微细加工技术在国内外发展趋势的研究
微纳米加工技术的研究现状和发展趋势

微纳米加工技术的研究现状和发展趋势微纳米加工技术是当今科技领域的一个热门研究方向,具有广泛的应用前景。
在微观或纳米尺度下加工材料和制造器件,可以实现高度精准度、高灵敏度、高效率和低成本等优点,涉及到材料科学、物理学、电子学、生命科学、环境科学等多个领域。
本文将介绍微纳米加工技术的研究现状和发展趋势,为读者提供一个全面了解该领域的视野。
一、微纳米加工技术的发展历程微纳米加工技术的起源可以追溯到20世纪50年代。
当时,瑞士IBM实验室的物理学家Hans Lüth和Wolfgang Haensch通过使用光刻技术制造微米尺度光栅,在光学领域掀起了一场革命。
此后,微纳米加工技术迅速发展,涌现了许多新的加工方法和应用领域,如电子束曝露、离子束曝露、扫描探针显微镜、纳米压印等。
二、微纳米加工技术的主要加工方法微纳米加工技术的主要加工方法包括光刻、电子束曝露、离子束曝露、扫描探针显微镜、纳米压印等。
其中,光刻技术是目前最为广泛应用的一种方法,它通过将光学芯片和掩膜联系在一起,在显微镜下定位曝光,形成微米级图形。
电子束曝露技术与光刻技术类似,但它使用的是电子束而不是光线照射掩膜。
在离子束曝露技术中,离子束照射目标表面,将表面的原子打击或溶解,形成所需的图形。
扫描探针显微镜使用一根极细的探针进行扫描,根据探针运动轨迹上的图形变化最终形成所需的图案。
纳米压印技术采用压印机在基板表面上施加高压和高温,将模板上的图形印刻到基板上。
三、微纳米加工技术的应用领域微纳米加工技术在各个领域都有广泛的应用。
在电子学领域,微纳米加工技术可以制造出高性能的集成电路、光学器件和传感器等。
在生物医学领域,微纳米加工技术可以制造出生物芯片、药物递送系统和生物传感器等。
在能源领域,微纳米加工技术可以制造出太阳能电池、燃料电池和储能器件等。
在环境领域,微纳米加工技术可以制造出气体传感器和水质监测传感器等。
此外,微纳米加工技术还可以应用于国防、交通运输、通信、农业等多个领域。
微细结构超精密加工技术的研究
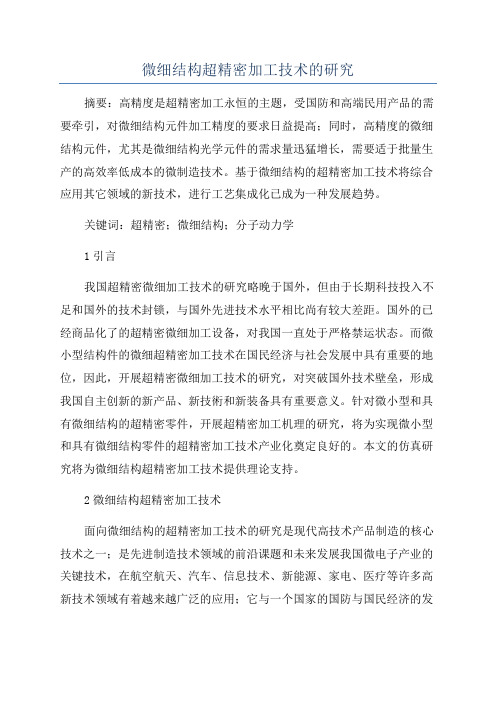
微细结构超精密加工技术的研究摘要:高精度是超精密加工永恒的主题,受国防和高端民用产品的需要牵引,对微细结构元件加工精度的要求日益提高;同时,高精度的微细结构元件,尤其是微细结构光学元件的需求量迅猛增长,需要适于批量生产的高效率低成本的微制造技术。
基于微细结构的超精密加工技术将综合应用其它领域的新技术,进行工艺集成化已成为一种发展趋势。
关键词:超精密;微细结构;分子动力学1引言我国超精密微细加工技术的研究略晚于国外,但由于长期科技投入不足和国外的技术封锁,与国外先进技术水平相比尚有较大差距。
国外的已经商品化了的超精密微细加工设备,对我国一直处于严格禁运状态。
而微小型结构件的微细超精密加工技术在国民经济与社会发展中具有重要的地位,因此,开展超精密微细加工技术的研究,对突破国外技术壁垒,形成我国自主创新的新产品、新技術和新装备具有重要意义。
针对微小型和具有微细结构的超精密零件,开展超精密加工机理的研究,将为实现微小型和具有微细结构零件的超精密加工技术产业化奠定良好的。
本文的仿真研究将为微细结构超精密加工技术提供理论支持。
2微细结构超精密加工技术面向微细结构的超精密加工技术的研究是现代高技术产品制造的核心技术之一;是先进制造技术领域的前沿课题和未来发展我国微电子产业的关键技术,在航空航天、汽车、信息技术、新能源、家电、医疗等许多高新技术领域有着越来越广泛的应用;它与一个国家的国防与国民经济的发展密切相关,是一个国家的国民经济、国防和科学技术综合实力的体现,已经成为许多国民经济领域的制造技术可持续发展的一个重要保障条件。
在精密工程应用领域,元件的几何形状精度经常需要控制在纳米量级,如:精密轴和孔的圆柱度、大规模集成电路使用的单晶硅片的平面度等等。
与此同时,元件还需要具有纳米级的表面质量,如表面平整性以及表面和次表面的损伤程度(包括微裂纹、物理结构的变化、大规模塑性变形和残余应力等)。
为满足这些指标要求,元件在加工过程中切削力的数量级必须控制在10-6N到10-9N的范围内,而相应的切削深度应该保持在10-6m到10-9m的范围内。
微细加工技术的研究与应用
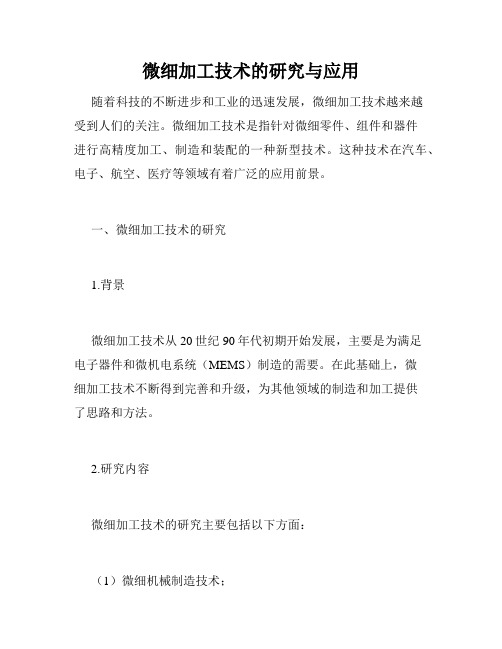
微细加工技术的研究与应用随着科技的不断进步和工业的迅速发展,微细加工技术越来越受到人们的关注。
微细加工技术是指针对微细零件、组件和器件进行高精度加工、制造和装配的一种新型技术。
这种技术在汽车、电子、航空、医疗等领域有着广泛的应用前景。
一、微细加工技术的研究1.背景微细加工技术从20世纪90年代初期开始发展,主要是为满足电子器件和微机电系统(MEMS)制造的需要。
在此基础上,微细加工技术不断得到完善和升级,为其他领域的制造和加工提供了思路和方法。
2.研究内容微细加工技术的研究主要包括以下方面:(1)微细机械制造技术;(2)微细电子制造技术;(3)微细光学制造技术;(4)微细生物制造技术。
其中,微细机械制造技术是应用最为广泛的一项技术,主要针对微型零部件、机械组件和器件等进行加工和制造。
3.研究难点微细加工技术的研究面临着许多难点,其中最主要的难点是如何实现高精度加工。
微细零部件的尺寸通常都在数微米至数百微米之间,而传统加工技术所能达到的精度却远远不够。
因此,如何在微小尺度下进行高精度加工,是微细加工技术研究的核心问题。
二、微细加工技术的应用1.汽车制造领域汽车制造领域是微细加工技术应用的主要领域之一。
在汽车制造中,许多零部件的尺寸都很小,而且对加工精度要求很高。
例如,发动机的火花塞、气门、燃油喷嘴等部件;车身的紧固件、密封件和缝合件等,都需要采用微细加工技术进行加工和制造。
2.电子制造领域电子制造领域也是微细加工技术应用的重要领域之一。
在电子制造中,许多IC芯片、闪存和存储器等器件的结构都非常微小,需要采用微细加工技术进行精密加工和制造。
同时,电子制造领域还需要采用微细加工技术进行导电薄膜的制造、微型电极的加工等工作。
3.医疗领域医疗领域也是微细加工技术应用的一个新兴领域。
在医疗领域中,微细加工技术可以用于制造微型手术器械、医用传感器、微型分析芯片等器件,从而为医疗诊断和治疗提供了新的手段和方法。
高速高效微细加工技术的发展研究

高速高效微细加工技术的发展研究摘要:高速高效微细加工技术就是综合了高速加工技术、高效加工技术和微细加工技术这三个方面的加工技术来提高制造工艺,它是集高效、优质、超精密微细和低耗于一身的先进制造工艺技术。
包括高速切削加工、高进给切削加工、大余量切削和高效复合切削加工、高速与超高速磨削、高效深切磨削、快速点磨削和缓进给深切磨削。
关键词:高速高效微细加工高速切削加工高速与超高速磨削前言:制造业为人类创造了辉煌的物质文明,它是一个国家经济发展先进与否的重要标志。
从古至今,制造业不断改变着人们的生产方式、经营管理模式乃至社会的组织结构形式和文化内容,尤其是机械制造,更是国民经济支柱。
高速高效微细加工技术随着社会对制造加工业提出更高的要求而成为各个加工制造业日益关注的技术,不断加大了对其的科研投入。
因此,我们要进一步发展机械制造业,就要向高速高效微细加工技术发展。
1.高速高效微细加工技术概述及应用1.1.高速切削加工技术高速切削加工技术中的“高速”是一个相对概念,随着切削加工技术的不断发展其速度范畴发生着变化,对于不同的加工方法和工件材料与刀具材料,高速切削加工时应用的切削速度也不相同。
从切削速度方面,一般以高于5 10 倍的普通切削速度的切削加工定义为高速切削加工。
从切削机理上定义为:切削加工过程通过能量转换,高硬刀具对工件材料的作用,导致其表面层产生高应变速率的高速切削变形和刀具与工件之间的高速切削摩擦学行为,形成的热、力耦合不均匀强应力场制造工艺。
1.2.高效加工技术近来,一些从事高效加工技术研究者,从开始就强调切削加工中加工零件的质量与生产效率的共同更大幅度的提高。
该研究继承了高速切削可以降低切削力﹑提高加工零件精度和表面质量等特点,着重从极大地提高生产效率的目的出发,进行了大量的切削试验研究,从理论和实践的结合上解决了许多技术难题,使高效率切削技术开发研究取得了长足的进展。
高效率加工技术的关键在于:采取了选用或新设计出具有足够的机床主轴转速与较大地传递力矩的能力的高功率、高刚性机床,进行大功率切削;选用目前最好的先进刀具材料;选用适合高速切削先进的刀具夹头;采用独具风格的特殊加工方法以及选择合理的切削参数等技术措施。
微细加工技术的发展与应用

微细加工技术的发展与应用随着科技的不断发展,微细加工技术成为现代工业中不可或缺的一部分。
微细加工技术是指对微小物体进行加工的技术,通常用于制造那些需要高精度或者微小尺寸的零件、设备和器件。
微细加工技术的应用范围非常广泛,包括微型机器人、光学器件、医疗器械、生物传感器等领域。
本文将探讨微细加工技术的发展历程、应用和未来发展趋势。
一、微细加工技术的发展历程微细加工技术源远流长。
在过去的几百年间,人们使用了各种手工工具和机械设备进行微细加工。
例如,19世纪英国人约瑟夫·温斯洛在1822年发明了摆线拖动齿轮切削机,实现了金属齿轮的精细加工。
这一技术被广泛应用于英国的纺织工业,并为工业革命的发展做出了贡献。
20世纪初,随着电气工程和电子学的发展,半导体器件的出现推动了微细加工技术的发展。
1947年,贝尔实验室的威廉·肖克利发明了第一个晶体管,奠定了现代电子工业的基础。
从此以后,微细加工技术得到了巨大的发展,出现了各种各样的微细加工工具和设备。
例如,扫描电子显微镜可以对微小物体进行高分辨率成像和表征,电子束光刻机可以用来制造半导体芯片、具有纳米尺度精度的纳米定位台可以用来进行精细的纳米加工等等。
二、微细加工技术的应用微细加工技术已经广泛应用于多个领域。
以下是一些例子:1. 光学器件光学器件包括激光器、光开关、波导器、光电探测器等。
微细加工技术可以提供高精度和可重复加工,适用于制造这些器件的需求。
例如,电子束光刻机已经被广泛应用于制造半导体激光器和光子晶体器件。
2. 医学器械微细加工技术可以用于制造医学器械,例如微型手术器械和医用传感器。
这些器械需要高精度和微小尺寸,以减少对患者的创伤和疼痛。
微细加工技术可以提供这些要求。
3. 生物传感器生物传感器利用生物体内的化学反应或者生物特性来检测生物分子和细胞。
微细加工技术可以用于制造这些传感器。
例如,电子束光刻机可以用来制造生物芯片,这些芯片可以用于生命科学研究和医学诊断。
微细加工技术研究现状
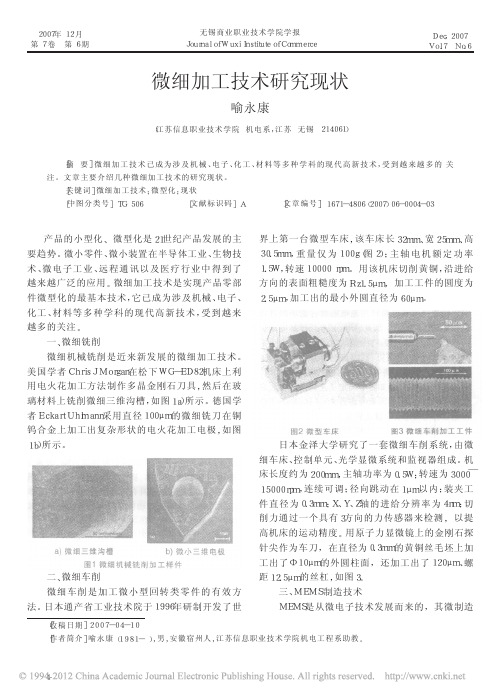
[收稿日期]2007-04-10[作者简介]喻永康(1981-),男,安徽宿州人,江苏信息职业技术学院机电工程系助教。
微细加工技术研究现状喻永康(江苏信息职业技术学院机电系,江苏无锡214061)[摘要]微细加工技术已成为涉及机械、电子、化工、材料等多种学科的现代高新技术,受到越来越多的关注。
文章主要介绍几种微细加工技术的研究现状。
[关键词]微细加工技术;微型化;现状[中图分类号]TG506[文献标识码]A[文章编号]1671-4806(2007)06-0004-03产品的小型化、微型化是21世纪产品发展的主要趋势。
微小零件、微小装置在半导体工业、生物技术、微电子工业、远程通讯以及医疗行业中得到了越来越广泛的应用。
微细加工技术是实现产品零部件微型化的最基本技术,它已成为涉及机械、电子、化工、材料等多种学科的现代高新技术,受到越来越多的关注。
一、微细铣削微细机械铣削是近来新发展的微细加工技术。
美国学者ChrisJMorgan在松下WG-ED82机床上利用电火花加工方法制作多晶金刚石刀具,然后在玻璃材料上铣削微细三维沟槽,如图1a)所示。
德国学者EckartUhlmann采用直径100μm的微细铣刀在铜钨合金上加工出复杂形状的电火花加工电极,如图1b)所示。
a)微细三维沟槽b)微小三维电极图1微细机械铣削加工样件二、微细车削微细车削是加工微小型回转类零件的有效方法。
日本通产省工业技术院于1996年研制开发了世界上第一台微型车床,该车床长32mm、宽25mm、高30.5mm,重量仅为100g(图2);主轴电机额定功率1.5W,转速10000rpm。
用该机床切削黄铜,沿进给方向的表面粗糙度为Rz1.5μm,加工工件的圆度为2.5μm,加工出的最小外圆直径为60μm。
图2微型车床图3微细车削加工工件日本金泽大学研究了一套微细车削系统,由微细车床、控制单元、光学显微系统和监视器组成。
机床长度约为200mm,主轴功率为0.5W;转速为3000 ̄15000rpm,连续可调;径向跳动在1μm以内;装夹工件直径为0.3mm;X、Y、Z轴的进给分辨率为4nm;切削力通过一个具有3方向的力传感器来检测,以提高机床的运动精度。
微纳制造技术的研究现状与发展前景

微纳制造技术的研究现状与发展前景随着科技的不断进步,微纳制造技术逐渐走进大众的视野。
微纳制造技术以其精密、高效、低成本的优秀特性,成为当今制造业的翘楚之一。
它促进了现代科技和产业的飞跃,为人们的生活带来了便利和实惠,也为制造业的可持续发展提供了支撑与保障。
现在,我们不妨深入探索微纳制造技术的研究现状与发展前景。
微纳制造技术的研究现状微纳制造技术主要从三个方面进行研究和实践:微制造技术、纳米制造技术、3D打印技术。
首先是微制造技术。
微制造技术是研究微型部件和微系统的加工和制造技术,主要包括微特种加工、光刻、微电子互连、微加工等。
通常通过微制造技术可以对微细结构进行表面处理、微小元器件组合和器件封装,实现微小化的加工和制造。
其次是纳米制造技术。
纳米级制造主要是研究纳米级尺度领域的干涉、编织、组装、表面处理等技术体系。
纳米级技术除了能作为衍生技术用于各种技术领域外,还重要应用于热、生物、化学和物理领域,可以制造出用于材料催化、纳米传感器、生物医学应用和智能材料等领域的微纳制造底层技术。
最后是3D打印技术,3D打印技术简单来说就是“数字化到现实化”的过程。
它不仅可以制造三维的图案、模型,更重要的是能够制造各种复杂的立体结构,并且可实现高度定制化制造。
由于3D打印技术在生产制造、医疗、航空航天、房屋建筑等领域有着广泛应用和显著优势,目前也是微纳制造技术中最热门的研究方向之一。
微纳制造技术的发展前景微纳制造技术的发展前景是无穷的。
在精密在海量化方面,微纳制造技术比传统的制造工艺具有天然的优势。
目前它在半导体、光电子、通讯、硅基微电子、仪器设备、生物医药、航空航天和军事等领域已经有了广泛的应用,且实际效果也十分出色。
在半导体制造领域,微纳制造技术的重要性越来越大。
随着物联网、云计算、大数据的普及,对集成电路的需求越来越大,微纳制造技术通过小型化件的制造来满足市场需求,随着研究不断深入,未来还会有更多的应用。
在生物医药领域,微纳制造技术的研究不仅可以用于细胞生长,医用材料、药物传输等领域,也可以为人体心血管的治疗提供实施装置,甚至制作出高端仿生假肢,在生物医学领域的应用前景巨大。
探究微细加工技术的发展应用

探究微细加工技术的发展应用微细加工技术是现代加工技术手段的新发展,是二十一世纪关键技术之一。
随着科学技术的发展,近年来在IT、医疗器械以及通讯领域,人们对微小型零件(如:微型传感器、微型加速度计、微透镜阵列等)的需求日益增加。
这种需求的增加促进了微细加工技术的发展。
在目前的多种微细加工技术中,微机电系统(MicroElectroMechanicalSystem,MEMS)一直是主流技术之一。
由于MEMS 技术衍生于微电子技术,它的主要加工对象被限制在硅基材料上,并且工件的几何形状基本上是简单的二维形状,因而只有在大规模集成电路的批量制造等方面才是经济的。
微细切削加工技术,特别是微细铣削作为MEMS技术的补充,由于其几乎不受加工对象材料和几何形状的限制而受到研究人员的重视,正在成为微细加工技术中的新生力量。
一、微细加工的含义微细加工原指加工尺度约在微米级范围的加工方法。
在微机械研究领域中,从尺寸角度,微机械可分为1mm~10mm的微小机械,1μm~1mm的微机械,1nm~1μm的纳米机械,微细加工则是微米级精细加工、亚微米级微细加工、纳米级微细加工的通称。
广义上的微细加工,其方式十分丰富,几乎涉及现代特种加工、微型精密切削加工等多种方式,微机械制造过程又往往是多种加工方法的组合。
从基本加工类型看,微细加工可大致分为四类:分离加工--将材料的某一部分分离出去的加工方式,如分解、蒸发、溅射、切削、破碎等;接合加工--同种或不同材料的附和加工或相互结合加工方式,如蒸镀、淀积、生长等;变形加工--使材料形状发生改变的加工方式,如塑性变形加工、流体变形加工等;材料处理或改性和热处理或表面改性等。
微细加工技术曾广泛用于大规模集成电路的加工制作,正是借助于微细加工技术才使得众多的微电子器件及相关技术和产业蓬勃兴起。
目前,微细加工技术已逐渐被赋予更广泛的内容和更高的要求,已在特种新型器件、电子零件和电子装置、机械零件和装置、表面分析、材料改性等方面发挥日益重要的作用,特别是微机械研究和制作方面,微细加工技术已成为必不可少的基本环节。
- 1、下载文档前请自行甄别文档内容的完整性,平台不提供额外的编辑、内容补充、找答案等附加服务。
- 2、"仅部分预览"的文档,不可在线预览部分如存在完整性等问题,可反馈申请退款(可完整预览的文档不适用该条件!)。
- 3、如文档侵犯您的权益,请联系客服反馈,我们会尽快为您处理(人工客服工作时间:9:00-18:30)。
。 线电极电火花
( 3%*# I’#$+*%$&’ R%,$?&*:# 6*%9;%9:) 磨削技术 3IR6 使 微细加工电极的在线制作、 安装得到较好的解决, 微细 ( E%$*) 2 IRE ) 因此有了迅速发展。 日本 电火花加工 东京大学增泽隆久等人采用微细电火花技术已加工出 直径 "ST / !G 的微细轴和孔径 "/ !G 的微细孔, 可 进行 /11 !G U .11 !G U S11 !G 三维微细轮廓的数控 ( E%$*) 2 OVE ) 电火花铣削加工。 微细激光加工 技术 应用范围广泛、 加工精度及效率高, 便于计算机控制, 是一 种 很 有 发 展 前 景 的 微 细 工 艺。 电 子 束 加 工 ( IVE) 用于小孔、 窄缝、 刻蚀等微细工艺, 加工孔径可 ( <VE ) 达 ". !G, 刻线宽度可达 1T 0 !G。离子束加工 可用于精密微量去除、 离子刻蚀、 离子镀膜等表面改性 ( 1T 110 !G ) , 中, 去除精度可达纳米级 镀膜精度可控 ( E%$*) W’+*&H 制在 0 Q 1T 10 !G。 微细超声加工 W!E
・! ./ ・
!" 电解微细加工机理
! ! 电解加工时, ( 阳极 ) 工件 表面因钝化作用产生的 ( 金属氧化物吸附膜或成相膜 ) 钝化膜 会阻止低电流 ( 在电流效率曲线上, 密度下的电解作用 钝化区电流 H , 密度一般在 ? > HC < S %B 之间) 常规电解加工用较高 的电流密度及高速流动的电解液来消除钝化、 清除电 解产物, 保持电解过程的连续高速进行。 而微细加工 材料去除量微小, 加工精度要求很高, 电解作用必须在 ( 处于效率曲线的钝化区 ) 低电位、 微电流密度下 进 行, 不能采用活性大但杂散腐蚀严重的 M’E( 电解液, 否则用单一电解方式加工时, 工件表面的钝化膜将难 以破坏, 电解作用不能持续进行, 使得单一电解方式在 微细加工中的应用受到限制。 实现电解微细加工必须解决好钝化膜剥落及从加 工区及时清除产物的问题。工件表面的钝化膜虽在单 纯的微电流电解作用下难以消除, 但其强度远低于基 体材料, 如在加工区加上高频振动, 利用电解液的振动 “ 负压空化” ( 必要时可在电解液中加入 冲击波及 作用 极细的微粉磨料 ) 来消除附着在工件表面的钝化膜, 使加工过程连续进行下去, 并可同时改善加工区状态。 基于上述设想, 将高频振动、 脉冲电流同时引入微 (可 电流电解过程中, 使脉冲电流与高频振动的频率 、 高于 HC OGT) 相位相互协调, 当工件与工具阴极相互
・- .. ・
12 国内外研究发展现状
EIE! 器件材料有硅、 金属、 压电材料、 磁性材料、 超导材料、 感光材料、 形状记忆合金等。依托大规模集 成电路工艺基础的硅微细加工技术主要通过光刻及化 学刻蚀得到微小的沟槽、 筋板、 孔洞等结构, 但此工艺 O<64 技术 只限于硅材料。相对于硅材料的微细加工,
!"# $#%#&’()*+ !,#*- ’. /)0,’ 2 (,’0#11)*+ !#0"*’&’+2 34 5’6# 3*- 78’3,3456 789 ( 68&9:;)9: <9;8,+*= >#$?9%$&’ @)’’#:# ,68&9:A?)8/01.11 ,@B5) $%&’()*’ :<9 *#,#&*$? )C +?# ;#D#’)"%9: +*#9; )C E%$*) 2 "*)$#,,%9: +#$?9)’):= &9; F&,%9: )9 +?# G%$*) 2 "*)$#,,H %9: +#$?9)’):= )C EIE! ,J# ,8::#,+ +?&+ 89;#* +?# ’)J ")+#9+%&’ &9; +?# #CC#$+ )9 "&,,%D%+= )C #’#$+*)H $?#G%$&’ &C+#* E%$*) 2 $8**#9+ ;#9,%+= ,J# $&9 8,# +?# ?%:? 2 C*#K8#9$= D%F*&+%)9 #CC#$+ +) *#’#&,# +?# "&,,%D%+= &9; 8,# +?# 9&**)J "8’,# $8**#9+ *)’# )C #’#$+*)’=+%$ &, J#’’ &, +?# ?%:? C*#K8#9$= D%F*&+%)9 C)* *#G)D%9: F);= G&+#*%&’L >?%, $&9 &$$)G"’%,? +?# G%$*) 2 "*)$#,,%9: )C $)G")89; #’#$+*)’=,%, J?%$? %, &’,) & 9#J $)9$#"+ &9; ;#D#’)"%9: +*#9; )C G%$*) 2 "*)$#,,%9: +#$?9)’):=L +,-./(0&:EIE! ;#D%$#,;B%:? 2 C*#K8#9$= M%F*&+%)9;5&**)J N8’,# @8**#9+;E%$*) 2 "*)$#,,%9: )C @)G")89; I’#$+*)’=,%, 现代工业的发展, 要求在有限空间内, 产品具有多 因而对产品小型化、 微型化的要求日益迫切。 种功能, 在航空、 航天、 医疗生物工程、 环境监测、 微型机器人、 传感器等众多领域中的微小机械有广泛应用前景, 计 算机技术、 微电子技术及航空航天等技术的进一步发 展也只有通过微型化和集成化来实现。 微机电系统 ( EIE!) 技术是产品微型化的技术支撑, 基于 EIE! 器件的微细加工技术集合、 交叉了多学科的内容, 是一 个融前沿高技术和工程应用于一体的科学技术体系, 受到国内外广泛重视, 发展非常迅速。因此, 研究国内 外微细加工技术的发展状况, 发掘电解加工机理的优 势, 并将其应用于 EIE! 器件的微细加工中, 目前已 成为一项很有应用前景的研究课题。 ( 制版、 电铸、 注塑 ) 可以对许多金属材料进行微细加 尺寸可小至 0 !G, 精度达亚 !G 级, 已使 EIE! 领 工, 域产生重大进展。但 O<64 技术所需要的深层 P 射线 辐射源价格昂贵, 推广应用受到限制。 而采用电铸工 艺, 不需要同步 P 射线辐射源的准 O<64 技术成为又 一研究热点, 但研究还有待深入
!"#$%&’ (#")*+, 综- 述 ( 可达 !, 级 ) , 接近时为脉冲加电区 退离时为脉冲间 由于电解作用在工件表面产生厚 歇区。加工开始后, 度极薄、 强度远低于基体材料的钝化膜, 利用高频振动 钝化膜破坏后的表面由于电解作用 作用消除钝化膜; 又迅速产生新的钝化膜, 阻止进一步电解, 这样可避免 通常大电流密度电解时产生的杂散腐蚀作用。由于阴 极无损耗的特殊优点, 加工型面将会完全根据阴极形 ( 拷贝式) ( 展成式) 状 或包络轨迹 成形, 而阴极可由线 ( 0123 ) ( 或采用快速 电极电火花磨削 技术在线制作 , 原型 4 精密微细电铸及掩模式刻蚀 ) 这个特点非常 有利于 515! 器件立体型面加工。 由于采用高频脉 “ 负压 冲电流, 电解作用间歇进行, 高频振动冲击波及 空化” 作用能有效、 及时地去除加工区的电解产物, 改 善及加强电解作用。 这种特性对 515! 器件的高深 度比沟槽加工非常重要。这种方式的材料去除是以钝 ( 亚 !6 级 ) , 化膜层为单位 电解钝化与高频振动作用 机理上可保证加工过程中钝化膜产生 消除交替进行, 和去除的协调配合, 解决电解微细加工过程难以持续 使其实用成为可能; 此外, 高频振动冲击及空 的问题, 化作用只起消除钝化膜的作用, 不直接参与去除基体 材料, 所以通过对微能电源参数的控制, 就可能实现微 ( 深度) 细加工速度及去除量 的自动控制。 电解微细加工需采用钝化性电解液, 如浓度 78 9 :8 的 ;&;<. 或 超 纯 水, 不 具 污 染 性, 且在高频振 动、 脉冲电流作用时只需采用静液加工, 不会产生常规 大电流电解加工在工件、 设备、 环境保护方面存在的多 种问题, 便于实现清洁、 绿色制造。 脉冲电源的正极接加工的微器件, 负极接工具阴 极。为了保证加工区电流密度处于电流效率曲线的钝 化区, 脉冲电压幅值 $ 可取 7 9 . = 或更小。将微能电 源的脉冲电压信号通过转换与功率放大电路产生同频 交变电压信号, 输入给压电元件换能器, 使高频振动头 带动阴极作高频振动。 其振幅 % 可由交变电压幅值 调节, 工作台振动频率、 相位与阴极、 工件间的脉冲电 压的频率、 相位协调同步, 保证阴极与工件接近时加脉 ( 如图 : ) , 冲, 分离时为脉冲间隔 即在一个脉冲区间, 钝化膜产生、 钝化消除、 材料去除、 产物排除过程分别 进行一次, 电解则以钝化膜层为单位有条不紊地在小 ( > 7? !6 ) 间隙 下进行。 在脉冲间隔区, 有限的加工 产物在电解液振动冲击波及空化作用下可及时清除, 外部电解液亦可循环更新, 无须泵液系统。 # 微位移伺服工作台发出位置 据 ! 轴深度信息, 给 "、 进行位置调节或三轴运动合成型面展成加 控制指令, 工所需的轨迹。因此, 本试验装置不但可以进行三维 还可以进行展成铣削式型面 型面的拷贝式微细加工, 加工, 可简化微细阴极的制作。