发动机悬置设计
动力总成悬置系统设计案例

动力总成悬置系统六自由度分析模型(3个橡胶悬置)
(2)优化设计
• 设计目标:6个自由度方向解耦率超过指定下限; 6个固有频率配置在指定范围;
• 设计约束:各悬置刚度的压剪比;
• 设计变量:3个橡胶悬置的三向刚度 3个橡胶悬置的安装位置
(3)优化模型
目标函数:
悬置刚度压剪比约束:
优化效果验证
左悬 置
后悬置
总结:
案例四、动力总成悬置系统稳健优化
1、动力总成悬置系统模型
汽车动力总成悬置系统
六自由度分析模型
动力总成悬置系统的设计要求:
1. 每个悬置在其3个弹性主轴方向的线刚度应满足动力总成固 有频率和解耦率的要求;3个方向上的力—位移非线性特性 ,应能有效控制在汽车的各种行驶工况下(典型工况和极限 工况)动力总成的运动位移。
汽车动力总成悬置系统 设计案例
目录
一、动力总成悬置系统设计案例一 二、动力总成悬置系统设计案例二 三、动力总成悬置系统设计案例三 四、动力总成悬置系统稳健优化
一、动力总成悬置系统设计案例一
纵置动力总成悬置系统
某商用车动力总成悬置系统模型(四个橡胶悬置)
(1)悬置系统参数
(2)优化设计
• 设计目标:6个自由度方向解耦率最大
• 各悬置支承点在Z方向上的动反力频域响应 对比
动反力 降低
后左悬置支承点在Z方向上的动反力频域响应(虚线为优化后,实线为优化前)
(3)优化设计结果
• 各悬置支承点在Z方向上的动反力频域响应 对比
动反力 降低
后右悬置支承点在Z方向上的动反力频域响应(虚线为优化后,实线为优化前)
二、动力总成悬置系统设计案例二
0.85 dRatioPitc h
发动机悬置设计1

Fig.5 隔振橡胶的特征—1 1. 材料本身具有弹性要素的同时、还具有衰减性
2. 具有三方向的弹性主轴
橡胶材料本身就具有弹性要素的同时,还具有衰减性。而且从产品状态上来分析,还同时具有X、Y、Z 三个弹性主轴。 一般来考虑弹性要素、衰减特性的大小、以及各悬置的弹性主轴方向等参数,来设计隔振橡胶。
隔振橡胶以及发动机悬置的基础知识
1.发动机悬置的实例(V6-FF) 2.历史 3.悬架方式 4.隔振橡胶的基础特性理论(1-7)
Fig.2
在右悬置上方还有一个拉杆
发动机悬置实例
后悬置
前悬置
左悬置
Fig.2: 搭载在V6发动机的FWD车型上所使用的发动机悬置案例: 前悬置、后悬置以及左悬置三点来支撑起发动机。然后通过拉杆来控制加、减速时发动机的位移。
Fig.17 橡胶材料的特征-2
天然橡胶 丁苯橡胶 顺丁橡胶 丁基橡胶 乙丙橡胶 氯丁橡胶
隔振橡胶所使用的橡胶材料特征示意 天然橡胶在隔振橡胶元件里是使用最多的,但是根据要求性能的要求,为了取得更好的性能平衡性,也 有采取各种配方的橡胶。
1.系统设计 2.悬置系统的例 3.系统和特性分析(roll刚性) 4.6自由度固有频率分析 5.怠速振动分析 6.单体特征分析 7.液压悬置的基本构造(1-2) 8.主动悬置
剪切方向(S)的刚度计算方法示意: 此处的Gap是只当做横刚度来表示。当然其中,包含有支配和压缩(C)方向一样的h/a形状的项目。但是 剪切方向的变形一般来说厚度(h)变化小,因此剪切方向的刚度是比较线性的。
Fig.8 隔振橡胶的特征—4 倾斜搭载的场合
倾斜搭载的场合时刚度计算方法示意: 一般来说,纵置发动机的悬置系统会有一个倾斜角度。作为整车的上下(Z)方向的刚度要求,可根据悬 置单体以及压缩(C)方向、剪切(S)方向的刚度来计算出来。
发动机悬置设计4
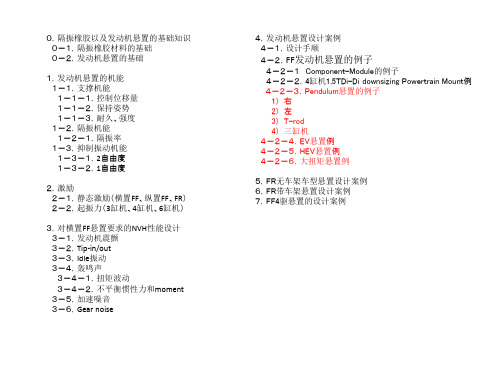
〇
Nissan Note
1.2supchgDI CVT
O-balance Pendulum
〇
China A test-car
1.0TDI 6AT +N-idle
Nothing Pendulum
〇
Engineering judgement for NVH
1)Outer-balance and Pendulum is OK ⇒we need check our design
2nd gear toothing
Motor noise
100
600
rotation unbalance
2K
12K
Electro-magnetic noise
power-plant bending1 power-plant bending2
Igen values AC compressor
distribution
Φ85mm
Type B
4点Pendulum和Upper T-rod的案例(1)
数值Upper T-rod的案例
2-3. Pendulum悬置的案例 1) 右 2) 左
3) T-rod 4) 三缸机
3)Engine-mount for new 3cylinder
If we put hydraulic resonance at 15Hz, New peak comes up at 20-24Hz
Diff order noise
Typical EV acceleration Noise 3D MAP
400Hzat3000rpm
3) 2)
800Hzat1000rpm
发动机悬置系统设计

17
总结
悬置系统设计步骤
18
液体阻尼悬置介绍
悬置系统理想特性要求 液阻元件结构介绍
19
振动模型简化理论基础
发动机振动模型是以刚体弹性支承理论作为基础,认为发动机 是一空间自由刚体,通过3~4个具有三维弹性的元件支承在刚性的、 质量为无限的机架上,它具有6个自由度运动(图示),它已被汽车工 程界广为接受,且有较好的效果。 为了计算方便,现导出其矩阵形式的振动微分方程式 无阻尼自由振动运动微分方程式,一般具有如下形式
培训
发动机悬置系统设计
1 发动机悬置系统设计
介绍
概说 设计考虑 支承布置方案 隔振分析计算 橡胶支承元件结构设计计算 总结――悬置系统设计步骤 液体阻尼悬置介绍
2
概说
悬置系统的历史发展和作用 设计的重要性
悬置设计的含意
3
设计考虑
要从隔振、防震的角度来考虑振源来自两个 方面
[M]{d2q/dt2} + [K]{q} = 0
[ M]-质量阵
[K]-刚度阵 {q}-广义坐标列向量
11
隔振分析计算
振动模型简化理论基础
振动系统的动能可以写成广义速度的函数,其二 次型表达式为:
T=1/2{dq/dt}T[M]{dq/dt}
其势能可以写成广义坐标函数,其二次型表达式 为:
U=1/2{q}T[K]{q}
5
支承布置方案
四点式――V形布置前两点后两点,用于较重的发动机
6
支承布置方案
支点位置初选
弯曲振动节点 打击中心理论
7
隔振分析计算
单自由度振动系统隔振原理
强迫振动微分方程
发动机悬置系统设计理论基础
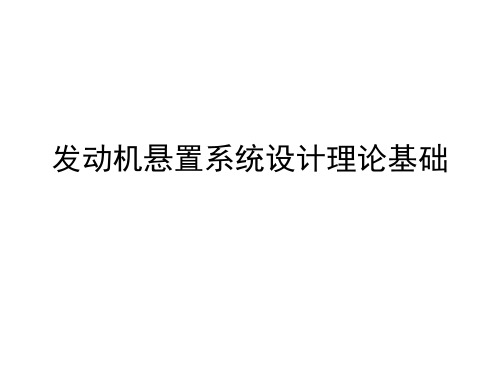
7-9Hz
60%
>1Hz
Fore/Aft 7-9Hz
80%
>1Hz
Pitch
10.5-11.5Hz 90%
>1Hz
Roll
<13Hz
60%
>1Hz
Yaw
<13Hz
60%
>1Hz
For Idle Condition
• 所有模态频率必须高于6Hz,以减少与车身刚体模态的耦合 • 所有模态频率必须低于21Hz,以减少与车身、转向柱及动力传动系统等模态的耦合 • Bounce与Pitch的模态频率的解耦率要着重关注 • Pitch与Fore/Aft 的模态频率至少隔开2Hz,Pitch与Bounce的模态频率至少隔开2Hz,
1) 在低频路面激励下,车辆的左右两个车轮 轨迹输入具有较高的相关性,即认为左右轮输 入基本一致。
2) 在高频路面激励下,车辆所受的激励实际 上大多只涉及到车轮跳动,对车身运动影响甚 微,这样车身左右两边的相对运动就可忽略。
这样,就将七自由度模型简化成一个线性的 四自由度半车模型。
再用一个动力学等效系统来代替上面的半车模型, 在动力学等效处理中,车辆系统的三个等效质量必 须满足以下三个力学条件,即:
1. 基本概念 发动机悬置系统的模型 能量解耦理论 悬置的布置理论
4. 悬置的布置理论
• 弹性中心定理
az (L 1) tan ay L tan2 1
• 打击中心定理
使A、B 两点互为撞击中心
1 2 J y / m
式中,Jy为绕通过质心的Y轴的转动惯量, m为刚体质量,α1、α2为A 、B 两 点到质心(C. G点) 的水平距离
某一车型动力总成刚体模态频率与解耦(pp=0.2mm)
发动机悬置设计介绍-中文译文

固有频率的决定 弹性模数的决定
振动传递率→固有频率 固有频率→动弹性模数
悬置(INSURATOR)的决定
材料、形状的选定 目标规格设定
表达机械防振时, 设机械的加振力为F0(机械的强制振幅为a0), 传到基础的力为F(机械的振幅为a)。 其传递的比例叫做传递率,由(1)式表示。
频率比和防振效果
振动传递率由机械的强制振动频率和防振支承时的固有频率之 比决定。
计算实例
动力总成载荷 发动机转速 200kg(支承载荷100kg) 700rpm(12Hz)
固有频率(f) 根据振动传递率10~15%的振动传递率曲线 N/f=3
f=N/3=700/3=233.3(rpm)=4Hz
动弹性模数(K) kd=(2πf)2xm/ 1000 =(2xπx4)2x100/1000 =59.7 (N/mm) 静弹性模数(K) ks=kd/α =42.6 (N/mm) α=1.4
Butadiene Rubber 苯 丁 橡 胶 ) 胶)
・ BR (Polybutadiene Rubber 聚 丁 二 烯 橡
・IR (Isoprene Rubber异戊二烯橡胶)
(2)特别要求耐油性加硫橡胶・NBR (Acrylonitrile Butadiene Rubber丙烯 氰聚丁橡胶) (3)特别要求耐候性加硫橡胶 ・CR (Chloroprene Rubber) ・PDM
中间连接板
倾斜配置
3-2.发动机悬置支架设计必要条件
(a)振动必要条件 目标:fn>500Hz; 通常因发动机振动产生噪声的频率为200~ 400Hz,设计时让支架在此频率之间不产 生共振。 (b)強度必要条件 ①在坏路行驶时由路面输入的上下载荷; ②由起步、停止和加减速引起的驱动反力。 发动机和变速器悬置 FF車 上:10G,下:20G 前、后滚动阻尼器 加速0.6G 减速0.3G
动力总成悬置系统设计总结
动力总成悬置系统设计总结第一章悬置系统的经验设计悬置系统的功能与设计原则发动机悬置系统是发动机应用工程的重要组成部分。
悬置系统的功能与设计原则大致可归纳如下:1隔离振动在发动机所有工作转速范围内,发动机产生的振动必须通过悬置系统加以隔离,尽可能降低传递给汽车底盘和车身的振动。
同时悬置系统还必须隔离道路不平引起的车轮悬挂系统的振动,防止这一振动向发动机传递,避免发动机振动加剧以满足车辆运行时的平稳性和舒适性,并保证怠速和停机时发动机的稳定性。
2发动机支承和定位为了隔离振动,发动机被支承在几个弹簧软垫上。
因而在发动机本身振动和外界作用力驱动下,发动机和底盘之间必然存在着相对运动。
所以悬置系统必须具有控制发动机相对运动和位移的功能,使发动机始终保持在相对稳定和正确的位置上,决不能让发动机在向各方向运动中与底盘车身上的零件发生干涉和碰撞。
3保护发动机车辆在行驶过程中同时承受着动态负荷和冲击负荷。
悬置系统应具有保护发动机的能力,防止发动机上个别部位因承受过大的冲击载荷而损坏,特别要保证发动机缸体后端面与飞轮壳的结合面上的弯曲力矩不超过制造厂规定的限值。
此外车辆在崎岖道路上行驶时,车架的扭曲变形会使发动机承受扭曲应力,使发动机局部受到损伤。
悬置系统应布置合理,并正确选择软垫刚度等参数,以保证能充分缓冲和抵御外力的冲击并消除薄弱环节。
4克服和平衡因扭矩输出而产生的反作用力悬置系统必须有足够强度,当发动机变速箱总成输出最大扭矩时能克服最大扭矩所产生的最大反作用力。
悬置软垫和支架在这种条件下都必须具有足够的可靠性。
5发动机与底盘之间的连接零件必须有足够柔性这些零件是排气管进气管、燃油管、冷却水管、压缩空气管、油门操纵机构及变速箱操纵机构等。
如果它们的刚度较大,则发动机的振动容易造成这些零件的损坏,特别是在怠速停机和出现共振时表现得尤其剧烈。
另一方面如果它们刚度较大,也会改变发动机悬置系统的刚度和自振频率,从而影响隔振效果并导致噪声升高,因此这些连接件必须采用柔性软管或柔性连接。
发动机-悬置参数设计要求
发动机-悬置参数设计要求根据人体生理学的研究,人体对振动最敏感的频率范围为4~8Hz,车辆的振动特性要保证人的乘坐舒适性,就要避开4~8Hz时的振动。
在车辆设计中,车身-悬挂系统的设计频率一般在1.9~3Hz,簧下质量的振动频率即轴头跳动频率一般在11~15Hz左右,发动机-悬置系统作为一个振动子系统,它其中的悬置是连接发动机和车身的唯一部件,它不但要支承发动机的重量,而且还起到在发动机和车身之间隔振的作用。
悬置的刚度太大,就起不到有效的隔振作用,太软又会降低其使用寿命。
根据隔振原理,发动机-悬置系统振动的频率要大于车身-悬挂频率的1.4倍,才能起隔振作用。
最理想的是2倍以上。
(最大不大于2.5倍) ,因此发动机-悬置系统振动的最低频率要保证不小于3×2=6Hz,其次,发动机动力总成作为整车动力减振器,其垂向振动频率应为轴头跳动频率的0.8~0.9倍,换成频率就是12~13.5Hz,另外,发动机怠速时的转速约为750~800转∕分,对应激励频率为28Hz(四缸机),它要大于发动机动力总成绕曲轴轴线转动频率的2倍,即28∕2=14Hz。
所以,发动机-悬置系统的设计频率就是6~14Hz。
在这个范围内,频率设计区间越小越好。
根据这个设计原理,如果把发动机-悬置系统的频率固定在6~14Hz的话,就要求车架的最低阶频率(一般即为扭转频率)要保证在大于3Hz和小于6Hz之间。
或者大于15Hz以上。
这要根据车辆设计具体的要求而定。
没有统一的模式;但如果发动机悬置的参数达到合理设计(如刚度、布置角度,安装位置等),能够使发动机动力总成-悬置系统的振动频率在6~14Hz内区间更缩小的话,如8~12Hz,那么对车架的频率要求就会宽松一些。
因此,这是一个系统参数优化与合理匹配的问题。
在汽车研究领域,国内还没有成熟的经验和有用的参考数据,还需作长期、大量的工作来解决。
发动机悬置的结构、作用、设计要求
目录发动机悬置的结构、作用、设计要求 (2)1.1 悬置的作用 (2)1.2 悬置的设计要求 (2)1.3 悬置的设计结构 (2)1.4 悬置的布置 (5)1.5 悬置系统设计程序 (9)1.1 悬置系统安装要求 (10)发动机悬置的结构、作用、设计要求1.1 悬置的作用悬置元件既是弹性元件又是减振装置,其特性直接关系到发动机振动向车体的传递,并影响整车的振动与噪声。
1.2 悬置的设计要求1.2.1 能在所有工况下承受动、静载荷,并使发功机总成在所有方向上的位移处于可接受的范围内,不与底盘上的其他零部件发生干涉。
同时在发动机大修前,不出现零部件损坏。
1.2.2 能充分地隔离由发动机产生的振动向车架及驾驶室的传递,降低振动噪声。
1.2.3 能充分地隔离由于路面不平产生的通过悬置而传向发动机的振动,降低振动噪声。
1.2.4 保证发动机机体与飞轮壳的连接面弯矩不超过发动机厂家的允许值。
1.3 悬置的设计结构1.3.1 发动机悬置软垫的设计-金属板件和橡胶组成1.3.1.1 悬置软垫的负荷通常前悬置位于发功饥机体前端或机体前部两侧,与后悬置相比、远离动力总成的质心,因此动力总成的垂直静负荷主要由后悬置承担,而前悬置主要承受扭转负荷。
对后悬置来说.距离动力总成的主惯性轴较近,承受较小的扭转负荷及振幅。
同时,由于它处于发动机动力输出端,受传动系不平衡力的严重干扰和外部轴向推力的冲击,当发动机输出最大转矩时.支承点出现的最大反作用力也应由后悬挂来承担。
所以后悬置的垂直刚度较大,也起着限制动力总成前后位移的作用。
悬置系统同样还承受了汽车行驶在平平道路上的颠簸、冲击、汽车制动及转向时所产生的动负荷。
1.3.1.2 悬置软垫的机构形式在设计发动机悬置时。
必须充分的考虑悬置的使用日的,例如支承的质量和限制的位移等,选择合理的形状。
悬置的基本形式有三中,即压缩式、剪切式和倾斜式。
给出了这二种悬置的基本特性及用途。
通常采用倾斜式的悬置结构,利用这种悬置的弹性特性,支点设定可以获得较大的自由度。
汽车发动机悬置系统的设计指南
1 发动机悬置系统的设计指南1.1 悬置系统的设计意义及目标简介现代汽车发动机无一不是采用弹性支承安装的,这在汽车行业称之为“悬置”,在力学及振动工程中则是个隔振问题。
如果不用中间弹性元件而直接将发动机刚性地固紧在汽车车架(底盘)上,则当汽车在不平坦的路面上行驶时将导致机身由于车架的变形、冲击而损坏;而当汽车在平坦光滑的路面上行使时来自发动机的振动将导致车架、车身产生令人厌恶的结构噪声。
此外弹性悬置还能补偿在发动机安装及运动过程中由车架变形导致的相对位置的不精确。
由此可知,悬置系统的设计目标值:1) 能在所有工况下承受动、静载荷,并使发动机总成在所有方向上的位移处于可接受的范围内,不与底盘上的其它零部件发生干涉;2) 能充分地隔离由发动机产生的振动向车架及驾驶室的传递,降低振动噪声;3) 能充分地隔离由于地面不平产生的通过悬置而传向发动机的振动,降低振动噪声;4) 保证发动机机体与飞轮壳的连接弯矩不超过发动机厂家的允许值。
1.2 悬置系统的布置方式选择每个隔振器(悬置系统)不论其结构形状如何都可以看作由三个相互垂直的弹簧组成,按照这三个弹簧的刚度轴线和参考坐标轴线间的相对位置关系,悬置系统弹性支承的布置可以有常见的三种不同方式:1) 平置式。
这是常用的、传统的布置方式,其特征是布局简单、安装容易。
在这种布置方式中,每个弹性支承的三个相互垂直的刚度轴各自对应地平行于所选取的参考坐标轴。
2) 斜置式。
这是一种目前汽车发动机中用得最多的布置方式。
在这种布置方式中,每个弹性支承的三个相互垂直的刚度轴相对于参考坐标轴的布置是:除一个轴平行于参考坐标外,其他两个轴分别与参考坐标轴有一夹角。
一般斜置式的弹性支承都是成对地对称布置于垂向纵剖面的两侧,但每对之间的夹角可以不同,坐标位置也可任意。
这种布置方式的最大优点是:它既有较强的横向刚度,又有足够的横摇柔度,因此特别适用于象汽车发动机这样既要求有较大的横向稳定性,又要求有较低的横摇固有频率以隔离由不均匀扭矩引起的横摇振动。
- 1、下载文档前请自行甄别文档内容的完整性,平台不提供额外的编辑、内容补充、找答案等附加服务。
- 2、"仅部分预览"的文档,不可在线预览部分如存在完整性等问题,可反馈申请退款(可完整预览的文档不适用该条件!)。
- 3、如文档侵犯您的权益,请联系客服反馈,我们会尽快为您处理(人工客服工作时间:9:00-18:30)。
发动机悬置设计5.1 概述汽车的乘坐舒适性——NVH(Noise-噪声、Vibration-振动和 Harshness-声振舒适性)越来越受到人们的重视和关注,因为噪声、振动和舒适性,是衡量汽车制造质量的一个综合问题,它给汽车用户的感觉是最直接和最表面的。
作为汽车动力源的发动机是汽车主要的振动激励源之一,其气缸燃气压力、转速及输出转矩的周期性波动及不平衡惯性力(矩)既激起发动机动力总成本身的刚体振动和弹性振动,又激起汽车动力传动的扭转振动和弯曲振动等,从而导致十分严重的振动、噪声及结构问题,最终传递给车身,引起整车振动与噪声。
汽车动力总成悬置系统是指动力总成(包括发动机、离合器及变速箱等)与车架或车身之间通过弹性悬置元件连接而成的系统,发动机动力总成的振动与路面激励力是通过弹性悬置元件传给车身,该项系统性能设计的好坏直接关系到发动机振动向车体的传递,影响整车的 NVH 特性。
因此,最大限度的减小发动机动力总成所产生的振动及噪声向车身传递,是汽车减振和降噪的主要研究内容之一。
5.2、悬置系统功能介绍5.2.1悬置总成的功用a)悬置系统的首要作用即最基本的作用是支承动力总成的动、静载荷,并使发动机动力总成在所有方向上的位移处于可接受的范围内,不与前舱内其它零部件发生干涉;b)隔离发动机动力总成的振动,最大限度地降低从发动机动力总成传递到车身/车架上的振动,能有效的降低振动及噪音;c)在汽车做紧急制动、加速或受其它外界负荷的作用下时,发动机不应有过大的位移;d)隔离由于轮胎及车身的抖动而产生的振动和噪音通过悬置系统而传向发动机动力总成,降低振动及噪音;e)悬置系统元件需有足够的使用寿命。
5.3 动力总成悬置系统设计方法5.3.1 设计需解决的问题a)主要起支撑减振的作用,因而,悬置必须要能够支撑起动力总成,并且保证其三个方向的位移和绕三个轴的转角在一定的限度内;b)发动机自身振动的隔离,即不让发动机不平衡力所造成的振动过分地传向车向车身,这就要求各悬置的固有频率与各激励源的频率必须满足f i f IDLE / 2的条件,其中,f i为各悬置的固有频率,f IDLE为怠速时各激励源的频率。
车身结构振动的降低,十分有利于降低结构的噪声辐射。
c)路面的激励下发动机的晃动问题。
即在低频段内,发动机固有频率与整车特性不匹配时,路面激励所造成的发动机晃动可能引起汽车乘坐舒适性问题,也可能影响到汽车的操纵舒适性。
5.3.2 主要设计参数的决定因素和最优化的目标a)布置空间,悬置系统的设计很大程度上受到布置空间的制约,由于轿车的前舱一般空间很有限,加上其它系统如排气系统、进气系统、冷却系统及转向系统及空调系统等都在前舱内布置,所以悬置系统首先要满足布置上的要求;b)发动机的工作模态,由于发动机的工作频率很宽,通过改变悬置元件的刚度、安装位置、安装角度以及改变悬置元件的阻尼系数,合理的匹配发动机动力总成悬置系统的各向固有频率,最大限度发挥现有悬置元件的潜能,以达到减振的目的。
5.3.3 满足的工作环境悬置系统的工作条件一是持续承受动力总成的重量,克服传动轴对动力总成的反作用扭矩,二是承受发动机工作时的前舱高温(约 100ºC),三是承受整车启动后一定频率的来自动力总成和车轮的激励振动。
5.3.4 发动机动力总成设计的基本步骤a) 动力总成悬置系统方案布置设计,这时,需要了解的是项目背景及与整车项目相关的一些信息,比如,整车设计的市场定位,对悬置系统的要求(包括成本投入,综合性能的目标等),前舱的边界条件及悬置系统的布置方案的选择等;因为悬置系统与动力总成的结构及特性有很大的关系,为了便于组建数据库,需在设计前期就必需了解动力总成的特性(比如,发动机的型号,变速箱的型号,动力总成(或发动机与变速箱)的重量,重心点坐标及转动惯量等;b)动力总成悬置系统零部件的概念设计,依据总布置给的边界条件及动力总成的特性及转动惯量,利用相应的理论指导(如撞击中心理论、刚度矩阵解耦法、能量解耦法等),来确定悬置系统的布置方式及悬置点的布置位置。
c)动力总成悬置系统零部件的详细设计,依据悬置系统概念设计过程中得到的边界数模,并利用相应的软件(如 ADAMS、NASTRA、NANSYS、CAE 等)分析为指导,以发动机动力总成悬置系统的固有频率的合理分布为目标,详细设计悬置系统各零部件工艺数模、细化二维图纸及初步确定悬置系统各方向上的动、静刚度值,这时除了要更新《设计构想书》及《零部件清单》之外,《技术装配说明书》、DVP、DFME、专利分析等需在此阶段完成。
d)发动机动力总成悬悬置系统零部件试制,按照数模(或图纸)及相关的标准在规定的时间内制造合格的工装(或手工)样件,此时需按需要装配几台准备作试验用的样机;e)动力总成悬置系统零部件验证(包括台架试验、悬置系统 CAE 分析及整车 NVH 性能试验等),通过对悬置系统进行台架、相关的性能分析及测试,检测动力总成悬置系统在各个工况下的工作特性、隔振及对噪音的衰减性能,这一般由供应商和整车厂共同进行,并对试验结果进行分析,得出进一步优化动力总成悬置系统的方案,由于发动机动力总成系统的工作频率是一个很宽的范围(一般会在 10~500Hz 之间),并且要求悬置系统在低频大振幅(如发动机怠速状况)提供大的阴尼特性,而在高频低幅振动激励下提供低的动刚度特性,以衰减高频噪声。
可是实际上悬置系统由于受到材料(特别是橡胶悬置)的限制,很难满足动力总成各工作模态下的要求,我们的目标就是最大范围的满足动力总成常见工作模态下响应,f)动力总成悬置系统改进优化,依据台架试验数据、CAE 分析的反馈信息及整车测试的结果对动力总成及悬置系统进行分析,优化悬置元件的结构及橡胶的动、静刚度,以达到满足整车 NVH 及相关的综合性能,此时,相关的文件(比如数模,二维图,动、静刚度曲线图都需及时更新);g)对动力总成悬置系统再一轮的样件制作及试验验证,至到达到相关的国家标准及满意的效果为止;5.3.5 设计发动机动力总成悬置系统还应注意的其它几个因素a)影响装配位置因素,因悬置元件大多为铸造件及冲压件,因其结构的不规则性,在进行悬置系统详细设计时需要考虑悬置系统的可装配性;b)修理的方便性,指在进行悬置系统详细设计时不仅要考虑悬置系统的可装配性,还要考虑悬置软垫的更换及对动力总成进行保养时的方便动力总成的拆卸和安装。
5.4、悬置系统的布置5.4.1 悬置系统布置的要求及依据要保证悬置本身在保证结构强度的前提下不与其他件干涉,要考虑到运动过程中橡胶件为弹性体,悬置位置必定会有约 10~20mm 左右的变动。
二是要保证由悬置限制位置的动力总成不与周围车身件和发动机附件干涉,尤其注意与燃油管路,传动轴等安全件的干涉;悬置点的数目及其位置选择,汽车发动机的悬置系统多采用三点或四点支承。
一般较老式的发动机多在风扇端设置一个或两个支承点,而在飞轮端设置两个支承点;新式的则反过来,在风扇端设置两个支承点,而在飞轮端则放一个或两个。
这主要是根据发动机类型(是汽油机还是柴油机),前后承载重量分配以及激振力情况而定的。
三点支承的优点是不管汽车怎样颠簸、跳动,它总能保证各支承点处在一个平面上,这就大大改善了机体的受力情况,目前有很多汽车发动机即使是采用四点支承的也力求将飞轮端的那两点尽量靠拢,以达到三点支承的效果。
此外三点悬置系统,通过合理设计可以达到上下方向、扭转振动的独立解耦,从而大幅减小了耦合振动。
其中左右悬置通常接近扭转惯性轴位置布置,特别支持上下方向的振动解耦。
右悬置通常采用效果更佳的液压悬置,与发动机连接布置,支持隔离发动机燃烧激励、惯性力激励、路面激励。
左悬置通常就采用普通的橡胶悬置,与变速箱连接布置,在隔离激振的同时起到动力总成限位的作用。
后悬置通常与变速箱连接布置,承受扭矩,重点起到动力总成的纵向限位。
四点悬置系统,同样可以达到上下方向、扭转振动的独立解耦,从而大幅减小了耦合振动的要求。
其中左右悬置也接近扭转惯性轴位置布置,特别支持上下方向的振动解耦。
前后悬置主要承受由行驶工况引起的扭矩,重点起到动力总成的纵向限位。
相对于三点悬置系统,四点悬置系统的优点是发动机摇振和怠速工况振动效果良好,但此种布置中前后悬置的刚度变化将引起发动机位置变化,导致怠速的预载变化,其次通常需要前横梁支撑前悬置,导致减振效果的下降。
通常在选择支承点的布置位置时除了要满足整车布置协调、系统解耦条件外还有两个问题需要考虑:一是打击中心问题。
设计良好的悬置系统发动机本身的运动即使是在恶劣的道路条件下也不会很大,且隔振器也不会遭受过大的动载荷。
但在有些发动机中,如直列式四缸发动机,当曲柄间隔为 180 度时存在着严重的二次不平衡惯性力,由它将引起机组剧烈的纵摇振动。
在这种情况下如应用打击中心理论将发动机的前支承布置在激振力的作用平面内(气缸体的横向中心面处),后支承布置在打击中心处,就可以大大减轻激振力通过后支承向车身的传递,有效地减小汽车振动。
二是机身一阶弯曲振动问题。
现代汽车发动机机组作为一个弹性体其一阶弯曲振动的固有频率并不是很高的,而功率强大的发动机的高频段的激励频率却是很丰富的,因此很有可能导致机身产生一阶弯曲振动共振。
在这种情况下如能将支承点安置在振型曲线的节点处,对于减轻隔振器的附加载荷是很有利的。
5.4.2 发动机动力总成悬置系统布置图举例图 a 常见的四点悬置布置形式如图 a 为常见的四点悬置布置形式,前、后、左、右各一点,左、右悬置承受动力总成的绝大部分重量,并且布置在动力总成的扭矩轴附近,前、后悬置点布置在动力总成弯曲振形的节点上,可以起到限制动力总成的扭转并使悬置软垫变形量最小。
动力总成悬置系统一般存在着弹性耦合和惯性耦合,各悬置点布置遵循以上原则外,还应从动力总成的模态解耦上考虑,应尽量使悬置点的弹性中心与发动机动力总成的重心重合。
图 b 典型的三点悬置软垫的结构形式如图 b,LHS 为悬置轴线垂直布置,该结构有利于提高 Y 向刚度;RHS 轴线水平布置,有利于提高 Z 向刚度,ROD 为扭力杆,其只限制 X 方向的刚度,运动的顺从性好,避免造成车身的扭曲。
单个零件的结构选择首先考虑的是在允许悬置布置的空间内灵活构思,完成结构设计,整个悬置系统就必须考虑各个方向的刚度限制,图 4.2.2 所示的系统由于 XYZ 三个方向的刚度都能得到保证,因而该系统是一个成功布置的典型范例。
5.4.3 悬置与周边间隙布置举例由于前舱温度较高,要求前悬置与排气管间隙≥50mm。
为了防止发动机侧倾影响,一般要求右悬置与皮带轮间隙≥10mm。
考虑传动轴的跳动与发动机的振动,要求后悬置与传动轴间隙≥35mm。