合成氨各工序工艺详细流程
合成氨生产工艺介绍

1、合成氨生产工艺介绍1)造气工段造气实质上是碳与氧气和蒸汽的反应,主要过程为吹风和制气。
具体分为吹风、上吹、下吹、二次上吹和空气吹净五个阶段。
原料煤间歇送入固定层煤气发生炉内,先鼓入空气,提高炉温,然后加入水蒸气与加氮空气进行制气。
所制的半水煤气进入洗涤塔进行除尘降温,最后送入半水煤气气柜。
造气工艺流程示意图2)脱硫工段煤中的硫在造气过程中大多以H2S的形式进入气相,它不仅会腐蚀工艺管道和设备,而且会使变换催化剂和合成催化剂中毒,因此脱硫工段的主要目的就是利用DDS脱硫剂脱出气体中的硫。
气柜中的半水煤气经过静电除焦、罗茨风机增压冷却降温后进入半水煤气脱硫塔,脱除硫化氢后经过二次除焦、清洗降温送往压缩机一段入口。
脱硫液再生后循环使用。
脱硫工艺流程图3)变换工段变换工段的主要任务是将半水煤气中的CO在催化剂的作用下与水蒸气发生放热反应,生成CO2和H2。
河南中科化工有限责任公司采用的是中变串低变工艺流程。
经过两段压缩后的半水煤气进入饱和塔升温增湿,并补充蒸汽后,经水分离器、预腐蚀器、热交换器升温后进入中变炉回收热量并降温后,进入低变炉,反应后的工艺气体经回收热量和冷却降温后作为变换气送往压缩机三段入口。
变换工艺流程图4)变换气脱硫与脱碳经变换后,气体中的有机硫转化为H2S,需要进行二次脱硫,使气体中的硫含量在25mg/m3。
脱碳的主要任务是将变换气中的CO2脱除,对气体进行净化,河南中科化工有限责任公司采用变压吸附脱碳工艺。
来自变换工段压力约为1.3MPa左右的变换气,进入水分离器,分离出来的水排到地沟。
变换气进入吸附塔进行吸附,吸附后送往精脱硫工段。
被吸附剂吸附的杂质和少量氢氮气在减压和抽真空的状态下,将从吸附塔下端释放出来,这部分气体称为解析气,解析气分两步减压脱附,其中压力较高的部分在顺放阶段经管道进入气柜回收,低于常压的解吸气经阻火器排入大气。
变换与脱硫工艺流程图5)碳化工段5.1、气体流程来自变换工段的变换气,依次由塔底进入碳化主塔、碳化付塔,变换气中的二氧化碳分别在主塔和付塔内与碳化液和浓氨水进行反应而被吸收。
合成氨生产工艺流程
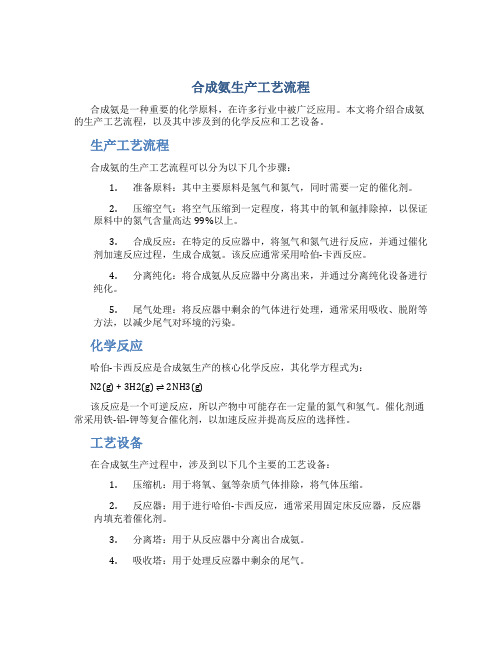
合成氨生产工艺流程合成氨是一种重要的化学原料,在许多行业中被广泛应用。
本文将介绍合成氨的生产工艺流程,以及其中涉及到的化学反应和工艺设备。
生产工艺流程合成氨的生产工艺流程可以分为以下几个步骤:1.准备原料:其中主要原料是氢气和氮气,同时需要一定的催化剂。
2.压缩空气:将空气压缩到一定程度,将其中的氧和氩排除掉,以保证原料中的氮气含量高达99%以上。
3.合成反应:在特定的反应器中,将氢气和氮气进行反应,并通过催化剂加速反应过程,生成合成氨。
该反应通常采用哈伯-卡西反应。
4.分离纯化:将合成氨从反应器中分离出来,并通过分离纯化设备进行纯化。
5.尾气处理:将反应器中剩余的气体进行处理,通常采用吸收、脱附等方法,以减少尾气对环境的污染。
化学反应哈伯-卡西反应是合成氨生产的核心化学反应,其化学方程式为:N2(g) + 3H2(g) ⇌ 2NH3(g)该反应是一个可逆反应,所以产物中可能存在一定量的氮气和氢气。
催化剂通常采用铁-铝-钾等复合催化剂,以加速反应并提高反应的选择性。
工艺设备在合成氨生产过程中,涉及到以下几个主要的工艺设备:1.压缩机:用于将氧、氩等杂质气体排除,将气体压缩。
2.反应器:用于进行哈伯-卡西反应,通常采用固定床反应器,反应器内填充着催化剂。
3.分离塔:用于从反应器中分离出合成氨。
4.吸收塔:用于处理反应器中剩余的尾气。
合成氨是一种十分重要的化学原料,其生产工艺流程麻烦且多种化学反应涉及其中,因此需要一系列的工艺设备来完成整个生产过程。
哈伯-卡西反应是该生产过程的核心反应,通过复合催化剂加速反应过程并提高反应的选择性。
通过合理的工艺流程设计和设备选型,能够实现高效、稳定的合成氨生产。
合成氨的工艺流程
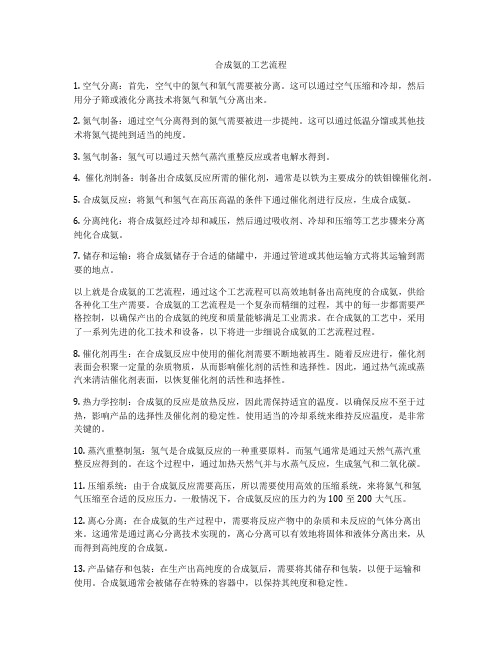
合成氨的工艺流程1. 空气分离:首先,空气中的氮气和氧气需要被分离。
这可以通过空气压缩和冷却,然后用分子筛或液化分离技术将氮气和氧气分离出来。
2. 氮气制备:通过空气分离得到的氮气需要被进一步提纯。
这可以通过低温分馏或其他技术将氮气提纯到适当的纯度。
3. 氢气制备:氢气可以通过天然气蒸汽重整反应或者电解水得到。
4. 催化剂制备:制备出合成氨反应所需的催化剂,通常是以铁为主要成分的铁钼镍催化剂。
5. 合成氨反应:将氮气和氢气在高压高温的条件下通过催化剂进行反应,生成合成氨。
6. 分离纯化:将合成氨经过冷却和减压,然后通过吸收剂、冷却和压缩等工艺步骤来分离纯化合成氨。
7. 储存和运输:将合成氨储存于合适的储罐中,并通过管道或其他运输方式将其运输到需要的地点。
以上就是合成氨的工艺流程,通过这个工艺流程可以高效地制备出高纯度的合成氨,供给各种化工生产需要。
合成氨的工艺流程是一个复杂而精细的过程,其中的每一步都需要严格控制,以确保产出的合成氨的纯度和质量能够满足工业需求。
在合成氨的工艺中,采用了一系列先进的化工技术和设备,以下将进一步细说合成氨的工艺流程过程。
8. 催化剂再生:在合成氨反应中使用的催化剂需要不断地被再生。
随着反应进行,催化剂表面会积聚一定量的杂质物质,从而影响催化剂的活性和选择性。
因此,通过热气流或蒸汽来清洁催化剂表面,以恢复催化剂的活性和选择性。
9. 热力学控制:合成氨的反应是放热反应,因此需保持适宜的温度。
以确保反应不至于过热,影响产品的选择性及催化剂的稳定性。
使用适当的冷却系统来维持反应温度,是非常关键的。
10. 蒸汽重整制氢:氢气是合成氨反应的一种重要原料。
而氢气通常是通过天然气蒸汽重整反应得到的。
在这个过程中,通过加热天然气并与水蒸气反应,生成氢气和二氧化碳。
11. 压缩系统:由于合成氨反应需要高压,所以需要使用高效的压缩系统,来将氮气和氢气压缩至合适的反应压力。
一般情况下,合成氨反应的压力约为100至200大气压。
合成氨的工艺流程
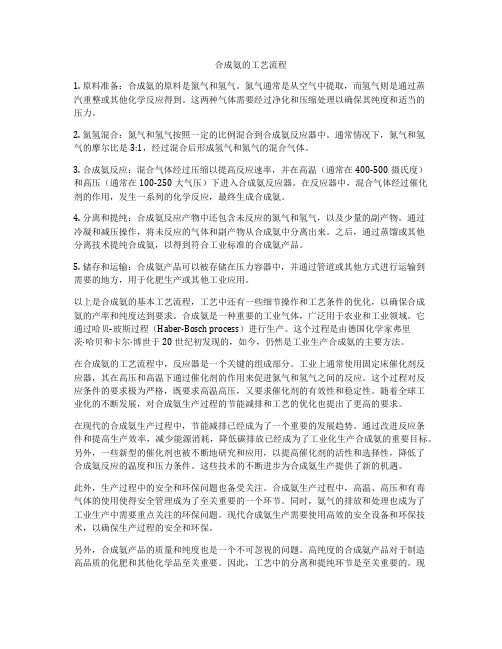
合成氨的工艺流程1. 原料准备:合成氨的原料是氮气和氢气。
氮气通常是从空气中提取,而氢气则是通过蒸汽重整或其他化学反应得到。
这两种气体需要经过净化和压缩处理以确保其纯度和适当的压力。
2. 氮氢混合:氮气和氢气按照一定的比例混合到合成氨反应器中。
通常情况下,氮气和氢气的摩尔比是3:1,经过混合后形成氢气和氮气的混合气体。
3. 合成氨反应:混合气体经过压缩以提高反应速率,并在高温(通常在400-500摄氏度)和高压(通常在100-250大气压)下进入合成氨反应器。
在反应器中,混合气体经过催化剂的作用,发生一系列的化学反应,最终生成合成氨。
4. 分离和提纯:合成氨反应产物中还包含未反应的氮气和氢气,以及少量的副产物。
通过冷凝和减压操作,将未反应的气体和副产物从合成氨中分离出来。
之后,通过蒸馏或其他分离技术提纯合成氨,以得到符合工业标准的合成氨产品。
5. 储存和运输:合成氨产品可以被存储在压力容器中,并通过管道或其他方式进行运输到需要的地方,用于化肥生产或其他工业应用。
以上是合成氨的基本工艺流程,工艺中还有一些细节操作和工艺条件的优化,以确保合成氨的产率和纯度达到要求。
合成氨是一种重要的工业气体,广泛用于农业和工业领域。
它通过哈贝-玻斯过程(Haber-Bosch process)进行生产。
这个过程是由德国化学家弗里茨·哈贝和卡尔·博世于20世纪初发现的,如今,仍然是工业生产合成氨的主要方法。
在合成氨的工艺流程中,反应器是一个关键的组成部分。
工业上通常使用固定床催化剂反应器,其在高压和高温下通过催化剂的作用来促进氮气和氢气之间的反应。
这个过程对反应条件的要求极为严格,既要求高温高压,又要求催化剂的有效性和稳定性。
随着全球工业化的不断发展,对合成氨生产过程的节能减排和工艺的优化也提出了更高的要求。
在现代的合成氨生产过程中,节能减排已经成为了一个重要的发展趋势。
通过改进反应条件和提高生产效率,减少能源消耗,降低碳排放已经成为了工业化生产合成氨的重要目标。
合成氨各工序工艺详细流程

合成氨各工序工艺详细流程合成氨是一种重要的化工原料,广泛用于合成各类农药、肥料、化学品等。
下面将详细介绍合成氨的工序和流程。
合成氨的工艺主要分为三个步骤:气体净化、气体压缩和反应制氨。
1.气体净化:合成氨的原料气体主要有空气和甲烷。
在进入反应装置之前,需要进行气体净化处理。
空气首先经过过滤装置去除微小杂质、灰尘和固体颗粒物。
然后通过制冷装置降低气体温度,使其中的水蒸气凝结成液体,然后被排放。
甲烷通过碳分子筛吸附去除杂质。
这样可以保证反应装置中气体的纯度和稳定性。
2.气体压缩:经过气体净化后的空气和甲烷被分别压缩到一定压力,以满足反应器中的需求。
通常使用压缩机进行压缩,然后将压缩后的气体分别输送到反应器中。
3.反应制氨:反应制氨是整个过程的关键步骤。
通常采用哈柏法(Haber-Bosch)来实现反应制氨。
反应器中,高温高压的空气与甲烷的混合气体通过催化剂床进行催化反应。
常用的催化剂是铁与铁-铝的混合物,也可以加入少量的钾、镁等元素。
反应是一个放热反应,反应温度一般在380-550°C 之间,压力一般在1.7-3.5 MPa之间。
催化剂的存在可以提高反应速率,但也会增加反应的等离子体强度,导致了碳催化剂和蒸汽的选择性降低,产生非氮气杂质。
反应过程中,氮气与氢气进行反应生成氨气。
原料气体经过催化剂床后,反应转化率不高,需要多次通过催化剂床进行反应。
一般采用多级反应器和中间冷却装置,提高氨气的产率和纯度。
经过多级反应后,氨气还需要进行冷却和净化处理,以达到合成氨的纯度要求。
以上是合成氨的工序和流程的详细介绍。
合成氨的过程需要进行气体净化、气体压缩和催化反应制氨。
这个过程需要确保原料气体的纯度和稳定性,通过压缩提高原料气体的压力,催化剂的存在可以提高反应速率和转化率。
经过多级反应,最终得到高纯度的合成氨。
合成氨工艺的不断优化和改进,可以提高合成氨的生产效率和氨气的纯度,降低生产成本。
合成氨工艺流程
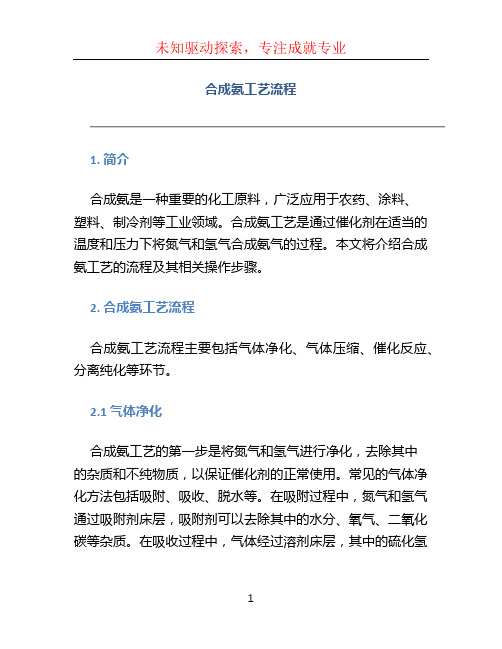
合成氨工艺流程1. 简介合成氨是一种重要的化工原料,广泛应用于农药、涂料、塑料、制冷剂等工业领域。
合成氨工艺是通过催化剂在适当的温度和压力下将氮气和氢气合成氨气的过程。
本文将介绍合成氨工艺的流程及其相关操作步骤。
2. 合成氨工艺流程合成氨工艺流程主要包括气体净化、气体压缩、催化反应、分离纯化等环节。
2.1 气体净化合成氨工艺的第一步是将氮气和氢气进行净化,去除其中的杂质和不纯物质,以保证催化剂的正常使用。
常见的气体净化方法包括吸附、吸收、脱水等。
在吸附过程中,氮气和氢气通过吸附剂床层,吸附剂可以去除其中的水分、氧气、二氧化碳等杂质。
在吸收过程中,气体经过溶剂床层,其中的硫化氢等有毒气体被吸收掉。
同时,还可以使用脱水剂去除气体中的水分。
2.2 气体压缩在气体净化后,将净化后的氮气和氢气进行压缩,提高其压力,以便后续的催化反应。
氮气和氢气分别进入压缩机进行压缩,压缩机通常采用多级压缩,保证气体压力的稳定和可控。
2.3 催化反应经过气体压缩后的氮气和氢气进入催化剂床层,进行合成氨的催化反应。
催化剂通常采用铁、钼或镍等金属催化剂,催化剂在适当的温度和压力下,使氮气和氢气发生反应,生成合成氨气。
催化反应是一个放热反应,需要控制温度以避免过高的温度导致副反应的发生。
2.4 分离纯化经过催化反应生成的合成氨气含有大量的副产物和未反应的氮气、氢气等杂质。
在分离纯化环节中,需要进行吸附、压缩、蒸馏等操作,将合成氨气中的杂质去除,提高纯度。
常见的分离纯化方法包括低温吸附法、压缩法和蒸馏法。
3. 工艺条件和参数合成氨工艺的实施需要满足一定的工艺条件和参数,以确保反应的进行和产出的质量。
常见的工艺条件和参数包括温度、压力、催化剂种类和配比、气体流速等。
3.1 温度催化反应的温度是合成氨工艺中的关键参数之一。
温度过高会导致副反应的发生,影响合成氨气的产量和纯度;温度过低则会降低反应速率。
一般情况下,催化反应的温度在300-500°C之间控制。
合成氨的工艺流程
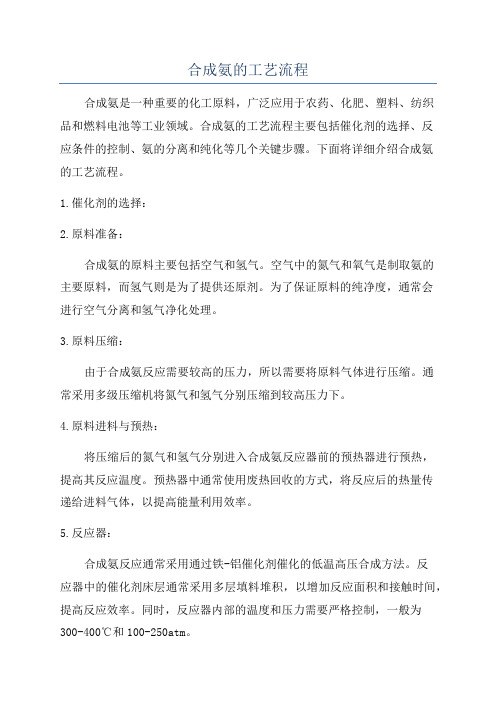
合成氨的工艺流程合成氨是一种重要的化工原料,广泛应用于农药、化肥、塑料、纺织品和燃料电池等工业领域。
合成氨的工艺流程主要包括催化剂的选择、反应条件的控制、氨的分离和纯化等几个关键步骤。
下面将详细介绍合成氨的工艺流程。
1.催化剂的选择:2.原料准备:合成氨的原料主要包括空气和氢气。
空气中的氮气和氧气是制取氨的主要原料,而氢气则是为了提供还原剂。
为了保证原料的纯净度,通常会进行空气分离和氢气净化处理。
3.原料压缩:由于合成氨反应需要较高的压力,所以需要将原料气体进行压缩。
通常采用多级压缩机将氮气和氢气分别压缩到较高压力下。
4.原料进料与预热:将压缩后的氮气和氢气分别进入合成氨反应器前的预热器进行预热,提高其反应温度。
预热器中通常使用废热回收的方式,将反应后的热量传递给进料气体,以提高能量利用效率。
5.反应器:合成氨反应通常采用通过铁-铝催化剂催化的低温高压合成方法。
反应器中的催化剂床层通常采用多层填料堆积,以增加反应面积和接触时间,提高反应效率。
同时,反应器内部的温度和压力需要严格控制,一般为300-400℃和100-250atm。
6.反应气体的冷却与净化:经过反应后,反应气体中除了产生的氨气外,还会有未反应的氮气、氢气以及其他杂质气体。
这些气体需要经过冷却器和废热回收器进行冷却和净化处理,以去除其中的杂质。
7.氨的分离与纯化:在反应气体中,氨气的浓度相对较低,需要进行分离与纯化。
常用的方法是采用低温吸附分离技术,将氨气吸附在吸附剂上,然后通过加热解吸的方式将氨气从吸附剂中释放出来。
8.尾气处理:总的来说,合成氨的工艺流程包括催化剂的选择、原料准备、压缩、进料与预热、反应器、冷却与净化、分离与纯化以及尾气处理等主要步骤。
合理控制每个步骤的条件和参数,能够提高合成氨的产率和质量,减少能源消耗和环境污染。
合成氨的生产流程

合成氨的生产流程合成氨是一种广泛应用于农业和化工领域的重要化学品,它用作肥料和原材料,在现代社会具有重要的意义。
本文将深入探讨合成氨的生产流程,帮助读者更好地理解这一过程的关键步骤和技术。
一、引言合成氨是一种通过将氮气和氢气合成而成的无色气体。
它被广泛应用于农业领域,用于制造氨水肥料,也是合成其他化学品的重要原料。
合成氨的生产流程主要由催化剂反应、气体净化和氨合成等步骤组成。
二、催化剂反应在合成氨的生产过程中,第一步是制备催化剂。
常用的催化剂是铁或铑基催化剂。
这些催化剂具有高度的活性和选择性,能够促使氮气和氢气发生反应。
2.1 清洁气体合成氨的生产过程开始之前,必须先准备清洁的氮气和氢气。
这些气体通常来自裂解炉或氢氟酸生产工艺中的副产品。
在这一步骤中,气体被送入净化系统,去除其中的杂质和不纯物质。
2.2 压力调节氮气和氢气经过净化后,需要将其压力进行调节。
调节后的压力必须与催化剂反应器的工作压力相匹配,以保证反应的正常进行。
2.3 催化剂载体合成氨的催化剂是由催化剂载体和催化剂活性组分组成。
催化剂载体通常是铝、硅和稳定剂等物质的混合物,用于支撑和固定催化剂活性组分。
2.4 催化剂的还原催化剂在装配后,必须进行还原处理。
这一步骤的目的是去除催化剂中的氧化物,提高其活性。
催化剂通常置于高温下,并与一个还原剂(如氨气)反应,还原催化剂的金属离子。
2.5 反应区域设计在合成氨的生产过程中,催化剂反应器的设计十分关键。
反应器通常是由多层催化剂床组成,以提高反应效率。
而且,反应器会在压力、温度和流量等方面进行控制,以确保最佳的反应条件。
三、气体净化在通过催化剂反应产生氨气后,我们需要对气体进行净化处理,以去除催化剂的残留物和其他杂质。
3.1 氨气冷却合成氨反应产生的气体含有大量热量。
在净化处理之前,需要通过冷却处理降低气体的温度,使其达到适合净化的温度范围。
3.2 气体压力调节与催化剂反应步骤类似,氨气也需要在净化过程中进行气压的调节。
- 1、下载文档前请自行甄别文档内容的完整性,平台不提供额外的编辑、内容补充、找答案等附加服务。
- 2、"仅部分预览"的文档,不可在线预览部分如存在完整性等问题,可反馈申请退款(可完整预览的文档不适用该条件!)。
- 3、如文档侵犯您的权益,请联系客服反馈,我们会尽快为您处理(人工客服工作时间:9:00-18:30)。
一、合成氨装置工艺流程说明合成氨装置由一氧化碳变换、酸性气体脱除、硫回收、气体精制、合成气压缩、氨合成、冷冻工序共7个工序组成。
1.一氧化碳变换工序工艺流程说明来自煤气化装置的粗煤气(242.25℃ 6.25MPag)进入变换原料气分离器(S04101),分离夹带的水分,再进入煤气过滤器(S04102),除去煤气中的其他杂质。
净化后的煤气经煤气换热器(E04101)加热到280℃左右,后进第一变换炉(R04101)进行变换反应,出第一变换炉的高温变换气进煤气换热器(R04101)换热,在煤气换热器(E04101)中加热煤气化装置来的粗煤气,换热后的变换器进入中压废热锅炉(E04103)中,在此,副产 2.6MPa(G)的中压饱和蒸汽,然后在265℃左右进入第二变换炉(R04102)。
第二变换炉(R04103)出来的变换气经过中压废锅II(E04102)调温至260℃左右后进第三变换炉(R04103)继续进行反应。
出第三变换炉(R04103)的变换气进低压废热锅炉(E04105)副产0.6MPa(G)的低压饱和蒸汽,此时变换气温度降至202℃左右,进入1#变换气分离器(S04104)分离出冷凝液后,变换气继续进入锅炉给水预热器(E04113)降温,在2#变换气分离器(S04104)分离冷凝液后进入除盐水预热器II(E04107),在5#变换分离器(S04110)中分离出冷凝液后继续进入除盐水预热器(E04114)中,此时温度降至70℃,经3#变换气分离器(S04105)后分离冷凝液,而后再进入变换气水冷器(E04108),冷却至40℃后进入酸性气体脱除工序。
从1#、2#和5#分离器(S04103、S04104、S04110)出来的高温冷凝液经冷凝液闪蒸槽(S04109)汇合并闪蒸后,液相经冷凝液泵II(P04103A/B)加压后,直接送往煤气化装置。
一氧化碳变换工序的低温工艺冷凝液、低温甲醇洗来的洗氨水以及塔顶回流液进入冷凝液汽提塔上部(冷凝液汽提塔操作压力0.4MPaa),在冷凝液汽提塔中用来自管网的低压蒸汽汽提,从冷凝液汽提塔底部出来的汽提后工艺冷凝液NH3含量小于10ppm,从冷凝液汽提塔顶部出来的气体尾气在汽提气水冷器(E04109)中用循环水冷却到40℃后进尾气分离器(S04107),尾气分离器(S04107)分离出来的冷凝液一部分送到冷凝液汽提塔顶部作为回流液,约有33-55%的冷凝液送氨法脱硫装置,出汽尾气分离器(S04107)的汽提尾气送火炬焚烧处理。
变换催化剂的升温硫化设置单独的升温硫化系统,升温还原介质经过氮气鼓风机(B04101)加压后,经开工加热炉(F04101)加热至200-400℃后进入各段变换炉对催化剂分别进行升温硫化,出各段变换炉的升温硫化介质经过氮气冷却器(E04110)后进氮气分离器(S04108),分离出液态水分后进入氮气鼓风机形成循环,同事补充少量氮气、氢气及二硫化碳。
另外,设有CS2贮槽(T04101)盛装CS2,做升温硫化用。
2.酸性气体脱除工序工艺流程说明(1) H2S和CO2的吸收从变换工序来的变换气(流量253186Nm3/h,温度40℃),在5.87MPaA的压力下被送到甲醇洗装置,先在变换气洗氨塔C04207内洗涤到NH3<2ppm。
洗氨后的变换气中含有饱和水,为防止变换气中的水分在冷却后冻结,需要向其内喷射注入少量的贫甲醇溶液。
注射了贫甲醇的变换气在原料气冷却器E04201中与液氮洗来的冷合成气、二氧化碳和尾气换热,冷凝后的甲醇与水的混合物从原料气分离罐S04201中分离出后进入洗涤塔C04201,用甲醇洗涤以脱除酸性气体,当净化气中CO2≤20ppm,总硫<0.1ppm后送往液氮洗装置。
洗涤塔分为上下塔,共四段,上塔为三段,下塔一段。
从P04204泵出来的贫甲醇溶液,经水冷器E04218,1#甲醇冷却器E04209,2#甲醇冷却器E04222,以及3#甲醇冷却器E04208中换热降温至约-61.77℃,进入C04201塔顶部作为洗涤液(流量283832kg/h )。
上塔顶段为精洗段,以确保净化气指标,中间两段为CO2初洗段和主洗段,用经段间换热器E04205,E04206换热冷却后的甲醇(入主洗段-43.92℃,入初洗段-43.30℃)在低温下吸收气体中的CO2,吸收了CO2后的富甲醇在上塔底部分成两部分,一部分送至下塔作为脱除H2S,COS等组分的洗涤液(约占50%,温度-8.74℃),另一部分经换热器E04217、E04207和E04204与合成气、富甲醇和氨蒸发换热后降温至-33℃左右进入闪蒸罐S04203,在1.75MpaA压力下进行闪蒸。
吸收H2S后的甲醇溶液由下塔底部排出,经换热器E04219、E04207和E04203分别与二氧化碳气、富甲醇和氨蒸发换热后进入闪蒸罐S04202,在1.75MpaA压力下进行闪蒸。
S04203和S04202的闪蒸气汇合后并与液氮洗来的循环氢混合后经循环气压缩机K04201增压送至洗氨塔后本工序的原料气中,以回收有用组分H2。
(2) H2S的浓缩从S04203底部引出的含CO2不含硫的甲醇液,经节流减压进入C04202塔顶部,闪蒸出大部分CO2气体,其液体作为C04202和C04203塔上部的回流液,洗涤含硫甲醇解析出的H2S组分,回流液流量分配通过FV-04209调整,以确保离开C04202塔顶部产品CO2气和C04203塔顶部尾气中硫含量达标;从S04202底部引出的含硫甲醇液经节流减压分别进入CO2解析塔C04202中段(流量51166kg/h,用FV-04208调整)和H2S浓缩塔C04203上塔(流量204662kg/h ),在此部分将CO2和H2S从甲醇中解析出来。
收集于C04202塔下部塔盘上的甲醇液,经液位控制LV-04225阀送到C04203塔上塔底部。
进入C04203上塔的三股溶液经减压气提解析出大部分CO2,由于CO2解析吸热,使其温度降至整个系统最低。
该低温甲醇液收集于C04203塔中部集液盘上,经P04201泵加压送至2#甲醇冷却器E04208和洗涤塔段间冷却器E04206回收冷量后温度升高,进入S04207闪蒸罐闪蒸。
S04207闪蒸出的气体后进入C04202塔下部,甲醇液经P04202泵加压并在E04207中换热升温后也进入C04202塔下部。
C04202塔底部的甲醇液经LV-04223阀节流膨胀进入C04203下塔中部,进一步被减压气提。
为使甲醇液中的CO2进一步得到解析,浓缩H2S,在C04203塔底部通入低压氮(12500Nm3/h),用N2气破坏原系统内的气液平衡,降低CO2在气相中的分压,使液相中的CO2进一步向气相中释放。
经C04203塔解析出的CO2随着气提N2作为尾气由塔顶送出。
(3)甲醇热再生从C04203塔底部出来的甲醇液中含有系统几乎全部的H2S和少量CO2,经泵P04203增压和JF04202过滤后,在1#甲醇冷却器E04209和热再生塔进料加热器E04210中加热后进入热再生塔C04204,经甲醇蒸汽加热气提再生后,硫化物和残余CO2随甲醇蒸汽由塔顶排出。
甲醇蒸汽在水冷器E04212中冷却后入热再生塔回流罐S04206,部分冷凝下的甲醇分离出来,经泵P04206送至C04204塔顶作为回流液。
S04206罐的气体继续在E04214和氨冷器E04213冷却后入S04205罐,冷凝下的甲醇送至C04203底部回收,而气体部分循环至C04203,部分经E04214升温后送至界外硫回收。
经C04204再生后的甲醇由塔底送出。
塔底贮罐有隔板将其分为冷区和热区,热区侧用再沸器E04211提供热量,冷热区在塔外有连通管,热区的甲醇溶液经泵P04205抽出,在贫甲醇过滤器JF04201中过滤,然后大部分甲醇溶液与从冷区底出来的甲醇液汇合在E04210中换热降温后到甲醇贮罐S04204,而小部分甲醇在E04216中换热后进入甲醇/水分离塔C04205顶部作为该塔的回流液。
S04204中的甲醇经泵P04204升压后,在水冷器E04218,1#甲醇冷却器E04209,2#甲醇冷却器E04222,以及3#甲醇冷却器E04208中换热降温至约-61.77℃,进入C04201塔顶部作为洗涤液。
出E04218的贫甲醇有一小部分作为注射甲醇送至E04201前的原料气管线内。
(4)甲醇/水分离从原料气分离罐S04201底部引出的含水甲醇在换热器E04216中与C04204塔底来的贫甲醇换热,经S04208闪蒸后进入C04205塔,参与蒸馏。
从塔C04206底部来的甲醇水溶液经水循环泵P04207加压,在E04220中换热升温后进入C04205塔参与蒸馏;该塔的塔顶回流液为来自泵P04205出口经E04216换热的那一小部分贫甲醇。
C04205塔顶产生的甲醇蒸汽直接送往C04204塔参与OH≤0.01%)再生,塔底的蒸馏水经E04220回收热量后,作为废水排放(CH3送至污水处理; C04205塔由再沸器E04215提供热量来维持塔的热平衡。
(5) CO气和尾气水洗2从C04203塔顶出来的低温尾气,经氮气冷却器E04221、2#甲醇冷却器E04222、原料气冷却器E04201回收冷量温度升高后进尾气水洗塔C04206,同气,经E04219和E04201回收冷量升温后大部分送时产自C04202塔的低温CO2压缩机,多余部分并入尾气中,用塔顶来的脱盐水(流量4800 kg/h)洗往CO2涤,为防止洗涤后尾气中所含的饱和水冷凝,可部分尾气(50%的左右)进C04206。
尾气水洗塔顶得到符合排放标准的尾气排放至大气。
3.硫回收工序工艺流程说明S主燃来自甲醇洗工序的酸性气经酸气加热器用蒸汽加热至140℃,进入H2烧炉(Z05101),在H2S主燃烧炉(Z05101)中,酸性气和一定比例配入的氧气混合发生燃烧,并与炉内另一股酸气发生H2S的克劳斯反应。
在燃烧炉中主要反应的反应式为:H 2S+1/2O2→S+H2OH 2S+3/2O2→SO2+H2O出炉的高温气体在废热锅炉E05101与锅炉软水换热,生成0.6MPa饱和蒸汽,并在此分离出液态的硫。
从废热锅炉出来的气体经过一级过程气加热器升温至240℃进入一级克劳斯反应器R05101A床层进行催化转化反应,反应器内装填硫回收多功能催化剂,在反应器中主要的化学反应式如下:2H2S+SO2→3/XSX+2H2OCOS+H2O→H2S+CO2CS2+2H2O→2H2S+CO2反应后的气体进入一级硫冷凝器降温至160℃回收硫磺,脱硫后的气体进入二级过程气加热器用中压蒸汽加热至220℃左右进入二级反应器进行二段催化反应。