Ansys nCode疲劳分析
pera ANSYS nCode DeaignLife 高级疲劳分析技术

疲劳分析背景
哈维兰彗星型客机 —第一个喷气客机(1952) -机体反复承受增压和减压引发金属疲劳 -裂缝在尖角萌生然后扩展至失效 -加压机身的失效引起整个结构的崩溃
民航历史上首次发生因金属疲劳导致的空难事件。
疲劳分析背景
据不完全统计,欧洲每年早期断裂造成的 损失达800亿欧元;
美国每年早期断裂造成的损失达1190亿 美元;
焊缝疲劳
• • • • • 焊接材料不均匀,金相组织不均匀; 焊缝处存在残余应力; 焊缝处几何不连续,存在较大的应力集中; 焊缝处经常存在焊接缺陷; 相对于母材,焊接的疲劳寿命分散性更大。
焊缝疲劳
焊缝Байду номын сангаас劳
• nCode公司与Volvo公司、Chalmers大学联合开发; • 支持多种焊接形式:贴脚焊(fillet)、搭接焊 (overlap)、激光焊(laser); • 能够智能识别模型中焊缝的信息,从而简化疲劳分析 流程; • 具有焊缝材料拉伸、弯曲情况下的疲劳数据,适合于 weld toe, root 和 throat的破坏;
nCode分析-五框图
ANSYS nCode功能特色
强大的结果输出功能: • 云图、标记显示 • 输出自动鉴别疲劳关键区域和热点; • 疲劳分析结果表格输出; • Studio Glyph自动报告生成
nCode分析-五框图
1 CONTENTS
2
ANSYS nCode特点
3
高级疲劳分析技术
焊缝疲劳
E[0]
m2 m0
m4 E[ P] m2
振动疲劳
LaLanne • 通用宽带技术 • 许多军用标准使用 • 是 ANSYS nCode DesignLife 的默认使用方法
ANSYSnCodeDesignlife高级疲劳寿命分析

ANSYS nCode 的价值
1. 预先进行耐久性评估,减少物理 试验,避免设计和加工改变而导致 的重大损失 2. 通过模拟优化物理试验载荷谱, 大幅减少试验时间和成本
© 2012 Pera Corporation Ltd. All rights reserved.
4 用户案例
© 2012 Pera Corporation Ltd. All rights reserved.
目录
1 产品简介
© 2012 Pera Corporation Ltd. All rights reserved.
ANSYS nCode产品简介
ANSYS nCode DesignLife是 集成在ANSYS Workbench 平台上的高级疲劳分析模块, 为客户提供先进的疲劳分析 解决方案。
完全集成于ANSYS WorkBench平台
Click & Drag操作方式,易学易用
先进的疲劳分析技术 构建任意复杂的载荷谱
强大的疲劳结果输出功能
© 2012 Pera Corporation Ltd. All rights reserved.
完全集成于ANSYS WorkBench平台
支持常幅值、单时间历程、多时间历程载荷
客户定制流程开发
© 2012 Pera Corporation Ltd. All rights reserved.
目录
2 功能特色
© 2012 Pera Corporation Ltd. All rights reserved.
ANSYS nCode功能特色
焊点、焊缝的焊接疲劳计算; 高级振动疲劳分析计算(PSD); 在多轴应力状态评估的基础上, 自动选择计算方法;
ANSYS nCode 2016中文

ANSYS Whanical使用 • Mechanical Pro,Premium, Enterprise等模块中包含
4
© 2016 ANSYS, Inc.
ANSYS Confidential
DesignLife接口
Available Data
Workspace
Glyph Palette
有限元数据
结果数据
5
© 2016 ANSYS, Inc.
疲劳分析
输入数据
ANSYS Confidential
ANSYS nCode DesignLife
– 低周期疲劳
• 破坏为止的周期数大(1 - 10万回以上) • 反复的负荷以振幅为基准的评价方法 • 疲劳的分析中Stress Life(应力寿命)法适合的
2
© 2016 ANSYS, Inc.
ANSYS Confidential
ANSYS疲劳分析软件nCode
ANSYS nCode DesignLife
– Ksur = Ktreatment * Kuser * Kroughness
• Ktreatment = surface treatment factor
• Kuser
= user surface factor
• Kroughness = surface roughness type
9
© 2016 ANSYS, Inc.
8
© 2016 ANSYS, Inc.
nCode疲劳材料数据库
ANSYS Confidential
Ansys nCode疲劳分析

通过“疲劳缺口系数” 修正S-N曲线中的S;
缺口附近的Von Mises 应力
© 2015 ANSYS, Inc.
29
3.2 缺口应力集中对疲劳寿命的影响
应用S-N曲线,光滑试样的耐久极限应力幅除以疲劳缺口系 数Kf就得到同样耐久力情况下缺口部分的疲劳强度估计值
。
© 2015 ANSYS, Inc.
临界平面法计算平面应力和在几个径向平面进行重新求解
− 默认是每10度 (18 个平面)
− 雨流计数法在每个平面上计算疲劳损伤 − 准则平面是最大损伤的平面
© 2015 ANSYS, Inc.
支持的有限元结果: 静态分析(线性/非线 性) 瞬态分析 模态分析 频谱响应
能够读取ANSYS、Abaqus、 Nastran等软件的有限元计算结果
nCode分析-五框图
© 2015 ANSYS, Inc. 18
ANSYS nCode 的功能特色
创建内存模板材料 用户可自定义材料; 丰富的材料数据库; 利用material manager自定义材料
最大剪切应力
最大主应力
标记的 Von-Mises
应力是最常用的
− 用于脆性材料
绝对最大主应力 任一分量的应力 临界平面法
© 2015 ANSYS, Inc.
40
3.4 多轴状态对疲劳寿命的影响
如果加载过程中主应力方向改变,计算应力范围使用一个派生的单轴应力可 能是不正确的
临界平面法可用于计算主应力方向改变的情况
nCode分析-五框图
© 2015 ANSYS, Inc. 19
ANSYS nCode 的功能特色
时间序列 恒幅载荷
时间步载荷
AnsysMechanical内嵌nCode疲劳仿真工具

AnsysMechanical内嵌nCode疲劳仿真工具疲劳分析是分析结构受到周期性载荷作用下,结构应力远小于强度极限情况,甚至结构应力比弹性极限还低的情况下就可能发生破坏的情况。
Ansys nCode是国际著名的疲劳耐久性仿真分析软件,其多个版本以前已经可以和Ansys Mechanical进行无缝以进行联合分析。
而在最新版的Ansys Mechanical 2020R2中可以进一步将nCode进行内嵌,完成结构分析后即可进行疲劳仿真设置,从而提高疲劳仿真效率。
已安装完成nCode Embedded DesignLifeEmbedded nCode 疲劳分析模块内嵌系统分析流程树示意图Embedded nCode Designlife内嵌到Mechanical模块中,需要使用到以下插件MechanicalEmbeddedDesignLife.wbex,其操作方法参见附录。
下面是笔者实际工作中的一个疲劳仿真案例,说明如何在Ansys Mechanical中使用Embedded nCode分析工具。
如下图,为某空调压缩机模型,外壳通过三处安装柱以螺纹形式进行固定,皮带轮在外载荷作用下,带动内部压缩阀等部件转动,进而实现空气压缩。
由于压缩机工作过程为高速运转过程,同时其上的皮带轮所受到的外部载荷具有较大的波动性,因此容易造成压缩机壳体等部件在工作过程中发生疲劳失效,进而影响压缩机的正常工作,从而需要对压缩机壳体等部件进行疲劳仿真计算。
之前版本的Ansys Mechanical软件需要在完成结构分析后,在拖入nCode的相应模块进行疲劳仿真,如下图所示。
要进行疲劳仿真需要打开nCode界面,并在nCode模块中进行设置,此种方式的优势在于可以使用全面的nCode功能。
但是缺点在于需要在不同的界面进行切换以及数据传递更新。
新的Ansys Mechanical 2020R2 将nCode的部分功能内嵌到Mechanical,在完成结构分析或者调整后,可以直接在同一个界面下进行仿真计算。
ANSYS nCode Designlife高级疲劳分析

ANSYS nCode功能特色
完全集成于ANSYS WorkBench平台 Click & Drag操作方式,易学易用 先进的疲劳分析技术 构建任意复杂的载荷谱 强大的疲劳结果输出功能
© 2012 Pera Corporation Ltd. All rights reserved.
案例3 焊缝疲劳分析
© 2012 Pera Corporation Ltd. All rights reserved.
案例4 风电主轴疲劳寿命分析
© 2012 Pera Corporation Ltd. All rights reserved.
Thank You
完全集成于ANSYS WorkBench平台
以流程图形式建立分析任务; 无缝读取ANSYS计算结果; 与ANSYS共享材料数据库; 在WB平台上统一进行参数管 理,可用DX进行优化。
© 2012 Pera Corporation Ltd. All rights reserved.
Click & Drag操作方式,易学易用
能够读取ANSYS、Abaqus、 Nastran等软件的有限元计算结果
支持常幅值、单时间历程、多时间历程载荷
© 2012 Pera Corporation Ltd. All rights reserved.
录
2 功能特色
© 2012 Pera Corporation Ltd. All rights reserved.
ANSYS nCode 的主要用途
提供专业的疲劳分析技术,协助用户在产品设计中:
1. 避免设计缺陷引起的疲劳破坏 产品出现不应当发生 的疲劳失效,会使企 业的信誉受损,经济 损失更大! 2. 避免过于保守的设计
ANSYS nCode DesignLife疲劳分析材料属性定义
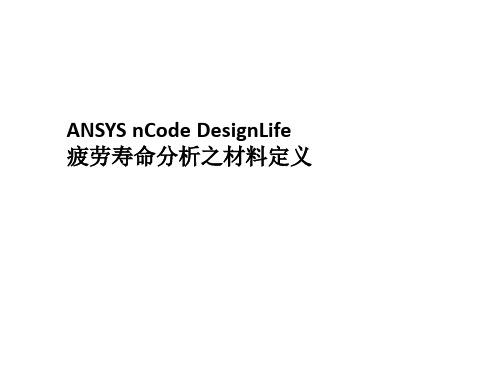
nCode Material Data
• DesignLife requires specific material information – particular information depends on material type – duplicate similar material
5 Box Trick
• CAE fatigue process can be described in 5 basic steps
FE Input
Material Mapping
Load Mapping
CAE Fatigue Analysis
Fatigue Results Display
Material mapping defines the fatigue properties for the materials
• Each material in the DesignLife material library typically has either stress-life (SN) or strain-life (EN) fatigue properties, although some have both.
Rename New Material
• After duplicating > rename material
Modify Properties
• Modify propertiesand “Refresh Project”
Defining New Material
• New material is now available in Mechanical and for downstream use in DesignLife
ANSYS nCode DesignLife 疲劳仿真
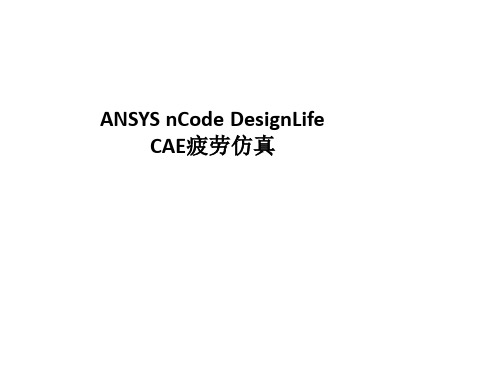
应力-寿命方法
⚫ 应力-寿命(SN)疲劳方法假设疲劳损伤是由波动的应力产生的 • 仅适用于弹性应力,因此限于低应力/高循环应用 ✓ 通常对于韧性金属来说,疲劳失效需要超过100,000个循环 • 疲劳寿命基于交变应力范围和Wöhler疲劳曲线(S-N曲线) • 原始的数值疲劳方法 • 丰富的行业经验 • 简单的技术 • 通常可以通过手工计算进行验证
阶段 II 裂纹
⚫ 微裂纹穿过 2-3 个晶粒边界后,发展成疲劳裂纹(阶段 II 裂纹) ✓ 相对于材料的微观结构,疲劳裂纹较大 ✓ 裂纹本身在物理上中断了应力的流动
⚫ 应力集中导致裂纹尖端出现塑性应力 ✓ 局部塑性应力导致裂纹改变方向
⚫ 裂纹的生长现在由裂纹尖端的循环塑性应力驱动 ⚫ 裂纹方向垂直于最大主应力
疲劳破坏
•如果存在足够的能量,阶段 II 裂纹会继续生长,直到发生拉伸破坏 • 大多数裂纹缺乏足够的能量穿越晶粒边界 • 裂纹“停滞”
滑移带
微裂纹
疲劳裂纹
拉伸破坏
初始裂纹
疲劳损伤 产生条纹 (又称“海滩标记”)
快速最终断裂由于拉伸破坏 - 无条纹
CAE疲劳分析
•CAE可以在虚拟环境中预测疲劳损伤 ✓ 评估可以在设计阶段进行 ✓ 可以评估由多个载荷引起的累积损伤
⚫ 疲劳方法 • 使用计算出的应力/应变和材料疲劳曲线来预测失效的周期数(寿命) •两种基本的疲劳分析方法
• 应力-寿命(SN) ✓ 使用弹性应力
• 应变-寿命(EN) ✓ 使用弹性-塑性应变
CAE疲劳方法
⚫ 应力-寿命(SN)方法使用弹性计算的应力和应力与循环疲劳失效曲线(S-N曲线) • 假设应力驱动疲劳 • 仅适用于高循环疲劳 • 对于韧性金属来说,通常指超过100,000个循环
- 1、下载文档前请自行甄别文档内容的完整性,平台不提供额外的编辑、内容补充、找答案等附加服务。
- 2、"仅部分预览"的文档,不可在线预览部分如存在完整性等问题,可反馈申请退款(可完整预览的文档不适用该条件!)。
- 3、如文档侵犯您的权益,请联系客服反馈,我们会尽快为您处理(人工客服工作时间:9:00-18:30)。
© 2015 ANSYS, Inc.
38
4 多轴状态对疲劳寿命的影响
用来创建S-N曲线的测试数据主要是单轴状态,但有限元结果 通常是多轴的
多轴应力结果必须被转换为一个用于S-N曲线单轴值
基本假设是派生的单轴量(e.g., σeqv) 引起的损伤等同于,在单 轴应力状态下零件经历相同数量引起的损伤
31
3.2 缺口应力集中对疲劳寿命的影响
ANSYS nCode DesignLife如何考虑?
基于应力梯度作为一个替代方法 − Auto:如果应力梯度存在则使用应力梯度校正
– User:从查找表中用户自定义应力梯度校正
– Off: 不考虑应力梯度校正
© 2015 ANSYS, Inc.
32
3.2 缺口应力集中对疲劳寿命的影响 − Auto:如果应力梯度存在则使用应力梯度校正
现代设计方法
© 2015 ANSYS, Inc.
14
Ansys nCode疲劳分析优势(二)
ANSYS nCode DesignLife是ANSYS与HBM的nCode强强 联合的结晶。Ncode公司是国际著名的疲劳耐久性工程专 业公司和技术领导者。自80 年代公司成立至今,引导并推 动了疲劳理论在工业领域中的应用及其发展。
平滑区域
扰动载荷 局部性 发展过程
5
疲劳分析方法
应力疲劳分析(S-N)
第一种疲劳分析方法 循环应力水平低、寿命长
应变疲劳分析(E-N)
循环应力水平高、寿命短 屈服后应变变化大、应力变化小
高周疲劳:材料在低于其屈服强度 的循环应力作用下,经104-105以上 循环产生的失效;
低周疲劳:材料在接近或超过其屈服 强度的应力作用下,低于104-105次塑 性应变循环产生的失效;
© 2015 ANSYS, Inc.
39
3.4 多轴状态对疲劳寿命的影响
von-Mises 应力 标记的 von-Mises 应力
− 以最大绝对主应力的符号标记
最大剪切应力 最大主应力
− 用于脆性材料
绝对最大主应力 任一分量的应力 临界平面法
标记的 Von-Mises 应力是最常用的
© 2015 ANSYS, Inc.
1. 避免设计缺陷引起的疲劳破坏
2. 避免过于保守的设计
产品出现不应当发生 的疲劳失效,会使企 业的信誉受损,经济 损失更大!
过于保守设计,使得产 品的成本增加,市场竞 争力下降!
© 2015 ANSYS, Inc.
17
ANSYS nCode 的功能特色
支持的有限元结果: 静态分析(线性/非线 性) 瞬态分析 模态分析 频谱响应
© 2015 ANSYS, Inc.
28
2 缺口应力集中对疲劳寿命的影响
疲劳裂纹起始于峰值应力区域
– 由于应力集中引起 – 疲劳计算中必须考虑
通过“疲劳缺口系数” 修正S-N曲线中的S;
缺口附近的Von Mises 应力
© 2015 ANSYS, Inc.
29
3.2 缺口应力集中对疲劳寿命的影响 应用S-N曲线,光滑试样的耐久极限应力幅除以疲劳缺口系 数Kf就得到同样耐久力情况下缺口部分的疲劳强度估计值 。
© 2015 ANSYS, Inc.
25
3.1 材料表面状况对疲劳寿命的影响
在 ANSYS nCode DesignLife中,用表面因子(Ksur)同时考虑表面光洁度和处 理对疲劳的影响
− 表面因子用来调整材料s-n曲线
Ksur是三个用户定义因子的乘积 − Ksur = KTreatment * Kuser * Kroughness
40
3.4 多轴状态对疲劳寿命的影响
如果加载过程中主应力方向改变,计算应力范围使用一个派生的单轴应力可 能是不正确的
临界平面法可用于计算主应力方向改变的情况
临界平面法计算平面应力和在几个径向平面进行重新求解
− 默认是每10度 (18 个平面) − 雨流计数法在每个平面上计算疲劳损伤 − 准则平面是最大损伤的平面
3 平均应力对疲劳寿命的影响
4 多轴状态对疲劳寿命的影响
© 2015 ANSYS, Inc.
24
1 材料表面状况对疲劳寿命的影响
表面粗糙度的影响 表面处理的影响
表面粗糙会使局部应 力集中程度加大,裂 纹萌生寿命短。
表面喷丸处理,引入残余 压应力,提高疲劳寿命; 焊接、气割等引入残余拉 应力,降低疲劳寿命。
© 2015 ANSYS, Inc.
N 恒幅载荷下的s-n曲线
8
疲劳分析理论
变幅载荷:雨流计数法——周期统计
循环 ADA’ BCB’ EHE’ FGF’ IJI’
幅值 9 4 7 3 2
均值 0.5 1 0.5 -0.5 -1
© 2015 ANSYS, Inc.
9
疲劳分析理论
米勒准则(Miner准则)-—— 损伤计算
ANSYS nCode Designlife 高级疲劳寿命分析
© 2015 ANSYS, Inc.
1
目录
1 疲劳理论介绍 2 ANSYS nCode Designlife功能特色 3 S-N疲劳分析概述及案例介绍 4 随机振动疲劳分析概述
© 2015 ANSYS, Inc.
2
疲劳分析理论
只通过静力来确定 材料的机械性能时 ,机械性能没有充 分反映材料在交变 载荷作用下的特性 。使用过程中往往 会发生突如其来的 破坏。
© 2015 ANSYS, Inc.
6
疲劳分析方法
应力疲劳分析(S-N)
S
光滑标准件,在恒幅对称循环应力作用下 进行疲劳试验。 施加不同应力幅Sa,记录相应的寿命N。 恒幅对称载荷应力比R为-1,平均应力为Sm 为0.
© 2015 ANSYS, Inc.
N
7
疲劳S-N曲线
S
变 幅 载 荷? 随 机 载 荷?
能够读取ANSYS、Abaqus、 Nastran等软件的有限元计算结果
nCode分析-五框图
© 2015 ANSYS, Inc.
18
ANSYS nCode 的功能特色 用创丰利户建富用可内的m自存材a定模te料义板ri数a材l 据m料a库;n;ager自定义材料
nCode分析-五框图
© 2015 ANSYS, Inc.
1
Sm Su
2
Se
Sa =应力幅 Sm = 平均应力 Su = 极限抗拉强度 Se = 疲劳极限
Gerber平均应力修正理论假定一个抛物线
© 2015 ANSYS, Inc.
37
3.4 平均应力对疲劳寿命的影响
Sa 1 Sm Se Su
• Goodman 更保守 • 实际的数据往往介于Goodman 和Gerber之间
19
ANSYS nCode 的功能特色
时间序列 恒幅载荷 时间步载荷 温度载荷 Hybird载荷 振动载荷 Duty Cycle
nCode分析-五框图
© 2015 ANSYS, Inc.
20
ANSYS nCode 的Байду номын сангаас能特色
ANSYS nCode DesignLife 具有全面 的疲劳分析能力
应力疲劳 (单一,多曲线,Haigh图) 应变疲劳(自动多轴修正) 多轴安全系数分析(Dang Van) 焊缝和点焊疲劳分析 高温疲劳分析 振动疲劳(振动台模拟)
(n/N) = 1
n1 + n2
=1
N1
N2
© 2015 ANSYS, Inc.
10
2 ANSYS nCode Designlife功能特色
Ansys nCode疲劳分析优势 功能特色介绍
© 2015 ANSYS, Inc.
11
Ansys nCode疲劳分析优势(一)
传统的疲劳分析方法
设计
样机
22
3 S-N疲劳分析概述
S-N 曲线: • 在恒幅对称载荷下破坏多个试样; • 试样为光滑标准件; • 拟合曲线通过绘制数据拟合;
考虑平均应力
材料的S-N曲线
考虑几何缺口
考虑表面处理、表面光洁度、环境
© 2015 ANSYS, Inc.
23
疲劳寿命的影响因素
1 材料表面状况对疲劳寿命的影响
2 缺口应力集中对疲劳寿命的影响
© 2015 ANSYS, Inc.
30
3.2 缺口应力集中对疲劳寿命的影响
理论分析:
与材料相关的参数,可通过下式估算:
q:缺口敏感系数
© 2015 ANSYS, Inc.
缺口半径
Kf:疲劳缺口系数 光滑件疲劳极限与缺口件疲劳极限之比
Kt:弹性应力集中系数 缺口处最大实际应力与该处名义应力之比
一般Kf小于Kt ,两者的关系可以用缺口敏 感系数q表征。
© 2015 ANSYS, Inc.
26
3.1 材料表面状况对疲劳寿命的影响
可以输入表面处理系数 (KTreatment)和用户表面系数(Kuser) − 默认值为1
© 2015 ANSYS, Inc.
27
3.1 材料表面状况对疲劳寿命的影响
表面粗糙度(Kroughness)的影响可以通过选择进行定义 − 默认的为“Polished”
在nCode中采用FKM的应力梯度法
– 确定校正系数
在雨流计数前得到有效应力分量:
© 2015 ANSYS, Inc.
33
3.2 缺口应力集中对疲劳寿命的影响
− User:从查找表中用户自定义应力梯度校正
自定义格式:
Stress gradient correction factor file v1.0 Dimension=mm #Normalized stress gradient G, correction factor n StartCorrectionData 0,1 1,1.1 10,1.2 100,1.3 EndCorrectionData