以盐酸为原料合成一氯甲烷(150kta)工艺设计
一氯甲烷生产工艺

一氯甲烷生产工艺
一氯甲烷(又称氯仿)是一种重要的有机化学原料,广泛应用于医药、化工、农药等领域。
本文将介绍一氯甲烷的生产工艺。
一氯甲烷的生产工艺主要有两种,即直接氯化法和间接氯化法。
直接氯化法是利用甲烷和氯气在高温高压条件下直接反应生成一氯甲烷。
该方法需要高温高压反应器,反应温度为400-500℃,反应压力为3-5MPa。
甲烷和氯气按一定的比例进入反应器,反应产物通过冷却器冷却后,得到液态一氯甲烷。
直接氯化法生产一氯甲烷的主要优点是反应简单,产率高,但由于反应温度高,易产生不良的副反应,同时由于使用氯气,存在一定的安全风险。
间接氯化法是将甲烷和氯化氢在催化剂的作用下反应生成一氯甲烷。
该方法反应温度较低,反应条件温和,具有安全性高的优点。
间接氯化法的反应机理是:甲烷和氯化氢在催化剂的作用下发生氢氯酸化反应生成甲醇和氯化氢,然后甲醇和氯化氢继续反应生成一氯甲烷。
间接氯化法生产一氯甲烷的主要优点是反应条件温和,安全性高,同时可以回收利用氯化氢。
在实际生产中,间接氯化法是目前主要采用的一种生产工艺。
其主要流程如下:首先将甲烷加热到400-500℃,使其分解成碳和氢,然后将氢与氯气进行反应生成氯化氢,再将氯化氢和甲醇在催化剂的作用下反应生成一氯甲烷。
反应产物通过冷却器冷却后,得到液
态一氯甲烷。
此外,间接氯化法生产一氯甲烷还可以回收利用氯化氢进行循环使用,提高了生产效率和经济效益。
一氯甲烷是一种重要的有机化学原料,其生产工艺主要有直接氯化法和间接氯化法。
在实际生产中,间接氯化法是主要采用的一种工艺,具有反应条件温和、安全性高、可回收利用氯化氢等优点。
氯甲烷生产工艺设计

氯甲烷生产工艺设计
氯甲烷,化学式为CH3Cl,是一种无色气体,具有强烈的刺激性气味。
在工业中,氯甲烷主要用作溶剂、催化剂和冷冻剂。
以下是关于氯甲烷的
生产工艺设计的一个概述。
首先,氯甲烷的主要生产原料是甲烷和氯气。
甲烷是天然气的主要组
成部分,可通过液化石油气或天然气分离获得。
氯气则是通过电解盐水或
氯石制备得到。
氯甲烷的生产工艺主要分为两个步骤:氯化反应和热分解反应。
氯化反应是将甲烷和氯气通过催化剂反应生成氯甲烷。
反应方程式如下:
CH4+Cl2→CH3Cl+HCl
在反应器中,甲烷和氯气以适当的比例混合并通入反应器中。
反应器
内的催化剂对反应进行催化,加速反应的速率。
反应产生的氯甲烷和氯化
氢会被吸附和分离,以保持反应的平衡。
热分解反应是将氯甲烷在高温下分解为甲烷和氯气。
反应方程式如下:CH3Cl→CH4+Cl2
热分解反应需要在高温下进行,通常是在800至1000°C之间进行。
反应器内的氯甲烷被加热,分解成甲烷和氯气。
产生的甲烷和氯气可以经
过冷凝、洗涤和分离等步骤进行回收和再利用。
总结来说,氯甲烷的生产工艺设计包括甲烷和氯气的混合、氯化反应
和热分解反应。
这些步骤通过合适的催化剂和反应条件,将甲烷和氯气转
化成氯甲烷,并在后续的分离步骤中将产物进行回收和再利用。
工艺设计
的关键点包括反应器的设计、催化剂的选择和反应条件的控制。
此外,安全性和环保性也是氯甲烷生产工艺设计中需要考虑的重要因素,包括废气处理和水处理等方面的设计。
一氯甲烷生产工艺

一氯甲烷生产工艺
一氯甲烷,化学式CH3Cl,又称氯甲烷,是一种无色易燃气体。
它是一种重要的有机合成原料,广泛应用于制药、农药、塑料、溶剂等领域。
一氯甲烷的生产工艺可以通过多种方法实现,其中最常用的是通过甲醇与氯化氢反应来合成一氯甲烷。
下面介绍一种常用的工艺流程。
1. 原料准备:甲醇和氯化氢是合成一氯甲烷的主要原料。
首先要确保原料的纯度和质量符合生产要求。
2. 混合反应:将甲醇和氯化氢按一定的比例混合后,通过加热,使其反应生成一氯甲烷。
反应方程式为:CH3OH + HCl → CH3Cl + H2O
3. 分离和纯化:由于反应产物中可能还会存在其他杂质和未反应的原料,需要进行分离和纯化工作。
一般可以通过冷凝、蒸馏、萃取等方法,将一氯甲烷从反应混合物中分离出来。
4. 产品收集:将纯化后的一氯甲烷收集并进行包装、储存,以备后续使用。
在实际生产中,还需要注意以下几个方面的问题:
1. 反应条件的选择:反应温度、反应压力等条件会直接影响反
应速率和产物质量。
需要根据实际情况进行调整和优化。
2. 设备和材料选择:选择适合反应的容器、管道等设备,并保证其材料能够耐受反应条件下的腐蚀和高温。
同时,还要注意防止反应产生的氯化氢泄漏和甲醇的挥发,保证操作的安全性。
3. 能源利用和环境保护:在工艺中要尽量减少能源消耗和减少废气排放,以达到可持续发展和环境保护的要求。
综上所述,生产一氯甲烷的工艺主要包括原料准备、混合反应、分离纯化和产品收集等步骤。
通过合理选择反应条件和设备,进行优化调整,可以生产出高质量的一氯甲烷产品。
以盐酸为原料合成一氯甲烷(150kta)工艺设计

毕业设计(论文)任务书题目:以盐酸为原料合成一氯甲烷(150kt/a)工艺设计学生姓名:班级:学号:题目类型:工程设计指导教师:崔孝玲一、设计原始资料1、原料:有机硅副产质量浓度为30%的盐酸甲醇液体,纯度99.9% 含小于0.5%(质量)水蒸汽。
2、重点设计:浓盐酸提馏制氯化氢和一氯甲烷合成系统3、生产时间:8000小时4、设计基本数据氯化氢提馏过程:(1)提馏塔操作压力0.16MPa(绝压,以下同);(2)原料酸常温进料,进料温度20'C;(3)原料酸质量浓度30%,稀盐酸产品质量浓度21%;(4)年操作时间8000小时。
一氯甲烷合成系统给定的工艺数据为:(1)反应器温度1500C,压力0.14MPa(绝压,以下同);(2)一、二级冷凝器压力0.13MPa;(3)甲醇进料温度20℃,压力0.15MPa;(4)氯化氢进料温度20℃,压力。
.15MPa;(5)甲醇汽体过热温度120 ℃,压力0.15MPa;(6)返回反应器的循环液压力0.15MPa;(7)离开二级冷凝器的气体温度40 ℃;(8)甲醇的总转化率90%(摩尔);(9)进料甲醇和氯化氢的摩尔比1;1.1;5、建厂地点:兰州二、设计工作内容(建议):第一部分前言第二部分文献概述第三部分设计的内容及要求3.1设计范围及技术方案的确定3.2设计内容及深度要求3.2.1浓盐酸提馏制氯化氢系统3.2.2一氯甲烷合成系统第四部分氯化氢提馏工艺设计计算4.1提馏系统工艺设计计算4.1.1计算模型4.1.2计算步骤4.1.3计算结果4.2提馏系统主要设备设计计算4.2.1填料提馏塔4.2.2一级冷凝器4.2.3二级冷凝器4.2.4塔底再沸器4.2.5浓酸预热器4.3提馏塔内件设计计算4.3.1.进料液体分布器第五部分氯甲烷合成系统设计计算5.1合成系统工艺设计计算5.2合成系统主要设备设计计算第六部分主要参考资料第七部分外文文献翻译(2篇)三、绘制设计图1. 机绘带主要控制点的氯化氢提馏工艺流程图一张(A1);2. 手绘以盐酸为原料合成一氯甲烷的物料平衡图一张(A2);3. 机绘提馏塔的工艺尺寸图一张(A2)。
氯化氢和甲醇反应生成一氯甲烷的工艺流程
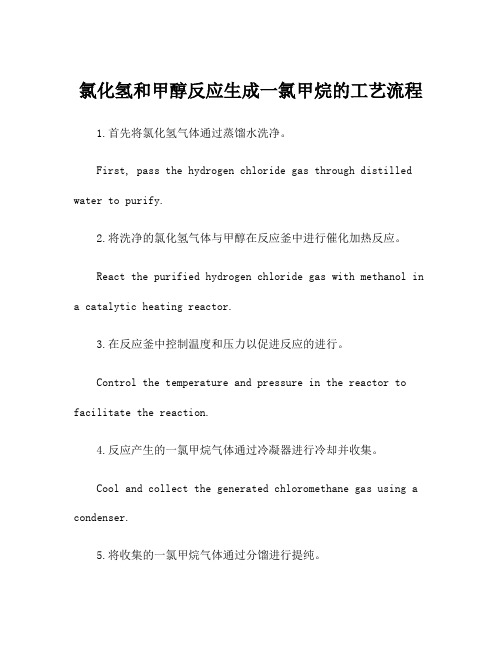
氯化氢和甲醇反应生成一氯甲烷的工艺流程1.首先将氯化氢气体通过蒸馏水洗净。
First, pass the hydrogen chloride gas through distilled water to purify.2.将洗净的氯化氢气体与甲醇在反应釜中进行催化加热反应。
React the purified hydrogen chloride gas with methanol ina catalytic heating reactor.3.在反应釜中控制温度和压力以促进反应的进行。
Control the temperature and pressure in the reactor to facilitate the reaction.4.反应产生的一氯甲烷气体通过冷凝器进行冷却并收集。
Cool and collect the generated chloromethane gas using a condenser.5.将收集的一氯甲烷气体通过分馏进行提纯。
Purify the collected chloromethane gas through fractional distillation.6.最终得到高纯度的一氯甲烷作为产物。
Obtain high-purity chloromethane as the final product.7. Chlorine gas is bubbled through methanol in the presence of a catalyst to initiate the reaction.氯气在催化剂的作用下通入甲醇中以启动反应。
8. The reaction vessel is maintained at a specific temperature and pressure to optimize the reaction conditions.反应釜保持特定温度和压力以优化反应条件。
一氯甲烷工艺流程模拟与分析

一氯甲烷工艺流程模拟与分析陈丹【摘要】通过使用流程模拟软件HYSYS,对氯甲烷分离段工艺进行模拟与分析,找出了较适合的理论板数,进料位置,回流比,得到了氯甲烷较小的排放量,满足了一氯甲烷收率所应达到的标准。
【期刊名称】《科技风》【年(卷),期】2013(000)010【总页数】1页(P80-80)【关键词】一氯甲烷;流程模拟;HYSYS【作者】陈丹【作者单位】信息产业电子第十一设计研究院有限公司,四川成都 610000【正文语种】中文一氯甲烷主要是生产甲基氯硅烷,全世界有50%~90%的一氯甲烷用于有机硅的生产,基本上为有机硅生产企业自备原料,只有少量供应市场。
有机硅及其深加产品广泛应用于电子工业、航天航空领域和国民领域,是当今世界新兴的化工材料,也是我国重点扶持的产业,素有“工业味精”之称的有机硅,近几年发展迅速,从而带动一氯甲烷的发展,一氯甲烷的生产与有机硅的发展密切相关。
笔者结合我国自贡鸿鹤化工厂氯甲烷生产技术,选择热氯化法生产氯甲烷的工艺流程,对设计规模为年产10万吨一氯甲烷生产工艺进行模拟。
1 流程模拟与分析1.1 技术分析1.1.1 流程描述分别来自烧碱车间,配气站和反应装置的氯气和天然气,按一定配比,其中甲烷过量,氯气流量为:55.765mol/h,甲烷流量为65.142mol/h,进入混合器,以避免反应气进入反应器后局部浓度过高引起爆炸,反应气混合均匀后进入反应器,进行甲烷热氯化反应,反应气组成为:一氯甲烷,少量的四氯化碳,氯化氢和未反应的甲烷。
由于反应过程中要放出大量的热量,若热量不及时移出,会发生一些副反应,因此为了提高反应的转化率以及有效利用能源,故将反应生成的高温粗氯化气通过换热器,用于加热原料反应气氯气和甲烷,粗氯化气温度降为100度左右,由于下个流程为水洗,为了减小氯甲烷在水中的溶解度和水解程度,因此还需将粗氯化气经空气冷却器冷却到10℃后,进入水洗系统,除去所含的氯化氢,以及少量的四氯化碳,再经浓硫酸干燥系统除去所含的水,最后经过精馏得到产品一氯甲烷和甲烷,甲烷回收利用继续参加反应。
利用有机硅单体副产盐酸合成一氯甲烷工艺设计
利用有机硅单体副产盐酸合成一氯甲烷工艺
设计
1概况
一氯甲烷(一氯乙烷)是一种无色可燃性气体,由C₁、H₃Cl组成,具有苯环烷烃的气味。
它具有高蒸气压、低折射率、质轻易挥发性等特点,且有耐温高、耐酸碱性高兼容性强等特点,在市场上十分受欢迎。
一氯甲烷可广泛应用于塑料、橡胶、染料、精油、醇、树脂、调味品等的生产,也可作为安全防护用品的原料。
2一氯甲烷的工艺设计
一氯甲烷的工艺设计是化学反应操作的一道重要考题,根据先进分子设计技术,考虑了反应原料用量、反应条件等,可采用有机硅单体副产盐酸法合成一氯甲烷,具体步骤如下:
1.准备原料
准备一氯乙烷二氯乙烷副产品,同时准备少量的一氯乙烷铵溶液,以及一定量的盐酸。
2.反应罐操作
将原料放入反应罐中,并将一氯乙烷铵溶液滴入,搅拌均匀。
3.添加盐酸
慢慢向反应罐中加入适量的盐酸,以控制反应的pH值,并增加反应产物的溶解度。
4.加热反应
将反应罐加热至一定温度(常温至摄氏60度),然后稳定进行反应操作,即可得到一氯甲烷。
3结论
使用有机硅单体副产盐酸法合成一氯甲烷是一种高效无氧的节能绿色的合成工艺,只需在常温及恒温下进行简单的准备操作和反应操作,就可完成一氯甲烷的高效合成。
年产12万吨一氯甲烷工艺设计
年产12万吨一氯甲烷工艺设计一氯甲烷是一种重要的有机化工原料,广泛应用于制冷剂、溶剂和化学合成等领域。
本文旨在对年产12万吨一氯甲烷的工艺设计进行详细介绍,以期提供具有指导意义的信息。
一氯甲烷的工艺设计主要包括原料准备、反应路径选择、反应器设计、分离与提纯、废物处理等环节。
下面将分步骤进行说明。
首先,原料准备阶段是确保生产过程顺利进行的重要环节。
一氯甲烷的制备原料主要包括甲烷和氯气,因此需要对这两种原料进行储存、输送和准确的配比控制。
在确保安全的前提下,通过有效的储罐系统和严格的控制措施,确保原料供应的稳定性和充足性。
其次,反应路径的选择对产品的纯度和产率具有重要影响。
在一氯甲烷的制备过程中,主要采用氯化甲烷和次氯甲烷两条反应路径,因此需要根据产品质量要求和经济性考虑,确定合适的反应路径。
氯化甲烷反应路径相对简单,但次氯甲烷反应路径产率更高。
因此,在工艺设计中要综合考虑这两种反应路径的优劣,选择适合的方案。
接下来,反应器设计是确保反应过程高效进行的关键环节。
针对年产12万吨的生产规模,应当选择大型连续式反应器作为核心设备。
通过优化反应器的结构和控制参数,提高反应的转化率和选择性。
同时,合理设计反应器的热交换和冷却系统,以控制反应温度和确保安全运行。
分离与提纯是工艺设计中另一个重要环节。
一氯甲烷的产物通常伴随着其他杂质,例如氯化氢、二氯甲烷和三氯甲烷等。
为了获得高纯度的一氯甲烷产品,需要设计合适的分离工艺,例如精馏、萃取和冷凝等。
通过合理配置分离设备,实现一氯甲烷的高效提纯,同时回收和处理产生的废物。
最后,废物处理也是工艺设计中不能忽视的环节。
一氯甲烷的制备过程中会产生一些废气和废液,其中含有一氯甲烷、氯化氢和其他有机化合物等。
为了满足环保要求和资源利用的要求,需要对废物进行正确处理。
例如,可以采用吸收塔和活性炭吸附等装置对废气进行处理,同时可以选择适当的处理方法对废液进行处理和回收。
总之,年产12万吨一氯甲烷的工艺设计需要从原料准备、反应路径选择、反应器设计、分离与提纯以及废物处理等多个环节进行综合考虑。
一氯甲烷生产工艺设计
广西工业职业技术学院一氯甲烷生产工艺设计系部:石油与化学工程系专业:应用化工技术班级________学号:G201040232姓名________________、八—刖言甲烷氯化物包括一氯甲烷、二氯甲烷、三氯甲烷和四氯化碳,是一类常用的化学制剂,在化工、建材等多个领域有广泛的应用。
其中一氯甲烷还常常作为中间体或者是反应组分应用于多个技术领域,它的重要性和应用的广泛型正在日益的扩大。
作为合成甲基氯硅烷的基础原料,氯甲烷成本占甲基氯硅烷成本的40%,氯甲烷生产的经济模化一直是制约我国有机硅行业发展的关键性技术之一,国内外的生产现状表明我们存在的距离。
随着我国加入WTO,国内有机硅的生产与发展已经面临更加激烈的国际竞争。
如何提高氯甲烷的生产技术水平,尤其是有机硅单体生产企业利用有机硅单体副产盐酸合成氯甲烷进一步提高其工艺技术及装备水平的研究,其意义十分重大。
一氯甲烷的生产方法主要有两种:甲醇氢氯化法和甲烷氯化法。
本设计经过对比国内外各使用的生产方法、经济技术上的分析及根据国内综合情况,最终选择了甲醇氢氯化法的生产方法。
目录第一章一氯甲烷相关介绍第一节一氯甲烷的基本性质第二节一氯甲烷的应用第三节国内外甲烷氯化物的发展概况1.3.1国内13 2国外第二章生产工艺设计第一节生产方法的选择2.1.1气一液相非催化法2.1.2气一液相催化法2.1.3气一固相催化法第二节甲醇氢氯化法生产原理第三节物料衡算第四节热量衡算2.4.1.a 料口2.4.2塔顶2.4.3塔釜第一章一氯甲烷相关介绍第一节一氯甲烷的基本性质外观与性状:无色气体,具有醚样的微甜气味。
主要用途:用作致冷剂、甲基化剂,还用于有机合成。
熔点:-97 . 7 3沸点:-24 . 2相对密度(水=1) : 0 . 92相对密度(空气=1): 1 . 78密度0.9159g/cm318C时溶解度280ml/水饱和蒸汽压(kPa) : 506 . 62/22 C溶解性:易溶于水、氯仿、丙酮,能溶于乙醇等。
一氯甲烷生产工艺设计
一氯甲烷生产工艺设计一氯甲烷,又称氯仿,是一种重要的有机化学品,广泛应用于医药、农药、橡胶、金属和电子等多个行业。
本文将以制备一氯甲烷的工艺设计为例,介绍一氯甲烷的制备工艺。
一氯甲烷的制备工艺可分为两步:乙烯氯化和氯化甲基化反应。
乙烯氯化是将乙烯和氯气进行反应,生成氯乙烷,也是一氯甲烷的前驱体。
该反应一般在高温、高压下进行,反应方程式如下:C2H4+Cl2->C2H3Cl+HCl乙烯与氯气按摩尔比1:2进行反应,反应温度为300-400摄氏度,反应压力为5-10大气压。
此反应为自发反应,产物在反应过程中会生成HCl,可通过控制反应压力来调节反应速率。
氯化甲基化反应是将氯乙烷与氢氯酸反应生成一氯甲烷。
反应方程式如下:C2H3Cl+HCl->CH3Cl+HCl2该反应需要催化剂存在,常用的催化剂为氯化铝。
反应温度为100-200摄氏度,在一定的温度范围内,调节反应温度可以控制产物的选择性。
整个工艺流程如下:1.将乙烯和氯气按摩尔比1:2混合,送入反应器中,在高温、高压条件下进行乙烯氯化反应。
反应器内安装搅拌器,以保证反应的充分均匀。
2.乙烯氯化反应结束后,将反应器中的氯乙烷抽出,进行纯化处理。
纯化处理可以采用蒸馏、萃取等方法,将其中的杂质去除。
3.将纯化后的氯乙烷与氢氯酸按摩尔比1:3混合,加入氯化铝催化剂,在适当的温度下进行氯化甲基化反应。
反应器内同样安装搅拌器,以保证反应的均匀进行。
4.氯化甲基化反应结束后,将反应器内的产物抽出,进行纯化处理。
纯化过程同样可以采用蒸馏、萃取等方法,将其中的杂质去除。
5.最后,将纯化后的产物进行脱水、脱色等后处理步骤,得到最终的一氯甲烷产品。
在实际生产中,还需要考虑反应条件的优化、催化剂的选择和再生、工艺的节能减排等问题。
此外,工艺安全和环境保护也是制备过程中需要重视的方面。
总之,一氯甲烷的制备工艺设计需要考虑乙烯氯化和氯化甲基化两个反应步骤,并结合纯化和后处理等步骤,以获得高纯度的一氯甲烷产品。
- 1、下载文档前请自行甄别文档内容的完整性,平台不提供额外的编辑、内容补充、找答案等附加服务。
- 2、"仅部分预览"的文档,不可在线预览部分如存在完整性等问题,可反馈申请退款(可完整预览的文档不适用该条件!)。
- 3、如文档侵犯您的权益,请联系客服反馈,我们会尽快为您处理(人工客服工作时间:9:00-18:30)。
毕业设计(论文)任务书
题目:以盐酸为原料合成一氯甲烷(150kt/a)工艺设计
学生姓名:班级:学号:
题目类型:工程设计指导教师:崔孝玲
一、设计原始资料
1、原料:有机硅副产质量浓度为30%的盐酸甲醇液体,纯度99.9% 含小于0.5%(质量)水蒸汽。
2、重点设计:浓盐酸提馏制氯化氢和一氯甲烷合成系统
3、生产时间:8000小时
4、设计基本数据
氯化氢提馏过程:
(1)提馏塔操作压力0.16MPa(绝压,以下同);
(2)原料酸常温进料,进料温度20'C;
(3)原料酸质量浓度30%,稀盐酸产品质量浓度21%;
(4)年操作时间8000小时。
一氯甲烷合成系统给定的工艺数据为:
(1)反应器温度1500C,压力0.14MPa(绝压,以下同);
(2)一、二级冷凝器压力0.13MPa;
(3)甲醇进料温度20℃,压力0.15MPa;
(4)氯化氢进料温度20℃,压力。
.15MPa;
(5)甲醇汽体过热温度120 ℃,压力0.15MPa;
(6)返回反应器的循环液压力0.15MPa;
(7)离开二级冷凝器的气体温度40 ℃;
(8)甲醇的总转化率90%(摩尔);
(9)进料甲醇和氯化氢的摩尔比1;1.1;
5、建厂地点:兰州
二、设计工作内容(建议):
第一部分前言
第二部分文献概述
第三部分设计的内容及要求
3.1设计范围及技术方案的确定
3.2设计内容及深度要求
3.2.1浓盐酸提馏制氯化氢系统
3.2.2一氯甲烷合成系统
第四部分氯化氢提馏工艺设计计算
4.1提馏系统工艺设计计算
4.1.1计算模型
4.1.2计算步骤
4.1.3计算结果
4.2提馏系统主要设备设计计算
4.2.1填料提馏塔
4.2.2一级冷凝器
4.2.3二级冷凝器
4.2.4塔底再沸器
4.2.5浓酸预热器
4.3提馏塔内件设计计算
4.3.1.进料液体分布器
第五部分氯甲烷合成系统设计计算
5.1合成系统工艺设计计算
5.2合成系统主要设备设计计算
第六部分主要参考资料
第七部分外文文献翻译(2篇)
三、绘制设计图
1. 机绘带主要控制点的氯化氢提馏工艺流程图一张(A1);
2. 手绘以盐酸为原料合成一氯甲烷的物料平衡图一张(A2);
3. 机绘提馏塔的工艺尺寸图一张(A2)。
四、设计进程
五、主要参考文献
[1] 汤月明.新建甲烷氯化物装置简介.中国氯碱.2001
[2] 方源福.甲醇氢氯化技术.中国氯碱通讯1989
[3] 乐晓兵.Stauffer化学公司甲烷氯化物技术.中国氯碱.1996
[4]俞潭洋.甲醇液氯法联产氯代甲烷的工艺特点及其发展前景.上海化工.1998
[5] 艾米.日本有机硅工业发展动向.化工新型材料.1990
[6]黄立道.我国有机硅单体产业发展形势分析.中国化工信息.2000
[7] 郑建军.我国三大有机硅单体生产装置发展概述.化工新型材料.1999
[8] 幸松民.加速我国的有机硅单体工业.中国化工.1997
[9] 北京石油化工工程公司.氯碱工业理化常数手册[M].化学工业出版社, 1989.
[10] Gustin J L. Safety of chlorine production and chlorination processes[J]. Chemical Health and
Safety, 2005, 12(1):5-16
[11] Phabyanno R L, Almir M, Marcio H S A, et al. Energy loss in electrochemical diaphragm
process of chlorine and alkali industry–A collateral effect of the undesirable generation of chlorate[J]. Energy, 2010, 35(5): 2174-2178.。