铝矿石成分对氧化铝生产的影响
煅烧生成氧化铝
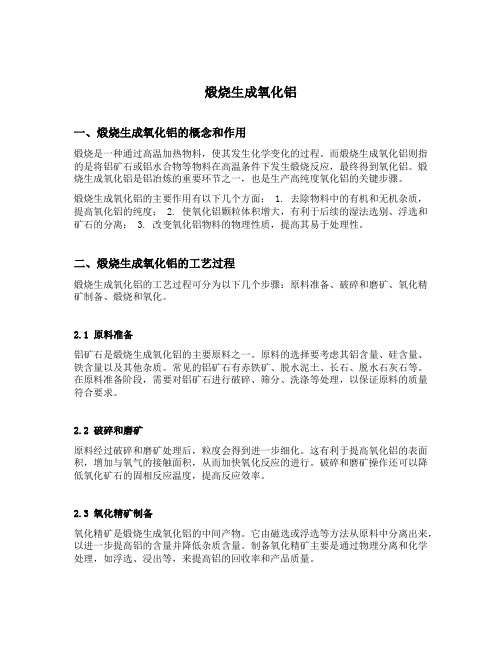
煅烧生成氧化铝一、煅烧生成氧化铝的概念和作用煅烧是一种通过高温加热物料,使其发生化学变化的过程。
而煅烧生成氧化铝则指的是将铝矿石或铝水合物等物料在高温条件下发生煅烧反应,最终得到氧化铝。
煅烧生成氧化铝是铝冶炼的重要环节之一,也是生产高纯度氧化铝的关键步骤。
煅烧生成氧化铝的主要作用有以下几个方面: 1. 去除物料中的有机和无机杂质,提高氧化铝的纯度; 2. 使氧化铝颗粒体积增大,有利于后续的湿法选别、浮选和矿石的分离; 3. 改变氧化铝物料的物理性质,提高其易于处理性。
二、煅烧生成氧化铝的工艺过程煅烧生成氧化铝的工艺过程可分为以下几个步骤:原料准备、破碎和磨矿、氧化精矿制备、煅烧和氧化。
2.1 原料准备铝矿石是煅烧生成氧化铝的主要原料之一。
原料的选择要考虑其铝含量、硅含量、铁含量以及其他杂质。
常见的铝矿石有赤铁矿、脱水泥土、长石、脱水石灰石等。
在原料准备阶段,需要对铝矿石进行破碎、筛分、洗涤等处理,以保证原料的质量符合要求。
2.2 破碎和磨矿原料经过破碎和磨矿处理后,粒度会得到进一步细化。
这有利于提高氧化铝的表面积,增加与氧气的接触面积,从而加快氧化反应的进行。
破碎和磨矿操作还可以降低氧化矿石的固相反应温度,提高反应效率。
2.3 氧化精矿制备氧化精矿是煅烧生成氧化铝的中间产物。
它由磁选或浮选等方法从原料中分离出来,以进一步提高铝的含量并降低杂质含量。
制备氧化精矿主要是通过物理分离和化学处理,如浮选、浸出等,来提高铝的回收率和产品质量。
2.4 煅烧和氧化在煅烧过程中,氧化精矿经过高温煅烧,使其发生氧化反应,生成氧化铝。
煅烧的温度一般在1000~1200摄氏度之间,可以根据不同的原料和生产要求进行调整。
煅烧的时间也是影响煅烧效果的重要参数。
过长或过短的煅烧时间都会影响氧化铝的质量。
氧化反应的化学方程式如下: 2Al(OH)3 -> Al2O3 + 3H2O在煅烧过程中,氧化精矿中的铝水合物逐渐分解,形成二氧化铝,并释放出水蒸气。
铝矿石成分对氧化铝生产的影响

氧化铝质量对铝电解生产的影响

氧化铝质量对铝电解生产的影响生产氧化铝的原料主要是铝土矿,根据矿石的不同,采用的工艺有拜耳法、烧结法和混联法。
国外的铝土矿多为高铝硅比的三水铝石和一水软铝石,通过拜耳法生产出的氧化铝为砂状;而我国可经济应用的铝土矿资源大部分是高铝、高硅、低铁、难溶(铝硅比较低)的中低品位一水硬铝石,通过烧结法或混联法生产出的氧化铝为粉状,并且杂质含量比较高。
标签:氧化铝;物理化学性能;铝电解;电流效率對氧化铝除了要求其具有较高的纯度和稳定的质量外,还要求其具有优良的物理性质:流动性好、强度高、溶解性好、不产生粉尘、具有较高的比表面积等。
1 氧化铝质量对铝电解的影响1.1 氧化铝质量要求氧化铝质量现行有效的国家标准是GB/T24487-2009,其中化学成分为应符合表1的规定。
氧化铝微量元素主要包括V2O5 P2O5 MnO TiO2等。
物理性能主要包括粒度、比表面积、松装密度等项目。
铝电解厂对氧化铝的质量要求,化学成分一般按国家标准,也均能符合,质量差别不大;氧化铝质量的好否更是具体体现在物理性能的优劣,物理性能满足的程度越高氧化铝质量越好,产品越受用户的青睐。
1.2 化学性质的影响影响原铝质量的主要因素是氧化铝的化学纯度,同时铝电解过程的技术经济指标也受到影响。
①氧化钠。
氧化铝产品中的主要杂质是氧化钠,氧化钠含量过高影响电解槽的运行。
当电解质中钠含量增高时,为维持正常的NaF/A1F3值必须多加入氧化铝,造成氟化盐耗费量增加,同时电解槽中电解质的体积也跟着增加。
氧化钠在电解质化学变化和电解槽的传料和工艺控制方面发挥着重要作用;②其他氧化物杂质。
氧化铝中含有的比铝更具正电性的氧化物杂质Fe203、Si02、Ti02等,电解时这些杂质元素首先在阴极上析出而使原铝的质量降低,同时影响电流效率。
1.3 物理性质的影响目前铝电解厂需要氧化铝的物理性能良好,这样可以在电解质中的溶解速度加快,减少槽底沉淀:流动性好,使得自动向电解槽添加和风动输送非常方便:其加料和输送过程中减少飞扬损失,使氧化铝单耗降低,环境得以改善:吸附氟化氢的能力强,改善氧化铝做吸附剂的干法烟气净化的效果:保温性强,在电解质上能够形成良好的结膜,隔绝电解质熔体,减少热流失:有效预防阳极氧化,减少阳极消耗。
氧化铝的生产原理和方法
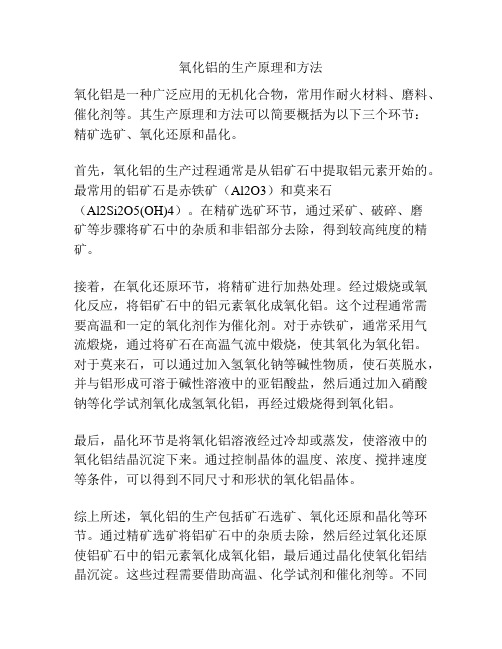
氧化铝的生产原理和方法氧化铝是一种广泛应用的无机化合物,常用作耐火材料、磨料、催化剂等。
其生产原理和方法可以简要概括为以下三个环节:精矿选矿、氧化还原和晶化。
首先,氧化铝的生产过程通常是从铝矿石中提取铝元素开始的。
最常用的铝矿石是赤铁矿(Al2O3)和莫来石(Al2Si2O5(OH)4)。
在精矿选矿环节,通过采矿、破碎、磨矿等步骤将矿石中的杂质和非铝部分去除,得到较高纯度的精矿。
接着,在氧化还原环节,将精矿进行加热处理。
经过煅烧或氧化反应,将铝矿石中的铝元素氧化成氧化铝。
这个过程通常需要高温和一定的氧化剂作为催化剂。
对于赤铁矿,通常采用气流煅烧,通过将矿石在高温气流中煅烧,使其氧化为氧化铝。
对于莫来石,可以通过加入氢氧化钠等碱性物质,使石英脱水,并与铝形成可溶于碱性溶液中的亚铝酸盐,然后通过加入硝酸钠等化学试剂氧化成氢氧化铝,再经过煅烧得到氧化铝。
最后,晶化环节是将氧化铝溶液经过冷却或蒸发,使溶液中的氧化铝结晶沉淀下来。
通过控制晶体的温度、浓度、搅拌速度等条件,可以得到不同尺寸和形状的氧化铝晶体。
综上所述,氧化铝的生产包括矿石选矿、氧化还原和晶化等环节。
通过精矿选矿将铝矿石中的杂质去除,然后经过氧化还原使铝矿石中的铝元素氧化成氧化铝,最后通过晶化使氧化铝结晶沉淀。
这些过程需要借助高温、化学试剂和催化剂等。
不同的原料和条件可以得到不同性质的氧化铝,满足不同领域的应用需求。
氧化铝(Al2O3)是一种重要的无机化合物,具有广泛的应用领域。
其生产原理和方法涉及矿石选矿、氧化还原和晶化等环节,下面将对各个环节进行详细介绍。
首先,精矿选矿是氧化铝生产过程的第一步。
常用的铝矿石有赤铁矿和莫来石等。
赤铁矿是氧化铝的主要矿石,其化学式为Al2O3。
莫来石则是含铝硅酸盐矿石,化学式为Al2Si2O5(OH)4。
在选矿过程中,首先进行采矿,将矿石从地下或地表开采出来。
然后,通过破碎和磨矿等工艺手段,将矿石粉碎成较小的粒度,以方便后续处理。
工业氧化铝生产工艺

工业氧化铝生产工艺工业氧化铝是以铝矿石为原料,通过一系列工艺步骤加工而成的一种重要工业原料。
它具有高熔点、耐磨性强、化学稳定等优点,被广泛应用于电子、陶瓷、玻璃、医药、化工等多个行业中。
下面将介绍一般工业氧化铝的生产工艺。
一、铝矿石的选矿工业氧化铝的原料主要是含铝矿石,如赤铁矿、脱硅赤铁矿、高岭土等。
在选矿过程中,首先需要将矿石经物理或化学方法进行破碎、磨矿,以便提高矿石中的铝含量。
然后通过浮选、重选等方法,将矿石中的非铝矿物分离。
最后,经过干燥、研磨等工艺步骤,得到细粉末的铝酸盐。
二、铝酸盐的烧结将铝酸盐通过烧结工艺进行加热,使其结晶成纯净度较高的氧化铝。
一般的烧结工艺有制砂法、烧结法、酸法等。
制砂法是将铝酸盐粉末与其他辅助原料混合,并通过热处理,使其烧结成球形的粒子。
烧结法是将铝酸盐粉末进行加热,使其结晶成固态的氧化铝颗粒。
酸法是将铝酸盐溶液加入盐酸或硫酸中反应,得到氧化铝沉淀。
三、氧化铝的粉磨和分级经过烧结工艺得到的氧化铝颗粒尺寸较大,需要经过粉磨和分级工艺进行加工,使其具备所需的颗粒粒度和颗粒形状。
粉磨一般采用球磨机、棒磨机等设备,通过不同的研磨介质和研磨时间,使得颗粒变得更加细小。
分级则通过风力或震荡筛进行,将不同尺寸的颗粒分离出来,得到粒度均匀的氧化铝粉末。
四、氧化铝的综合加工得到粉末状的氧化铝后,还需要进行综合加工,以得到符合使用要求的工业氧化铝产品。
一般综合加工工艺包括漂白、除铁、筛分、烘干、包装等环节。
漂白是为了去除粉末中的杂质,提高纯度。
除铁是为了去除粉末中的杂质铁,以免对产品造成影响。
筛分是将粉末分为不同颗粒大小的产品,以满足不同用户的需求。
烘干是为了去除粉末中的水分,提高产品的稳定性和储存期限。
最后,经过包装工艺,将氧化铝产品打包,以便储存和运输。
以上是一般工业氧化铝的生产工艺。
不同的原料和工艺要求可能会有所差异,但总体的流程和步骤大致相同。
工业氧化铝的生产过程需要严格控制各个环节的参数和条件,以确保产品的质量和性能。
氧化铝的生产
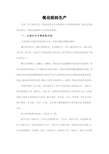
氧化铝的生产目前,生产铝的方法一般是采用先从含铝的矿石中制得氧化铝,然后以氧化铝为原料,用熔盐电解的方法制取金属铝。
一、从铝矿石中提取氧化铝从含铝矿石提取氧化铝的方法,目前有碱法和酸法两种。
碱法有拜尔法、碱石灰烧结法、石灰烧结法、拜尔-烧结联合法、高压水化学法等。
拜尔法一直是生产氧化铝的主要方法,其产量约占全世界氧化铝总产量的90%以上。
酸法有硫酸法、盐酸法、硝酸法。
酸法是用无机酸溶出和处理含铝原料,原料中的氧化硅基本上不与酸反应而留在渣中,得到含铁的铝酸盐酸性水溶液,经除铁净化后的铝盐酸性溶液可通过不同方法得到铝盐水化合物结晶或氢氧化铝结晶,煅烧后得到氧化铝。
酸法主要用于处理粘土、高岭土等高硅低铁含铝原料。
含铝矿物有250余种,其中能用于工业生产的矿物主要是铝土矿、明矾石、霞石和高岭土等。
据统计,2002年,全世界已探明的铝土矿储量约246.9亿吨,储量丰富的主要国家有几内亚、澳大利亚、牙买加、巴西、印度等,其中几内亚、澳大利亚、牙买加、巴西、印度、圭亚那六国的储量约占世界铝土矿总储量的70%。
铝土矿床的赋存状态,大致分为三类:新生代红土型矿床、古生代岩溶型矿床、古生代(或中生代)其他型矿床。
红土型矿床以三水铝石型矿石为主,其次为三水铝石和一水软铝石混合型矿石。
矿石质量较好,以高铁、低硅、高铝硅比(铝和硅之比)为特点,是铝工业的优质原料,主要分布在赤道附近地区的国家,如几内亚、澳大利亚、牙买加、巴西、印度等国家。
岩溶型矿床以一水硬铝石为主,其次为一水硬铝石和一水软铝石混合型矿石。
矿石以高铝、高硅、中低铝硅比为特点。
主要分布在中国、南欧和加勒比海等一些国家。
其他型矿床的矿石类型与岩溶型矿床相似,但矿床规模较小,矿石质量较差,工业意义不大。
在欧、亚大陆及北美东西部有大量分布。
这里主要是介绍碱法生产氧化铝(一)拜尔法拜尔法是奥地利科学家拜尔(K.J.Bayer)于1889年发明的,其原理用苛性钠溶液在高温下溶解铝土矿中的氧化铝,得到铝酸钠溶液。
氧化铝

1.铝土矿是目前氧化铝生产中最主要的原料,主要成分为三氧化二铝二氧化硅三氧化二铁二氧化钛等。
氧化铝主要以三水铝石,一水软铝石或一水硬铝石状态存在,按氧化铝水合物类型可分为三水铝石型,一水软铝石型,一水硬铝石型或各种混合型。
2.衡量铝土矿质量好坏的标准为铝硅比,氧化氯含量,矿物类型。
铝硅比是指矿石中三氧化二铝和二氧化硅含量的百分比。
3.硅量指数是指铝酸钠溶液中是氧化二铝和二氧化硅的质量比4.我国铝土矿的主要特点是高铝高硅低铁的一水硬铝石型铝土矿。
5.生产氧化铝的方法有碱法酸法热法和酸碱联合法,在工业上应用的只有碱法,其重要的中间产物有氯酸钠溶液。
碱法生产有拜耳法,碱石灰烧结法。
拜耳—烧结联合法。
6.拜耳法的两大过程:分解与溶出7.电解炼铝用的氧化铝必须在氧化铝的纯度和氧化铝的物理性质上符合一定的质量要求8.铝酸钠溶液液的分子比是指氯酸钠溶液中氧化钠和三氧化二铝的摩尔比。
他表示氯酸钠溶液的饱和程度和稳定性。
分子比越低过饱和度越大溶液的稳定性越低。
9.拜耳法的循环碱量是指生产一吨氧化铝在循环母液中必须含有的碱量,是循环效率的倒数10.铝酸钠溶液中的碱通常分为苛性碱,碳酸碱和硫酸碱其中苛性碱和碳酸碱的和称为全碱11.铝酸钠溶液的稳定性通常是用从过饱和的氯酸钠溶液开始分解析出氢氧化铝所需的时间长短来衡量。
12.配料量分子比是指预期矿石中三氧化二铝充分溶出时,溶出液所能达到的分子比。
13.铝土矿溶出过程的强化:铝土矿的预处理,添加剂和溶出条件。
14.含硅矿物的危害:引起三氧化二铝和氧化钠的损失;钠硅渣进入氢氧化钠后,降低成品质量;钠硅渣在生产设备和管道上,特别是在换热表面上析出成为结疤,使传热系数打打增加,增加能耗和清理工作量;大量钠硅渣的生成增大赤泥量,并且可能成为极分散的悬浮体,极不利于赤泥的分离和洗涤。
防治措施:预脱硅。
15.溶出过程添加氧化钙的作用:消除了铝土矿中二氧化钛的不良影响,避免了太酸钠的生成;提高三氧化二铝的溶出速度;促进针铁矿转变为赤铁矿;降低碱耗;清楚杂质;改善赤泥的沉降性能。
氧化铝成本构成

氧化铝成本构成氧化铝是一种广泛用于各种工业应用的化学物质,它是由铝矿石经过一系列的化学处理过程制成的。
在这个过程中,氧化铝的成本构成是由多个因素决定的,包括原材料成本、生产过程成本、能源成本、人工成本、运输成本等等。
1. 原材料成本氧化铝的主要原材料是铝矿石,它的价格受到市场供需关系的影响。
铝矿石的价格波动较大,因此原材料成本是氧化铝成本构成中最不稳定的因素之一。
此外,氧化铝生产过程中还需要使用一些辅助原料,如碳酸钠、氢氧化钠等,这些原料的价格也会对氧化铝成本产生影响。
2. 生产过程成本氧化铝的生产过程包括矿石选矿、矿浆制备、氧化还原反应、过滤、洗涤、干燥等多个环节。
每个环节都需要消耗能源和化学药剂,因此生产过程成本是氧化铝成本构成中的重要因素之一。
此外,生产过程中还需要使用大量的设备和机械,这些成本也会对氧化铝成本产生影响。
3. 能源成本氧化铝生产需要大量的能源,包括电力、天然气、燃料油等。
能源成本是氧化铝成本构成中的重要因素之一。
能源价格的波动对氧化铝成本影响较大,因此能源成本的管理和控制对于降低氧化铝成本具有重要意义。
4. 人工成本氧化铝生产需要大量的人力资源,包括工程师、技术人员、操作工等。
人工成本是氧化铝成本构成中的重要因素之一。
人工成本的管理和控制对于降低氧化铝成本具有重要意义。
5. 运输成本氧化铝生产通常需要将产品运输到客户处,因此运输成本也是氧化铝成本构成中的重要因素之一。
运输成本包括物流、运输、保险等多个方面,这些成本对氧化铝成本产生影响。
综上所述,氧化铝成本构成是由多个因素决定的,包括原材料成本、生产过程成本、能源成本、人工成本、运输成本等等。
这些因素的管理和控制对于降低氧化铝成本具有重要意义。
- 1、下载文档前请自行甄别文档内容的完整性,平台不提供额外的编辑、内容补充、找答案等附加服务。
- 2、"仅部分预览"的文档,不可在线预览部分如存在完整性等问题,可反馈申请退款(可完整预览的文档不适用该条件!)。
- 3、如文档侵犯您的权益,请联系客服反馈,我们会尽快为您处理(人工客服工作时间:9:00-18:30)。
铝矿石成分对氧化铝生产的影响1.山西分公司铝土矿资源概况我国铝土矿资源较为丰富,主要集中在山西、河南、贵州、广西四省,总储量23.4亿吨,其中山西省储量为9.89亿吨,占总储量的42%。
截至2005年上半年,山西分公司已取得采矿权的铝土矿区10个,保有资源量7029万吨,其中:A/S 8以上高品位矿1248万吨(占17.76%);A/S 6.5-8的中等品位矿石2253万吨(占32.05%);A/S 6.5以下低品位矿3528万吨(占50.19%),高品位铝矿石较少,主要为中低品位的铝土矿,山西分公司2007年计划供矿:老系统拜耳法A/S≥9.0,AO≥67%,烧结法A/S6.5±0.3,AO≥62%,新系统A/S7.0±0.3 ,AO≥65%。
近年来,我国氧化铝企业为提高产量,降低成本,尽量提高供矿品位,而我国80%以上的铝土矿为中低品位,平均铝硅比仅为5.56,随着高品位铝土矿储量日渐减少,供矿品位不得不下降,结果引起产量减少,碱耗和矿耗指标明显升高,导致成本升高。
因此,需要合理选择供矿品位,深入研究不同铝土矿的性质特点及杂质对氧化铝生产的影响,最大程度地发挥不同品位铝土矿生产氧化铝的效益,有效利用有限的铝土矿资源,成为山西分公司氧化铝生产企业的迫切任务。
2.山西铝土矿化学成分及矿物组成铝土矿是一种组成复杂,化学成分变化很大的矿石。
铝土矿的化学成分主要为Al2O3、SiO2、Fe2O3、TiO2、H2O,次要成分有S、CaO、MgO、K2O、Na2O、CO2、有机质等,微量成分有Ga、Ge、Nb、Ta、TR、Co、Zr、V、P、Cr、Ni等,铝土矿的化学组成及矿物组成取决于铝土矿矿床的成因,根据铝土矿的成因主要有红土型铝土矿和沉积型铝土矿两大类。
红土型铝土矿是最主要的铝土矿矿床,约占铝土矿总储量的92%,以三水铝石为主。
沉积型铝土矿约占铝土矿总储量的8%,以一水硬铝石为主,山西铝土矿属一水硬铝石型,总体特征是高铝、高硅、低硫低铁、中低铝硅比,矿石质量差,加工难度大。
2006年山西分公司140万吨拜耳法实际供矿石化学成分平均为:AL2O3 SiO2 Fe2O3 TiO2 CaO A/S69.6 7.0 3.0 3.3 1.0 9.94AL2O3含量波动范围在65~72%之间,SiO2波动范围在6.0~7.5%之间,Fe2O3含量在2~4%,TiO2含量在3%左右。
矿石A/S11月份最低,为8.94,8月份最高,为10.26,波动范围高达1.32。
主要的矿物组成为:一水硬铝石,高岭石,锐钛矿,赤铁矿,方解石,石英。
2006年矿物组成含量平均为:一水硬铝石高岭石锐钛矿石英方解石赤铁矿76.2 14.2 3.2 1.1 1.15 2.92006年80万吨拜耳法矿石平均化学成份为:AL2O3 SiO2 Fe2O3 TiO2 CaO A/S66.8 8.9 3.5 3.0 1.5 7.50AL2O3含量波动范围在65~68%之间,SiO2波动范围在7.5~10%之间,Fe2O3含量在2~4%,TiO2含量在2.5~3%左右。
主要的矿物组成为:一水硬铝石,高岭石,锐钛矿,赤铁矿,方解石,石英。
矿物组成含量平均为:一水硬铝石高岭石锐钛矿石英赤铁矿72.6 17.2 3.0 1.2 3.5郑州轻研院2006年为80万吨石灰拜耳法矿石所做的物相组成为:一水硬铝石高岭石伊利石锐钛矿石英赤铁矿金红石方解石72.7 11.3 4.7 2.5 2.0 3.2 0.5 0.5从以上矿石物相组成来看,山西矿的主要物相为一水硬铝石和高岭石,两者含量之和超过90%,其余矿物含量较少,杂质硅主要以高岭石形态存在,矿物组成较为单一,但郑州轻研院分析中有少量伊利石存在。
3.铝土矿类型决定氧化铝的生产方法氧化铝生产过程就是从铝矿石中提取氧化铝使之与杂质分离的过程。
自然界中的铝矿石类型很多,同一类型的铝土矿中各种杂质的含量各有差异。
为了最经济地生产氧化铝,不同的铝矿需采用不同的生产方法。
拜耳法只适宜处理高铝硅比矿石,处理低铝硅比铝土矿是不经济的,这是由于矿石中的SiO2在溶出时转变为含水铝硅酸钠,需要消耗昂贵的苛性碱。
低品位铝矿石适宜采用碱—石灰烧结法,这时矿石的SiO2主要转变为原硅酸钙,而且使用和消耗的是廉价的碳酸钠。
特别是我国一水硬铝石型铝硅比低于4的矿石,采用烧结法生产更为有利。
碱—石灰烧结法虽可以处理低铝硅比铝土矿,但能耗高,产品质量差。
混联法可以兼有拜耳法和烧结法的优点,有利于充分利用我国中低品位矿石资源,但其工艺流程复杂,能耗较高。
4.铝土矿中成分及形态对氧化铝生产的影响4.1矿石粒度的影响孝义矿在常规的破碎方式下,具有一定的选择性解理特性,其中粗颗粒矿物的铝硅比明显高于细颗粒矿物的铝硅比,这与组成矿物一水硬铝石、高岭石的物理性质一致,即由于一水硬铝石和高岭石的硬度不同,矿物在相同的作用力方式下,高岭石矿物更容易被破碎进入细粒级产物当中,造成细粒级矿物的铝硅比明显低于粗粒级矿物的铝硅比。
我们从一车间矿石堆场取回孝义高铝矿进行了不同粒度的分析,将其分为细中粗三个粒级,其中,细粒级在小于0.6mm,中粒级5~10mm,粗粒级20~40mm,分析结果如下:中粒矿石5~10mm 8.04 1.46 66.3 1 8.25粗粒矿石20~40mm 3.39 0.87 75.6 0.7 22.3分析结果表明,硬度大的大颗粒的矿石氧化铝含量高,硅含量低,一水硬铝石含量大,A/S高,达到22.3,细颗粒的矿石硅含量较高,A/S低,只有6.59,高岭石的硬度较小,可以看出,粒度越大,A/S 的差值越大。
因此如果矿石均化不好,很容易使矿石的A/S产生一定波动,利用有用矿物与杂质硬度的不同的特点,可以进行筛选,选出一部分高品位的矿石。
目前,我厂进厂矿石粒度在20mm以下,粒度偏大会增加磨矿的负荷,使磨机的产能受到限制,磨矿效率下降,能耗升高,磨矿产品的均匀性变差,对烧结法直接影响料浆细度和烧结熟料的质量。
对拜耳法来说,矿石的粒度越细,表面积越大,溶出速率增加,氧化铝的溶出率提高,不同粒级的矿石溶出效果不同。
下图为不同粒度的山西矿溶出率变化曲线。
从右图中可以看出,各粒级在不同时间的溶出率有明显的差别。
粒级越粗,短时间内效果越差。
由此可见,矿石粒度对氧化铝生产的重要性,为了保证矿石溶出粒级要求,提高磨矿效率,可采用多破少磨的方法降低入磨矿石粒度,提高磨机的产能和产品粒度的均匀性。
设备名称电机功率设计产能电耗原料磨1000KW 50t/h 20kwh/t格子磨1250KW 55 t/h 22.7kwh/t圆锥破碎机280KW 200~280 t/h Max 1.4kwh/t 资料表明,如矿石粒度由-20mm预破至-10mm,需增加300kwh圆锥破碎机一台,可将磨机实际产能由70t/h提高到100t/h,总电耗相应的由17.8降到14.09kwh/t。
对优化磨矿工艺,降低生产能耗起到了积极的作用。
如矿山能直接将矿石粒度破碎至要求粒度,降低的能耗幅度要更大。
经实际考察,要想在原料磨和格子磨入口处添加破碎机,由于自身重量和用电负荷不能承受,添加很困难,是否考虑以后再新建磨机时,在磨头设计添加破碎机,在翻车机后添加破碎机问题较大,一个是很难找到合适的地方,二是破碎飞扬损失会很大,需要更进一步详细的论证。
4.2矿石类型的影响我国一水硬铝石型铝土矿比三水铝石和一水软铝石的氧化铝生产能耗高,主要因为一水硬铝石矿结构致密,一水硬铝石与脉石矿物嵌布紧密,包裹程度较大,与溶液的接触条件较差,很难溶出。
据统计,我厂氧化铝生产综合能耗为33.2GJ/t-AO,而澳大利亚宾加拉厂采用三水铝石矿生产氧化铝综合能耗仅为11.17 GJ/t-AO,希腊圣.尼古拉厂采用一水软铝石矿生产综合能耗14.59 GJ/t-AO。
4.3.矿石中AL2O3含量的影响Al2O3含量越高,对降低铝土矿消耗越有利,我国铝土矿以一水硬铝石居多,但氧化铝含量较高,一般在60-70%,较国外三水铝石矿的消耗小。
对拜耳法来说,矿石Al2O3含量提高1%,铝土矿消耗将降低0.02t/t-AO,流程中的杂质含量相对降低,赤泥量降低,碱耗、能耗降低,对生产的正常运行,指标的优化,起到良好的作用。
对烧结法来说,熟料中Al2O3含量越高,则熟料折合比越低,赤泥量可以减少,设备的负荷可以减轻,产能相应的提高。
但生料中A/S增大时,相对的Fe2O3的含量减少,因此熟料中相应的Na2O·Fe2O3和2CaO·SiO2也减少,导致烧成温度升高,易出现欠烧料。
反之,当A/S降低,物料虽然易烧,但烧成范围缩小,熟料窑操作不好控制,还会造成熟料窑烧结带结圈,下料口堵塞等生产故障。
因此,,在3.0~5.0范围内,熟料铝硅比偏高控制较好。
混联法氧化铝生产中,生料的铝硅比不可能太高。
因为拜耳法赤泥铝硅比只有2.0左右。
如果生料铝硅比太高,则处理一吨拜耳法赤泥要配入大量的矿石。
这样会使混联法生产氧化铝的优越性显著降低。
4.4.铝土矿中杂质SiO2的影响在碱法生产氧化铝的过程中,硅是铝土矿中最有害的杂质,溶出时生成铝硅酸钠,引起铝的损失,增加了碱耗。
资料表明:用拜耳法生产氧化铝,矿石中SiO2每增加1%,每吨矿石多消耗氢氧化钠6.6公斤,氧化铝8.5公斤。
SiO2主要以高岭石状态存在与碱液在70~95℃下就可反应,作用的速度大于一水硬铝石,生成钠硅渣(Na2O.Al2O3.1.7SiO2.2H2O)进入赤泥中,SiO2含量越高,造成Na2OK和Al2O3的损失越大,拜尔法末次洗涤赤泥的N/S约为0.4-0.5,A/S达到1.3以上,即1kg SiO2消耗0.4-0.5 kgNa2O,1kg SiO2消耗1.3kg以上的氧化铝,使氧化铝的回收率降低,产生的赤泥量也相应增大,对赤泥分离洗涤造成不良影响,并在管道和设备器壁上产生结疤,降低传热效果,妨碍生产正常进行,残留在铝酸钠溶液中的SiO2在分解时会随同氢氧化铝一起析出,影响产品质量。
因此,生产过程中要控制和减少SiO2的有害作用在烧结法系统,,二氧化硅主要以原硅酸钙(β-CaO.SiO2)的形式进入赤泥而外排,当SiO2含量升高时,配钙量也增加,资料表明,矿石中SiO2 每增加1%,则多消耗石灰石3.5公斤,增大了赤泥量,对分离、洗涤系统造成一定影响,二次反应程度加大,氧化铝溶出率下降。
矿石中以伊利石(KAI2[(SI·AI)4O10](OH)2·nH2O)形态存在的SiO2含量很少,在180℃以上才与碱液发生明显的反应,难以用预脱硅的方法除去,构成了对预热器传热效率的严重危害,应该了解其溶解性质。