复合材料课件第五章 钛基复合材料-镁基复合材料
复合材料应用PPT课件

石墨烯/铜 复合材料
石墨烯/银 复合材料
石墨烯是目前发现的唯一存在的一种由碳原子致密堆积而成的二维蜂窝状晶格结构的环 保型碳质新材料,具有超大比表面积(2630 m 2/g),是目前已知强度最高的材料(达130 gpa)。
美国科学家研发了一 种全新的金属材料,能够 漂浮在水面上。在设计上, 这种镁合金基复合材料利 用中空碳化硅颗粒进行加 固,密度只有每立方厘米 0.92克,相比之下,水的 密度为每立方厘米1克。 无论是制造船只甲板、汽 车零部件、浮力模块还是 车辆装甲,这种新材料都 拥有广阔的应用前景
应力工ቤተ መጻሕፍቲ ባይዱ下的耐高温材料。
陶瓷基复合材料(CMC)由于其本身耐温高、密度低的优势,在航空发动机上的应用 呈现出从低温向高温、从冷端向热端部件、从静子向转子的发展趋势。 CMC材料具有耐温 高、密度低、类似金属的断裂行为、对裂纹不敏感、不发生灾难性损毁等优异性能,有望取 代高温合金满足热端部件在更高温度环境下的使用,不仅有利于大幅减重,而且还可以节约 甚至无须冷气,从而提高总压比,实现在高温合金耐温基础上进一步提升工作温度400~ 500℃,结构减重50%~70%,成为航空发动机升级换代的关键热结构用材。
树脂基复合材料在国外先进航空发动机冷端上的主要应用部位
树脂基复合材料在短舱的主要应用部位
树脂基复合材料由于其优异的比强度和比刚度,最初应用于航空航 天领域,目前正在快速商业化到其他行业,如汽车和体育用品行业。树 脂基复合材料通过成分设计和结构设计,实现特殊应用,这种功能定制 设计能实现许多其他功能,如电、热、光和/或磁性性能。MGI列出了 树脂基复合材料的9个重点发展方向。
复合材料pdfPPT课件

良好的热导性
某些复合材料具有良好的热导性,适用于需要散热或传热的场合。
耐高温性能
通过选择合适的基体和增强材料,复合材料可以在高温环境下保持 较好的力学性能。
电学性能
绝缘性能
大多数复合材料具有良好的绝缘性能,适用于电气 和电子设备中。
后处理与加工
固化处理
对成型的复合材料进行加热或自然固化,使其达到所需的物理和化 学性能。
机械加工
对固化后的复合材料进行切割、钻孔、打磨等机械加工,以满足产 品形状和尺寸的要求。
表面处理
对复合材料表面进行喷漆、电镀、阳极氧化等处理,以提高其耐腐蚀 性、装饰性等性能。
04
复合材料的性能特点
力学性能
成型工艺
手糊成型
在模具上涂刷脱模剂,然后铺贴一层纤 维布或毡,再涂刷一层树脂,如此反复
直至达到所需厚度。
模压成型
将预浸料或纤维与树脂混合物放入模 具中,在加热和加压的条件下固化成
型。
喷射成型
将树脂和固化剂分别通过喷嘴喷到模 具上,同时用喷枪将纤维切断并喷到 树脂中,形成复合材料层。
注射成型
将树脂和固化剂混合后注入到装有纤 维的模具中,然后在一定温度和压力 下固化成型。
复合材料的组成与结构
基体材料
聚合物基体
如环氧树脂、聚酰亚胺等,具有良好的可加工性和韧 性。
金属基体
如铝、镁、钛等合金,具有高比强度和优异的导电导 热性能。
陶瓷基体
如氧化铝、氮化硅等,具有高温稳定性和耐磨损性。
增强材料
纤维增强材料
如碳纤维、玻璃纤维、芳纶纤维等,具有高比 强度和模量。
复合材料概述PPT课件
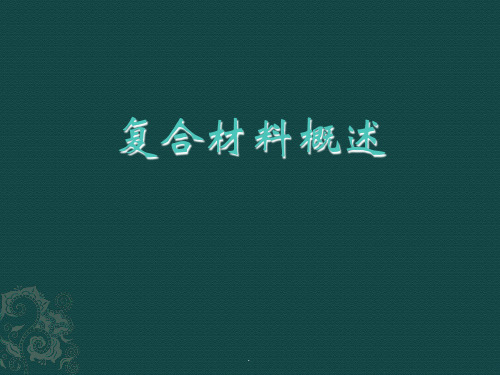
.
2、高温力学性能 室温下,复合材料的抗弯强度比基体材料高约10倍,弹性模
量提高约2倍。复合材料的抗弯强度至700℃保持不变,然 后强度随温度升高而急剧增加;但弹性模量却随着温度升 高从室温的137GPa降到850℃的80 GPa。这一变化显然与 材料中残余玻璃相随温度升高的变化相关。
其中一个组分是细丝(连续的或短切的)、薄片或颗粒 状,具有较高的强度、模量、硬度和脆性,在复合材料承受 外加载荷时是主要承载相,称为增强相或增强体。增强相或 增强体在复合材料中呈分散形式,被基体相隔离包围,因此 也称作分散相;复合材料中的另一个组分是包围增强相并相 对较软和韧的贯连材料,称为基体相。
1、室温力学性能
对陶瓷基复合材料来说,陶瓷基体的失效应变低于纤维的 失效应变,因此最初的失效往往是基体中晶体缺陷引起 的开裂。 材料的拉伸失效有两种:
第一:突然失效。如纤维强度较低,界面结合强度高,基 体较裂纹穿过纤维扩展,导致突然失效。
第二:如果纤维较强,界面结合较弱,基体裂纹沿着纤维 扩展。纤维失效前纤维/基体界面在基体的裂纹尖端和尾 部脱粘。
.
复合材料是由多相材料复合而成,共同特点主要有三个:
(1)综合发挥各种组成材料的优点,使一种材料具有多种性能, 具有天然材料所没有的性能。例如,玻璃纤维增强环氧基复合材料, 既具有类似钢材的强度,又具有塑料的介电性能和耐腐蚀性能。
(2)可按对材料性能的需要进行材料的设计和制造。如,针对方向性 材料强度的设计,针对某种介质耐腐蚀性能的设计等。 (3)可制成所需的任意形状的产品,可避免多次加工工序。例如,可 避免金属产品的铸模、切削、磨光等工序。
陶瓷基复合材料具有优异的耐高温性能,主要用作高温及耐磨 制品。其最高使用温度主要取决于基体特征。陶瓷基复合材料 已实用化或即将实用化的领域有刀具、滑动构件、发动机制件 、能源构件等。法国已将长纤维增强碳化硅复合材料应用于制 造高速列车的制动件,显示出优异的摩擦磨损特性,取得满意 的使用效果。
《复合材料》PPT课件(2024)

复合材料能够抵抗循环载荷作用下的疲劳破坏,具有较长的疲劳寿命, 适用于承受交变应力的结构件。
2024/1/26
03
良好的减震性能
Hale Waihona Puke 复合材料具有较好的阻尼性能,能够吸收和分散振动能量,降低结构的
振动和噪音水平。
16
物理性能
耐高低温性能
复合材料能够在极端温度环境下保持稳定的性能,适用于高温或低 温工作条件。
2024/1/26
25
建筑领域应用
建筑结构
复合材料可用于制造建 筑结构部件,如梁、板 、柱和墙体等,具有轻 质、高强度和耐腐蚀等 优点。
2024/1/26
建筑材料
复合材料还可作为建筑 材料使用,如复合地板 、复合门窗和复合墙板 等,具有美观、环保和 耐用等特点。
装饰装修
复合材料也可用于建筑 装饰装修领域,如吊顶 、隔断和家具等,具有 多样化的外观和优良的 性能。
X射线衍射(XRD)
分析复合材料的晶体结构和相组成,确定增 强体和基体的晶体类型。
2024/1/26
透射电子显微镜(TEM)
揭示复合材料内部微观结构,如增强体的分 布、取向和缺陷等。
原子力显微镜(AFM)
研究复合材料表面纳米级形貌和力学性质。
20
宏观性能测试方法
拉伸试验
测定复合材料的拉伸强度、弹性模量 和断裂伸长率等力学性能指标。
性能变化。
疲劳试验
2024/1/26
研究复合材料在交变应力作用下的疲 劳性能,预测其疲劳寿命和疲劳强度
。
耐化学腐蚀试验
测试复合材料在不同化学介质中的耐 腐蚀性能,评估其耐酸、耐碱、耐盐 雾等能力。
加速老化试验
金属基复合材料(MMC)
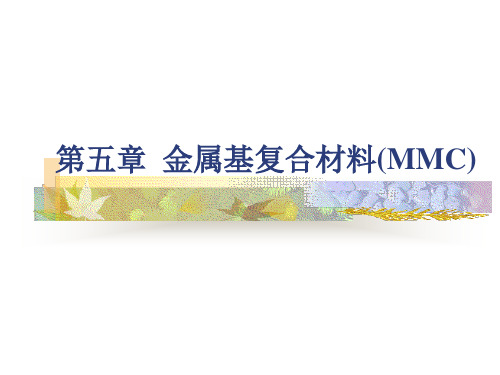
3.熔渗
将增强材料制成多孔预制体,置基体金属熔 体的上方或内部,利用毛细力的使熔体作用渗 入预制中。也可将预制体和基体金属坯料装入 一可通入流动氮气的加热炉中。通过加热,基 体金属熔化,自发渗透入网络状增强材料预制 体中
三、喷涂与喷射沉积
喷涂沉积主要应用于纤维增强金属基复合材 料的须制层的制备,也可以获得复合层状复合 材料的坯料。喷射沉积则主要用于制备颗粒增 强金属基复合材料。喷射与喷涂沉积工艺的最 大特点是增强材料与基体金属的润湿性要求低; 增强材料与熔融金属基体的接触时间短,界面 反应量少。喷涂沉积制备纤维增强金属基复合 材料时,纤维的分布均匀,获得的薄单层纤维 增强预制层可以很容易地通过扩散结合工艺形 成复合材料结构形状和板材。喷涂与喷射沉积 工艺,可以与各种陶瓷纤维或颗粒复合,即基 体金属的选择范围广。
高温性能优良。合金化后的耐热性显著提高,可以作为 高温结构材料使用,如航空发动机的压气机转子叶片等, 长期使用最高温度已达540℃
在大气和海水中有优异的耐蚀性.在硫酸、盐酸、硝酸 相氢氧化纳等介质中都很稳定
导电与导热性差.导热系数只有铜的1/l 7和铝的l/10, 比电阻为铜的25倍
常用钛合金的性能
第五章 金属基复合材料(MMC)
第一节 概 述
一、MMC的沿革与发展
二、MMC的分类
1、按增强材料形态分类 纤维增强金属基复合材料 颗粒和晶须增强金属基复合材料 2、按金属基体分类 铝基复合材料 钛基复合材料 镁基复合材料 高温合金复合材料 金属间化合物复合材料
第二节 金属基体
热压
在真空或保护气氛下直接放入热压模 或平板进行热压合热压工艺参数主要为: 热压温度、压力和时间
扩散结合的优缺点:
【大学课件】复合材料PPT

.
28
③ 基体金属与增强物的相容性
金属基复合材料需要在高温下成型,制备 过程中,处于高温热力学非平衡状态下的纤维与 金属之间很容易发生化学反应,在界面形成反应 层。界面反应层大多是脆性的,当反应层达到一 定厚度后,材料受力时将会因界面层的断裂伸长 小而产生裂纹,并向周围纤维扩展,容易引起纤 维断裂,导致复合材料整体破坏。
• 仿照骨骼的组织特点,人们制造了类似结构的风力发电机和 直升飞机的旋翼,外层是刚度、强度高的碳纤维复合材料, 中层是玻璃纤维增强复合材料、内层是硬泡沫塑料。
.
20
9.3 复合材料的基体材料
复合材料的原材料: • 基体材料
– 金属材料 – 陶瓷材料 – 聚合物材料
• 增强材料
– 纤维 – 晶须 – 颗粒
则、增韧机制和界面作用; • 了解复合材料的成型工艺。
.
3
参考书目
• 王荣国 主编,复合材料概论,哈尔滨工业大学 出版社,1999
• 闻荻江主编,复合材料原理,武汉理工大学出 版社,1998
• 鲁云,先进复合材料,机械工业出版社,2004 • ASM International, Engineered materials
– 基体主要是镍基、铁基耐热合金和金属间化合物。较成熟 的是镍基、铁基高温合金,金属间化合物基复合材料尚处 于研究阶段。
.
31
9.3.1.3 功能用金属基复合材料的基体
• 要求材料和器件具有优良的综合物理性能,如同时具 有高力学性能、高导热、低热膨胀、高导电率、高抗 电弧烧蚀性、高摩擦系数和耐磨性等。
Chapter 9 Composites
复合材料
.
1
本章内容
1. 复合材料概述 2. 复合材料分类 3. 复合材料的基体 4. 复合材料的增强相 5. 复合材料的复合原理 6. 复合材料的成型工艺
复合材料课件第五章 钛基复合材料-镁基复合材料
应用: 超高音速宇航飞行器和先进航空发动机 Ti-47Al-2V-7%TiB2作用导弹翼片 汽车工业
航空发动机叶轮
②连续纤维增强钛基复合材料
增强体: SiC、TiC、 SiC包覆硼纤维、耐高温的金属纤维。 制备方法:
复合难度大,只能采用固相法合成,后用热等静压、真 空热压锻造方法压实成形。 制备方法:交替叠轧法、等离子喷涂、高速物理气相沉积法
Al2O3纤维
涂覆Y2O3 (~1m厚)
涂覆W (~0.5m厚)
电镀镍层 (~0.5m厚)
纤维排布在镍 基合金薄板之间
真空加压 扩散结合法
Al2O3f/Ni3Al复合材料
镍基复合材料的性能
图5-3 Al2O3/Ni3Al,Ni3Al基体(真空热压+热挤压) 以及铸造Ni3Al的比屈服强度和温度的关系
布 应
均 小
匀 ,
, 利
基体组织不均匀, 易损伤纤维,合 金成分不可控
高速物理气相沉 积
单根纤维涂一层 纤维分布均匀,
基体粉,叠起来 无聚集,纤维体
热压成型
积含量高
合金成分不可控
电子束蒸涂
同上
涂层速度高
金属利用率低
三极管溅射 磁控溅射
同上 同上
金属利用率高 金属利用率高
沉积速度低 沉积速度低
性能: 各向异性很强,横向拉伸强度仅为纵向的30~45%, 纵向拉伸强度比基体高得多。 纵向:提高弹性模量、拉伸、蠕变强度
基体: 纯镍、镍铬合金、镍铝合金
Ni3Al合金的屈服强度具有反 常的温度关系,在600℃左 右达到最大。
NiAl合金具有高熔点、低密 度及极佳的抗氧化性能。
增强体: Al2O3、SiC 颗粒、晶须、纤维 TiC和TiB2颗粒 W丝
第五章 金属基复合材料
• 用于集电和电触头的金属基复合材料有:碳(石墨)纤
维或颗粒、金属丝、陶瓷颗粒增强铝、铜、银及合金等 金属基复合材Βιβλιοθήκη 。三、金属基复合材料的性能特征
金属基复合材料的性能取决于所选的金属或合金基体和 增强体的特性、含量、分布等。通过优化组合可以既发挥 金属特性,又具有高比强度、高比模量、耐热、耐磨等综 合性能。其主要的性能特点有: 高比强度、比模量 良好的断裂韧性和抗疲劳性能 热膨胀系数小、尺寸稳定性好 良好的导电、导热性能 良好的高温性能 良好的耐磨性与阻尼性 性能再现性及可加工性好 不吸潮、不老化、气密性好
合金以及金属间化合物作为基体材料。如碳化硅/钛、钨丝/镍基超合
金复合材料可用于喷气发动机叶片、转轴等重要零件。
汽车发动机:要求其零件耐热、耐磨、导热、一定的高温强
度等,同时又要求成本低廉,适合于批量生产,因此选用铝合金作基 体材料与陶瓷颗粒、短纤维组成颗粒(短纤维)/铝基复合材料。如碳 化硅/铝复合材料、碳纤维或氧化铝纤维/铝复合材料可制作发动机活
•
Cgr/Al基复合材料在500℃高温下,仍具有600MPa的强 度,而铝基体在300℃时强度已下降到100MPa以下; Wf/耐热合金,在1100℃/100h下持久强度为207MPa, 而基体耐热合金在同样条件下的持久强度只有48MPa.
•
•
硼纤维增强铝在近400 ℃温度下仍有较好的高温比强度。
第四章
金属基复合材料
(Metallic Matrix Composites)
主要内容
一、基本概念和分类
二、金属基体
三、金属基复合材料的性能特征 四、金属基复合材料的界面及优化 五、金属基复合材料的制备工艺 六、铝基复合材料 七、镁基复合材料 八、钛基复合材料 九、镍基复合材料
金属基复合材料ppt课件
(3)、热膨胀系数小、尺寸稳定性好
金属基复合材料中的碳纤维、碳化硅纤维、晶须、颗 粒、硼纤维等均具有很小的热膨胀系数,又具有很高的 模量,特别是高模量、超高模量的石墨纤维具有负的热 膨胀系数。加入相当含量的增强物不仅大幅度提高材料 的强度和模量,也使其热膨胀系数明显下降,并可通过 调整增强物的含量获得不同的热膨胀系数,以满足各种 应用的要求。
铝基复合材料是在金属基复合材料中应用得最广
的一种。由于铝的基体为面心立方结构,因此具有良好的塑 性和韧性,再加之它所具有的易加工性、工程可靠性及价格 低廉等优点,为其在工程上应用创造了有利的条件。
在制造铝基复合材料时,通常并不是使用纯铝而是用各 种铝合金。
铝基复合材料
• 大型运载工具的首选材料。如波音747、757、767 • 常用:B/Al、C/Al、SiC/Al • SiC纤维密度较B高30%,强度较低,但相容性好。 • C纤维纱细,难渗透浸润,抗折性差,反应活性较高。 • 基体材料可选变形铝、铸造铝、焊接铝及烧结铝。它们
(2)、导热导电性能
虽然有的增强体为绝缘体,但在复合材料中占 很小份额,基体导电及导热性并未被完全阻断, 金属基复合材料仍具有良好的导电与导热性。
为了解决高集成度电子器件的散热问题,现已 研究成功的超高模量石墨纤维、金刚石纤维、金 刚石颗粒增强铝基、铜基复合材料的热导率比纯 铝、铜还高,用它们制成的集成电路底板和封装 件可有效迅速地把热量散去,提高了集成电路的 可靠性。
氧化铝和硅酸铝短纤维增强铝基复合材料的室温 拉伸强度并不比基体合金高,但它们的高温强度明显 优于基体,弹性模量在室温和高温都有较大的提高, 热膨胀系数减小,耐磨性能得到改善。
• 纤维增强复合材料的强度和刚性与纤维方向密纤维使材料具有明显的各向异性。纤维采 用正交编织,相互垂直的方向均具有好的性能。纤维 采用三维编织,可获得各方向力学性能均优的材料。
镁基复合材料讲稿
镁基复合材料讲稿镁基复合材料镁基复合材料密度小,仅为铝或铝基复合材料的2/3 左右,具有高的比强度和比刚度以及优良的力学和物理性能,在新兴高新技术领域中比传统金属材料和铝基复合材料的应用潜力更大,因此,自20 世纪80 年代末,镁基复合材料已成为金属基复合材料领域的研究热点之一。
今天我们组将简要介绍下镁基复合材料的组成,制备方法,性能,应用现状以及镁基复合材料研究领域存在的问题,并对它的研究发展趋势做了展望。
首先我们从材料科学的四要素结构、性能、加工和使用状况出发,简单的了解下镁基复合材料。
先看镁基复合材料结构组成镁基复合材料主要由镁合金基体、增强相和基体与增强相间的接触面——界面组成。
基体有镁合金、铸镁和镁化合物,因纯镁强度低,不适于作为镁基复合材料的基体,一般需要添加合金元素进行合金化。
常用基体合金目前主要有:Mg-A1,Mg-Mn,Mg-Li ,高强度基体Mg-Zn,Mg-Zr,于较高温度下工作的合金系Mg-Re、Mg-Ag,此外,还有用于储氢的Mg-Ni。
镁基复合材料根据其使用性能选择基体合金,侧重铸造性能的可选择铸造镁合金为基体;侧重挤压性能的则一般选用变形镁合金。
主要合金元素有A1、Zn、Li、Ag、Zr、Th、Mn、Ni 和稀土金属等,其中A1、Zn、Li 最为常用。
它们在镁合金中具有固溶强化、沉淀强化、细晶强化等作用。
增强相选择要求与铝基复合材料大致相同,都要求物理、化学相容性好,润湿性良好,载荷承受能力强,尽量避免增强相与基体合金之间的界面反应等。
常用的增强相主要有C 纤维、Ti 纤维、B 纤维,Al2O3短纤维,SiC晶须,B4C 颗粒、SiC颗粒和A12O3颗粒等。
长纤维增强金属基复合材料性能好,但造价昂贵,不利于向民用工业发展,另外其各向异性也是阻碍因素之一.颗粒或晶须等非连续物增强金属复合材料各向同性,有利于进行结构设计,可以二次加工成型,可进一步时效强化,并具有高的强度,模量,硬度,尺寸稳定性,优良的耐磨、耐蚀、减振性能和高温性能,巳日益引起人们的重视.由于镁及镁合金比铝和铝合金化学性质更活泼,因而所用增强相与铝基复合材料不尽相同。
- 1、下载文档前请自行甄别文档内容的完整性,平台不提供额外的编辑、内容补充、找答案等附加服务。
- 2、"仅部分预览"的文档,不可在线预览部分如存在完整性等问题,可反馈申请退款(可完整预览的文档不适用该条件!)。
- 3、如文档侵犯您的权益,请联系客服反馈,我们会尽快为您处理(人工客服工作时间:9:00-18:30)。
材料
AZ91
Vf/%
0
SiCW/AZ91(酸性 21 磷酸铝粘结剂)
SiCW/AZ91(硅胶 21 粘结剂)
SiCW/AZ91
22
σ0.2/MPa
102 240
236
223
σb/MPa
205 370
332
325
伸长率/%
6.00 1.12
E/GPa
46 86
0.82
80
1.08
81
与基体合金AZ91相比, SiCW/AZ91的屈服强度、拉伸 强度和弹性模量均大大提高,而伸长率下降。
性能 各向同性 提高方面: 硬度、耐磨性、刚度、高温强度好
降低方面: 塑性、断裂韧性、耐疲劳性能、室温强度与基体相
近或更差。
TiC和SiC颗粒增强钛基复合材料的力学性能
①增室强温T下M,CST拉iC伸增强强度的比T基MC体S的还拉低。伸强度与基体相近,SiC颗粒 ②在高温下,颗粒增强TMCS拉伸强度均比基体高。 ③料基的体塑的性断与裂基伸体长相率比均下大降于。颗粒增强TMCS,这表示此复合材
制备方法:
挤压铸造法
(1)制备预制块
搅拌铸造法:
搅拌铸造法制备镁合金复合材料示意图
粉末冶金法: 粉末冶金工艺流程
SiCp 送粉装置
喷射沉积法:
镁熔体 喷嘴 雾化室 沉积底盘
抽风口
表5-17 几种主要镁合金材料制备方法
制备工艺 增强体类型
优点
缺点
短纤维、 挤压铸造 晶须、
颗粒
粉末冶金 颗粒
Al2O3纤维
涂覆Y2O3 (~1m厚)
涂覆W (~0.5m厚)
电镀镍层 (~0.5m厚)
纤维排布在镍 基合金薄板之间
真空加压 扩散结合法
Al2O3f/Ni3Al复合材料
镍基复合材料的性能
图5-3 Al2O3/Ni3Al,Ni3Al基体(真空热压+热挤压) 以及铸造Ni3Al的比屈服强度和温度的关系
增强体: SiC、TiC、TiB2、TiB等颗粒 制备方法: 熔铸法;
固相法:粉末冶金并应用原位反应技术,采用真空高温活化烧 结、真空热压及等静压等特殊工艺。
为什么要采用原位反应技术?
因为所有的强化剂与活性的Ti基都会发生界面反应而形成一种 或是多种化合物。
氩气保护
熔铸法制备钛合金基复合材料装置示意图
搅拌铸造
晶须、 颗粒
工艺简单、成本低、 易于批量生产;铸造缺 陷少;界面结合良好;
复合材料力学性能较 高
难以直接制备形状 复杂的零件;增强 体体积分数有一定 限制
增强体分布均匀;体积 分数任意可调
工艺设备复杂;小 批量成本高;不安 全
铸造气孔较多;颗 设备简单;生产效率高 粒分布不均匀,易
偏聚
短纤维、 喷射沉积 晶须、
基体: 纯镍、镍铬合金、镍铝合金
Ni3Al合金的屈服强度具有反 常的温度关系,在600℃左 右达到最大。
NiAl合金具有高熔点、低密 度及极佳的抗氧化性能。
增强体: Al2O3、SiC 颗粒、晶须、纤维 TiC和TiB2颗粒 W丝
制备方法
❖ 例如: Al2O3f/Ni3Al复合材料、 Al2O3f/NiCr复合材料的 制备工艺
5.5 钛基复合材料
❖钛及其合金具有高强度、低密度、低热膨胀系数、优良的耐 高温和耐蚀性等性能,是高性能结构材料的首选材料。
❖钛基复合材料(TMCs)具有比钛合金更高的比强度和比模量、 极佳的耐疲劳和抗蠕变性能、以及优异的高温性能和耐蚀性能, 它克服了原钛合金耐磨性和弹性模量低等缺点。
❖可成型形状复杂的零部件,减少了废料和机加工损耗。
❖到目前为止,对Ni3Al合金基体强化效果最好的增强体是TiC颗粒。
TiC增强镍基复合材料和屈服强度与基体相似,具有反 常温度关系。 复合材料的弹性模量优于基体,但延伸率、塑性下降。
镍基复合材料的应用前景 在燃气轮机,航天等领域已经取得了较大的进展,较为成熟。 金属间化合物基复合材料一新的高温复合材料领域。
SiC在复合材料的制备及高温固溶处理中都没有发 现界面化学反应。
因此,SiC和B4C纤维、晶须或颗粒是镁基复合材料 合适的增强活力体。
为进一步提高增强体与基体合金的润湿性,增加界 面结合强度,保护增强体免受基体合金液侵蚀,寻 找合适的增强体涂层,或采用原位反应合成方法产 生增强体---对于活泼的Mg-Li基复合材料尤为重要。
增强相而言,随着温度的升高,屈服强度、拉伸强度、弹性模量
都有所降低,伸长率有所提高,说明温度对这种材料的性能有较
大的影响。对铸态复合材料进行压延,可使其力学性能大大提高
,压延之所以能达到这种效果是由于经过压延陶瓷颗粒增强相在 基体内分布更加均匀,消除了气孔、缩松等缺陷。
采用不同粘结剂的SiCW/AZ91镁基复合材料的拉伸性 能
横向:性能低于基体材料,这是由于载荷是由基材 和基材与强化剂界面来承担。
应用:航天航空事业,汽车工业
材料
SiCp/Ti-based alloy
连续SiCf/Ti-6Al-4V
连续SiCf/Ti-22Al23Nb
连续SiCf/Ti-6Al-4V 连续SiCf/Ti-22Al-
10Nb-3V-1Mo
项目或财政资助
美怀特实验室的计划 美空军资助
宇航飞机和先进战斗机的 涡轮部件
劳斯莱斯股份有限公司
超音速飞机蒙皮
德 国与以色列科学合作项 目资助
先进航空器
5.6 镁基复合材料
镁及镁合金是密度最小的复合材料之一(1.738g/cm3), 铝的66%左右,比强度和比刚度高。
基体的选择: 因纯镁的强度较低,性能不高,不适于作为镁基复合材 料的基体,一般需要添加合金元素,主要有Al、Zn、Li、 Ag、Zr、Mn、Ni和稀土金属等。利用固溶强化、沉淀强 化和细晶强化等作用提高强度。
温度℃ σ0.2MPa σbMPa δ%
E GPa
15.1% SiCp/AZ91
21
19.6% SiCp/AZ91
21
25.4% SiCp/AZ91
21
207.9 212.1 231.7
235.9 1.1 53.9 231.0 0.7 57.4 245.0 0.7 65.1
25.4% SiCp/AZ91
应用:
密度小、比强度大、比刚度高、尺寸稳定和优良的 铸造性能,正成为现代高新技术领域中最有希望采 用的一种复合材料,其综合性能优于铝基复合材料。
镁合金摩托车车轮
镁合金汽车车轮
笔记本电脑外壳
全新的宝马3系L6镁铝合金发动机,世界第一台镁 合金发动机
发动机的重量比采用铝材减轻了30%,油耗减少 了16%。
应用: 超高音速宇航飞行器和先进航空发动机 Ti-47Al-2V-7%TiB2作用导弹翼片 汽车工业
航空发动机叶轮
②连续纤维增强钛基复合材料
增强体: SiC、TiC、 SiC包覆硼纤维、耐高温的金属纤维。 制备方法:
复合难度大,只能采用固相法合成,后用热等静压、真 空热压锻造方法压实成形。 制备方法:交替叠轧法、等离子喷涂、高速物理气相沉积法
应用
美国综合高性能发 动 机
技术和高速民用运输机项 目,英国材料战略局 的 科
技远景规划
风扇叶片,压气机盘和排 气嘴和转轴等,飞机蒙皮 和刚性件供麦道公司,英 国航天飞机的纵梁蒙皮,
美国航天飞机机身结构
美国先进研究计划和国家 航空航天局资助,英国航
天局结构材料中心
汽轮机及其它航空结构件, 航空汽轮机部件
最终的结果是:复合镁合金的曲轴箱的重量比全铝曲 轴箱的重量轻了10公斤,新发动机仅重161公斤,是全 世界同一性能等级的六缸发动机中重量最轻的。
福建坤孚股份有限公司-武平
ZK60 镁合金铸锭
ME20 镁合金半连续铸棒
ME20 镁合金板
5.7 镍基复合材料
耐热一最具有前途的应用一燃气涡轮发动机的叶片
碳纤维 × ? C 不与纯镁反应,却与镁合金中的Al、Li等反应。 生成立Al4C3、Li2C2等化合物,损伤碳纤维。
需在碳纤维表面进行涂层,C-Si-O梯度涂层处理。
B4C √ ? B4C与纯镁不反应,但颗粒表面的玻璃态B2O3与Mg发
生界面反应:
4Mg(L) + B2O3(L) = MgB2(S) + 3MgO(S) 液相的产生使得润湿性增加,不但不降低界面的结合 强度,还有利于复合材料具有优良的力学性能。
177
25.4% SiCp/AZ91
260
159.6 53.2
176.4 1.5 56.0
68.6 3.6
-
20% SiCp/AZ91
25+压延 251.0
336.0 5.7 79.0
在同一温度下,SiCp体积含量增加,复合材料的屈服强度、拉伸 强度、弹性模量都有所提高,伸长率则有所下降。对于同一含量
颗粒
基体合金晶粒度小;近 无界面反应
复合材料致密度不 高;界面属机械结 合,强度不高
性能: 提高方面: 硬度、弹性模量
降低方面: 延伸率 表5-18、表5-19
表5-18 SiC(晶须、颗粒)增强镁合金复合材料的力学性能
熔炼法
表5-19 硼的长纤维增强镁合金基复合材料的力学性能
材料
SiCp/Mg复合材料不同温度的力学性 能
Mn ---提高耐腐蚀性 Zr ---细化晶粒,提高抗热裂倾向 稀土---类似Zr,同时改善铸造、焊接、耐热和消除应力。 Li ---降低密度,改善塑性
增强体:
Al2O3 × ? 3Mg + Al2O3 = 2Al + 3MgO 降低结合强度 2Mg + SiO2 = Si + 2MgO 2Mg + Si =Mg2Si(沉淀,危害界面结合强度) 因此,镁基复合材料中较少采用Al2O3 作为增强体。