发动机悬置系统设计
发动机悬置的结构、作用、设计要求

发动机悬置得结构、作用、设计要求1.概述:随着当前底盘、发动机技术得日臻完善,车辆得振动、噪声得控制转而成为各个整车厂在研发上得重中之重。
据统计分析在一个车辆系统得上万个零部件中,对振动起关键作用得大概有二百个。
它们又分别在整车得振动系统中起不同得作用。
这里仅对发动机产生得振动经由发动机悬置到车身得振动系统得结构、作用、设计要求给出一定程度得阐述与说明.振动情况及位置频率Hz路面激励得频率范围车体1~3座椅与驾驶员4~8发动机总成5~18前后桥10~16车轮共振11~15排气管机械系统12~22发动机得振动频率范围怠速抖动20~30车体弯曲扭转25~40方向盘抖动25~40发动机总成弯曲130~230排气管气体系统100~1000变速器噪声350~600进气系统噪声100~600发动机噪声1000~5000基于汽车振动学得相应设计优化,应最大可能得避免整车主要部件在各种工况下得振动耦合.悬置得作用概括来说就就是对发动机振动与路面激励得隔离与吸收,减少乘客舱中人所受得影响,降低其她零部件因为过多振动产生得疲劳破坏。
2.悬置系统得结构2.1布置概念:◆前轮驱动——较低排量,◆后轮驱动-—较大排量.质量发动机+变速箱发动机+变速箱+驱动轴转距约1/4得驱动转距T全部得驱动转距T转距纵向横向方向●动力总成横置,如尊驰、骏捷等。
4G63 4G64 4G934G18 等动力总成中华1、8T 宝来等车得动力总成。
2.2结构概念:●橡胶悬置悬置结构为橡胶+金属支架,在低频、大振幅得动刚度与滞后角变化小。
在高频、小振幅激励下得动刚度与滞后角变化不大,容易产生动态硬化现象,常用于发动机前后悬置,阻止发动机过渡扭转。
●液力悬置悬置结构为橡胶形腔+液体(乙二醇)+金属支架,在低频、大振幅得激励下具有大阻尼;在高频、小振幅得激励下具有小刚度。
可根据实际与成本情况决定采用一个液压悬置还就是采用多个液压悬置。
常用于发动机左右悬置。
动力总成悬置系统优化设计与匹配---基本理论
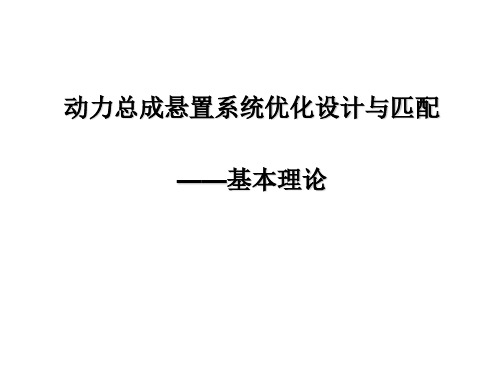
目录
一、悬置系统的典型结构及基本理论 二、悬置系统的主要布置方式 三、悬置系统的设计原则 四、悬置系统对汽车N&V特性的影响 五、悬置系统的设计流程和计算方法 六、悬置系统的匹配样车要求及N&V匹配方法
一、悬置系统的基本理论及典型结构
1、悬置的定义:装配在动力总成与车身(架)之间起支撑连接作用并使二者间 的力的传递产生衰减的弹性减振元件。
动力总成的完全解耦布置
动力总成的部分解耦布置
四、悬置系统的设计原则
撞击中心理论:
撞击中心理论主要用于选择前后悬置的位置。当动力总成视为 刚体,前后悬置如果处于互为撞击中心的位置上时,当一个悬置受 到干扰时或冲击时,另一个悬置上的响应为零。
扭轴理论:
当发动机的主惯性轴偏离曲轴轴线 一定角度, 在发动机激振力矩作用下, 发动机体将绕某一固定的“扭轴”作 白由振动。这时悬置布置应围绕“扭 轴”布置更为合理。
2、悬置系统(悬置+发动机+变矩器+变速箱)典型结构
3、各种类型悬置结构
一、悬置系统的基本理论及典型结构
悬置的结构型式日趋复杂。主要分为:橡胶悬置、液压悬置、 半主动/主动悬置。
橡胶悬置:结构简单,成型容易、成本低廉,被大量的使用在各型 车辆。缺点:存在高频硬化现象。下面为橡胶悬置常见结构:
压缩式
一、悬置系统的基本理论及典型结构
悬置系统六自由度力学方程的建立(势能)
一、悬置系统的基本理论及典型结构
悬置系统六自由度力学方程的建立(势能)
一、悬置系统的基本理论及典型结构
悬置系统六自由度力学方程的建立(耗散能)
一、悬置系统的基本理论及典型结构
汽车发动机悬置系统的设计指南

1 发动机悬置系统的设计指南1.1 悬置系统的设计意义及目标简介现代汽车发动机无一不是采用弹性支承安装的,这在汽车行业称之为“悬置”,在力学及振动工程中则是个隔振问题。
如果不用中间弹性元件而直接将发动机刚性地固紧在汽车车架(底盘)上,则当汽车在不平坦的路面上行驶时将导致机身由于车架的变形、冲击而损坏;而当汽车在平坦光滑的路面上行使时来自发动机的振动将导致车架、车身产生令人厌恶的结构噪声。
此外弹性悬置还能补偿在发动机安装及运动过程中由车架变形导致的相对位置的不精确。
由此可知,悬置系统的设计目标值:1) 能在所有工况下承受动、静载荷,并使发动机总成在所有方向上的位移处于可接受的范围内,不与底盘上的其它零部件发生干涉;2) 能充分地隔离由发动机产生的振动向车架及驾驶室的传递,降低振动噪声;3) 能充分地隔离由于地面不平产生的通过悬置而传向发动机的振动,降低振动噪声;4) 保证发动机机体与飞轮壳的连接弯矩不超过发动机厂家的允许值。
1.2 悬置系统的布置方式选择每个隔振器(悬置系统)不论其结构形状如何都可以看作由三个相互垂直的弹簧组成,按照这三个弹簧的刚度轴线和参考坐标轴线间的相对位置关系,悬置系统弹性支承的布置可以有常见的三种不同方式:1) 平置式。
这是常用的、传统的布置方式,其特征是布局简单、安装容易。
在这种布置方式中,每个弹性支承的三个相互垂直的刚度轴各自对应地平行于所选取的参考坐标轴。
2) 斜置式。
这是一种目前汽车发动机中用得最多的布置方式。
在这种布置方式中,每个弹性支承的三个相互垂直的刚度轴相对于参考坐标轴的布置是:除一个轴平行于参考坐标外,其他两个轴分别与参考坐标轴有一夹角。
一般斜置式的弹性支承都是成对地对称布置于垂向纵剖面的两侧,但每对之间的夹角可以不同,坐标位置也可任意。
这种布置方式的最大优点是:它既有较强的横向刚度,又有足够的横摇柔度,因此特别适用于象汽车发动机这样既要求有较大的横向稳定性,又要求有较低的横摇固有频率以隔离由不均匀扭矩引起的横摇振动。
发动机悬置系统设计理论基础

发动机悬置系统常用材料
高强度钢
用于制造承受较大载荷的悬置支架和 连接件,具有较高的强度和刚度。
铝合金
复合材料
如玻璃纤维增强塑料(GFRP)和碳纤 维增强塑料(CFRP),具有轻质、高 强度和耐腐蚀等优点,适用于需要减 轻重量的部件。
质量轻,散热性好,常用于制造需要 轻量化的部件,如悬置支架和连接件 。
引入仿真分析
利用仿真分析工具对悬置系统进行优 化设计,提高设计效率。
强化试验验证
通过试验验证设计的有效性,确保实 际应用中的性能表现。
持续改进与创新
关注行业动态,不断改进和创新发动 机悬置系统设计技术,提高整车性能 。
感谢您的观看
THANKS
材料创新
新型高阻尼材料和复合材料的出现将为发动机悬 置系统的发展提供更多可能性,提高减振效果和 耐久性。
模块化设计
为了便于维护和更换,发动机悬置系统将趋向于 采用模块化设计,降低生产成本和维修成本。
05
发动机悬置系统设计中的 问题与解决方案
发动机悬置系统设计中的常见问题
振动传递
发动机产生的振动通过悬置系 统传递至车架,影响整车舒适
发动机悬置系统设计理论基 础
目 录
• 发动机悬置系统概述 • 发动机悬置系统设计理论 • 发动机悬置系统材料与制造工艺 • 发动机悬置系统设计实例分析 • 发动机悬置系统设计中的问题与解决方案
01
发动机悬置系统概述
发动机悬置系统的定义
发动机悬置系统是汽车动力总成的重 要组成部分,主要负责将发动机固定 在车架上,并隔离发动机的振动和噪 音,以保证车辆的舒适性和稳定性。
它由多个橡胶悬置组成,每个悬置具 有不同的刚度和阻尼特性,以适应不 同的振动频率和幅度。
发动机悬置设计

整车技术部设计指南73发动机悬置设计5.1 概述汽车的乘坐舒适性——NVH(Noise-噪声、Vibration-振动和 Harshness-声振舒适性)越来越受到人们的重视和关注,因为噪声、振动和舒适性,是衡量汽车制造质量的一个综合问题,它给汽车用户的感觉是最直接和最表面的。
作为汽车动力源的发动机是汽车主要的振动激励源之一,其气缸燃气压力、转速及输出转矩的周期性波动及不平衡惯性力(矩)既激起发动机动力总成本身的刚体振动和弹性振动,又激起汽车动力传动的扭转振动和弯曲振动等,从而导致十分严重的振动、噪声及结构问题,最终传递给车身,引起整车振动与噪声。
汽车动力总成悬置系统是指动力总成(包括发动机、离合器及变速箱等)与车架或车身之间通过弹性悬置元件连接而成的系统,发动机动力总成的振动与路面激励力是通过弹性悬置元件传给车身,该项系统性能设计的好坏直接关系到发动机振动向车体的传递,影响整车的 NVH 特性。
因此,最大限度的减小发动机动力总成所产生的振动及噪声向车身传递,是汽车减振和降噪的主要研究内容之一。
5.2、悬置系统功能介绍5.2.1 悬置总成的功用a)悬置系统的首要作用即最基本的作用是支承动力总成的动、静载荷,并使发动机动力总成在所有方向上的位移处于可接受的范围内,不与前舱内其它零部件发生干涉;b)隔离发动机动力总成的振动,最大限度地降低从发动机动力总成传递到车身/车架上的振动,能有效的降低振动及噪音;c)在汽车做紧急制动、加速或受其它外界负荷的作用下时,发动机不应有过大的位移;d)隔离由于轮胎及车身的抖动而产生的振动和噪音通过悬置系统而传向发动机动力总成,降低振动及噪音;e)悬置系统元件需有足够的使用寿命。
5.3 动力总成悬置系统设计方法5.3.1 设计需解决的问题a)主要起支撑减振的作用,因而,悬置必须要能够支撑起动力总成,并且保证其三整车技术部设计指南74个方向的位移和绕三个轴的转角在一定的限度内;b)发动机自身振动的隔离,即不让发动机不平衡力所造成的振动过分地传向车向车f i f IDLE / 2身,这就要求各悬置的固有频率与各激励源的频率必须满足的条件,其中,f i为各悬置的固有频率,f IDLE为怠速时各激励源的频率。
发动机悬置设计
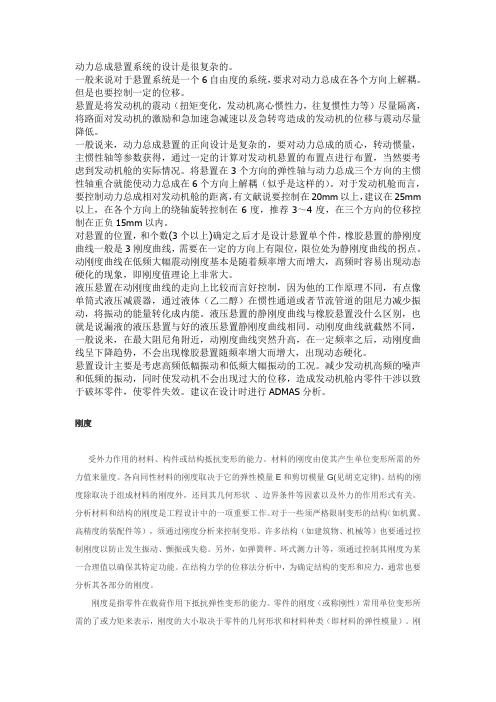
动力总成悬置系统的设计是很复杂的。
一般来说对于悬置系统是一个6自由度的系统,要求对动力总成在各个方向上解耦。
但是也要控制一定的位移。
悬置是将发动机的震动(扭矩变化,发动机离心惯性力,往复惯性力等)尽量隔离,将路面对发动机的激励和急加速急减速以及急转弯造成的发动机的位移与震动尽量降低。
一般说来,动力总成悬置的正向设计是复杂的,要对动力总成的质心,转动惯量,主惯性轴等参数获得,通过一定的计算对发动机悬置的布置点进行布置,当然要考虑到发动机舱的实际情况。
将悬置在3个方向的弹性轴与动力总成三个方向的主惯性轴重合就能使动力总成在6个方向上解耦(似乎是这样的)。
对于发动机舱而言,要控制动力总成相对发动机舱的距离,有文献说要控制在20mm以上,建议在25mm 以上,在各个方向上的绕轴旋转控制在6度,推荐3~4度,在三个方向的位移控制在正负15mm以内。
对悬置的位置,和个数(3个以上)确定之后才是设计悬置单个件,橡胶悬置的静刚度曲线一般是3刚度曲线,需要在一定的方向上有限位,限位处为静刚度曲线的拐点。
动刚度曲线在低频大幅震动刚度基本是随着频率增大而增大,高频时容易出现动态硬化的现象,即刚度值理论上非常大。
液压悬置在动刚度曲线的走向上比较而言好控制,因为他的工作原理不同,有点像单筒式液压减震器,通过液体(乙二醇)在惯性通道或者节流管道的阻尼力减少振动,将振动的能量转化成内能。
液压悬置的静刚度曲线与橡胶悬置没什么区别,也就是说漏液的液压悬置与好的液压悬置静刚度曲线相同。
动刚度曲线就截然不同,一般说来,在最大阻尼角附近,动刚度曲线突然升高,在一定频率之后,动刚度曲线呈下降趋势,不会出现橡胶悬置随频率增大而增大,出现动态硬化。
悬置设计主要是考虑高频低幅振动和低频大幅振动的工况。
减少发动机高频的噪声和低频的振动,同时使发动机不会出现过大的位移,造成发动机舱内零件干涉以致于破坏零件,使零件失效。
建议在设计时进行ADMAS分析。
发动机悬置设计4
〇
Nissan Note
1.2supchgDI CVT
O-balance Pendulum
〇
China A test-car
1.0TDI 6AT +N-idle
Nothing Pendulum
〇
Engineering judgement for NVH
1)Outer-balance and Pendulum is OK ⇒we need check our design
2nd gear toothing
Motor noise
100
600
rotation unbalance
2K
12K
Electro-magnetic noise
power-plant bending1 power-plant bending2
Igen values AC compressor
distribution
Φ85mm
Type B
4点Pendulum和Upper T-rod的案例(1)
数值Upper T-rod的案例
2-3. Pendulum悬置的案例 1) 右 2) 左
3) T-rod 4) 三缸机
3)Engine-mount for new 3cylinder
If we put hydraulic resonance at 15Hz, New peak comes up at 20-24Hz
Diff order noise
Typical EV acceleration Noise 3D MAP
400Hzat3000rpm
3) 2)
800Hzat1000rpm
发动机悬置系统设计理论基础
7-9Hz
60%
>1Hz
Fore/Aft 7-9Hz
80%
>1Hz
Pitch
10.5-11.5Hz 90%
>1Hz
Roll
<13Hz
60%
>1Hz
Yaw
<13Hz
60%
>1Hz
For Idle Condition
• 所有模态频率必须高于6Hz,以减少与车身刚体模态的耦合 • 所有模态频率必须低于21Hz,以减少与车身、转向柱及动力传动系统等模态的耦合 • Bounce与Pitch的模态频率的解耦率要着重关注 • Pitch与Fore/Aft 的模态频率至少隔开2Hz,Pitch与Bounce的模态频率至少隔开2Hz,
1) 在低频路面激励下,车辆的左右两个车轮 轨迹输入具有较高的相关性,即认为左右轮输 入基本一致。
2) 在高频路面激励下,车辆所受的激励实际 上大多只涉及到车轮跳动,对车身运动影响甚 微,这样车身左右两边的相对运动就可忽略。
这样,就将七自由度模型简化成一个线性的 四自由度半车模型。
再用一个动力学等效系统来代替上面的半车模型, 在动力学等效处理中,车辆系统的三个等效质量必 须满足以下三个力学条件,即:
1. 基本概念 发动机悬置系统的模型 能量解耦理论 悬置的布置理论
4. 悬置的布置理论
• 弹性中心定理
az (L 1) tan ay L tan2 1
• 打击中心定理
使A、B 两点互为撞击中心
1 2 J y / m
式中,Jy为绕通过质心的Y轴的转动惯量, m为刚体质量,α1、α2为A 、B 两 点到质心(C. G点) 的水平距离
某一车型动力总成刚体模态频率与解耦(pp=0.2mm)
发动机悬置系统设计
[ M]-质量阵
[K]-刚度阵 {q}-广义坐标列向量
2
隔振分析计算
振动模型简化理论基础
振动系统的动能可以写成广义速度的函数,其二 次型表达式为:
T=1/2{dq/dt}T[M]{dq/dt}
其势能可以写成广义坐标函数,其二次型表达式 为:
U=1/2{q}T[K]{q}
率 系统要解耦
5
橡胶支承元件结构设计计算
弹性元件结构型式
压缩型 剪切型 复合型
橡胶元件刚度计算
k = G•F•D G-橡胶的静态剪切模量 数F-和橡胶件形状有关的系 D-尺寸因素 H为肖氏G =硬G度50•H/(100-H)
6
橡胶支承元件结构设计计算
橡胶元件刚度计算
7
橡胶支承元件结构设计计算
7
支承布置方案
支点位置初选
弯曲振动节点 打击中心理论
8
隔振分析计算
单自由度振动系统隔振原理
强迫振动微分方程
m(d2x/dt2)
响应振幅 A:
+
c(dx/dt)
+kx
=F0ejωt
A= F0∕[k((1-λ2) +4ζ2λ2)1/2]
λ=ω∕p ζ= c ∕2mp
p=(k∕m)1/2
作用于地基的力的幅值:
Me=Mo + ΣMrsin(rωt+φr) [ω=2π/T]
对单缸机而言: 多缸机而言,直立、四冲程发动机
f=n•i/120 Hz n - 发动机转速 i - 缸数
1
隔振分析计算
振动模型简化理论基础
发动机振动模型是以刚体弹性支承理论作为基础,认为发动机 是一空间自由刚体,通过3~4个具有三维弹性的元件支承在刚性的、 质量为无限的机架上,它具有6个自由度运动(图示),它已被汽车工 程界广为接受,且有较好的效果。 为了计算方便,现导出其矩阵形式的振动微分方程式 无阻尼自由振动运动微分方程式,一般具有如下形式
发动机悬置设计步骤
由于车型开发中需要对发动机悬置进行设计计算,需贵公司提供如下数据,望贵公司能给予帮助,谢谢。
1、发动机总成的总质量,包括内部注满的机油和冷却液。
2、发动机总成的质心位置.
3、发动机总成主惯性袖的位置;
4、动力总成绕三个主惯性铀的转动惯量;
5、发动机机体后端面与飞轮壳接合面上的静态弯矩,
6、发动机的最大扭矩及怠速转速,
8、计算发动机变速器总成在悬置软垫上可能引起的最大转矩反作用力.可用两种计算标准,一是发动机发出最大扭矩时,另一是发动机在额定功率点时(包括最大变速器减速比),然后根据软垫制造商提供的软点"负荷-变形"曲线,核对所选择的软垫是否能承受这一作用力及软垫的最大变形量是否在合理的范围内
9、按实际应用情况,确定动态负荷冲击加速度的数值.
10、设计悬置支架按动态负荷进行强度校核若发动机制造商没有提供机体后端面与飞轮壳结合部位的静态弯矩限制,则应按动态负荷计算该部位的弯矩和工作应力,保证该薄弱环节安全可靠
11、选择合适的悬置软垫,应能承受上述动静态负荷,并满足隔振要求,确定软垫的刚度12、根据所选择的软垫的压缩和剪切刚度及系统布置形式,分别计算前后悬置的垂直综合刚度,侧向综合刚度和扭矩综合刚度及相应的固有频率(如果是平置式布置,则系统的垂直方向固有频率和隔振效率可从软垫制造商提供的坐标图上根据静态变形量确定)
13、确定发动机的外激振频率
14、通过软垫制造商提供的坐标图,按照软垫的静态压缩量以及外激振频率,确定悬置系统的隔振效率.
15、检查悬置系统是否具备克服其他外力和惯性力的能力,必要时应设置限位装置
16、选择能满足工作环境条件的需要的悬置软垫的材料
17、校核悬置系统的结构布置能否适应整车提供的空间,确保不与周围的零部件发生干涉18、试验。
- 1、下载文档前请自行甄别文档内容的完整性,平台不提供额外的编辑、内容补充、找答案等附加服务。
- 2、"仅部分预览"的文档,不可在线预览部分如存在完整性等问题,可反馈申请退款(可完整预览的文档不适用该条件!)。
- 3、如文档侵犯您的权益,请联系客服反馈,我们会尽快为您处理(人工客服工作时间:9:00-18:30)。
- 发动机自身的振动
- 来自路面或轮胎不平衡输入激励
支承重量 承受各种负荷,如汽车加速、制动、转弯时的惯性力, 发动机反扭矩 容纳发动机一定运动 注意使用环境――高温、高寒、油污等 注意动力总成的静变矩 有足够的使用寿命
4
支承布置方案
三点式――V形布置前两点后一点呈对称用于轻型FR车 FF车三点无规律
[M]{d2q/dt2} + [K]{q} = 0
[ M]-质量阵
[K]-刚度阵 {q}-广义坐标列向量
11
隔振分析计算
振动模型简化理论基础
振动系统的动能可以写成广义速度的函数,其二 次型表达式为: T=1/2{dq/dt}T[M]{dq/dt} 其势能可以写成广义坐标函数,其二次型表达式
为:
U=1/2{q}T[K]{q} 这样,就可得到6自由度振动微分方程式
5
支承布Байду номын сангаас方案
四点式――V形布置前两点后两点,用于较重的发动机
6
支承布置方案
支点位置初选
弯曲振动节点 打击中心理论
7
隔振分析计算
单自由度振动系统隔振原理
强迫振动微分方程
响应振幅 A:
m(d2x/dt2) + c(dx/dt) +kx =F0ejωt
A= F0∕[k((1-λ2) +4ζ 2λ2)1/2] λ=ω∕p ζ = c ∕2mp p=(k∕m)1/2
14
橡胶支承元件结构设计计算
弹性元件结构型式
压缩型 剪切型 复合型
橡胶元件刚度计算
k = G•F•D G-橡胶的静态剪切模量 F-和橡胶件形状有关的系 数 D-尺寸因素 G = G50•H/(100-H) H为肖氏硬度
15
橡胶支承元件结构设计计算
橡胶元件刚度计算
16
橡胶支承元件结构设计计算
培训
发动机悬置系统设计
发动机悬置系统设计
1
介绍
概说 设计考虑 支承布置方案 隔振分析计算 橡胶支承元件结构设计计算 总结――悬置系统设计步骤 液体阻尼悬置介绍
2
概说
悬置系统的历史发展和作用 设计的重要性
悬置设计的含意
3
设计考虑
要从隔振、防震的角度来考虑振源来自两个 方面
2) 工作过程不均衡引起的干扰力矩 Me呈周期化的变化 周期函数可展开成富里哀级数
Me=Mo + ΣMrsin(rωt+φr) [ω=2π/T] 对单缸机而言: 多缸机而言,直立、四冲程发动机 f=n•i/120 Hz n - 发动机转速 i - 缸数
10
隔振分析计算
振动模型简化理论基础
发动机振动模型是以刚体弹性支承理论作为基础,认为发动机 是一空间自由刚体,通过3~4个具有三维弹性的元件支承在刚性的、 质量为无限的机架上,它具有6个自由度运动(图示),它已被汽车工 程界广为接受,且有较好的效果。 为了计算方便,现导出其矩阵形式的振动微分方程式 无阻尼自由振动运动微分方程式,一般具有如下形式
19
元件的材料和许用应力
大多用天然胶,特殊情况用合成胶 元件损坏在于疲劳,平均应变对疲劳寿命影响很大, 拉伸工作对元件寿命很不利
许用应力 压缩 剪切
100~150N/cm2 10~20N/cm2
许用应变
15~20% 20~30%
17
总结
悬置系统设计步骤
18
液体阻尼悬置介绍
悬置系统理想特性要求 液阻元件结构介绍
12
隔振分析计算
发动机子系统与 整车匹配
1)隔振与解耦
数学上理解 运动学上的理解 在一定条件,解耦 对于隔振只是一种用起 来方便的措施 用计算机寻优的方法 可以解决
13
隔振分析计算
发动机子系统与整车匹配
2)系统的匹配 考虑发动机激励,绕θx的固有频率要比发动机怠 速激励频率低至少为1/√2至1/2 考虑路面,要注意避开车架一弯、一扭和车桥的频 率 系统要解耦
作用于地基的力的幅值:
8
隔振分析计算
激振源频率成份分析 发动机的干扰力和力矩 1) 惯性力引起的干扰力 2 旋转质量 pr =m1rωe 2 往复质量 pj =m1rωe (cosωet +λ cos2ωet) λ =r/l 总体合成:对直立四缸机有 pj II 六、八缸机有 pj=0
9
隔振分析计算