焊接热裂纹产生原因及防止措施
几种焊缝热影响区裂纹的成因及对策研究
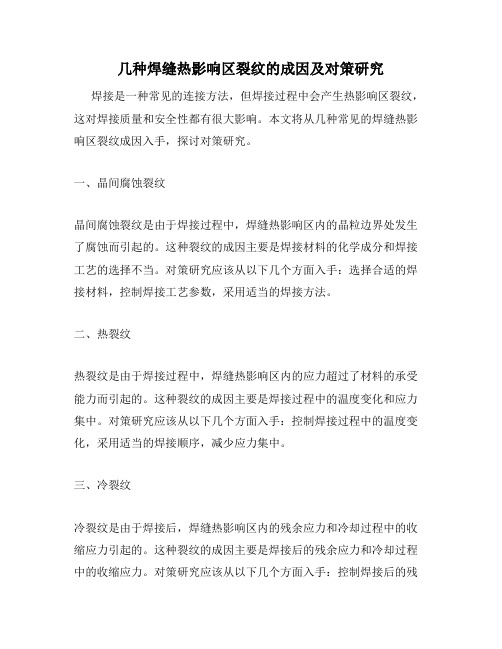
几种焊缝热影响区裂纹的成因及对策研究焊接是一种常见的连接方法,但焊接过程中会产生热影响区裂纹,这对焊接质量和安全性都有很大影响。
本文将从几种常见的焊缝热影响区裂纹成因入手,探讨对策研究。
一、晶间腐蚀裂纹
晶间腐蚀裂纹是由于焊接过程中,焊缝热影响区内的晶粒边界处发生了腐蚀而引起的。
这种裂纹的成因主要是焊接材料的化学成分和焊接工艺的选择不当。
对策研究应该从以下几个方面入手:选择合适的焊接材料,控制焊接工艺参数,采用适当的焊接方法。
二、热裂纹
热裂纹是由于焊接过程中,焊缝热影响区内的应力超过了材料的承受能力而引起的。
这种裂纹的成因主要是焊接过程中的温度变化和应力集中。
对策研究应该从以下几个方面入手:控制焊接过程中的温度变化,采用适当的焊接顺序,减少应力集中。
三、冷裂纹
冷裂纹是由于焊接后,焊缝热影响区内的残余应力和冷却过程中的收缩应力引起的。
这种裂纹的成因主要是焊接后的残余应力和冷却过程中的收缩应力。
对策研究应该从以下几个方面入手:控制焊接后的残
余应力,采用适当的焊接顺序,控制冷却速度。
综上所述,焊缝热影响区裂纹的成因主要有晶间腐蚀裂纹、热裂纹和
冷裂纹。
对策研究应该从选择合适的焊接材料、控制焊接工艺参数、
采用适当的焊接方法、控制焊接后的残余应力、采用适当的焊接顺序、控制冷却速度等方面入手。
只有这样,才能有效地预防焊缝热影响区
裂纹的产生,提高焊接质量和安全性。
焊接裂纹产生机理及其防治
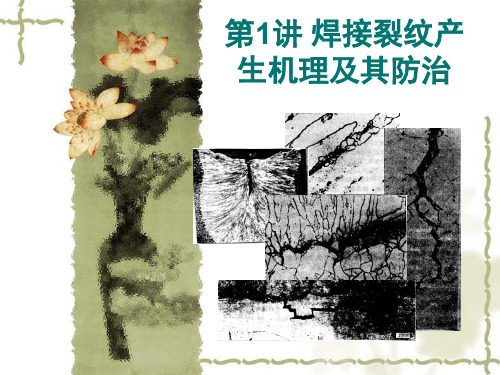
σcr ——插销试验临界应力(N/mm2);
[H]——扩散氢含量(JIS测氢法)(mL/100g);
t8/5——800~500℃冷却时间(s); t100——由峰值温度冷至100℃冷却时间。
cr (132 .3 27.5lg([H] 1) 0.216 HV 0.0102 t100) 9.8 式中 [H]——扩散氢含量(mL/100g); HV——热影响区的平均最大硬度(维氏).
第1讲 焊接裂纹产生机理及其防治
结晶裂纹产生条件: a.脆性温度区间TB大小; b.脆性温度区间金属塑性Pmin ; c.脆性温度区间应变增长率. 脆性温度区间TB/脆性温度区间金属塑性Pmin 取决于: a.焊缝化学成分; b.偏析程度; c.晶粒大小和方向. 脆性温度区间应变增长率取决于: a.金属热物理性能;a.接头刚度;c.焊接工艺参数
在焊缝结晶过程固相线附近,由于凝固金属收缩, 残余液体金属不足而不能及时填充,在应力作用下发 生沿晶开裂. 特征:a.裂纹断面有氧化彩色;b.焊缝中发生. 结晶裂纹产生原因: a.焊缝含杂质多(含硫、磷、碳、 硅偏高); b.凝固过程产生拉伸应力.
第1讲 焊接裂纹产生机理及其防治
图1 焊缝中的结晶裂纹
b. 减小焊接过程应力; c. 降低温度;
第1讲 焊接裂纹产生机理及其防治
第1讲 焊接裂纹产生机理及其防治
二 冷裂纹(Cold Cracking) 焊后冷至较低温度(马氏体转变温度Ms附近),由 拘束应力/淬硬组织和氢共同作用产生. 特征:a.主要在热影响区;b.焊缝少(横向裂纹). 1. 延迟裂纹 特点:a.具有延迟现象. b.决定于钢种淬硬倾向 /焊 接接头应力状态和熔敷金属中扩散氢含量. 2. 淬硬脆化裂纹 特征:a.钢种淬硬倾向大;b.没有氢诱发/仅拘束应 力作用;c.没有延迟现象;d.出现热影响区或焊缝. 3. 低塑性脆化裂纹 特点:a.低塑性材料;b.无延迟现象.
焊接裂纹产生原因及防治措施

以下为焊接裂纹产生原因及防治措施,一起来看看吧。
1、焊接裂纹的现象在焊缝或近缝区,由于焊接的影响,材料的原子结合遭到破坏,形成新的界面而产生的缝隙称为焊接裂缝,它具有缺口尖锐和长宽比大的特征。
按产生时的温度和时间的不同,裂纹可分为:热裂纹、冷裂纹、应力腐蚀裂纹和层状撕裂。
在焊接生产中,裂纹产生的部位有很多。
有的裂纹出现在焊缝表面,肉眼就能观察到;有的隐藏在焊缝内部,通过探伤检查才能发现;有的产生在焊缝上;有的则产生在热影响区内。
值得注意的是,裂纹有时在焊接过程中产生,有时在焊件焊后放置或运行一段时间之后才出现,后一种称为延迟裂纹,这种裂纹的危害性更为严重。
2、焊接裂纹的危害焊接裂缝是一种危害大的缺陷,除了降低焊接接头的承载能力,还因裂缝末端的尖锐缺口将引起严重的应力集中,促使裂缝扩展,最终会导致焊接结构的破坏,使产品报废,甚至会引起严重的事故。
通常,在焊接接头中,裂缝是一种不允许存在的缺陷。
一旦发现即应彻底清除,进行返修焊接。
3、焊接裂纹的产生原因及防治措施由于不同裂缝的产生原因和形成机理不同,下面就热裂缝、冷裂缝和再热裂缝三类分别予以讨论。
3.1、热裂纹热裂缝一般是指高温下(从凝固温度范围附近至铁碳平衡图上的A3线以上温度)所产生的裂纹,又称高温裂缝或结晶裂缝。
热裂缝通常在焊缝内产生,有时也可能出现在热影响区。
原因:由于焊接熔池在结晶过程中存在着偏析现象,低熔点共晶和杂质在结晶过程中以液态间层存在形成偏析,凝固以后强度也较低,当焊接应力足够大时,就会将液态间层或刚凝固不久的固态金属拉开形成裂缝。
此外,如果母材的晶界上也存在有低熔点共晶和杂质,则在加热温度超过其熔点的热影响区,这些低熔点化合物将熔化而形成液态间层,当焊接拉应力足够大时,也会被拉开而形成热影响区液化裂缝。
总之,热裂缝的产生是冶金因素和力学因素综合作用的结果。
防治措施:防止产生热裂缝的措施,可以从冶金因素和力学因素两个方面入手。
控制母材及焊材有害元素、杂质含量限制母材及焊接材料(包括焊条、焊丝、焊剂和保护气体)中易偏析元素及有害杂质的含量。
热裂纹和冷裂纹产生的原因
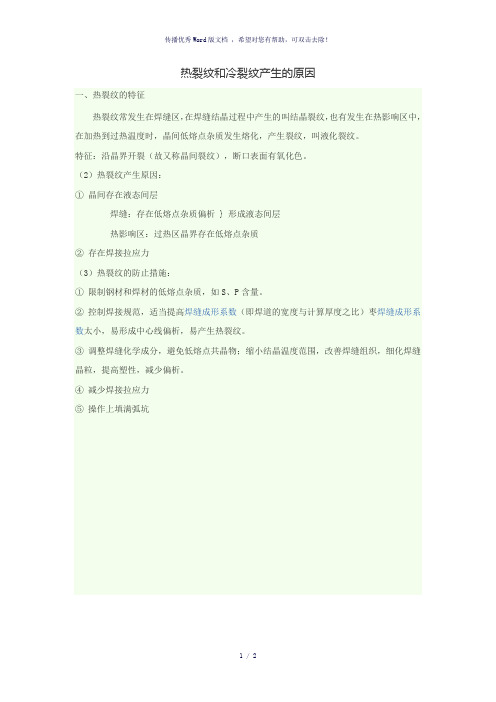
热裂纹和冷裂纹产生的原因一、热裂纹的特征热裂纹常发生在焊缝区,在焊缝结晶过程中产生的叫结晶裂纹,也有发生在热影响区中,在加热到过热温度时,晶间低熔点杂质发生熔化,产生裂纹,叫液化裂纹。
特征:沿晶界开裂(故又称晶间裂纹),断口表面有氧化色。
(2)热裂纹产生原因:①晶间存在液态间层焊缝:存在低熔点杂质偏析 } 形成液态间层热影响区:过热区晶界存在低熔点杂质②存在焊接拉应力(3)热裂纹的防止措施:①限制钢材和焊材的低熔点杂质,如S、P含量。
②控制焊接规范,适当提高焊缝成形系数(即焊道的宽度与计算厚度之比)枣焊缝成形系数太小,易形成中心线偏析,易产生热裂纹。
③调整焊缝化学成分,避免低熔点共晶物;缩小结晶温度范围,改善焊缝组织,细化焊缝晶粒,提高塑性,减少偏析。
④减少焊接拉应力⑤操作上填满弧坑1 / 2二、冷裂纹的形态和特征焊缝区和热影响区都可能产生冷裂纹,常见冷裂纹形态有三种冷裂纹形态 { 焊道下裂纹:在焊道下的热影响区内形成的焊接冷裂纹,常平行于熔合线发展焊指裂纹:沿应力集中的焊址处形成的冷裂纹,在热影响内扩展焊根裂纹:沿应力集中的焊缝根部所形成的冷裂纹,向焊缝或热影响发展a-焊道下裂纹; b-焊趾裂纹;c-焊根裂纹特征:无分支、穿晶开裂、断口表面无氧化色。
最主要、最常见的冷裂纹为延迟裂纹(即在焊后延迟一段时间才发生的裂纹-------因为氢是最活跃的诱发因素,而氢在金属中扩散、聚集和诱发裂纹需要一定的时间)。
(2)延迟裂纹的产生原因①焊接接头存在淬硬组织,性能脆化。
②扩散氢含量较高,使接头性能脆化,并聚集在焊接缺陷处形成大量氢分子,造成非常大的局部压力。
(氢是诱发延迟裂纹的最活跃因素,故有人将延迟裂纹又称氢致裂纹)③存在较大的焊接拉应力(3)防止延迟裂纹的措施①选用碱性焊条,减少焊缝金属中氢含量、提高焊缝金属塑性②减少氢来源枣焊材要烘干,接头要清洁(无油、无锈、无水)③避免产生淬硬组织枣焊前预热、焊后缓冷(可以降低焊后冷却速度)④降低焊接应力枣采用合理的工艺规范,焊后热处理等⑤焊后立即进行消氢处理(即加热到250℃,保温2~6左右,使焊缝金属中的扩散氢逸出金属表面)。
焊接热裂纹产生的原因

焊接热裂纹产生的原因一、引言焊接是现代工业生产中常用的加工方法之一。
在焊接过程中,热裂纹是一个常见的问题,会导致焊接件的损坏和失效。
因此,了解热裂纹产生的原因对于提高焊接质量和可靠性具有重要意义。
二、热裂纹的定义热裂纹是指在焊接过程中或后期使用过程中由于温度变化而引起的材料开裂。
它通常出现在高强度合金钢、不锈钢、铝合金等材料上。
三、热裂纹产生的原因1. 组织不均匀性组织不均匀性是导致热裂纹产生的主要原因之一。
当材料中存在缺陷或组织不均匀时,其内部应力分布也会不均匀。
在焊接过程中,由于受到加热和冷却的影响,这种应力分布会发生变化,从而导致材料出现开裂。
2. 焊接参数不当焊接参数包括电流密度、电压、速度等多个方面。
如果这些参数设置不当,就会导致局部过热或过快的冷却,从而引起热裂纹的产生。
3. 残余应力残余应力是指焊接后材料内部的应力。
在焊接过程中,由于加热和冷却的影响,焊接件内部会产生应力。
如果这些应力没有得到合理的处理,就会在后期使用中导致材料发生开裂。
4. 材料选择不当不同材料具有不同的物理性质和化学成分。
如果选择不当的材料进行焊接,就会导致组织不均匀、化学成分变化等问题,从而引起热裂纹的产生。
5. 焊接工艺不合理焊接工艺包括预热、焊接顺序、后续处理等多个方面。
如果这些工艺设置不当或者操作不规范,就会导致局部过热或者过快冷却等问题,从而引起热裂纹的产生。
四、热裂纹防治措施1. 优化组织结构通过对原材料进行特殊处理或者采用合适的退火工艺可以改善材料组织结构,并减少组织不均匀性带来的影响。
2. 合理设置焊接参数通过合理设置焊接参数,如电流密度、电压、速度等,可以控制焊接过程中的温度和冷却速度,减少热裂纹的产生。
3. 处理残余应力通过对焊接件进行退火或者热处理等工艺可以处理残余应力,并减少热裂纹的产生。
4. 合理选择材料在选择材料时应根据具体情况选择合适的材料,并进行必要的预热和后续处理等工艺,以减少热裂纹的产生。
碳钢焊接裂纹产生的原因及预防措施
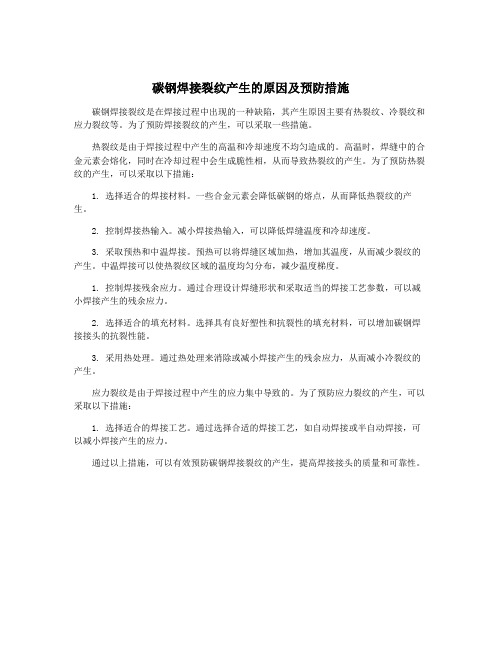
碳钢焊接裂纹产生的原因及预防措施
碳钢焊接裂纹是在焊接过程中出现的一种缺陷,其产生原因主要有热裂纹、冷裂纹和应力裂纹等。
为了预防焊接裂纹的产生,可以采取一些措施。
热裂纹是由于焊接过程中产生的高温和冷却速度不均匀造成的。
高温时,焊缝中的合金元素会熔化,同时在冷却过程中会生成脆性相,从而导致热裂纹的产生。
为了预防热裂纹的产生,可以采取以下措施:
1. 选择适合的焊接材料。
一些合金元素会降低碳钢的熔点,从而降低热裂纹的产生。
2. 控制焊接热输入。
减小焊接热输入,可以降低焊缝温度和冷却速度。
3. 采取预热和中温焊接。
预热可以将焊缝区域加热,增加其温度,从而减少裂纹的产生。
中温焊接可以使热裂纹区域的温度均匀分布,减少温度梯度。
1. 控制焊接残余应力。
通过合理设计焊缝形状和采取适当的焊接工艺参数,可以减小焊接产生的残余应力。
2. 选择适合的填充材料。
选择具有良好塑性和抗裂性的填充材料,可以增加碳钢焊接接头的抗裂性能。
3. 采用热处理。
通过热处理来消除或减小焊接产生的残余应力,从而减小冷裂纹的产生。
应力裂纹是由于焊接过程中产生的应力集中导致的。
为了预防应力裂纹的产生,可以采取以下措施:
1. 选择适合的焊接工艺。
通过选择合适的焊接工艺,如自动焊接或半自动焊接,可以减小焊接产生的应力。
通过以上措施,可以有效预防碳钢焊接裂纹的产生,提高焊接接头的质量和可靠性。
焊接裂纹成因分析及其防治措施

焊接裂纹成因分析及其防治措施1、焊接裂纹的现象在焊缝或近缝区,由于焊接的影响,材料的原子结合遭到破坏,形成新的界面而产生的缝隙称为焊接裂缝,它具有缺口尖锐和长宽比大的特征。
按产生时的温度和时间的不同,裂纹可分为:热裂纹、冷裂纹、应力腐蚀裂纹和层状撕裂。
在焊接生产中,裂纹产生的部位有很多。
有的裂纹出现在焊缝表面,肉眼就能观察到;有的隐藏在焊缝内部,通过探伤检查才能发现;有的产生在焊缝上;有的则产生在热影响区内。
值得注意的是,裂纹有时在焊接过程中产生,有时在焊件焊后放置或运行一段时间之后才出现,后一种称为延迟裂纹,这种裂纹的危害性更为严重。
常见裂纹的发生部位与型态如下图所示。
常见裂纹的发生部位与型态2、焊接裂纹的危害焊接裂缝是一种危害最大的缺陷,除了降低焊接接头的承载能力,还因裂缝末端的尖锐缺口将引起严重的应力集中,促使裂缝扩展,最终会导致焊接结构的破坏,使产品报废,甚至会引起严重的事故。
通常,在焊接接头中,裂缝是一种不允许存在的缺陷。
一旦发现即应彻底清除,进行返修焊接。
3、焊接裂纹的产生原因及防治措施由于不同裂缝的产生原因和形成机理不同,下面就热裂缝、冷裂缝和再热裂缝三类分别予以讨论3.1、热裂纹热裂缝一般是指高温下(从凝固温度范围附近至铁碳平衡图上的A3线以上温度)如下图所示所产生的裂纹,又称高温裂缝或结晶裂缝。
热裂缝通常在焊缝内产生,有时也可能出现在热影响区,如图所示。
原因:由于焊接熔池在结晶过程中存在着偏析现象,低熔点共晶和杂质在结晶过程中以液态间层存在形成偏析,凝固以后强度也较低,当焊接应力足够大时,就会将液态间层或刚凝固不久的固态金属拉开形成裂缝。
此外,如果母材的晶界上也存在有低熔点共晶和杂质,则在加热温度超过其熔点的热影响区,这些低熔点化合物将熔化而形成液态间层,当焊接拉应力足够大时,也会被拉开而形成热影响区液化裂缝。
总之,热裂缝的产生是冶金因素和力学因素综合作用的结果。
防治措施:防止产生热裂缝的措施,可以从冶金因素和力学因素两个方面入手。
碳钢焊接裂纹产生的原因及预防措施

碳钢焊接裂纹产生的原因及预防措施
碳钢焊接裂纹是焊接过程中常见的质量问题,其产生原因可以归结为以下几个方面:
1. 温度应力:焊接过程中,材料受到加热和冷却的影响,会产生热应力和冷却应力。
如果这些应力超过了材料的承受能力,就会导致裂纹的产生。
2. 焊接残余应力:焊接完成后,材料内部可能会留下残余应力。
这些应力可以是热
应力、冷却应力或由于金属的体积变化而产生的内部应力。
这些应力会导致材料在使用过
程中出现裂纹。
3. 晶间腐蚀:在某些条件下,焊接过程中产生的晶间腐蚀会导致裂纹的产生。
通常
是由于焊接过程中金属的组织发生变化,导致晶间的腐蚀性改变。
1. 控制焊接过程中的温度:通过控制焊接过程中的加热和冷却速度,可以减少温度
应力的产生。
可以采用预热或者控制焊接速度的方式来控制温度。
2. 降低焊接残余应力:使用合适的工艺参数,例如预热和后热处理,可以降低焊接
残余应力的产生。
合理的焊接工艺设计和材料选择也可以降低残余应力的产生。
3. 选择合适的焊接材料:合理选择焊接材料,可以降低晶间腐蚀的风险。
选择抗晶
间腐蚀性能好的焊接材料,可以减少晶间腐蚀引起的裂纹。
4. 采用适当的焊接工艺:选择合适的焊接工艺,可以减少温度和应力的集中,从而
减少裂纹的产生。
采用适当的焊接参数、焊接方法和焊接顺序等。
为了预防碳钢焊接裂纹的产生,需要从控制温度应力、降低焊接残余应力、选择合适
的焊接材料和采用适当的焊接工艺等多个方面进行综合考虑和控制。
- 1、下载文档前请自行甄别文档内容的完整性,平台不提供额外的编辑、内容补充、找答案等附加服务。
- 2、"仅部分预览"的文档,不可在线预览部分如存在完整性等问题,可反馈申请退款(可完整预览的文档不适用该条件!)。
- 3、如文档侵犯您的权益,请联系客服反馈,我们会尽快为您处理(人工客服工作时间:9:00-18:30)。
焊接热裂纹产生原因及防止措施
摘要:本文主要分析了焊接热裂纹产生机理及影响因素,并根据分析依据制定出防止产生裂纹的措施。
关键词:焊接热裂纹产生原因防止措施
随着钢铁、石油化工、电力等工业的发展,在焊接结构方面都取向大型化、大容量和高参数的方向发展,有的还在低温、深冷、腐蚀介质等环境下工作,因此,各种低合金、高强钢、中高合金钢、超高强钢,以及各种合金材料的应用日益广泛。
但是随着这些钢种和合金材料的应用,在焊接生产上带来了许多新问题,其中较为普遍而又十分严重的就是焊接热裂纹,它是引起焊接结构发生破坏事故的主要原因。
为了能有效的减少由于焊接热裂纹引起的事故,很有必要对焊接热裂纹产生原因进行分析,并制定出防止产生裂纹的措施。
一、焊接热裂纹的分类
热裂纹又可分为:结晶裂纹、高温液化裂纹、多边化裂纹。
在这里将对常见的结晶裂纹、高温液化裂纹、多边化裂纹进行讨论、分析。
二、焊接热裂纹形成机理与影响条件
1.结晶裂纹形成机理与影响条件
1.1结晶裂纹形成机理
焊缝在结晶过程中先结晶的金属较纯,后结晶的金属杂质较多,并富集在晶界,这些杂质所形成的共晶都具有较低的熔点。
低熔点共晶被排挤在柱状晶体交遇的中心部位,形成一种所谓《液态薄膜》,此时由于收缩而受到了拉伸应力,这时焊缝中的液态薄膜就成了薄弱地带,在拉伸应力的作用下就有可能在这个薄弱地带开裂而形成结晶裂纹。
结晶裂纹多发生在焊缝中树枝状晶的交界处。
1.2影响结晶裂纹的因素
1.2.1冶金因素的影响。
结晶裂纹的冶金因素主要是合金状态图的类型、化学成分和结晶组织形态,随着合金状态图结晶温度区间的增大,结晶裂纹的倾向也增大。
1.2.2合金元素的影响。
合金元素对产生结晶裂纹的影响十分复杂,但又非常重要,是影响裂纹最本质的因素。
多种合金元素的相互影响,往往比单一元素复杂的多。
如在碳钢和低合金钢中,硫磷都会增高结晶裂纹的倾向,即便是微量存在也会使结晶区间大为增加。
钢中的碳元素是影响结晶裂纹的主要元素,并能
加剧其他元素的有害作用,如硫、磷等元素。
1.2.3一次结晶组织形态的影响。
焊缝在结晶后,晶粒的大小、形态和方向以及析出的初生相等对抗裂性都有很大的影响,一般来说晶粒越粗大,越易产生裂纹,柱状晶的方向越明显,则产生结晶裂纹的倾向就越大。
2.液化裂纹形成机理与影响因素
2.1液化裂纹形成机理
液化裂纹是一种沿奥氏体晶界开裂的微裂纹,一般认为是由于焊接时近缝区金属或焊缝层面间金属,在高温下低熔点共晶组成物被重新熔化,在拉伸应力的作用下,沿奥氏体晶面开裂而形成的裂纹。
另外,在不平衡的加热和冷却条件下,由于金属间化合物分解和元素的扩散,造成了局部地区共晶成分偏高而发生局部晶间液化,同样也会产生液化裂纹。
2.2液化裂纹的影响因素
液化裂纹的形成机理与结晶裂纹基本一致,因此,影响因素也大致相同,也是冶金因素和力学因素共同作用的结果。
冶金因素的影响与结晶裂纹影响因素一致。
从工艺因素影响来看,其中焊接线能量对液化裂纹有很大的影响,线能量越大,由于输入的热量多,晶界低熔相的熔化就越严重,晶界处于液态的时间就越长,因此液化裂纹的倾向也就越大。
另外,由于许多薄层焊道组成的焊缝,比几个厚焊层组成的焊缝的总应力低,因此,线能量的增加,不仅能促使晶界液化,而且也增加了焊缝的应力,使液化裂纹倾向增大。
熔池的形状与产生液化裂纹有关,如焊缝的断面呈明显的倒草帽形,该处易产生液化裂纹。
3.多边化裂纹形成机理与影响因素
3.1多边化裂纹形成机理多边化裂纹多数是在焊缝中产生,它是在结晶前沿已凝的固相晶粒中萌生出大量的晶格缺陷,并且在快速的冷却条件下,由于不易扩散,它们以过饱和状态保留于焊缝金属中,在一定温度和应力的条件下,晶格缺陷由高能部位向低能部位转化,即发生移动和聚集,从而形成二次边界,即所谓的“多边化边界”。
另外,母材热影响区在焊接热循环的作用下,由于热应变,金属中的畸变能增加,同样也会形成多边化边界。
这种多边化的边界,一般情况下并不与一次晶界重合,在焊接后的冷却过程中,由于热塑性降低,导致沿多边化的边界产生裂纹。
3.2多边化裂纹的影响因素
3.2.1合金成分的影响。
由分析我们知道,多边化所需的激活能越高,则晶格缺陷的移动和聚集就越慢,形成多边化的时间就越大,因此,焊缝金属中元素激活能量越低,就越容易产生多边化裂纹。
3.2.2温度的影响。
在形成多边化过程中,温度越高,所需时间就越短,因此,就会增加形成多边化裂纹的倾向。
三、焊接热裂纹防止措施
1.防止热裂纹的措施
由于焊接时产生结晶裂纹的影响因素很多,因此,应抓住不同情况下产生裂纹的主要矛盾,根据大量的生产实践和研究所得,防止焊接结晶裂纹可以从以下两个方面着手。
1.1冶金方面
1.1.1控制焊缝中硫、磷、碳等有害杂质的含量,它们不仅能形成低熔共晶,而且还能促使偏析,因此,这些元素将会大大增加裂纹的敏感性,因此尽可能的限制母材和焊接材料中的硫、磷、碳的含量。
根据标准规定:S、P都应小于0.03~0.04%,用于低碳钢和低合金钢的焊丝含碳量一般不超过0.12%,焊接高合金钢时要求更高,硫、磷含量必须控制在0.02%以下。
对重要的焊接结构应采用碱性焊条或焊剂,能有效地控制有害杂质,防止结晶裂纹产生或降低倾向。
1.1.2改善焊缝一次结晶、细化晶粒是提高抗裂性的重要途径。
采用的办法是向焊缝中加入细化晶粒元素(如Mo、V、Ti、Nb、Zr、A1、稀土等),对于不锈钢焊接时,为了提高抗裂性、抗腐性,希望得到铁素体和奥氏体的双相组织焊缝。
2.工艺因素方面
工艺方面主要是焊接规范、预热、接头形式和焊接顺序等,用工艺方法主要是改善焊接时的应力从而防止结晶裂纹。
2.1焊接工艺及规范。
经过实践证明,适当增加焊接线能量和提高预热温度,可以减小焊缝金属的应变率,从而降低结晶裂纹的倾向。
2.2接头形式。
焊接接头形式不同,将影响接头的受力状态,结晶条件和热的分布等,因而结晶裂纹的倾向也不同,在设计和施工时应特别注意,如表面堆焊和熔深较浅的对接焊缝抗裂性较高,熔深较大的对接和各种角接、搭接、T型接头和外角接焊缝抗裂性较差,因为这些焊缝所承受得应力正好作用在焊缝的结晶面上,而这个面是晶粒之间联系较差,杂质聚集的地方,故易于引起裂纹。
对于厚板焊接结构,施工时常用多层焊,裂纹倾向比单层焊有所缓和,但对各层的熔深应注意控制。
2.3焊接技术。
在接头处尽量避免应力集中(错边、咬肉、未焊透等),也是降低裂纹倾向的有效方法。
2.4焊接次序。
施工时焊接次序是很重要的,同样的焊接方法和焊接材料,焊接次序不同,具有不同的结晶裂纹倾向。
总的原则是尽量使大多数焊缝能在较小刚度条件下焊接,使焊缝的受力较小。
例如,锅炉板与管束的焊接,采用同心圆式和平行线式都不利于应力疏散,只有采用放射交叉式的焊接次序才能分散应力。
在一般情况下,尽可能采用对称施焊,以利分散应力,减小裂纹倾向。
四、结论
通过以上分析和讨论,只要我们在设计和施工过程中,认真选材,科学制定施工程序,在很大程度上可以有效的防止焊接热裂纹的产生,从而可以防止由于焊接裂纹而导致事故的发生。
参考文献[1]《实用焊接技术手册》: 2002年9月,河北科学技术出版社.[2]《焊接手册》2001年7月机械工业出版社.[3]《焊接技师手册、金属管道焊接工艺手册》2005年1月,机械工业出版社.[4]《焊接原理》机械工业出版社.[5]《焊接冶金学》2002年1月,机械工业出版社.。