高炉喷煤方案及概算
高炉喷煤概论
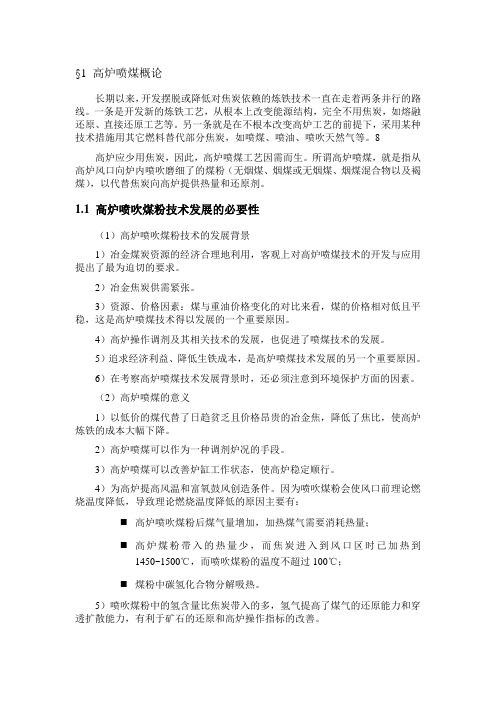
§1 高炉喷煤概论长期以来,开发摆脱或降低对焦炭依赖的炼铁技术一直在走着两条并行的路线。
一条是开发新的炼铁工艺,从根本上改变能源结构,完全不用焦炭,如熔融还原、直接还原工艺等。
另一条就是在不根本改变高炉工艺的前提下,采用某种技术措施用其它燃料替代部分焦炭,如喷煤、喷油、喷吹天然气等。
8高炉应少用焦炭,因此,高炉喷煤工艺因需而生。
所谓高炉喷煤,就是指从高炉风口向炉内喷吹磨细了的煤粉(无烟煤、烟煤或无烟煤、烟煤混合物以及褐煤),以代替焦炭向高炉提供热量和还原剂。
1.1 高炉喷吹煤粉技术发展的必要性(1)高炉喷吹煤粉技术的发展背景1)冶金煤炭资源的经济合理地利用,客观上对高炉喷煤技术的开发与应用提出了最为迫切的要求。
2)冶金焦炭供需紧张。
3)资源、价格因素:煤与重油价格变化的对比来看,煤的价格相对低且平稳,这是高炉喷煤技术得以发展的一个重要原因。
4)高炉操作调剂及其相关技术的发展,也促进了喷煤技术的发展。
5)追求经济利益、降低生铁成本,是高炉喷煤技术发展的另一个重要原因。
6)在考察高炉喷煤技术发展背景时,还必须注意到环境保护方面的因素。
(2)高炉喷煤的意义1)以低价的煤代替了日趋贫乏且价格昂贵的冶金焦,降低了焦比,使高炉炼铁的成本大幅下降。
2)高炉喷煤可以作为一种调剂炉况的手段。
3)高炉喷煤可以改善炉缸工作状态,使高炉稳定顺行。
4)为高炉提高风温和富氧鼓风创造条件。
因为喷吹煤粉会使风口前理论燃烧温度降低,导致理论燃烧温度降低的原因主要有:⏹高炉喷吹煤粉后煤气量增加,加热煤气需要消耗热量;⏹高炉煤粉带入的热量少,而焦炭进入到风口区时已加热到1450~1500℃,而喷吹煤粉的温度不超过100℃;⏹煤粉中碳氢化合物分解吸热。
5)喷吹煤粉中的氢含量比焦炭带入的多,氢气提高了煤气的还原能力和穿透扩散能力,有利于矿石的还原和高炉操作指标的改善。
6)喷吹煤粉代替了部分焦炭,不仅缓解了焦煤的供需紧张状况,也减少了对炼焦设施的投资和建设,降低了炼焦生产对环境的污染。
1080m3高炉喷煤方案

3# 老系统
5# 石 灰
1#
3# 老系 统5# 石灰 Nhomakorabea1#
3# 老系统
5#
2# 备 3
4# 老系统
6# 球团 3
2#
4# 老系统
6# 球团 3
2#
4# 老系统
6#
二、供气系统:
(一)、空气: 1、现状:老系统目前有40 m3空压机一台, 20m3四台,目前空压机开4台20m3时,压 力达不到7.5公斤,波动大,加载时间长, 很紧张;开一台40 m3和3台20 m3空压机 时,工作正常;新系统两台20 m3空压机, 一用一备,有时全开。
五、喷吹管道:
1、使用方案一,喷吹管道采用DN80mm,相当 于两座540m3高炉喷煤。 2、使用方案二,双管道双分配器,一用一备, 喷吹罐引射管采用DN80mm,通过两次最终变 径为DN100mm管道。 3、从老喷煤新气包上出一趟DN80管道,供新 高炉炉前使用。 4、喷煤管道尽量采用6毫米以上的厚皮管,弯 头全部采用耐磨弯头。
4# 高 炉 更衣处 3 5 拉门 6 4 3500 7 B 1 8 9 2 10 车间办公室 3500
4# 高 炉
2# 高 炉
4# 高 炉 更衣处 3 5 拉门 6
更衣处 3 5 拉门 6 4 3500 7 3# 高 炉 9 2 10 3500
控 制
室
控
制
室 4 7
3500
控
制 室
B
B 1 8 9 2 车间办公室 10 车 间办公室 3500
3
5 40 0
2 #高 炉
新 喷 煤 ( 罐 容 20 . 5m ) C B A
3
2 #高 炉
高炉自动喷煤控制方案设计与实现

为 提 高煤 比创 造 条 件 。本 文 以炼 铁 厂 A 区 喷煤
系统为例 ,阐述 了高炉 自动喷煤控制方案 的设
计 与 实现 过程 。
作 者 :李明亮,工程硕士 ,工程师 ,现从 事 自动化 仪表运行 管理工作。
自动 喷 煤对 控 制 的要 求 : ( 1 )可 实 现 喷煤 量 的全 自动 调 节 ,0 . 5 h和 1 h喷 煤 量 偏 差 满 足
装煤 。 ( 4 ) 有 堵 煤 、停 煤 预 警 及 应 急联 锁 保
高炉要求 。 ( 2 )可实现 自动倒罐和 自动装煤 ,
一
个 罐 喷完 后 自动 切 换至 另一 喷 吹 罐 ,不 停 煤 。
( 3 ) 可实 现 各 喷 吹 罐 问 的 自动 平 衡 泄 压 ,一 个
罐 喷完后 ,将罐 内氮气 自动泄自动
应 用效 果 。
关键 词 : 自动化 ;高炉 ;喷煤 ;倒 罐 ;平衡 泄压 ;喷吹 率
D e s i g n a n d R e a l i z a t i o n o f Au t o ma t i c C o a l I n j e c t i o n C o n t r o l
1 前 言
高 炉 喷 煤 是 指从 高 炉 风 口 向炉 内直 接 喷 吹 磨 细 了 的煤粉 ( 无 烟煤 、烟煤 或 混合 煤 粉 ) ,以 代 替 部 分 焦 炭 向高 炉 提 供 热 量 和 还 原 剂 。 高 炉 喷 煤 存 在 手 动 调 节 和 自动 喷 吹两 种 方 式 。手 动 调 节 喷 煤 喷 煤 量 不 均 匀 ,造 成 高 炉 热 制 度 经 常 性 波 动 ,不 利 于 高 炉 炉 况 的 稳 定 及 煤 比 的进 一 步 提 高 ,采 用 自动 喷 煤 技 术 可 使 人 炉 煤 粉 量 更
高炉经济喷煤比计算

关于高炉经济喷煤比的理论计算通过查阅资料得知:经济喷煤比取决于喷煤量水平、高炉煤焦置换比、能量消耗利用程度。
喷煤对高炉工序成本降低的影响可按照公式(1)计算。
1000)(m k P R P X J -⨯=∆ (1) 其中:J ∆---炼铁工序成本降低值,元/t ;X------喷煤量,kg/t ;P k -----焦炭价格,元/t ;R------煤焦置换比;P m ----喷吹煤粉的价格加工序成本,元/t ;经查阅资料得知:在生产条件稳定条件下,煤焦置换比与喷煤比存在线性关系如公式(2)所示。
R=1.025-0.00158X (2) 煤粉配比按照无烟煤55%,烟煤45%标准计算。
所以,可以得出结论:1000)]%45%55()00158..0025.1([m 工烟无m m k P P P X P X J +⨯+⨯--⨯=∆ (3)其中:无m p ---无烟煤价格;烟m p ---烟煤价格;工m p ---煤粉工序成本;公式(3)中:P k ,无m p ,烟m p ,工m p 依据成本表查询实时价格,可以认为是常数,所以公式(3)是高炉工序成本下降值J ∆关于喷煤比X 的二次函数,所以在一定生产条件下,存在一个合适的喷煤比,最大程度的降低高炉的工序成本。
例:依8月成本数据进行计算:(1)480高炉合适的喷煤比:P k = 1865.61元/t 无m p = 1188.25元/t烟m p = 742.87元/t 工m p =10元/t带入公式(3)计算:J ∆=1000)10%4587.742%5525.1188()00158.0025.1(61.1865[+⨯+⨯--⨯X X =0.001X (1912.25-2.95X-997.83)=-2.95⨯⨯-310X 2+914.42⨯⨯-310X依据抛物线的性质得知:当X=95.2242.914⨯-=154.98kg/t 时,高炉成本下降值最大 480max J ∆=70.86元/t(2)1080高炉合适的喷煤比:P k =1920.28元/t 无m p = 1188.25元/t烟m p = 742.87元/t 工m p =10元/t带入公式(3)计算:J ∆=1000)10%4587.742%5525.1188()00158.0025.1(28.1920[+⨯+⨯--⨯X X =0.001X (1912.25-2.95X-997.83)=-3.03⨯⨯-310X 2+970.46⨯⨯-310X依据抛物线的性质得知:当X=03.3246.970⨯-=160.14kg/t 时,高炉成本下降值最大 1080max J ∆=77.71元/t所以,以8月成本计算,480高炉合适的喷煤比为154.98kg/t,1080高炉合适的喷煤比为160.14kg/t。
炼铁厂喷煤试喷方案

江苏长强钢铁有限公司炼铁厂喷煤试喷方案二00六年五月打印:编制:审核:公司审核:审批:炼铁厂喷煤试喷方案根据喷煤工程的进展情况,经研究决定于5月24日17:18向1#高炉试喷煤粉,据此制定本方案。
为加强领导,确保试喷安全、有序地进行,成立喷煤领导小组,1、领导小组:组长:李小东副组长:郑棉斌、彭明成员:张贵滨、梁尉国、陈世民、李义光、韩新、张建军、石阿明技术保障:一冶长强项目部:刘平、彭云国天目、电装、机装设备厂家:南京三埃、沈重双马、合肥水泥设计院、启东冶金机械2、具体分工:现场总指挥:李小东工艺负责人:郑棉斌设备负责人:彭明内部间协调:张贵滨喷煤负责人:梁尉国1#高炉炉内:陈世民插枪负责人:李义光机械负责人:韩新安全负责人:石阿明电气负责人:张建军一、前提条件:1、各系统已空负荷联动试车完毕,试车中发现问题于5月23日8:00前解决处理完毕。
2、烟气炉烘炉工作完成,具备供气能力。
3、操作规程、安全规程所要求的其它条件均已具备。
4、参加试车的各岗位操作人员已经过岗前培训,并通过安全技术考试。
5、通讯、安全(防爆、消防、煤气防护、照明)等设施齐全、可靠。
(3、4、5三条由安环部22日下班前检查落实完毕)6、生产所需的一切物资5月23日上午必须备好,做到随时可用,如洗精无烟煤、煤气、压缩空气、蒸汽、水、氮气等等。
同时要求:氮气、压缩空气压力0.5~0.7MPa,循环水压力不低于0.3 MPa。
7、检测设备安全,必要的检测工作已做好。
试车前质管部必须对原煤成分(挥发分、灰分、碳、硫、水分)、可磨性进行测定并报出分析结果,由质管部负责,22日前完成。
8、记录报表,交接班记录本等已送至各岗位。
9、必要的工器具,备品备件,润滑油脂均配备齐全。
二、试车步骤:1、烟气炉送气准备5月21日17:18烟气炉开始按“烟气炉烘炉曲线”进行烘炉(见附录一),22日17:00引煤气继续烘炉,在烘炉完毕后,具备送气的待机状态。
高炉喷吹煤给料技术方案
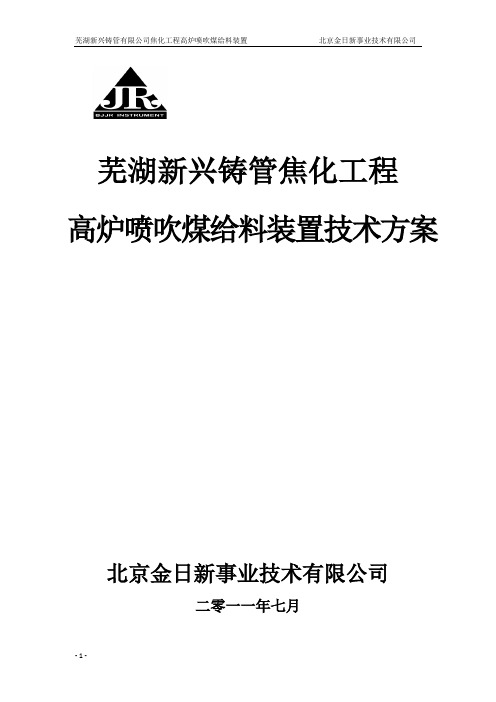
芜湖新兴铸管焦化工程高炉喷吹煤给料装置技术方案北京金日新事业技术有限公司二零一一年七月1.概述高炉喷吹煤系统的任务是将卸车后的高炉喷吹用煤进行贮存,并根据制粉系统工作制度及系统处理能力的要求,将储存在贮煤槽内的煤料连续、稳定、均匀的给料并输送至制粉系统,加工成满足高炉喷吹生产要求的煤粉。
中冶焦耐(大连)工程技术有限公司提供的贮配煤室安装图为:贮配煤室横剖面图1电气室储配煤室0.150平面布置:图2(共计15个储煤槽,其中1-3号槽用于高炉喷吹煤给料系统)- 4 -贮配煤室纵剖面图3 - 5 -贮配煤室中1#、2#、3#槽储存的是高炉喷吹煤,其储量为~8000t×3=~24000t。
在储配煤槽的设计中,每个槽共设2×2=4个槽嘴,3个槽共12个槽嘴,每个槽嘴设电液动平板闸门(业主供货)及直拉式称量带式输送机。
储槽内的煤料通过电液动平板闸门由直拉式称量带式输送机按规定的给料量拖出,经带式输送机运送至制粉系统。
2.高炉喷吹煤给料装置方案概述虽然高炉喷吹煤储槽与焦化储配煤槽同处建设,并利用焦化工程的卸车、输送系统将高炉喷吹煤运送至储槽储存,但其给料装置及控制系统是一个独立的系统。
因此我公司结合本项目高炉喷吹煤储槽的建设特点,提出给料装置及控制系统的技术方案如下:(1)储煤槽采用德国原装申克电子皮带秤及直拉式拖料皮带机自动给料,整个系统的操作均在焦化工程自动配煤控制室内进行。
为了便于现场管理,我们在高炉制粉系统的中控室设置一台上位机作为监控,喷吹煤给料装置的柜体设备均安装在储煤槽附近设置的焦化工程自动配煤控制室内。
(2)在焦化工程建设的自动配煤控制室内安装PLC柜、变频柜、供电系统和自动配煤装置集中供电。
(3)焦化工程自动配煤控制室详见储配煤室纵剖面图。
(4)储煤槽设置的高能破拱助流器的开、关的控制程序由喷吹煤给料装置控制系统完成(业主只需将空气炮启动/停止的信号引入到配煤控制室再增加一些开关量控制模块即可实现空气炮系统的集中控制)。
D12喷煤工艺设计与计算
・ !"") ・
第三章
煤粉制备
第三章
煤粉制备
第一节
原煤和煤粉要求
一、 原煤
粒度 水分 三块 一般不大于 !"##, 小型磨煤机要求不大于 $!##, 最小为 !##; 一般应小于 %"& ; 即木块、 铁块和石块, 要求全部去除, 特别是中速磨煤机更应去除干净。
二、 对煤粉的要求
粒度 一般要求通过 $"" 目筛网的煤粉占 ’"& ( )"& , 烟煤粉粒度可稍大一些。目
・ &%!$ ・
第十二篇
喷煤工艺设计与计算
第二节
喷煤规模和设备能力的确定
一、 高炉喷煤量的确定
高炉喷煤量定多少, 应根据高炉的原燃料条件、 质量、 各项技术经济指标以及所喷煤 的煤质、 煤种和供煤量进行考虑和计算。理论计算不仅比较繁杂, 而且计算结果往往与 生产实际情况差距较大, 故可结合生产实践经验进行设计。在确定高炉喷煤装置的能力 时, 一般采用如下公式计算: ・! $%& ! ! " " #・ ! 式中 — —小时喷煤量, !!— ) * !; — —高炉有效容积, " #— +, ; — —高炉有效容积利用系数, ; )( * +,・ -) !— — —吨铁喷煤量, !— )$)。 吨铁喷煤量 ! , 无富氧时, 一般都是取 . / ’ 0 . / ’%) * ), 而在确定高炉喷煤装置的最大 喷吹能力时, 若同时考虑富氧大喷煤时 ! 值则应按 . / %1 0 . / ,)$ ! 值应按 . / ’1) * ) 选取, ) 选取。 (’% ( ’ ( ’)
二、 多种煤贮运
高炉喷煤技术方案 2
1 概述上世纪60年代初,我国高炉喷煤试验获得成功后,高炉喷煤技术在我国逐渐推广应用。
进入90年代,特别是经过“八五”“氧煤强化炼铁”项目攻关后,我国高炉喷煤技术发展跃上了一个新的台阶,已经赶上了世界先进水平,吨铁喷煤量和覆盖率大幅度增加。
2002年全国54家重点(原重点和地方骨干)联合钢铁企业吨铁喷煤量已达到125kg/t,企业喷煤覆盖率达到85%以上。
高炉喷吹煤粉及提高喷煤量已经成为现代高炉炼铁技术的发展方向,同时也是降低生产成本最直接和最有效的手段之一。
当前我国炼铁生产规模正在迅速扩大,生产效率也在不断提高,对焦炭的需求量日益增加,导致冶金焦价格高,资源紧缺,高炉大量喷煤是解决这一矛盾的最佳措施。
贵公司现有两座高炉450立方米的高炉。
年产生铁约126万吨。
如两座高炉采用全焦冶炼,每年需要焦炭约70万吨。
高炉生产成本较高,采用高炉喷煤技术,不但在很大程度上可以缓解焦炭的供需矛盾,减轻焦炭质量波动对高炉操作的影响,而且也会进一步降低炼铁生产成本,同时也为高炉操作增加了下部调节手段,有利于改善高炉生产的技术经济指标。
鉴于上述情况,以及着眼于贵公司长期的发展战略目标,拟建设高炉喷煤工程,工程建设指标为喷煤工艺及设备能力正常XX kg/t,最大达到XXX kg/t喷煤比能力,喷吹煤种为无烟煤浓相输送设计。
置换比按X计算,可以代替约X万吨焦炭。
2.喷煤设计工艺要求2.1 喷煤量根据贵公司对喷煤工程的要求,和参照国内外喷煤技术的发展…。
2.2 设计条件喷吹用煤…。
2.3工艺流程设计采用…方案,以节省投资和占地面积。
…本喷煤工程包括…高炉。
目前高炉喷煤系统有关的工艺参数如表1所示。
表1 喷吹系统有关的基本参数2.4 喷吹站喷吹站采用并罐浓相喷吹工艺。
喷吹站的操作全部自动联锁,整个系统各设备既可自动也可手动。
2.5 原煤理化指标2.6 安全措施(1)喷吹罐设防爆孔及温度监控;(2)喷吹罐和煤管道采取防静电措施。
高炉喷煤方案及概算
1、概述1.1现状高炉喷煤是冶金企业节焦降耗行之有效的重要途径。
我厂目前有750m3高炉两座,120m3高炉四座,均已有喷煤设施。
750m3高炉目前平均喷煤量160㎏/t铁,120m3高炉平均喷煤量70㎏/t铁。
喷煤车间现有ZGM95型中速磨煤机一台,制粉铭牌出力为36t/h,刚好满足上述高炉喷煤。
2#750m3高炉易地大修投产后,一台ZGM95型中速磨煤机的生产能力已不能满足所有高炉的喷煤要求,须新上制粉设备。
喷吹系统也不能满足新高炉的喷煤需要。
同时,煤场实际贮煤量只有3640t,当喷吹量都为最大时,煤场贮煤量只能满足2.8 d生产,若都按目前正常喷吹量,则煤场贮煤量能满足3.5 d生产。
显然煤场太小,需要扩建。
烟气炉的能力也需进一步加大。
1.2设计依据莱芜钢铁股份有限公司规划部[2001]96号文《关于下达2#750m3高炉大修设计任务计划的通知》。
1.3设计原则(1)优化设计,做到先进、适用、经济、顺行、高效。
(2)设计中做到总体考虑,合理布局,兼顾将来的进一步发展;尽量不影响现有设施的生产;尽量减少占地、拆迁和工程量。
(3)按照喷吹烟煤设计,制粉系统设气氛保护。
(4)制粉系统采用短流程,用高浓度布袋收粉器作为一级收粉设备,不设旋风收粉器。
为减少危险点,布袋与煤粉仓之间不设螺旋输送机。
(5)喷吹采用浓相输送技术。
(6)考虑检修、备品备件方便,制粉采用ZGM95型中速磨煤机。
(6)严格执行国家有关环保、安全、工业卫生和消防等规定。
1.4设计范围本工程设计范围包括:原煤场扩建及贮运,烟气系统,制粉系统,喷吹系统。
1.5主要经济技术指标1.6设计特点及采用的新技术⑴按照喷吹烟煤设计,系统设惰性气体保护措施。
⑵制粉采用以中速磨煤机为核心的短流程工艺,用一级高浓度袋式煤粉收集器收粉。
⑶节能,每吨煤粉耗电28度。
⑷煤场的煤仓及圆盘给料机可以适应喷吹烟煤、无烟煤、混合煤各煤种的要求。
⑸喷吹罐采用单罐并列布置。
南钢炼铁厂新1#高炉喷煤技改初步方案
南钢炼铁厂新1#高炉喷煤系统收尘器技改初步方案编制单位:湖南益天环保科技有限公司单位地址:湘乡市红仑经济开发区电话传真: 0731—编制时间:二O一四年七月目录一、现状情况及原因分析二、原除尘器的基本技术参数三、设计思路四、主要大修改造内容五、改造后设备基本技术参数六、施工特点七、技术特点八、设备质量标准九、投资概算十、预计工期十一、效益分析十二、项目联系人、电话附:设备布置图一、现状情况及原因分析:2014年7月,我公司技术部彭崇清、销售部刘文辉应邀前往方大特钢炼铁厂,对新1#高炉喷煤原除尘器现场进行了深入细致的了解,与炼铁厂能源环保部、制粉车间就除尘器存在的问题及改进意见进行了多方位的技术交流。
根据原系统基本情况及工程要求,综合我公司技术人员在方大特钢炼铁厂新1#高炉喷煤现场所掌握的情况,制定本工程技改方案。
1、新1#高炉喷煤原除尘器已使用多年,一直没有进行过大、中修,现收尘器运行情况差。
2、由于原设备选型偏小,过滤风速偏高,制粉系统受到一定影响。
3、原设备运行阻力大,约为:2500Pa—3000Pa,排放浓度超标严重,达到100mg/m3以上,不能满足2015年排放标准要求。
4、产品严重浪费,产量远低于设计值。
二、原除尘器的基本技术参数:原收尘器型号:LLMC168-4(M)过滤面积:1820m2,分4个室处理风量:90000m3/h正常状态过滤风速:0.82 m/min清灰状态过滤风速:1.1m/min设备运行阻力:2500—3000Pa排放浓度:≥100 mg/m3三、设计思路:除尘器既要适应系统工艺,又要满足系统使用要求,必须做到以下几点:①、能使气流重新分布,袋荷均匀;②、气流不冲刷滤袋;③、不得有积灰区,不得有切割边与滤袋碰撞;④、不产生二次吸附现象;⑤、有足够的清灰强度;⑥、设置泄爆安全阀门。
所以从减少改造、维护工作量、节约改造费用、运行可靠等多方面考虑,我公司对此次改造的总体原则是:1)对原收尘器扩容,根据现有场地,新增一台收尘器;2)原收尘器分4个室,每室过滤面积455 m2,新增收尘器单室过滤面积基本相当,确保各室负荷均匀;3)扩容后收尘器清灰状态下过滤风速控制在0.7m/min左右;4)电气控制系统扩展5) 除尘器排放颗粒物符合GB28662-2012标准表中的≤25mg/m3;四、主要大修改造内容:4.1新增一台过滤面积为850平方米的成套袋式除尘器。
- 1、下载文档前请自行甄别文档内容的完整性,平台不提供额外的编辑、内容补充、找答案等附加服务。
- 2、"仅部分预览"的文档,不可在线预览部分如存在完整性等问题,可反馈申请退款(可完整预览的文档不适用该条件!)。
- 3、如文档侵犯您的权益,请联系客服反馈,我们会尽快为您处理(人工客服工作时间:9:00-18:30)。
1、概述1.1现状高炉喷煤是冶金企业节焦降耗行之有效的重要途径。
我厂目前有750m3高炉两座,120m3高炉四座,均已有喷煤设施。
750m3高炉目前平均喷煤量160㎏/t铁,120m3高炉平均喷煤量70㎏/t铁。
喷煤车间现有ZGM95型中速磨煤机一台,制粉铭牌出力为36t/h,刚好满足上述高炉喷煤。
2#750m3高炉易地大修投产后,一台ZGM95型中速磨煤机的生产能力已不能满足所有高炉的喷煤要求,须新上制粉设备。
喷吹系统也不能满足新高炉的喷煤需要。
同时,煤场实际贮煤量只有3640t,当喷吹量都为最大时,煤场贮煤量只能满足2.8 d生产,若都按目前正常喷吹量,则煤场贮煤量能满足3.5 d生产。
显然煤场太小,需要扩建。
烟气炉的能力也需进一步加大。
1.2设计依据莱芜钢铁股份有限公司规划部[2001]96号文《关于下达2#750m3高炉大修设计任务计划的通知》。
1.3设计原则(1)优化设计,做到先进、适用、经济、顺行、高效。
(2)设计中做到总体考虑,合理布局,兼顾将来的进一步发展;尽量不影响现有设施的生产;尽量减少占地、拆迁和工程量。
(3)按照喷吹烟煤设计,制粉系统设气氛保护。
(4)制粉系统采用短流程,用高浓度布袋收粉器作为一级收粉设备,不设旋风收粉器。
为减少危险点,布袋与煤粉仓之间不设螺旋输送机。
(5)喷吹采用浓相输送技术。
(6)考虑检修、备品备件方便,制粉采用ZGM95型中速磨煤机。
(6)严格执行国家有关环保、安全、工业卫生和消防等规定。
1.4设计范围本工程设计范围包括:原煤场扩建及贮运,烟气系统,制粉系统,喷吹系统。
1.5主要经济技术指标1.6设计特点及采用的新技术⑴按照喷吹烟煤设计,系统设惰性气体保护措施。
⑵制粉采用以中速磨煤机为核心的短流程工艺,用一级高浓度袋式煤粉收集器收粉。
⑶节能,每吨煤粉耗电28度。
⑷煤场的煤仓及圆盘给料机可以适应喷吹烟煤、无烟煤、混合煤各煤种的要求。
⑸喷吹罐采用单罐并列布置。
⑹喷吹系统采用喷吹罐下口大流化床流化、总管加分配器形式,浓相输送,既节省压缩空气,又减少管道磨损,还避免喷吹脉动现象。
⑺分配器采用1分18的盘式分配器,阻损小,分配均匀,体积小,效率高。
⑻噪音底,中速磨噪音低于85db。
⑼煤粉仓与喷吹罐中间设上、下“U”型球阀,密封性能好,下煤快,寿命长。
1.7投资估算本工程投资估算为1467.31万元。
2、工艺2.1工艺流程见附图[FA]L62T-9-1。
2.2设计规模为满足所有高炉的喷煤要求,本工程投产后,1#、2#750m3高炉喷煤量为150~200㎏/t铁,新2#750m3高炉喷煤量为180~220㎏/t铁,4×120m3高炉喷煤量为80~100㎏/t铁。
2.3车间组成及工艺综述本工程由原煤场扩建及贮运系统,烟气系统,制粉系统,喷吹系统组成。
2.3.1 原煤场扩建及贮运系统原煤贮运系统原设计为一座620m3高炉用,烟煤和无烟煤分开储存,总有效堆存面积1280m2,总贮煤量3200吨。
2×750m3高炉喷煤工程只将一部分露天煤场加上防雨棚,面积未加大。
由于煤场太小,本设计只考虑喷吹烟煤,可贮煤3640吨。
各高炉喷煤量见下表1。
表1各高炉喷煤量每小时最大量:31.25+17.19+6=54.44 t/h每天最大量:750+412.5+144=1306.5 t/d当喷吹量都为最大时,煤场贮煤量只能满足:3640÷1306.5=2.8 d若都按目前正常喷吹量,2×750m3高炉喷煤160kg/t铁,新2#750m3高炉喷煤180kg/t铁,4×120m3高炉喷煤80kg/t铁,那么每小时喷煤量:43.8 t/h,每天最大量:1052.7 t/d,则煤场贮煤量能满足:3640÷1052.7=3.5 d上述计算表明,煤场贮煤量太小,将给生产带来极大困难。
所以必须扩建煤场。
为了增加煤场面积,本设计考虑在动力煤场的南面扩建一煤场,有效面积1100m2,贮煤量3000吨,总的贮煤量6640吨,各高炉喷吹量都为最大时,可满足5天生产;喷吹量都为目前正常量时,可满足7天生产。
扩建煤场设一5t行车抓斗,设两座26m3料仓,料仓下各设一ф1800圆盘给料机,下设6#皮带机通廊,抓斗将原煤抓进料仓,通过给料圆盘落到6#皮带机上,经转运站、7#皮带机、8#皮带机转运至3#皮带机上,再经4#皮带机、5#皮带机落进原煤仓。
3#皮带机需加长,4#皮带机头部需改造。
若喷混合煤,本煤场可通过圆盘配料实现。
2.3.2烟气系统两座ZGM95中速磨制粉需要的250℃的最大入磨一次风量为91200Nm3/h,现有高温风机抽风能力为120℃的热风炉废气69500 Nm3/h,而现有烟气炉的位置影响本设计的工艺布置,并且操作控制落后,危险因素多,效率低,只是针对一座中速磨供废气,不能向两座中速磨同时供废气。
因此需要拆除另建。
在原球磨机烟气炉位置建一新型烟气炉,高炉煤气消耗量为10000 Nm3/h,产生900℃高温废气17300 Nm3/h,当两座中速磨的制粉量都为最大时,还差4400 Nm3/h烟气量。
在管道上采用兑空气的办法,兑4400 Nm3/h 冷空气,入磨处烟气含氧量可控制在5.5%以下,是可以安全喷吹烟煤的。
新烟气炉设助燃风机一台,煤气、空气量可根据需要调节,严格控制气氛含氧量。
烟气炉一头设混风室,高温废气、热风炉废气在此汇合,制粉量大时稍兑一些冷空气,形成250℃的含氧量在5.5%以下的煤粉干燥气。
烟气炉另一头设值班室。
2.3.3制粉系统在原主厂房的东面扩建一12m×12m跨,内设原煤仓、给煤机及中速磨煤机。
4#皮带机头部加高后,下接5#皮带机,并设双侧犁式卸料器向新原煤仓进行三点给料。
原ZGM95型中速磨的原煤仓靠4#皮带机的犁式卸料器两点给料。
新原煤仓容积为160m3,可装煤110t,满足中速磨3~4个小时连续生产。
原煤仓采用电子秤称重进行上料控制。
给煤机采用与中速磨配套皮带秤给煤机,该机特点是控制精度高,寿命长。
考虑设备管理统一,备品备件方便等,设一台ZGM95型中速磨煤机制粉。
该设备比现有ZGM95型中速磨更先进,具有国际先进水平,设计铭牌制粉能力为36t/h,负压操作。
入磨一次风量为45600Nm3/h,本身带有粗粉分离器,该机具有出力大、研磨件使用寿命长、磨煤电耗低、设备可靠及运行平稳、噪音低等特点,目前在电力行业、冶金行业得到广泛应用。
收粉采用高浓度煤粉袋式收集器进行一级收粉的短流程工艺,取消旋风。
该设备特点是粉尘进口浓度高,达500~1000 g/Nm3,出口含尘浓度底,<80mg/Nm3,采用原装进口电磁阀进行脉动,电磁阀及布袋寿命长,效率高。
布袋及其前面设备及管道设充氮设施,当气氛含氧量高时,及时向气氛中充氮气,使气氛含氧量降到规定数值。
在中速磨煤机出口管道设木块分离器,清除原煤中的木块等物。
布袋收粉器灰斗下方设煤粉振动筛,筛除混在煤粉中的木屑等杂质。
振动筛下方设一螺旋输送机,当原中速磨制粉量不足时向原系统提供煤粉。
2.3.4喷吹系统在现主厂房西侧设两个煤粉仓,每仓有效容积70m3,可装煤粉45t。
煤粉仓下锥体设氮气流化,一方面使气氛惰化,保证安全,另一方面下料快,不堵料。
煤粉仓采用电子秤称重控制仓内煤量。
煤粉仓下设上、下“U”型球阀,该阀具有下料快,寿命长等优点,在国内其他厂家的使用得到证实,比目前广为流行的球面偏置钟阀、代钟阀球阀及目前我厂使用的老式钟阀更为先进和实用。
两阀中间设软连接。
喷吹罐采用单罐并列式,每罐容积为23m3,可装煤粉10t以上,每罐可喷吹1小时以上。
罐体设排压装置,设计压力为1.3MPa。
喷吹罐采用电子秤称重控制倒罐时间。
喷吹系统采用总管加分配器的流化上出料浓相输送工艺流程:在喷吹罐下煤口处直接连接流化罐,流化罐为流化床上出料形式。
其工作原理是流化罐下部设流化气室,气体经流化板均匀进入罐内使煤粉流态化,在流化区域与输送罐间压差作用下将煤粉输送到罐外。
流化罐出料口安装煤粉切断阀,在倒罐过程中使用,阀门连接补气调节器,依靠调节煤粉管道中气阻与固气比,改变输送管内的煤粉状态,以达到调节煤粉量的目的和远距离输送的要求。
煤粉分配器采用盘式分配器,1分18,该分配器特点是煤粉分配均匀,精度高,体积小,耐磨性好,使用寿命长。
喷煤主控室设在原球磨机厂房内,球磨机及其附属设施拆除。
2.3.5主要设备选型⑴ZGM95型中速磨煤机1台,铭牌出力36t/h,入磨一次风量35000~45600Nm3/h,通风阻力5.91kPa,主电机功率450kW,密封风量4930 Nm3/h,磨煤机磨煤电耗率5~10kW·h/t,磨辊寿命>15000h,噪音<85db,设备重量110t。
带式给煤机为DPG50型,随中速磨成套,具有控制精度高,寿命长的特点。
⑵高浓度煤粉收集器1台,CD-Ⅲ-1400型,处理风量75000Nm3/h,过滤面积1400m2,运行温度<120℃,入口煤粉浓度500~1000g/Nm3,出口含尘浓度<80mg/Nm3,设备耐压-15000Pa,原装进口电磁阀脉动,滤料采用必达福防静电针刺毡,设备重量78.5t。
⑶烟气炉1座,包括燃烧室、混风室,可燃高炉煤气10000Nm3/h,生成900℃废气量为17300 Nm3/h,进口煤气及助燃空气自动调节,可控制气氛含氧量,具有体积小、效率高的特点。
⑷煤粉风机1台,M9-26No.14D型,风量75000 Nm3/h,负压14000Pa,设变频调速器。
⑸ф2200喷吹罐2台,设备耐压1.3MPa,容积23m3,可装煤粉13t左右,满足高炉连续喷吹1小时以上。
罐体设排压装置,在喷吹罐下煤口处直接连接流化罐,流化罐为流化床上出料形式。
⑹DN500上、下“U”型球阀4台,该阀具有下料快,寿命长等优点。
⑺5t行车抓斗1台,跨距31.5m,H=7m。
⑻ф1800圆盘给料机2台,给料能力约100t/h。
⑼煤粉振动筛2台,TZSM-70-200型。
⑽B=800皮带机5条,运输量216t/h。
2.3.6主要技术经济指标3、电气3.1设计依据:本初步设计是根据工艺专业所提条件并结合喷煤现状编写的。
3.2设计范围:新2#750m3高炉喷煤工程的供配电、电气传动控制、照明、防雷和接地。
3.3供配电:3.3.1负荷计算:高炉喷煤系统中用电设备多属一、二类负荷,因此应有两路独立电源作为正常生产用的工作电源。
3.3.2系统现状及供电措施:①6Kv系统:喷煤车间现有6kV配电室一座,两路电源进线均引自老高炉高配室,进线电缆为YJV-6KV,3X185,进线断路器为630A。
现在仅投入一路电源,母联合闸,实际运行电流约为180A。