加工表面质量
机械制造工艺学 第四节 机械加工表面质量
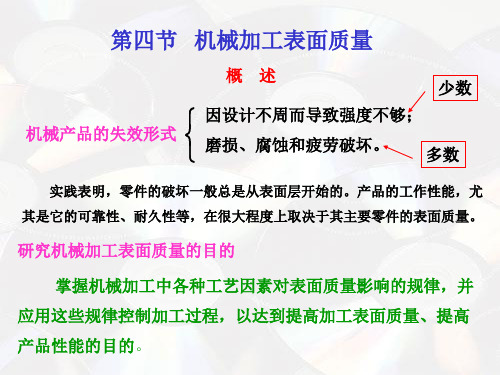
2)砂轮的粒度和砂轮的修整对表面粗糙度的影响
砂轮的粒度
磨粒间的距离
磨粒的大小
砂轮的粒度号越大, 磨粒和磨粒间离越小
砂轮的粒度号↑ ,参与磨削的磨粒↑ ,粗糙度↓ ;
修整砂轮时,纵向进给量对表面粗糙度的影响甚大; 纵向进给量↓ ,砂轮表面的等高性越好 ,粗糙度 ↓ ;
(2)金属表面层的塑性变形 在磨削过程中,由于磨粒大多具有很大的负前角,很不锋 利,所以大多数磨粒在磨削时只是对表面产生挤压作用而使表 面出现塑性变形,磨削时的高温更加剧了塑性变形,增大了表 面粗糙度值。
表面层的加工硬化对疲劳强度影响 适当的加工硬化能阻碍已有裂纹的继续扩大和新裂纹的产生,有助于 提高疲劳强度。但加工硬化程度过大,反而易产生裂纹,故加工硬化程度 应控制在一定范围内。
拉应力加剧疲劳裂纹的产生和扩展;
3.表面质量对零件耐腐蚀性的影响 表面粗糙 表面粗糙度值越大,越容易积聚腐蚀性物质; 度的影响 波谷越深,渗透与腐蚀作用越强烈。 零件的耐腐蚀性在很大程度上取决于表面粗糙度 表面残余应力对零件耐腐蚀性影响
(二)、表面层的残余应力 l、表面层残余应力及其产生的原因 表面层残余应力 外部载荷去除后,工件表面层及其与
基体材料的交界处仍残存的互相平衡的应力。
表面层残余应 力产生的原因
(1)冷态塑性变形引起的残余应力 (2)热态塑性变形引起的残余应力 (3)金相组织变化引起的残余应力
(1)冷态塑性变形引起的残余应力
其中: H——加工后表面层的显微硬度
H0——材料原有的显微硬度
(2)表面层金相组织变化
指的是加工中,由于切削热的作用引起表层金属金相组织 发生变化的现象。如磨削时常发生的磨削烧伤,大大降低表面 层的物理机械性能。 (3)表面层产生残余应力 指的是加工中,由于切削变形 和切削热的作用,工件表层及其基 体材料的交界处产生相互平衡的弹 性应力的现象。残余应力超过材料
机械加工表面质量PPT51页课件

*
3. 表面纹理对耐磨性的影响
表面纹理的形状及刀纹方向对耐磨性的影响,纹理形状及刀纹方向影响有效接触面积与润滑液的存留。
4.表面层产生的金相组织变化对零件耐磨性的影响
金相组织的变化引起基体材料硬度的变化,进而影响零件的耐磨性。
5.2 加工表面质量对零件使用性能的影响
5.2 加工表面质量对零件使用性能的影响
*
2.表面层冷作硬化与残余应力对耐疲劳性的影响 适度的表面层冷作硬化能提高零件的疲劳强度; 残余应力有拉应力和压应力之分, 残余拉应力:易使已加工表面产生裂纹并使其扩展而降低疲劳强度。 残余压应力:能够部分地抵消工作载荷施加的拉应力,延缓疲劳裂纹的扩展,从而提高零件的疲劳强度。
5.4 影响加工表面层物理机械性能的因素
*
衡量表面层加工硬化程度的指标有下列三项: 1)表面层的显微硬度H; 2)硬化层深度h; 3)硬化程度N N=(H-H0)/H0×100% 式中 H0——工件原表面层的显微硬度。
粗糙度越大,耐腐蚀性越差
压应力提高耐腐蚀性,拉应力反之则降低耐腐蚀性
总结:
*
机械加工中,表面粗糙度形成的原因大致可归纳为几何因素和物理力学因素两个方面。
(一)切削加工时表面粗糙度的影响因素
1. 几何因素
刀尖圆弧半径rε 主偏角kr、副偏角kr′ 进给量f
5.3 影响加工表面粗糙度的因素
(一)表面质量对零件耐磨性的影响
5.2 加工表面质量对零件使用性能的影响
零件磨损三个阶段:初期磨损阶段;正常磨损阶段;剧烈磨损阶段
零件耐磨性的影响因素: 摩擦副的材料;润滑条件;表面质量(接触面积)。
图5-1 磨损过程的基本规律
浅谈机械加工零件表面的质量控制措施

浅谈机械加工零件表面的质量控制措施机械加工零件表面质量对于产品的性能和外观有着重要影响,因此对于机械加工零件表面质量的控制尤为重要。
本文将从机械加工零件表面的质量要求、表面质量的评价和控制措施三个方面进行论述。
一、机械加工零件表面的质量要求机械加工零件表面的质量要求包括光洁度、平整度、粗糙度和表面缺陷等方面。
1. 光洁度要求:光洁度是指零件表面的平滑程度,光洁度的要求取决于零件所处的工作环境以及外观要求。
对于机械零件的表面,要求表面光滑、无明显的划痕和凹凸不平,以保证零件配合的精度和摩擦的稳定性。
2. 平整度要求:平整度是指零件表面的平坦程度,主要包括平面度、轮廓度等指标。
平整度的要求取决于零件的安装和工作要求,例如对于密封面零件,要求平面度较高,以确保密封性能。
3. 粗糙度要求:粗糙度是指零件表面的粗糙程度,常用Ra值来表示。
粗糙度的要求取决于零件的工作环境和功能要求,例如对于滑动副零件,要求表面粗糙度较低,以减小摩擦阻力和磨损。
4. 表面缺陷要求:表面缺陷包括划痕、毛刺、气孔、裂纹等。
表面缺陷的要求取决于零件的功能和外观要求,例如对于高精度的零件,要求表面无明显的划痕和缺陷,以保证零件的性能和外观质量。
二、表面质量的评价机械加工零件表面质量的评价可以通过目视检查、手感检查、测量检查等方法进行。
1. 目视检查:通过肉眼观察零件表面的光洁度、平整度和表面缺陷等方面的质量。
目视检查主要适用于外观质量要求较高的零件。
2. 手感检查:通过手触零件表面来判断光洁度、平整度和表面缺陷等方面的质量。
手感检查主要适用于外观质量要求较低但性能要求较高的零件。
3. 测量检查:通过使用测量仪器对零件表面的光洁度、平整度、粗糙度等指标进行测量,以得到数值化的表面质量数据。
测量检查主要适用于对表面质量有精确要求的零件。
三、控制措施为了保证机械加工零件表面质量的控制,可以采取以下措施。
1. 加工前准备措施:在进行加工前,要对机床、刀具等进行检查和维护,保证加工设备的正常运行。
金属加工表面质量的影响因素及改进措施
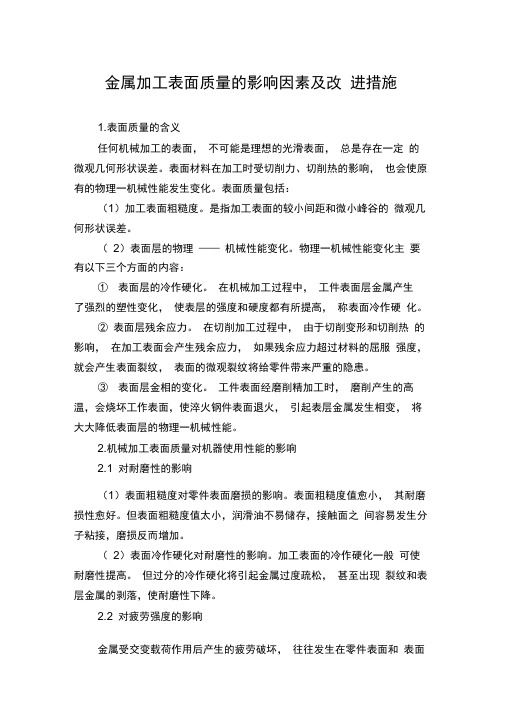
金属加工表面质量的影响因素及改进措施1.表面质量的含义任何机械加工的表面,不可能是理想的光滑表面,总是存在一定的微观几何形状误差。
表面材料在加工时受切削力、切削热的影响,也会使原有的物理一机械性能发生变化。
表面质量包括:(1)加工表面粗糙度。
是指加工表面的较小间距和微小峰谷的微观几何形状误差。
(2)表面层的物理——机械性能变化。
物理一机械性能变化主要有以下三个方面的内容:①表面层的冷作硬化。
在机械加工过程中,工件表面层金属产生了强烈的塑性变化,使表层的强度和硬度都有所提高,称表面冷作硬化。
②表面层残余应力。
在切削加工过程中,由于切削变形和切削热的影响,在加工表面会产生残余应力,如果残余应力超过材料的屈服强度,就会产生表面裂纹,表面的微观裂纹将给零件带来严重的隐患。
③表面层金相的变化。
工件表面经磨削精加工时,磨削产生的高温,会烧坏工作表面,使淬火钢件表面退火,引起表层金属发生相变,将大大降低表面层的物理一机械性能。
2.机械加工表面质量对机器使用性能的影响2.1 对耐磨性的影响(1)表面粗糙度对零件表面磨损的影响。
表面粗糙度值愈小,其耐磨损性愈好。
但表面粗糙度值太小,润滑油不易储存,接触面之间容易发生分子粘接,磨损反而增加。
(2)表面冷作硬化对耐磨性的影响。
加工表面的冷作硬化一般可使耐磨性提高。
但过分的冷作硬化将引起金属过度疏松,甚至出现裂纹和表层金属的剥落,使耐磨性下降。
2.2 对疲劳强度的影响金属受交变载荷作用后产生的疲劳破坏,往往发生在零件表面和表面冷硬层下面,因此零件的表面质量对疲劳强度影响很大。
(1)表面粗糙度对疲劳强度的影响。
在交变载荷作用下,表面粗糙度的凹谷部位容易引起应力集中,产生疲劳裂纹。
表面粗糙度值愈大,表面的纹痕愈深,纹底半径愈小,抗疲劳破坏的能力就愈差。
(2 )残余应力、冷作硬化对疲劳强度的影响。
表面层残余拉应力,将使疲劳裂纹扩大,加速疲劳破坏;而表面层残余压应力,能够阻止疲劳裂纹的扩展,延缓疲劳破坏的产生:表面冷硬化一般伴有残余压应力的产生,可以防止裂纹产生并阻止已有裂纹的扩展,对提高疲劳强度有利。
影响机械加工表面质量的因素及采取的措施

影响机械加工表面质量的因素及采取的措
施
机械加工表面质量受到多种因素的影响,以下是一些常见因素及采取的措施:
1. 切削参数:
- 切削速度:过高的切削速度可能导致表面粗糙度增加,应根据工件材料和刀具选择适当的切削速度。
- 进给速度:过高的进给速度会增加切削力,可能导致振动和不稳定,影响表面质量,应选择适当的进给速度。
- 切削深度:过大的切削深度可能导致切削力增加和刀具失稳,影响表面质量,应选择适当的切削深度。
2. 刀具选择:
- 刀具材料和涂层:选择适当的刀具材料和涂层,能够提供更好的切削性能和寿命,有利于提高表面质量。
- 刀具尺寸和几何形状:选择合适的刀具尺寸和几何形状,以确保切削稳定性和表面质量。
3. 工件夹持和支撑:
- 夹持方式:选择适当的夹持方式和夹具,确保工件固定稳定,避免振动和变形,有利于提高表面质量。
- 支撑结构:对于柔性或薄壁工件,提供适当的支撑结构,以减少振动和变形,有助于改善表面质量。
4. 切削润滑和冷却:
- 切削润滑剂:使用适当的切削润滑剂,可以减少摩擦和热量,改善切削过程,提高表面质量。
- 冷却剂:使用合适的冷却剂冷却切削区域,防止过热,减少切削力和刀具磨损,有利于提高表面质量。
5. 切削震动和振动控制:
- 刀具和工件的几何匹配:确保刀具和工件的几何匹配,减少切削震动和振动的发生,有助于提高表面质量。
- 切削参数的优化:通过调整切削参数,降低切削震动和振动的发生,有助于改善表面质量。
以上是一些常见的影响机械加工表面质量的因素和采取的措施。
在实际应用中,还需根据具体情况进行综合考虑和调整,以获得满足要求的表面质量。
加工表面质量名词解释

加工表面质量名词解释
加工表面质量是指通过加工制造过程中对零件表面的加工精度、表面形状、表面光洁度等方面的要求。
下面是一些常见的加工表面质量名词解释:
1. 光洁度:表面光滑程度的度量,通常使用Ra值表示。
Ra值越小,表面越光滑。
2. 平面度:平面与某个基准面之间的最大距离差,通常使用mm或μm表示。
3. 圆度:圆形轮廓与理论圆形之间的最大距离差,通常使用mm或μm表示。
4. 残余毛刺:加工后留在零件表面的微小凸起,通常使用μm 表示。
5. 毛坯余量:零件加工后与最终尺寸之间的距离差,通常使用mm或μm表示。
6. 粗糙度:表面的不规则程度,通常使用Rz、Rmax、Rt值表示。
Rz值越小,表面越光滑。
这些参数通常用于描述零件表面的质量要求,以确保零件能够达到其设计要求并且具有所需的性能和可靠性。
机械加工表面质量

机械加工表面质量1. 简介机械加工表面质量是机械制造过程中一个重要的质量指标,其直接影响着制品的外观和性能,特别是在涉及到接触表面的机械零件中。
机械加工表面质量的好坏会直接影响到摩擦、磨损、润滑和密封等方面的性能。
因此,对于机械加工表面质量的控制和评估非常重要。
2. 常见的机械加工表面缺陷机械加工表面质量的主要缺陷包括以下几种:2.1 粗糙度粗糙度是表面峰谷的高低起伏程度的度量,它直接影响到接触面的摩擦性能和润滑性能。
通常,粗糙度越小,表面质量越好。
2.2 铁锈机械加工过程中,如果没有采取适当的防护措施,金属表面容易受到空气中的氧气和水蒸气的腐蚀而产生铁锈。
铁锈不仅会损坏表面的光洁度,还会降低金属的强度和耐腐蚀性能。
2.3 划痕和切削工艺痕迹在机械加工过程中,操作不当或切削刀具磨损会导致表面出现划痕和切削工艺痕迹。
这些痕迹会影响零件的密封性能和外观质量。
2.4 焊接瑕疵在焊接过程中,不完全熔化、气孔、裂纹等问题容易导致焊接瑕疵。
焊接瑕疵不仅会降低表面质量,还会影响焊接接头的强度和密封性能。
2.5 水渍机械加工过程中,如果不对工件进行适当的清洗,可能会在表面留下水渍。
水渍不仅会降低表面的光洁度,还会影响涂层的附着力和防腐性能。
3. 表面质量评估为了评估机械加工表面质量,常见的方法包括目测评估和仪器测量两种。
3.1 目测评估目测评估是通过肉眼观察和触摸来对表面质量进行评估。
一般来说,表面光洁度、缺陷的数量和大小以及表面的平整程度可以通过目测进行初步评估,但是目测评估存在主观性较强,缺乏量化数据的问题。
3.2 仪器测量仪器测量可以通过使用专业的测量仪器来获取表面质量的精确数据。
常用的仪器包括三坐标测量仪、表面粗糙度测量仪等。
这些仪器可以对表面的粗糙度、平整度、峰谷高度等参数进行测量,并生成相应的数据报告。
4. 改善机械加工表面质量的方法为了改善机械加工表面质量,可以采取以下几种方法:4.1 选择合适的切削刀具和工艺参数在机械加工中,选择合适的切削刀具和工艺参数是提高表面质量的关键。
简析机械加工表面质量对零件使用性能的影响问题

简析机械加工表面质量对零件使用性能的影响问题
机械加工表面质量对零件的使用性能有很大的影响,它直接影响到零件的摩擦、磨损、耐蚀性和疲劳寿命等方面。
以下是对机械加工表面质量影响因素的简析:
1. 摩擦和磨损:机械加工表面的粗糙度会直接影响零件与其他物体之间的摩擦及磨
损情况。
如果表面太光滑,摩擦系数往往会较高,在摩擦过程中容易产生滑脱现象;而如
果表面太粗糙,摩擦系数虽然较低,但易引起磨损严重。
要根据实际情况选择合适的加工
表面质量,以达到最佳的摩擦和磨损阻力。
2. 耐蚀性:机械加工表面质量对零件的耐蚀性也有很大影响。
粗糙表面易于积存氧
化物和磨料,从而加速零件的腐蚀过程;而光滑表面往往能更好地抵御外部环境的侵蚀。
所以,在需要耐蚀性较高的零件上,要尽可能采用较为光滑的加工表面质量。
3. 疲劳寿命:机械加工表面质量还会对零件的疲劳寿命产生影响。
粗糙表面容易形
成微小的裂纹和应力集中点,从而加速零件的疲劳破坏;而光滑表面则能减少应力集中,
延长零件的使用寿命。
在需要较高疲劳寿命的零件上,应该优先考虑提高加工表面的光滑度。
机械加工的表面质量对零件的使用性能有着显著的影响。
为了提高零件的使用寿命和
工作效率,需要根据具体应用需求选择合适的加工表面质量,并通过合理的加工工艺和设备,确保零件的表面质量达到要求。
- 1、下载文档前请自行甄别文档内容的完整性,平台不提供额外的编辑、内容补充、找答案等附加服务。
- 2、"仅部分预览"的文档,不可在线预览部分如存在完整性等问题,可反馈申请退款(可完整预览的文档不适用该条件!)。
- 3、如文档侵犯您的权益,请联系客服反馈,我们会尽快为您处理(人工客服工作时间:9:00-18:30)。
零件表面质量
表面微观几 何形状特征
表面物理力 学性能变化
表面粗糙度 表面波度
表面层冷作硬化 表面层残余应力 表面层金相组织变化
(1)表面粗糙度
表面的微观几何形状误差,即L1/H1 < 40 。
(2)波度
介于加工精度(宏观,即L3/H3 > 1000 )与表面粗糙度 之间的周期性几何形状误差,即40 ≤L2/H2≤1000。它主要是 加工过程中工艺系统的振动引起。
2. 表面质量对零件疲劳强度的影响
(1)表面粗糙度对零件疲劳强度的影响
表面粗糙度越大,抗疲劳破坏的能力越差。
对承受交变载荷零件的疲劳强度影响很大。在 交变载荷作用下,表面粗糙度的凹谷部位容易引起 应力集中,产生疲劳裂纹。
表面粗糙度值越小,表面缺陷越少,工件耐疲 劳性越好;反之,加工表面越粗糙,表面的纹痕越 深,纹底半径越小,其抗疲劳破坏的能力越差。
区
纤维层 :加工材料与刀具间的
摩擦力造成。
切削热也会使表面层产生 相变
基 体
及晶粒大小变化。
材 料
二、表面质量对零件使用性能的影响
1. 表面质量对零件耐磨性的影响
(1)表面粗糙度对零件耐磨性的影响 ? 表面粗糙度太大和太小都不耐磨,图54-2。 ? 表面粗糙度太大,接触表面的实际压强增大,粗糙不平 的凸峰相互咬合、挤裂、切断,故磨损加剧; ? 表面粗糙度太小,也会导致磨损加剧。因为表面太光滑, 存不住润滑油,接触面间不易形成油膜,容易发生分子粘 结而加剧磨损。 ? 表面粗糙度的最佳值与机器零件的工作情况有关 ,载荷 加大时,磨损曲线向上、向右移动,最佳表面粗糙度值也 随之右移。
表面质量对零件使用太大、太小都不耐磨 适度冷硬能提高耐磨性
零件表 面质量
对疲劳强 度的影响
对工作精 度的影响
粗糙度越大,疲劳强度越差 适度冷硬、残余压应力能提高
疲劳强度 粗糙度越大、工作精度降低
残余应力越大,工作精度降低
对耐腐蚀性 能的影响
粗糙度越大,耐腐蚀性越差
压应力提高耐腐蚀性 拉应力则降低耐腐蚀性
(2)表面层冷作硬化与残余应力对零件疲 劳强度的影响
? 适度的表面层冷作硬化能提高零件的疲劳强度。 ? 残余应力有拉应力和压应力之分, 残余拉应力
容易使已加工表面产生裂纹并使其扩展而 降低疲
劳强度。
? 残余压应力 则能够部分地抵消工作载荷施加的
拉应力,延缓疲劳裂纹的扩展,从而 提高零件的
疲劳强度。
工表面愈粗糙。故对中碳钢和低碳钢材料的工件,为改善切 削性能,减小表面粗糙度,常在粗加工或精加工前安排正火 或调质处理。
在铸造、锻造、焊接、热处理等加工过程产生的内应力 与这里介绍的表面残余应力的区别在于 前者是在整个工件上 平衡的应力,它的重新分布会引起工件的变形; 后者则是在 加工表面材料中平衡的应力,它的重新分布不会引起工件变 形,但它对机器零件表面质量有重要影响。
(5) 表面层金相组织变化
机械加工过程中,在工件的加工区域,温度会急剧升
因此,对配合精度要求比较高的零件应该规定较小的 表面粗糙度。
(2)表面残余应力对零件工作精度的影响 零件表面层有较大的残余应力,就会影响其 工作精度
的稳定性。
4. 表面质量对零件耐腐蚀性能的影响
(1)表面粗糙度对零件耐腐蚀性能的影响 零件表面越粗糙,越容易积聚腐蚀性物质,凹谷越深,
渗透与腐蚀作用越强烈。 因此,减小零件表面粗糙度,可以提高其耐腐蚀性能。
H
?
cot
f
? r ? cot
?
' r
对于刀尖圆弧半径rε≠0的刀具,工件表面残留面积的高度:
H ? f2 8 r?
2. 物理因素 切削加工表面粗糙度的实际轮廓形状,一般都与纯几何
因素形成的理论轮廓有较大的差别,这是由于切削加工中有 塑性变形的缘故。
(1)工件材料的影响
? 塑性材料:工件材料韧性愈好,金属塑性变形愈大,加
三、影响加工表面粗糙度的主要因素及其控制
机械加工中,表面粗糙度形成的原因大致可归纳为 : 几何因素和物理力学因素两个方面。
(一)切削加工表面粗糙度
切削加工的表面粗糙度值主要取决于切削残留面积 的高度。
1. 几何因素
? 刀尖圆弧半径 rε ? 主偏角 kr、副偏角 kr′ ?进给量 f
对于刀尖圆弧半径rε=0的刀具,工件表面残留面积的高度:
高,当温度升高到超过工件材料金相组织变化的临界点时,
就会发生金相组织变化。如磨削淬火钢件时,常会出现回
火烧伤、退火烧伤等金相组织变化,将严重影响零件的使
用件能。
吸
附
右图为加工变质层示意图。
层
显微硬度
残余应力
吸附层 :氧化膜或其他化合物,
纤
并吸收、渗进了气体、液体和
维
层
固体的粒子。
压
缩
压缩区:塑性变形区。
(2)表面残余应力对零件耐腐蚀性能的影响 零件表面残余压应力使零件表面紧密,腐蚀性物质不易
进入,可增强零件的耐腐蚀性,而表面残余拉应力则降低零 件耐腐蚀性。
表面质量对零件使用性能还有其它方面的影响: 如减小 表面粗糙度可提高零件的接触刚度、密封性和测量精度;对 滑动零件,可降低其摩擦系数,从而减少发热和功率损失。
(3)表面层冷作硬化
机械加工过程中表面层金属产生强烈的塑性变形,使 晶 格扭曲、畸变,晶粒间产生剪切滑移,晶粒被拉长 ,这些都 会使表面层金属的硬度增加,塑性减小,统称为 冷作硬化。
(4)表面层残余应力
机械加工过程中由于切削变形和切削热等因素的作用 在工件表面层材料中产生的内应力,称为 表面层残余应力。
图54-2 表面粗糙度与初期磨损量的关系
(2)表面层冷作硬化对零件耐磨性的影响
? 加工表面的冷作硬化,一般能提高零件的耐 磨性。 因为它使磨擦副表面层金属的显微硬度提 高,塑性降低,减少了摩擦副接触部分的弹性变 形和塑性变形。
? 并非冷作硬化程度越高,耐磨性就越高。 这 是因为过分的冷作硬化,将引起金属组织过度 “疏松”,在相对运动中可能会产生金属剥落, 在接触面间形成小颗粒,使零件加速磨损。
3. 表面质量对零件工作精度的影响
(1)表面粗糙度对零件配合精度的影响 间隙配合:如果配合表面粗糙度较大,则在初期磨损
阶段磨损量就大,造成零件尺寸和形状发生变化,影响到 配合间隙量,改变了配合性质。
过盈配合:如果配合表面粗糙,则装配后表面的波峰 产生塑性变形,从而使有效的过盈量减小,减弱了过盈配 合的结合强度。