消除内应力
消除内应力说明

说明:塑料制品退火处理的目的是消除内应力。
比如在制品薄厚的交接部位,厚的部位降温慢、薄的部位降温快些,则连接处发生不均匀收缩,结果这里有应力集中现象。
在有金属镶件的四周,这种现象更明显。
如不进行退火处理,过段时间,在应力集中部位会产生裂纹,甚至开裂或者变形。
退火方法:一般是把制品浸在热油或热水中,也可在热风循环中,按塑料品种的不同,调节退火温度,一般用低于制品热变形温度10-20度,过高温度中制品要变形,但不能温度过低,过低温度退火,不能达到退火效果。
几种常用塑料的退火条件见下表:。
消除工件内应力的热处理方法

消除工件内应力的热处理方法1. 内应力是什么?内应力,听起来是不是很专业?其实就是工件在制造过程中,由于各种原因,比如冷却速度不均匀、加工过程中的变形等,导致的内部压力。
这就像一个人被压得喘不过气来,心里总是有种不舒服的感觉,时不时还得爆发一下。
工件也一样,如果内应力得不到处理,可能会在使用中出现裂纹,或者直接导致失败。
哎,这可真是让人心疼啊!所以,咱们今天要聊聊,怎么通过热处理来消除这些“隐形”的内应力。
别担心,不会让你觉得枯燥无味,我会用轻松幽默的方式,把这些技术性内容讲得简单明了。
准备好了吗?2. 热处理的原理2.1 加热和冷却首先,热处理的核心在于“加热”和“冷却”。
就像你在冬天想喝热汤一样,先把水加热,然后再让它慢慢冷却。
工件也是如此,通过加热到一定温度,让金属内部的分子运动起来,打破那种沉闷的内应力。
想象一下,金属的分子就像聚在一起的小伙伴,热了一下,大家都开始蹦跶,内应力自然就被“舞动”给消除了一部分。
不过,这个过程可不能马虎,冷却速度也要控制好。
有些材料需要慢慢降温,像是给它们一个温柔的拥抱,而有些则可以快速冷却,犹如给它们来个猛然的“冷水浴”。
不同的工件、不同的材料,处理方式也各有千秋,真是让人琢磨不透!2.2 热处理的类型说到热处理,种类可多了,咱们最常见的有退火、正火、淬火和回火。
听起来很复杂,其实就像点菜一样,各有各的特色。
退火:简单来说,就是把工件加热到一定温度,保持一段时间,然后缓慢冷却。
就像给工件一个大大的安慰,让它放松心情,内应力自然就消失得无影无踪。
正火:这个有点像“火锅”,把工件放在高温中,然后再在空气中冷却。
能提高它的力学性能,让工件“练出一身好本领”。
淬火:别小看这个名字,淬火可是个狠角色!加热后迅速冷却,强大的冷却速度让内应力瞬间消失,但这也会让工件变得脆弱,需要再来一次回火,才能让它强壮起来。
3. 热处理的好处3.1 提高性能那么,热处理的好处有哪些呢?首先,它能显著提高工件的力学性能。
消除内应力的方法
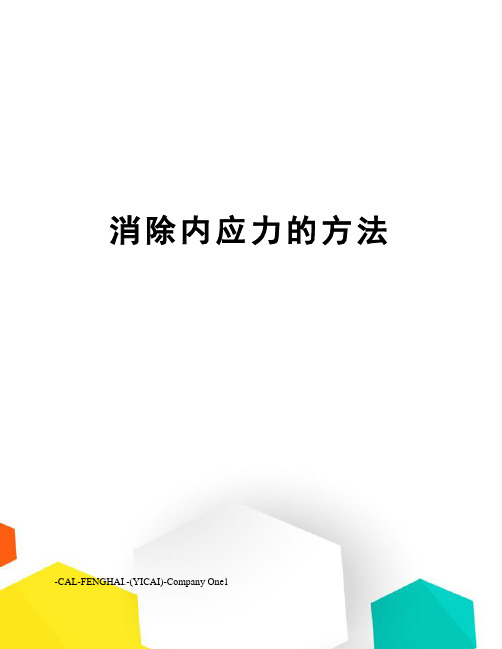
消除内应力的方法-CAL-FENGHAI.-(YICAI)-Company One1消除内应力的方法1,震动消除应力,振动消除应力简介振动时效又称振动消除应力法,是将工件(包括铸件、锻件、焊接结构件等)在其固有频率下进行数分钟至数十分钟的振动处理,消除其残余应力,使尺寸精度获得稳定的一种方法。
这种工艺具有耗能少、时间短、效果显着等特点。
近年来在国内外都得到迅速发展和广泛应用。
振动时效的实质是以振动的形式给工件施加附加应力, 当附加应力与残余应力叠加后, 达到或超过材料的屈服极限时, 工件发生微观塑性变形, 从而降低和均化工件内的残余应力, 并使其尺寸精度达到稳定.在工件上施加附加应力的方法有很多种。
施加静力或静力矩也可得到消除应力、稳定精度的效果,这就是静态过载法以动力形式施加的附加应力也可以是冲击、随机振动或周期振动,周期振动中包括共振。
在本世纪五十年代前后,随着现代科学技术的发展,振动理论、测试技术和激振设备都得到迅速发展,从而发现,在工件的共振频率下进行振动,可以缩短振动处理时间,消除应力和稳定精度的效果更好,能源消耗也最少。
同时出现了相应的振动设备。
这种新型的振动时效工艺和设备的出现,立即受到各国的高度重视,迅速应用于生产实践中。
目前各国采用的振动时效工艺,大多数是共振时效。
这种工艺是将激振器牢固地夹持在被处理工件的适当位置上,通过振动设备的控制部分,根据工件的大小和形状调节激振力,并根据工件的固有频率调节激振频率,直至使联结在工件上的振动传感器(速度计或加速度计)所接收的信号达到一个最大值。
这时标志工件已达到共振。
在这种状态下持续振动一段时间,即可达到消除应力、稳定尺寸精度的目的。
由于这种工艺日趋成熟,振动和控制设备日臻完善,振动时效已为十多个工业发达国家广泛采用。
美国某应力消除公司,进行5000多项振动时效处理,结果分析成本仅为热时效的10%,在消除应力方面完全可取代热时效。
英国和西德对飞机装配型架的焊接梁和框架普遍采用了振动时效,苏联金属切削机床实验科学研究院将振动时效工艺推荐给各机床厂,某些重型机床厂的大件和基础零件全部采用了振动时效。
消除内应力的热处理方法
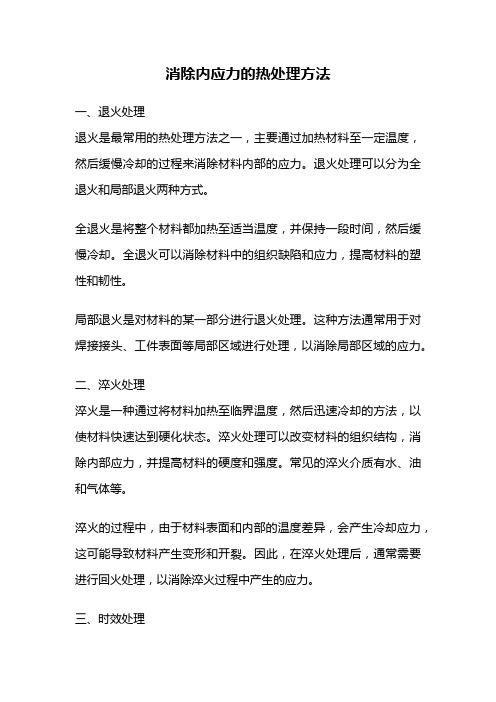
消除内应力的热处理方法一、退火处理退火是最常用的热处理方法之一,主要通过加热材料至一定温度,然后缓慢冷却的过程来消除材料内部的应力。
退火处理可以分为全退火和局部退火两种方式。
全退火是将整个材料都加热至适当温度,并保持一段时间,然后缓慢冷却。
全退火可以消除材料中的组织缺陷和应力,提高材料的塑性和韧性。
局部退火是对材料的某一部分进行退火处理。
这种方法通常用于对焊接接头、工件表面等局部区域进行处理,以消除局部区域的应力。
二、淬火处理淬火是一种通过将材料加热至临界温度,然后迅速冷却的方法,以使材料快速达到硬化状态。
淬火处理可以改变材料的组织结构,消除内部应力,并提高材料的硬度和强度。
常见的淬火介质有水、油和气体等。
淬火的过程中,由于材料表面和内部的温度差异,会产生冷却应力,这可能导致材料产生变形和开裂。
因此,在淬火处理后,通常需要进行回火处理,以消除淬火过程中产生的应力。
三、时效处理时效处理是指将材料在一定温度下保持一段时间,以改变材料的组织结构和性能的方法。
时效处理可以消除材料中的残余应力,并使材料具有更好的稳定性和抗变形能力。
时效处理通常应用于高强度合金材料,如铝合金、镍基合金等。
在时效过程中,材料的晶粒和析出物会发生变化,从而改变材料的性能。
四、焊后热处理在焊接过程中,由于局部加热和快速冷却,会导致焊接接头产生应力集中和变形。
为了消除这些应力和变形,常常需要进行焊后热处理。
焊后热处理包括回火处理和退火处理。
回火处理是将焊接接头加热至一定温度并保持一段时间,然后缓慢冷却的过程。
退火处理是将焊接接头整体加热至一定温度,并保持一段时间,然后缓慢冷却。
通过焊后热处理,可以使焊接接头中的应力得到释放,改善焊接接头的组织和性能。
退火处理、淬火处理、时效处理和焊后热处理是常用的消除内应力的热处理方法。
不同的材料和工艺需要选择适合的热处理方法,以达到消除内应力、改善材料性能的目的。
热处理过程中需要严格控制温度和冷却速率,以保证处理效果。
内应力的产生及消除方法

内应力的产生及消除方法内应力是指物体内部各部分之间以及各个分子之间产生的相互作用力。
内应力的产生主要是由于物体的形状变化或外部作用力的影响,而内应力的消除可以通过物体的形状恢复或有效地去除外部作用力来实现。
下面将详细介绍内应力的产生及消除方法。
一、内应力的产生1.形状变化:当物体的形状发生变化时,内部各部分之间的相互作用力会发生变化,产生内应力。
例如,当拉伸金属丝时,金属丝内部的晶格结构发生变形,使金属丝受到拉伸内应力。
2.外部作用力:当物体受到外部作用力时,外部作用力在物体内部传递,使内部各部分之间产生相互作用力,产生内应力。
例如,当压缩弹簧时,弹簧内部的分子间相互作用力增大,产生压缩内应力。
3.温度变化:当物体受到温度变化时,物体的形状会产生变化,分子之间的相互作用力也会发生变化,从而产生内应力。
例如,当金属材料受到高温热膨胀时,内部分子间的相互作用力会增大,产生热膨胀内应力。
二、内应力的消除方法1.形状恢复:通过改变物体的形状,使内部各部分之间的相互作用力恢复到原始状态,从而消除内应力。
例如,当金属材料受到变形时,可以通过加工、锻造等方法来恢复其原始形状并消除内应力。
2.降低外部作用力:减小物体受到的外部作用力,从而减小内部各部分之间的相互作用力,进而消除内应力。
例如,当弹簧受到压缩时,可以减小外部作用力来消除内应力。
3.控制温度变化:通过控制物体所处的温度,使其形状保持稳定,从而减小内应力。
例如,在制造金属制品时,可以控制金属材料的加热和冷却过程,以避免或减小温度变化引起的内应力。
4.应力放松:通过在物体上施加一个与内应力相反方向的应力来消除内应力。
例如,当金属材料受到弯曲后,可以施加相反方向的拉伸力来消除内应力。
5.材料选择:选择具有较小内应力的材料来制造物体,从而减小内应力的产生。
例如,选择材料的热膨胀系数较小的特性,可以减小温度变化引起的内应力。
综上所述,内应力的产生主要是由于物体的形状变化或外部作用力的影响。
退火消除内应力的机理

退火消除内应力的机理引言:退火是一种常见的金属加工工艺,通过加热和冷却过程中的晶格再排列,来消除材料内部的应力。
本文将详细介绍退火消除内应力的机理,以及其在金属加工中的重要性。
一、退火的定义和作用退火是指将材料加热到一定温度,保持一定时间后再缓慢冷却的过程。
通过这种方法,可以使材料内部的应力得到释放和消除,从而提高材料的机械性能和稳定性。
二、退火的机理1. 晶体结构的再排列退火过程中,材料的晶体结构会发生再排列。
晶体内部的位错和缺陷会通过原子的扩散运动,重新分布和排列,从而减少晶界和位错的密度,进而降低材料的内部应力。
2. 晶粒长大和细化退火过程中,晶粒的尺寸会发生变化。
在加热过程中,原子的扩散速度增加,晶粒会长大;而在冷却过程中,原子的扩散速度减慢,晶粒会细化。
晶粒的长大和细化可以改变材料的内部应力分布,进而减小应力集中区域,提高材料的抗应力集中能力。
3. 残余应力的释放退火过程中,材料中的残余应力会逐渐释放。
在加热过程中,材料内部的应力会逐渐减小,达到平衡状态;在冷却过程中,由于晶体结构的再排列,材料的内部应力会进一步减小,直至消除。
三、退火对材料性能的影响1. 提高材料的塑性和韧性退火可以使材料的晶体结构更加均匀和稳定,减少内部应力和缺陷,从而提高材料的塑性和韧性。
在退火后的材料中,原子的扩散能力增强,晶体结构更加完善,有利于材料的变形和形变。
2. 改善材料的硬度和强度虽然退火可以提高材料的塑性和韧性,但同时也会降低材料的硬度和强度。
在退火过程中,晶界和位错的密度减小,晶粒尺寸增大,导致材料的强度降低。
因此,在金属加工过程中,需要根据实际需求来选择合适的退火工艺,以平衡材料的硬度和韧性。
3. 优化材料的微观组织和性能退火可以优化材料的微观组织和性能。
通过合理的退火工艺,可以调控材料的晶粒尺寸、晶界特征和位错密度,从而改善材料的力学性能、耐腐蚀性能和热稳定性。
四、退火在金属加工中的应用退火是金属加工工艺中不可或缺的环节。
焊接件消除内应力的方法
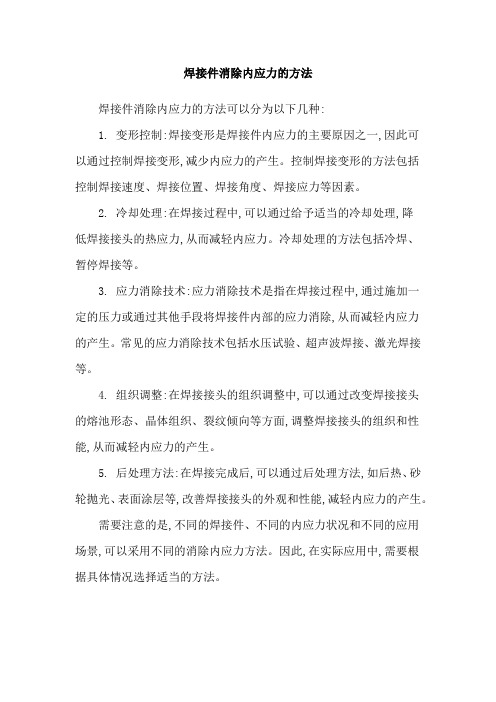
焊接件消除内应力的方法
焊接件消除内应力的方法可以分为以下几种:
1. 变形控制:焊接变形是焊接件内应力的主要原因之一,因此可
以通过控制焊接变形,减少内应力的产生。
控制焊接变形的方法包括
控制焊接速度、焊接位置、焊接角度、焊接应力等因素。
2. 冷却处理:在焊接过程中,可以通过给予适当的冷却处理,降
低焊接接头的热应力,从而减轻内应力。
冷却处理的方法包括冷焊、
暂停焊接等。
3. 应力消除技术:应力消除技术是指在焊接过程中,通过施加一
定的压力或通过其他手段将焊接件内部的应力消除,从而减轻内应力
的产生。
常见的应力消除技术包括水压试验、超声波焊接、激光焊接等。
4. 组织调整:在焊接接头的组织调整中,可以通过改变焊接接头
的熔池形态、晶体组织、裂纹倾向等方面,调整焊接接头的组织和性能,从而减轻内应力的产生。
5. 后处理方法:在焊接完成后,可以通过后处理方法,如后热、砂轮抛光、表面涂层等,改善焊接接头的外观和性能,减轻内应力的产生。
需要注意的是,不同的焊接件、不同的内应力状况和不同的应用
场景,可以采用不同的消除内应力方法。
因此,在实际应用中,需要根
据具体情况选择适当的方法。
焊接结构件消除内应力退火工艺守则
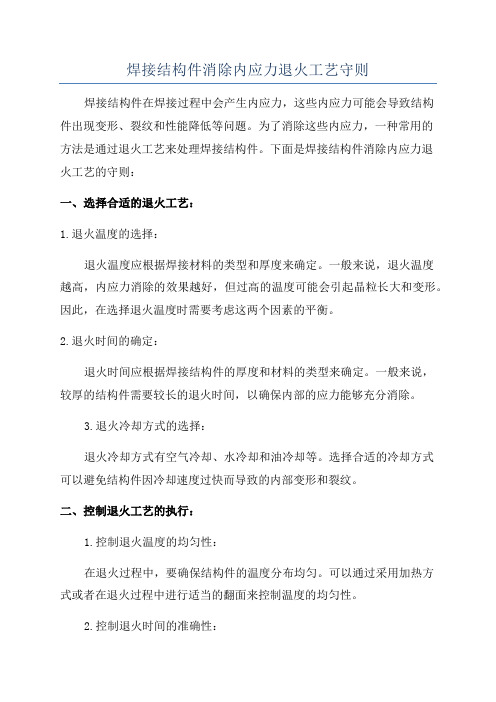
焊接结构件消除内应力退火工艺守则焊接结构件在焊接过程中会产生内应力,这些内应力可能会导致结构件出现变形、裂纹和性能降低等问题。
为了消除这些内应力,一种常用的方法是通过退火工艺来处理焊接结构件。
下面是焊接结构件消除内应力退火工艺的守则:一、选择合适的退火工艺:1.退火温度的选择:退火温度应根据焊接材料的类型和厚度来确定。
一般来说,退火温度越高,内应力消除的效果越好,但过高的温度可能会引起晶粒长大和变形。
因此,在选择退火温度时需要考虑这两个因素的平衡。
2.退火时间的确定:退火时间应根据焊接结构件的厚度和材料的类型来确定。
一般来说,较厚的结构件需要较长的退火时间,以确保内部的应力能够充分消除。
3.退火冷却方式的选择:退火冷却方式有空气冷却、水冷却和油冷却等。
选择合适的冷却方式可以避免结构件因冷却速度过快而导致的内部变形和裂纹。
二、控制退火工艺的执行:1.控制退火温度的均匀性:在退火过程中,要确保结构件的温度分布均匀。
可以通过采用加热方式或者在退火过程中进行适当的翻面来控制温度的均匀性。
2.控制退火时间的准确性:退火时间应严格控制,以确保结构件的内应力能够充分消除。
可以通过在退火过程中进行监测和记录来控制退火时间的准确性。
3.控制退火冷却速度:退火冷却速度不能过快,否则可能会引起结构件的变形和裂纹。
可以通过改变冷却介质的性质或者调整冷却介质的温度来控制退火冷却速度。
三、注意焊接结构件的预处理:1.去除焊接结构件表面的油污和氧化物等杂质,以避免这些杂质在退火过程中产生不良影响。
2.控制焊接结构件的加热速度和温度分布,以避免在焊接过程中产生过高的内应力。
以上就是焊接结构件消除内应力退火工艺的守则。
通过合理选择退火工艺以及控制退火工艺的执行,可以有效地消除焊接结构件的内应力,提高结构件的性能和耐久性。
- 1、下载文档前请自行甄别文档内容的完整性,平台不提供额外的编辑、内容补充、找答案等附加服务。
- 2、"仅部分预览"的文档,不可在线预览部分如存在完整性等问题,可反馈申请退款(可完整预览的文档不适用该条件!)。
- 3、如文档侵犯您的权益,请联系客服反馈,我们会尽快为您处理(人工客服工作时间:9:00-18:30)。
对应:消除内应力的方法1形变与应力关系材料的力学特性是指材料在外力的作用下,产生变形,流动与破坏的性质,反应材料基本力学性质的量主要有两类;一类是反应材料变形情况的量如模量或柔度,泊桑比;另一类是反应材料破坏过程的量,如比例极限,拉伸强度,屈服应力,拉伸断裂等作用。
从力学观?憧矗 牧掀苹凳且桓龉 潭 皇且桓龅恪?BR>2应力与时间的关系应力对其作用时间的依赖性,这是聚合物材料主要特征之一。
聚合物在较高温度下力作用时间较短的应力松驰行为和在温度较低力作用时间较长的应力松驰行为是一致的。
3形变与时间关系聚合物材料在一定温度下承受恒定载荷时,将讯速地发生变形,然后在缓慢的速率下无限期地变形下去。
若载荷足够高时变形会继续到断裂为此。
这种在温度和载荷都是恒定的条件下,变形对时间依赖的性质,即称蠕变性质。
第四节聚合物的流变性能一概述注塑中把聚合物材料加热到熔融状态下进行加工。
这时可把熔体看成连续介质,在机器某些部位上,如螺杆,料筒,喷嘴及模腔流道中形成流场。
在流场中熔体受到应力,时间,温度的联合作用发生形变或流动。
这样聚合物熔体的流动就和机器某些几何参数和工艺参数发生密切的联系。
处于层流状态下的聚合物熔体,依本身的分子结构和加工条件可分近似牛顿型和非牛顿型流体它们的流变特性暂不予祥细介绍。
1 关于流变性能(1)剪切速率,剪切应力对粘度的影响通常,剪切应力随剪切速率提高而增加,而粘度却随剪切速率或剪切应力的增加而下降。
剪切粘度对剪切速率的依赖性越强,粘度随剪切速率的提高而讯速降低,这种聚合物称作剪性聚合物,这种剪切变稀的现象是聚合物固有的特征,但不同聚合物剪切变稀程度是不同的,了解这一点对注塑有重要意义。
(2)离模膨胀效应当聚合物熔体离开流道口时,熔体流的直径,大于流道出口的直径,这种现象称为离模膨胀效应。
普遍认为这是由聚合物的粘弹效应所引起的膨胀效应,粘弹效应要影响膨胀比的大小,温度,剪切速率和流道几何形状等都能影响熔体的膨胀效应。
所以膨胀效应是熔体流动过程中的弹性反映,这种行为与大分子沿流动方向的剪切应力作用和垂直于流动方向的法向应力作用有关。
在纯剪切流动中法向效应是较小的。
粘弹性熔体的法向效应越大则离模膨胀效应越明显。
流道的影响;假如流道长度很短,离模效应将受到入口效应的影响。
这是因为进入浇口段的熔体要收剑流动,流动正处在速度重新分布的不稳定时期,如果浇口段很短,熔体料流会很快地出口,剪切应力的作用会突然消失,速度梯度也要消除,大分子发生蜷? 曰指矗 饣崾估肽E蛘托в 泳纭H绻 鞯雷愎怀ぃ 虻 杂Ρ淠苡凶愎坏氖奔浣 械 运沙邸U馐庇跋炖肽E蛘托вΦ闹饕 蚴俏榷 鞫 钡募羟械 院头ㄏ蛐вΦ淖饔谩?BR>(3)剪切速率对不稳定流动的影响剪切速率有三个流变区:低剪切速率区,在低剪切速率下被破坏的高分子链缠结能来得及恢复,所以表现出粘度不变的牛顿特性。
中剪切区,随着剪切速率的提高,高分子链段缠结被顺开且来不及重新恢复。
这样就助止了链段之间相对运动和内磨擦的减小。
可使熔体粘度降低二至三个数量级,产生了剪切稀化作用。
在高剪切区,当剪切速率很高粘度可降至最小,并且难以维持恒定,大分子链段缠结在高剪切下已全部被拉直,表现出牛顿流体的性质。
如果剪切速率再提高,出现不稳定流动,这种不稳定流动形成弹性湍流熔体出现波纹,破裂现象是熔体不稳定的重要标志。
当剪切速率达到弹性湍流时,熔体不仅不会继续变稀,反而会变稠。
这是因为熔体发生破裂。
(4)温度对粘度的影响粘度依赖于温度的机理是分子链和“自由体积”与温度之间存在着关联。
当在玻璃化温度以下时,自由体积保持恒定,体积随温度增长而大分子链开始振动。
当温度超过玻璃化温度时,大链段开始移动,链段之间的自由体积增加,链段与链段之间作用力减小,粘度下降。
不同的聚合物粘度对温度的敏感性有所不同。
(5)压力对粘度的影响聚合物熔体在注塑时,无论是预塑阶段,还是注射阶段,熔体都要经受内部静压力和外部动压力的联合作用。
保压补料阶段聚合物一般要经受1500~2000kgf/cm2压力作用,精密成型可高达4000kgf/cm2,在如此高的压力下,分子链段间的自由体积要受到压缩。
由于分子链间自由体积减小,大分子链段的靠近使分子间作用力加强即表现粘度提高。
在加工温度一定时,聚合物熔体的压缩性比一般液体的压缩性要大,对粘度影响也较大。
由于聚合物的压缩率不同,所以粘度对压力的敏感性也不同;压缩率大的敏感性大。
聚合物也由于压力提高会使粘度增加,能起到和降低熔体温度一样的等效作用。
(6)分子量对粘度的影响一般情况下粘度随分子量增加而增加,由于分子量增加使分子链段加度,分子链重心移动越慢,链段间的相对们移抵消? 嵩蕉啵 肿恿吹娜嵝约哟蟛 岬阍龆啵 吹慕馔押突 评 选J沽鞫 讨υ龃螅 枰 氖奔浜湍芰恳苍黾印?BR>由于分子量增加引起聚合物流动降低,使注塑困难,因此常在高分子量的聚合物中加入一些低分子物质,如增塑剂等,来降低聚合物的分子量,以达到减小粘度,改善加工性能。
特此声明:此资料是网上转载经本人整理供注塑人第三章制品成型机理第一节结晶效应1结晶概念聚合物的超分子结构对注塑条件及制品性能的影响非常明显。
聚合物按其超分子结构可分为结晶型和非结晶型,结晶型聚合物的分子链呈有规则的排列,而非结晶态聚合物的分子链呈不规则的无定型的排列。
不同形态表现出不同的工艺性质误物理—机械性质。
一般结晶型聚合物具有耐热性和较高的机械强度,而非结晶型则相反。
分子结构简单,对称性高的聚合物都能生成结晶,如PE等,分子链节虽然大,但分子间的作用力很强也能生成结晶,如POM,PA等。
分子链刚性大的聚合物不易生成结晶,如PC,PSU,PPO等。
评定聚合物结晶形态的标准是晶体形状,大小及结晶度。
2 聚合物结晶度对制品性能的影响(1)密度. 结晶度高说明多数分子链已排列成有序而紧密的结构,分子间作用力强,所以密度随结晶度提高而加大,如70%结晶度的PP,其密度为0.896,当结晶度增至95%时则密度增至o.903。
(2)拉伸强度结晶度高,拉伸强度高。
如结晶度70%的聚丙烯其拉伸强度为27.5m pa,当结晶度增至95%时,则拉伸强度可提高到42m pa。
(3)冲击强度冲击强度随结晶度提高而减小,如70%结晶度的聚丙烯,其缺口冲击强度15.2kgf-cm/cm2,当结晶度95%时,冲击强度减小到4.86kgf-cm/cm2。
(4)热性能结晶度增加有助于提高软化温度和热变形温度。
如结晶度为70%的聚丙烯,载荷下的热变形温度为125度,而结晶度95%时侧为151度。
刚度是注塑制品脱模条件之一,较高的结晶度会减少制品在模内的冷却周期。
结晶度会给低温带来脆弱性,如结晶度分别为55%,85%,95%的等规聚丙烯其脆化温度分别为0度,10度,20度。
(5)翘曲结晶度提高会使体积减小,收缩加大,结晶型材料比非结晶型材料更易翘曲,这是因为制品在模内冷却时,由于温度上的差异引起结晶度的差异,使密度不均,收缩不等,导致产生较高的内应力而引起翘曲,并使耐应力龟裂能力降低。
(6)光泽度结晶度提高会增加制品的致密性。
使制品表面光泽度提高,但由于球晶的存在会引起光波的散射,而使透明度降低。
3影响结晶度的因素(1)温度及冷却速度结晶有一个热历程,必然与温度有关,当聚合物熔体温度高于熔融温度时大分子链的热运动显著增加,到大于分子的内聚力时,分子就难以形成有序排列而不易结晶;当温度过低时,分子链段动能很低,甚至处于冻结状态,也不易结晶。
所以结晶的温度范围是在玻璃化温度和熔融温度之间。
在高温区(接近熔融温度),晶核不稳定,单位时间成核数量少,而在低温区(接近玻璃化温度)自由能低,结晶时间长,结晶速度慢,不能为成核创造条件。
这样在熔融温度和玻璃化温度之间存在一个最高的结晶速度和相应的结晶温度。
温度是聚合物结晶过程最敏感性因素,温度相差1度,则结晶速度可能相差很多倍。
聚合物从熔点温度以上降到玻璃化温度以下,这一过程的速度称冷却速度,它是决定晶核存在或生长的条件。
注塑时,冷却速度决定于熔体温度和模具温度之差,称过冷度。
根据过冷度可分以下三区。
a等温冷却区,当模具温度接近于最大结晶速度温度时,这时过冷度小,冷却速度慢,结晶几乎在静态等温条件下进行,这时分子链自由能大,晶核不易生成,结晶缓慢,冷却周期加长,形成较大的球晶。
b快速冷却区,当模具温度低于结晶温度时过冷度增大,冷却速度很快结晶在非等温条件下进行,大分子链段来不及折叠形成晶片,这时高分子松驰过程滞后于温度变化的速度,于是分子链在骤冷下形成体积松散的来不及结晶的无定型区。
例如:当模具型腔表面温度过低时,制品表层就会出现这种情况,而在制品心部由于温度梯度的关系,过冷度小,冷却速度慢就形成了具有微晶结构的结晶区。
c中速成冷却区,如果把冷却模温控制在熔体最大结晶速度温度与玻璃化温度之间,这时接近表层的区域最早生成结晶,由于模具温度较高,有利于制品内部晶核生成和球晶长大。
结晶的也比较完整。
在这一温度区来选择模温对成型制品是有利的,因为这时结晶速率常数大,模温较低,制品易脱模,具注塑周期短。
例如:PETP。
建议模温控制在(140~190度),PA6, PA66,模温控制在(70~120度),PP模温控制在(30~80)这有助于结晶能力提高在注塑中模温的选择应能使结晶度尽可能达到最接近于平衡位置。
过低过高都会使制品结构不稳定,在后期会发生结晶过程在温度升高时而发生变化,引起制品结构的变化。
(2)熔体应力作用,熔体压力的提高,剪切作用的加强都会加速结晶过程。
这是由于应力作用会使链段沿受力方向而取向,形成有序区,容易诱导出许多晶胚,使用权晶核数量增加,生成结晶时间缩短,加速了结晶作用。
压力加大还会影响球晶的尺寸和形状,低压下容易生成大而完整的球晶,高压下容易生成小而不规则的球晶。
球晶大小和形状除与大小有关还与力的形式有关。
在均匀剪切作用下易生成均匀的微晶结构,在直接的压力作用下易生成直径小而不均匀的球晶。
螺杆式注塑机加工时,由于熔体受到很大的剪切力作用,大球晶被粉碎成微细的晶核,形成均匀微晶。
而塞式注塑机相反。
球晶的生成和发展与注塑工艺及设备条件有关。
用温度和剪切速率都能控制结晶能力。
在高剪切速率下得到的PP制品冷却后具有高结晶度的结构,而且PP受剪切作用生成球晶的时间比无剪切作用在静态熔体中生成球晶的时间要减少一半。
对结晶型聚合物来说,结晶和取向作用密切相关,因此结晶和剪切应力也就发生联系;剪切作用将通过取向和结晶两方面的途径来影响熔体的粘度。
从而也就影响了熔体在喷嘴,流道,浇口,型腔中的流动。
根据聚合物取向作用可提前结晶的道貌岸然理,在注塑中提高注射压力和注射速率而降低熔体粘度的办法为结晶创造条件。