷镦变形力是确定工艺参数、
模具设计、设备设计和选择设备的重要依据。在正常生产中,一般不需经 常进行变形力的计算,但对于非标零件与几何形状复杂零件加工时,为便 于合理地选用设备、设计工艺和模具等,必要时需要进行变形力计算,所 以必须掌握变形力的计算方法。
4.冷镦变形力计算方法 F=KσT A 式种: F — 冷镦变形力 (MPa)
K — 镦锻头部的形状系数, 一般螺钉、螺栓取 2~2.4 σT — 考虑到冷作硬化后的变形抗力
σT = σbIn (A/A0) (MPa) σb — 金属材料的强度极限 (MPa)
试样裂纹的出现,是由于侧表面处附加拉应力作用的结果 。工具 与试 样接触表面的摩擦力、散热条件、试样几何尺寸等因素,都会 影响到附加拉应力的大小。因此,用镦粗法测定塑性指标时,为使 所得结果可进行比较,必须制定相应的规程,说明试验条件。在冷 镦生产中,常采用与工件变形条件相近的试验规程,以测定材料对 于冷镦工艺的适合性。 c. 塑性变形的基本定律 在冷镦加工中广泛应用的塑性变形的基本定律是:体积不变定律
镦粗试验在冷镦加工中常被采用。它是将试验材料制成圆 柱形试样,高度Ho一般为直径Do的1.5倍,然后在压力机或落 锤上进行镦粗,直至试样表面出现第一条肉眼可见的裂纹为止, 此时的压缩比ε即为塑性指标。
冷镦模具设计介绍ppt

定期检查
定期检查模具的磨损情况,发现异 常及时修复。
清洗保养
定期清洗模具,保持清洁干燥,防 止锈蚀和积垢。
调整维修
对磨损严重的模具进行修复或更换 ,调整模具间隙和高度,保证正常 使用。
润滑保养
定期为模具涂抹润滑脂,减少磨损 和摩擦阻力,延长模具使用寿命。
05
冷镦模具设计发展趋势
高效节能设计
高效节能设计理念
未来冷镦模具设计将更加注 重材料的选择和优化,采用 高性能材料和新型复合材料 ,提高模具的强度、耐磨性 和抗疲劳性。
未来冷镦模具设计将更加注 重绿色制造和可持续发展, 采用环保材料和节能技术, 减少对环境的负面影响,推 动制造业可持续发展。
THANKS
谢谢您的观看
冷镦模具设计技术不断发展,可以提高模具设计 效率、减少设计成本、提高模具精度和寿命等方 面的优势。
对未来发展的展望
未来,随着制造业的快速发 展和技术的不断创新,冷镦 模具设计将会有更加广泛的 应用和发展。
技术创新是推动冷镦模具设 计发展的关键因素,未来可 以通过采用先进的 CAD/CAM软件、智能制造 技术等手段进一步提高模具 设计精度和效率。
高稳定性设计
优化模具材料和热处理工艺,提高模具材料的强度和稳定性,降低模具变形 和开裂的风险,提高生产效率。
高寿命、低成本设计
高寿命设计
选用高性能模具材料和表面强化技术,提高模具的耐磨性和抗疲劳性能,延长模 具的使用寿命。
低成本设计
采用优化结构设计、标准化模块化设计等手段,降低模具制造成本和提高维修维 护效率,实现低成本高效益的目标。
制造工艺:采用先进的数控机床进行高 精度加工,确保模具各部件的精度和表 面粗糙度。
模具材料选择:电子零件材质多为铜、 铝等有色金属,应选择专用的不锈钢或 硬质合金。
定期检查模具的磨损情况,发现异 常及时修复。
清洗保养
定期清洗模具,保持清洁干燥,防 止锈蚀和积垢。
调整维修
对磨损严重的模具进行修复或更换 ,调整模具间隙和高度,保证正常 使用。
润滑保养
定期为模具涂抹润滑脂,减少磨损 和摩擦阻力,延长模具使用寿命。
05
冷镦模具设计发展趋势
高效节能设计
高效节能设计理念
未来冷镦模具设计将更加注 重材料的选择和优化,采用 高性能材料和新型复合材料 ,提高模具的强度、耐磨性 和抗疲劳性。
未来冷镦模具设计将更加注 重绿色制造和可持续发展, 采用环保材料和节能技术, 减少对环境的负面影响,推 动制造业可持续发展。
THANKS
谢谢您的观看
冷镦模具设计技术不断发展,可以提高模具设计 效率、减少设计成本、提高模具精度和寿命等方 面的优势。
对未来发展的展望
未来,随着制造业的快速发 展和技术的不断创新,冷镦 模具设计将会有更加广泛的 应用和发展。
技术创新是推动冷镦模具设 计发展的关键因素,未来可 以通过采用先进的 CAD/CAM软件、智能制造 技术等手段进一步提高模具 设计精度和效率。
高稳定性设计
优化模具材料和热处理工艺,提高模具材料的强度和稳定性,降低模具变形 和开裂的风险,提高生产效率。
高寿命、低成本设计
高寿命设计
选用高性能模具材料和表面强化技术,提高模具的耐磨性和抗疲劳性能,延长模 具的使用寿命。
低成本设计
采用优化结构设计、标准化模块化设计等手段,降低模具制造成本和提高维修维 护效率,实现低成本高效益的目标。
制造工艺:采用先进的数控机床进行高 精度加工,确保模具各部件的精度和表 面粗糙度。
模具材料选择:电子零件材质多为铜、 铝等有色金属,应选择专用的不锈钢或 硬质合金。
冷镦基础知识和工艺分析ppt
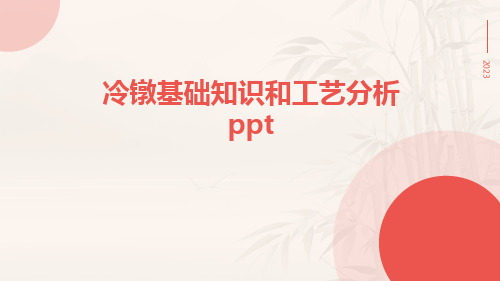
2023
冷镦基础知识和工艺分析 ppt
contents
目录
• 冷镦成型工艺简介 • 冷镦成型工艺特点 • 冷镦成型工艺影响因素 • 冷镦成型工艺应用场景 • 冷镦成型工艺发展趋势 • 冷镦成型工艺常见问题及解决方案
01
冷镦成型工艺简介
冷镦成型工艺定义
冷镦成型工艺是指利用模具在常温下对金属坯料施加压力, 使其产生塑性变形而形成所需形状和尺寸的零件的一种成型 方法。
03
在冷镦成型工艺中,模具是关键的工艺装备之一,其结构形式、材料选择、热 处理工艺等因素直接影响到零件的质量和生产效率。
02
冷镦成型工艺特点
提高生产效率
加工效率
采用多工位冷镦成型方式,可同时处理多个零件,提高生产效率。
生产周期
通过减少或消除加热、矫直、打磨等辅助工序,缩短了生产周期。
提高零件强度
材料纯净度
3
材料中的杂质会对成型效果产生不良影响。
模具设计因素
模具结构
合理的模具结构可以降低成型难度和提高成型效 果。
模具材料
模具材料的硬度、耐磨性和抗冲击性能对成型效 果有影响。
模具加工精度
模具加工精度对成型件的尺寸和形状精度有影响 。
工艺参数选择
冷镦速度
速度过快会导致成型不充分,速 度过慢则会影响生产效率。
优化材料性能
材料利用率
冷镦成型工艺可以最大限度地利用原材料,提高材料的利用率,降低生产成本。
性能优化
通过合理的材料选择和冷镦工艺优化,可以进一步优化零件的性能,提高其使用 效果和寿命。
03
冷镦成型工艺影响因素
材料因素
1 2
材料硬度
硬度过高会导致成型困难,硬度过低则会使成 型效果不佳。
冷镦基础知识和工艺分析 ppt
contents
目录
• 冷镦成型工艺简介 • 冷镦成型工艺特点 • 冷镦成型工艺影响因素 • 冷镦成型工艺应用场景 • 冷镦成型工艺发展趋势 • 冷镦成型工艺常见问题及解决方案
01
冷镦成型工艺简介
冷镦成型工艺定义
冷镦成型工艺是指利用模具在常温下对金属坯料施加压力, 使其产生塑性变形而形成所需形状和尺寸的零件的一种成型 方法。
03
在冷镦成型工艺中,模具是关键的工艺装备之一,其结构形式、材料选择、热 处理工艺等因素直接影响到零件的质量和生产效率。
02
冷镦成型工艺特点
提高生产效率
加工效率
采用多工位冷镦成型方式,可同时处理多个零件,提高生产效率。
生产周期
通过减少或消除加热、矫直、打磨等辅助工序,缩短了生产周期。
提高零件强度
材料纯净度
3
材料中的杂质会对成型效果产生不良影响。
模具设计因素
模具结构
合理的模具结构可以降低成型难度和提高成型效 果。
模具材料
模具材料的硬度、耐磨性和抗冲击性能对成型效 果有影响。
模具加工精度
模具加工精度对成型件的尺寸和形状精度有影响 。
工艺参数选择
冷镦速度
速度过快会导致成型不充分,速 度过慢则会影响生产效率。
优化材料性能
材料利用率
冷镦成型工艺可以最大限度地利用原材料,提高材料的利用率,降低生产成本。
性能优化
通过合理的材料选择和冷镦工艺优化,可以进一步优化零件的性能,提高其使用 效果和寿命。
03
冷镦成型工艺影响因素
材料因素
1 2
材料硬度
硬度过高会导致成型困难,硬度过低则会使成 型效果不佳。
冷镦模具设计介绍课件
和使用性能。
04
冷镦模具的应用与发展
冷镦模具的应用范围
汽车零件制造
冷镦模具被广泛应用于汽车零件的制造,如 螺栓、螺母、齿轮等。
机械制造业
机械制造业中,冷镦模具用于生产各种紧固 件、连接件等。
建筑行业
在建筑行业中,冷镦模具用于生产钢筋、螺 杆等紧固件。
其他行业
如航空航天、电子、家具、家电等行业,都 离不开冷镦模具的应用。
冷镦模具的结构设计应考虑成形 工艺的特点,如拉伸、冲压等, 以及零件的形状、尺寸和材料等
因素。
冷镦模具的材料选择
01
根据成形工艺和零件材料的不同,冷镦模具的材料选择也有所 不同。
02
常用的冷镦模具材料包括优质碳素结构钢、合金结构钢、不锈
钢、硬质合金等。
在选择冷镦模具材料时,需要考虑材料的耐磨性、抗冲击性和
提高解决实际问题的能力。
展望
随着制造业的快速发展,冷镦模具设 计领域面临着越来越多的挑战和机遇 。未来,该领域将更加注重技术创新 和跨学科融合,推动产业升级和发展 。
新材料和新工艺的不断涌现将为冷镦 模具设计带来更多的可能性,如采用 高性能材料制造高精度、长寿命的模 具,以及利用3D打印技术实现快速原 型制作等。
此外,随着智能制造和数字化转型的 加速推进,冷镦模具设计将更加注重 信息化和智能化,实现数据驱动的设 计优化和生产自动化。
06
参考文献与致谢
参考文献
01
参考文献1
作者1,书名,出版社,出版年份 。
参考文献3
作者3,书名,出版社,出版年份 。
03
02
参考文献2
作者2,书名,出版社,出版年份 。
参考文献4
作者4,书名,出版社,出版年份 。
04
冷镦模具的应用与发展
冷镦模具的应用范围
汽车零件制造
冷镦模具被广泛应用于汽车零件的制造,如 螺栓、螺母、齿轮等。
机械制造业
机械制造业中,冷镦模具用于生产各种紧固 件、连接件等。
建筑行业
在建筑行业中,冷镦模具用于生产钢筋、螺 杆等紧固件。
其他行业
如航空航天、电子、家具、家电等行业,都 离不开冷镦模具的应用。
冷镦模具的结构设计应考虑成形 工艺的特点,如拉伸、冲压等, 以及零件的形状、尺寸和材料等
因素。
冷镦模具的材料选择
01
根据成形工艺和零件材料的不同,冷镦模具的材料选择也有所 不同。
02
常用的冷镦模具材料包括优质碳素结构钢、合金结构钢、不锈
钢、硬质合金等。
在选择冷镦模具材料时,需要考虑材料的耐磨性、抗冲击性和
提高解决实际问题的能力。
展望
随着制造业的快速发展,冷镦模具设 计领域面临着越来越多的挑战和机遇 。未来,该领域将更加注重技术创新 和跨学科融合,推动产业升级和发展 。
新材料和新工艺的不断涌现将为冷镦 模具设计带来更多的可能性,如采用 高性能材料制造高精度、长寿命的模 具,以及利用3D打印技术实现快速原 型制作等。
此外,随着智能制造和数字化转型的 加速推进,冷镦模具设计将更加注重 信息化和智能化,实现数据驱动的设 计优化和生产自动化。
06
参考文献与致谢
参考文献
01
参考文献1
作者1,书名,出版社,出版年份 。
参考文献3
作者3,书名,出版社,出版年份 。
03
02
参考文献2
作者2,书名,出版社,出版年份 。
参考文献4
作者4,书名,出版社,出版年份 。
冷挤压工艺及模具设计 ppt课件
ppt课件
பைடு நூலகம்
4
冷挤压工艺及模具设计
3.复合挤如图5-3所示,挤压时,金属流动方向相对于 凸模运动方向,一部分相同,另一部分相反,适用于各种复 杂形状制件的挤压;改变凹模孔口或凸、凹模之间缝隙的轮 廓形状,就可以挤出形状和尺寸不同的各种空心件和实心件。
图5-1 正挤压图
5-2 反挤压图
ppt课件
5-3 复合挤
ppt课件 14
冷挤压工艺及模具设计
对于有些材料,为了确保冷挤压过程中的润滑层不被过 大的单位接触压力所破坏,毛坯要经过表面化学处理。例如 碳钢的磷酸盐处理(磷化)、奥氏体不锈钢的草酸盐处理、 铝合金的氧化、磷化或氟硅化处理、黄铜的钝化处理等。经 化学处理后的毛坯表面,覆盖一层很薄的多孔状结晶膜,它 能随毛坯一起变形而不剥离脱落,经润滑处理后在孔内吸附 的润滑剂可以保持挤压过程中润滑的连续性和有效的润滑效 果。
h0 V坯 。 F0
ppt课件
(5-2)
10
冷挤压工艺及模具设计
5.1.3.2 坯料的制备
冷挤压坯料制作要求十分细致、严格,有一定的平面度, 表面粗糙度、精度要求。可采用剪切加工、板料落料加工、 切削加工及其它特殊方法加工,毛坯的上、下端面必须平整。
5.1.3.3 毛坯的软化热处理 对毛坯进行软化热处理的目的是降低材料硬度,提高塑 性,得到良好的金相组织,消除内应力,以降低材料的变形 抗力,提高模具的寿命和零件质量。
ppt课件 3
冷挤压工艺及模具设计
5.1.1 冷挤压的分类 根据金属被挤出的方向与凸模运动方向的关系,冷挤压 一般可分为正挤压、反挤压、复合挤压三种基本方式。 1.正挤压如图5-1所示,挤压时金属流动方向与凸模流 动方向相同,适用于各种形状的实心件、管件和环形件的挤 压; 2.反挤压如图5-2所示,挤压时金属流动方向与凸模运 动方向相反,适用于各种截面形状的杯形件的挤压;
典型螺母冷镦工艺设计ppt
THANKS
感谢观看
3
背景:传统螺母制造方法生产效率低下,成本 较高,不能满足现代制造业发展需求。
螺母冷镦工艺定义
螺母冷镦工艺是一种利用金属材料的塑性变形和镦粗原理, 在室温下将原材料加工成所需形状和尺寸的工艺方法。
冷镦工艺是一种高效、节能、环保的加工方法,具有生产效 率高、成本低、产品质量稳定等优点。
工艺分类
根据加工原理,镦、复合型冷镦等。
典型螺母冷镦工艺设计
xx年xx月xx日
目 录
• 介绍 • 螺母冷镦工艺设计 • 螺母冷镦工艺的优缺点 • 案例分析 • 比较分析 • 总结
01
介绍
目的和背景
1
螺母冷镦工艺是一种在室温下将原材料通过压 力加工成型的工艺方法,广泛应用于机械制造 、汽车、航空航天等领域。
2
目的:提高生产效率、降低成本、提高产品质 量和经济效益。
方案2
由于采用普通设备,初期投资成本较低,但生产效率较低,反而 增加生产成本。
方案3
由于采用特种设备,虽然制造成本较高,但可满足特定领域的需 求,提高产品附加值。
各厂家的螺母冷镦工艺可靠性比较
方案1
采用自动化生产线,减少人为操作失误,提高产 品的一致性和可靠性。
方案2
由于人工操作较多,产品质量容易受到操作者技 能水平的影响。
方案3
由于特种设备的维护和操作技术要求较高,若维 护不当或操作失误容易导致生产事故。
06
总结
螺母冷镦工艺在机械制造行业的应用前景
应用领域广泛
螺母冷镦工艺是一种广泛应用 于机械制造行业的基本工艺, 可应用于汽车、航空航天、能
源等领域。
高效、高精度
螺母冷镦工艺具有高效、高精度 的特点,能够实现大批量、高效 率的生产。
冷镦模具设计培训资料课件
定制化
绿色环保
随着个性化消费需求的增加,冷镦模具设 计正朝着定制化方向发展,以满足不同客 户的需求。
随着环保意识的提高,冷镦模具设计正朝 着绿色环保方向发展,采用环保材料和工 艺,降低能耗和减少废弃物排放。
技术展望
数字化设计
利用数字化技术进行冷镦模具设计, 实现参数化、可视化和优化设计,提 高设计效率和精度。
模具表面处理技术
总结词
模具表面处理技术是提高模具表面性能的关 键环节,它涉及到表面涂层、表面强化以及 表面改性等方面。
详细描述
常用的模具表面处理技术包括渗碳淬火、氮 化处理、离子注入、物理气相沉积(PVD) 、化学气相沉积(CVD)等。通过表面处理 技术,可以改变模具表面的成分、结构和性 能,从而提高模具的耐磨性、耐腐蚀性和抗 疲劳性能,延长模具的使用寿命。
模具材料处理
总结词
模具材料处理是保证模具性能的重要环节,它涉及到材料的选用、材料的加工以及材料 的热处理等方面。
详细描述
在选择模具材料时,需要考虑材料的强度、硬度、耐磨性、耐腐蚀性以及热稳定性等因 素。同时,还需要根据材料的特性,选择合适的加工工艺,如铸造、锻造、切削加工、 电火花加工等。此外,合理的热处理工艺可以充分发挥材料的潜力,提高模具的使用寿
增材制造
利用增材制造技术进行冷镦模具制造 ,实现快速原型制造和个性化定制。
智能检测
利用智能检测技术对冷镦模具进行质 量检测和寿命预测,提高产品质量和 可靠性。
虚拟仿真
利用虚拟仿真技术进行冷镦模具设计 和分析,实现虚拟装配和优化设计。
THANK YOU
命。
模具热处理工艺
总结词
模具热处理工艺是提高模具性能的关键 环节,它涉及到加热、保温和冷却等过 程。