航空发动机叶片增材制造
航空发动机叶片关键技术发展现状分析
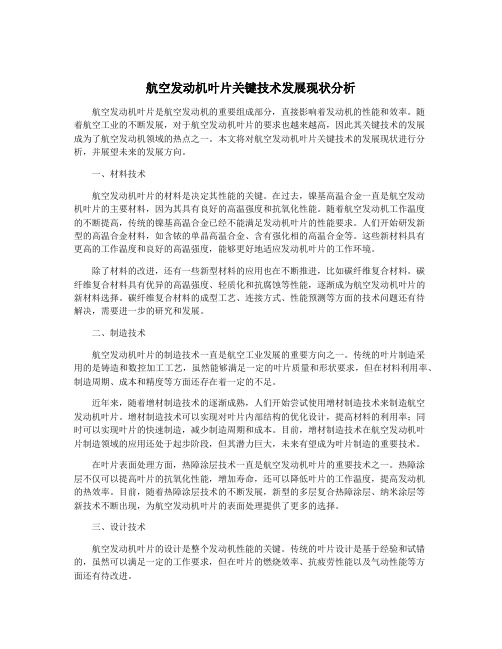
航空发动机叶片关键技术发展现状分析航空发动机叶片是航空发动机的重要组成部分,直接影响着发动机的性能和效率。
随着航空工业的不断发展,对于航空发动机叶片的要求也越来越高,因此其关键技术的发展成为了航空发动机领域的热点之一。
本文将对航空发动机叶片关键技术的发展现状进行分析,并展望未来的发展方向。
一、材料技术航空发动机叶片的材料是决定其性能的关键。
在过去,镍基高温合金一直是航空发动机叶片的主要材料,因为其具有良好的高温强度和抗氧化性能。
随着航空发动机工作温度的不断提高,传统的镍基高温合金已经不能满足发动机叶片的性能要求。
人们开始研发新型的高温合金材料,如含铱的单晶高温合金、含有强化相的高温合金等。
这些新材料具有更高的工作温度和良好的高温强度,能够更好地适应发动机叶片的工作环境。
除了材料的改进,还有一些新型材料的应用也在不断推进,比如碳纤维复合材料。
碳纤维复合材料具有优异的高温强度、轻质化和抗腐蚀等性能,逐渐成为航空发动机叶片的新材料选择。
碳纤维复合材料的成型工艺、连接方式、性能预测等方面的技术问题还有待解决,需要进一步的研究和发展。
二、制造技术航空发动机叶片的制造技术一直是航空工业发展的重要方向之一。
传统的叶片制造采用的是铸造和数控加工工艺,虽然能够满足一定的叶片质量和形状要求,但在材料利用率、制造周期、成本和精度等方面还存在着一定的不足。
近年来,随着增材制造技术的逐渐成熟,人们开始尝试使用增材制造技术来制造航空发动机叶片。
增材制造技术可以实现对叶片内部结构的优化设计,提高材料的利用率;同时可以实现叶片的快速制造,减少制造周期和成本。
目前,增材制造技术在航空发动机叶片制造领域的应用还处于起步阶段,但其潜力巨大,未来有望成为叶片制造的重要技术。
在叶片表面处理方面,热障涂层技术一直是航空发动机叶片的重要技术之一。
热障涂层不仅可以提高叶片的抗氧化性能,增加寿命,还可以降低叶片的工作温度,提高发动机的热效率。
目前,随着热障涂层技术的不断发展,新型的多层复合热障涂层、纳米涂层等新技术不断出现,为航空发动机叶片的表面处理提供了更多的选择。
航空发动机叶片再制造技术的应用及其发展趋势

航空发动机叶片再制造技术的应用及其发展趋势航空发动机叶片再制造技术是指对废旧的航空发动机叶片进行修复、再制造或更新的技术,以降低航空发动机的维修成本、延长使用寿命,并提高发动机的性能和可靠性。
这一技术在航空领域中具有重要意义,能够进一步推动航空发动机的发展与创新。
1.修复与再制造:通过对叶片进行修复和再制造,使其恢复到原有性能水平,以减少修复成本和提高使用寿命。
修复过程中主要包括清洗、去除受损材料、填充修补、表面处理等步骤,再制造则涉及到材料选择、加工和热处理等工艺。
通过修复和再制造,航空发动机叶片的性能可以恢复到几乎与新制品相当。
2.更新与改进:利用再制造技术,对旧有叶片进行更新和改进,以提高性能和可靠性。
例如通过采用新材料、改变叶片结构、优化叶片内部流道等方式,实现对叶片性能的提升。
这样可以延长航空发动机的使用寿命,提高发动机的性能指标,同时降低运营成本。
3.节能环保:再制造技术对航空工业的发展有着重要意义。
航空发动机叶片是航空发动机中易受损的关键部件,采用再制造技术可以降低其对环境的影响。
通过再制造,可以避免废旧叶片的填埋和焚烧,减少对环境的污染,同时还可节约大量原材料和能源的消耗。
1.材料创新:新型材料的研发将是航空发动机叶片再制造技术的重要发展方向。
高温合金、复合材料等新材料的应用可以提高叶片的耐用性、抗疲劳性和耐高温性能,从而延长其使用寿命。
2.进一步精细化加工:随着精密制造技术的不断发展,航空发动机叶片再制造将越来越具有精细化的特点。
高精度加工和表面处理技术的应用可以进一步提高叶片的空气动力性能和剩余寿命,实现优化再制造。
3.数字化技术的应用:随着数字化技术的飞速发展,航空发动机叶片再制造也将借助于数字化技术的应用实现更高效、更精准的再制造。
通过建立叶片的数字模型、使用虚拟仿真技术和智能制造技术,可以提高制造过程的一体化和智能化水平。
4.航空维修市场的需求:全球航空业的持续发展将对航空发动机叶片再制造技术提出更高的要求。
航空发动机部件增材制造修复工艺及质量检测

航空发动机部件增材制造修复工艺及质量检测航空发动机部件增材制造修复工艺及质量检测是航空工业中的一个重要领域。
增材制造修复工艺是指利用3D打印等技术对损坏的航空发动机部件进行修复的方法。
它可以将金属材料逐层添加或熔化,将部分或整个部件复原到设计要求的尺寸和形状。
以下是航空发动机部件增材制造修复工艺及质量检测的一般步骤和关键点:1. 损伤评估:对损坏的部件进行彻底的评估和分析,确定修复的可行性和必要性。
这包括对损伤的类型、大小、位置和严重程度进行检查和记录。
2. 设计修复方案:根据损伤评估结果,设计适当的修复方案。
这包括确定修复区域、修复方式、修复材料等。
3. 工艺规划:制定增材制造修复的详细工艺规划。
这包括选择合适的增材制造设备和参数,确定部件的分层加工路径和能源输入方式。
4. 制造修复:根据工艺规划,进行增材制造修复过程。
这可能涉及到激光熔化、电子束熔化、电弧增材制造等技术,根据需要进行适当的预热、后处理和热处理等工艺步骤。
5. 完成加工和后处理:对修复部件进行机械加工、表面处理和热处理等工艺,以满足设计要求的尺寸、形状和性能。
6. 质量检测:对修复部件进行全面的质量检测和评估。
这包括非破坏性检测(如超声波、X射线、磁粉检测等)、金相显微镜分析、机械性能测试等。
7. 质量控制和认证:建立合适的质量控制体系,确保修复部件符合相关标准和要求。
对修复部件进行认证和授权,以确保其安全可靠性。
航空发动机部件增材制造修复工艺及质量检测需要综合考虑材料特性、工艺参数、设备性能和修复部件的使用环境等因素。
通过严格的修复工艺和质量检测,可以保证修复部件的性能和可靠性,延长航空发动机的使用寿命,减少航空公司的成本和维修时间。
航空发动机叶片材料及制造技术现状
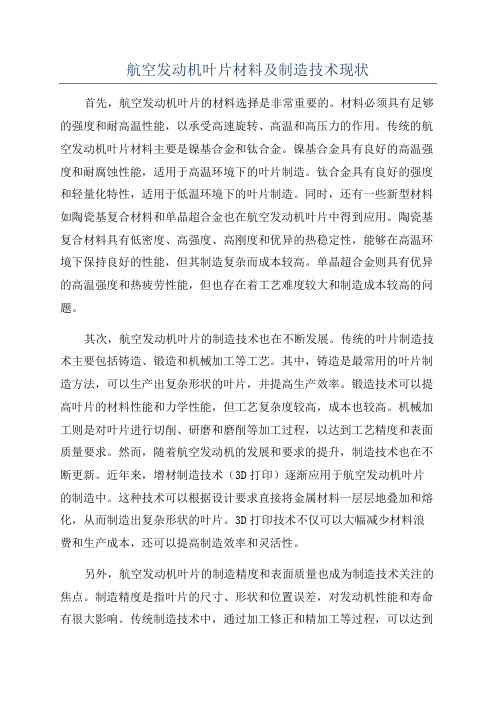
航空发动机叶片材料及制造技术现状首先,航空发动机叶片的材料选择是非常重要的。
材料必须具有足够的强度和耐高温性能,以承受高速旋转、高温和高压力的作用。
传统的航空发动机叶片材料主要是镍基合金和钛合金。
镍基合金具有良好的高温强度和耐腐蚀性能,适用于高温环境下的叶片制造。
钛合金具有良好的强度和轻量化特性,适用于低温环境下的叶片制造。
同时,还有一些新型材料如陶瓷基复合材料和单晶超合金也在航空发动机叶片中得到应用。
陶瓷基复合材料具有低密度、高强度、高刚度和优异的热稳定性,能够在高温环境下保持良好的性能,但其制造复杂而成本较高。
单晶超合金则具有优异的高温强度和热疲劳性能,但也存在着工艺难度较大和制造成本较高的问题。
其次,航空发动机叶片的制造技术也在不断发展。
传统的叶片制造技术主要包括铸造、锻造和机械加工等工艺。
其中,铸造是最常用的叶片制造方法,可以生产出复杂形状的叶片,并提高生产效率。
锻造技术可以提高叶片的材料性能和力学性能,但工艺复杂度较高,成本也较高。
机械加工则是对叶片进行切削、研磨和磨削等加工过程,以达到工艺精度和表面质量要求。
然而,随着航空发动机的发展和要求的提升,制造技术也在不断更新。
近年来,增材制造技术(3D打印)逐渐应用于航空发动机叶片的制造中。
这种技术可以根据设计要求直接将金属材料一层层地叠加和熔化,从而制造出复杂形状的叶片。
3D打印技术不仅可以大幅减少材料浪费和生产成本,还可以提高制造效率和灵活性。
另外,航空发动机叶片的制造精度和表面质量也成为制造技术关注的焦点。
制造精度是指叶片的尺寸、形状和位置误差,对发动机性能和寿命有很大影响。
传统制造技术中,通过加工修正和精加工等过程,可以达到较高的制造精度。
而3D打印技术可以根据设计要求直接打印出精密的叶片,可以实现更高的制造精度。
叶片的表面质量是指叶片的光洁度和粗糙度等表面特性。
传统制造技术中,通常需要通过机械加工和抛光等过程来改善叶片的表面质量。
航空发动机叶片制造及再制造技术研究
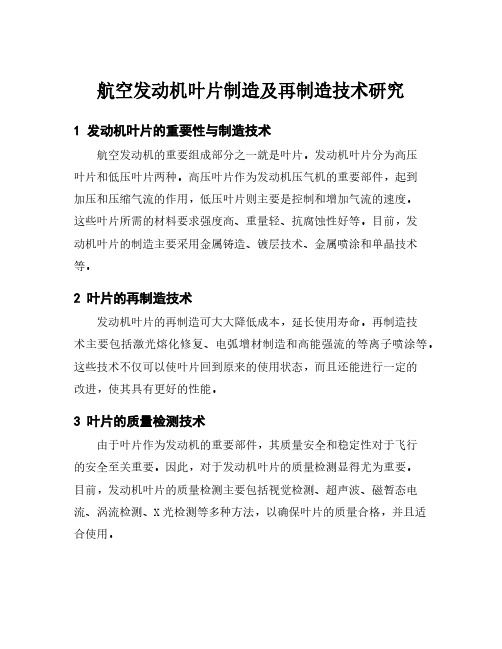
航空发动机叶片制造及再制造技术研究
1 发动机叶片的重要性与制造技术
航空发动机的重要组成部分之一就是叶片。
发动机叶片分为高压
叶片和低压叶片两种。
高压叶片作为发动机压气机的重要部件,起到
加压和压缩气流的作用,低压叶片则主要是控制和增加气流的速度。
这些叶片所需的材料要求强度高、重量轻、抗腐蚀性好等。
目前,发
动机叶片的制造主要采用金属铸造、镀层技术、金属喷涂和单晶技术等。
2 叶片的再制造技术
发动机叶片的再制造可大大降低成本,延长使用寿命。
再制造技
术主要包括激光熔化修复、电弧增材制造和高能强流的等离子喷涂等。
这些技术不仅可以使叶片回到原来的使用状态,而且还能进行一定的
改进,使其具有更好的性能。
3 叶片的质量检测技术
由于叶片作为发动机的重要部件,其质量安全和稳定性对于飞行
的安全至关重要。
因此,对于发动机叶片的质量检测显得尤为重要。
目前,发动机叶片的质量检测主要包括视觉检测、超声波、磁暂态电流、涡流检测、X光检测等多种方法,以确保叶片的质量合格,并且适
合使用。
发动机叶片是一个复杂的工艺要求高的零部件,需要不断研究和探索,以提高其质量和稳定性,确保飞行的安全。
对于发动机叶片的制造和再制造技术的研究如今已经非常成熟,但其在未来的发展和研究仍会是一个不断探索和突破的领域。
飞机发动机零部件粉末床融合增材制造工艺-概述说明以及解释
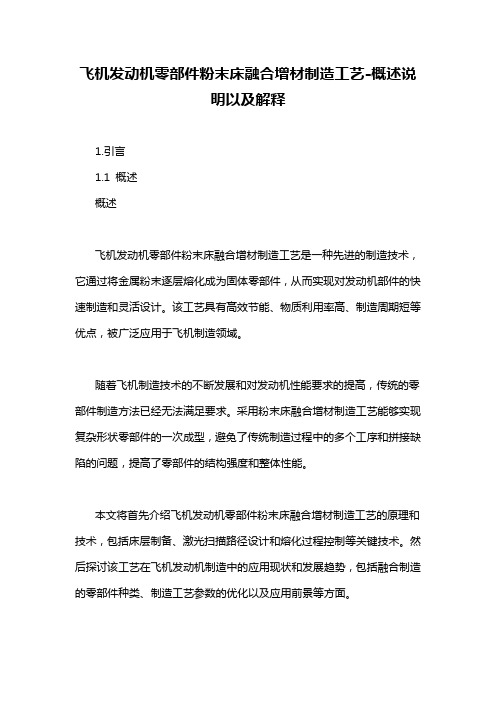
飞机发动机零部件粉末床融合增材制造工艺-概述说明以及解释1.引言1.1 概述概述飞机发动机零部件粉末床融合增材制造工艺是一种先进的制造技术,它通过将金属粉末逐层熔化成为固体零部件,从而实现对发动机部件的快速制造和灵活设计。
该工艺具有高效节能、物质利用率高、制造周期短等优点,被广泛应用于飞机制造领域。
随着飞机制造技术的不断发展和对发动机性能要求的提高,传统的零部件制造方法已经无法满足要求。
采用粉末床融合增材制造工艺能够实现复杂形状零部件的一次成型,避免了传统制造过程中的多个工序和拼接缺陷的问题,提高了零部件的结构强度和整体性能。
本文将首先介绍飞机发动机零部件粉末床融合增材制造工艺的原理和技术,包括床层制备、激光扫描路径设计和熔化过程控制等关键技术。
然后探讨该工艺在飞机发动机制造中的应用现状和发展趋势,包括融合制造的零部件种类、制造工艺参数的优化以及应用前景等方面。
通过对飞机发动机零部件粉末床融合增材制造工艺的研究和应用,可以提高飞机的整体性能和可靠性,实现对零部件性能和质量的精确控制。
同时,该工艺也具有很大的经济效益和环境效益,能够提高制造效率,降低能源消耗和废料产生。
在未来,飞机发动机零部件粉末床融合增材制造工艺有望进一步发展,推动飞机制造技术的革新和升级。
随着材料科学和工艺技术的不断进步,相信该工艺在飞机制造领域的应用前景将更加广阔,为飞机制造产业的发展提供了新的思路和解决方案。
1.2 文章结构文章结构部分的内容可以描述整篇文章的组织结构和内容安排,包括各个章节的主题和内容概述。
以下是一个可能的编写内容:文章结构:本篇文章主要分为引言、正文和结论三个部分,具体结构安排如下:1. 引言在引言部分,将会对飞机发动机零部件粉末床融合增材制造工艺进行概述,介绍其重要性和应用领域。
同时,还会简要介绍本文的结构和目的,为读者提供整体的内容框架。
2. 正文正文部分将分为两个主要章节:飞机发动机零部件粉末床融合增材制造工艺的原理和技术以及其应用与发展。
航 空 发 动 机 叶 片 涂 层

航空发动机叶片涂层技术一.涡轮叶片是先进航空发动机核心关键之一航空发动机被称为现代工业“皇冠上的明珠”,航空发动机是飞机的“心脏”,价值一般占到整架飞机的20%-25%。
目前,能独立研制、生产航空发动机的国家只有美、英、法、俄、中5个。
但是,无论“昆仑”、“秦岭”发动机、还是“太行”系列,我国航空发动机的水平距离这一领域的“珠穆朗玛”依然存在不小的差距。
美、俄、英、法四个顶级“玩家”能够自主研发先进航空发动机。
西方四国由于对未来战场与市场的担忧,在航空发动机核心技术上一直对中国实施禁运和封锁。
技术难关有很多。
本人认为涡轮叶片是先进航空发动机的核心技术之一。
随着航空航天工业的发展,对发动机的性能要求越来越高,要使发动机具有高的推重比和大的推动力,所采用的主要措施是提高涡轮进口温度。
国外在20世纪90年代,要求涡轮前燃气进口温度达1850-1950K。
美国在IHPTET计划中要求:在海平面标准大气条件下,航空燃气涡轮机的的涡轮进口温度高达2366K。
涡轮进口温度的提高要求发动机零件必须具有更高的抗热冲击、耐高温腐蚀、抗热交变和复杂应力的能力。
对于舰载机,由于在海洋高盐雾环境下长期服役,要求发动机的叶片的耐腐蚀性更高;常在沙漠上飞行的飞机,发动机的叶片要具有更好的耐磨蚀。
众所周知:镍基和钴基高温合金具有优异的高温力学和腐蚀性能,广泛用于制造航空发动机和各类燃气轮机的涡轮叶片(blade and vane)。
就材质来看:各国的高温合金型号虽各不相同,但就相近成分的高温合金来说,其性能相近(生产工艺方法不同有也造成性能有大的差异)。
好的高温合金的使用温度也只有1073K左右,为达到前面所说的要求温度,采用的方法有二:一是制成空心的叶片。
空心叶片自20世纪60年代中期出现以来,经历了对流冷却、冲击冷却、气膜冷却以及综合冷却的发展历程,使进气口温度高出叶片材料约300—500℃,内腔的走向复杂化和细致化。
这一步的改进仍难满足需要,且英国发展计划将取消冷却。
先进航天发动机叶片材料

先进航天发动机叶片材料先进航天发动机叶片材料的研究与开发,是航天航空技术领域的一个重要方向。
航天发动机的叶片材料需要具备高温抗氧化、高强度、低密度、高刚度等特点,以满足航天器在极端工作环境下的要求。
近年来,随着航天技术的不断发展,对航天发动机叶片材料的要求也越来越高,因此针对这些要求,科学家们进行了大量的研究工作。
目前,常用于航天发动机叶片材料的有镍基合金、钛基合金和复合材料等。
镍基合金具有良好的高温抗氧化性能和高强度,广泛用于航空发动机叶片材料。
钛基合金在高温和高强度方面具有优良的性能,尤其适用于航天飞行器中的高温燃气轮机叶片材料。
复合材料则以其低密度、高强度和良好的热稳定性,在航天三维推进系统中得到了广泛应用。
镍基合金是当前航天发动机叶片材料中使用最广泛的一类。
镍基合金具有优异的高温抗氧化性能、高强度和高热蠕变强度,并且在高温环境中具有良好的抗腐蚀性能。
此外,镍基合金还具有良好的可加工性和焊接性能,使其成为最常用的航天发动机叶片材料。
然而,传统的镍基合金在高温下容易发生热疲劳,这限制了其在航天发动机中的使用。
为了克服传统镍基合金的缺点,科学家们提出了许多改进的镍基合金材料。
例如,含有微量添加元素的高温合金,在提高镍基合金的高温强度和耐热性能的同时,还能够减轻材料的热蠕变损伤。
此外,也有研究人员提出了采用股状晶粒结构的大晶粒镍基合金,该结构能够阻止晶粒细化和晶界破坏,从而提高材料的高温持久性能。
钛基合金是另一类常用于航天发动机叶片材料的材料。
由于钛基合金具有低密度、高强度和优良的高温性能,因此被广泛应用于航天飞行器的高温燃气轮机叶片材料中。
钛基合金可以分为α+β型和β型两类,其中β型钛基合金具有优异的高温强度和低温塑性,因此在高速航空领域具有很大的潜力。
除了镍基合金和钛基合金,复合材料也在航天发动机叶片材料的研发中发挥着重要的作用。
复合材料以其低密度、高强度和良好的热稳定性而受到广泛关注。
目前,复合材料在航空航天领域中的应用主要是碳纤维增强复合材料。
- 1、下载文档前请自行甄别文档内容的完整性,平台不提供额外的编辑、内容补充、找答案等附加服务。
- 2、"仅部分预览"的文档,不可在线预览部分如存在完整性等问题,可反馈申请退款(可完整预览的文档不适用该条件!)。
- 3、如文档侵犯您的权益,请联系客服反馈,我们会尽快为您处理(人工客服工作时间:9:00-18:30)。
航空发动机叶片增材制造调查报告
总体来说,有这样几种可行性方向。
一、工艺方向,包括整体增材制造或者表面增材强化:
1. 整体增材制造:使用3d打印代替传统加工工艺,整体打印。
目前可行的3d打印技术包括:
FDM:熔融沉积(Fused Deposition Modeling)
SLM:选择性激光熔融技术(Selective Laser Melting)
SLS:选择性激光烧结成型法(Selective Laser Sintering)
DMLS:直接金属激光烧结(Direct Metal Laser Sintering)
LMD:激光金属沉积(laser metal deposition)
相比于熔模铸造,增材制造具有的优势多于劣势,因此具有较大研究价值。
如何解决增材制造新工艺存在的技术弱点正是需要研究的方向。
总结有如下几点:
①强度问题:目前最常用为镍基合金增材,使用何种材料可提升强度?
②精度问题:粘结剂喷射,然后是适当的烧结和表面处理是一种很有前途的合金制造工艺
[1],如何进一步提升表面精度?
③温度问题:3d打印叶片目前只是在常温叶片制造上有一些应用,针对于航空发动机涡轮的耐高温叶片(1400-1700℃)则鲜有研究。
需要解决问题包括:除镍基合金外,打印粉末采用何种耐高温材料(金属、非金属、复合材料[2])?最佳的高温合金打印方法是哪一种?
④建立模型:建立增材制造叶片的收缩模型、疲劳模型、力学模型等。
2.表面增材强化:使用激光熔覆或等离子喷涂,在已有叶片表面上增加强化散热层,叶片为多层结构。
(滕海灏)
二、产品方向,叶片结构智能化和新材料应用。
目前叶片结构如下图所示[3],采用熔模铸造的工艺方案,其优缺点见上表。
如前所述,如果采用3d打印工艺加工这种空心叶片结构将会实现多方面的优化。
就产品本身而言,可以在如下方面进行研究。
图1 图2
1、叶片结构智能化(4d打印)
如图2,这是风力发电机叶片结构[3],利用仿生学模仿植物脉络,将单一叶片材料更新为主动(智能)材料和被动材料两种,又称为“4d打印”。
这种新型结构采用PLA作为主动材料,利用其热响应机制实现根据外力“自适应”调整自身形状。
因此实现了叶片的智能化,提升了发电效率,另外还具有消除噪音、增强散热效果、取消叶片传感器等优点。
这种新型叶片由“硬”变“软”实现了结构的革命。
但是,目前这种结构仅仅针对于常温材料的叶片结构,高温工作叶片则鲜有报道。
因此,将此结构应用于航空涡轮的高温叶片是否可行?
2、叶片新材料
如果采用上述智能结构应用于高温工作叶片,采用何种材料作为主动材料(记忆合金?纳米材料?)、何种作为被动材料,是否采用上述仿生结构,或者采用其它植物结构,如棕榈树、橡树等[4]。
如果高温合金结构无法实现软质智能化结构,也可以采用加强筋结构提升叶片强度,这种结构很难通过传统工艺实现,只能依靠3d打印工艺实现。
参考文献
[1]Amir Mostafaei,Characterizing surface finish and fatigue behavior in binder-jet 3D-printed nickel-based superalloy 625,Additive Manufacturing 24 (2018) 200–2
[2]航空发动机复合材料叶片设计及成形技术研究,宋超,南航硕士学位论文
[3]Y.W. Dong,Modeling of shrinkage during investment casting of thin-walled hollow turbine blades,Journal of Materials Processing Technology 244 (2017) 190–203
[4]Farhang Momeni,Plant leaf-mimetic smart wind turbine blades by 4D printing, Renewable Energy 130 (2019) 329e351
[5]Markus Bambach,Hot workability and microstructure evolution of the nickel-bsuperalloy Inconel 718 produced by laser metal deposition,Journal of Alloys and Compounds 740 (2018) 278e287
[6]Yao Li,Mechanism of heat affected zone cracking in Ni-based superalloy DZ125L fabricated by laser 3D printing technique,Materials and Design 150 (2018) 171–181。