薄板成型简介
薄板制作工艺流程概述
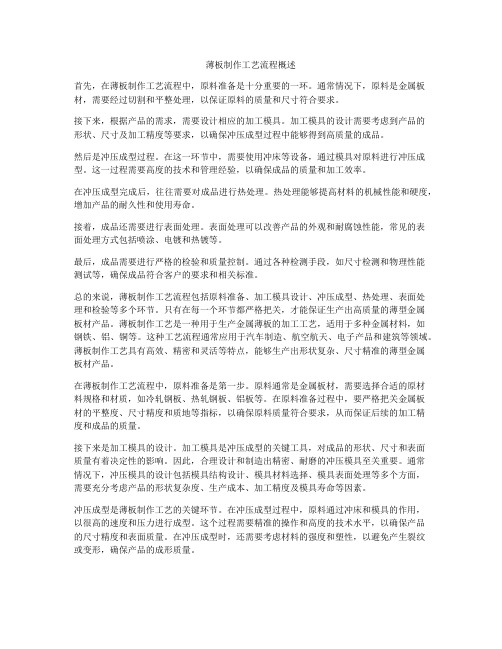
薄板制作工艺流程概述首先,在薄板制作工艺流程中,原料准备是十分重要的一环。
通常情况下,原料是金属板材,需要经过切割和平整处理,以保证原料的质量和尺寸符合要求。
接下来,根据产品的需求,需要设计相应的加工模具。
加工模具的设计需要考虑到产品的形状、尺寸及加工精度等要求,以确保冲压成型过程中能够得到高质量的成品。
然后是冲压成型过程。
在这一环节中,需要使用冲床等设备,通过模具对原料进行冲压成型。
这一过程需要高度的技术和管理经验,以确保成品的质量和加工效率。
在冲压成型完成后,往往需要对成品进行热处理。
热处理能够提高材料的机械性能和硬度,增加产品的耐久性和使用寿命。
接着,成品还需要进行表面处理。
表面处理可以改善产品的外观和耐腐蚀性能,常见的表面处理方式包括喷涂、电镀和热镀等。
最后,成品需要进行严格的检验和质量控制。
通过各种检测手段,如尺寸检测和物理性能测试等,确保成品符合客户的要求和相关标准。
总的来说,薄板制作工艺流程包括原料准备、加工模具设计、冲压成型、热处理、表面处理和检验等多个环节。
只有在每一个环节都严格把关,才能保证生产出高质量的薄型金属板材产品。
薄板制作工艺是一种用于生产金属薄板的加工工艺,适用于多种金属材料,如钢铁、铝、铜等。
这种工艺流程通常应用于汽车制造、航空航天、电子产品和建筑等领域。
薄板制作工艺具有高效、精密和灵活等特点,能够生产出形状复杂、尺寸精准的薄型金属板材产品。
在薄板制作工艺流程中,原料准备是第一步。
原料通常是金属板材,需要选择合适的原材料规格和材质,如冷轧钢板、热轧钢板、铝板等。
在原料准备过程中,要严格把关金属板材的平整度、尺寸精度和质地等指标,以确保原料质量符合要求,从而保证后续的加工精度和成品的质量。
接下来是加工模具的设计。
加工模具是冲压成型的关键工具,对成品的形状、尺寸和表面质量有着决定性的影响。
因此,合理设计和制造出精密、耐磨的冲压模具至关重要。
通常情况下,冲压模具的设计包括模具结构设计、模具材料选择、模具表面处理等多个方面,需要充分考虑产品的形状复杂度、生产成本、加工精度及模具寿命等因素。
金属塑性加工的润滑(金属加工之二)
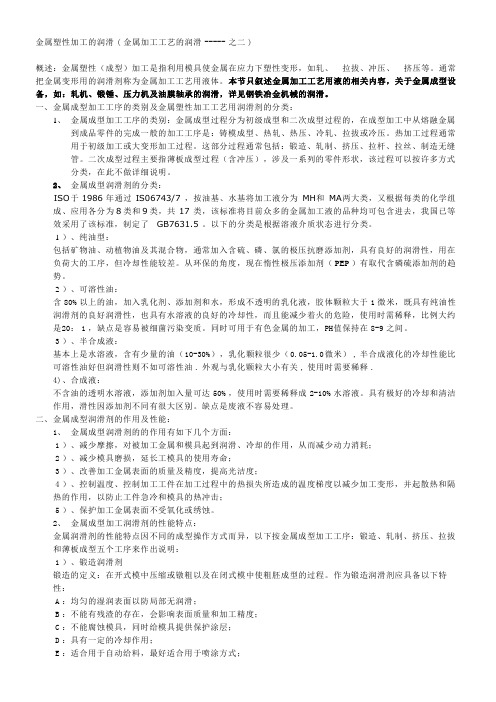
金属塑性加工的润滑(金属加工工艺的润滑-----之二)概述:金属塑性(成型)加工是指利用模具使金属在应力下塑性变形,如轧、拉拔、冲压、挤压等。
通常把金属变形用的润滑剂称为金属加工工艺用液体。
本节只叙述金属加工工艺用液的相关内容,关于金属成型设备,如:轧机、锻锤、压力机及油膜轴承的润滑,详见钢铁冶金机械的润滑。
一、金属成型加工工序的类别及金属塑性加工工艺用润滑剂的分类:1、金属成型加工工序的类别:金属成型过程分为初级成型和二次成型过程的,在成型加工中从熔融金属到成品零件的完成一般的加工工序是:铸模成型、热轧、热压、冷轧、拉拔或冷压。
热加工过程通常用于初级加工或大变形加工过程。
这部分过程通常包括:锻造、轧制、挤压、拉杆、拉丝、制造无缝管。
二次成型过程主要指薄板成型过程(含冲压),涉及一系列的零件形状,该过程可以按许多方式分类,在此不做详细说明。
2、金属成型润滑剂的分类:ISO于1986年通过IS06743/7,按油基、水基将加工液分为MH和MA两大类,又根据每类的化学组成、应用各分为8类和9类,共17类,该标准将目前众多的金属加工液的品种均可包含进去,我国已等效采用了该标准,制定了GB7631.5。
以下的分类是根据溶液介质状态进行分类。
1)、纯油型:包括矿物油、动植物油及其混合物,通常加入含硫、磷、氯的极压抗磨添加剂,具有良好的润滑性,用在负荷大的工序,但冷却性能较差。
从环保的角度,现在惰性极压添加剂(PEP)有取代含磷硫添加剂的趋势。
2)、可溶性油:含80%以上的油,加入乳化剂、添加剂和水,形成不透明的乳化液,胶体颗粒大于1微米,既具有纯油性润滑剂的良好润滑性,也具有水溶液的良好的冷却性,而且能减少着火的危险,使用时需稀释,比例大约是20:1,缺点是容易被细菌污染变质。
同时可用于有色金属的加工,PH值保持在8-9之间。
3)、半合成液:基本上是水溶液,含有少量的油(10-30%),乳化颗粒很少(0.05-1.0微米),半合成液化的冷却性能比可溶性油好但润滑性则不如可溶性油.外观与乳化颗粒大小有关,使用时需要稀释.4)、合成液:不含油的透明水溶液,添加剂加入量可达50%,使用时需要稀释成2-10%水溶液。
铝合金冷轧及薄板生产技术
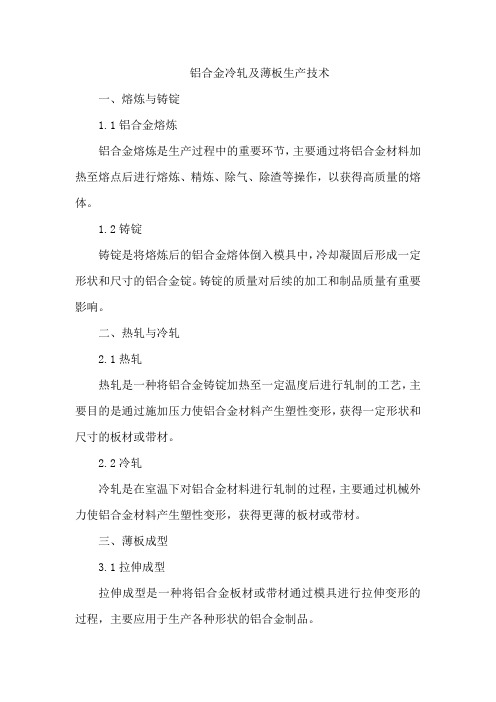
铝合金冷轧及薄板生产技术一、熔炼与铸锭1.1铝合金熔炼铝合金熔炼是生产过程中的重要环节,主要通过将铝合金材料加热至熔点后进行熔炼、精炼、除气、除渣等操作,以获得高质量的熔体。
1.2铸锭铸锭是将熔炼后的铝合金熔体倒入模具中,冷却凝固后形成一定形状和尺寸的铝合金锭。
铸锭的质量对后续的加工和制品质量有重要影响。
二、热轧与冷轧2.1热轧热轧是一种将铝合金铸锭加热至一定温度后进行轧制的工艺,主要目的是通过施加压力使铝合金材料产生塑性变形,获得一定形状和尺寸的板材或带材。
2.2冷轧冷轧是在室温下对铝合金材料进行轧制的过程,主要通过机械外力使铝合金材料产生塑性变形,获得更薄的板材或带材。
三、薄板成型3.1拉伸成型拉伸成型是一种将铝合金板材或带材通过模具进行拉伸变形的过程,主要应用于生产各种形状的铝合金制品。
3.2弯曲成型弯曲成型是一种将铝合金板材或带材通过模具进行弯曲变形的过程,主要应用于生产各种弯曲形状的铝合金制品。
四、表面处理4.1抛光抛光是通过机械或化学方法对铝合金表面进行加工,以获得光滑、亮泽的表面效果。
常用的抛光方法包括机械抛光、化学抛光和电化学抛光等。
4.2喷涂与电镀喷涂和电镀是在铝合金表面涂覆或镀覆其他金属或非金属材料,以提高铝合金制品的耐腐蚀性、美观度和功能性。
常用的喷涂和电镀材料包括油漆、塑胶、金属等。
五、质量检测5.1外观检测外观检测是对铝合金制品的表面质量进行检测的过程,主要通过目视、触觉等方法对制品的外观缺陷进行检查。
5.2尺寸检测尺寸检测是对铝合金制品的尺寸精度进行检测的过程,主要通过测量工具对制品的尺寸进行精确测量。
5.3力学性能检测力学性能检测是对铝合金制品的力学性能进行检测的过程,主要包括硬度、抗拉强度、屈服强度、延伸率等指标的检测。
六、环保与安全6.1有害物质控制铝合金冷轧及薄板生产过程中会产生一些有害物质,如废气、废水、废渣等,需要进行有效的控制和处理,以减少对环境和人体的危害。
热镀锌薄钢板介绍
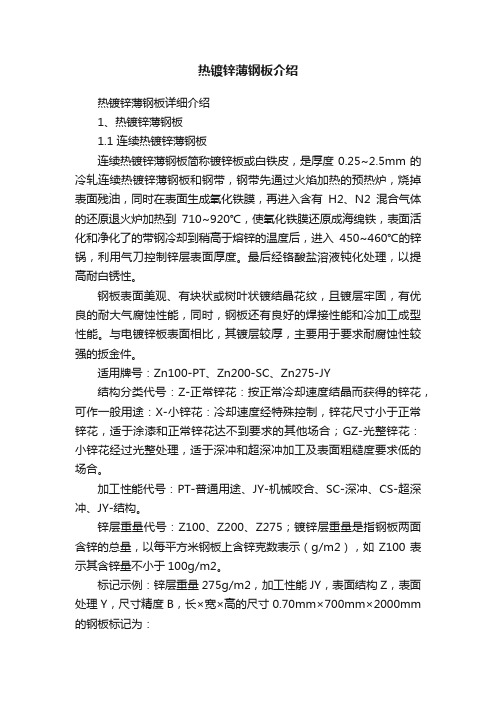
热镀锌薄钢板介绍热镀锌薄钢板详细介绍1、热镀锌薄钢板1.1 连续热镀锌薄钢板连续热镀锌薄钢板简称镀锌板或白铁皮,是厚度0.25~2.5mm的冷轧连续热镀锌薄钢板和钢带,钢带先通过火焰加热的预热炉,烧掉表面残油,同时在表面生成氧化铁膜,再进入含有H2、N2混合气体的还原退火炉加热到710~920℃,使氧化铁膜还原成海绵铁,表面活化和净化了的带钢冷却到稍高于熔锌的温度后,进入450~460℃的锌锅,利用气刀控制锌层表面厚度。
最后经铬酸盐溶液钝化处理,以提高耐白锈性。
钢板表面美观、有块状或树叶状镀结晶花纹,且镀层牢固,有优良的耐大气腐蚀性能,同时,钢板还有良好的焊接性能和冷加工成型性能。
与电镀锌板表面相比,其镀层较厚,主要用于要求耐腐蚀性较强的扳金件。
适用牌号:Zn100-PT、Zn200-SC、Zn275-JY结构分类代号:Z-正常锌花:按正常冷却速度结晶而获得的锌花,可作一般用途:X-小锌花:冷却速度经特殊控制,锌花尺寸小于正常锌花,适于涂漆和正常锌花达不到要求的其他场合;GZ-光整锌花:小锌花经过光整处理,适于深冲和超深冲加工及表面粗糙度要求低的场合。
加工性能代号:PT-普通用途、JY-机械咬合、SC-深冲、CS-超深冲、JY-结构。
锌层重量代号:Z100、Z200、Z275;镀锌层重量是指钢板两面含锌的总量,以每平方米钢板上含锌克数表示(g/m2),如Z100表示其含锌量不小于100g/m2。
标记示例:锌层重量275g/m2,加工性能JY,表面结构Z,表面处理Y,尺寸精度B,长×宽×高的尺寸0.70mm×700mm×2000mm 的钢板标记为:钢板:275-JY-Z-Y-B-0.70×700×2000-GB2518-81产地:宝钢、鞍钢和武钢等1.2 日本热浸镀锌薄钢板适用牌号:SGCC、SGCD1、SGCD2、SGCD3锌层代号:Z12、Z18、Z20、Z22、Z25、Z27符号:S-钢(Steel)、G-冷轧(Cold)、第四位C-普通级(common)、D-冲压(Draw);1、2-冲压级、3-深冲级;Z-镀锌层(Zine)、12,…,27-锌附着量×10g/m2。
钣金成型

钣金成形是对薄板、薄壁型材和薄壁管材等金属毛料施以外力,使之发生塑性变形或剪断,从而成为具有预期形状和性能的零件加工方法。
钣金成形 对薄板、薄壁型材和薄壁管材等金属毛料施以外力,使之发生塑性 变形或剪断,从而成为具有预期形状和性能的零件加工方法。
飞行器钣金零件的特点是尺寸大、刚度小、外形复杂。
生产的特点是品种多、批量小、成形方法多样化。
钣金零件种类 飞行器钣金零件可分为三类。
①具有气动力外形的零件:包括飞机机身、机翼、尾翼和进气道的蒙皮,导弹弹身、舵面的蒙皮,火箭发动机的燃烧室和喷管等。
②骨架零件:包括纵向、横向和斜向构件,如梁、桁条、隔框、翼肋等。
③内装零件:包括燃料、操纵、通信等系统以及生活服务设施中的各种钣金件,如油箱、各种导管、支架、座椅等。
对飞行器钣金零件的基本要求是:具有气动力外形的零件有准确、光滑、流线的曲面形状;骨架零件能以最小的自重保有最高的结构效率;所有钣金零件在规定的使用和贮存期限内具有要求的强度、刚度以及抗疲劳、抗腐蚀和耐热等物理化学性能。
飞行器钣金零件不但形状复杂,而且需要使用多种比强度高和耐热、抗腐蚀材料。
在各种材料中,用量最大的是硬铝、超硬铝和防锈铝合金。
铬-镍-钛不锈钢在火箭发动机中用量很大。
钛合金不但比强度高,而且耐热、抗腐蚀性能好,在飞行器钣金零件用料中所占的比例在不断增加,主要用于制造蒙皮、隔框和气瓶等零件。
主要工艺方法 飞行器钣金零件除采用机械制造中通用的各种冷冲压方法之外,还采取一些独特的成形方法。
①橡皮液压成形:向装于容框中的橡皮胎内充高压液体,使之膨胀,从而推动毛料按照模胎的形状形成零件。
这样形成的零件准确度高,表面无压痕。
橡皮胎是一种通用的柔性凹模,所以在工作台上可以安放多个不同形状的模胎。
液压机在一次循环中就能压出多个零件,因而效率高,成本低。
这种方法主要用于成形翼肋、隔框等浅弯边零件,所用设备为橡皮囊液压机。
②拉弯成形:先将型材毛料沿长度方向拉伸至屈服极限,然后保持拉力并使毛料按拉弯模的型面弯曲成形。
不锈钢成形简介讲解

100
硬度HRB
95
95.3
95.5 96.0
90
85 80
82.7 80.4 79.5 81.9 84.2 85.8
86.7
75
76.6
70
钢种
950
抗拉强度TS 905
940 927
850
750
706
650
652
717
762
674
711
606
550
498
450
钢种
450
降伏强度YS0.2%
400
406
404 413
350
330 328
327
326
300
297 275 282 294
250
钢种
0.500 0.450 0.400 0.350 0.300 0.250 0.200
3.3 n、r 值
应变硬化指数n
0.4430.4190.4060.441
0.4580.473
0.4680.445
0.408
Swift拉深试验 1-凸模 2-压边圈 3-试件 4-凹模
L DR Dmax d
拉深时筒形件上不同位置板厚变化图
D C C
A
B
厚度
拉深时筒形件上不同位置板厚变化
试样1
试样二
0.9
0.8
0.7
0.6
0.5
0.4
0.3
0.2
A
B
C
D
位置
2.6 杯凸试验( Erichsen )
试验原理:试验系用端部为球形的冲头,将夹紧的试样 压入压模内,直至出现穿透裂缝为止,所测量的杯突深 度即为试验结果Er值。
不锈钢薄板深拉伸成型工艺及模具设计

不锈钢薄板深拉伸成型工艺及模具设计伴随我国工业领域的快速发展,许多行业如汽车、电子、化工、石油等对不锈钢的应用性能提出更高的要求。
如不锈钢薄板,其作为部分产品关键零件,加工难度较大,需引入有效的加工工艺与设计方法,在加工效率提高的同时保证产品质量。
本次研究将对不锈钢薄板深拉伸成型工艺、模具设计思路以及不锈钢薄板深拉伸成型工艺与模具设计其他注意事项进行分析。
标签:不锈钢薄板;深拉伸成型工艺;模具设计前言:作为当前工业领域中常用的材料,不锈钢材料本身在工艺性能、使用性能上都有一定的优势。
本次研究中主要选择由不锈钢薄板构成的套筒为对象,不锈钢材料为06Cr19Ni10奥氏体型不锈钢,有低温韧性、可塑性、耐腐蚀性等优势,但值得注意的是做套筒加工中,若直接以传统数控加工方式为主,将面临加工难度大、费时费力等问题,此时便可考虑引入拉伸模模具成型方法,可使加工质量得以保证。
因此,本文对不锈钢薄板深拉伸成型工艺与模具设计研究,具有十分重要的意义。
1不锈钢薄板深拉伸成型工艺1.1研究对象本次研究中所选取对象为薄壁厚度为0.3mm的深型腔结构,其深度、内径比控制为2:3。
因壁厚过薄不适合采用精铸或直接数控加工,可能会导致型腔变形,且不利于大批量生产。
1.2工艺方案选择深拉伸工艺应用下,要求圆筒形件在拉伸系数、毛坯尺寸上合理控制,且保工序尺寸满足拉伸模设计要求。
以圆筒形件拉伸规律为依据,且选择拉伸面积相等为条件,进行套筒拉伸毛坯尺寸的确定,可为Φ54mm。
同时对压边圈下圆筒形拉伸件拉伸系数确定,具体确定中一般需借助相关的公式,如毛坯尺寸、工件直径、总拉伸系数分别以D、d、m表示,第1次与第n次拉伸时拉伸件直径分别以d1、dn表示,第1次与第n次拉伸系数分别以m1、mn表示,则有m=d/D=15.3/54=0.283;m1=d1/D;m2=d2/d1;mn=dn/dn-1。
由于本次研究所选取加工件需经过四次拉伸,所以需做四次拉伸系数计算,确保拉伸系数滿足加工要求。
金属薄板成形性能试验
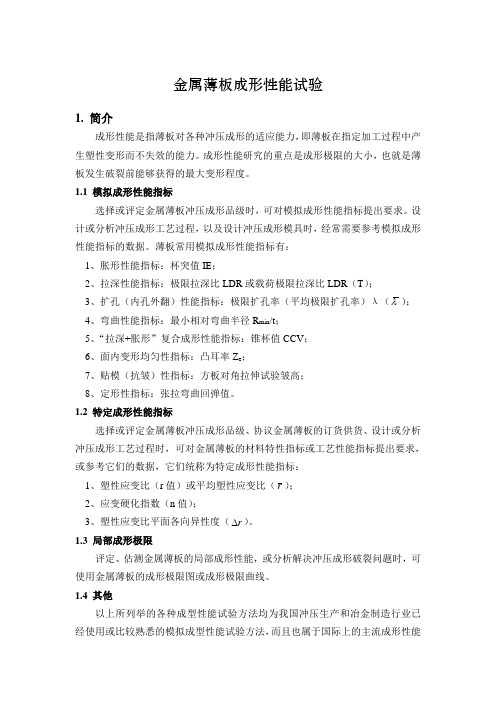
金属薄板成形性能试验1. 简介成形性能是指薄板对各种冲压成形的适应能力,即薄板在指定加工过程中产生塑性变形而不失效的能力。
成形性能研究的重点是成形极限的大小,也就是薄板发生破裂前能够获得的最大变形程度。
1.1 模拟成形性能指标选择或评定金属薄板冲压成形品级时,可对模拟成形性能指标提出要求。
设计或分析冲压成形工艺过程,以及设计冲压成形模具时,经常需要参考模拟成形性能指标的数据。
薄板常用模拟成形性能指标有:1、胀形性能指标:杯突值IE;2、拉深性能指标:极限拉深比LDR或载荷极限拉深比LDR(T);3、扩孔(内孔外翻)性能指标:极限扩孔率(平均极限扩孔率)λ(λ);4、弯曲性能指标:最小相对弯曲半径R min/t;5、“拉深+胀形”复合成形性能指标:锥杯值CCV;6、面内变形均匀性指标:凸耳率Z e;7、贴模(抗皱)性指标:方板对角拉伸试验皱高;8、定形性指标:张拉弯曲回弹值。
1.2 特定成形性能指标选择或评定金属薄板冲压成形品级、协议金属薄板的订货供货、设计或分析冲压成形工艺过程时,可对金属薄板的材料特性指标或工艺性能指标提出要求,或参考它们的数据,它们统称为特定成形性能指标:1、塑性应变比(r值)或平均塑性应变比(r);2、应变硬化指数(n值);3、塑性应变比平面各向异性度(r∆)。
1.3 局部成形极限评定、估测金属薄板的局部成形性能,或分析解决冲压成形破裂问题时,可使用金属薄板的成形极限图或成形极限曲线。
1.4 其他以上所列举的各种成型性能试验方法均为我国冲压生产和冶金制造行业已经使用或比较熟悉的模拟成型性能试验方法,而且也属于国际上的主流成形性能试验范畴。
除这些方法外,国际上还流行其他一些模拟成形性能试验,见图1。
图1 模拟成形性能试验方法注:整体成形极限指金属薄板在冲压过程中发生颈缩、破裂、皱曲等成形缺陷之前,某种特定的整体几何尺寸或某种几何特征的整体尺寸可以达到的极限变形程度。
局部成形极限指金属薄板在冲压过程中发生颈缩、破裂、皱曲等成形缺陷之前,局部点位或局部变形区域可以达到的极限变形程度。
- 1、下载文档前请自行甄别文档内容的完整性,平台不提供额外的编辑、内容补充、找答案等附加服务。
- 2、"仅部分预览"的文档,不可在线预览部分如存在完整性等问题,可反馈申请退款(可完整预览的文档不适用该条件!)。
- 3、如文档侵犯您的权益,请联系客服反馈,我们会尽快为您处理(人工客服工作时间:9:00-18:30)。
将金属薄板加工成具有不同断面形状和几何造型的制件的加工过程。薄板成 形有压缩、伸长、伸长 一压缩复合、弯曲、剪切等 5 类近 20 种基本成形方法。 (见表)对薄板成形的研究工作,在初期主要是研究成形模具、薄板材料以及润滑, 找出它们之间的相互关 系并应用于实践。随着成形工艺的发展成形设备以及成 形作业方式等方面的工作也列入了薄板成形的基本研究内容。它们之间的关系见 图。
冷弯成形的工具是轧辊。合理的冷弯辊孔型设计是决定冷弯道次和冷弯产品 质量的关键。
在模具制造技术方面,二次大战后研制成功的电火花加工和大型仿形铣床是 冲模制造的主要加工技 术和设备。模具制造周期的缩短和尺寸精度的提高使预 制模具更加容易,有助于缩短成形件生产前的准备和成形件的大批量生产。数控 铣床的发展和使用使模具制造 技术得以进一步提高。总之,对模具材料、模具 表面处理方法及加工技术的研究已成为提高模具制造技术的基础。
成形作业 如前面的图所示,如果把成形件设计、成形模具、成形设备、薄板材 料和润滑等信息看作薄板成形的第一次信息输入,则对薄板成形的输出即成形件 起重要作用的还 有第二阶段的信息输入即成形作业。它将薄板成形的所有第一 次输入信息看成是成形系统的组成部分,在考虑它们各自作用的同时还要考虑它 们的相互影响和牵制以 及对成形件产品的综合作用。成形系统的各种因素和工 艺技术参数可以有数以百计的组合,怎样全面分析、评价可能的组合,确定出成 形系统的关键工艺和技术参 数,是一个复杂的过程。这一过程中可能需要在生 产现场进行许多测量和调试。过去是靠试错来简单地作出决定,现在则是依据对 成形的认识和经验知识来进行估 算,确定一个比较合理的组合。从成品产品设 计、工艺流程制定(成形工艺选定)、模具设计、模具制造及安装调试,成形设备 及配套装置选定到成形工艺控制,都 能进行科学地预报计算和得出一个最佳组 合,是人们今后工作的目标。
成形设备 冷弯的成形设备是冷弯成形机组,冲压和板金工艺的成形设备是压力 机。压力机有机械式和液压式两类。机械式压力机有曲柄式、肘节式、连杆式、 肘板式及无曲柄 式压力机;液压式压力机有通用单缸压力机及拉延用双缸或三 缸压力机。压力机的选择要考虑到设备吨位、行程、工作台规格、精度、刚度等。 曲柄压力机适用于中 小尺寸零件的各种成形加工,大型成形件如汽车覆盖件的 成形应选用大型双缸液压机。
性应变比、硬化指数等基本 成形性和成形极限图,甚至还包括起皱(见压缩失稳) 和形状尺寸精度等对成形难易程度的影响。
反映薄板成形和使用中表面抗摩擦和损伤的表面特性及薄板使用性能中的 耐蚀性和减噪性等也是开发和使用现代化成形技术所要涉及的重要内容。
润滑 薄板与模具接触面间的摩擦除增加成形力和影响材料的流动特性外,还 会损伤模具及成形件表面,降低模具有效寿命,影响产品质量。进行润滑可以防 止模具与薄板 的表面损伤和调节接触表面的摩擦系数。薄板成形通常使用水溶 性的或者低粘度的油作润滑剂,以利于成形后脱脂废液的处理。润滑一方面要根 据固体的塑性接触以 及这种接触的物理化学现象来选择使用润滑剂,另一方面 是开发自润滑板材,在有的国家既防锈又具自润滑特性的软钢薄板已开始使用。 当然,从模具材料和表面加 工来考虑防止擦伤仍是基本的和重要的。
薄板材料 提高材料的性能和缩小性能的不均匀性,是薄板高速成形和自动化作 业的重要前提。钢和铸钢,铝和铝合金,不管是哪种材料,都是从提高延展性和 改善硬化特性来 提高材料的性能的。这些性能是模具工艺学和其他成形基本内 容间的主要结合因素,除力学性能外,还有材料的成形性(见薄板成形性)。成形 性直接用来作为开发 材料韵指南并使材料直接与成形作业的结果相结合。成形 性概念本身也在发生变化,从弯曲性能、胀形性能、拉延性能等模拟成形性到塑
成形模具 过去仅限于指成形用模具的形状和尺寸,现在已扩展到包括成形件设 计、成形工艺规划、模具设计、模具加工等构成模具工艺学范畴的内容,而这些 内容都同控制成 形件的形状和尺寸直接相关。因此,成形模具的形状、尺寸及 成形方式是薄板成形各基本内容间相互关系解析及其体系化的中心因素。
冲压和板金工艺的成形工具是冲模。为了保持凹模与凸模间准确的相对位 置,其导杆必须坚固,整 个模具需具有良好的刚性,但与此同时,模具的自重 也随之增加。由此带来的不经济性,可以通过采用一套模具进行多次成形的方法 来补偿。成形件的尺寸越大,这 种补偿就越重要。此外,模具的设计应留有修 改的余地,以便试冲时对模具设计提出修正。
子 设备的制造业中发展起来,并迅速成为薄板成形工艺的主体。冷弯则是随着 二次世界大战后建筑业和制造业对冷弯型钢的大量需求而发展起来并成为薄板 成形的一大 领域的。冲压、板金工艺和冷弯三大成形方式仅是使用的模具和成 形设备不同,它们的变形方式和规律基本一致。在薄板成形的初创时期,从模具 设计到薄板成形性 能,大量的是未知的,试错是这个时期成形的标准方法,冲 压成形系统的概念还没有形成,润滑也没有被看作成形系统中的一个重要部分。 随着研究的深入和不断实 践,对成形系统的组成部分逐渐有所了解,复杂的冲 压成形被分解为性质不同的组成部分,如拉延、胀形、弯曲、拉胀(拉延和胀形 复合成形的简称)和翻边等。认 识到薄板的硬化指数 n 值和塑性应变比 γ 值与 成形性能有关。摩擦系数被作为测定接触表面相互作用和润滑剂特性的指标。模 具材料也不断创新。
薄板基本成形方法
成形类别
基 本 成 形 方 法
伸长-
压缩类 变薄拉伸
伸长类 拉胀
旋压
扩口
拉延
胀形
翻边 压胀
压缩类 压印 缩口 校形
弯曲类 拉弯 压弯 滚弯 冷弯 折弯
剪切类 冲裁
第 1 次输入信息
薄板成形基本研究内容及其相互关系
发展简史 薄板成形的最早形式是板金工艺。公元前 4000 年,埃及人开始用手 工敲制各种铜器和金器。中国明代(1637 年)出版的宋应星著的《天工开物》中 也记载了 古代敲制铜镜的手艺。手工模具压印和局部成形出现于公元前 1500 年。冲压起源于 1400~1568 年问出现在瑞士等地的拉延。1850 年第一台曲柄压 力 机制造成功后,英国人于 1857 年首次在压力机上完成了拉延成形。1913 年 美国人用钢板冲压出汽车车身,从此,冲压成形工艺开始在汽车、家用电器及电