橡胶配合体系
【详细】橡胶的各种硫化体系讲解!(收藏)
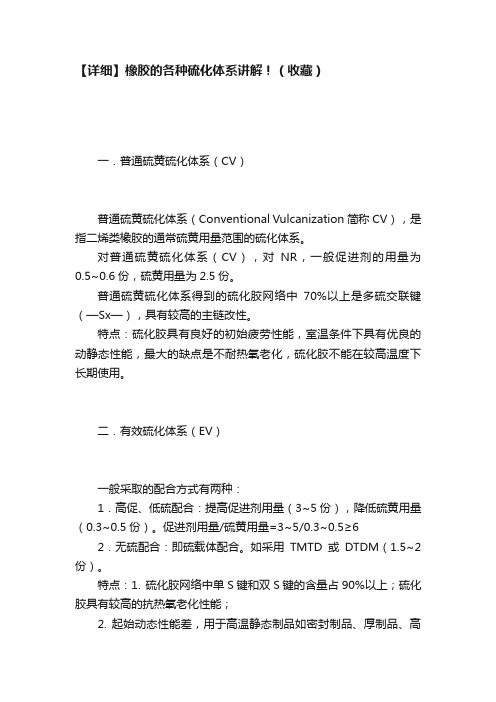
【详细】橡胶的各种硫化体系讲解!(收藏)一.普通硫黄硫化体系(CV)普通硫黄硫化体系(Conventional Vulcanization简称CV),是指二烯类橡胶的通常硫黄用量范围的硫化体系。
对普通硫黄硫化体系(CV),对NR,一般促进剂的用量为0.5~0.6份,硫黄用量为2.5份。
普通硫黄硫化体系得到的硫化胶网络中70%以上是多硫交联键(—Sx—),具有较高的主链改性。
特点:硫化胶具有良好的初始疲劳性能,室温条件下具有优良的动静态性能,最大的缺点是不耐热氧老化,硫化胶不能在较高温度下长期使用。
二.有效硫化体系(EV)一般采取的配合方式有两种:1.高促、低硫配合:提高促进剂用量(3~5份),降低硫黄用量(0.3~0.5份)。
促进剂用量/硫黄用量=3~5/0.3~0.5≥6 2.无硫配合:即硫载体配合。
如采用TMTD或DTDM(1.5~2份)。
特点:1. 硫化胶网络中单S键和双S键的含量占90%以上;硫化胶具有较高的抗热氧老化性能;2. 起始动态性能差,用于高温静态制品如密封制品、厚制品、高温快速硫化体系。
三.半有效硫化体系(SEV)为了改善硫化胶的抗热氧老化和动态疲劳性能,发展了一种促进剂和硫黄的用量介于CV和EV之间的硫化体系,所得到的硫化胶既具有适量的多硫键,又有适量的单、双硫交联键,使其既具有较好的动态性能,又有中等程度的耐热氧老化性能,这样的硫化体系称为半有效硫化体系(SEV)。
用于有一定的使用温度要求的动静态制品。
一般采取的配合方式有两种:1.促进剂用量/硫用量=1.0/1.0=1(或稍大于1);2.硫与硫载体并用,促进剂用量与SEV中一致。
NR的三种硫化体系配合如下表所示:配方成分C V EV高促低硫无硫配合Semi—EV高促低硫硫\硫载体并用SNOB STMT DDMD T 2.50.60.53.0 1.10.6 1.11.11.5 1.51.5 0.60.6四.高温快速硫化体系随着橡胶工业生产的自动化、联动化,高温快速硫化体系被广泛采用,如注射硫化、电缆的硫化等。
橡胶的配合
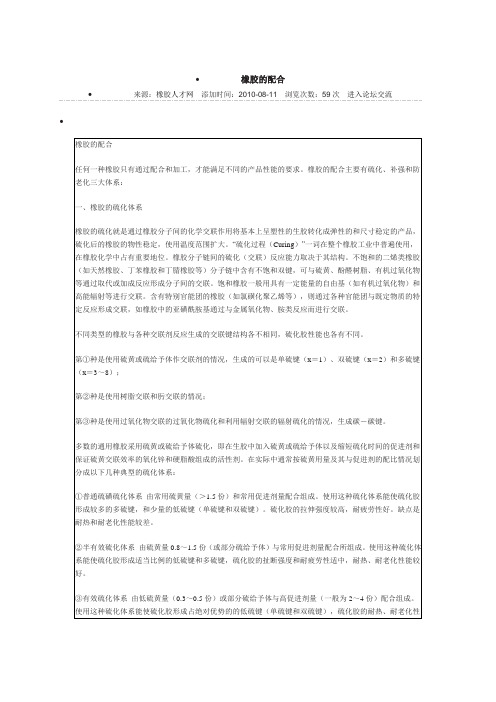
∙橡胶的配合∙来源:橡胶人才网添加时间:2010-08-11浏览次数:59次进入论坛交流∙橡胶的配合任何一种橡胶只有通过配合和加工,才能满足不同的产品性能的要求。
橡胶的配合主要有硫化、补强和防老化三大体系:一、橡胶的硫化体系橡胶的硫化就是通过橡胶分子间的化学交联作用将基本上呈塑性的生胶转化成弹性的和尺寸稳定的产品,硫化后的橡胶的物性稳定,使用温度范围扩大。
“硫化过程(Curing)”一词在整个橡胶工业中普遍使用,在橡胶化学中占有重要地位。
橡胶分子链间的硫化(交联)反应能力取决于其结构。
不饱和的二烯类橡胶(如天然橡胶、丁苯橡胶和丁腈橡胶等)分子链中含有不饱和双键,可与硫黄、酚醛树脂、有机过氧化物等通过取代或加成反应形成分子间的交联。
饱和橡胶一般用具有一定能量的自由基(如有机过氧化物)和高能辐射等进行交联。
含有特别官能团的橡胶(如氯磺化聚乙烯等),则通过各种官能团与既定物质的特定反应形成交联,如橡胶中的亚磺酰胺基通过与金属氧化物、胺类反应而进行交联。
不同类型的橡胶与各种交联剂反应生成的交联键结构各不相同,硫化胶性能也各有不同。
第①种是使用硫黄或硫给予体作交联剂的情况,生成的可以是单硫键(x=1)、双硫键(x=2)和多硫键(x=3~8);第②种是使用树脂交联和肟交联的情况;第③种是使用过氧化物交联的过氧化物硫化和利用辐射交联的辐射硫化的情况,生成碳-碳键。
多数的通用橡胶采用硫黄或硫给予体硫化,即在生胶中加入硫黄或硫给予体以及缩短硫化时间的促进剂和保证硫黄交联效率的氧化锌和硬脂酸组成的活性剂。
在实际中通常按硫黄用量及其与促进剂的配比情况划分成以下几种典型的硫化体系:①普通硫磺硫化体系由常用硫黄量(>1.5份)和常用促进剂量配合组成。
使用这种硫化体系能使硫化胶形成较多的多硫键,和少量的低硫键(单硫键和双硫键)。
硫化胶的拉伸强度较高,耐疲劳性好。
缺点是耐热和耐老化性能较差。
②半有效硫化体系由硫黄量0.8~1.5份(或部分硫给予体)与常用促进剂量配合所组成。
三元乙丙(EPDM)橡胶配方的配合体系介绍

三元乙丙(EPDM)橡胶配方的配合体系介绍三元乙丙橡胶可以采用二烯烃类橡胶用的普通硫化方法硫化,但由于硫化速度较慢,故近年发展了高不饱和度三元乙丙橡胶,其硫化速度不低于高不饱和橡胶的。
三元乙丙橡胶通常可用硫黄、过氧化物、醌肟和反应性树脂等多种硫化体系进行硫化。
不同的硫化体系对其混炼胶的门尼粘度、焦烧时间、硫化速度以及硫化胶的次联键型、物理机械性能(如应力-应变、滞后、压缩变形以及耐热等性能)亦有着直接的影响。
硫化体系的选择要根据所用乙丙橡胶的类型、产品物理机械性能、操作安全性、喷霜以及成等因素加以综合考虑。
一、硫化体系乙丙橡胶常见交联剂体系的适用性和特点1硫黄硫化体系硫黄硫化体系是三元乙丙橡胶使用最广泛最主要的硫化体系。
在硫黄硫化体系中,由于硫黄在乙丙橡胶中溶解度较小,容易喷霜,不宜多用。
一般硫黄用量应控制在1~2份范围内。
在一定硫黄用量范围内,随硫黄用量增加,胶料硫化速度加快,焦烧时间缩短,硫化胶拉伸强度、定伸应力和硬度增高,拉断伸长率下降。
硫黄用量超过2份时,耐热性有下降,高温下压缩永久变形增大。
为使胶料不喷霜,促进剂的用量亦必须保持在三元乙丙橡胶的喷霜极限溶解度以下。
实际上,在工业生产中,基于以下原因几乎都是采用二种或多种促进剂的并用体系。
(1)多种促进剂并用,容易达到硫化作用平衡。
(2)许多促进剂在较低浓度时,就会发生喷霜,因此用量不宜太高。
(3)促进剂这间的协同效应,有利于导致硫化时间的缩短和交联密度的提高。
硫黄硫化体系中,促进剂的用量还可以通过增加硬脂酸的用量来提高,当其它条件不变的情况下,硬脂酸用量增加会导致交联密度、单硫和双硫交联键增加。
氧化锌用量的增加亦有助于在交联时形成促进剂,从而提高胶料的交联密度及抗返原性,改善动态疲劳性能和耐热性能。
2硫黄给予体硫化采用硫黄给予体代替部分硫黄,可使其生成的硫化胶主要具有单硫键或双硫键,因而可以改善胶料的耐热和高温下的压缩变形性能,延长焦烧时间。
橡胶配合体系
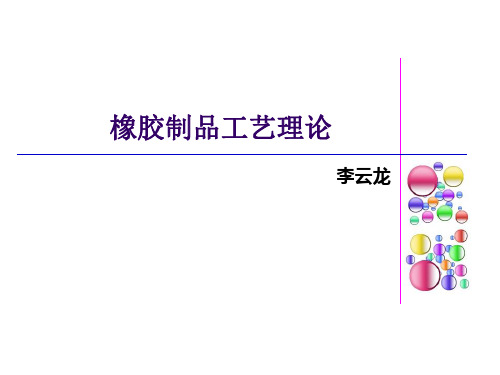
(二)硫化温度和硫化时间
硫化温度是硫化反应的最基本条件。硫化温度的高低,可直接影响硫化
速度、产品质量和企业的经济效益。 硫化温度高,硫化速度快,生产效率高; 反之生产效率低。
提高硫化温度会导致以下问题: (1)引起橡胶分子链裂解和硫化返原,导致胶料力学性能下降; (2)使橡胶制品中的纺织物强度降低;
炭黑、果壳粉、软木粉、木质素、煤粉、树脂等。 陶土、碳酸钙、硅铝炭黑等。 炭黑及绝大多数无机填料。
绝大多数树脂填料。
石棉、短纤维、碳纤维、金属晶须等。
黑色填料 按颜色分 非黑色填料
第二节 常用填充剂
一、炭黑 二、白炭黑 三、有机填充剂 四、无机填充剂 五、短纤维填充剂 六、纳米增强技术
一、炭黑
1. 炭黑的分类: 按制法分 炉法炭黑 槽法炭黑 热裂法 新工艺炭黑 硬质炭黑 软质炭黑
3. 选用原则
①促进剂的工艺性能
②制品的使用性能
从工艺性能角度出发, 要求胶料不易焦烧,硫 化速度快,而且不容易 过硫。
要求硫化胶有良好的物 理性能,硫化胶的性能由其 网络结构所决定。
三、活化剂
1.种类
(1)无机类: ZnO、MgO、PbO、 SnCl2 (2)有机类: 硬脂酸(锌)、月桂酸(锌)、 二乙醇胺、二苯基胺等
(二)硫化历程图
根据硫化历程分析,可将硫化曲线分成四个阶段 ◆ 焦烧阶段:热硫化开始前的延迟作用时间,反映了加工安全性。该阶段取决 于促进剂的品种和用量。 ◆ 热硫化阶段:硫化反应的交联阶段,逐渐产生网络结构,该阶段斜率的大小 反映了硫化速度的快慢。 ◆ 平坦硫化阶段:交联反应基本完成。硫化平坦期的长短取决于胶料配方。 ◆ 过硫化阶段:相当于硫化反应阶段中网构形成的后期。
炭黑
橡胶基本知识

橡胶是一种材料,它在大的形变下能迅速而有力恢复其形变,能够改性;橡胶的弹性模量非常小,并具有相当好的耐气透性以及耐各种化学介质和电绝缘的性能,它可以和多种材料物质并用、共混、复合由此进行改性,以得到良好的综合性能。
橡胶的配合的主要包括五大体系,分别是生胶、硫化体系、防护体系、软化增塑体系和补强体系。
一、生胶生胶是高弹性高聚物材料,作为橡胶的母体材料或称为基体材料。
按制取来源与方法分可以分成天然橡胶和合成橡胶两大类;其中合成橡胶按照应用范围与用途分又可以分成通用橡胶、半通用橡胶、专用合成橡胶和特种橡胶。
1、天然橡胶主要应用与轮胎、胶带、胶管、电线电缆等多数橡胶制品,是应用最广的橡胶。
2、丁苯橡胶大部分的丁苯橡胶用于轮胎工业。
其他产品有汽车零件、工业制品、电线电缆包皮、胶管胶带和鞋类等。
3、氯丁橡胶氯丁橡胶可用来制造轮胎胎侧、耐热阻燃运输带、耐油及耐化学腐蚀的胶管、容器衬里、垫圈、胶辊、汽车和拖拉机配件、门窗密封胶条、止水带等。
4、丁腈橡胶丁腈橡胶有良好的耐油性有可以保持较好的橡胶特性,可以广泛的应用于耐油制品如油封、输油胶管、化工容器衬里、油箱、印刷胶辊、耐油手套、耐油减震器等;由于丁腈橡胶具有半导性,所以可用于余姚导出静电,以免引起火灾的地方,如纺织皮辊、皮圈、阻燃运输带等。
5、乙丙橡胶主要应用于要求耐老化、耐水、耐腐蚀、电气绝缘几个领域,如用于密封垫圈、屋顶单层防水卷材、桥梁减震器、高低压电缆绝缘层、汽车玻璃密封条、轮胎胎侧等。
6、丁基橡胶丁基胶具有突出的气密性和耐热性,主要用于充气轮胎的内侧和无内胎轮胎的气密层,有极好的耐化学药品腐蚀性能可用于化工耐腐蚀容器衬里等。
二、硫化体系硫化体系包括硫化剂、促进剂、活性剂、防焦剂;为橡胶大分子进行化学反应使橡胶油线性大分子交联成空间网状结构。
1、硫化体系一般有硫磺硫化体系、过氧化物硫化体系、硫载体硫化体系;2、促进剂是能缩短硫化时间,降低硫化温度,减少硫化剂用量,提高和改善硫化胶物理力学性能和化学稳定性的化学物质。
实用橡胶工艺学复习资料大全

绪论橡胶配合加工内容●主要内容:原料及配合;加工工艺过程;性能测试。
●配合系统:生胶,硫化体系,补强填充体系,防老体系,增塑及操作体系,特种配合体系。
●加工过程:炼胶,压延,挤出,成型,硫化。
●塑炼:定义为降低分子量,增加塑性,改善加工性能,制成可塑性符合要求的塑料胶。
●混炼:定义为经过配合,将橡胶与配合剂均匀地混合和分散,制成混炼胶。
●门尼粘度:用门尼粘度计测量的是橡胶的本体黏度,原理是将胶料填充在粘度计的模腔和转子之间,合模,在一定温度下〔一般为100℃〕预热〔一般1min〕,令转子转动一定时间〔一般4min〕时测得的转矩值〔N·m〕。
该值越大,说明胶料的黏度越大,常用ML〔1+4〕100℃表示。
●门尼焦烧:这是个说明胶料焦烧时间的指标,通常是在120℃下测定〔加有硫化体系配合剂〕从最低点起,上升5个门尼值的时间。
这个时间越大说明胶料越不容易发生焦烧,加工越安全。
第一章生胶❖分类〔按来源〕:天然橡胶〔NR〕和合成橡胶。
合成橡胶又分为通用橡胶和特种橡胶。
❖通用橡胶:丁苯橡胶〔SBR〕、顺丁橡胶〔BR〕、异戊橡胶〔IR〕、丁腈橡胶〔NBR〕、氯丁橡胶〔CR〕、丁基橡胶〔IIR〕、乙丙橡胶〔EPM,EPDM〕.❖不饱和非极性橡胶:NR、SBR、BR、IR;不饱和极性橡胶:NBR、CR;饱和非极性橡胶:EPM、EPDM、IIR;❖天然橡胶〔NR〕主要由顺—1,4—聚异戊二烯构成,其综合性能好。
❖丁苯橡胶(SBR)是丁二烯和苯乙烯的共聚物,是产量最大的通用橡胶,70%用于轮胎业,根据聚合方法分为乳聚丁苯和溶聚丁苯。
❖苯乙烯含量对丁苯橡胶性能的影响:随着苯乙烯含量的增加,其SBR的性能向聚苯乙烯趋近。
表现为Tg、模量、硬度上升,耐热老化性变好,挤出收缩率变小,挤出物外表光滑,而耐磨性下降,弹性减小。
❖顺丁橡胶(BR)也称聚丁二烯橡胶,弹性最好的通用橡胶,滞后损失小,生热少。
❖乙丙橡胶(EPM,EPDM)属于碳链饱和非极性橡胶,耐臭氧老化性和耐热老化性是通用橡胶中最好的,被誉为不龟裂的橡胶。
橡胶配方设计基础

a
(小点)
x2
x1
b (大点)
b (大点)
应用实例
子午线轮胎子口包胶使用齐聚酯增硬。胶料要求为:
硬度(邵氏A)达到85度;拉伸强度不小于20MPa;扯
断伸长率不小于200%。
x2(0.382)
x1(0.618)
0
5.7
9.3
15
齐聚酯用量(质量份) 0 5.7(0.382) 9.3(0.618) 15
1.4 橡胶配方设计方法
橡胶配方设计主要依赖于人们在生产当中积累的 经验规律,通过大量而繁复的试验来优化配方,造 成大量人力、物力的浪费。
随着科学技术在各个领域的进步和发展,尤其是 计算机技术的迅速发展,橡胶行业已经开始采用计 算机进行配方设计。
1.单因素设计方法
因素:需要考察的影响试验胶料性能指标的因素, 如橡胶配方组分中的硫化剂、补强剂、防老剂等; 水平:每个试验因素可能取值的状态
作业:将下述基本配方换算成其它形式表示的配方, 假设炼胶机的容量为31. 50Kg,要求写出换算公式。
组分 质量/份 配方 /Kg
密度/ 体积/份 (g/cm3)
质量
体积
生产
百分数/% 百分数/%
NR 100.00 0.92 20.00
108.70
S 促M ZnO
2.75 0.75 5.00
2.05 1.42 5.57
250 225
218
200
试验结果:齐聚酯用量的合理范围为2.2~5.7质量份。
平分法(对分法)
如果在试验范围内,目标函数是单调的,要找出满 足一定条件的最优点,可以用平分法。平分法和黄 金分割相似,但平分法逼近最佳范围的速度更快, 在试验范围内每次都可以去掉试验范围的一半,而 且取点方便。
橡胶配合体系及检测
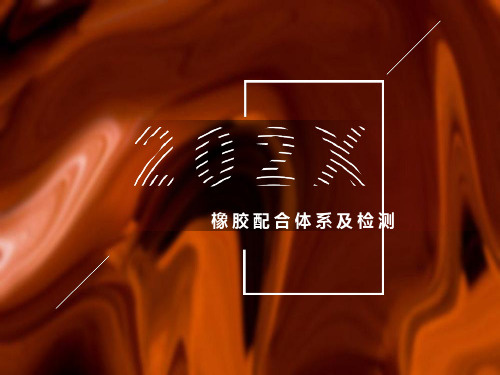
炭黑按制法的分类:
现在橡胶行业使用的C/B主要是炉法C/B。
橡胶配合剂(白炭黑)
2、白炭黑:白炭黑是是一种常用的橡胶补强剂。是硅橡胶最好的补强剂。 1)分类: 2)白炭黑其化学本质是SiO2·nH2O。其使用后能够改进胶料的抗撕裂性能和阻止胶料的裂口增长。 3)白炭黑在使用时一般与硅烷偶联剂并用,以增加其分散性。受硅烷偶联剂影响,炼胶时胶料加工温度一般不超过165 ℃(使用四硫偶联剂时)。
气象法白炭黑
沉淀法白炭黑
橡胶配合剂(填充剂)
1 使用目的: 1)改善加工性。如减少胶料形变,增加压出物表面平坦性等。 2)降低成本。使用后,容积单价与重量单价均大幅下降。 2 使用类型: 1)硅酸盐类。如陶土、高岭土。 2)碳酸盐类。如碳酸钙。
3 其它情况: 1)即使是惰性填充剂,依然有一定的补强性。 2)在表面活性化以后,补强性能有很大的提高。 3)惰性与活性是相对的。活性陶土对NR有补强,但对CR无效。
其中:M代表门(MV) L代表使用大转子测试 S代表使用小传子测试 1代表测试时预热一分钟;4代表检测四分钟
门尼
性能检测
橡胶硫化分四个阶段:焦烧阶段、热硫化阶段、平坦硫化阶段、过硫化阶段
- 1、下载文档前请自行甄别文档内容的完整性,平台不提供额外的编辑、内容补充、找答案等附加服务。
- 2、"仅部分预览"的文档,不可在线预览部分如存在完整性等问题,可反馈申请退款(可完整预览的文档不适用该条件!)。
- 3、如文档侵犯您的权益,请联系客服反馈,我们会尽快为您处理(人工客服工作时间:9:00-18:30)。
分类
硫( 硒,碲)、有机多硫化物、 有机过氧化物、金属氧化物、醌类、 树脂、胺类、特种硫化剂。
有机多硫化物:S、TT等,用于不饱和橡胶。
有机过氧化物:DCP、BPO ,用于饱和及不饱和橡胶。
合成树脂:2402酚醛树脂等 ,用于不饱和橡胶,多用于IIR。 金属氧化物:ZnO、MgO等,用于不饱和橡胶,多用于CR。 醌类化合物: IIR、NR、SBR等二烯类橡胶。主要用于IIR中。 马来酰亚胺衍生物:二烯类橡胶
对其它性能
(1)动态性能:橡胶的动态模量受炭黑的影响,加入炭黑使 G'(弹 性模量)、G"(损耗模量)均增加。炭黑的 比表面积大、活性高、 结构高均使 G'、G"增加,同时受测试条件(如温度、频率和振幅) 的影响。 (2)导电性能:炭黑填充胶会使胶料电阻率下降,其炭黑胶料的电 性能受炭黑结构影响最明显,其次受炭黑的 比表面积、炭黑表面 粗糙度、表面含氧基团浓度的影响。
4. 炭黑对硫化胶性能的影响 对一般性能
(1)粒径:粒径小,撕裂强度、定伸应力、硬度均提高,而弹性 和伸长率下降,压缩永久变形变化很小。 (2)结构:炭黑的结构对定伸应力和硬度均有较大的影响。 (3)表面性质:炭黑粒子表面的粗糙程度及炭黑的结晶状态对补强 作用有一定的影响;炭黑表面的含氧基团对通用不 饱和橡胶的补强作用影响不大,而对象 IIR 这类 近于饱和的弹性 体来说,含氧官能团对炭黑的补 强作用非常重要,含氧基团多得槽法炭黑补强性高。
填充
在橡胶中加入一种物质后,能够提高橡胶的 体积,降低橡胶制品的成本,改善加工工艺 性能,而又不明显影响橡胶制品性能的行为。 凡具有这种能力的物质称之为填充剂。
二、填料的分类
补强剂 按作用分 填充剂
有机填料 按来源分 无机填料 按形状分 粒状填料 树脂填料 纤维填料
炭黑、白炭黑、某些超细无机填料等。 陶土、碳酸钙、胶粉、木粉等。
二、促进剂
1.概念
起促进硫化作用的化学药品
按结构分为八大类:
噻唑类;秋兰姆类;次磺酰胺类;胍类; 二硫代氯基甲酸盐类;硫脲类;醛胺类;黄原酸盐类
2.促进剂的分类
按pH分为三类:
酸性;中性;碱性
按硫化速度分为五类:
超超速级;超速级;准速级;中速级;慢速级 按A、B、N(酸碱性)+数字1、2、3、4、5(速级) 分类: A5、N3、B2
三、硫化介质
◆饱和蒸汽 饱和蒸汽是温度大于100℃并带压力的蒸汽。 ◆过热蒸汽 过热蒸汽是将饱和蒸汽通过加热器加热而获得。 ◆热空气 热空气硫化可在常压和加压情况下进行,前者适应于薄制品硫化; 后者是在硫化罐中进行。 ◆过热水 在100℃以上还保持着液态,这样的水叫过热水。 ◆热水 优点:传热比较均匀,密度较高,制品变形倾向较小。 缺点:导热效率不高。 ◆固体介质 ◆微粒玻璃珠
硫化曲线(Curing curve)
三.理想的硫化曲线
较为理想的橡胶硫化曲线应满足下列条件: ■ 硫化诱导期要足够长,充分保证生产加工的安全性; ■ 硫化速度要快,提高生产效率,降低能耗; ■ 硫化平坦期要长(以保证硫化加工中的安全性,减少过硫危险,以
及保证制品各部位硫化均匀一致)。
第三节 硫化工艺
炭黑
按作用分类
按ASTM-1765-81标准分类:由四位数码组成一个炭黑的代号
2. 炭黑的性质
炭黑的三大基本性质(补强三要素): 粒径(或比表面 积)、结构性和表面活性。
(1)粒径(或比表面积)
炭黑粒子越小,比表面积越大,活性点越多,补强效果越好。 炭黑粒子大小是影响炭黑补强效果的广度因素。一般意义上来说, 相同量的炭黑,粒径越小,比表面越大,补强效果越好。但是太 小的话,炭黑在胶料中难以分散,导致影响补强效果。
(3)防焦剂CTP或PVI
第二节 硫化历程 一、硫化的定义
线性的高分子在物理或化学作用下,形成三维网状体型结构的过程。
实际上就是把塑性的胶料转变成具有高弹性橡胶的过程。
二.硫化历程及硫化参数
(一)硫化历程 1.诱导阶段 硫化剂、活性剂、促进剂之间的反应,生成活性中间化合物,然后进一步引发 橡胶分子链,产生可交联的自由基或离子。 2.交联反应阶段 可交联的自由基或离子与橡胶分子链之间产生连锁反应,生成交联键。 3.网构形成阶段 交联键的重排、短化,主链改性、裂解。
四.硫化方法
(一)硫化室温法 硫化在常温常压下进行。 应用: 1、胶粘剂;2、室温硫化胶浆 (二)冷硫化法
多用于薄膜制品的浸渍硫化。 此法硫化的产品老化性能差,目前很少使用。
(三)热硫化法 1.直接硫化法 (1)热水硫化法 (2)直接蒸汽硫化罐硫化法 (3)热空气硫化 2.间接硫化法 3.加压硫化法 (1)压力机硫化法 (2)罐式硫化机硫化法 (3)个体硫化机硫化 法 (四)连续硫化法
(2)结构性 炭黑粒子结构性:炭黑粒子的基本聚集体的结构形态。是影响 炭黑补强效果的第三因素。形状因素。基本聚集体是炭黑在胶料中 的最小可分散结构。以前衡量结构性采用形状因素F=L/W其中L和 W分别是聚集体整体长度和宽度。F越大,结构性越高。 近年来,采用形态参数主要是不对称度和松密度衡量。形态参数 指电镜下得到的基本聚集体的形态投影用一等效椭圆来模拟。 不对称度=等效椭圆长半径/等效椭圆短半径 松密度=等效椭圆面积/炭黑聚集体平面投影面积 不对称度越大,活性越高。不对称度相近,松密度越大(分叉越 多),活性越大。
炭黑、果壳粉、软木粉、木质素、煤粉、树脂等。 陶土、碳酸钙、硅铝炭黑等。 炭黑及绝大多数无机填料。
绝大多数树脂填料。
石棉、短纤维、碳纤维、金属晶须等。
黑色填料 按颜色分 非黑色填料
第二节 常用填充剂
一、炭黑 二、白炭黑 三、有机填充剂 四、无机填充剂 五、短纤维填充剂 六、纳米增强技术
一、炭黑
1. 炭黑的分类: 按制法分 炉法炭黑 槽法炭黑 热裂法 新工艺炭黑 硬质炭黑 软质炭黑
3. 选用原则
①促进剂的工艺性能
②制品的使用性能
从工艺性能角度出发, 要求胶料不易焦烧,硫 化速度快,而且不容易 过硫。
要求硫化胶有良好的物 理性能,硫化胶的性能由其 网络结构所决定。
三、活化剂
1.种类
(1)无机类: ZnO、MgO、PbO、 SnCl2 (2)有机类: 硬脂酸(锌)、月桂酸(锌)、 二乙醇胺、二苯基胺等
(3)表面活性
炭黑粒子的化学活性:炭黑粒子与橡胶的结合能力。因此,炭 黑粒子的化学活性越大,补强效果越好。——强度因素
3. 炭黑对橡胶的补强作用机理
“微观多相 结构”理论
代表性的补强理论
分子链 滑动学说
4. 炭黑对橡胶加工性能的影响
对混炼的影响 (1)炭黑的粒径越细混炼越困难,吃料慢,耗能高,生热高,分 散越困难。 (2)高结构比低结构吃料慢,但分散快。 (3)炭黑粒径越小,填充量越高,混炼胶的粘度越高,结合胶量 也越多;炭黑的结构度越高,包容 胶量越多,炭黑的有效填 充体积分数增大,混炼胶粘度也提高。
3.专用仪器法
用于测定橡胶硫化特性的测试仪器有各类硫化仪和门尼粘度计。 (1)硫化仪法 (2)门尼粘度仪 门尼焦烧时间 t5:随硫化时间增加,胶料门尼值下降到最低点又开始上升, 一般由最低点上升 至 5 个门尼值的时间称为门尼焦烧时间。 门尼硫化时间 t35:由最低点上升至 35个门尼值所需硫化时间称为门尼硫化 时间。 正硫化时间= t5+10(t35- t5)
(三)硫化参数
1.T10:胶料从加热开始至转矩上升到最大转矩的 10%所需要的时间。 M10=ML+(MH-ML)×10% 2.诱导期(焦烧期):从胶料放入模具至出现轻微硫化的整个过程所需要的 时间叫硫化诱导期, 又称为焦烧时间。 诱导期反应了胶料的加工安全性。 诱导期短,加工安全性差;诱导期太长,会降低生产效率。
(3)导致胶料焦烧时间缩短,减少了充模时间,造成制品局部缺胶;
(4)由于厚制品会增加制品的内外温差,导致硫化不均。
影响硫化温度的因素:
(1) 胶料配方的影响:主要影响因素是橡胶种类和硫化体系。
(2) 硫化方法的影响
注射、连续硫化需要硫化温度相对较高,模压硫化工艺硫化温度相对较低。
(3) 制品外观尺寸的影响 若制品的外形尺寸较厚、规格较大,硫化温度不宜过高,否则会导致表面 过硫、内部欠硫。
门尼硫化速度(Δt30):Δt30= t35-t5
二.硫化条件的选取及确定
硫化条件通常指硫化压力、温度和时间——硫化三要素。
(一)硫化压力
(1) 防止胶料产生气泡,提高胶料的致密性; (2) 使胶料流动,充满模具,以制得花纹清晰的制品; (3) 提高制品中各层(胶层与布层或金属层、布层与布层)之间的粘 着力,改善硫化胶的物 理性能(如耐屈挠性能)。
二、白炭黑
1. 白炭黑分类
白炭黑结构式为:SiO2· 2O nH
习题 1、名词: (1)焦烧;(2)理论正硫化时间;(3)工艺正硫化时间
2、橡胶的硫化曲线分为几个阶段?各阶段的实质和意义是什么?
第三章 补强与填充体系
第一节 概述
第二节 常用填充剂
第一节 概述
一.何谓补强与填充? 补强
在橡胶中加入一种物质后,使硫化胶的耐磨 性、抗撕裂强度、拉伸强度、模量、抗溶胀 性等性能获得较大提高的行为。凡具有这种 作用的物质称为补强剂。
3.焦烧:胶料在存放和加工过程中出现的早期硫化现象。
4.工艺正硫化时间:胶料从加热开始,至转矩上升到最大转矩的90%时所需 要的时间。 M90=ML+(MH-ML)×90% 5.理论正硫化时间:交联密度达到最大程度时所需要的时间。 6.硫化返原:如果胶料再继续硫化就会使交联结构产生降解,性能下降,这 种现象就称为硫化返原。
(二)硫化历程图
根据硫化历程分析,可将硫化曲线分成四个阶段 ◆ 焦烧阶段:热硫化开始前的延迟作用时间,反映了加工安全性。该阶段取决 于促进剂的品种和用量。 ◆ 热硫化阶段:硫化反应的交联阶段,逐渐产生网络结构,该阶段斜率的大小 反映了硫化速度的快慢。 ◆ 平坦硫化阶段:交联反应基本完成。硫化平坦期的长短取决于胶料配方。 ◆ 过硫化阶段:相当于硫化反应阶段中网构形成的后期。