第二章 已加工表面质量分析
机械制造(第2版)第二章课后习题解答
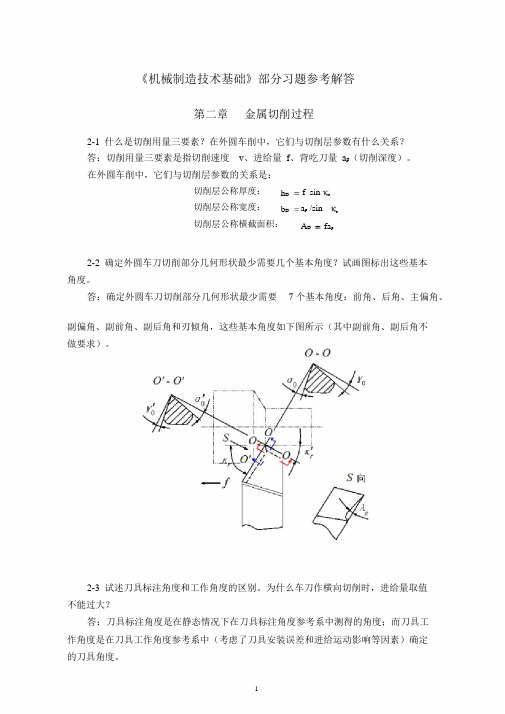
Fc
C a f v K x Fc pFc
yFc n
c Fc
sFc
900 31 0.4 0.75 80 0 1.0 1358N
Fp
xFp
yFp nFp
CFpap f vc K sFp
530 3 0.9 0.4 0.75 80 0 1.5 1075N
Ff
xFf
yFf nFf
CFf ap f vc K sFf
450 31 0.4 0.4 80 0 0.75 702N
再根据 p38公式(2-17),可得切削功率 P c Fcvc 10 3 1358 80/ 60 10 3 1.81 KW
2-11 影响切削力的主要因素有哪些?试论述其影响规律。 答:(P41-42)影响切削力的主要因素有工件材料、切削用量、刀具几何参数、刀具 磨损、切削液和刀具材料。 工件材料的影响:工件材料强度、硬度越高,切削力越大; 切削用量的影响:背吃刀量 ap影响最大,几乎成正比; f 次之,v 最小。
2-13 试分析刀具磨损四种磨损机制的本质与特征,它们各在什么条件下产生? 答:(P47)刀具磨损四种磨损机制的本质和特征: 硬质点划痕:工件材料有硬质点,造成机械磨损,有划痕、划伤。 冷焊磨损:即粘接磨损,在高压高温作用下,刀具材料被粘接、撕裂,导致磨损。 扩散磨损:在高温下刀具材料中金属原子扩散,导致材料软化磨损。 化学磨损:由于化学腐蚀、氧化作用产生的磨损。
2-6 怎样划分切削变形区?第一变形区有哪些变形特点? 答:切削形成过程分为三个变形区。第一变形区切削层金属与工件分离的剪切滑移 区域,第二变形区前刀面与切屑底部的摩擦区域;第三变形区刀具后刀面与已加工表面 的摩擦区域。 第一变形区的变形特点主要是:金属的晶粒在刀具前刀面推挤作用下沿滑移线剪切 滑移,晶粒伸长,晶格位错,剪切应力达到了材料的屈服极限。
金属材料切削加工性分析

第一章 金属材料切削加工性切削加工性:Machinability ,指金属材料被切削加工成合格零件的难易程度。
例如:以车削45#钢为例:材料硬度 HB200(正火) 单位切削力 κc =200kg/mm 2用YT15车刀车削: IT8νc =120 θ=800ºC此种车削方法家喻户晓,人人皆知,谁都会做,没什么难点。
1. 铝合金,这是比较好加工的,κc =70, νc =800m/min 时,θ也不高,T 很长。
2. 灰口铸铁HT200 κc =114 断屑 切削加工性评价指标: ① 刀具耐用度高; T ② 许用切削速度高; νc③ 已加工表面易于达到; ④ 车削时断屑;⑤ 切削力小,切削温度低。
F c θ 3. 45#淬火 HRC50切削力F c 大,切削温度θ高,刀具耐用度T 低。
一般情况下不车,只能磨削。
IT8§1—1 衡量切削加工性指标以车削45#钢(HB200)为参照基准:刀具材料:YT15;刀具耐用度:T=60min ; [ν60]j =100m/min ;当切削L Y12 ν60=300m/min 相比[]60603003100r j νκν=== 一、称相对加工性1. 刀具耐用度T :T 较长,加工性较好。
例:45#钢 T=60min30C r M n SiA T=20min 加工性差。
2. 切削速度νc :例:45#钢 νc =100m/min YT15LY12 νc =300m/min YG153003100r κ== 加工性好。
泰勒公式: 0.4c ATν=切削速度是根据刀具耐用度确定的。
一定刀具耐用度下有一个允许的切削速度νT 。
3. 切削力F c (或者κc )凡切削力大者,加工性差。
4. 切削温度(凡是切削温度高者,加工性差。
条件: νc pθº10 20 30 40 50 60 70 80 90 100 110 120 130 νc m/min图(一)1—GH131 2—1Cr18Ni9Ti 3—45#钢(正火) 4—HT200 YT15—45# YG8—GH131 1Cr18Ni9Ti HT200γo =15º α0=8º κr =75º λs =0º γε=0.2 a p =3 f=0.15. 已加工表面质量:包括:表面粗糙度表面残余应力加工硬化程度及深度 ① ()''44r r a r ff R ctg ctg ctg κκκ==+2r πκ=时 ctg κc =0 R a (µm)f 决定R a 。
机械加工零件表面的质量控制措施分析
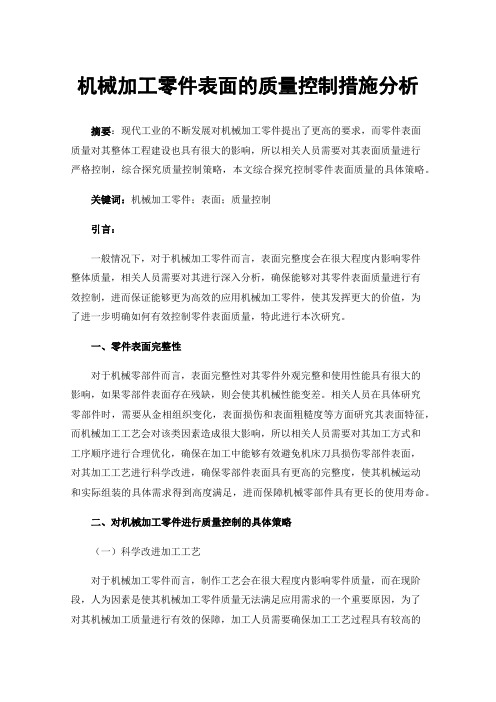
机械加工零件表面的质量控制措施分析摘要:现代工业的不断发展对机械加工零件提出了更高的要求,而零件表面质量对其整体工程建设也具有很大的影响,所以相关人员需要对其表面质量进行严格控制,综合探究质量控制策略,本文综合探究控制零件表面质量的具体策略。
关键词:机械加工零件;表面;质量控制引言:一般情况下,对于机械加工零件而言,表面完整度会在很大程度内影响零件整体质量,相关人员需要对其进行深入分析,确保能够对其零件表面质量进行有效控制,进而保证能够更为高效的应用机械加工零件,使其发挥更大的价值,为了进一步明确如何有效控制零件表面质量,特此进行本次研究。
一、零件表面完整性对于机械零部件而言,表面完整性对其零件外观完整和使用性能具有很大的影响,如果零部件表面存在残缺,则会使其机械性能变差。
相关人员在具体研究零部件时,需要从金相组织变化,表面损伤和表面粗糙度等方面研究其表面特征,而机械加工工艺会对该类因素造成很大影响,所以相关人员需要对其加工方式和工序顺序进行合理优化,确保在加工中能够有效避免机床刀具损伤零部件表面,对其加工工艺进行科学改进,确保零部件表面具有更高的完整度,使其机械运动和实际组装的具体需求得到高度满足,进而保障机械零部件具有更长的使用寿命。
二、对机械加工零件进行质量控制的具体策略(一)科学改进加工工艺对于机械加工零件而言,制作工艺会在很大程度内影响零件质量,而在现阶段,人为因素是使其机械加工零件质量无法满足应用需求的一个重要原因,为了对其机械加工质量进行有效的保障,加工人员需要确保加工工艺过程具有较高的科学性,确保能够使其零件加工时间得到有效减少,进而使其由于时间问题导致出现的工程延误,得到有效避免。
在对零件进行机械加工之前,需要科学完善准备工作,确保一次性完成,使其重复加工造成的原料损失和误差得到有效减少。
(二)合理优化加工程序在进行机械零件加工时,加工制作技术会对其零件整体质量造成很大的影响,在我国现阶段,具体进行零件机械加工时,无法确保高度满足表面质量标准,同时,人为元素也会在很大程度内影响机械表面质量,导致零件机械加工之后,表面质量很难满足行业标准。
机械加工表面质量解析PPT课件

刀具相对于工件作进给运动时,在加工表面留下了切削层残留面 积,其形状是刀具几何形状的复映。其理论上的最大粗糙度 Rmax可由刀具形状、进给量f,按几何关系求得。 1) 当刀尖圆弧半径rε一定时: 2) 当背吃刀量ap和进给量f很小时,粗糙度主要由刀尖圆弧构 成: 措施:减小进给量f、主偏角Kr、副偏角Kr'以及增大刀尖圆弧半 径rε,均可减小残留面积的高度。
➢ 3、表面层残余应力:是由于加工过程中切削变形和 切削热的影响,工件表面层产生残余应力。
第4页/共45页
二、表面质量对零件使用性能的影响
1、 表面质量对耐磨性的影响
➢
粗糙度过大或过小都会引起工作时的迅速磨损,
一定工作条件下通常存在一个最佳表面粗糙度。
✓
表面粗糙度值过大—〉实际接触面积↓—〉单位
应力↑—〉峰部之间产生塑性变形、弹性变形和剪
实际机械加工后的表面层残余应力及其分布,是上 述三方面因素综合作用的结果,在一定条件下,其中某 一或二种因素可能起主导作用。
第21页/共45页
2、 磨削裂纹的产生
磨削加工中热态塑性变形和金相组织变化的影响较大, 故大多数磨削零件的表面层往往有残余拉应力。当残余拉 应力超过材料的强度极限时,零件表面就会出现裂纹。有 的磨削裂纹也可能不在工件的外表面,而是在表面层下成 为肉眼难以发现的缺陷。磨削裂纹一般很浅 。
金属冷作硬化的结果,使金属处于高能位不稳定状态, 只要一有条件,金属的冷硬结构本能地向比较稳定的结构转 化。这些现象统称为弱化(回复)。机械加工过程中产生的 切削热,将使金属在塑性变形中产生的冷硬现象得到恢复。
由于金属在机械加工过程中同时受到力因素和热因素的作 用,机械加工后表面层金属的最后性质取决于强化和弱化两 个过程的综合。
机械制造技术基础第二章课后答案

机械制造技术基础第二章课后答案#1.金属切削过程的实质是什么答:金属切削过程就是刀具从工件上切除多余的金属,使工件得到符合技术要求的几何精度和表面质量的过程。
2.切削运动可分哪两类,各有什么特点答:切削运动可分为主运动和进给运动。
主运动在切削过程中速度最高,消耗的功率最大,并且在切削过程中切削运动只有一个。
进给运动的速度较低、消耗的功率较小,进给运动可以有一个或多个。
3.切削用量的主要参数有哪些答.:切削用量的参数有切削速度、进给量和背吃刀量。
4.试述车刀前角、后角、主偏角、负偏角和刃倾角的作用,并指出如何使用答:前角对切削的难易程度有很大的影响,前角大小的选择与工件材料、刀具材料、加工要求有关。
后角的作用是为了减小后刀面与工件之间的摩擦和减少后刀面的磨损。
主偏角的大小影响切削条件、刀具寿命和切削分力的大小。
!5.车外圆时,车刀装得过高或过低、偏左或偏右,刀具角度会发生哪些变化什么情况下可以利用这些变化答:当刀尖高于工作中心时,刀具工作前角将增大,工作后角将减小。
如果刀尖低于工作中心,则刀具工作前角减小,后角增大。
若刀杆右偏,则车刀的工作主偏角将增大,负偏角将减小。
若刀杆左偏,则车刀的工作主偏角将减小,负偏角将增大。
6.试标出图刀具的五个基本角度及主切削刃和副切削刃。
7.列举外圆车刀在不同参考系中的主要标准角度及其定义。
答:1)前角:在正交平面内测量的前刀面与基面之间的夹角;后角:在正交平面内测量的主后刀面与切削平面之间的夹角;主偏角:在基面内测量的主切削刃在基面上的投影与进给方向的夹角;副偏角:在基面内测量的副切削刃在基面上的投影与进给运动反方向的夹角;刃倾角:在切削平面内测量的主切削刃与基面之间的夹角;副后角:在副切削刃上选定点的副正交平面内,副后刀面与副切削平面之间的夹角。
8.偏角的大小对刀具耐用度和三个切削分力有何影响当车削细长轴时,主偏角应选得较大还是较小为什么答:当切削面积不变时,主偏角增大,切削厚度也随之增大,切屑变厚,因而主切削力随着主偏角的增大而减小,但当主偏角增大到60~70之间时,主切削力又逐渐增大主偏角;背向力随着主偏角的增大而减小,进给力随着主偏角的增大而增大。
机械制造技术基础课后答案第二章

a2-1.金属切削过程有和特征?用什么参数来表示和比较?p答:金属切削过程是指刀具与工件相互作用形成切屑的过程。
在这一过程中会出现许多物理现象:如切削刀,切削热,积屑瘤,刀具磨损和加工硬化等。
切削要素包括切削用量和切削层几何参数:切削用量:1.切削速度V 2.进给量f 3.背吃刀量a切削层几何参数1.切削宽度a 2切削厚度a 3切削面积A2-2.切削过程的三个变形区各有何特点?他们之间有什么关联?答:第一变形区,﹙基本变形区﹚.变形量最大。
常用它来说明切削过程的变形情况.第二变形区,﹙摩擦变形区﹚.切屑形成后与前面之间存在压力.所以沿前面流出时必然有很大的摩擦.因而使切屑底层又一次产生塑性变形。
第三变性区﹙加工表面变形区﹚:工件已加工表面与后面接触的区域.产生加工硬化这三个变形区汇集在切削刀附近.此处的应力比较集中而且复杂.金属的被切削层就在此处与工件基本发生分离.大部分变形切屑.很小一部分留在已加工表面上。
2-3分析积屑瘤产生的原因及其对加工的影响。
生产中最有效的控制积屑瘤的手段是什么?答:产生的原因:在切削速度不高而又能形成连续切屑情况下。
加工一般钢料或其它塑性材料时。
常常在道具前面粘着一块剖面有时呈三角状的硬块。
在处于比较稳定的状态时。
能够代替切削刀进行切削。
影响:引起道具实际角度的变化,如可增大前角,延长道具寿命等。
积屑瘤不稳定,增大到一定程度后破碎。
容易嵌入已加工表面内,增大表面粗糙度值。
手段1.降低切削速度,使温度降低,不易粘结。
2.增加切削速度,使温度高于产生切屑瘤的温度。
3.采用润滑性比较好的切屑液。
4.增大切屑前角,有效降低铁屑和前刀面挤切。
5.适当提高工件硬度,减小加工硬化。
2-4有区别切屑形成后与前面之间存在压力。
所以沿前面流出时必有很大的摩擦,因而使切屑层又一次产生塑性变形,而一般刚体之间的滑动摩擦是两刚体之间的相对运动引起的。
2-5道具要从工件上切下金属,必须具有一定的切削速度,也正是由于切削角度才决定了道具切削部分各表面的空间位置。
金属切削原理与刀具复习大纲
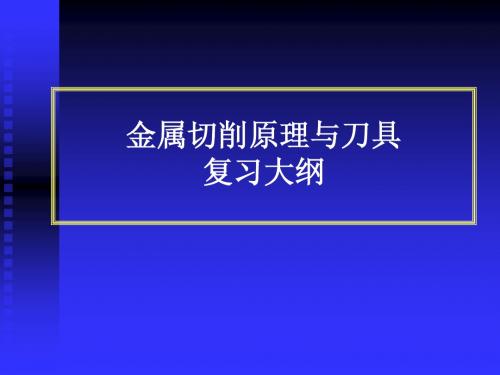
2. 各种刀具材料使用于加工什么材料?
第三章 金属切削过程的基本规律
第一变形区:(基本变形区) OA~OM之间的区域,是切削 第二变形区: 第三变形区: 过程中的主要变形区,是切削 切屑底层与前刀面之间的摩擦 工件已加工表面与刀具后刀面之 力和切削热的主要来源。 间的挤压、摩擦变形区域。 变形区。主要影响切屑的变形 主要特征: 造成工件表面的纤维化与加工硬 和积屑瘤的产生。 剪切面的滑移变形 化。
带状切屑
节状切屑
粒状切屑
三、变形程度的表示方法
1.
变形系数:( 切削厚度压缩比Λ h )
h ch h hD
厚度变形系数:
长度变形系数:
lc l lch
h l 1
根据体积不变原理数:
hch OM cos( o ) cos( o ) hD OM sin sin
延长刀具寿命,便于刀具的制造,资源丰富,价格低廉。
2. 常用刀具材料
高速钢 硬质合金 陶瓷
有钨钴类硬质合金、 钨钛钴类硬质合金和 钨钛钽(铌)类硬质 合金。 推广使用新型刀具 材料如涂层刀具、陶瓷 刀具、天然金刚石、聚 晶金刚石、立方氮化硼 等。 能制造结构复杂 的成形刀具
超硬刀具材料
(1)硬质合金的分类
3-3 切削热
一、切削热的来源:
切削层挤 裂变形 前刀面与切 屑摩擦
切削热的分布:
热量的20%∼50%传给刀具→ 刀具磨损、硬度降低
二、影响切削温度的因素分析
1、切削用量对切削温度的影响:Vc →f →ap
vc、f、ap↗ θ ℃↗
x c y
C v f
ap
z
用YT15刀具,切削45#钢时( σ b=75kg/cm2)
机械加工表面质量分析

科 技论 坛 f f f
机械加工表 面质量分析
李 晓 明
( 河北钢铁 集团唐钢公司技 术中心 , 河北 唐 山 0 30 ) 60 0
摘 要 : 究加工表面质量的 目 研 的就是要掌握机械加工过程 中各种因素对表面质量的影响规律 , 并通过这些规律控制加工过程 , 高零件的加 提 工表 面质量 , 最终提 高产品的使 用性能。 关键词 :t z ; f  ̄ r 表面质量 ; _ 零件 ; 使用性能 零件的机械加工质量不仅指加 工精度 , 还有表面质量 。机械加工表 面质量, 是指零件在机械加工后表面 层的微观几何形状误差和物理力学 性能。 产品的工作性能、 可靠性、 寿命 在很大程度上取决于主要零件 的表 面质量。机器零件的破坏 , 在多数情 况下都是从表面开始的, 这是由于表 表 面粗糙 度 面是零件材料的边界, 常常承受工作 图 2磨损过程的基本规律 图3表 面粗糙度与初期磨损量的关 系 负荷所引起的最大应力和外界介质 1轻 负荷 ;一 负荷 一 2重 的侵蚀, 表面上有着引起应力集 中而 ( a ) ( b ) ( c ) 佳 表 面粗糙 度 配合中, 如果零件的配合表面粗糙 , 则会使配合件 导致破坏的根源 , 以这些表面直接 所 图 I加 工表 面层 沿深度 方向的变化情况 值 最佳表面粗 很快磨损而增大配合间隙 , 改变配合性质, 降低配 与机器零件的使用性能有关。 在现代 a .3 — .2 u 。表面纹理方 向 合精度 ; 在过盈配合中,如果零件的配合表面粗 机器中, 许多零件是在高速 、 、 高压 高温、 高负荷下 糙度 R 值约为 0 2 1 5 m 对耐磨性也有影响 ,这是因为它能影响金属表面 糙, 则装配后配合表面的凸峰被挤平 , 配合件间的 工作的, 对零件的表面质量提出了更高的要求。 留情况。 轻载时, 两 有效过盈量减小 , 降低配合件间连接强度, 影响配 1 机械加工表面质量的含义。任何机械加工 磨损最 合的可靠性。因此 , 对有配合要求的表面, 必须规 方法所获得的加工表面都不可能是绝对理想的表 表面的纹理方向与相对运动方向一致时, 零件的表面质量对零件 小; 当两表面纹理方向与相对运动方向垂直时, 磨 定较小的表面粗糙度值 。 面, 总存在着表面粗糙度、 表面波度等微观几何形 但是在重载情况下 , 由于压强、 分子亲和 的使用性能还有其他方面的影响。 例如, 对于液压 状误差。 表面层的材料在加工时还会产生物理、 力 损最大。 储存等因素的变化 , 其规律与上述 缸和滑阀, 较大的表面粗糙度值会影响密封性; 对 学性能变化,以及在某些情况下产生化学性质的 力和润滑液的 有所不同。 表面层的加工硬化, 一般能提高耐磨性 于工作时滑动的零件, 当的表面粗糙度值能提 恰 变化。 l 图 (羡示加工表面层沿深度方向的变化 晴 a .5 l 这是因为加工硬化提高了表面层的强 高运动的灵活性, 减少发热和功率损失 ; 零件表面 况。在最外层生成有氧化膜或其他化合物,并吸 0 ~ 倍。 减少了表面进一步塑性变形和咬焊的可能。 但 层的残余应力会使加工好的零件因应力重新分布 收、 渗进了气体 、 液体和固体的粒子 , 称为吸附层, 度, 其厚度一般不超过 8 m。压缩层即为表面塑性变 过度的加工硬化会使金属组织疏松 ,甚至出现疲 而在使用过程中逐渐变形,从而影响其尺寸和形 n 从而使耐磨性下降。 状精度等。总之, 所以 提高加工表面质量 , 对保证零件 形 区, 由切削力造成 , 厚度约为几十至几百微米 , 劳裂纹和产生剥落现象, 其上部为纤维层, 是由 零件的表面硬化层必须控制在一定的范围之内。 的使用性能,提高零件的使用寿命是很重要的。 2 2表面质量对零件疲劳强度的影响。 零件在交变 2 _ 5磨削加工后的表面。 被加工材料与刀具之间的摩擦力所造成的。另外, 切削热也会使表面层产生各种变化 , 如同淬火、 载荷的作用下,其表面微观不平的凹谷处和表面 随机分 布磨粒的砂轮和工件 的相对运动来 实现 回 在磨削过程 中, 磨粒在工件表面上滑擦、 耕犁 火一样使材料产生相变 以及晶粒大小的变化等 。 层的缺陷处容易引起应力集中而产生疲劳裂纹 , 的。 造成零件的疲劳破坏。 试验表明 , 减小零件表面粗 和切下切屑, 把加工表面刻划出无数微细的? , 勾 槽 因此, 表面层的物理力学性能不同于基体, 产生了 使零件的疲劳强度有所提高。 此 , 因 对 沟槽两边伴随着塑性隆起, 形成表面粗糙度。a 磨 如图 l 晰 、 的显微硬度和残余应力变化。综 糙度值可以 于一些承受交变载荷的重要零件,如曲轴其曲拐 削用量对表面粗糙度的影响提高砂轮速度,可以 E 所述, 表面质量的含义有两方面的内容。 同时 , 塑性变形造 2加工表面质量对零件 使用性能的影响 。 与轴颈交接处精加工后常进行光整加工 ,以减小 增加在工件单位面积上的刻痕 , 提高其疲劳强度。 加工硬化 而下降 ,所以粗 21表面质量对零件耐磨f . 生的影响。 零件的耐磨眭 零件的表面粗糙度值 , 表 面层 的适 度硬 糙度值减小。 在其他条件不变的情况下 , 提高工件 与摩擦副的材料 、润滑条件和零件的表面质量等 在工件表面上的刻痕数 因素有关。 特别是在前两个条件已确定的前提下 , 化可以在零件表面形成—个硬化层 ,它能阻碍表 速度,磨粒在单位时间内 从而使零件疲劳强度提高 。 减少, 因而将增大磨削表面粗糙度值。 磨削深度增 零件的表面质量就起着决定性的作用 。零件的磨 面层疲劳裂纹的出现 , 反而易于产生裂纹 , 加 , 磨削过程中磨削力及磨削温度都增加, 磨削表 损可分为三个阶段, 如图 2所示。第 1 阶段际初期 但零件表面层硬化程度过大, 从而增大表面粗糙度值。b  ̄ . P l f 磨损阶段。 由于摩擦副开始工作时 , 两个零件表面 故零件的硬化程度与硬化深度也应控制在—定 的 面塑性变形增大, 范围之内。表面层 的残余应力对零件疲劳强度也 对表面粗糙度的影响砂轮的粒度。砂轮的粒度越 互相接触 , 一开始只是在两表面波峰接触 , 实际的 当表面层为残余压应力时 , 能延缓疲 细, 单位面积上的磨粒数越多, 工件表面上的刻痕 接触面积只是名义接触面积的一小部分。当零件 有很大影响 , 提高零件的疲劳强度 ; 当表面层为 密而细 , 则表面粗糙度值越小。但磨粒过细时, 砂 受力时 , 波峰接触部分将产生很大的压强 , 因此磨 劳裂纹的扩展, 残余拉应力时, 容易使零件表面产生裂纹而降低 轮易堵塞, 磨削性能下降, 反而使粗 糙度值增大。 。 损非常显著。经过初期磨损后,实际接触面积增 3 硬度的大小应合适。 砂轮太硬, 磨粒 大, 磨损变缓 , 进人磨损 的第 Ⅱ阶段 , 即正常磨损 其疲劳强度。2 表面质量对零件耐腐蚀性 的影 砂轮的硬度。 阶段。 这一阶段零件的耐磨性最好, 持续的时间也 响。零件的耐腐蚀性在很大程度上取决于零件 的 钝化后仍不能脱落,使工件表面受到强烈摩擦和 塑性变形程度增加 , 表面粗糙度值增大 表面粗糙度。 零件表面越粗糙 , 越容易积聚腐蚀性 挤压作用, 较长。最后, 由于波峰被磨平, 表面粗糙度值变得 凹谷越深, 渗透与腐蚀作用越强烈。 因此 , 减 或使磨削表面烧伤。砂轮太软 , 磨粒易脱落 , 常会 非常小, 不利于润滑油的储存, 且使接触表面之间 物质, 而使表面粗糙度值变差。 砂 的分子亲和力增大 , 甚至发生分子粘合, 使摩擦阻 小零件表面粗糙度值,可以提高零件的耐腐蚀性 产生磨损不均匀现象 , 能。 零件表面残余压应力使零件表面紧密 , 腐蚀性 轮的修整。砂轮修整的目的是为了去除外层已钝 力增大, 从而进 入 磨损的第Ⅲ阶段, 即急剧磨损阶 可增强零件的耐腐蚀性, 而表面残 化的或被磨屑堵塞的磨粒,保证砂轮具有足够的 段。 表面粗糙度对摩擦副的初期磨损影响很大, 但 物质不易进入 , 2 4表面质量对 等高微刃。 微刃等高性越好, 磨出工件的表庙 组 糙 也不是表面粗糙度值越小越耐磨。图 3 是表面粗 余拉应力则降低零件的耐腐蚀性。 . 配合性质及零件其他性能的影响。相配零件间的 度值越小。 糙度对初期磨损量影响的实验曲线。 从图中看到, 在间隙 在一定工作条件下,摩擦副表面总是存在一个最 配合关系是用过盈量或间隙值来表示的。
- 1、下载文档前请自行甄别文档内容的完整性,平台不提供额外的编辑、内容补充、找答案等附加服务。
- 2、"仅部分预览"的文档,不可在线预览部分如存在完整性等问题,可反馈申请退款(可完整预览的文档不适用该条件!)。
- 3、如文档侵犯您的权益,请联系客服反馈,我们会尽快为您处理(人工客服工作时间:9:00-18:30)。
22
加工后表层金属性质
取决于强化和弱化综合作用的结果。
弱化:被冷作硬化的金属处于高能位的
不稳定状态,金属的不稳定状态向比较稳 定的状态转化, 弱化作用的大小取决于温度的高低、时间 的长短和强化程度的大小。
3.相变引起体积变化; 一般表面金属产生残余拉应力
33
影响残余应力的因素(刀具方面)
1、刀具前角越小,残余拉应力越小
34
影响残余应力的因素(刀具方面)
2、刀具磨损量增大,残余拉应力越大
35
影响残余应力的因素(工件方面)
3、工件材料塑性越大,残余拉应力越大;
36
影响残余应力的因素(加工条件方面)
23
评定冷作硬化指标,
三项 表层金属的显微硬度HV; 硬化层深度h; 硬化程度N。
24
影响加工硬化的因素: 1.刀具方面
1、前角愈大, 硬化层深度愈小;
25
影响加工硬化的因素:
2、钝圆半径越大,加工硬化也越大
26
影响加工硬化的因素:
3.刀具磨损越大,加工硬化也越大;
27
影响加工硬化的因素:
各种工序(车、刨、钻、拉、滚齿、螺纹切 削)均会产生;
切削塑性材料是主要原因。
16
表面粗糙度产生原因
鳞刺产生过程:
1.抹拭 2.导裂 3.层积 来自.切顶17表面粗糙度产生原因
4切削过程中变形;
挤裂切屑形成时 单元切屑形成时
18
表面粗糙度产生原因
5.刀具的边界磨损;
6、刀刃与工件相对位置变动; 19
➢ 在交变载荷作用下,从提高抗疲劳角度考 虑,终工序应选择能在该表面产生残余压 应力的加工方法
40
精密加工的表面质量
精密加工的概念:Ra1.25-0.63微米的加工,又分精密切 削和超精密切削。
措施: 刀具方面: ➢刀刃的锋利性和平整形; ➢刀刃的钝圆半径; ➢刀具材料的有选择; 切削条件方面: ➢切削用量;(高速度、小进给量) ➢工艺系统刚性; 切削液方面:
4、切削速度越高, 残余拉应力越大, 残余应力层却减少;
37
影响残余应力的因素(加工条件方面)
5、进给量增大, 残余拉应力也增大;
38
影响残余应力的因素(加工条件方面)
6、背吃刀量对残余 应力的影响不太显著
39
零件工作表面最终加工方法选择
➢最终工序留下的残余应力将直接影响机器 零件使用性能。
➢选择最终工序加工方法时,须考虑该零件 主要工作表面的具体工作条件和可能的破坏 形式。
➢表面残余应力概念: 工件经过切削加工后,没有外力作用的情况 下,已加工表面内部保持的平衡而存留的不 同应力称为表面残余应力。
➢ 分类:表面残余应力又分为表面残余拉应力 表面
残余压应力
32
产生残余应力的原因
1.机械应力引起塑性变形; 形式较多,但一般产生表面残余拉应力
2.热应力引起塑性变形发生; 一般产生表面层残余拉应力
其纤维方向平行于已加工表面, ※已加工表面表层的金属具有和基体组织
不同的性质,所以称为加工变质层。
9
加工变质层概念
10
已加工表面粗糙度
表面粗糙度产生原因: 1、几何因素所产生的粗糙度,
决定于残留面积高度; 2、由于切削过程不稳定因素所
产生的粗糙度。
11
表面粗糙度产生原因
1.残留面积:切削时,由于刀具与工件的相对运动及刀
第二章 已加工表面质量
1
已加工表面质量
包括两方面: 1、表面几何学方面 主要指零件外表面的几何形状方面质
量 2、表面层材质变化 零件外表面一定深度的组织、力学、
物化性能
2
表面几何学方面
评定标志: 1、表面粗糙度; (主要指标)
(微观方面:以微米单位计量) 2. 表面波度:
(介于微观方面与宏观方面:宏观方面误差通 常是指几何误差,如形状精度、位置精度等) 3. 加工纹理方向; 4. 加工后表面伤痕。
6
已加工表面的形成过程
刀刃钝圆部分OB、 VB、及CD三部 分 构成后刀面上的总 接触长度,它的接 触情况对已加工表 面质量有很大影响。
7
前刀面应力分布
用光弹法测得的 应力分布
8
加工变质层概念
※被切金属进入第一变形区时,晶粒因压 缩而变长;
※接近刀刃,晶粒更为伸长成为纤维层; ※已加工表面的金属纤维被拉伸得更细,
影响表面粗糙度因素
1.刀具方面
※ 几何参数 ※ 刀面及刀刃粗糙度 ※ 刀具材料 ※ 刀具的磨损
20
影响表面粗糙度因素
2.工件方面:
材料塑性影响; 金相组织影响;
3.切削条件:
速度影响; 进给量影响; 切削液影响;
21
表面层加工硬化
加工硬化形成 塑性变形使晶格扭曲、畸变; 晶粒间产生剪切滑移,甚至破碎; 晶粒被拉长和纤维化, 结果:增大金属变形的阻力
具 几何形状的关系,有一小部分金属未被切下来而残留 在已加工表面上,称为残留面积。
12
刀尖圆弧半径不等于零时: 刀尖圆弧半径等于零时:
13
表面粗糙度产生原因
2.积屑瘤;
形成过切:
形成鳞片状毛刺
14
表面粗糙度产生原因
3、鳞刺;
15
表面粗糙度产生原因
鳞刺产生原因
中低速度切中碳钢、铬钢、不锈钢、铝合金、 铜合金;
2.工件方面 工件材料塑性越大,硬化越严重 3.切削条件方面 切削速度影响
28
影响加工硬化的因素:
3.切削条件方面 进给量影响
29
影响加工硬化的因素:
3.切削条件方面 背吃刀量影响
30
影响加工硬化的因素:
3.切削条件方面 进给量影响
31
残余应力
➢ 表面残余应力的性质、大小是已加工表面 质量的主要指标之一
3. 表面层的金相组织
4
已加工表面质量对零件使用性能的影响
表面粗糙度对零件使用性能影响: 耐磨性; 接触性能; 抗疲劳强度; 抗腐蚀能力; 润滑性能。 注意表面粗糙度合理选用问题 (加工成本与正常使用要求关系)
5
已加工表面质量对零件使用性能的影响
加工硬化对零件使用性能影响: 耐磨性;(会出现硬度不均) 抗疲劳强度; 加速刀具的磨损; 残余应力对零件使用性能影响: 零件变形; 抗疲劳能力; 耐腐蚀能力。
3
表面材质的变化
评定标志: 1、表面层的加工硬化程度及硬化层深度;
(主要指标)
加工硬化:工件经过切削加工后,已加工表面的硬度将高于工件材 料的原来的硬度的现象称为加工硬化
2. 表面残余应力的性质、大小; (主要指标)
表面残余应力:工件经过切削加工后,没有外力作用的情况下,已 加工表面内部保持的平衡而存留的不同应力称为表面残余应力。