吨钢可比能耗限额与计算方法
工序单位能耗的计算方法、及企业吨钢可比能耗计算方法

一、各工序单位能耗计算方法:二、其它能耗计算方法的资料中国8个钢铁企业产量达千万吨近几年中国钢铁工业生产规模明显扩大,年产钢1000万吨以上的企业已有8家,年产钢500万吨以上的共有1 7家,年产钢300万吨以上的有30多家。
2005年产钢1000万吨以上企业由2000年的1家(宝钢)上升到8家(宝钢、鞍钢、唐钢、武钢、首钢、沙钢、济钢、莱钢),合计产钢11191.9万吨,占全国钢产量的31.76%。
产钢大于500万吨小于1000万吨企业由2000年的3家(鞍钢、首钢、武钢)上升到2005年的9家 (马钢、华菱钢铁、包钢、邯钢、攀钢、钢铁、太钢、酒钢、建龙钢铁),合计产钢6051.21万吨,占全国钢产量的17. 17%。
产钢300万吨以上企业共30家,合计产钢22079.65万吨,占全国钢产量的62.65%。
据介绍,中国钢产量已由2000年的1.28亿吨上升到2005年的3.52亿吨,钢产量占世界钢产量的比例由2000年的15.2%上升至2005年的31.1%。
标准煤系数就是把某一能源品种的实物量折合成标准量时所采用的系数,换句话说,就是单位能源的实际发热值与7000千卡的比率:即:单位能源的实际发热值7000千卡=该能源品种折标准煤系数例如:1公斤焦炭的平均低位发热量为6800千卡,其折标准煤系数为:6800千卡÷7000千卡=0.9714。
也就是说,1公斤焦炭相当于0.9714公斤标准煤,1000吨焦炭相当于971.4吨标准煤。
在企业部同一能源品种,由于到货时间、供货单位的不同,其实际发热值也不一样。
在此情况下,确定企业标准煤系数,一般采用“加权算术平均数”的计算方法,加权算术平均数是反映次数结构影响的算术平均数,它的计算方法是总体各标志值(变量值)乘以相应的次数(权数)之和与总次数(总权数)的比。
例如:某企业2002年5月份先后从枣庄、肥城、、兖州等地购入原煤的实际数量分别为150吨、175吨、250吨、250吨,每次到货后实测发热值分别为4910千卡/公斤、4509千卡/公斤、5101千卡/公斤、5250千卡/公斤,这些原煤在本月全部消耗,那么该企业5月份消耗煤炭折标准煤587.62吨,折标准煤系数为0.7123。
钢铁生产能耗

钢铁能耗▼吨钢综合能耗:它以生产钢铁所耗能源与粗钢产量之比计算。
因工序不同,可比性很差。
▼吨钢可比能耗:规定只限于从焦化起到轧钢这些生产过程的能耗,以及为这些生产提供的燃料加工、运输、动力等能源消耗。
规定了工序范围,有可比性。
我国1980年重点企业吨钢综合能耗1660kg标煤,吨钢可比能耗1200kg标煤。
1987年下降至吨钢综合能耗1411kg标煤和681kg标煤吨。
钢可比能耗分别是kg标煤。
1978年美国、日本吨钢综合能耗分别是894kg标煤,吨钢可比能耗1200kg标煤。
▼炼铁工序能耗某厂某月炼铁工序能耗!炼铁工序能耗400〜500 kg标煤/t-铁,大约是烧结工序能耗的7〜8倍。
焦化工序能耗150〜200 kg标煤八—焦。
•钢铁企业工序能耗情况(摘自《炼铁技术通讯》2007-5王维兴)中国钢铁工业的能耗占全国总能耗的10%左右,是个能耗大户,也是排放大户源结构是:煤炭70%,电力26.8%,燃料油3%,天然气0.2%。
煤炭中48%为炼焦煤2006年重点钢铁企业工序能耗情况说明:1.0.404 kgce/0.1229 kgce/2.烧结和球团、转炉和电炉工序能耗占行业比例值是考虑各产品产量因素。
3.动力能耗中包括了制氧、高炉鼓风、压缩空气、蒸汽、发电、煤气管网能耗等。
4.吨钢综合能耗、可比能耗的先进与落后值只取长流程有轧钢工序的企业进行比较。
5.国际先进水平值是2004年水平。
・高炉炉顶煤气压差发电技术(TRT)、低热值煤气燃气轮机技术(CCPP)TRT 发电能力是随炉顶煤气压力而变化,一般每吨生铁可发电20〜40度电。
CCPP采用加压的混合煤、空气进入燃气轮机的燃烧室燃烧并燃烧,所产生的高温高压废气进入燃气透平机组膨胀做功,燃气轮机通过减速齿轮传递到发电机组发电,该工艺的能量转化率约为45%左右,设备技术要求高。
传统的煤气——蒸汽——发电工艺的能量转化率约为30%。
•烧结工序节能(摘自《炼铁技术通讯》2007-5王维兴)1.料层厚度增加10mm,可降低燃耗1〜3kg/t;2.漏风率减少10%,可节电2度/t;3.料温每提高10℃,可降低燃耗2kg/t,利用系数提高3〜5%;4.返矿量减少1.5〜3%,节焦粉0.6 kg/t;5. 热风烧结可节约点火燃料10%;6.烧结矿FeO含量上升1%,工序能耗会升高0.68 kg/t;7. 固体燃料分加,可降低焦粉消耗4 kg/t;8. 每100℃热风,可降低固体燃耗5%;9.控制点火负压,可降低燃料消耗6〜12%;10.使用催化助燃剂,可降低燃料消耗13%,增产5%;11.烧结矿温度在600〜800℃进行余热回收,可降低工序能耗2.5 kg/t;12.余热锅炉蒸汽回收,可降低工序能耗2.5 kg/t;13.烧结废气中CO会带走热量,其热量占烧结总热量的10〜25%, 所以要实现烧结的完全燃烧应增加空气量;使用高效节能点火炉,对煤、空气双预热(煤气预热到300〜350℃,空气预热到 450〜500℃)。
钢铁行业铁合金单位产品能源消耗限额标准

注:*为估测值.其它铁合金中的2009年镍铁产量约为350万吨.
2009* 2209.4 ~520 ~800 ~160
~95 ~128 ~506.4
6
我国铁合金发展现状
近年部分铁合金的出口数量 单位:万吨
年度 出口总量 铬系铁合金 锰系铁合金 硅铁合金
电解锰 金属硅
2005 254.73
9.12 54.84 71.78 27.53 53.61
先进值(国际领先水平)
铁合金单位产品能耗的先进值依据目前国际或国内先进水平确定的。
3.2 能耗统计范围及计算方法
铁合金产品能耗统计范围
铁合金工序能耗应包括用于加热炉料、维持正常炉况耗用的冶炼 电力能源消耗,用于还原矿石所需的碳质还原剂(冶金焦丁或气煤半 焦焦粒)消耗,以及生产加工过程中的原料准备、供应、冶炼、合金 浇注、精整和物料与合金运输的动力耗能,扣除工序回收并外供的能 源后的实际消耗的各种能源总量。
入炉矿品位
备注 入炉矿品位每升高降低1%, 电耗限额值可降低升高值, kWh/t
8800 1980 4600
/ /
2700 790
4400 1030
3500 900
焦炭1350kg/t ―
1610
2380
1950
Mn 34% 60
Mn 40% Cr2O3 37%
100
80 铬铁比≥2.2
1250 Mn 37% 焦炭30kg/t
3200~4000 (南非)
焦比1.1t/t锰矿品 位>40%(法国)
国内企业 先进企业 电炉容量 12.5MVA 一般企业
3.3 能耗限额指标取值与依据
铁合金单位产品能耗准入值 (强制性)
钢铁行业单位产品能耗限额标准

钢铁行业单位产品能耗限额标准
钢铁行业的单位产品能耗限额标准因不同的产品种类和生产工艺而有所不同。
在中国,针对钢铁行业,国家制定了相应的能耗限额标准,其中包括了不同的产品种类的能耗限额标准。
以下是一些常见的钢铁产品能耗限额标准:
1. 转炉钢吨钢综合能耗:≤ /t;
2. 电炉钢吨钢综合能耗:≤ /t;
3. 轧钢综合能耗:≤ /t;
4. 高炉炼铁工序单位产品能耗:≤ 437kgce/t;
5. 转炉炼钢工序单位产品能耗:≤ 122kgce/t;
6. 电炉炼钢工序单位产品能耗:≤ 120kgce/t;
7. 烧结工序单位产品能耗:≤ /t;
8. 球团工序单位产品能耗:≤ /t。
需要注意的是,这些标准是针对不同的钢铁产品种类和生产工艺而制定的,而且随着技术的不断进步和环保要求的提高,这些标准也在不断更新和调整。
因此,在实际生产中,钢铁企业需要按照最新的标准进行节能降耗,以实现可持续发展。
吨钢可比能耗计算

吨钢可比能耗计算
先计算出吨钢在各工序的耗能量,再∑
吨钢可比能耗=∑(各工序上方数*下方数)+吨钢辅助工序及亏损耗能
1、工序上方红色数据:表示吨钢所耗钢前各工序的产品量或所产出钢后工序的产品量,即相当于以吨钢计算的物流;工序下方绿色数据:表示吨钢在该工序所耗能量,即各工序的吨钢能耗。
即1.45*54.9+0.99*415.30+1*(-7.68)+0.97*42.94=524.73kgce/t
2、吨钢辅助工序及亏损耗能:
亏损耗能:燃料加工与运输、机车运输、企业能源亏损。
⑴2012年高炉煤气放散率11.66%,氧气放散率
22.32%,氮气放散率21.5%,柴油914.36吨。
(11.66%*12412万m3*0.11+22.32%*15978万m3*0.062+21.5%*19854万m3*0.033+914.36*1.4571)/钢产量=24.53+1.77+1.13+1.07=28.5kgce/t
⑵辅助工序(石灰工序+矿渣粉工序+动力工序)即:
(石灰工序总能耗+矿渣粉工序总能耗+动力工序总能
耗)/钢产量
=(21991.57+8873.03+11201.96+296.03)/1245391*1000
34.01kgce/t
3、综合上述:2012年企业吨钢可比能耗524.73+28.5+34.01=587.24kgce/t。
2009年有限公司吨钢可比能耗541 kgce/t、2008年559 kgce/t、2007年544 kgce/t。
钢铁企业能耗数据模型及采集

以下资料来自《全国工商联冶金业商会统计指标解释(2007年12月)》一.技术经济指标分类钢铁工业技术经济指标分为工序指标和综合指标两大类。
二.工序能耗指标解释指标1. 烧结工序燃料消耗指标烧结矿燃料消耗指标是反映人造块矿燃料消耗水平的指标。
烧结矿使用的燃料有固体燃料(煤粉、焦粉)、非固体燃料两类。
固体燃料一般直接加入烧结矿的混合料中,基本上参与烧结(焙烧)的全过程;非固体燃料用于点火和焙烧(球团)。
各种燃料的消耗应分别统计。
烧结矿固体燃料耗用量(千克)1)烧结矿固体燃料消耗(千克/吨)=烧结矿产出量(吨)烧结矿煤粉耗用量(千克)a) 烧结矿煤粉消耗(千克/吨)=烧结矿产出量(吨)烧结矿焦粉耗用量(千克)b) 烧结矿焦粉消耗(千克)=烧结矿产出量(吨)2)烧结矿固体燃料折标煤消耗(千克标准煤/吨)=各种固体燃料折算成标煤后的耗用量(千克标准煤)烧结矿产出量(吨)计算说明:烧结矿的固体燃料计算中均以干基为准,其水分化验应由质检部门核准或认可,企业按实际情况可对实物消耗量分别计算毛耗(包括各种损耗及计量溢损)和净耗。
2.高炉(生铁)工序燃料燃料消耗指标燃料比是反映高炉冶炼1吨合格生铁所消耗的燃料量。
其计算公式为:燃料耗用总量(千克)燃料比(千克/吨)=生铁合格产出量(吨)计算说明:燃料耗用总量是指入炉的干焦、干焦丁、煤粉、重油等燃料总量。
严格来说,焦比属于能源消耗类指标,但由于焦炭在炼铁生产中的特殊作用,特将焦比指标单列。
由于高炉冶炼的铁种和使用的燃料不同,焦比(即焦耗)有以下几种计算公式:1)入炉焦比入炉焦比是反映高炉冶炼每1吨合格生铁所消耗的干焦炭量。
其计算公式为:干焦耗用量(千克)入炉焦比(千克/吨)=生铁合格产出量(吨)2)综合焦比综合焦比是指高炉冶炼每1吨合格生铁所消耗的综合干焦(将各种燃料均折合成干焦计算)量。
其计算公式为:综合干焦耗用量(千克)综合焦比(千克/吨)=生铁合格产出量(吨)3)喷煤比喷煤比是反映高炉冶炼1吨合格生铁所消耗的煤量。
国家节能中心能效评价技术依据

国家节能中心能效评价技术依据钢铁行业(征求意见稿)一、能效评价技术依据的适用范围本技术依据适用于国家节能中心相关工作涉及的钢铁生产企业,主要适应于传统的高炉-转炉生产流程。
对于电炉生产流程及非高炉生产流程评价依据另行制订。
二、能效评价指标钢铁企业生产的工艺流程比较复杂,从流程长短可以分为“长流程”和“短流程”企业。
电炉与转炉流程的吨钢综合能耗指标相差数倍,很难有一个或者某几个指标单独评价一个企业整体能效利用水平。
钢铁企业的能源评价指标较多,有全厂性能源指标如吨钢综合能耗,有焦化、烧结、球团、炼铁、炼钢、轧钢等工序能耗指标,以及焦比、煤比等主要设备能效指标等。
由于钢铁行业中钢铁联合企业吨钢综合能耗受生产工艺流程、物料条件、装备水平、工序完整程度、加工深度、环保因素、能源加工转换、管理水平等多方面因素影响,造成吨钢综合能耗可比性不强。
在行业单位产品能耗限额标准中,钢铁行业未制订吨钢综合能耗的产品限额值,仅有烧结、炼铁、炼钢等几个工序能耗数值。
工序能耗指标用于评价企业某一生产工序的能效利用水平,工序能耗指标虽然也受物料条件、装备大小等因素影响,但用于评价一个工序的水平相对比较准确。
但由于工序之间能耗也互相影响,某一个工序节能不代表一个系统节能,如烧结、球团、焦化工序是为炼铁服务的,烧结、球团、焦化工序能耗不能仅追求本工序能耗达到最低,也要考虑产品质量为高炉服务,应以整个铁前工序能耗能够达到最低为最终目的。
转炉炼钢系统将铁水预处理、转炉冶炼、精炼和连铸放在一个系统考虑,近年来主要考虑的是炼钢冶炼系统能耗;电炉冶炼由于目前多采用不同比例的铁水比,电炉冶炼能耗值波动范围太大,暂不作研究。
钢铁联合企业加工深度不一,但是加工深度到一次材的吨钢综合能耗指标波动在一个合适范围,可以研究到加工深度只到一次材的钢铁企业吨钢综合能耗合理水平。
为此,从系统节能角度出发,充分考虑现有工作基础和能耗数据的可获得性,重点研究3个主要能耗指标:(1)铁前系统(含烧结、球团、焦化和炼铁)能耗折吨铁产品能耗;(2)转炉炼钢系统(含铁水预处理、转炉冶炼、精炼和连铸)折吨坯能耗;(3)高炉-转炉生产流程到一次材的吨钢综合能耗。
额和电炉钢冶炼电耗限额及计算方法
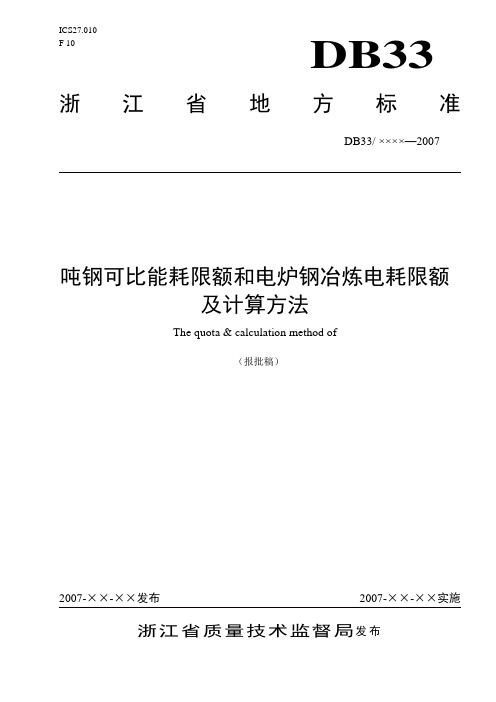
ICS27.010 F 10DB33吨钢可比能耗限额和电炉钢冶炼电耗限额及计算方法 The quota & calculation method of(报批稿)浙江省质量技术监督局发布前言本标准由浙江省经济贸易委员会提出。
本标准由浙江省能源标准化技术委员会归口。
本标准起草单位:浙江省节能协会、杭州钢铁集团本标准主要起草人:徐良友、杨辉、金海峰、刘建芬、任岚。
吨钢可比能耗限额和电炉钢冶炼电耗限额及计算方法1 范围本标准规定了钢铁联合企业吨钢可比能耗限额和钢铁企业电炉钢冶炼电耗限额及计算方法。
本标准分别适用于钢铁联合企业和钢铁企业(含不锈钢)的电炉炼钢工序。
2 术语和定义下列术语和定义适用于本标准。
2.1吨钢可比能耗吨钢可比能耗是指钢铁企业在报告期内,每生产一吨粗钢,从炼焦、烧结、炼铁、炼钢直到企业最终钢材配套生产所必须的耗能量及企业燃料加工与运输、机车运输能耗及企业能源亏损所分摊在每吨粗钢上的耗能量之和。
不包括钢铁工业企业的采矿、选矿、铁合金、耐火材料制品、炭素制品、煤化工产品及其它产品生产、辅助生产及非生产的能耗。
2.2电炉钢冶炼电耗是指报告期内炼钢电炉冶炼过程中的单位合格产品用电量。
2.3电炉电力耗用量是指报告期内炼钢电炉变压器一次侧表,即炉前电度表指示的耗电量,包括为提高电炉钢质量服务的LF等炉外精炼炉所耗电量。
不包括电炉炼钢工序(车间)的其它用电量。
2.4电炉钢合格产出量是指报告期内生产的全部钢坯(锭)量-本期产生的炼钢废品量-本期发生的炼钢责任退货量+供铸造用合格钢水量。
3 限额指标限额指标见表1,适用期限为2006年~2010年。
4 计算方法4.1 吨钢可比能耗的计算方法钢铁企业可参照钢铁行业相关文件的规定,定期编制《钢铁企业能源平衡表》,并依照以下表2的计算方法计算吨钢可比能耗。
4.2 电炉钢冶炼电耗计算方法电炉钢冶炼电耗按以下计算公式计算。
)().()/.(吨电炉钢合格产出量时千瓦电炉钢电力耗用量吨时千瓦电炉钢冶炼电耗=——————————————。
- 1、下载文档前请自行甄别文档内容的完整性,平台不提供额外的编辑、内容补充、找答案等附加服务。
- 2、"仅部分预览"的文档,不可在线预览部分如存在完整性等问题,可反馈申请退款(可完整预览的文档不适用该条件!)。
- 3、如文档侵犯您的权益,请联系客服反馈,我们会尽快为您处理(人工客服工作时间:9:00-18:30)。
ICS
备案号:
DB33
吨钢可比能耗限额与计算方法
(征求意见稿)
浙江省质量技术监督局 发布
前言
本标准由浙江省经济贸易委员会提出并归口。
本标准起草单位:浙江省节能协会。
本标准主要起草人:
吨钢可比能耗限额与计算方法
(征求意见稿)
1 范围
本标准规定了钢铁联合企业吨钢可比能耗限额及计算方法。
本标准适用于钢铁联合企业。
2 规范性引用文件
下列文件中的条款通过本标准的引用而成为本标准的条款。
凡是注日期的引用文件,其随后所有的修改单(不包括勘误的内容)或修订版均不适用于本标准,然而,鼓励根据本标准达成协议的各方研究是否可使用这些文件的最新版本。
凡是不注日期的引用文件,其最新版本适用于本标准。
GB 17167-2006《用能单位计量器具配备与管理通则》;
GB/T 6422《企业能耗计量与测试通则》;
GB33/××××-××××《用能单位能源消耗量化管理要求》;
《关于颁发〈钢铁企业能源平衡及能耗指标计算办法的暂行规定〉的通知》冶金工业部(82)冶能字第551号;
《关于统一钢铁企业能源统计报表中各类能源折算系数的通知》冶金工业部(84)冶能办字第005号;
《主要行业产品能源消耗指标培训材料》主编单位:国家统计局工交司、中国钢铁工业协会等,2006年8月。
3 定义
吨钢可比能耗是指钢铁企业在报告期内,每生产一吨粗钢,从炼焦、烧结、炼铁、炼钢直到企业最终钢材配套生产所必须的耗能量及企业燃料加工与运输、机车运输能耗及企业能源亏损所分摊在每吨粗钢上的耗能量之和。
不包括钢铁工业企业的采矿、选矿、铁合金、耐火材料制品、炭素制品、煤化工产品及其它产品生产、辅助生产及非生产的能耗。
4 吨钢可比能耗的限额
本限额适用期限为2006年~2010年。
指标名称计量单位指标限额
吨钢可比能耗千克标准煤/吨 630
5 吨钢可比能耗的计算方法
钢铁企业可参照本标准引用文件中相关文件的规定,定期编制《钢铁企业能源平衡表》,并依照以下计算方法计算吨钢可比能耗,见表1。
表1 吨钢可比能耗计算方法。