基于CATIA和ANSYS的连杆疲劳分析
基于ANSYS软件对棒球棒的疲劳的有限元分析报告

基于ANSYS软件对棒球棒的疲劳的有限元分析报告一、概述本次大作业主要利用ANSYS软件对棒球棒的疲劳进行分析,计算出棒球棒的最大寿命。
然后与实际情况进行比较,证明分析的正确性,从而为棒球棒的优化分析提供了充分的理论依据,并且通过对ANSYS软件的实际操作深刻体会有限元分析方法的基本思想,对有限元分析方法的实际应用有一个大致的认识。
二、问题分析如下图所示为某棒球棒三维模型,自定义尺寸建立几何模型,材料为铝合金,假设每打一次球,等效在棒球棒端部施加1000N载荷,试分析棒球棒的寿命。
图1 棒球棒三、有限元建模寿命分析之前需要进行强度分析,在Windows“开始”菜单中执行ANSYS—Workbench 命令。
创建项目A,进行静力学分析,双击左侧的static structure即可图 2 强度分析项目如图 3所示,采用材料默认的结构铝合金即可,材料的杨氏模量为7.1e10Pa,泊松比为0.33,密度2770kg/m3,端部黑色部分为护套,采用橡胶材料。
图 3 材料定义双击Geometry进入几何模型建立模块,进行几何建模。
棒球棒为圆周对称模型,所以需要建立截面进行旋转,截面草绘如下:旋转后几何模型如下所示:再在端面建立厚度为2mm的橡胶环,同样通过旋转方式建立,如下所示:进入Workbench进行材料设置,其中螺栓和棒球棒分别设置材料为结构钢。
进行网格划分,设置网格尺寸为2mm,最终有限元网格模型如下图所示:图7 网格设置图8 网格模型模拟实际情况,橡胶外表面固定,棒球棒右端施加1000N载荷,如下图所示图9 载荷约束四、有限元计算结果(1)位移变化,如图12所示,结果最大变形为6.5mm,图12 位移云图(2)等效应力计算结果,如图3所示,最大等效应力为88.015MPa图13 等效应力云图添加Fatigue tool进行疲劳分析,Fatigue设置如下寿命云图如下所示,应力最大区域,寿命最小,该棒球棒最多可以使用1e5次,此后便会发生裂纹破坏。
ansys疲劳分析报告基本方法

疲劳是指结构在低于静态极限强度载荷的重复载荷作用下,出现断裂破坏的现象。
例如一根能够承受 300 KN 拉力作用的钢杆,在 200 KN 循环载荷作用下,经历1,000,000 次循环后亦会破坏。
导致疲劳破坏的主要因素如下:载荷的循环次数;每一个循环的应力幅;每一个循环的平均应力;存在局部应力集中现象。
真正的疲劳计算要考虑所有这些因素,因为在预测其生命周期时,它计算“消耗”的某个部件是如何形成的。
3.1.1 ANSYS程序处理疲劳问题的过程ANSYS 疲劳计算以ASME锅炉和压力容器规范(ASME Boiler and Pressure Vessel Code)第三节(和第八节第二部分)作为计算的依据,采用简化了的弹塑性假设和Mimer累积疲劳准则。
除了根据 ASME 规范所建立的规则进行疲劳计算外,用户也可编写自己的宏指令,或选用合适的第三方程序,利用 ANSYS 计算的结果进行疲劳计算。
《ANSYS APDL Programmer‘s Guide》讨论了上述二种功能。
ANSYS程序的疲劳计算能力如下:对现有的应力结果进行后处理,以确定体单元或壳单元模型的疲劳寿命耗用系数(fatigue usage factors)(用于疲劳计算的线单元模型的应力必须人工输入);可以在一系列预先选定的位置上,确定一定数目的事件及组成这些事件的载荷,然后把这些位置上的应力储存起来;可以在每一个位置上定义应力集中系数和给每一个事件定义比例系数。
3.1.2 基本术语位置(Location):在模型上储存疲劳应力的节点。
这些节点是结构上某些容易产生疲劳破坏的位置。
事件(Event):是在特定的应力循环过程中,在不同时刻的一系列应力状态,见本章 §3.2.3.4。
载荷(Loading):是事件的一部分,是其中一个应力状态。
应力幅:两个载荷之间应力状态之差的度量。
程序不考虑应力平均值对结果的影响。
3.2疲劳计算完成了应力计算后,就可以在通用后处理器 POST1 中进行疲劳计算。
ansys疲劳分析基本方法

疲劳是指结构在低于静态极限强度载荷的重复载荷作用下,出现断裂破坏的现象;例如一根能够承受 300 KN 拉力作用的钢杆,在 200 KN 循环载荷作用下,经历 1,000,000 次循环后亦会破坏;导致疲劳破坏的主要因素如下:载荷的循环次数;每一个循环的应力幅;每一个循环的平均应力;存在局部应力集中现象;真正的疲劳计算要考虑所有这些因素,因为在预测其生命周期时,它计算“消耗”的某个部件是如何形成的;ANSYS程序处理疲劳问题的过程ANSYS 疲劳计算以ASME锅炉和压力容器规范ASME Boiler and Pressure Vessel Code第三节和第八节第二部分作为计算的依据,采用简化了的弹塑性假设和Mimer累积疲劳准则;除了根据 ASME 规范所建立的规则进行疲劳计算外,用户也可编写自己的宏指令,或选用合适的第三方程序,利用 ANSYS 计算的结果进行疲劳计算;ANSYS APDL Programmer‘s Guide讨论了上述二种功能;ANSYS程序的疲劳计算能力如下:对现有的应力结果进行后处理,以确定体单元或壳单元模型的疲劳寿命耗用系数fatigue usage factors用于疲劳计算的线单元模型的应力必须人工输入;可以在一系列预先选定的位置上,确定一定数目的事件及组成这些事件的载荷,然后把这些位置上的应力储存起来;可以在每一个位置上定义应力集中系数和给每一个事件定义比例系数;基本术语位置Location:在模型上储存疲劳应力的节点;这些节点是结构上某些容易产生疲劳破坏的位置;事件Event:是在特定的应力循环过程中,在不同时刻的一系列应力状态,见本章§;载荷Loading:是事件的一部分,是其中一个应力状态;应力幅:两个载荷之间应力状态之差的度量;程序不考虑应力平均值对结果的影响;疲劳计算完成了应力计算后,就可以在通用后处理器 POST1 中进行疲劳计算;一般有五个主要步骤:1、进入后处理 POST1,恢复数据库;2、建立位置、事件和载荷的数目,定义材料疲劳性质,确定应力位置和定义应力集中系数;3、存储不同事件和不同载荷下关心位置的应力,并指定事件的重复次数和比例系数;4、激活疲劳计算;5、查看结果;进入POST1和恢复数据库依照下列步骤进行疲劳计算:1、进入POST1命令:POST1GUI:Main Menu>General Postproc2、把数据库文件读入到在内存中如果所要做的疲劳计算是正在进行的 ANSYS 计算过程的继续,则文件已在内存中;结果文件必须已经存在并将其读入内存; 命令:RESUMEGUI:Utility Menu>File>Resume from建立疲劳计算的规模、材料疲劳性质和疲劳计算的位置定义下列数据:位置、事件和载荷的最大数目;材料的疲劳性质;应力位置与应力集中系数SCFs;1、定义位置、事件和载荷的最大数目缺省情况下,疲劳计算最多包括5个节点位置,10个事件,每个事件中3个载荷;如果需要,可以通过下面的命令来设置较大的规模即较多的位置、事件和载荷; 命令:FTSIZEGUI:Main Menu>General Postproc>Fatigue>Size Settings2、定义材料的疲劳性质为了计算各种耗用系数,以及为了包含简化弹塑性效应,必须定义材料的疲劳性质;在疲劳计算中,感兴趣的材料性质有:S-N 曲线:应力幅Smax -Smin/2-疲劳循环次数的关系曲线;ASME S-N 曲线考虑了最大平均应力的影响;如果需要,应把输入的 S-N 曲线进行调节以便考虑平均应力强度效应;如果不输入S-N曲线,那么对于各种可能的应力状态的组合,应力幅将降序排列,但不计算耗用系数;命令:FPGUI:Main Menu>General Postproc>Fatigue>S-N TableSm-T曲线:设计应力强度值-温度曲线;如要考虑检查应力范围是否进入塑性,就必须定义该曲线;命令:FPGUI:Main Menu>General Postproc>Fatigue>Sm_T Table弹塑性材料参数 M 和 N应变强化指数;只在需要使用简化的弹塑性准则时,才输入 M、N;这些参数可以从 ASME 规范中获得;命令:FPGUI:Main Menu>General Postproc>Fatigue>Elas-plas Par下述例子说明了用于输入疲劳材料性质的FP命令的使用方法:Define the S-N table:FP,1,10,30,100,300,1000,10000 Allowable Cycles, NFP,7,100000,1000000 "FP,21,650,390,240,161,109,59 Alternating Stress-FP,27,37,26 Intensity Range, S, ksiDefine the Sm-T table:FP,41,100,200,300,400,500,600 Temperature, deg FFP,47,650,700,750,800 "FP,51,20,20,20,,, "Design Stress-IntensityFP,57,,, Value", Sm =2/3Sy or1/3 Su, ksiDefine the elastic-plastic material parameters:FP,61,,.3 M and N3、定义应力位置和应力集中系数下面的选项允许用户显式地定义疲劳计算中关心的节点位置、该位置的应力集中系数,以及在该位置的一个短的标题可用20个字母;命令:FLGUI:Main Menu>General Postproc>Fatigue>Stress Locations注意--不是所有的疲劳分析都需要使用FL命令;如果使用FS、FSNODE或FSSECT等命令见下,则疲劳节点位置是自动定义的;假使在建模时包含有足够细的网格,则所计算的应力是准确的,因此不必指定应力集中系数 SCFs 但是如果考虑表面影响、尺寸影响和腐蚀影响,则仍然需要指定 SCFs ;在计算疲劳时如果只需要考察一个位置,则可以省略标题;假使定位明确,或是不需要应力集中系数和标题,则可完全不使用FL命令;这里给出了在一个圆柱筒分析中应用FL命令的例子;整体坐标 Y 轴为旋转轴;在不同璧厚交界处的外壁给出了应力集中系数 SCFs 针对轴向线性化应力; FL,1,281,,,,Line 1 at insideFL,2,285,,,,Line 1 at outsideFL,3,311,,,,Line 2 at insideFL,4,315,,,,Line 2 at outside图3-1 圆柱筒应力集中系数 SCFs储存应力、指定事件循环次数和比例因子储存应力为了进行疲劳计算,程序必须知道每一个位置上不同事件和载荷时的应力,以及每一个事件的循环次数;可采用下列选项来存储每一个位置、事件和载荷组合情况下的应力:人工储存应力;从文件中取得节点应力;横截面应力;警告:程序从不假定存在0应力条件;如果一定要考虑零应力条件,就必须在每一个事件中明确地输入何处产生零应力;下面的命令序列,说明如何存储应力;在某些情况下,用户也可以用LCASE命令代替SET命令;人工储存应力: FS从中取出节点应力: SET,FSNODE横截面应力: PATH,PPATH,SET,FSSECT横截面计算也需从的数据中取得可以用不同的方法在一个事件中储存应力;下面说明各种不同的方法;.1 人工储存应力可以人工存储应力和温度不是直接从的结果文件取得;在这种情况下,实际并没有将 POST1 的疲劳模块作为后处理器,而是仅仅作为疲劳计算器使用;线单元如梁单元的应力必须人工输入,因为疲劳模块不能如体元或壳元那样从结果文件中读取数据;命令:FSGUI:Main Menu>General Postproc>Fatigue>-Store Stresses-Specified Val下面的例子说明用上述命令输入的方式:FS,201,1,2,1,,,,,,FS,201,1,2,7,在这个例子中,只输入了全应力1~6项和温度;如果还要输入线性化应力,它们将紧随在温度后面,即8~13项;注意--对只有轴向应力的梁单元,只需输入一个应力分量SX,其余各项空白;.2 从结果文件中提取应力该方法把包含有6个分量的节点应力向量直接储存在结果的数据库内;随后可以用FS命令修正存入的应力分量;注意--在执行FSNODE命令之前,必须使用SET命令,可能还有SHELL命令;SET命令从数据库的文件中读取某一特殊载荷子步下的结果,SHELL命令可选择从壳单元的顶面、中面或底面读取结果缺省是从顶面读取结果;命令:FSNODEGUI:Main Menu>General Postproc>Fatigue>-Store Stresses-From rst File下面给出用FSNODE命令在一个事件的一个节点位置输入应力结果的例子: SET,1 Define data set for load step 1FSNODE,123,1,1 Stress vector at node 123 assigned to event 1,loading 1.SET,2 Define data set for load step 2FSNODE,123,1,2 ...event 1, loading 2SET,3 ...load step 3FSNODE,123,1,3 ...event 1, loading 3图3-2 一个事件中的三个荷载.3 横截面应力本选项计算和存储截面路径它是由以前的PATH和PPATH命令定义的端点的线性化应力;因为通常线性化应力计算是在能代表两个表面的最短距离的线段上进行的,因此,只需在两个表面上各取一个点来描述PPATH命令中的路径;这一步骤将从计算结果的数据库中获得应力;因此必须在SET命令之前使用FSSECT 命令;用FSSECT命令储存的应力分量可用FS 命令修正;命令:FSSECTGUI:Main Menu>General Postproc>Fatigue> -Store Stresses -At Cross Sect使用FSSECT命令的方法可用下述例子说明;如果节点位置没有在FL命令中指定,则在该例子中命令FSSECT将自动给两个路径节点 391 和 395 设定位置编号;见图3-3;图3-3 在执行 FSSECT 命令之前由 PPATH 命令识别的表面节点列表、显示或删除储存的应力用下列选项对储存的应力进行列表、绘图或删除;1、列出每一个位置、每一个事件、每一种载荷或每一种应力状态下的储存应力:命令:FSLISTGUI:Main Menu>General Postproc>Fatigue>-Store Stresses- List Stresses2、对某一位置和事件,以载荷号的函数来显示应力项:命令:FSPLOTGUI:Main Menu>General Postproc>Fatigue>-Store Stresses- Plot Stresses3、删除储存在某一位置、事件和载荷下的应力状态:命令:FSDELEGUI:Main Menu>General Postproc>Fatigue>-Store Stresses- Dele Stresses4、删除某一位置上的所有应力:命令:FLGUI:Main Menu>General Postproc>Fatigue>Stress Locations 5、删除在某一事件中各种载荷下的所有应力:命令:FEGUI:Main Menu>General Postproc>Fatigue>Erase Event Data设定事件重复次数和比例系数本选项确定事件重复次数对该事件的所有荷载和所有位置;也可对该事件中构成载荷的所有应力施加比例系数;命令:FEGUI:Main Menu>General Postproc>Fatigue>Assign Events下面给出该步骤的一个例子:FE,1,-1 Erase all parameters and fatigue stresses formerlyused for event 1.FE,2,100, Assign 100 occurrences to events 2, 3 and 4,REPEAT,3,1 and scale by .FE,5,500 Assign 500 occurrences to event 5.获得准确的耗用系数结构常常承受各种最大和最小应力,它们发生的顺序是未知的甚至是随机的;因此就必须小心地考虑如何在各种可能的应力范围内,得到正确的重复循环次数,以获得有效的疲劳寿命耗用系数;ANSYS 程序自动计算所有可能的应力范围,同时采用我们通常所知道的“雨流”法记数,跟踪这些应力发生的次数;在选定的节点位置,对所有事件进行搜索,以寻找产生最大应力幅的载荷对应力矢量;记录这些应力幅的重复次数,同时包含这些载荷的事件的剩余重复次数随之减少;最终至少有一个事件在某一位置被“用光”,而属于这一事件的其它应力状态,在随后的过程中将被忽略;这一过程一直进行着,直到所有的应力幅及重复次数都被计及后结束;警告通常容易误用疲劳模块的记数功能;如果需要使疲劳计算得到正确的耗用系数,就必须小心地设计好事件;设计事件时遵循下列规则:1、了解 ANSYS 的内部逻辑记数算法,参见ANSYS Theory Reference§,详细地讲述 ANSYS 程序如何记数;2、由于在三维应力状态,很难预测哪一个载荷步具有极值应力,因此可以对每一个事件采用多个载荷群,以便成功获得极值应力见图3-2;3、如果在某一给定的事件中,只包含一个极值应力,则将获得一个较保守的结果;如果在一个事件中,引入不止一个极值应力,则有时将产生不保守的结果;如下例所示:考察一个加载历程,由两个稍有不同的循环构成:载荷循环1:做 500次循环,Sx = + ~ ksi;载荷循环2:做1000次循环,Sx = + ~ ksi;显然这是应力幅为 50 Ksi的 1500 次循环;然而,如果不小心把这些载荷划分成两个事件,则将导致不正确的记数结果;请看该结果如何:事件1 载荷1: Sx = 500次循环载荷2: Sx =事件2 载荷1: Sx = 1000次循环载荷2: Sx =可能的应力幅是:a、从 E1,L1 到 E1,L2: ksib、从 E1,L1 到 E2,L1: ksic、从 E1,L1 到 E2,L2: ksid、从 E1,L2 到 E2,L1: ksie、从 E1,L2 到 E2,L2: ksif、从 E2,L1 到 E2,L2: ksi把这些应力幅从大到小排列:d、从 E1,L2 到 E2,L1: ksia、从 E1,L1 到 E1,L2: ksif、从 E2,L1 到 E2,L2: ksic、从 E1,L1 到 E2,L2: ksib、从 E1,L1 到 E2,L1: ksie、从 E1,L2 到 E2,L2: ksi则记数将如此:d、从 E1,L2 到 E2,L1 500 次循环 - E1 和 E2 用去500 次循环a、从 E1,L1 到 E1,L2 0 次循环 - E1 已用光f、从 E2,L1 到 E2,L2 500 次循环 - E2 又用去 500 次循环c、从 E1,L1 到 E2,L2 0 次循环 - 两个事件都用光b、从 E1,L1 到 E2,L1 0 次循环 - 两个事件都用光e、从 E1,L2 到 E2,L2 0 次循环 - 两个事件都用光上面记录了 50 ksi 应力幅的 1000 次循环,而不是已知的 1500 次循环;这个错误的结果是由于不恰当的事件组合导致的;假使载荷被描述为各自分离的事件如E1,L1 => E1; E1,L2 => E2; E2,L1 => E3; E2,L2 => E4,则将得到下列的记数范围:d、从E2 到E3 的500次循环,用去 500次循环a、从 E1 到 E2 的 0 次循环,因为E2“用光”了f、从 E3 到 E4 的 500 次循环,E3 又用去500次循环,E4 用去500次循环c、从 E1 到 E4 的 500 次循环,E4 又用去500次循环d、从 E1 到 E3 的 0 次循环,因为E3 “用光”了e、从 E2 到 E4 的 0 次循环,因为 E2 和 E4 都“用光”了;上述情况恰当地记录了累积疲劳损伤被,即 50 ksi 应力幅的 1500 次循环;4、相反,对每一个最大和最小应力条件应用分离的事件,则将使记录变得太保守;在这种情况下,应小心地选择应被一起记数的载荷,将它们划分为同一事件;下面的示例说明一些事件如何才能够包括多个极值应力条件;考虑由两个载荷循环组成的载荷历程:载荷循环1:从 Sx = + 到 + ksi,做 500 次循环载荷循环2:从 Sx = + 到 + ksi,做 1000 次循环显然这些循环的最不利组合为以大约 25 ksi 的应力幅做 500 次循环;在本例中,如果将载荷划分为两个事件,则产生了 25 ksi 范围内进行 500 次循环的正确记录;如每一个载荷作为一个独立的事件,将产生一种过于保守的记录,形成 25 ksi 应力幅的 1000 次循环;激活疲劳计算现在有了位置、应力、事件及所有指定的材料参数,可在指定位置执行疲劳计算;位置的确定可用节点本身,也可用位置编号;命令:FTCALCGUI:Main Menu>General postproc>Fatigue>Calculate Fatig查看计算结果疲劳计算结果被输出在输出窗口;如果你将输出转向/OUTPUT到文件中如,就可打开该文件查看结果;命令:LISTGUI:Utility Menu>List>Files>Other>如果用户已输入 S-N 曲线,则所有部位的应力幅从大到小排列与相应的事件/载荷、使用循环次数、允许循环次数、温度和阶段耗用系数一起以表格形式输出;随后输出累积寿命耗用系数;正如前面提到的,FTCALC输出时,将对任一给定的应力幅显示相应的事件和载荷,这些信息能帮助分离出那些引起最大的疲劳损伤的事件与载荷;修正事件的一个方便的方法是把所有的疲劳数据写入文件中它可以在执行FTCALC命令前或后做;写入文件的数据是疲劳模块的命令流;可通过编辑文件文本文件来修改事件,然后用/INPUT命令重新读入被修改的疲劳命令;命令:FTWRITEGUI:Main Menu>General postproc>Fatigue>Write Fatig Data.其它记数方法前面曾介绍过“雨流”记数法;在时间-载荷历程未知的情况下,这一技术才有用处;如果时间-载荷历程已知,对每一个接连的事件分别做疲劳分析FTCALC,然后人工相加这些耗用系数,则可避免得到不恰当的保守结果;疲劳分析示例命令流方法下面是一个疲劳计算输入命令流:Enter POST1 and Resume the Database:/POST1RESUME,...Number of Locations, Events, and LoadingsFTSIZE,...Material Fatigue Properties:FP,1,.... N valuesFP,21,... S valuesFP,41,... T valuesFP,51,... Sm valuesFP,61,... Elastic-plastic material parametersLocations, Stress Concentration Factors, and Location TitlesFL,...Store Stresses 3 Different MethodsStore Stresses Manually:FS,...Retrieve Stresses from the Results File: SET,...FSNODE,...Store Stresses at a Cross-Section:PPATH,...SET,...FSSECT,...Event Repetitions and Scale FactorsFE,...Activate the Fatigue CalculationsFTCALC,...Review the Results List the output fileFINISH其中的 FTSIZE,FP,FL,FS,FSNODE,PPATH,FSSECT,FE 和FTCALC 命令,请参考ANSYS Commands Reference;ANSYS 疲劳计算以ASME锅炉和压力容器规范ASME Boiler and Pressure Vesse l Code第三节和第八节第二部分作为计算的依据,采用简化了的弹塑性假设和M imer累积疲劳准则; 除了根据 ASME 规范所建立的规则进行疲劳计算外,用户也可编写自己的宏指令,或选用合适的第三方程序,利用 ANSYS 计算的结果进行疲劳计算;ANSYS APDL Programmer‘s Guide讨论了上述二种功能; ANSYS 程序的疲劳计算能力如下:对现有的应力结果进行后处理,以确定体单元或壳单元模型的疲劳寿命耗用系数fatigue usage factors用于疲劳计算的线单元模型的应力必须人工输入;可以在一系列预先选定的位置上,确定一定数目的事件及组成这些事件的载荷,然后把这些位置上的应力储存起来;可以在每一个位置上定义应力集中系数和给每一个事件定义比例系数; 基本术语位置Location:在模型上储存疲劳应力的节点;这些节点是结构上某些容易产生疲劳破坏的位置; 事件Event:是在特定的应力循环过程中,在不同时刻的一系列应力状态,见本章§; 载荷Loading:是事件的一部分,是其中一个应力状态; 应力幅:两个载荷之间应力状态之差的度量;程序不考虑应力平均值对结果的影响;疲劳计算完成了应力计算后,就可以在通用后处理器 POST1 中进行疲劳计算;一般有五个主要步骤: 1、进入后处理 POST1,恢复数据库; 2、建立位置、事件和载荷的数目,定义材料疲劳性质,确定应力位置和定义应力集中系数;3、存储不同事件和不同载荷下关心位置的应力,并指定事件的重复次数和比例系数;4、激活疲劳计算;5、查看结果; 进入POST1和恢复数据库依照下列步骤进行疲劳计算: 1、进入POST1 命令:POST1 GUI:Main Menu>General Postproc 2、把数据库文件读入到在内存中如果所要做的疲劳计算是正在进行的 ANSYS 计算过程的继续,则文件已在内存中;结果文件必须已经存在并将其读入内存; 命令:RESUME GUI:Utility Menu>File>Resume from 建立疲劳计算的规模、材料疲劳性质和疲劳计算的位置定义下列数据:位置、事件和载荷的最大数目;材料的疲劳性质;应力位置与应力集中系数SCFs; 1、定义位置、事件和载荷的最大数目缺省情况下,疲劳计算最多包括5个节点位置,10个事件,每个事件中3个载荷;如果需要,可以通过下面的命令来设置较大的规模即较多的位置、事件和载荷; 命令:FTSIZE GU I:Main Menu>General Postproc>Fatigue>Size Settings 2、定义材料的疲劳性质为了计算各种耗用系数,以及为了包含简化弹塑性效应,必须定义材料的疲劳性质;在疲劳计算中,感兴趣的材料性质有: S-N 曲线:应力幅-疲劳循环次数的关系曲线;ASME S-N 曲线考虑了最大平均应力的影响;如果需要,应把输入的 S-N 曲线进行调节以便考虑平均应力强度效应;如果不输入S-N曲线,那么对于各种可能的应力状态的组合,应力幅将降序排列,但不计算耗用系数; 命令:FP GUI:Main Menu>General Postproc>Fatigue>S-N Table Sm-T曲线:设计应力强度值-温度曲线;如要考虑检查应力范围是否进入塑性,就必须定义该曲线; 命令:FP GUI:Main Menu>General Postproc>Fatigue>Sm_T Ta ble 弹塑性材料参数 M 和 N应变强化指数;只在需要使用简化的弹塑性准则时,才输入 M、N;这些参数可以从 ASME 规范中获得; 命令:FP GUI:Main Menu>General Postproc>Fatigue>Elas-plas Par 下述例子说明了用于输入疲劳材料性质的FP命令的使用方法: Define the S-N table: FP,1,10,30,1 00,300,1000,10000 Allowable Cycles, N FP,7,100000,1000000 " FP,2 1,650,390,240,161,109,59 Alternating Stress- FP,27,37,26 Intensity Range, S, ksi Define the Sm-T table: FP,41,100,200,300,400,500,600 Temperature, deg F FP,47,650,700,750,800 " FP,51,20,20,20,,, " Design Stress-Intensity FP,57,,, Value", Sm =2/3Sy or 1/3 Su, ksi Define the elastic-plastic material parameters: FP,61,,.3 M and N 3、定义应力位置和应力集中系数下面的选项允许用户显式地定义疲劳计算中关心的节点位置、该位置的应力集中系数,以及在该位置的一个短的标题可用20个字母; 命令:FL GUI:Main Menu>General Postproc>Fatigue>Str ess Locations 注意--不是所有的疲劳分析都需要使用 FL 命令;如果使用 F S、FSNODE 或 FSSECT 等命令见下,则疲劳节点位置是自动定义的;假使在建模时包含有足够细的网格,则所计算的应力是准确的,因此不必指定应力集中系数 SC Fs 但是如果考虑表面影响、尺寸影响和腐蚀影响,则仍然需要指定 SCFs ;在计算疲劳时如果只需要考察一个位置,则可以省略标题;假使定位明确,或是不需要应力集中系数和标题,则可完全不使用 FL 命令; 这里给出了在一个圆柱筒分析中应用 FL 命令的例子;整体坐标 Y 轴为旋转轴;在不同璧厚交界处的外壁给出了应力集中系数 SCFs 针对轴向线性化应力;。
ANSYS疲劳分析结果实例

这里有2个事件,2个载荷,ANSYS疲劳分析是通过雨流计数法进行计数的。
首先它会从大到小找出应力幅值。
最大的应力幅值为:事件1的载荷1 和事件1的载荷2 组合
应力幅值= (E1L1-E1L2)/2 = MPa
MPa 对应疲劳曲线上的次数(许用次数7779)
实际循环次数为5次所以损伤系数为5/7779=
第二大的应力幅值为:事件2的载荷1 和事件2的载荷2 组合
应力幅值= (E2L1-E2L2)/2 = MPa
MPa 对应疲劳曲线上的次数(许用次数)
实际循环次数为5次所以损伤系数为=
累积损伤系数为+=<1 符合要求。
这里事件没有交叉组合,比较容易理解,如果事件有交叉的话,使用过
的次数要从实际循环次数中减去,依次求的各种组合的系数,最后相加。
你这个都比较简单了,没考虑弹塑性应变的修正,如果一次加二次应力幅值
超过了3Sm,是要用一个大于1的修正系数对应变幅进行修正,也即对应力幅的修正。
应力幅度不是单纯地用2个载荷组合的结果直接相减再除以2,而是要用6个应力分量
先相减,然后再重新组合成应力强度幅度。
如果事件和载荷很多的话你是没办法直接
用FSNODE从模型存储结果的,要人工存储FS, 总之要深入是件很复杂的事。
很多人认为应力幅就是2个应力直接相减,那是错误的观念,不同载荷主应力方向都
在变化你能直接相减吗得先求得6个分量的幅度,然后在组合成第三强度或者第四强度
的等效应力幅。
ansys公司培训教材疲劳分析

疲劳模块
本章概述
• • 本章将介绍疲劳模块拓展功能的使用:
– 使用者要先学习第4章线性静态结构分析.
培训手朋
ANSYS Workbench – Simulation ANSYS Workbench – Simulation ANSYS Workbench – Simulation ANSYS Workbench – Simulation
– 否则,则称为变化振幅或非恒定振幅 载荷 (本章之后将给予讨论).
February 20, 2004 Inventory #002018 14-4
疲劳模块
… 成比例载荷
•
培训手朋
ANSYS Workbench – Simulation ANSYS Workbench – Simulation ANSYS Workbench – Simulation ANSYS Workbench – Simulation
Availability x x x x x x
February 20, 2004 Inventory #002018 14-11
疲劳模块
… 疲劳程序
•
培训手朋
ANSYS Workbench – Simulation ANSYS Workbench – Simulation ANSYS Workbench – Simulation ANSYS Workbench – Simulation
… 恒定振幅载荷
• 在前面曾提到, 疲劳是由于重复加载 引起:
– 当最大和最小的应力水平恒定时, 称 为恒定振幅载荷. 我们将针对这种最 简单的形式,首先进行讨论.
培训手朋
ANSYS Workbench – Simulation ANSYS Workbench – Simulation ANSYS Workbench – Simulation ANSYS Workbench – Simulation
毕业论文参考-基于ANSYS的连杆应力有限元分析及结构优化
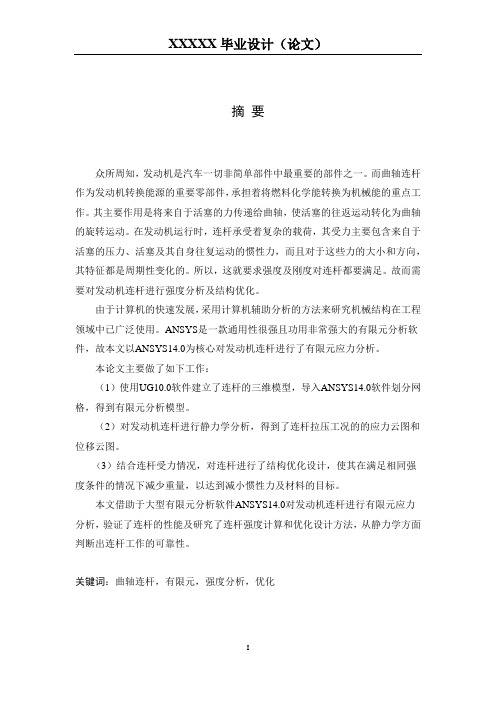
XXXXX毕业设计(论文)摘要众所周知,发动机是汽车一切非简单部件中最重要的部件之一。
而曲轴连杆作为发动机转换能源的重要零部件,承担着将燃料化学能转换为机械能的重点工作。
其主要作用是将来自于活塞的力传递给曲轴,使活塞的往返运动转化为曲轴的旋转运动。
在发动机运行时,连杆承受着复杂的载荷,其受力主要包含来自于活塞的压力、活塞及其自身往复运动的惯性力,而且对于这些力的大小和方向,其特征都是周期性变化的。
所以,这就要求强度及刚度对连杆都要满足。
故而需要对发动机连杆进行强度分析及结构优化。
由于计算机的快速发展,采用计算机辅助分析的方法来研究机械结构在工程领域中已广泛使用。
ANSYS是一款通用性很强且功用非常强大的有限元分析软件,故本文以ANSYS14.0为核心对发动机连杆进行了有限元应力分析。
本论文主要做了如下工作:(1)使用UG10.0软件建立了连杆的三维模型,导入ANSYS14.0软件划分网格,得到有限元分析模型。
(2)对发动机连杆进行静力学分析,得到了连杆拉压工况的的应力云图和位移云图。
(3)结合连杆受力情况,对连杆进行了结构优化设计,使其在满足相同强度条件的情况下减少重量,以达到减小惯性力及材料的目标。
本文借助于大型有限元分析软件ANSYS14.0对发动机连杆进行有限元应力分析,验证了连杆的性能及研究了连杆强度计算和优化设计方法,从静力学方面判断出连杆工作的可靠性。
关键词:曲轴连杆,有限元,强度分析,优化IXXXXX毕业设计(论文)ABSTRACTAs we all know, engine is one of the most important parts of all the complex parts of automobile. Crankshaft connecting rod, as an important part of engine power conversion, undertakes the core task of converting fuel chemical energy into mechanical energy.Its main function is to transfer the force from the piston to the crankshaft, so that the reciprocating motion of the piston can be transformed into the rotating motion of the crankshaft. When the engine works, the connecting rod bears harsh working conditions and complex loads. The force mainly comes from the gas force of the piston, the inertia force of the piston and its reciprocating motion, and the magnitude and direction of these forces show periodic changes. Therefore, it requires the connecting rod to have enough strength and stiffness. Therefore, it is necessary to analyze the strength and optimize the structure of the engine connecting rod.Because of the rapid development of computer, the method of computer aided analysis has been widely used in the field of engineering. ANSYS is a very versatile and powerful finite element analysis software, so this paper takes ANSYS14.0 as the core to carry out finite element stress analysis of engine connecting rod.The main work of this paper is as follows:(1) The three-dimensional model of the connecting rod is established by UG10.0 software, and meshed by ANSYS14.0 software, the finite element analysis model is obtained.(2) Static analysis of engine connecting rod is carried out to check the correctness of finite element model and boundary conditions, and stress nephogram which is in accordance with actual working conditions is obtained.(3) Optimized design of the connecting rod in combination with the force of the connecting rod, so that the weight of the connecting rod can be reduced under theIIXXXXX毕业设计(论文)same strength condition, in order to achieve the purpose of reducing inertial force and material.In this paper, the finite element stress analysis of engine connecting rod is carried out by means of the large-scale finite element analysis software ANSYS14.0. The performance of the connecting rod is verified, the strength calculation and the optimization design method of the connecting rod are studied, and the reliability of the connecting rod is judged from the static aspect.KEY WORDS:crankshaft connecting rod, finite element, strength analysis, optimizationIIIXXXXX毕业设计(论文)目录摘要 (I)ABSTRACT ......................................................................................................................I I 目录 . (IV)第一章绪论 (1)1.1论文研究背景和意义 (1)1.2有限元法研究现状 (1)1.3发动机连杆有限元分析研究现状 (2)1.4本章小结 (3)第二章有限元分析基础 (4)2.1有限元法介绍 (4)2.1.1有限元法发展历史 (4)2.1.2有限元法基本理论 (5)2.1.3有限元法分析步骤 (7)2.2ANSYS软件介绍 (9)2.3本章小结 (9)第三章连杆的受力分析 (10)3.1连杆受载情况及参数 (10)3.1.1连杆受力分析 (10)3.1.2已知参数 (11)3.2燃气压力计算 (11)3.3惯性力计算 (12)IVXXXXX毕业设计(论文)3.5连杆最大压应力工况受力分析 (15)3.6本章小结 (16)第四章连杆应力有限元分析与结构优化 (17)4.1连杆三维模型的建立 (17)4.1.1 UG10.0软件介绍 (17)4.1.2建立连杆三维模型 (18)4.1.3三维模型的简化 (19)4.2有限元模型前处理 (22)4.2.1三维模型的导入 (22)4.2.2材料参数的设定 (24)4.2.2单元类型的选择及网格划分 (25)4.3连杆载荷施加及边界条件 (28)4.3.1连杆载荷处理与分布 (28)4.3.1.1载荷处理 (28)4.3.1.2连杆大小端拉应力加载 (29)4.3.1.3连杆大小端压应力加载 (31)4.3.2连杆位移边界条件的确定 (34)4.4运算及结果分析 (35)4.5连杆结构优化分析 (37)4.6.1连杆优化概述 (37)4.6.2连杆优化分析 (38)4.6本章小结 (40)第五章总结与展望 (41)5.1工作总结 (41)5.2工作展望 (42)参考文献 (44)VXXXXX毕业设计(论文)致谢 (46)毕业设计小结 (47)VIXXXXX毕业设计(论文)第一章绪论1.1论文研究背景和意义以往对发动机的主要组成部件的受力分析,只能靠传统力学计算方法,大致反映这些零件受力状态,因为这些零件受力复杂且形状不规则,比如活塞、连杆、气缸、曲轴等。
基于ANSYS汽车连杆的模态分析

基于ANSYS汽车连杆的模态分析摘要:振动现象是机械结构经常需要面对的问题之一。
由于振动会造成结构的共振或或疲劳,从而破坏结构。
所以必须了解结构固有的频率和振型,避免在实际工况中因振动因素造成结构的损坏。
模态分析主要研究结构或机器部件的结构特性,将得到结构的固有频率和振型,对复杂结构进行精确的模态分析,将为评价现有结构的特性特性、新产品和诊断动态性能的预估及优化设计,提供科学的依据。
关键词:ansys;汽车连杆;模态分析1引言汽车众所周知的最常用的交通工具之一,在整个汽车的复杂系统中,发动机就是其中最重要的之一,常常也称作汽车的心脏。
当汽车发动机工作时,活塞燃烧室产生的气体其爆炸力通过连杆传递给曲轴,曲轴带动飞轮转动从而将动力输出。
在这工作的过程中,发动机连杆在传递燃料爆炸作用力的同时也承受了最大最强烈的冲击力、动态应力,因此,连杆成为发动机动力学负荷最高的部件。
连杆是发动机传递力最重要的零部件之一,同时也肩负着传递力的方向的重任。
所以,汽车发动机连杆的质量和性能就直接关系到整个发动机工作的稳定性以及故障率。
利用有限元对汽车连杆零部件进行模态分析,有利于对连杆零部件更科学的使用。
2基本原理2.1ANSYS简介ANSYS软件是可以处理的分析类型:结构分析、热分析、电磁分析、流体分析、耦合场分析。
结构分析首先待求的自由度是位移,而其他量诸如应变、应力、反应力等均是通过位移值来得到的。
在ANSYS中,结构分析主要包括7种:静力分析、模态分析、谱分析、瞬态动力学分析、谐响应分析、特征屈服分析、专项分析。
而模态分析是本论文的着重应用,主要分析用于计算结构的自然频率和振型,用于解决实际生活中的机械振动。
2.2ANSYS模态分析简介结构动力学分析不同于静力学分析,常用来确定时变载荷对整个结构或部件的影响,同时还要考虑阻尼及惯性效应的作用效果。
模态分析是动力学分析功能的一种。
动力学分析是用来确定质量(惯性)和阻尼起重要作用的结构和构件动力学特性的技术。
抽油机连杆结构疲劳强度优化探讨

抽油机连杆结构疲劳强度优化探讨发布时间:2023-03-20T07:22:19.074Z 来源:《科技新时代》2023年第1期作者:李青松[导读] 以10型抽油机为研究对象,建立有限元模型,通过使用SOLIDWORKS和ANSYS软件,分析连杆结构疲劳性能,结果显示连杆套筒有较大的疲劳断裂隐患李青松大庆油田装备制造集团采油装备制造分公司抽油机总装厂黑龙江大庆163357摘要:以10型抽油机为研究对象,建立有限元模型,通过使用SOLIDWORKS和ANSYS软件,分析连杆结构疲劳性能,结果显示连杆套筒有较大的疲劳断裂隐患。
为提升该结构疲劳特性,并保证不降低使用要求,对连杆套筒做出轻质化处理,在保证抽油机稳定运行的同时,减缓对连杆结构的冲击力,延长疲劳寿命。
关键词:抽油机;连杆结构;疲劳强度;优化改进在我国当前的能源结构体系中,石油作为一种重要的能源,占有至关重要的地位,不仅如此,我国的经济发展也离不开石油的贡献。
石油开采是石油生产过程中的一个重要环节,这个过程主要是靠抽油机实现的,现在应用最为广泛的抽油机是游梁式抽油机,这种抽油机有很多的优点,因此更适合石油开采。
一个完整的抽油机可以分成多个结构部件,各个部件紧密联系,不可或缺,其中任何一个出现故障,抽油机将不能正常工作。
对于游梁式抽油机,其中一个重要组成就是连杆结构,这是因为石油开采的环境一般都较为恶劣,而抽油机长期在这种环境中工作,其连杆结构要在交变荷载下持续工作,对其强度有很大的威胁性,在这种情况下极易造成连杆结构微裂纹,严重时会疲劳断裂,这些都会对采油工作造成极大影响。
因此需要对连杆结构进行力学分析,尤其是疲劳强度,以此为依据优化连杆结构的设计,提高其使用寿命。
1、游梁式抽油机组成分析我国的石油开采过程多采用游梁式抽油机,其主要结构部件有驴头、游梁总成、横梁总成和连杆结构等,各个机械结构都有自己的功能,通过相互配合,实现抽油工作的正常运行。
- 1、下载文档前请自行甄别文档内容的完整性,平台不提供额外的编辑、内容补充、找答案等附加服务。
- 2、"仅部分预览"的文档,不可在线预览部分如存在完整性等问题,可反馈申请退款(可完整预览的文档不适用该条件!)。
- 3、如文档侵犯您的权益,请联系客服反馈,我们会尽快为您处理(人工客服工作时间:9:00-18:30)。
York: Addison-Wesley Publishing Company, 1998.
43
C H I N A
V E N T U R E
C A P I T A L
科技技术应用|TECHNOLOGY APPLICATION
基于 CATIA 和 ANSYS 的连杆疲劳分析
江苏省镇江市学府路江苏大学 唐 鑫
摘 要:本文中应用ANSYS软件对连杆进行有限元分析以得到应力及其分布图。首先连杆的三维模型由CATIA建立并导入ANSYS。根据 ANSYS处理结果,得到应力分布图。通过有限元分析可以针对应力分布情况对连杆的疲劳失效情况进行分析。针对分析结果,最终达到对连杆结 构进行优化的目的。
4. 分析结果 (1) 连杆应力分布是合理的。应力分布平均且正常,几乎 没有应力集中现象出现。 (2) 工作中的极限应力条件下 , 最大应力区域应力符合材料 的极限应力和屈服强度。 所有危险工作区域均符合强度准则。 根 据 连 杆 材 料 的 各 种 参 数 , 18Cr2Ni4WA 极 限 应 力 为 1175MPa 双侧疲劳强度为 507MPa。所以 , 定义 σa=(σ max-
很明显,连杆出于安全状态。 三、优化设计 燃油的减少使得汽车发动机的燃油经济性越来越受到重 视,连杆作为重要的回转件,它的轻量化设计对减少燃油消 耗有着重要的作用。受限于结构和其它因素设定最大厚度为 20mm 最小厚度为 7mm. 所受应力随厚度变化而变化。 优化目标是在符合应力条件的基础上寻找最佳厚度值,如 图 1 所示。优化后得到两个优化候选点,选取一个插入设计点。 从图中可以看到最佳厚度为 10mm. 根据结果建立模型并对模 型进行网格划分和应力分析,如图 2 所示。
σmin)/2 ,σm=(σmax+σmin)/2. 分别以其为横纵坐标做出图 表。图中 ABC 区域即为安全区域。
下表显示连杆单元的应力情况(单位为 Mpa)。
表 1 应力数据
σmax
σmin
σa
σm
1
159.79
-17.996
ห้องสมุดไป่ตู้
88.893
70.897
2
161.75
-35.551
98.651
63.100
图1
图2
四、结论
优化模型是合格的。通过分析和优化,我们在符合强度条
件的基础上得到了最佳的轻量化设计。对减少燃油消耗和提高
排放质量有着重要的影响作用。
参考文献 : [1]刘伟. 连杆的有限元分析[J]. 国际发动机零件, 2011(10) [2]王林.发动机连杆的静态分析[J].科技信息2011(29) [3]Ci Fan, PLD theory and application, Beijing institute of technology press, CN, 2006. [4]岳大兴,液压驱动和气动研究,北京技术研究报, CN, 2006 [5]Craig C C, Adaptive Control of Mechanical Manipulators. New
关键词:连杆; 疲劳分析; CATIA; AYSYS; 优化设计
一、Introduction 连杆是发动机中很重要的一个部件 . 因此对连杆的分析 优化可以很大的提高的发动机性能,是发动机变的更加高效 与节能。本研究用 CATIA 建立连杆的真实三维模型。并运用 ANSYS 强大的有限元分析和优化功能来实现连杆的疲劳分析。 ANSYS 是一款极其强大的有限元分析软件。通过数据接口, ANSYS 可以方便的实现从 CAD 软件中导入实体模型。因此, 将 CATIA 强大的建模功能与 ANSYS 优越的有限元分析功能结 合在一起可以极大地满足设计者在设计过程中对建模与分析的 需求。 二、真实连杆的分析 1. 建立真实三维模型 真实连杆结果复杂,为便于优化分析,对连杆结构进行简 化处理。 (1) 根据应力分布 , 螺纹孔和边缘倒角被合理忽略。 (2) 由于连杆顶端与连杆体间用螺栓相连,因此有限元分 析中,可以将二者看做一个整体。 (3) 连杆体上的空腔和凹槽对应力分析没有重要影响,因 此在建模过程中也忽略。 2. 将 CATIA 中的模型导入 ANSYS 首先将模型保存为 * model 格式。然后打开 ANSYS 进行 一下步骤 : plotctrl-stytle-solid model facets。在优化选项中选择 “fine”选项。最后点击”report”查看结果。 对连杆进行约束以限制其自由度。因为连杆孔尺寸较大, 此处变形量相对较小。因此我们将约束施加于连杆体两侧的端 面使其固定。 连杆材料选为 18Cr2Ni4WA,此种材料的屈服强度和应力 极限为 1127MPa 和 507MPa。 网格尺寸为 5mm. 进行划分得到 网格图。 3. 边界条件 在连杆有限元分析中 , 两岸承受载荷非常复杂 , 特别是连 杆边界应力分布尤为难以分析。 因此 equivalent load 方法被用 来分析应力分布。 当发动机工作时 , 连杆上的载荷有规律的变化,但是没有 必要对每个时刻的连杆状态进行分析,这就是说我们只需要考 虑极限条件即可。它们是由汽油爆炸引起的最大压力时刻和由 压力条件决定最大表面压力时刻。 汽 油 燃 烧 的 瞬 间 , 小 端 压 力 计 算 公 式 为 :P(θ)= Pmax cos(θπ/Ф)。对运动过程中连杆所受压力进行积分运算: