铸件超声波探伤特点及方法
铸件和锻件的超声波探伤方法应用

• 白点是因钢中含氢量较高时由锻造过程中 残余应力热加工后的相变应力和热应力等 原因产生,是一种细微的氢裂纹,在白点 纵向断口上呈银白色的园点或椭圆形斑点, 故称白点。
• 热处理缺陷:裂纹。由热处理工艺参数 不良引起。
• 二、探伤方法概述 • 轴类锻件探伤
①纵波(直探头)可在轴的园周方向和轴端部探 测。
• Δ也可用二次底波B1和B2调。工件只有一 个厚度,如某饼型锻件厚300mm,直径很 大,可利用始波T和B1调(但不太准)因T 对零,B1对某刻度,如8格,此时忽略了探
头中引起混响和保护膜引起的延迟,严格 说调好后始波不在零位,而是略后左移。
• 双晶直探头:
• 可在JB/T4730-2005双晶直探头标准试块 上调节,使始波对零,深45mm平底孔在第 8格以内。
• 疏松是由钢锭凝固时形成的不致密和孔穴, 锻造时锻压比不够未全熔合造成,主要存 在于钢锭中心及头部。铸造引起裂纹主要 是指锻钢件表面上出现的较浅的龟状表面 缺陷也称龟裂,是由于原材料成份不当, 表面状况不好,加热温度和加热时间不合 适等原因产生。
• 锻造缺陷:折叠、白点、裂纹等。
• 锻造裂纹可出现在工件中不同位置,可由缩孔残 余在锻造时扩大产生,表面下气泡锻造产生,柱 状晶粗大引起,轴芯晶间裂纹锻造时引起,非金 属夹杂物引起,锻造加热不当引起,锻造变形不
• 测:当量、位置。如分散性夹层、夹杂等。
• 3. 密集缺陷□--可能是疏松、非金属夹杂、 白点或成群小裂纹。
• 定义:JB/T4730-2005标准术语和定义第 3.16条规定。
• 在荧光屏扫描线上相当于50mm声程范围内 有5个或5个以上缺陷反射信号,或在 50mm×50mm检测面上发现在同一深度范 围内有5个或5个以上缺陷反射信号。其反
铝铸件超声波探伤标准

铝铸件超声波探伤标准超声波探伤是一种非常有效的无损检测技术,广泛应用于工业领域。
对于铝铸件这样的重要零部件,超声波探伤尤其重要。
本文将介绍铝铸件超声波探伤的标准和要求。
一、超声波探伤的目的铝铸件超声波探伤的目的是检测和评估铝铸件中的内部缺陷或不均匀性,以确定铸件的质量和可用性。
通过超声波探伤可以发现铸件中的气孔、夹杂物、裂纹等缺陷,对铝铸件的质量进行全面评估。
二、超声波探伤的方法常用的超声波探伤方法包括脉冲回波法和光栅频谱法。
脉冲回波法主要适用于探测铝铸件中的大型缺陷,如气孔和裂纹;光栅频谱法主要用于检测小型缺陷和不均匀性。
三、超声波探伤的设备和参数铝铸件超声波探伤的设备应选择频率适当、功率稳定,并采用合适的探头和耦合剂。
常用的频率范围为2-10 MHz。
超声波的传播速度和衰减系数是评估铝铸件质量的重要参数,应按照标准要求进行测定。
四、超声波探伤的标准和要求 1. 缺陷的评估要按照国际标准进行,包括缺陷的尺寸、形状、位置、数量等方面的评估。
2. 对于铝铸件中的气孔缺陷,应按照国际标准分类,并根据其尺寸和位置进行定级。
3. 对于铝铸件中的夹杂物缺陷,除了评估其尺寸、形状和位置外,还应评估其类型和数量。
4. 对于铝铸件中的裂纹缺陷,应评估其长度、深度、宽度和形状,并根据其特征进行分类。
5. 对于铝铸件的不均匀性,应评估其厚度、密度和声速的分布情况,确保其在规定范围内。
五、超声波探伤的操作要求 1. 操作人员应经过专业培训,熟悉超声波探伤设备的使用和操作。
2. 在进行超声波探伤前,需要对探头和样品进行校准,保证探头的灵敏度和精度。
3. 超声波探伤应按照标准的检测路径和扫描方式进行,确保全面覆盖铝铸件的各个部位。
4. 探测到缺陷后,应进行记录和标记,包括缺陷的位置、尺寸和形状等信息。
六、超声波探伤的结果评估超声波探伤结果的评估应根据标准要求进行,对于超过规定尺寸和数量的缺陷,铝铸件应被判定为不合格,并采取相应的措施修复或淘汰。
锻件与铸件超声波探伤详细教程(附实例解析)讲解
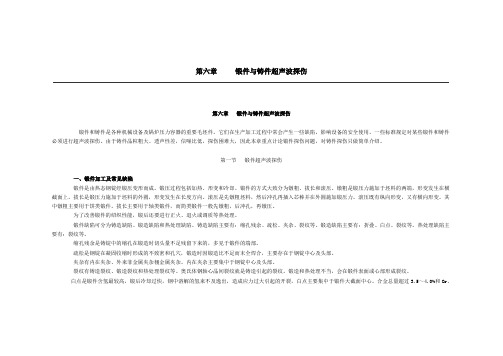
第六章锻件与铸件超声波探伤第六章锻件与铸件超声波探伤锻件和铸件是各种机械设备及锅炉压力容器的重要毛坯件。
它们在生产加工过程中常会产生一些缺陷,影响设备的安全使用。
一些标准规定对某些锻件和铸件必须进行超声波探伤。
由于铸件晶粒粗大、透声性差,信噪比低,探伤困难大,因此本章重点计论锻件探伤问题,对铸件探伤只做简单介绍。
第一节锻件超声波探伤一、锻件加工及常见缺陷锻件是由热态钢锭经锻压变形而成。
锻压过程包括加热、形变和冷却。
锻件的方式大致分为镦粗、拔长和滚压。
镦粗是锻压力施加于坯料的两端,形变发生在横截面上。
拔长是锻压力施加于坯料的外圆,形变发生在长度方向。
滚压是先镦粗坯料,然后冲孔再插入芯棒并在外圆施加锻压力。
滚压既有纵向形变,又有横向形变。
其中镦粗主要用于饼类锻件。
拔长主要用于轴类锻件,而简类锻件一般先镦粗,后冲孔,再镦压。
为了改善锻件的绍织性能,锻后还要进行正火、退火或调质等热处理。
锻件缺陷可分为铸造缺陷、锻造缺陷和热处理缺陷。
铸造缺陷主要有:缩孔残余、疏松、夹杂、裂纹等。
锻造缺陷主要有:折叠、白点、裂纹等。
热处理缺陷主要有:裂纹等。
缩孔残余是铸锭中的缩孔在锻造时切头量不足残留下来的,多见于锻件的端部。
疏松是钢锭在凝固收缩时形成的不致密和孔穴,锻造时因锻造比不足而末全焊合,主要存在于钢锭中心及头部。
夹杂有内在夹杂、外来菲金属夹杂栩金属夹杂。
内在夹杂主要集中于钢锭中心及头部。
裂纹有铸造裂纹、锻造裂纹和热处理裂纹等。
奥氏体钢轴心晶间裂纹就是铸造引起的裂纹。
锻造和热处理不当,会在锻件表面或心部形成裂纹。
白点是锻件含氢最较高,锻后冷却过快,钢中溶解的氢来不及逸出,造成应力过大引起的开裂,白点主要集中于锻件大截面中心。
合金总量超过3.5~4.0%和Cr、Ni、Mn的合金钢大型锻件容易产生白点。
白点在钢中总是成群出现。
二、探伤方法概述按探伤时间分类,锻件探伤可分为原材料探伤和制造过程中的探伤,产品检验及在役检验。
浅谈铸件疏松和超声波检测的优点
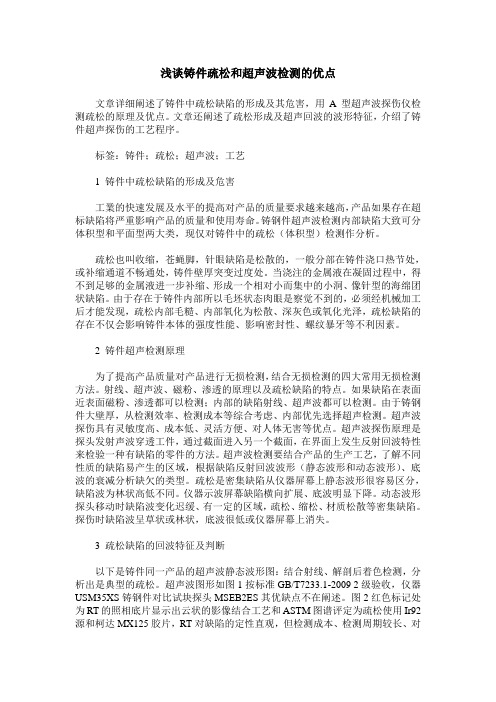
浅谈铸件疏松和超声波检测的优点文章详细阐述了铸件中疏松缺陷的形成及其危害,用A型超声波探伤仪检测疏松的原理及优点。
文章还阐述了疏松形成及超声回波的波形特征,介绍了铸件超声探伤的工艺程序。
标签:铸件;疏松;超声波;工艺1 铸件中疏松缺陷的形成及危害工業的快速发展及水平的提高对产品的质量要求越来越高,产品如果存在超标缺陷将严重影响产品的质量和使用寿命。
铸钢件超声波检测内部缺陷大致可分体积型和平面型两大类,现仅对铸件中的疏松(体积型)检测作分析。
疏松也叫收缩,苍蝇脚,针眼缺陷是松散的,一般分部在铸件浇口热节处,或补缩通道不畅通处,铸件壁厚突变过度处。
当浇注的金属液在凝固过程中,得不到足够的金属液进一步补缩、形成一个相对小而集中的小洞、像针型的海绵团状缺陷。
由于存在于铸件内部所以毛坯状态肉眼是察觉不到的,必须经机械加工后才能发现,疏松内部毛糙、内部氧化为松散、深灰色或氧化光泽,疏松缺陷的存在不仅会影响铸件本体的强度性能、影响密封性、螺纹暴牙等不利因素。
2 铸件超声检测原理为了提高产品质量对产品进行无损检测,结合无损检测的四大常用无损检测方法。
射线、超声波、磁粉、渗透的原理以及疏松缺陷的特点。
如果缺陷在表面近表面磁粉、渗透都可以检测;内部的缺陷射线、超声波都可以检测。
由于铸钢件大壁厚,从检测效率、检测成本等综合考虑、内部优先选择超声检测。
超声波探伤具有灵敏度高、成本低、灵活方便、对人体无害等优点。
超声波探伤原理是探头发射声波穿透工件,通过截面进入另一个截面,在界面上发生反射回波特性来检验一种有缺陷的零件的方法。
超声波检测要结合产品的生产工艺,了解不同性质的缺陷易产生的区域,根据缺陷反射回波波形(静态波形和动态波形)、底波的衰减分析缺欠的类型。
疏松是密集缺陷从仪器屏幕上静态波形很容易区分,缺陷波为林状高低不同。
仪器示波屏幕缺陷横向扩展、底波明显下降。
动态波形探头移动时缺陷波变化迟缓、有一定的区域,疏松、缩松、材质松散等密集缺陷。
铸钢件超声探伤及质量评级方法
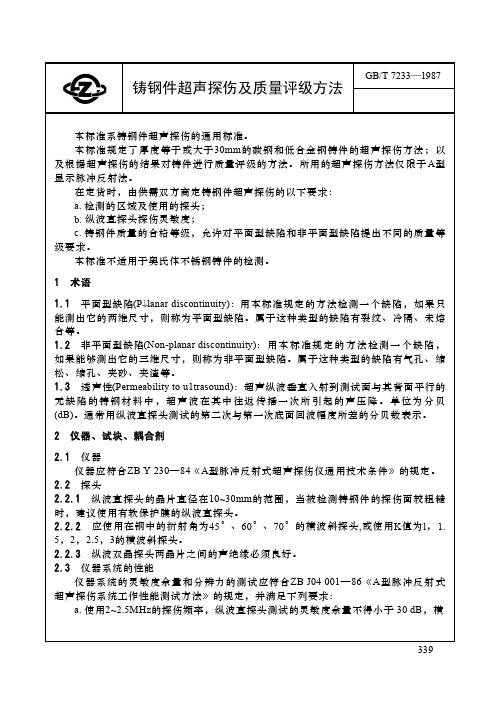
本标准系铸钢件超声探伤的通用标准。
本标准规定了厚度等于或大于及根据超声探伤的结果对铸件进行质量评级的方法。
所用的超声探伤方法仅限于339—GB/T 72331987340波斜探头测试的灵敏度余量不得小于。
50dB 在相应的探伤频率范围,纵波直探头和横波斜探头测试的分辨力应满足表的规b. 1定。
表仪器系统分辨力的下限值1 探头种类纵波直探头横波斜探头探伤频率,MHz<22~3>32~5分辨力,dB61520122.4试块2.4.1对比试块用铸造碳钢或低合金钢材料制做,其超声衰减系数应与被探伤铸钢件材 料的衰减系数相同或相近。
制做对比试块的材料必须预先进行超声探伤,不允许存在等于或大于同声程φ当量2平底孔的缺陷。
对比试块侧面要标明试块的名称、编号、材质、透声性。
2.4.2 供纵波直探头用的系列对比试块见附录(补充件)。
当被探伤铸钢件的厚ZGZ A 度大于时,要制做最大探250mm 测距离等于铸钢件厚度的试块。
系列对比试块仅在用试块调整纵波直探头探伤灵敏度时才使用。
ZGZ 2.4.3供 纵波双晶探头用的对比试块见附录补充件ZGS B()。
2.5耦合剂通常可选用机油、水溶性耦合剂、机油与黄甘油混合剂、水或浆糊作为耦合剂。
耦合剂不得在铸钢件成品上造成不允许的锈蚀。
调整仪器、校核仪器和检测铸钢件必须使用同种耦合剂。
3铸钢件3.1探伤面3.1.1铸钢件应在外观检查合格后进行超声探伤,铸钢件的探伤面及其背面所有影响超 声检测的物质应予清除。
3.1.2铸钢件探伤面的表面粗糙度应满足以下要求:机械加工表面,a. R 等于或小于。
a 10µm 铸造表面,b. R 等于或小于。
a 12.5µm 3.1.3如机械加工之后铸钢件的形状妨碍超声探伤时,应在加工之前进行检测。
3.2铸钢件壁厚层次的划分3.2.1 按交货时铸钢件的外形,将铸钢件的截面厚度划分为三层:外层、内层、外层。
铸钢件的厚度或截面尺寸小于者,各层各占厚度或截面尺寸的三分之一。
铸件的探伤报告

铸件的探伤报告一、引言探伤是一个重要的非破坏性检测方法,用于检测各种材料中的内部缺陷和表面缺陷。
在铸造工艺中,铸件探伤是确保铸件质量的关键步骤之一。
本文将对铸件的探伤报告进行详细介绍。
二、探伤方法常用的铸件探伤方法包括: - 声波探伤 - 磁粉探伤 - 超声波探伤 - X射线探伤三、探伤报告本次探伤针对XX公司的某型号铸件进行,采用超声波探伤方法进行检测。
以下为探伤报告的具体内容:1. 铸件信息•铸件材料:铸铁•铸件尺寸:直径300mm,高度150mm2. 探伤设备及参数•探伤设备:XX超声波探伤仪•探头频率:2MHz•脉冲重复频率:5kHz•脉冲宽度:100μs3. 探伤结果本次探伤对铸件进行了全面的扫描,发现了以下缺陷:缺陷1:声速变化•位置:铸件底部•形状:不规则•大小:直径约30mm•建议:进一步检测以确定缺陷性质缺陷2:表面裂纹•位置:铸件侧面•形状:直线状•长度:约50mm•深度:约2mm•建议:进行修补以提高铸件的完整性缺陷3:内部气孔•位置:铸件中心部分•形状:球状•大小:直径约10mm•数量:共计5个•建议:进行再铸造以改善材料质量4. 结论通过超声波探伤,我们检测到了铸件的一些缺陷,其中包括声速变化、表面裂纹和内部气孔。
根据检测结果,我们建议进一步检测以确定缺陷的性质,并进行相应的修补或再铸造,以提高铸件的质量。
四、总结铸件的探伤报告是检测铸件质量的重要依据,通过合适的探伤方法和设备,可以有效地检测出铸件的内部和表面缺陷。
本报告中使用超声波探伤方法对铸件进行了全面的检测,并给出了具体的缺陷情况和处理建议。
在实际应用中,应根据具体情况选择适合的探伤方法,并根据检测结果采取相应的措施,以确保铸件的质量和安全性。
铸件超声波探伤标准

铸件超声波探伤标准铸件超声波探伤是一种常用的无损检测方法,它能够有效地检测出铸件内部的缺陷和异物,对铸件的质量控制起着至关重要的作用。
本文将介绍铸件超声波探伤的标准,以及在实际应用中的注意事项和技术要点。
首先,铸件超声波探伤的标准主要包括国家标准、行业标准和企业标准。
国家标准是对铸件超声波探伤的技术要求和检测方法进行规范,确保其检测结果的准确性和可靠性。
行业标准是在国家标准的基础上,针对具体行业的特殊要求进行制定的,例如航空航天、汽车制造等行业都有相应的行业标准。
而企业标准则是根据企业自身的生产特点和技术水平进行制定的,旨在提高产品质量和生产效率。
其次,铸件超声波探伤的标准主要包括以下几个方面,探伤设备的选择和校准、探伤人员的培训和资质认证、探伤工艺的规范和操作流程、探伤结果的评定和记录等。
在实际应用中,需要严格按照标准的要求进行操作,确保探伤结果的准确性和可靠性。
另外,铸件超声波探伤的标准还包括对不同类型铸件的不同要求。
例如,对于铸铁件、铸钢件和铝合金铸件,其超声波探伤的技术要点和操作规程都有所不同。
在实际应用中,需要根据具体的铸件材质和结构特点,选择合适的探伤方法和参数,以确保对铸件内部缺陷的有效检测。
最后,铸件超声波探伤标准的制定和实施对于提高铸件质量、保障产品安全具有重要意义。
通过严格遵守标准的要求,可以有效地减少铸件内部缺陷的产生,提高产品的合格率和可靠性,降低因质量问题而造成的损失和风险。
综上所述,铸件超声波探伤标准是保障铸件质量和产品安全的重要保障,其制定和实施对于提高铸件质量、降低生产风险具有重要意义。
在实际应用中,需要严格遵守标准的要求,确保铸件超声波探伤工作的准确性和可靠性,为企业的可持续发展提供有力支持。
锻件与铸件超声波探伤详细教程(附实例解析)重点讲义资料
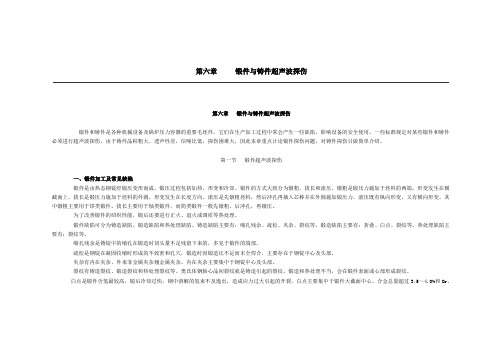
第六章锻件与铸件超声波探伤第六章锻件与铸件超声波探伤锻件和铸件是各种机械设备及锅炉压力容器的重要毛坯件。
它们在生产加工过程中常会产生一些缺陷,影响设备的安全使用。
一些标准规定对某些锻件和铸件必须进行超声波探伤。
由于铸件晶粒粗大、透声性差,信噪比低,探伤困难大,因此本章重点计论锻件探伤问题,对铸件探伤只做简单介绍。
第一节锻件超声波探伤一、锻件加工及常见缺陷锻件是由热态钢锭经锻压变形而成。
锻压过程包括加热、形变和冷却。
锻件的方式大致分为镦粗、拔长和滚压。
镦粗是锻压力施加于坯料的两端,形变发生在横截面上。
拔长是锻压力施加于坯料的外圆,形变发生在长度方向。
滚压是先镦粗坯料,然后冲孔再插入芯棒并在外圆施加锻压力。
滚压既有纵向形变,又有横向形变。
其中镦粗主要用于饼类锻件。
拔长主要用于轴类锻件,而简类锻件一般先镦粗,后冲孔,再镦压。
为了改善锻件的绍织性能,锻后还要进行正火、退火或调质等热处理。
锻件缺陷可分为铸造缺陷、锻造缺陷和热处理缺陷。
铸造缺陷主要有:缩孔残余、疏松、夹杂、裂纹等。
锻造缺陷主要有:折叠、白点、裂纹等。
热处理缺陷主要有:裂纹等。
缩孔残余是铸锭中的缩孔在锻造时切头量不足残留下来的,多见于锻件的端部。
疏松是钢锭在凝固收缩时形成的不致密和孔穴,锻造时因锻造比不足而末全焊合,主要存在于钢锭中心及头部。
夹杂有内在夹杂、外来菲金属夹杂栩金属夹杂。
内在夹杂主要集中于钢锭中心及头部。
裂纹有铸造裂纹、锻造裂纹和热处理裂纹等。
奥氏体钢轴心晶间裂纹就是铸造引起的裂纹。
锻造和热处理不当,会在锻件表面或心部形成裂纹。
白点是锻件含氢最较高,锻后冷却过快,钢中溶解的氢来不及逸出,造成应力过大引起的开裂,白点主要集中于锻件大截面中心。
合金总量超过3.5~4.0%和Cr、Ni、Mn的合金钢大型锻件容易产生白点。
白点在钢中总是成群出现。
二、探伤方法概述按探伤时间分类,锻件探伤可分为原材料探伤和制造过程中的探伤,产品检验及在役检验。
- 1、下载文档前请自行甄别文档内容的完整性,平台不提供额外的编辑、内容补充、找答案等附加服务。
- 2、"仅部分预览"的文档,不可在线预览部分如存在完整性等问题,可反馈申请退款(可完整预览的文档不适用该条件!)。
- 3、如文档侵犯您的权益,请联系客服反馈,我们会尽快为您处理(人工客服工作时间:9:00-18:30)。
铸件超声波探伤特点及方法
铸件的生产过程较为复杂,要保证铸件的质量,必须掌握冶炼、造型、浇注、出模、热处理等一系列工艺环节。
然而,在铸件中很难避免出现一些如裂纹、气泡、夹杂、疏松、缩孔等缺陷。
近年来,铸件品种不断增加,质量要求更高了,为此用超声波探伤仪对铸件内部缺陷进行探伤检测是很必要的。
一、铸件超声波探伤的特点
1。
铸件内部一般晶粒较粗,组织不均匀且不致密,与锻件相比,铸件衰减大,穿透性能差。
2。
在不均匀的粗大结构的界面上会产生漫反射,在荧光屏上会出现杂乱的晶界反射波。
特别在用高频率探伤时,尤为显著,妨碍对缺陷的判别。
3。
一般铸件自然表面的光洁度差,不易获得良好的声耦合。
4。
由于上述原因,造成铸件的探测灵敏度降低,只能发现面积较大的缺陷。
5。
铸件中的缺陷,多数呈有一定体积,常有多种形状和性质的缺陷混在一起,形状复杂、无明显方向,但出现部位有一定规律。
二、铸件超声波探伤的方法
在铸件中,铸钢(除奥氏体铸钢外)的穿透性较铸铁件好,探测频率可用2~6兆赫。
而铸铁、铸铜等穿透性较差,探测频率可用0。
5~2兆赫。
粗糙的铸钢件。
其表面光洁度差,使入射的声能减小,若用普通的机油做耦合剂,几乎不嫩探测,一般需用水浸法或黏度大的耦合剂或敷设塑料薄膜等方法探测。
为提高发现缺陷的能力,铸件一般需经粗加工,使光洁度符合探伤要求。
探伤铸件的方法,通常采用多次脉冲反射法,有时也用一次脉冲反射法来确定缺陷位置。
多次脉冲发射法是利用声波在缺陷界面的反射和缺陷对声波衰减的原理进行探测的。
对于较厚且形状简单的工件,用此方法探测是比较适宜的。
当工件内部无缺陷时,则出现铸件底部的多次反射波,其波幅铸件减小,并呈指数曲线衰减,如下图a所示,当工件内部存在疏松等缺陷时,会造成声波散射,使声能衰减,则底波反射次数减少,如下图b所示,当工件内部存在严重的缺陷,则底波消失或只有杂波,如下图c所示。
由工件底波的衰减状态,即可判断有无缺陷和严重程度。
图1:多次脉冲反射法探测铸件时的波形
(a:无缺陷时的波形;b:一般缺陷时的波形;c:严重缺陷时的波形。
)
若用一次脉冲反射法探测时,则由缺陷波的状态来判断铸件质量。
在正常情况下,有底波反射,若工件内部有缺陷时,其波形大致有三种:第一种是只有缺陷波或杂波而无底波,此属严重缩孔和疏松缺陷;第二种是有缺陷波而底波显著降低,此属一般缩孔或疏松;第三种是缺陷波与底波同时存在,底波无明显降低,此属单个缺陷。
铸件的生产过程较为复杂,要保证铸件的质量,必须掌握冶炼、造型、浇注、出模、热处理等一系列工艺环节。
然而,在铸件中很难避免出现一些如裂纹、气泡、夹杂、疏松、缩孔等缺陷。
近年来,铸件品种不断增加,质量要求更高了,为此用超声波探伤仪对铸件内部缺陷进行探伤检测是很必要的。
一、铸件超声波探伤的特点
1。
铸件内部一般晶粒较粗,组织不均匀且不致密,与锻件相比,铸件衰减大,穿透性能差。
2。
在不均匀的粗大结构的界面上会产生漫反射,在荧光屏上会出现杂乱的晶界反射波。
特别在用高频率探伤时,尤为显著,妨碍对缺陷的判别。
3。
一般铸件自然表面的光洁度差,不易获得良好的声耦合。
4。
由于上述原因,造成铸件的探测灵敏度降低,只能发现面积较大的缺陷。
5。
铸件中的缺陷,多数呈有一定体积,常有多种形状和性质的缺陷混在一起,形状复杂、无明显方向,但出现部位有一定规律。
二、铸件超声波探伤的方法
在铸件中,铸钢(除奥氏体铸钢外)的穿透性较铸铁件好,探测频率可用2~6兆赫。
而铸铁、铸铜等穿透性较差,探测频率可用0。
5~2兆赫。
粗糙的铸钢件。
其表面光洁度差,使入射的声能减小,若用普通的机油做耦合剂,几乎不嫩探测,一般需用水浸法或黏度大的耦合剂或敷设塑料薄膜等方法探测。
为提高发现缺陷的能力,铸件一般需经粗加工,使光洁度符合探伤要求。
探伤铸件的方法,通常采用多次脉冲反射法,有时也用一次脉冲反射法来确定缺陷位置。
多次脉冲发射法是利用声波在缺陷界面的反射和缺陷对声波衰减的原理进行探测的。
对于较厚且形状简单的工件,用此方法探测是比较适宜的。
当工件内部无缺陷时,则出现铸件底部的多次反射波,其波幅铸件减小,并呈指数曲线衰减,如下图a所示,当工件内部存在疏松等缺陷时,会造成声波散射,使声能衰减,则底波反射次数减少,如下图b所示,当工件内部存在严重的缺陷,则底波消失或只有杂波,如下图c所示。
由工件底波的衰减状态,即可判断有无缺陷和严重程度。
图1:多次脉冲反射法探测铸件时的波形
(a:无缺陷时的波形;b:一般缺陷时的波形;c:严重缺陷时的波形。
)
若用一次脉冲反射法探测时,则由缺陷波的状态来判断铸件质量。
在正常情况下,有底波反射,若工件内部有缺陷时,其波形大致有三种:第一种是只有缺陷波或杂波而无底波,此属严重缩孔和疏松缺陷;第二种是有缺陷波而底波显著降低,此属一般缩孔或疏松;第三种是缺陷波与底波同时存在,底波无明显降低,此属单个缺陷。